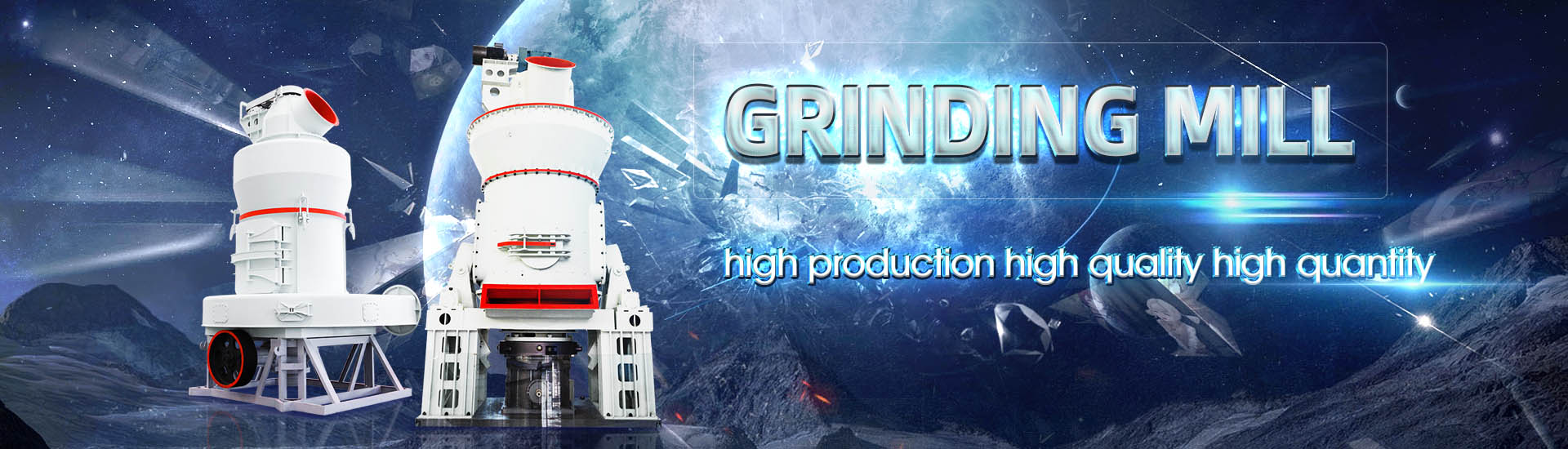
Cement secondary industrial grinding mill
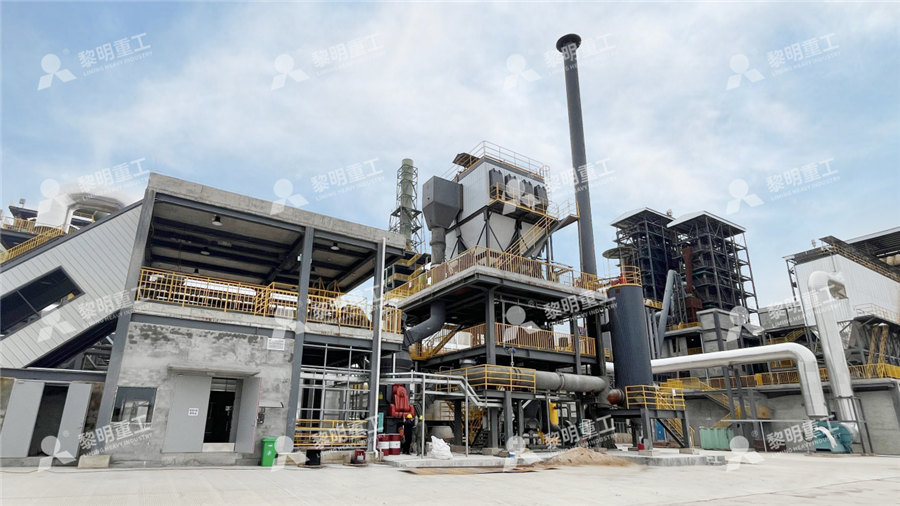
BALL MILLS Ball mill optimisation Holzinger Consulting
Ball mills and grinding tools Cement ball mills are typically twochamber mills (Figure 2), where the first chamber has larger media with lifting liners installed, providing the coarse grinding Basing on our decadelong experience and best consulting competence, we can plan the ideal grinding plant for every customer in the cement industry, ensuring economical grinding of PFEIFFER MILLS FOR THE CEMENT INDUSTRYOptimization of the Cement Ball Mill Operation Optimization addresses the grinding process, maintenance and product quality The objective is to achieve a more efficient operation and OPTIMIZATION OF CEMENT GRINDING OPERATION IN BALL MILLSCompact and easy to install, the FCB Horomill® offers process specificities that are ideal for modern cement plants Thanks to its advanced technology and its use in combination with the FCB TSV™ high efficiency classifier, the mill Fives Sustainable grinding with FCB Horomill®
.jpg)
quadropol® thyssenkrupp Polysius Grinding
The quadropol® concept for coal or pet coke grinding, with adapted table speed and high efficiency separator sepol®, ensures a safety mill operation and serves reliable the kiln burning process Mombasa Cement Ltd ordered a QMK² The roller grinding mill technology, patented in 1928 and continuously developed since then, has become synonymous with Loesche‘s pioneering engineering knowhow CEMENT BLAST FURNACE SLAG CEMENT RAW MATERIALCement Industry Loeschegrinding brittle materials, such as cement, is still the ballfilled ball mill The following types can be found: • singlecompartment mills, • twocompartment mills, • airswept mills as well as special Industrial Solutions polysius ball mills ThyssenKrupp2022年2月18日 World Cement invited industry leaders to share their thoughts on a range of grinding and millingrelated topics Contributions come from: FIVES FCB, Gebr Pfeiffer, and thyssenkrupp Industrial Solutions 1) In our World Cement Grinding Milling QA
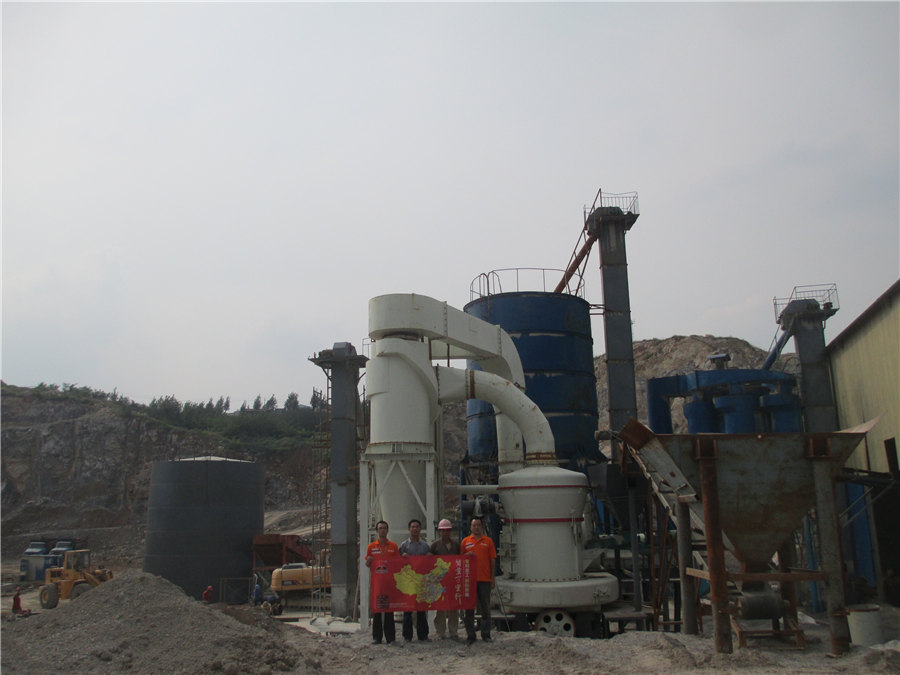
EnergyEfficient Technologies in Cement Grinding
2016年10月5日 In this chapter an introduction of widely applied energyefficient grinding technologies in cement grinding and description of the operating principles of the related equipments and comparisons over each other in 2016年10月12日 The simplest grinding circuit consists of a ball or rod mill in closed circuit with a classifier; the flow sheet is shown in Fig 25 and the actual layout in Fig 9Closed Circuit Grinding VS Open Circuit Grinding2014年2月1日 Samples of the input, output and return material of cement clinker grinding by a CKP mill are collected, based on the field sampling in the industrial mill The crushing kinetic process of the cement clinker in a CKP mill is analyzed, by using the particle size distribution and mass balances The following results have been obtained 1Effects of circulating load and grinding feed on the grinding o Finished grinding may consume 25 – 50 kWh/t cement, depending on the feed material grindability, additives used, plant design especially the required cement fineness Cement grinding is the single biggest consumer of electricity in the manufacturing process Whichever the mill types, grinding is inherently inefficientImprovements in New Existing Cement Grinding Mills by Tim

Cement mill Wikipedia
A 10 MW cement mill, output 270 tonnes per hour A cement mill (or finish mill in North American usage [1]) is the equipment used to grind the hard, nodular clinker from the cement kiln into the fine grey powder that is cementMost cement is currently ground in ball mills and also vertical roller mills which are more effective than ball millsUltra Fine Grinding Mill The ultrafine grinding system manufactured by AGICO is mainly used for grinding pulverized coal and cementTo meet the need for further grinding and 3D printing, in 2015, our company built an ultrafine powder grinding production line of 12t/d — 20t/dGrinding Mill Grinding Equipment Cement Mill AGICO6 Cement Production Technology –Cement Grinding –Mechanical Design and Function of Separator Separators –General Classification of Separating Principles •according to flow direction relative to particle track •according to kind of separating field separation by gravitational force separation by centrifugal forceCement Grinding myPolysiusServiceIndustrial experience has proven that due to the design of grinding parts and the high efficiency separator the OK mill, Figure 3, adequately addresses all the difficult grinding conditions associated with fine grinding of cement clinker and related products, enabling a high grinding efficiency and stable operationCement grinding Vertical roller mills VS ball mills
.jpg)
(PDF) An industrial comparative study of cement clinker grinding
The combinedgrinding cement had the shortest initial and final setting times, followed by the HPRMonly and horizontalrollermill cements, in the increasing order The horizontalrollermill cement demonstrated the longest total active setting time (111 minutes), defined as the final setting time minus the initial setting timeWhat Is A Cement Ball Mill The cement ball mill is a kind of cement grinding millIt is mainly used for grinding the clinker and raw materials of the cement plant, and also for grinding various ores in metallurgical, chemical, and electric power enterprisesIt has the characteristics of strong adaptability to materials, continuous production, a large crushing ratio, and easytoadjust the Cement Ball Mill Cement Grinding Machine Cement MillProduction Capacity: 400,000 ~ 700,000 TPY Grinding Mills: vertical roller mill / ball mill Grinding Systems: closed circuit ball mill grinding / vrm final grindingModular Grinding Plant AGICO Cement MachineryCrushing Grinding Ball Mill Drives David Brown Santasalo ball mill drives are optimised for primary and secondary grinding applications Extensively field tested and proven in harsh cement applications, our mill drive gearboxes Ball Mill Drives Crushing Grinding Drives David
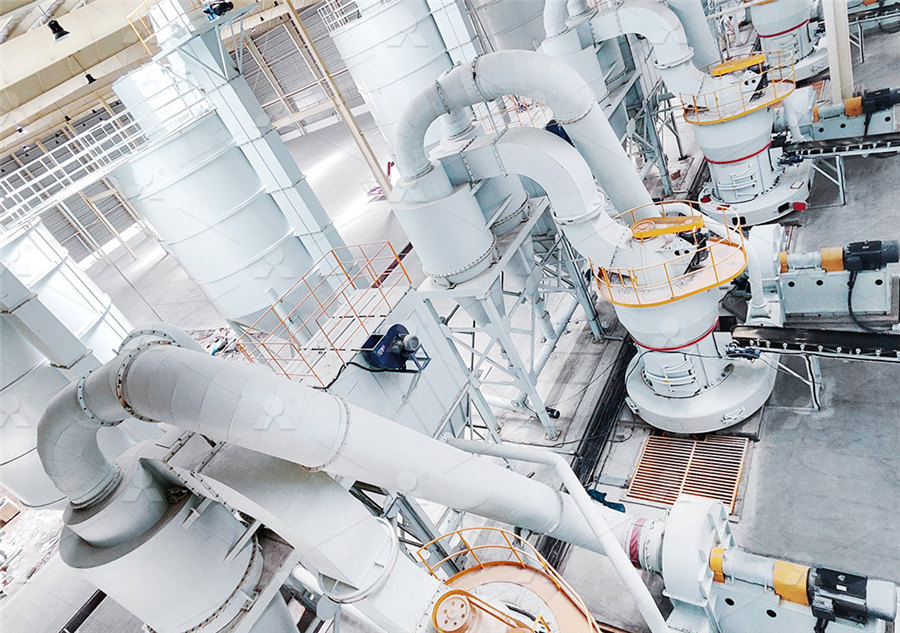
Overview of cement grinding: fundamentals,
2017年5月19日 Grinding is an essential operation in cement production given that it permits to obtain fine powder which reacts quickly with water, sets in few hours and hardens over a period of weeks i 2014年2月1日 Samples of the input, output and return material of cement clinker are collected and analyzed from an industrial CKP mill The model of firstorder crushing rate function is established and all the parameters are suitable for physical characterization by using the data of the material size distribution and mass balances The values of three parameters b, μ and γ Effects of circulating load and grinding feed on the grinding AGICO Cement Vertical Mill AGICO Cement Ball Mill Cement Vertical Mill Grinding System Cement vertical mill, also called roller mill, is another raw mill commonly used in cement pared with the cement ball mill, it has a great difference in structure, grinding principle, process layout, automatic control, and energy consumption, which play an important role in the Raw Mill – Raw Mill In Cement Plant AGICO Cement Raw MillCemento de Bolivia Cementos de Bolivia ordered a 3,000 tons per day kiln line, successfully commissioned in 2019 This was an EPC contract to the GermanSpanish polysiusImasaValoriza consortium The contract included a QMR² 38/19 for raw grinding and a QMC² 45/23 for cement grindingquadropol® thyssenkrupp Polysius Grinding Technologies
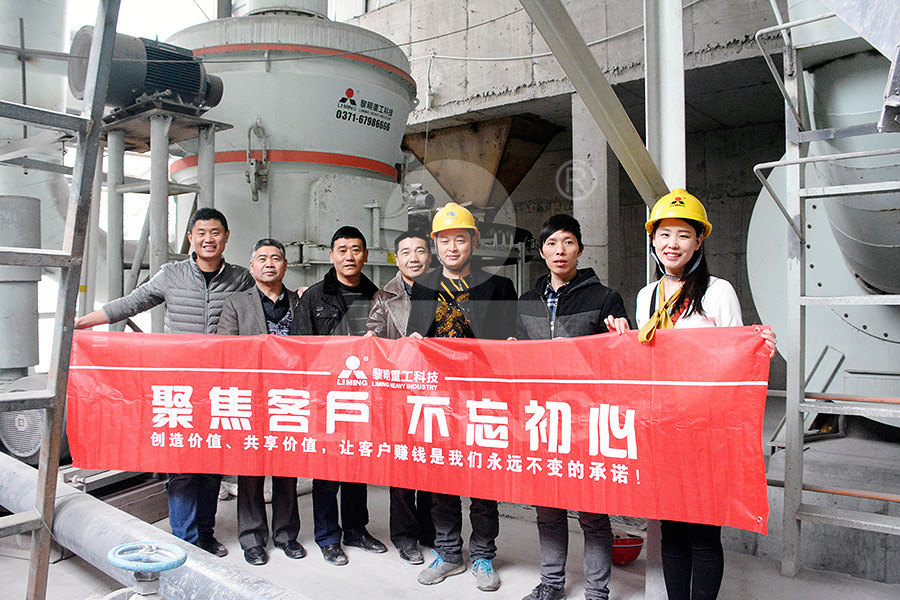
Effects of circulating load and grinding feed on the grinding
2014年2月1日 To investigate the effects of grinding media shapes on the grinding kinetics of ball mill cement clinker, the grinding effects with ϕ20 mm balls and ϕ20 × 20 mm cylinders on six different size The Metso Outotec® Open Ended Discharge Grinding Mill (OED Mill) EverRoast industrial grinder is produced to meet mass coffee grinding need of companies and it is perfect grinding solution for large volume of production vertical cement mills with productivity of 50250t/hLarge mill, Large grinding mill All industrial manufacturersReducing the clinker factor without compromising quality and the rising demand for highperformance cements are great challenges for the fine grinding technology used in cement plants As part of its green cement plant project, thyssenkrupp has expanded its product range with the polysius® booster mill While one cement manufacturer has already integrated the mill into his Let’s talk: polysius® booster mill – the next level in cement The opencircuit grinding system of the ball mill is shown as follows: materials (including clinker, gypsum, mixed materials, etc) mixed according to a certain proportion will be directly stored in the steel silo as finished cement products after being ground by the ball millBall Mill In Cement Plant Cement Ball Mill AGICO Cement
}@~3SRDG`IA1KP_ICWAA.jpg)
What is The Secondary Application of Industrial
2023年8月29日 1About Fly Ash 11 Main source 12 The Physical Attributes and Distinguishing Features 2Secondary Application of Fly Ash 21 Use in Cement and Concrete 22 Use in Building Materials 23 Use in Fertilizers and 2024年1月8日 Cement News tagged under: lowcarbon grinding mill FIDEtechnology prepares for industrial scaleup Pioneering startup FIDEtechnology, dedicated to decarbonising the construction industry, proudlCement News tagged : lowcarbon grinding mill Page 1 of 1 Understanding Our Proprietary Vertical Cement Mill Technology Magotteaux’s proprietary vertical cement mill technology has been developed through decades of innovation and expertise in grinding processesOur vertical cement mill Vertical Cement Mill MagotteauxUnit82 Cement Mill Free download as Powerpoint Presentation (ppt / pptx), PDF File (pdf), Text File (txt) or view presentation slides online This document provides information on industrial drives used in cement manufacturing plants It discusses the different types of drives used including raw mill and cement mill drives, kiln drives, crusher drives, and waste gas fan drivesUnit82 Cement Mill PDF Mill (Grinding) Scribd
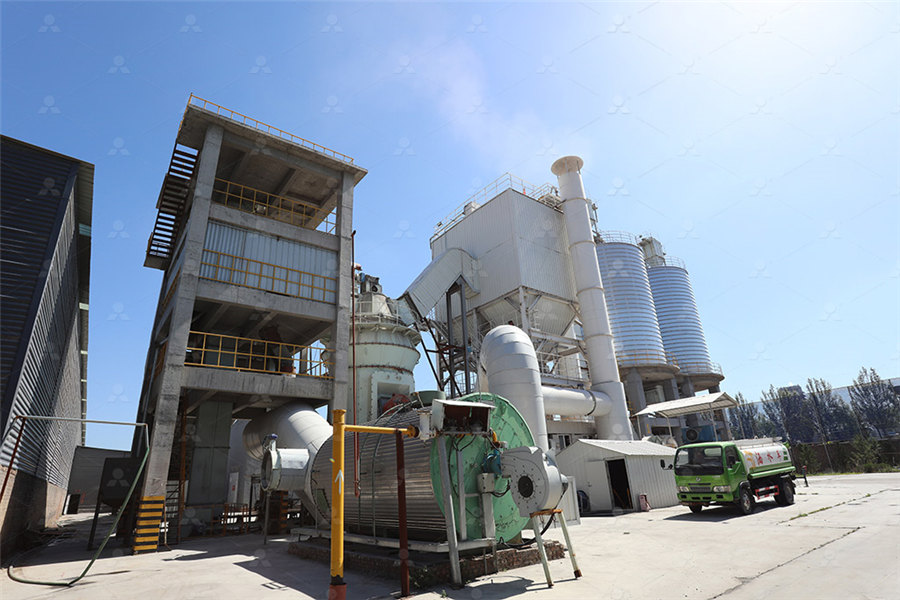
(PDF) A study of different grinding aids for lowenergy cement
2023年10月23日 In this study we compare the effects of three different grinding aids on clinker grinding using a ball mill A commercial grinding additive, triethanolamine (TEA), and two industrial grinding aids The FLS Tower Mill (FTM) reduces energy and media consumption, while minimising water usage in secondary and tertiary wet grinding of minerals The major design feature of the tower mill is a central agitator screw, the only moving machine compo nent in contact with the slurry and steel media, which allows size reduction by attritionFlexible, efficient grinding systems – FLS2016年10月5日 In this chapter an introduction of widely applied energyefficient grinding technologies in cement grinding and description of the operating principles of the related equip‐ ments and comparisons over each other in terms of grinding efficiency, specific energy consumption, production capacity and cement quality are given A case study per‐ formed on a EnergyEfficient Technologies in Cement Grinding2022年2月18日 What steps can be taken to reduce the environmental impact of cement grinding operations mill designers must ensure that energysaving comminution is possible and is further improved thyssenkrupp Industrial Solutions Cement producers can apply the following measures in order to reduce the environmental impact of their World Cement Grinding Milling QA
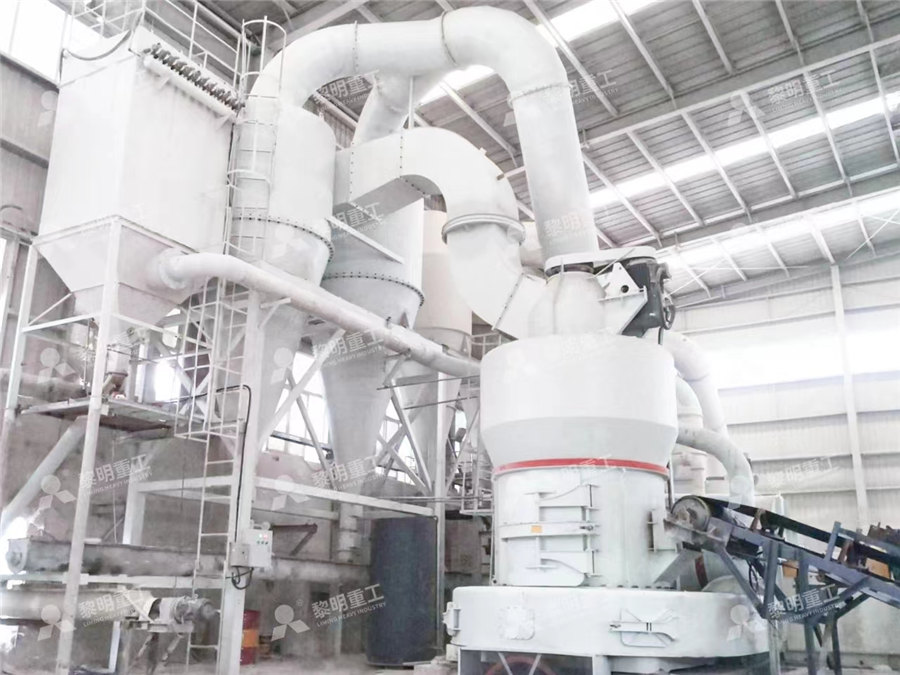
Cement Grinding Plant Expert Cement Grinding Solutions from
As a leading cement plant builder, AGICO offers an expert cement grinding plant EPC service Cement Grinding Unit EPC Solution With a strong RD team, experienced engineers, and firstclass technical services, we aim to provide users with the most advanced and optimized cement production solutionsThe industrial pin mill (also known as a universal mill, turbo mill, and impact mill) is a one pass grinding equipment ideal for achieving the micronization of bulk materials and powdered products Common applications involve the fine grinding of sugar, salt, sodium bicarb, etc The average achievable particle size range of the pin mill is around a d50 of 80 micronsGrinding mill Palamatic Process2016年10月5日 In this chapter an introduction of widely applied energyefficient grinding technologies in cement grinding and description of the operating principles of the related equipments and comparisons over each other in EnergyEfficient Technologies in Cement Grinding2016年10月12日 The simplest grinding circuit consists of a ball or rod mill in closed circuit with a classifier; the flow sheet is shown in Fig 25 and the actual layout in Fig 9Closed Circuit Grinding VS Open Circuit Grinding
.jpg)
Effects of circulating load and grinding feed on the grinding
2014年2月1日 Samples of the input, output and return material of cement clinker grinding by a CKP mill are collected, based on the field sampling in the industrial mill The crushing kinetic process of the cement clinker in a CKP mill is analyzed, by using the particle size distribution and mass balances The following results have been obtained 1o Finished grinding may consume 25 – 50 kWh/t cement, depending on the feed material grindability, additives used, plant design especially the required cement fineness Cement grinding is the single biggest consumer of electricity in the manufacturing process Whichever the mill types, grinding is inherently inefficientImprovements in New Existing Cement Grinding Mills by Tim A 10 MW cement mill, output 270 tonnes per hour A cement mill (or finish mill in North American usage [1]) is the equipment used to grind the hard, nodular clinker from the cement kiln into the fine grey powder that is cementMost cement is currently ground in ball mills and also vertical roller mills which are more effective than ball millsCement mill WikipediaUltra Fine Grinding Mill The ultrafine grinding system manufactured by AGICO is mainly used for grinding pulverized coal and cementTo meet the need for further grinding and 3D printing, in 2015, our company built an ultrafine powder grinding production line of 12t/d — 20t/dGrinding Mill Grinding Equipment Cement Mill AGICO
.jpg)
Cement Grinding myPolysiusService
6 Cement Production Technology –Cement Grinding –Mechanical Design and Function of Separator Separators –General Classification of Separating Principles •according to flow direction relative to particle track •according to kind of separating field separation by gravitational force separation by centrifugal forceIndustrial experience has proven that due to the design of grinding parts and the high efficiency separator the OK mill, Figure 3, adequately addresses all the difficult grinding conditions associated with fine grinding of cement clinker and related products, enabling a high grinding efficiency and stable operationCement grinding Vertical roller mills VS ball millsThe combinedgrinding cement had the shortest initial and final setting times, followed by the HPRMonly and horizontalrollermill cements, in the increasing order The horizontalrollermill cement demonstrated the longest total active setting time (111 minutes), defined as the final setting time minus the initial setting time(PDF) An industrial comparative study of cement clinker grinding What Is A Cement Ball Mill The cement ball mill is a kind of cement grinding millIt is mainly used for grinding the clinker and raw materials of the cement plant, and also for grinding various ores in metallurgical, chemical, and electric power enterprisesIt has the characteristics of strong adaptability to materials, continuous production, a large crushing ratio, and easytoadjust the Cement Ball Mill Cement Grinding Machine Cement Mill