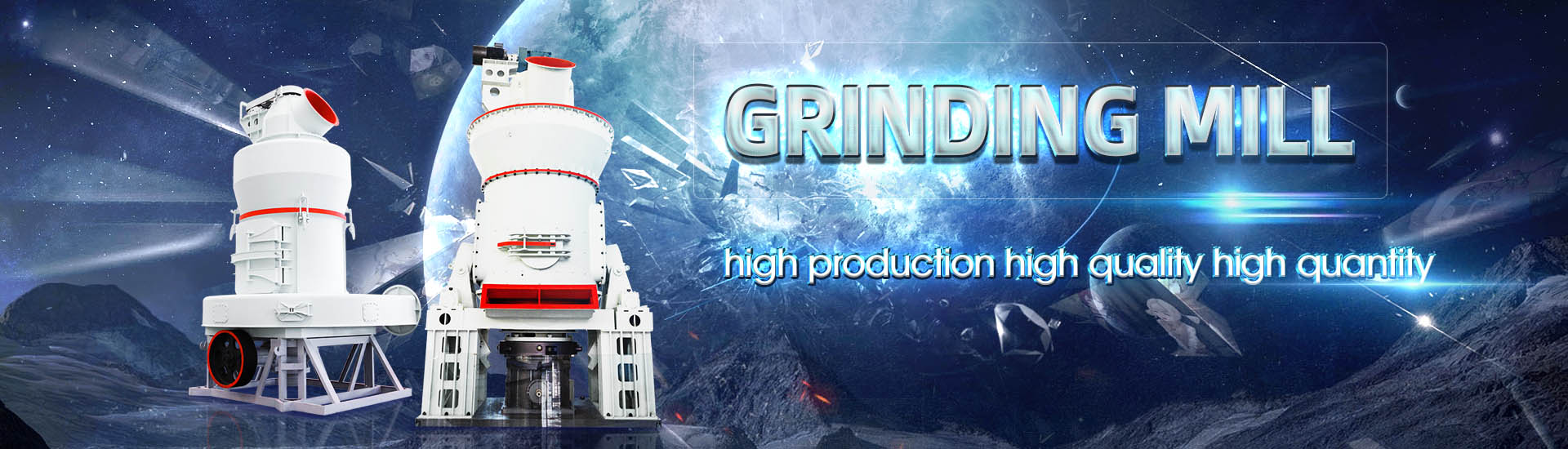
Reduced coal powder making process
.jpg)
(PDF) i) Direct Reduced Iron: Production ResearchGate
2016年3月30日 During the last four decades, a new route of ironmaking has rapidly developed for direct reduction (DR) of iron ore to metallic iron by using 2024年2月15日 Coalbased direct reduced iron (DRI) reduces CO 2 emissions by 38 % compared with traditional blast furnace–basic oxygen furnace (BFBOF) ironmaking Using a Direct reduction of iron to facilitate net zero emissions in the steel The Direct Iron Ore Smelting Reduction Process (DIOS) directly uses noncaking coal in a powder or granular form, and iron ore without the use of coke or a sintering process, which are 3A3 Direct Iron Ore Smelting Reduction Process (DIOS)Kobe Steel has developed coalbased direct reduction (DR) technologies, the FASTMET, FASTMELT and ITmk3 processes, which reduce carbon composite agglomerates (pellets or Prospects for Coalbased Direct Reduction Process KOBELCO
.jpg)
ENERGYEFFICIENT TECHNOLOGY OPTIONS FOR DIRECT
Direct reduction of iron (DRI) forms an important subsector of the Indian steel sector, accounting for about 33% of the total steel production, which is about 3415 million tonne of steel produced in2020年3月31日 The current development of coalbased smelting reduction iron making process is introduced with main features of 10 smelting reduction processes Up to now, only COREX is of bestDevelopment of Smelting Reduction Ironmaking 2015年12月1日 The direct reduction process has commonly been used by many companies to obtain metallic iron powder by the reaction of iron oxide (magnetite, hematite ore or mill scale) and reducing gases (CO/H 2) at high temperatures Direct Reduction of Ferrous Oxides to form an Iron 2020年8月14日 Today’s industrial technology offers to optimize and reutilize the resources available in terms of scum that remains after hot rolling in steel rerolling mills in Rajasthan, India Vast reserves of lowgrade coal exist and tons of mill scale are produced everyday after hot rolling in steel rerolling mills in Rajasthan, India The present research work aimed to optimize the Synthesis and Characterization of Metallic Iron Reduced from
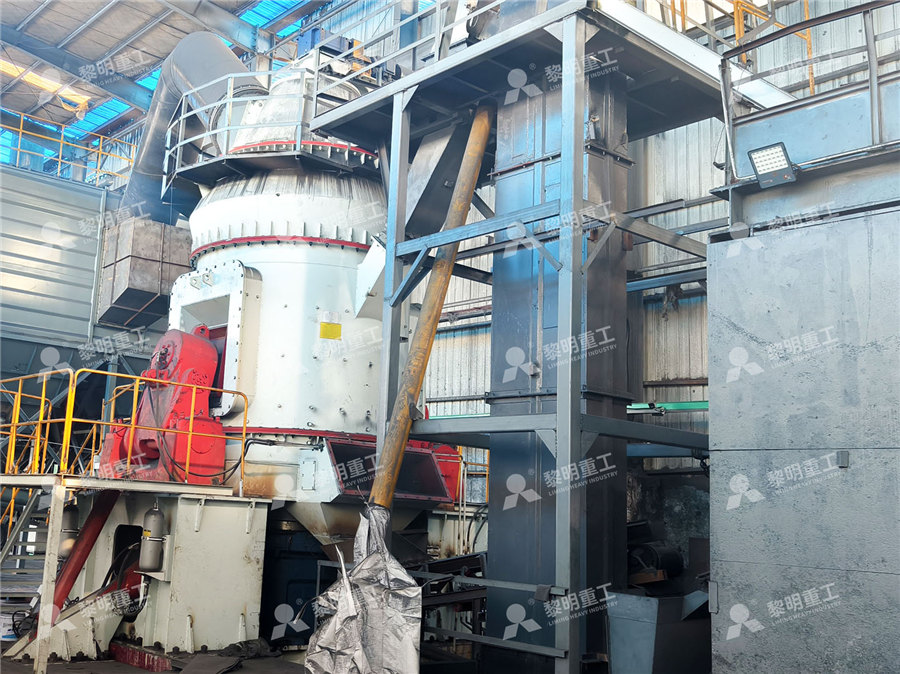
Sulphur removal in ironmaking and oxygen
2017年3月22日 The SM ladle treatment processes are comparable for both BFBOF and EAF steelmaking However, sulphur removal is less of an issue in the EAF process, since its raw materials (scrap, direct reduced iron) contain less 2015年12月1日 In this study, production of sponge iron by direct reduction of oxides and the effect of reductant on metallization were investigated In the first stage of the study, scale formed during hot rolling of slabs was reduced in a Direct Reduction of Ferrous Oxides to form an Iron 2020年2月11日 Abstract The feasibility of producing direct reduced iron from pellets made up of mill scale by utilizing coal as a reductant has been investigated The chemical and morphological characterization studies reveal that the mill scale contains around 71% Fe and comprises of a mixture of iron oxide phases such as magnetite and hematite with a little amount of wustite Investigation on the CoalBased Direct Reduction of Mill2024年2月15日 The global annual production of steel is approximately 2 billion tons, accounting for 8 % of the world's energy demand and 7 % of carbon dioxide (CO 2) emissions in the energy sectorCoalbased direct reduced iron (DRI) reduces CO 2 emissions by 38 % compared with traditional blast furnace–basic oxygen furnace (BFBOF) ironmaking Using a combination gas Direct reduction of iron to facilitate net zero emissions in the steel

Direct Reduced Iron and its Production Processes – IspatGuru
2013年3月16日 Fig 4 Flowsheet of Midrex process Coal based process In a coal based process, the reactor for the reduction reaction is a rotary kiln which is slightly inclined to the horizontal position The process of direct reduction is carried out with the operating temperatures maintained in a range from 1,000 deg C to 1,100 deg C2023年4月5日 21 Direct reduction process Direct Reduced Iron (DRI) is the product of the due to the problematic nature that is common to coke making process The noncoking coal has the advantage of not requiring preprocessing technique as intense catalytic nature that can be used in the powder metallurgical process 43 Reduction Recent Trends in the Technologies of the Direct Reduction and 2022年8月23日 Since coking coal is scarce [2,3], noncoking coal and charcoal can be used as alternative energy sources for the direct reduction process involving an iron extraction route that does not require (PDF) An Overview of the ReductionSmelting Process of Iron 2023年10月9日 This process is highly adaptable to raw material and fuel, has high product quality, and is suitable for the regions with lowpriced electricity Rotary Hearth Furnace Process A typical process is the Fastmelt process developed by the Midrex Company Iron ore powder and coal are mixed in proportion to make pelletDirect Reduction Ironmaking SpringerLink
.jpg)
Development of Smelting Reduction Ironmaking Process
2020年3月31日 The current development of coalbased smelting reduction iron making process is introduced with main features of 10 smelting reduction processes Up to now, only COREX is of best performance and 2023年12月9日 The process is developed by Pohang Iron and Steel Company and Voestalpine Group based on the COREX process, in which coal powder and mineral powder are directly used to produce hot metal In the Finex process, iron ore powder is preheated and reduced in the fourstage fluidized bed deviceSmelting Reduction Ironmaking SpringerLinkThe above process of reoxidation or rusting process results in the loss of metalized iron DRI fines, when left for long period of time, lead to loss over long period of storage which has been estimated to be as high as 15% by weight per month [1] Satish et al [2] described the usage of mill scale briquettes in steel making process by usingCold Briquetting of DRI Fines for Use in Steel Making Process2018年6月21日 The direct reduced iron process (DRI) In the electric steel process, the sponge iron obtained from the direct reduced iron process is used for crude steel making In general, scrap is also added to this process as well as Direct reduced iron process tecscience
.jpg)
Briquetting Process an overview ScienceDirect Topics
In BBCP, a maximum of 30% of coal is formed into briquettes, which are blended with coal powder and charged into the coking chamber (Yoshinaga et al, 1976) The apparent density of the briquette is 1100 drykg/m 3 , and the packing density is increased from 680700 to 740–750 kg/m 3 by a process of briquette blending2021年3月8日 Electric Arc Furnace (EAF): This steel making process using electric arc to heat charged materials such German research indicates that when using biomass coke powder to completely replace coal powder, Kirschen, M, Badr, K, Pfeifer, H (2011) Influence of direct reduced iron on the energy balance of the electric arc LowCarbon Production of Iron Steel: Technology Options, 2020年3月3日 The HIsmelt process combines prereduction and preheating of fine ore in a fluidized bed with final reduction in a smelter The smelter operates with enriched hot blast, generated in blast furnace type stoves A unique feature of the process is the submerged injection of coal and prereduced ore using the socalled solid injection lances (SIL)Smelting Reduction Processes SpringerLink2012年9月26日 1 Introduction During the last decades, the continuous casting process has made enormous advances and more than 90% of the world steel production is now continuously cast []In this process, the liquid steel is poured into a watercooled copper mould through a submerged entry nozzle (SEN), see Figure 1 []At this stage the solidification process beginsMould Fluxes in the Steel Continuous Casting Process
43.jpg)
Lowcarbon production of iron and steel: Technology options, economic
2021年4月21日 Japanese research suggests that pressed woody biomass can be used to prepare metallurgical coke after mixing with coal, achieving partial decarbonization 61 German research indicates that when using biomass coke powder to completely replace coal powder, the amount of carbon dioxide input in the blast furnace has been reduced by up to 45% 62 2019年6月1日 The ash content , sulphur content and volatile matter content of individual coking coals making a blend were found to be additive Carbonisation tar addition reduced ash content in the coal blend from 920 to 863 wt% A 568% reduction in coal fines (powder) was observed which consequently resulted in less coal dust pollution to the encironmentReduction in coal fines and extended coke production through the 2023年9月5日 It is the most challenging and significant factor in injection molding and constitutes the longest step in the process 26 The Origin of Powder Injection Molding Powder injection molding is a new process that combines powder metallurgy technology with plastic injection moldingPowder Metallurgy: A Comprehensive Guide for Beginners2018年11月26日 Coal briquetting process A simple coal briquetting process normally follow the way below Coal dust picking (making) – Mixing (with or without binder) – Briquetting – Drying Every step we should make things Coal briquetting technology process, binder and the
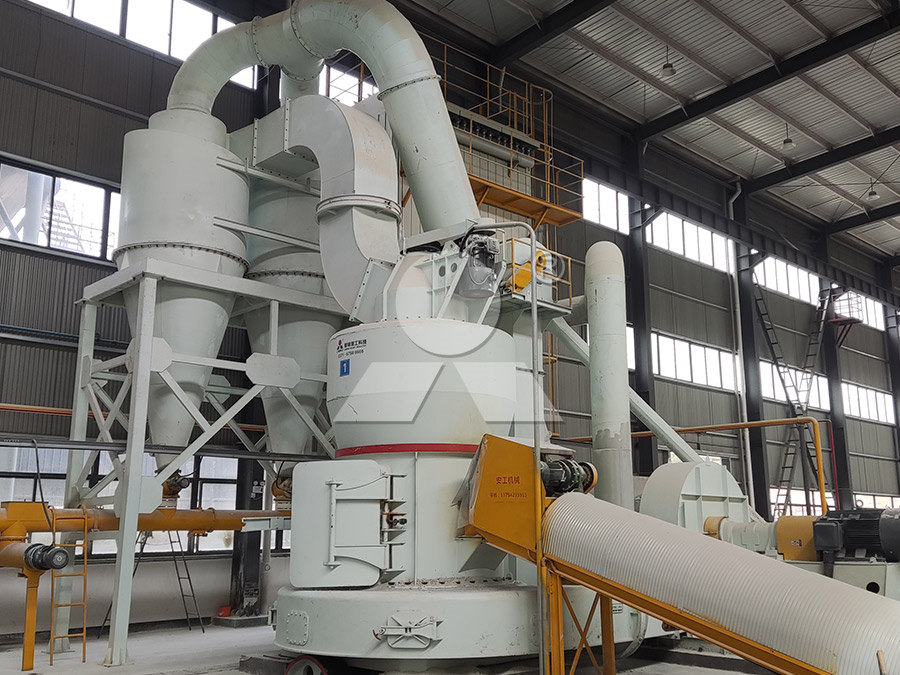
Comparative life cycle assessment of natural gas and coalbased
2022年5月1日 India's steel sector is unique in technology diversity integrated (BFBOF) process coexists with significant DRI capacity The Indian ironmaking industry is one of the more GHGintensive globally, with a noted emissions intensity of about 23 tCO 2 /TCS well above the global average of 185 tCO 2 /TCS (IEA, 2020; WSA, 2020a)Heavy reliance on coal, 2017年10月17日 The newer processes can use coal instead of coke and do not require nitrogen injection The elimination of nitrogen prevents the generation and release of nitrous oxide (NO) gas into the environment In the smelting From Ore to Iron with Smelting and Direct Iron The iron ore production has significantly expanded in recent years, owing to increasing steel demands in developing countries However, the content of iron in ore deposits has deteriorated and lowgrade iron ore has been processed The fines resulting from the concentration process must be agglomerated for use in iron and steelmaking This chapter shows the status of the Iron Ore Pelletizing Process: An Overview IntechOpen2023年12月1日 Industrialscale hydrogenironmaking, also known as direct reduction of iron (DRI) using hydrogen, is a process that aims to produce iron without the use of fossil fuels (Chevrier, 2020; van Vuuren et al, 2022; Tang et al, 2020; Wang et al, 2021; Ledari et al, 2023)This process has the potential to significantly reduce carbon dioxide emissions The perspective of hydrogen direct reduction of iron
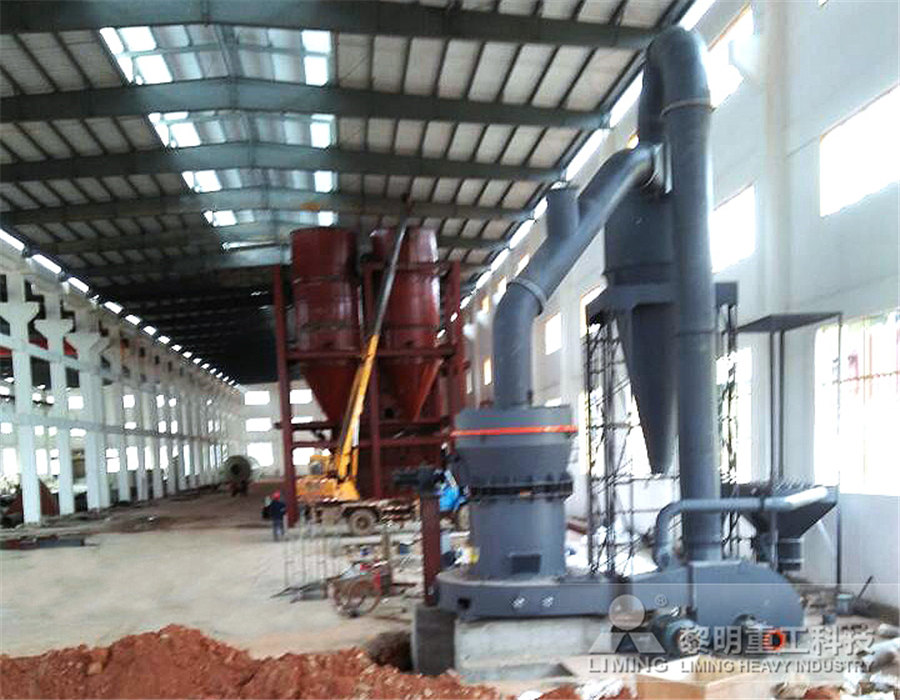
DirectReduced Iron an overview ScienceDirect Topics
Direct reduced iron is iron ore in the form of lumps, fines or pellets that have had the oxygen removed by using hydrogen and carbon monoxide Typical sources of carbon monoxide are natural gas, coal gas, and coal Other energy inputs into the production process often include oil 2019年7月19日 Operational efficiency, coke quality, and productivity are the main challenges obtained through stampcharged coke making technology The coal moisture control process (CMCP) is employed to monitor and adjust the moisture content of charge coals in the coal pretreatment procedure, for increasing the production of coke and enhancing the coke Coke Making: Most Efficient Technologies for Greenhouse Emissions 2022年7月21日 The direct reduction process is one of the solutions for the manufacturing of iron which is energyefficient and low in CO2 emissions Titanomagnetitetype iron sand is an important alternative source of iron minerals for countries with long coastlines Thus, the process of making iron through direct reduction and using iron sand as the main raw material becomes The Role of a Mixture of Coal and Dolomite in the Direct It was reported that mill scale iron powder with more than 99% degrees of metallization, 97% total Fe, and more than 96% metallic Fe was synthesized after 4 h of reduction at 1200 °C and 1300 °C a) SEM of reduced iron powder (b) SEM of reduced iron powder
.jpg)
Substitution of Biomass for Coal and Coke in Ironmaking Process
2011年5月1日 Replacing 20% of coal by biomass could also reduce the fossil emissions by 05 MtCO2/yr (62% of instate industrial emissions) without making changes to the facilities2020年8月14日 Today’s industrial technology offers to optimize and reutilize the resources available in terms of scum that remains after hot rolling in steel rerolling mills in Rajasthan, India Vast reserves of lowgrade coal exist and tons of mill scale are produced everyday after hot rolling in steel rerolling mills in Rajasthan, India The present research work aimed to optimize the Synthesis and Characterization of Metallic Iron Reduced from 2017年3月22日 The SM ladle treatment processes are comparable for both BFBOF and EAF steelmaking However, sulphur removal is less of an issue in the EAF process, since its raw materials (scrap, direct reduced iron) contain less Sulphur removal in ironmaking and oxygen 2015年12月1日 In this study, production of sponge iron by direct reduction of oxides and the effect of reductant on metallization were investigated In the first stage of the study, scale formed during hot rolling of slabs was reduced in a Direct Reduction of Ferrous Oxides to form an Iron
.jpg)
Investigation on the CoalBased Direct Reduction of Mill
2020年2月11日 Abstract The feasibility of producing direct reduced iron from pellets made up of mill scale by utilizing coal as a reductant has been investigated The chemical and morphological characterization studies reveal that the mill scale contains around 71% Fe and comprises of a mixture of iron oxide phases such as magnetite and hematite with a little amount of wustite 2024年2月15日 The global annual production of steel is approximately 2 billion tons, accounting for 8 % of the world's energy demand and 7 % of carbon dioxide (CO 2) emissions in the energy sectorCoalbased direct reduced iron (DRI) reduces CO 2 emissions by 38 % compared with traditional blast furnace–basic oxygen furnace (BFBOF) ironmaking Using a combination gas Direct reduction of iron to facilitate net zero emissions in the steel 2013年3月16日 Fig 4 Flowsheet of Midrex process Coal based process In a coal based process, the reactor for the reduction reaction is a rotary kiln which is slightly inclined to the horizontal position The process of direct reduction is carried out with the operating temperatures maintained in a range from 1,000 deg C to 1,100 deg CDirect Reduced Iron and its Production Processes – IspatGuru2023年4月5日 21 Direct reduction process Direct Reduced Iron (DRI) is the product of the due to the problematic nature that is common to coke making process The noncoking coal has the advantage of not requiring preprocessing technique as intense catalytic nature that can be used in the powder metallurgical process 43 Reduction Recent Trends in the Technologies of the Direct Reduction and

(PDF) An Overview of the ReductionSmelting Process of Iron
2022年8月23日 Since coking coal is scarce [2,3], noncoking coal and charcoal can be used as alternative energy sources for the direct reduction process involving an iron extraction route that does not require 2023年10月9日 This process is highly adaptable to raw material and fuel, has high product quality, and is suitable for the regions with lowpriced electricity Rotary Hearth Furnace Process A typical process is the Fastmelt process developed by the Midrex Company Iron ore powder and coal are mixed in proportion to make pelletDirect Reduction Ironmaking SpringerLink2020年3月31日 The current development of coalbased smelting reduction iron making process is introduced with main features of 10 smelting reduction processes Up to now, only COREX is of best performance and Development of Smelting Reduction Ironmaking Process