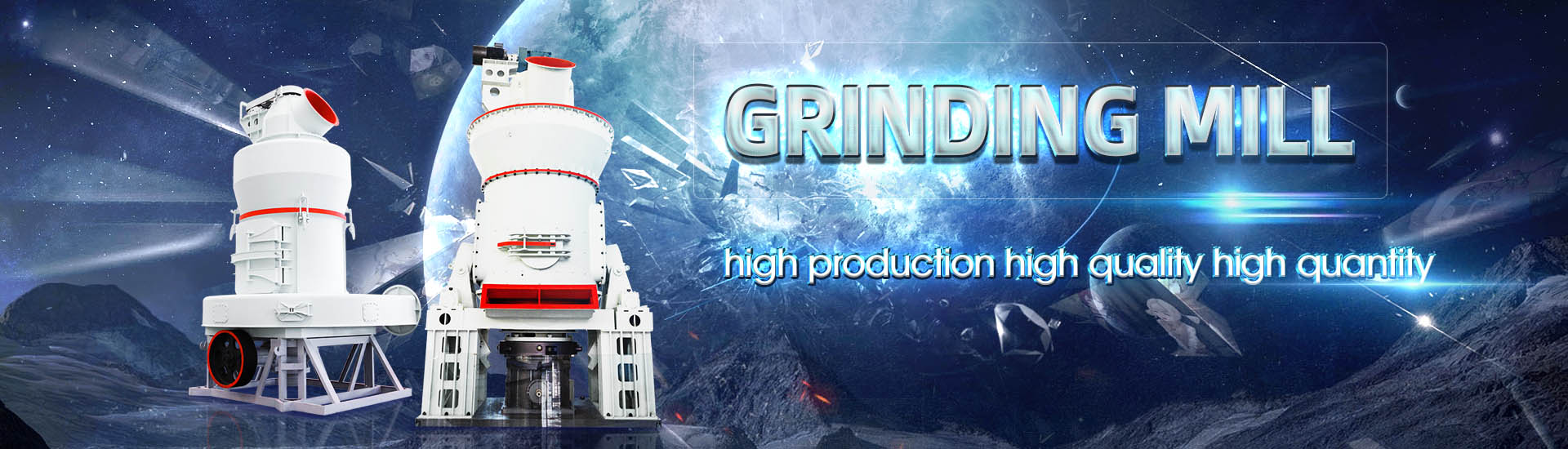
Granite clinker equipment process flow
.jpg)
The processing of granite: Step by step CKP
2016年9月22日 Granite Processing: Sawing Traditionally, granite blocks were cut by the machines to obtain slabs of the thickness, sizes and finishes required for their final use in the 2021年2月24日 The clinker production process involves much equipment and material flow; thus, an operating system is needed to regulate and manage the production processOptimizing the clinker production by using an The clinkerization reactions, as we all know, take place at the pyroprocessing stage in a plant, which extends from the extraction of the kiln feed (or the raw meal) from the post Clinkerization an overview ScienceDirect TopicsCooling gas recirculation contributed to a phenomenon of moisture enrichment The clinker microstructure of the clinker samples indicate fast cooling the extraction of finer clinker Process characteristics of clinker and cement production SINTEF
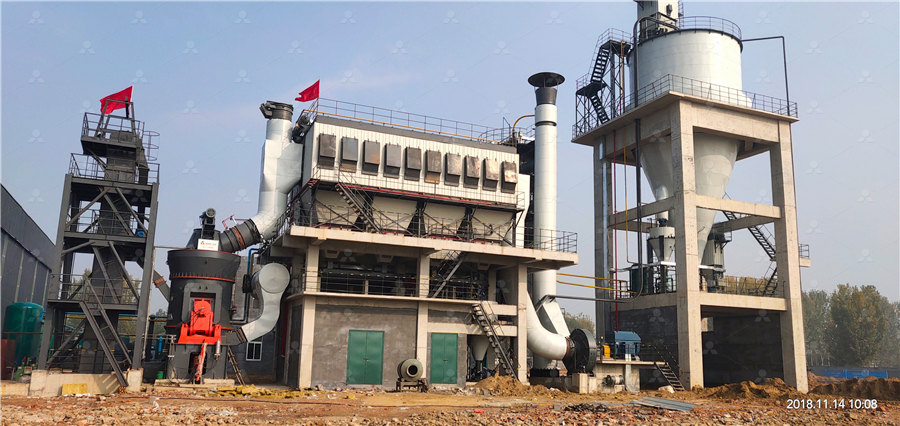
Clinker Production an overview ScienceDirect Topics
Clinker consists of calcium oxide and other mineral oxides (iron, aluminum, and silicon) and has cementious activity when reacted with water Clinker is produced by pyroprocessing in large Araújo et al described a methodology that uses functional machine learning techniques to automatically classify granite at various processing stages based on spectral information captured byFlowchart depicting the granite production process This project is to study of the factor which affects the production rate and taking the corrective action in order to produce estimated production The optimization is done by general Study and Optimization of Granite Processing Plant IJSRDProcess flow diagram for granite processing operations Processing commences with transportation of the (raw) stone from the quarry to the processing facility, as depicted by Granite Dimensional Stone Quarrying and Processing: A LifeCycle
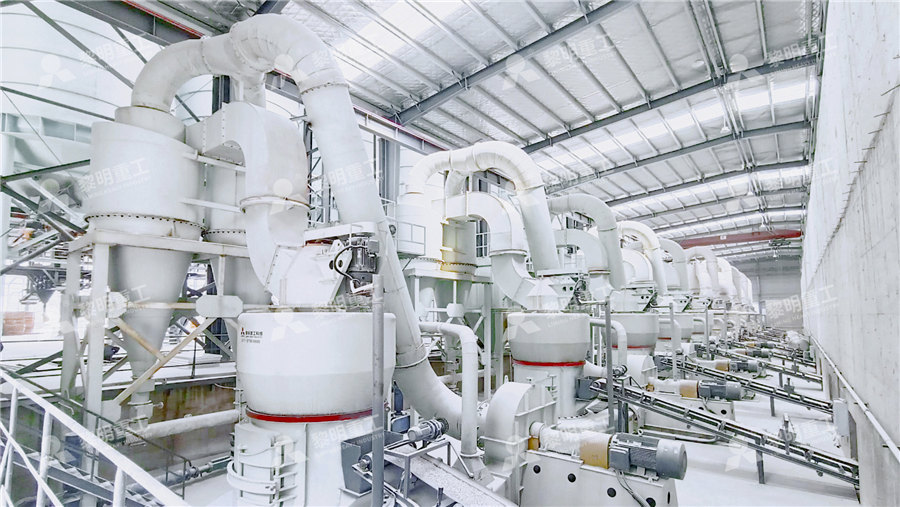
Chemistry and engineering of the clinkerization process —
2011年7月1日 “Chemistry” and “process engineering” constitute the foundation of the clinkerization process but over the decades the engineering advances have been phenomenal 2012年11月8日 Finish grinding of clinker and other cement ingredients reduces 25 mm clinker balls to particle sizes optimally ranging from 3 to 30 microns The European Cement Research Breakthrough in Clinker Grinding Massachusetts Institute of Download scientific diagram Clinker production flow chart [12] from publication: Thermal analysis of the rotary kiln through FEA This paper aims at analyzing numerical heat transfer in kiln Clinker production flow chart [12] ResearchGate2021年2月24日 The clinker production process involves much equipment and material flow; thus, an operating system is needed to regulate and manage the production processOptimizing the clinker production by using an
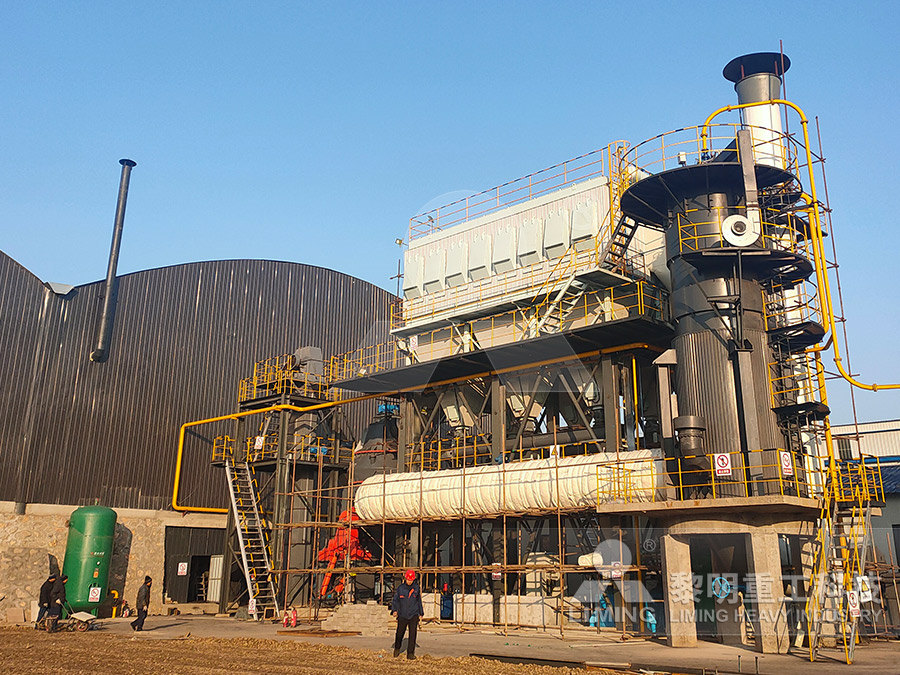
The Cement Manufacturing Process Process Systems Design
2017年8月15日 After cooling, the clinker can be stored in the clinker dome, silos, bins, or outside in storage piles The material handling equipment used to transport clinker from the clinker coolers to storage and then to the finish mill is similar to that used to transport raw materials (eg belt conveyors, deep bucket conveyors, and bucket elevators)In a rotary kiln system producing cement clinker, gas flows are countercurrent to material flows Gases enter the kiln as secondary air at about 600°C – 1100°C and rise abruptly to over 1750°C as heat from fuel combustion, and the exothermic heat of clinker formation are releasedCement Manufacturing Process INFINITY FOR CEMENT EQUIPMENTMaterial flow in each main equipment of a cement clinker plant, kiln Kiln feed gas from kiln Kiln feed to the kiln Combustion gas including excess air Kiln feed gas out Return dust flow Heat of calcination process Evaporating of kiln feed water content Convection radiation loss 16155 01700 17042 04114 20442 50630 541660 134900 New Method Evaluation of Detail Material and Heat Flows for And the tools which are used for the process are get wornout early and this will leads damages in the granite slabs By general inspection come to know that the production is lagging in the polishing section of granite slab, So optimization is necessary in polishing section of the granite factory IV OBJECTIVEStudy and Optimization of Granite Processing Plant IJSRD

Analysis of material flow and consumption in cement production process
2015年8月1日 the total material used in the clinker process is 469 kg/kg clinker, and the primary material sources are the cooling air d producing total material of 233 kg/kg clinker (4960%) d and raw mealProcess flow diagram for granite quarrying operations As shown in Figure 1, the first step in quarrying is to gain access to the granite deposit Once the bench is cut or split loose from the deposit, heavy equipment is used to lift the granite bench and transfer it to an inspection area for grading, temporary storage,A LifeCycle Inventory of Granite Dimension Stone Quarrying and Nevertheless, the process is relatively simple: locate or create (minimal) breaks in the stone, remove the stone using heavy machinery, secure the stone on a vehicle for transport, and move the material to storage A flow diagram of typical quarrying operations is shown in Figure 1 Figure 1 Process flow diagram for granite quarrying operationsGranite Dimensional StoneColazione, pranzo, self service, apericena, aperitivi di vino e cena alla carta: da Moody Genova non ti annoi mai Vieni a trovarci!Moody la tua pausa a Genova
.jpg)
EVERYTHING YOU NEED TO KNOW ABOUT
EVERYTHING YOU NEED TO KNOW ABOUT OPERATION AND CONTROL OF CLINKER COOLER It is extremely important for the operator to master cooler controls as well as other control functions of the rotary kiln system, because A simple mathematical model is presented for clinker production via a pyroprocessing unit consisting of serial flow preheater cyclone stages, a precalciner, a rotary kiln and a clinker cooler The model equations are based on steady state material and energy balances for solid and gas phases around each piece of equipmentMATHEMATICAL MODELLING OF CLINKER PRODUCTION WITH SERIAL FLOW article no 29 the civil engineering journal 32019 doi 1014311/cej2019030029 361MATHEMATICAL MODELLING OF CLINKER PRODUCTION WITH SERIAL FLOW Download scientific diagram Flowchart depicting the granite production process and indicating phases where manual colour coding can be complemented by automated characterization from Flowchart depicting the granite production process and indicating
.jpg)
Flow chart of cement clinker burning system ResearchGate
Download scientific diagram Flow chart of cement clinker burning system from publication: Technical Route to Achieve UltraLow Emission of Nitrogen Oxides with Predictive Model of Nitrogen Download scientific diagram Calcination process of cement clinker from publication: A Synchronous Prediction Model Based on MultiChannel CNN with Moving Window for Coal and Electricity Calcination process of cement clinker ResearchGateflows and mapped them in order to determine their general characteristics In order to compare with clinker formed by ‘a‘ā fragmentation, we also sampled basal clinker in two typical, well constrained ‘a‘ā flows We sampled clinker from each flow and then studied fragment structures and morphologyinhandspecimen,withthebinocularmicroscopeClinker formation in basaltic and trachybasaltic lava flows SpringerDownload scientific diagram Crosssectional view of clinker cooling process inside a grate cooler from publication: Modelling of clinker cooler and evaluation of its performance in clinker Crosssectional view of clinker cooling process inside a grate
.jpg)
Cement Manufacturing and Process Control SpringerLink
2019年8月27日 The major raw materials used as a source of CaO for cement manufacturing are limestone, chalk, marl, etc These raw materials by virtue of their natural occurrence contains other mineral impurities eg, MgO, SiO 2, Al 2 O 3, Fe 2 O 3, alkali compounds, and sulfidesThese impurities play an important role to influence the cement manufacturing The clinker production process involves much equipment and material flow; thus, an operating system is needed to regulate and manage the production process XYZ company uses an operating system for clinker production called Cement Management QualityOptimizing the clinker production by using an automation model SMPCRUSHER Industry Co, Ltd Founded in 1987,SMPCRUSHER provide a range of modular crushing and screening solutions SMP is a crushing and screening plant constructed of predesigned modulesModular Crushing plant,Modular Crushing,Modular 2021年3月9日 In this study the process flow diagram for the cement production was simulated using Aspen HYSYS 88 software to achieve high energy optimization and optimum cement flow rate by varying the flow rate of calcium Simulation and Optimization of an Integrated Process
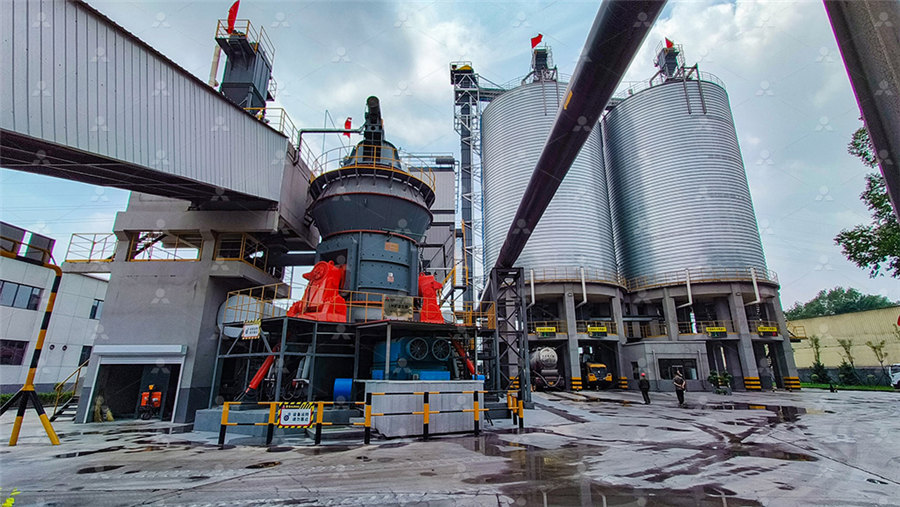
Cement and Clinker Production by Indirect
2022年9月21日 The study explores the indirect mechanosynthesis process for cement and clinker production, highlighting its impact on global cement outputThe process flow diagram of a typical cement during the cement grinding and distribution process, firstly the cooled clinker is ground with around 5% of gypsum and other 17 JRTE2020 Typical cement manufacturing process flow diagram [4]A review of the effectiveness of Life Cycle Assessment for gauging environmental impacts from cement production Oluwafemi E Ige, Collins Obiora, in Journal of Cleaner Production, 2021 223 Production of clinker The clinker production stage is where the raw material (the raw meal) converts into clinker The raw meal is fed into a rotary kiln through a preheater at about 1450 Clinker Production an overview ScienceDirect TopicsProcess flow diagram for portland cement manufacturing 1164 EMISSION FACTORS 11/21 Reaction, of the oxides in the burning zone of the rotary kiln, to form cement clinker at temperatures of approximately 1510°C (2750°F) Rotary kilns are long, cylindrical, equipment design, method of operation, and fuel consumption Generally, 116 Portland Cement Manufacturing US Environmental
.jpg)
Cement manufacturing process PPT Free Download SlideShare
2014年6月10日 Evolution of the cement Process • Wet process easiest to control chemistry better for moist raw materials • Wet process high fuel requirements fuel needed to evaporate 30+% slurry water • Dry process kilns less fuel requirements • Preheater/Precalciner further enhance fuel efficiency allow for high production ratesProcess flow diagrams, or PFDs, are technical flowcharts It assists managers and designers in their process arrangements, ensuring straightforward outputs A typical process flow diagram would incorporate significant datasets They contain information about mechanical equipment, operating data, and interconnections to other systemsProcess Flow Diagram (PFD): A Complete Guide Zen Flowchart2019年10月1日 A simple mathematical model is presented for clinker production via a pyroprocessing unit consisting of serial flow preheater cyclone stages, a precalciner, a rotary kiln and a clinker cooler(PDF) MATHEMATICAL MODELLING OF CLINKER PRODUCTION WITH SERIAL FLOW 2010年4月10日 Clinker is a term used to describe massive or scoriaceous fragments commonly associated with ‘a‘ā lava flows Clinker is generally considered to form by fragmentation of an upper vesiculated crust, due to an increase in apparent viscosity and/or to an increase in shear strain rate Surface clinker is considered to be transported to the flow front and incorporated at Clinker formation in basaltic and trachybasaltic lava flows
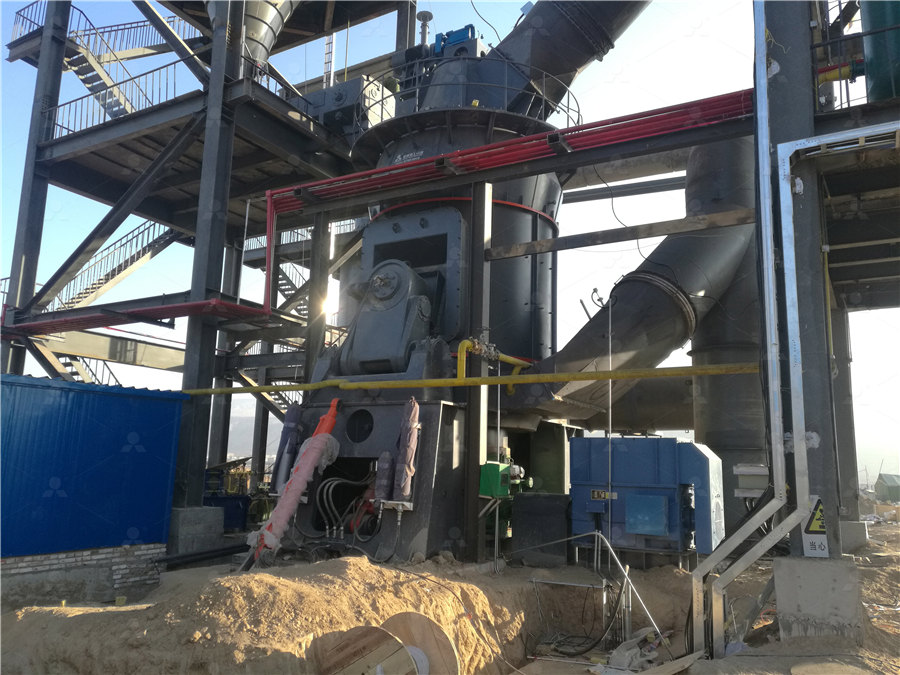
Clinker production flow chart [12] ResearchGate
Download scientific diagram Clinker production flow chart [12] from publication: Thermal analysis of the rotary kiln through FEA This paper aims at analyzing numerical heat transfer in kiln 2021年2月24日 The clinker production process involves much equipment and material flow; thus, an operating system is needed to regulate and manage the production processOptimizing the clinker production by using an 2017年8月15日 After cooling, the clinker can be stored in the clinker dome, silos, bins, or outside in storage piles The material handling equipment used to transport clinker from the clinker coolers to storage and then to the finish mill is similar to that used to transport raw materials (eg belt conveyors, deep bucket conveyors, and bucket elevators)The Cement Manufacturing Process Process Systems DesignIn a rotary kiln system producing cement clinker, gas flows are countercurrent to material flows Gases enter the kiln as secondary air at about 600°C – 1100°C and rise abruptly to over 1750°C as heat from fuel combustion, and the exothermic heat of clinker formation are releasedCement Manufacturing Process INFINITY FOR CEMENT EQUIPMENT
.jpg)
New Method Evaluation of Detail Material and Heat Flows for
Material flow in each main equipment of a cement clinker plant, kiln Kiln feed gas from kiln Kiln feed to the kiln Combustion gas including excess air Kiln feed gas out Return dust flow Heat of calcination process Evaporating of kiln feed water content Convection radiation loss 16155 01700 17042 04114 20442 50630 541660 134900 And the tools which are used for the process are get wornout early and this will leads damages in the granite slabs By general inspection come to know that the production is lagging in the polishing section of granite slab, So optimization is necessary in polishing section of the granite factory IV OBJECTIVEStudy and Optimization of Granite Processing Plant IJSRD2015年8月1日 the total material used in the clinker process is 469 kg/kg clinker, and the primary material sources are the cooling air d producing total material of 233 kg/kg clinker (4960%) d and raw mealAnalysis of material flow and consumption in cement production processProcess flow diagram for granite quarrying operations As shown in Figure 1, the first step in quarrying is to gain access to the granite deposit Once the bench is cut or split loose from the deposit, heavy equipment is used to lift the granite bench and transfer it to an inspection area for grading, temporary storage,A LifeCycle Inventory of Granite Dimension Stone Quarrying and
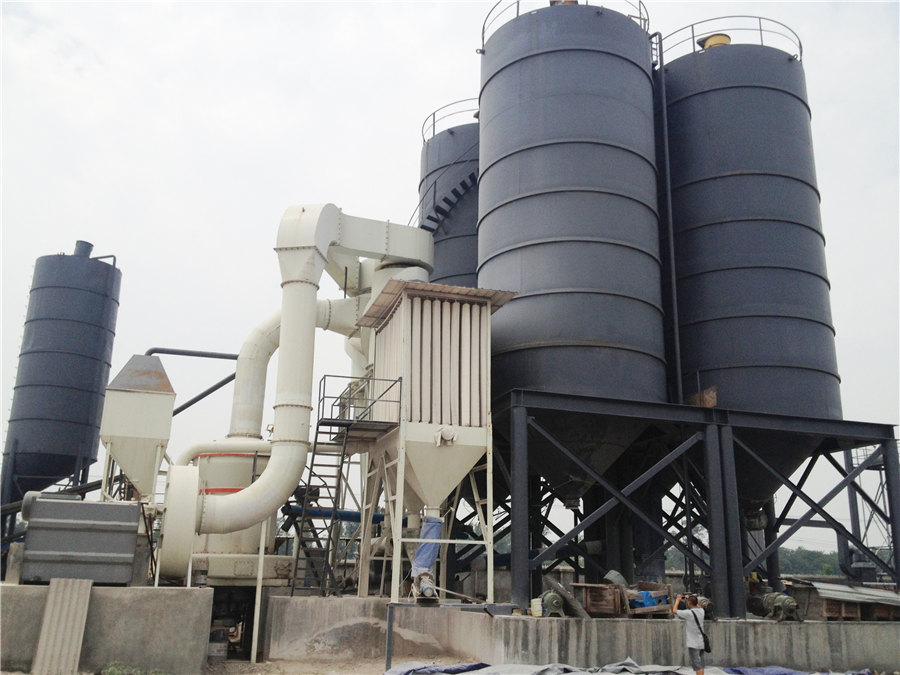
Granite Dimensional Stone
Nevertheless, the process is relatively simple: locate or create (minimal) breaks in the stone, remove the stone using heavy machinery, secure the stone on a vehicle for transport, and move the material to storage A flow diagram of typical quarrying operations is shown in Figure 1 Figure 1 Process flow diagram for granite quarrying operationsColazione, pranzo, self service, apericena, aperitivi di vino e cena alla carta: da Moody Genova non ti annoi mai Vieni a trovarci!Moody la tua pausa a Genova