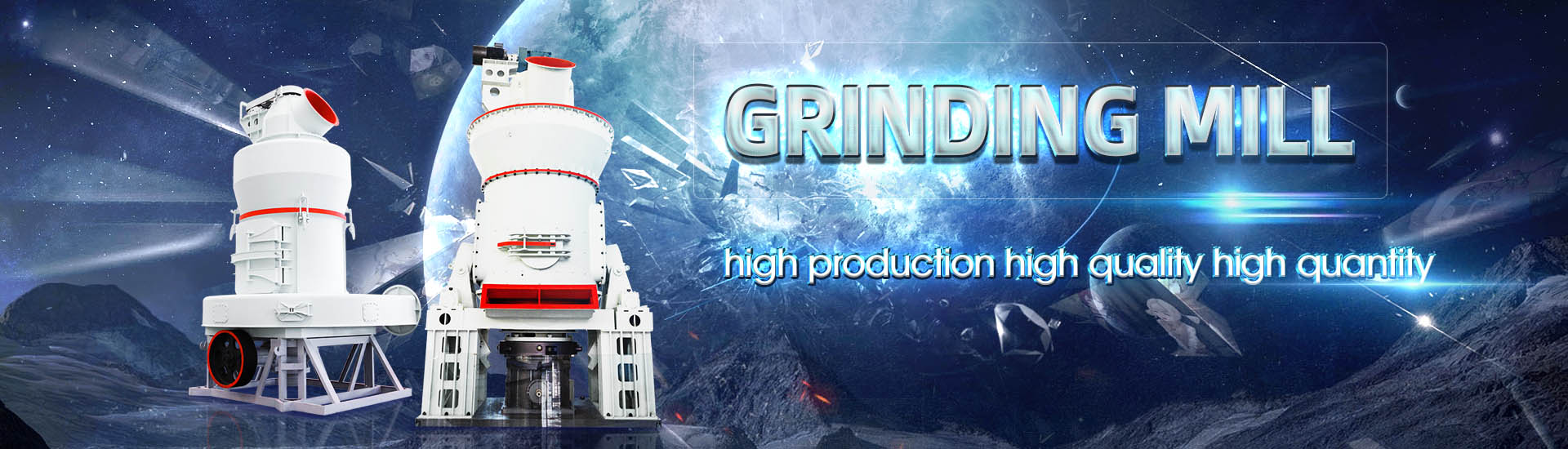
Energysaving technology of crushing instead of grinding for calcite ore
.jpg)
Modeling and Improving the Efficiency of Crushing
2023年6月30日 This article presents a systematic review of the task of improving the energy efficiency of crushing units This is achieved by studying modelling methods and results, the automation of crushing and grinding 2017年3月1日 Various alternative pretreatment methods have been tried by experts around the globe Although these methods yielded positive results in terms of reduction in energy Pretreatment of rocks prior to comminution ScienceDirect2023年6月30日 This is achieved by studying modelling methods and results, the automation of crushing and grinding processes, and the wear reduction of crusher componentsModeling and Improving the Efficiency of Crushing EquipmentA large mining company successfully achieved significant energy savings by introducing highefficiency crushing equipment and vertical mills, along with comprehensive optimization ofTechnological Innovation: Achieving Energy Savings and Medium
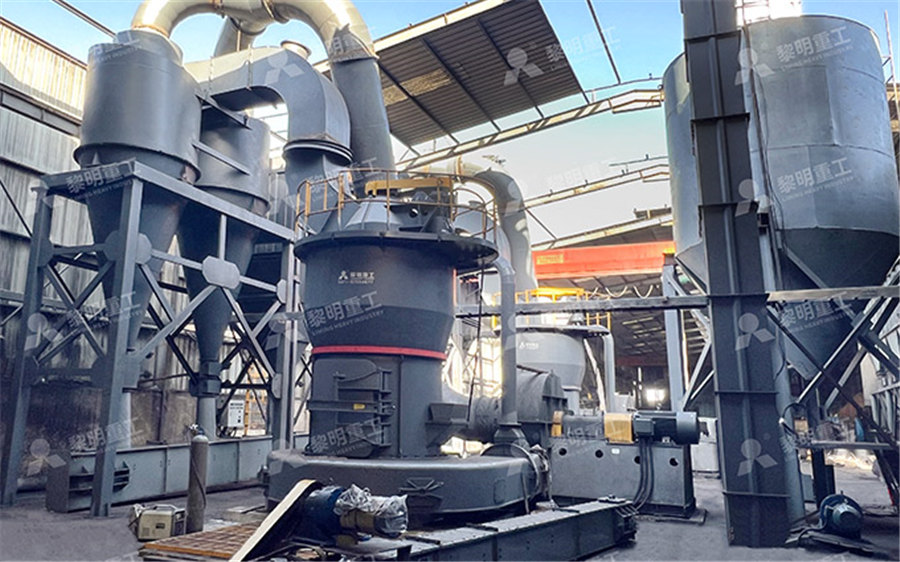
Sustainable Processing of Mineral Resources
A high potential for energy savings resides in the introduction of certain crusher types that help to move the size distribution towards fine particles, the application of HPGR or chokefed cone 2023年9月18日 “Move that limit down to 8 or 6 millimeters and there are significant amounts of energy, as well as water, to be saved Our stationary crushers have an energy efficiency of 50 Saving energy with sustainable solutions Sandvik Group2022年8月20日 Steam accelerates the reaction rate and reduces the calcination temperature by ∼100 °C Adding steam reduces the energy requirement, thus reducing the CO 2 footprint of The steamassisted calcination of limestone and dolomite for 2020年1月13日 In the way towards sustainability, the next generation of efficient and heavy duty of Sandvik's crushers, CH860 and CH865, are introduced for efficient crushing As the ENERGY EFFICIENCY IN COMMINUTION GETTING MORE FROM
G[R.jpg)
The Effects of Blasting on Crushing and Grinding Efficiency and
2003年1月1日 This paper examines the role blasting plays in optimum crushing and grinding with the emphasis on energy reduction The role of different blasting energy input on 2022年7月31日 Crushing develops more efficient particle breaking, avoiding fine particles, and optimizing energy consumption The liberation step is the grinding process and consumes Advances in Ore Processing Technologies: Crushing, Milling and2019年10月8日 The crushing and grinding operations are an important part of the processing of mineral resources, and it is also operation with high investment and high energy consumption In the case of metal mines, equipment Crushing and Grinding Process JXSC Machine2015年12月26日 In mineral processing or metallurgy, the first stage of comminution is crushing Depending of the type of rock (geometallurgy) to be crushed, there are 2 largely different techniques at your disposition for Crushing in Mineral Processing 911Metallurgist
.jpg)
Grinding down energy consumption in
2019年6月21日 According to the Coalition for EcoEfficient Comminution, comminution – the process of crushing and grinding ore – is by far the most energy consuming step in the mining processHigh Pressure Grinding Roll and Magnetic Separation for Energy Saving in Grinding and Simultaneously Improving Processing Capacity: A Case Study of a Magnetite Ore Jianwen Yu1,2,3 Yaxiong An 1,3 Peng Gao1,2,3 Yuexin Han 1,2,3 Received: 20 February 2024 / Accepted: 21 May 2024 / Published online: 31 May 2024High Pressure Grinding Roll and Magnetic Separation for Energy Saving 2017年11月18日 Therefore, optimizing the process of crushing and grinding is of great significance for achieving energysaving and costreducing in minerals processing Mineral processing is a predominant technology used to fulfill the enrichment of valuable minerals from coexisted (undesired) gangue minerals and then, provides raw materials for the following Tuning the Morphology and Surface Property of Mineral Particles 2017年1月27日 This paper presents experimental comparison of two machine crushing technologies: onestage and twostage The study was carried on a model doubletoggle jaw crusher which allows crushing forces (PDF) Analysis of Energy Consumption of Crushing Processes
.jpg)
Effect of grinding aids on the kinetics of fine grinding energy
2009年7月1日 Chemicals used as grinding aids, particularly in dry grinding processes, lead to a significant increase in energy saving, cement strength, surface area, energy efficiency, size reduction, avoid 2022年1月1日 Processing includes primary and secondary crushing followed by HPGR grinding and ball milling, magnetic separation, reverse flotation and thickening to produce 12Mtpa of magnetite concentrate HPGR technology was implemented for fine crushing to reduce the energy consumption processing very hard ore (Fig 821)Comminution and classification technologies of iron ore2016年10月5日 In this chapter an introduction of widely applied energyefficient grinding technologies in cement grinding and description of the operating principles of the related equipments and comparisons over each other in terms of grinding efficiency, specific energy consumption, production capacity and cement quality are given A case study performed on a EnergyEfficient Technologies in Cement Grinding IntechOpenparticle size with reduced specific energy consumption [12, 13] Unlike tumbling mills, which require steel balls as grinding media to act as an energy transfer medium, in HPGR the direct transfer of energy from the rolls to the particle bed leads to interparticle breakage [14, 15] The past research works by various researchers havePotential of HighPressure Grinding Roll (HPGR) for Size
.jpg)
Modeling of Bauxite Ore Wet Milling for the Improvement of
2021年9月5日 Modeling involves (i) the determination of the most suitable model, ie, Gates–Gaudin–Schuhmann (GGS), Rosin–Rammler (RR), and logistic distributions, for describing the particle size distribution of the grinding products, and (ii) the investigation of the grinding kinetics of the ore in order to improve process efficiency and reduce energy requirements and 2009年5月1日 In this study, the particle size distribution, fractal dimension, specific energy consumption, and grinding kinetics of chalcopyrite ore under high voltage pulse discharge were systematically Predicting the overall specific energy requirement 2024年8月27日 Staged crushing and highpressure grinding rolls (HPGR) circuits followed by ball mills are typically the most favourable financially when ores are competent and power cost is high, as they are more energyefficient than SAG millbased flowsheet optionsBeyond SAG milling – The future of grinding AusIMM2024年5月3日 In the mineral processing process, about 60% of the energy consumption is consumed in the crushing operation of ore, so crushing and grinding need to be considered as a whole For existing mineral processing plants, the crushing and grinding equipment is basically fixed, and efforts need to be made to balance the crushing and grinding capabilitiesMore Crushing and Less Grinding, A Wise Way to Saving Energy
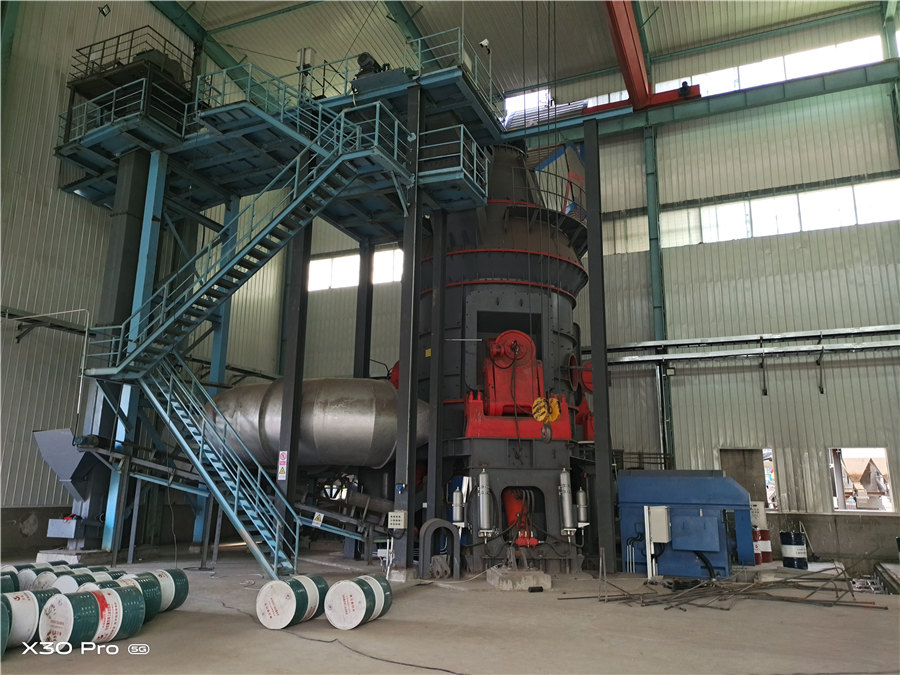
(PDF) Lowering of Grinding Energy and Enhancement of
2002年1月1日 KruppRenn process is an energysaving technology for ferronickel production from saprolitic laterite ores, in which a semifused zone (1 3001 350°C) in the rotary kiln is required for the 2024年6月29日 Grinding media influence the energy consumption and efficiency of the grinding process during the calculation of the Bond Work index (BWi), a wellknown method for selecting comminution equipment, evaluating milling efficiency, and calculating required milling power Traditional grinding tests often choose steel balls as the grinding media, but ceramic balls are A New Approach to the Calculation of Bond Work Index with 22 EnergySaving Techniques in the Grinding Process PreCrushing Technology: By reducing the mineral particle size to a suitable range for grinding through precrushing technology, energy Technological Innovation: Achieving Energy Savings and2013年1月1日 This paper investigates the production of calcite suspensions by a wet grinding process in a stirred media mill The experimental setup allows the circulation mode process in the presence of Grinding of calcite suspensions in a stirred media mill: Effect of
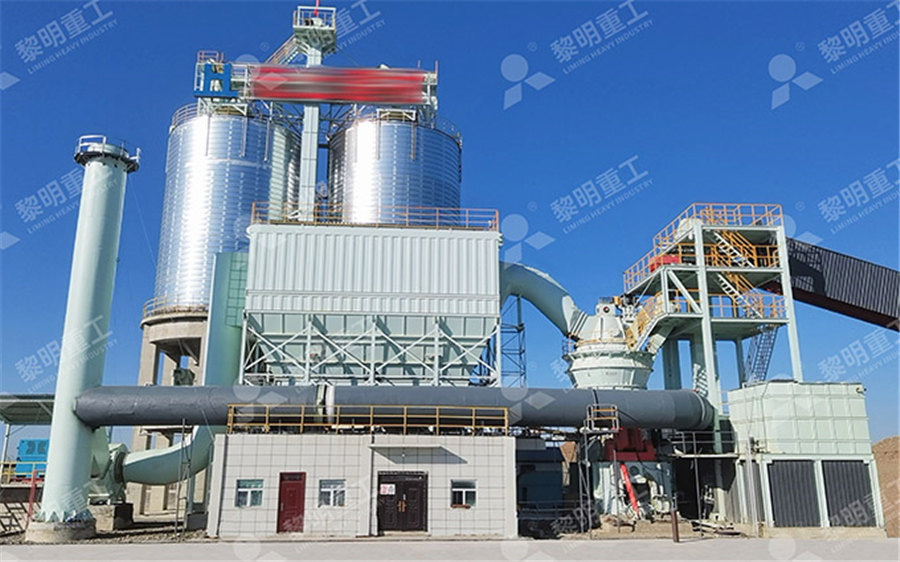
Effective role of grinding aids in the dry grinding performance of calcite
2023年8月1日 With the developing technology, the importance of fine and very fine grinding increases However, their energy consumption is also increasing, and therefore, grinding costs are also [1]Apart from high energy consumption, the most significant problem in grinding under a particle size of 10 μm is associated with particleparticle interactions, which depends on the 2023年6月30日 Considerable energy savings can be achieved by improving technological processes in all industries, including mining The improvement of technological and crushing processesModeling and Improving the Efficiency of Crushing Equipment2023年7月10日 The present literature review explores the energyefficient ultrafine grinding of particles using stirred mills The review provides an overview of the different techniques for size reduction and the impact of energy EnergyEfficient Advanced Ultrafine Grinding of 2010年1月31日 Grinding aids especially in dry microfine grinding processes remarkably increase grinding energy efficiency, bring down the limit of grinding, prevent the agglomeration of ground particles, avoid Effect of grinding aids on the grinding energy consumed during grinding
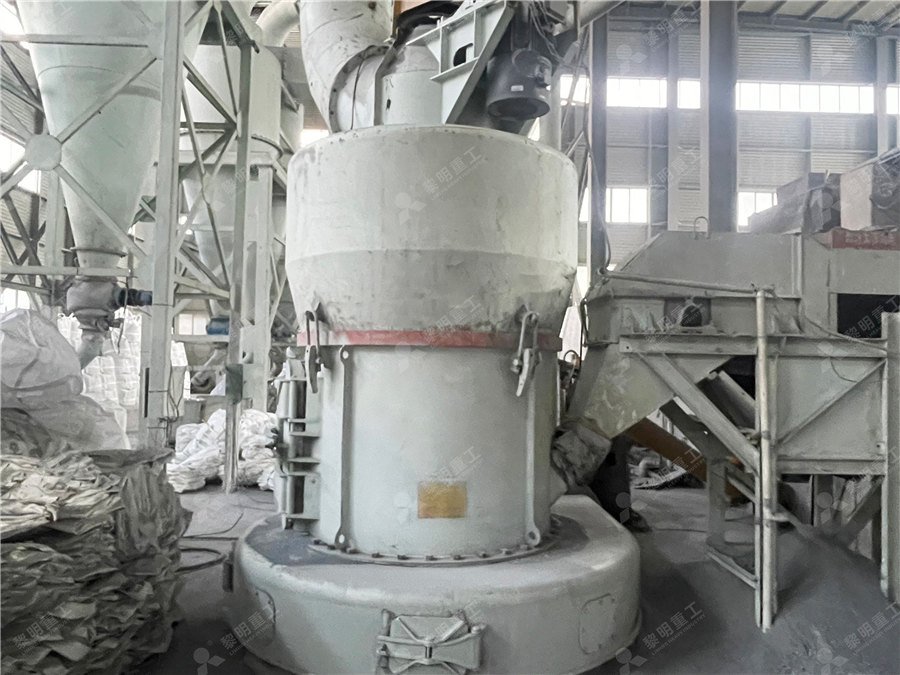
Methods of Ore Pretreatment for Comminution
2020年5月9日 The comminution of ores consumes a high portion of energy Therefore, different pretreatment methods of ores prior to their comminution are considered to reduce this energy However, the results of pretreatment Crushing and grinding operations are important for the entire mineral processing process, as well as two operations with huge investment and high energy consumption In terms of metal mines, the equipment investment of crushing and grinding operations accounts for 65% ~ 70% of the total investment in the whole plant, and the power consumption is about 50% ~ 65%3 Principles of Choosing the Crushing and Grinding Process2022年8月31日 Dear Colleagues, The grinding process, as a primary stage of ore/raw material processing, is a necessary operation in beneficiation plants It not only provides the appropriate particle size for subsequent separation operations but also enables the liberation of valuable minerals from the gangueGrinding Modeling and Energy Efficiency in Ore/Raw Material 2024年6月1日 Crushing processes taking place in highpressure grinding rolls devices (HPGR) are currently one of the most efficient methods of hard ore size reduction in terms of the energy consumptionImpact of HPGR operational pressing force and material moisture
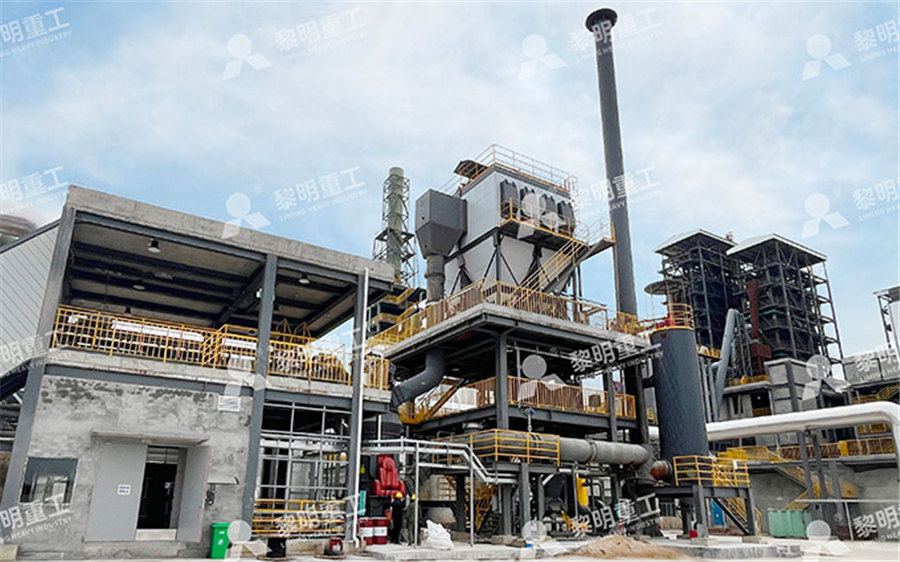
The Energy Saving Technology of Beneficiation of Iron Ore
The Energy Saving Technology of Beneficiation of Iron Ore V V KARMAZIN, M A BIKBOV AND A A BIKBOV MAGNETIC AND ELECTRICAL SEPARATION, VOL 11 (4), PP 211224 ABSTRACT The qualitative and quantitative evaluation of liberation of economic minerals and the level of contamination of the process products by waste components were carried out2014年10月15日 The energy costs required to refine metal values contained in ore to concentrates constitute the majority of the cost to produce metals On average across the mining industry, 44% of the total electricity consumption is dedicated to crushing and milling activities (Fig 1)Size reduction operations, nearly 150 × 10 9 kW h, are the largest single consumer of Development of ore sorting and its impact on mineral processing The purpose of this datafile is to tabulate typical cost estimates for crushinggrinding processes, which consume 12% of all the energy in the world and 2050% of the energy in some mining processes Our numbers are shown per ton of ore, so clearly lower ore grades translate into higher costs per unit of extracted material ()Energy economicsMining crushing grinding costs Thunder Said Energy2024年6月28日 The results demonstrate that the crushing efficiencies of ore crushing particles, raw material crushing particles, and cement crushing particles can respectively reach 807%, 7015%, and 8027% Energy Efficiency Measurement of Mechanical Crushing Based on
.jpg)
Crushing and Grinding Process JXSC Machine
2019年10月8日 The crushing and grinding operations are an important part of the processing of mineral resources, and it is also operation with high investment and high energy consumption In the case of metal mines, equipment 2015年12月26日 In mineral processing or metallurgy, the first stage of comminution is crushing Depending of the type of rock (geometallurgy) to be crushed, there are 2 largely different techniques at your disposition for Crushing in Mineral Processing 911Metallurgist2019年6月21日 According to the Coalition for EcoEfficient Comminution, comminution – the process of crushing and grinding ore – is by far the most energy consuming step in the mining processGrinding down energy consumption in High Pressure Grinding Roll and Magnetic Separation for Energy Saving in Grinding and Simultaneously Improving Processing Capacity: A Case Study of a Magnetite Ore Jianwen Yu1,2,3 Yaxiong An 1,3 Peng Gao1,2,3 Yuexin Han 1,2,3 Received: 20 February 2024 / Accepted: 21 May 2024 / Published online: 31 May 2024High Pressure Grinding Roll and Magnetic Separation for Energy Saving
.jpg)
Tuning the Morphology and Surface Property of Mineral Particles
2017年11月18日 Therefore, optimizing the process of crushing and grinding is of great significance for achieving energysaving and costreducing in minerals processing Mineral processing is a predominant technology used to fulfill the enrichment of valuable minerals from coexisted (undesired) gangue minerals and then, provides raw materials for the following 2017年1月27日 This paper presents experimental comparison of two machine crushing technologies: onestage and twostage The study was carried on a model doubletoggle jaw crusher which allows crushing forces (PDF) Analysis of Energy Consumption of Crushing Processes 2009年7月1日 Chemicals used as grinding aids, particularly in dry grinding processes, lead to a significant increase in energy saving, cement strength, surface area, energy efficiency, size reduction, avoid Effect of grinding aids on the kinetics of fine grinding energy 2022年1月1日 Processing includes primary and secondary crushing followed by HPGR grinding and ball milling, magnetic separation, reverse flotation and thickening to produce 12Mtpa of magnetite concentrate HPGR technology was implemented for fine crushing to reduce the energy consumption processing very hard ore (Fig 821)Comminution and classification technologies of iron ore
.jpg)
EnergyEfficient Technologies in Cement Grinding IntechOpen
2016年10月5日 In this chapter an introduction of widely applied energyefficient grinding technologies in cement grinding and description of the operating principles of the related equipments and comparisons over each other in terms of grinding efficiency, specific energy consumption, production capacity and cement quality are given A case study performed on a particle size with reduced specific energy consumption [12, 13] Unlike tumbling mills, which require steel balls as grinding media to act as an energy transfer medium, in HPGR the direct transfer of energy from the rolls to the particle bed leads to interparticle breakage [14, 15] The past research works by various researchers havePotential of HighPressure Grinding Roll (HPGR) for Size