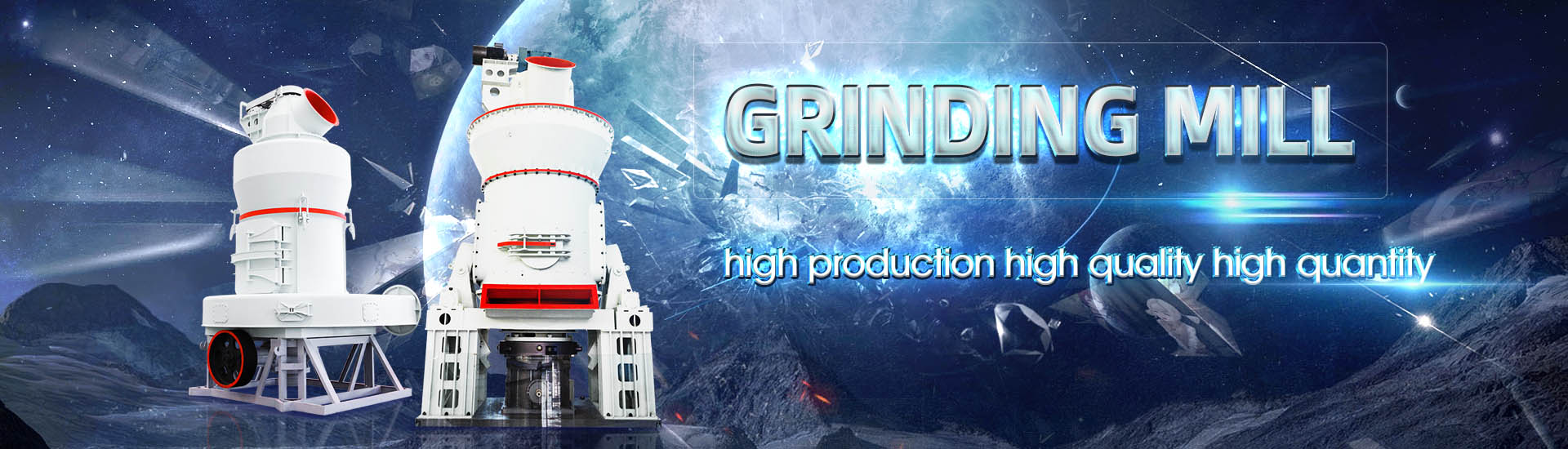
Coal injection mill
.jpg)
Pulverized coal injection method Wikipedia
The PCI method is based on the simple concept of primary air (termed the "conveying gas") carrying pulverized coal which injected through a lance to the tuyere (midbottom inlet of a blast furnace), then mixed with secondary hot air (termed the "blast") supplied through a blowpipe in the tuyere and then piped to a 展开The pulverized coal injection technology is based on a combination of several unit operations Main unit operations include: Hot blast backpressure as well as pressure drops in pneumatic Pulverized Coal Injection Paul Wurth2018年10月21日 Pulverized coal injection (PCI) is a wellestablished technology for hot metal (HM) production in a blast furnace (BF) It is practiced in most of the BFs and all the new BFs Understanding Pulverized Coal Injection in Blast Furnace2024年8月6日 In an integrated steel plant, the pulverized coal injection (PCI) mill plays an important role in providing pulverized coal to the blast furnace The main purpose of using PCI Failure Analysis of Pulverized Coal Injection (PCI) Mill Grinding
.jpg)
3A2 Pulverized Coal Injection for Blast Furnaces (PCI)
caking coal, pulverized coal increases the potential for the injection material owing to the adaptability of coal resources Pulverized coal injection technology has the potential to spur Increasing steel demand and growing competition from scrapbased minimills is forcing blast furnace (BF)based plants to improve their performance in order to reduce operating costs and, at the same time, increase productivity One way Use of PCI in blast furnaces ICSC2024年1月1日 Pulverized coal injection of blast furnace ironmaking is a smelting technology where pulverized coal is directly blown into the blast furnace hearth from the tuyere to replace Pulverized Coal Injection of Blast Furnace IronmakingPaul Wurth’s injection technology is based on our advanced ‘Dense Phase’ knowhow resulting in minimum nitrogen consumption (reduced operating costs) and low coal conveying speed – resulting in low pipeline and component abrasion, Blast Furnace Ironmaking Paul Wurth
46.jpg)
Suitability of pulverised coal testing facilities for blast furnace
2019年1月20日 Identifying coals suitable for blast furnace injection has become increasingly important due to rising injection rates This review of traditional pulverised coal reactivity Coal Injection 3 Advanced design 4 Technology you can trust 7 Technikum The Claudius Peters Technikum (Technical Center) offers clients the advantages of a mill inlet, thereby minimizing oxygen within the system and reducing the possibility of coal dust explosions Vertical millPulverized Coal Injection Ammermann2 The hot air is used for transportation of the recirculating coal within the mill and also for transporting the coal from the pulverizer to the furnace As the coal is continuously reduced in size, the smaller/lighter particles are swept from the Bowl Mill Coal Pulverizer COAL HANDLING PLANTSThe ATOX mill will grind and dry coal containing more than 20% moisture in one operation The possibility of customersupplied parts, along with the low civil costs that accompany compact mill installation, add to the excellent economy of the ATOX coal mill Working principles The raw coal enters the mill via a rotary sluice and feed chuteATOX COAL MILL
.jpg)
3A2 Pulverized Coal Injection for Blast Furnaces (PCI)
pulverized coal ratio to a 130 kg/t level, (Fig 2) Table 1 shows the various types of injection for the blast furnace pulverized coal equipment Table 2 shows the highest level attained in Japan for the typical operational index of blast furnaces utilizing pulverized coal injection technologyAbstract In an integrated steel plant, the pulverized coal injection (PCI) mill plays an important role in providing pulverized coal to the blast furnace The main purpose of using PCI coal is to reduce the hot metal production cost through the utilization of noncoking coal and to extend the available coke oven life Any unplanned outage of Failure Analysis of Pulverized Coal Injection (PCI) Mill Grinding Control Blast Furnace Pulverized Coal Injection to Increase PCI Rates Roland Weiser, Ingo Braune, Peter Matthes AMEPA GmbH Jülicher Str 320 D52070 Aachen Germany Tel: +49241168040 Fax: +492411680444 Email: info@amepa Key words: Pulverized coal injection, Coal flow meter, Controlled injection, Equal distribution, Increase of PCIControl Blast Furnace Pulverized Coal Injection to Increase PCI 2023年6月15日 The blast furnace injection process system is mainly composed of raw coal storage and transportation system, dry gas preparation system, pulverized coal preparation system, pulverized coal conveying system, pulverized coal injection system, and gas supply system (Fig 1)There is also a computer control center to control the entire pulverized coal Pulverized Coal Injection of Blast Furnace Ironmaking
.jpg)
Pulverized Coal Injection Project, MediumSpeed Vertical Mill,
Pulverized Coal Injection Project, MediumSpeed Vertical Mill, Ball Mill,Tìm chi tiết về Pulverized Coal Injection Project, PCI System của Pulverized Coal Injection Project, MediumSpeed Vertical Mill, Ball Mill Handan Metallurgical Engineering Research Co Ltd2024年1月1日 The blast furnace injection process system is mainly composed of raw coal storage and transportation system, dry gas preparation system, pulverized coal preparation system, pulverized coal conveying system, pulverized coal injection system, and gas supply system (Fig 1)There is also a computer control center to control the entire pulverized coal Pulverized Coal Injection of Blast Furnace IronmakingSignifi cant technical improvement in 2000, introducing mediumspeed coal mill for pulverizing,bag type fi rst grade powder collection,two streams of serial hopper direct injection, applied on two BFs (1780m3, Coal injection is set and the related parameters are automatically adjusted according to the requirements高炉喷煤技术 SHOUGANGIn this session, Ankit Ras will be discussing about Pulverizer Plant and Coal Mill from the TPP Engineering Watch the entire video to learn more about PulvePulverizer Plant Coal Mill Working With Major
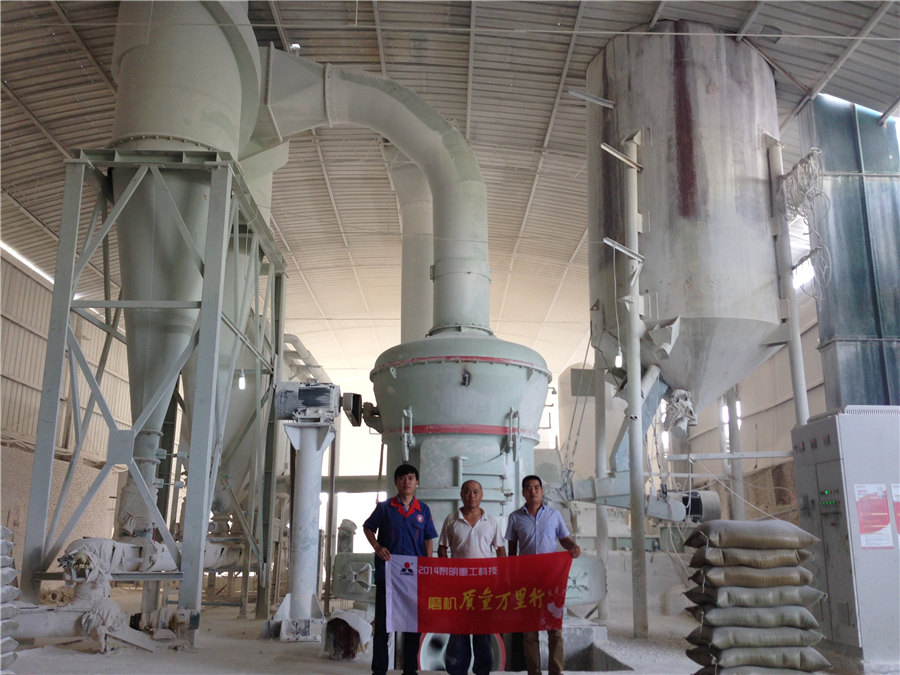
Pulverized Coal Boiler an overview ScienceDirect Topics
Fuel preparation for a pc boiler occurs in a mill, where coal is typically reduced to 70% through a 200mesh (74μm) screen Figure 2 shows a particlesize distribution from a bowlmill grinder typically used in power plants A typical utility specification for particle size distribution of the coal is that 70% of the mass should pass through a 200mesh screen, which is equivalent to 70% Coal Injection) 1990 Central coal grinding plant (LM 263 D) for gas and steam power station (coal gasification) 1992 Central coal grinding plant (LM 263 D) for the production of lignite (brown) coal dust 2002 Coal grinding plant (LM 232 D) for grinding wood pellets for power stations 2005 First 4roller pressure mill (LM 434 D) becomesLOESCHEMILLS2024年9月15日 Currently, the steelmaking process uses a pulverized coal injection (PCI) system that serves as the heat source and reductant for ironmaking (blast furnace and FINEX) where system uses expensive highgrade coal and high operating costs Hydrogen steelmaking is currently being developed to achieve carbonfree operation To achieve a softlanding during Combustion visualization analysis of alternative fuels in the Pulverized Coal Injection Project, coal mill Blast furnace PCI /rotary kiln PCI/vertical kiln PCI have been the main method for lime stone roasting, pellet roasting, coking, iron increasing, reduced cost, improve high efficiency smelting ,and promote blast furnace running smoothly, also is the main method for technical progress of blast furnace iron makingBall mill/ Vertical mill/Pulverized Coal Injection Handan
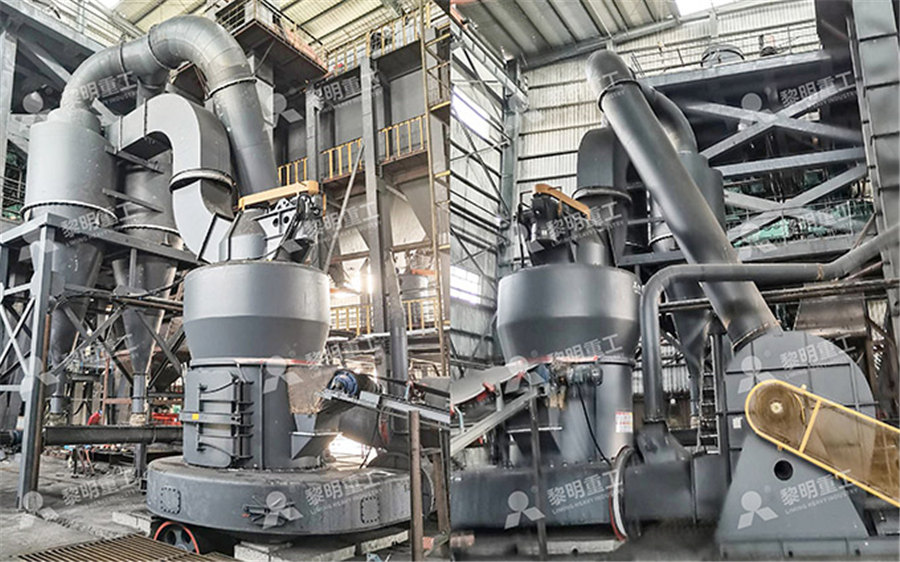
Effects of Cofiring Coal and Biomass Fuel on the Pulverized Coal
2022年1月17日 CO2 emissions are a major contributor to global warming Biomass combustion is one approach to tackling this issue Biomass is used with coal combustion in thermal power plants or with blast furnaces (BFs) because it is a carbonneutral fuel; therefore, biomass provides the advantage of reduced CO2 emissions To examine the effect of cofiring on pulverized coal 2022年6月1日 Coal pulverizer Power Plant #boiler #mechanical coal mill Operation maintenance Question Answer for interviews #thermalpowerplantcoal pulverizer plant Coal Mill working and operationOur ATOX® Coal Mill can also be equipped with a water injection system to compensate for low water content in the raw coal The ATOX® Coal Mill’s large rollers can handle up to 200mm feed lumps, reducing the need for a separate crusherATOX® Coal Mill FLSmidth Cementalso find an application in grinding a wide variety of coal types in cement and power plants Gebr Pfeiffer SE (GPSE) describes its vertical roller mills for coal grinding and provides a case study of an MPS225BK installed at CBR’s Lixhe cement works in Belgium COAL GRINDING Figure 1: MPS coal grinding mill with SLS highefficiency classifierCOAL GRINDING IMPS: more than meets the eye Gebr Pfeiffer
.jpg)
SAILBhilai Steel Plant Blast Furnace, SMS3 and Plate Mill create
2023年1月31日 Blast Furnaces, SMS3 and Blast Furnace8 and Plate Mill of SAILBhilai Steel Plant have set new records in production as well as in technoeconomics Skip to content Top Menu November 28, 2024 About Us; a new record was created in Blast Furnaces by increasing the quantity of daily Coal Dust Injection (CDI) By 30th January 2020年4月19日 ABSTRACT Partial substitution of pulverized coal (PCI) by renewable biocarbon for blast furnace injection is a practical approach to reduce GHGs in the steel production sector For using biocarbon as feedstock, it is critical to measure its grindability to understand its milling behavior compared to that of typical PCI coal, and thus help decide on adjusting grinding Grindability of biocarbon and coal blends in rolling mill2019年1月20日 The maximum coal injection rate is believed to be somewhere around 270 kg/t H M as a consequence of thermochemical and coke/burden PCI injection level during the blast furnace process would lead to decreased CO 2 emissions of an integrated steel mill due to a reduced coke consumption and production In addition, coking Suitability of pulverised coal testing facilities for blast furnace 2021年3月12日 1 Introduction Two mill systems are employed for most coal grinding applications in the cement industry These are, on the one hand, vertical roller mills (VRM) that have achieved a share of almost 90% and, on the other MPS mills for coal grinding AYS Engineering
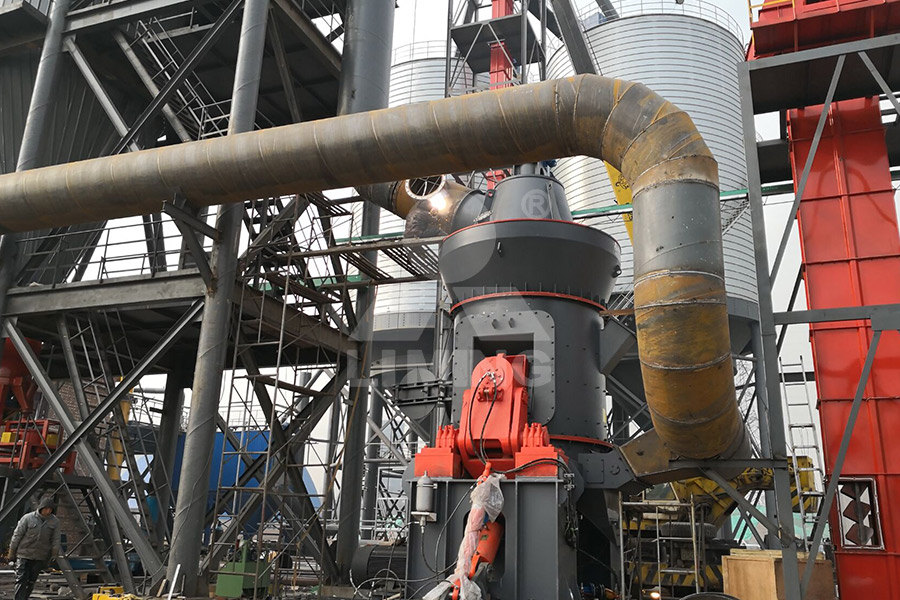
Pulverized coal injection (PCI) Iron Steel Kuettner Group
Pulverized Coal Injection (PCI) using the denseflow method The Küttner developed and perfected denseflow method offers several advantages over a lowerdensity system Higher injection rates are achieved with simultaneously lower coke rates, which can optimize the fuel costs of the blast furnaceThe replacement of pulverised coal injection (PCI) coal with hydrogen in blast furnaces looks like being an early decarbonising application Lowercost PCI coal is injected into blast furnaces to reduce coking coal consumption Essentially highquality thermal coal, PCI coal can be sold into either the metallurgical or thermal coal marketsPCI coal for steelmaking the first metallurgical coal grade to be In November 2011 Loesche GmbH obtained a contract for the first ever 4roller coal mill for the injection of pulverized coal into a blast furnace (PCI technology) The Loesche Mill Type LM 434 D has a capacity of 120 t/h and will be installed in the A coal mill for the injection of pulverized coalThe relative importance of different aspects of PCI coal quality has varied, as the technology for injection has improved and the rate of injection increased In the late 1970's, triggered by the oil crisis, interest in PCI was renewed and coal was considered as an PCI Coal Tech
36.jpg)
Coal Pulverizer Injection Machine JXSC Machine
The coal pulverizer and injection machine is a combined machine of hammer mill crushing and centrifugal air supply used for pulverizing coal and spraying coal powder directly into the combustion chamber for combustion in various reaction furnaces, boilers, drying kilns, tunnel kilns, annealing ( annealing) kiln, etc 【MP Series Coal Pulverizer】 FIRST SUCCESSFUL PULVERIZED COAL INJECTION STARTUP IN RUSSIA AT EVRAZ NTMK1 Alexey Kushnarev2 Philipp Bermes 3 Pierre Mahowald4 Georges Stamatakis5 Stephan Becker 6 André Oliveira7 (~ 4 h at nominal pulverised coal output) Mill type Loesche LM 353D Vertical roller mill with integrated dynamic classifier Mill nominal throughput 80 t/hFIRST SUCCESSFUL PULVERIZED COAL INJECTION ABM 1) The document provides a job safety analysis for the task of starting a coal mill It lists the preparation required, including lockout tagout, tool box talks, and checks of equipment 2) The task is broken down into steps, and potential hazards are identified for each step Controls to mitigate risks are also outlined 3) Responsibilities for completing checks and controls are 02 HIRAJSACoal Mill Operation PDF Safety NatureCoal Injection 3 Advanced design 4 Technology you can trust 7 Technikum The Claudius Peters Technikum (Technical Center) offers clients the advantages of a mill inlet, thereby minimizing oxygen within the system and reducing the possibility of coal dust explosions Vertical millPulverized Coal Injection Ammermann
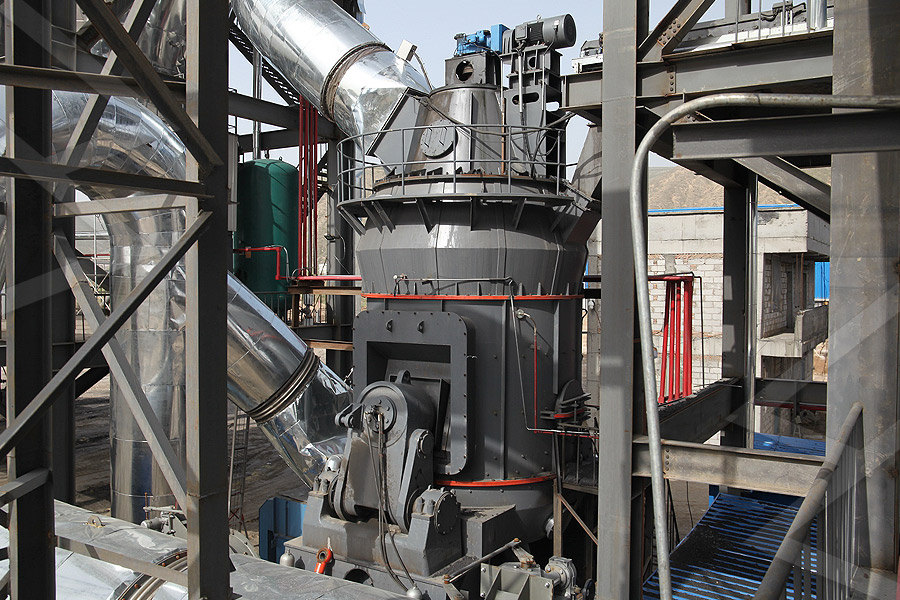
Bowl Mill Coal Pulverizer COAL HANDLING PLANTS
2 The hot air is used for transportation of the recirculating coal within the mill and also for transporting the coal from the pulverizer to the furnace As the coal is continuously reduced in size, the smaller/lighter particles are swept from the The ATOX mill will grind and dry coal containing more than 20% moisture in one operation The possibility of customersupplied parts, along with the low civil costs that accompany compact mill installation, add to the excellent economy of the ATOX coal mill Working principles The raw coal enters the mill via a rotary sluice and feed chuteATOX COAL MILLpulverized coal ratio to a 130 kg/t level, (Fig 2) Table 1 shows the various types of injection for the blast furnace pulverized coal equipment Table 2 shows the highest level attained in Japan for the typical operational index of blast furnaces utilizing pulverized coal injection technology3A2 Pulverized Coal Injection for Blast Furnaces (PCI)Abstract In an integrated steel plant, the pulverized coal injection (PCI) mill plays an important role in providing pulverized coal to the blast furnace The main purpose of using PCI coal is to reduce the hot metal production cost through the utilization of noncoking coal and to extend the available coke oven life Any unplanned outage of Failure Analysis of Pulverized Coal Injection (PCI) Mill Grinding
.jpg)
Control Blast Furnace Pulverized Coal Injection to Increase PCI
Control Blast Furnace Pulverized Coal Injection to Increase PCI Rates Roland Weiser, Ingo Braune, Peter Matthes AMEPA GmbH Jülicher Str 320 D52070 Aachen Germany Tel: +49241168040 Fax: +492411680444 Email: info@amepa Key words: Pulverized coal injection, Coal flow meter, Controlled injection, Equal distribution, Increase of PCI2023年6月15日 The blast furnace injection process system is mainly composed of raw coal storage and transportation system, dry gas preparation system, pulverized coal preparation system, pulverized coal conveying system, pulverized coal injection system, and gas supply system (Fig 1)There is also a computer control center to control the entire pulverized coal Pulverized Coal Injection of Blast Furnace IronmakingPulverized Coal Injection Project, MediumSpeed Vertical Mill, Ball Mill,Tìm chi tiết về Pulverized Coal Injection Project, PCI System của Pulverized Coal Injection Project, MediumSpeed Vertical Mill, Ball Mill Handan Metallurgical Engineering Research Co LtdPulverized Coal Injection Project, MediumSpeed Vertical Mill, 2024年1月1日 The blast furnace injection process system is mainly composed of raw coal storage and transportation system, dry gas preparation system, pulverized coal preparation system, pulverized coal conveying system, pulverized coal injection system, and gas supply system (Fig 1)There is also a computer control center to control the entire pulverized coal Pulverized Coal Injection of Blast Furnace Ironmaking
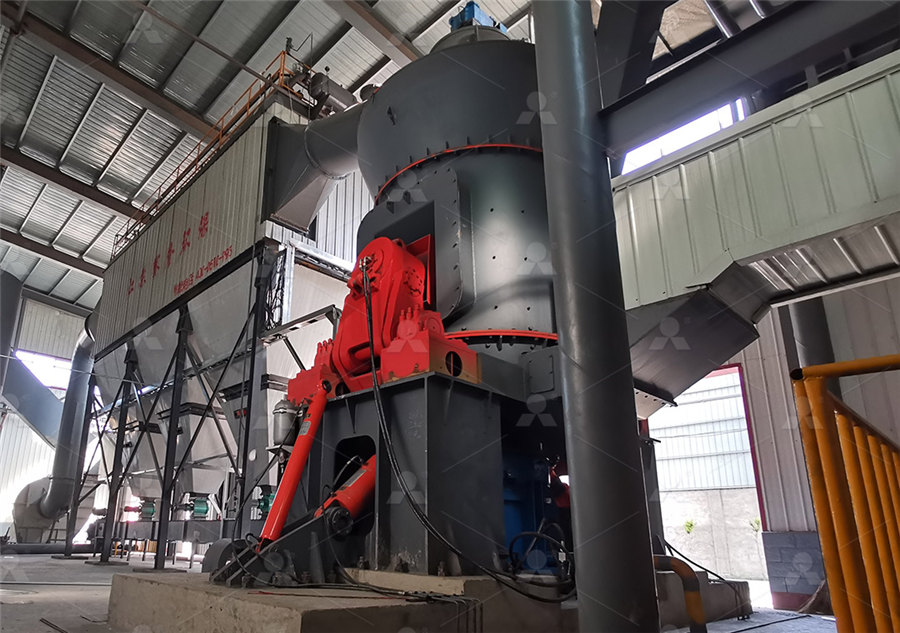
高炉喷煤技术 SHOUGANG
Signifi cant technical improvement in 2000, introducing mediumspeed coal mill for pulverizing,bag type fi rst grade powder collection,two streams of serial hopper direct injection, applied on two BFs (1780m3, Coal injection is set and the related parameters are automatically adjusted according to the requirements