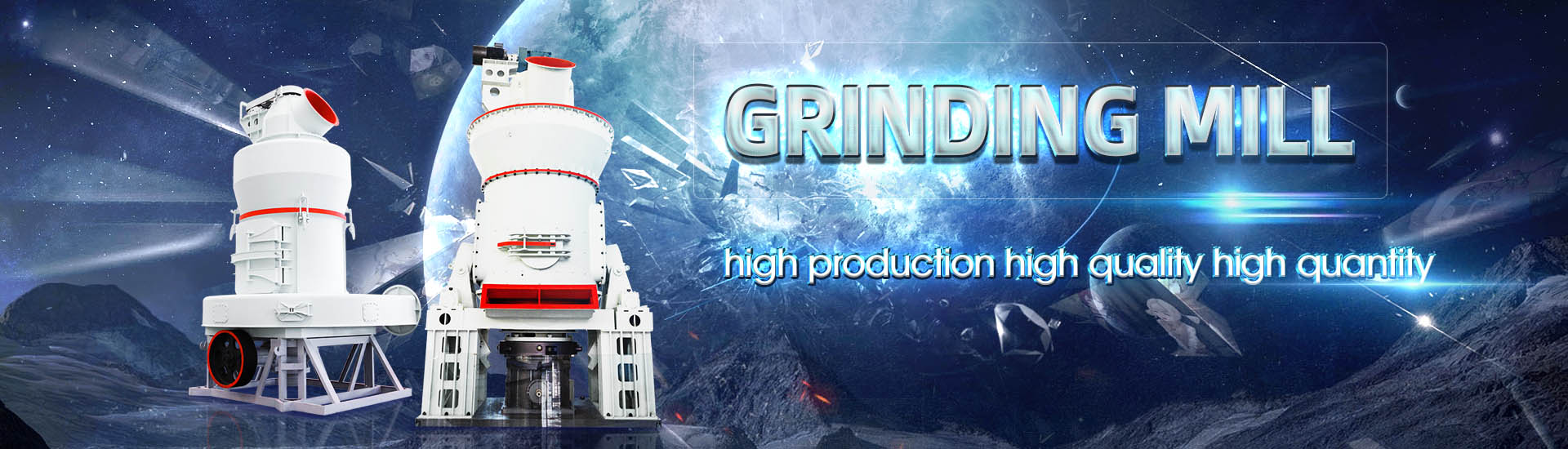
The reason for the sudden saturation of cement mill
.jpg)
BALL MILLS Ball mill optimisation Holzinger Consulting
As grinding accounts for a sizeable share in a cement plant’s power consumption, optimisation of grinding equipment such as ball mills can provide significant cost and CO 2Abstract: This research aims to investigate the effect of free lime and lime saturation factor on grindability of cement clinker Cement is a powdered substance that develops strong adhesive Effect of Free Lime and Lime Saturation Factor on Grindability of 2011年7月1日 High belite cements are an alternative to reduce CO 2 emissions in the cement production process They need less calcium than Portland cement (05 t of CO 2 per tonne Chemistry and engineering of the production process: State of the The mill performance is evaluated and recommendations are formulated based on the past history of the mill operations, inspections, process measurements, feed/product characteristics and PROCESS DIAGNOSTIC STUDIES FOR CEMENT MILL
.jpg)
Optimization of Cement Manufacturing Process ScienceDirect
1987年8月1日 Cement manufacturing process is now operated with the aid of various control systems, such as raw meal composition control, kiln control and mill control Those systems The cement mills on a cement plant are usually sized for a clinker consumption considerably greater than the output of the plant's kilns This is for two reasons: The mills are sized to cope Cement mill Wikipedia2020年1月10日 This research aims to investigate the effect of free lime and lime saturation factor on grindability of cement clinker Cement is a powdered substance that develops strong Effect of Free Lime and Lime Saturation Factor on Grindability of This document provides the standard operating procedure for starting up, shutting down, and operating cement mills at Anjani Portland Cement Limited It outlines the specific sequence SOPStartup Shutdown and Operation of Cement Mills
.jpg)
OPTIMIZATION OF CEMENT GRINDING OPERATION IN BALL MILLS
The consumption of energy by the cement grinding operation amounts to one third of the total electrical energy used for the production of cement The optimization of this process would The Cement Plant Operations Handbook is a concise, practical guide to cement manufacturing and is the standard reference used by plant operations personnel worldwide Providing a The Cement Plant Operations Handbook International Cement 2013年3月1日 This study investigated a mathematical model for an industrialscale vertical roller mill(VRM) at the Ilam Cement Plant in Iran The model was calibrated using the initial survey's data, and the Cements ground in the vertical roller mill fulfil the 6 The mill hot air inlet temperature should not exceed 315°C on systems using ambient air 7 The mill outlet temperature should not exceed 95°C on direct fired systems; the maximum outlet temperature on indirect systems is generally Everything you need to know about Kiln System
.jpg)
Effect of Free Lime and Lime Saturation Factor on Grindability of
About 30% of the energy are required to manufacture one ton of cement is used up in grinding It sums up to a substantial percentage of the over all cost of cement The consumption of energy in cement mill varies within, 165 to 635 KWh/ton, having an average of 2021年4月1日 In cement industry process control, extended efforts have been dedicated to raw meal homogeneity as it is the main factor affecting clinker activityInfluence of raw meal composition on clinker reactivity and cement 2004年12月1日 During the last decade, semifinishgrinding plants have been used more and more for the energy efficient grinding of highquality cement In 1999, it was found that by decreasing the ball charge Optimization of continuous ball mills used for finishgrinding of 2022年4月6日 6 Grinding of Clinker: • Cooled clinker is ground along with 3 5 % gypsum in a cement grinding mill (ball mill / VRM/ Roll press combined with a ball mill) to a fine powder, known as cement 7 Storage of Cement: • The ground cement is stored in cement silos (having different compartments) from where it is fed to packer machines 8From raw materials to 8 steps of cement manufacturing, read
.jpg)
The effect of water saturation degree on the electrical
2016年3月1日 The reason is that the conductivity of cementbased materials depends on the pore characteristics (porosity, pore connectivity, etc), and the pore characteristics are important factors that 2016年9月1日 Cement production is one of the most energyintensive manufacturing industries, and the milling circuit of cement plants consumes around 4% of a year's global electrical energy productionOperational parameters affecting the vertical roller mill 2019年6月6日 The optimum dosage of superplasticizer (SP) additives is determined by the saturation point of SP (SPS), obtained on cement paste by the utilization of the Marsh coneAnalytical method for determining the saturation point of Limestone and gypsum (additions) are taken from a cement mill doser (BK IV) and they dried in an oven at 105°C and 60°C, respectively to facilitate crushing and to prevent clogging in the mill Fly ash is taken from a cement mill doser (BK IV) They have a dry fine nature and they don't need any grinding or dryingEffect of clinker free lime and cement fineness on the cement
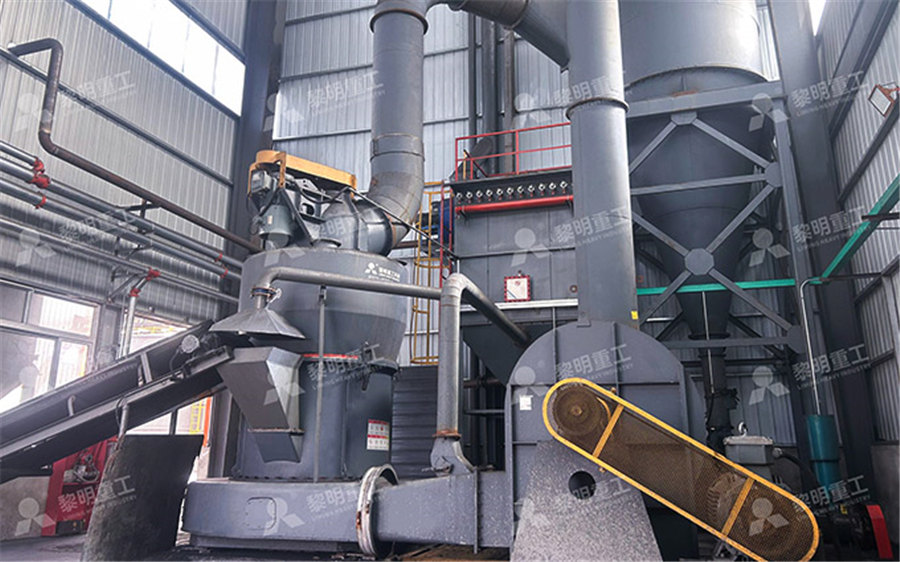
Effect of Free Lime and Lime Saturation Factor on Grindability of
Tikrit Journal of Engineering Sciences, 2016 Two types of Portland Cement Clinker quot;PCCquot; were used in this study: high fineness grinded and low fineness grinded , and after grinding of PCC, hydrated lime was used in 5%,10% and 15%; by weight, as a replacement of the blend cement with a constant 3% addition of gypsum by the blend weightexercise caution when it came to establishing new cement plants The result was that, between 1980 and 2000, no new cement company was established in Nigeria (Mojekwu et al 2012) Despite this, cement demand in the country continued to increase, resulting in the importation of more cement into the countryDangote Cement: The Challenges of PanAfrican Expansion2015年12月31日 Small gel and capillary pores in the cement matrix fill quickly on exposure to water, but larger pores (entrapped and entrained air voids) require longer times or other methods to achieve saturation(PDF) Using Neutron Radiography to Quantify Water Request PDF On Jul 1, 2016, Stephy Retnam and others published Development of Fuzzy Logic Controller for Cement Mill Find, read and cite all the research you need on ResearchGateDevelopment of Fuzzy Logic Controller for Cement Mill
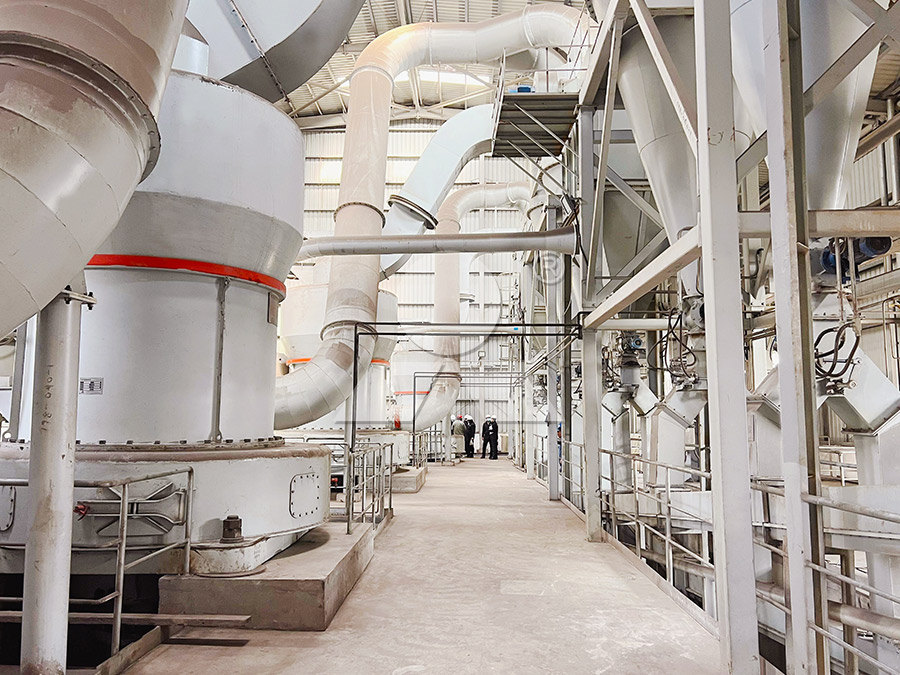
The Decision Algorithm of Cement Mill Operation Index
Request PDF On Jan 25, 2023, Chong Liu and others published The Decision Algorithm of Cement Mill Operation Index Based on Improved Differential Evolution Algorithm Find, read and cite all the 2022年12月23日 This review provides an indepth analysis of the complex chemistry of cement, offering valuable insights for researchers(PDF) An Insight into the Chemistry of Cement—A ReviewOne reason is that most cement plants manufacture different types of cement such as highearlystrength, block and sulfateresistant; therefore, composition of the kiln feed must change from time to time as different kinds of cement are being manufactured Every time the feed composition changes, burnability in the kiln will also changeEVERYTHING YOU NEED TO KNOW ABOUT THE CHEMISTRY OF 2015年2月14日 However, the measurement of material flow rates was not easier Costea et al [13] developeda fuzzy logicbased control architecture in which the ball mill grinding process was considered as a Control System Architecture for a Cement Mill Based on Fuzzy
.jpg)
(PDF) Empirical Assessment of Performance of Dangote Cement
By enforcing the retailing of cement at a markup on the cost at which wholesalers make the goods available in their shops, price can be stabilized and uniform for longer periods of time thus, putting an end to sudden increase in prices 144 European Journal of Business and Management ISSN 22221905 (Paper) ISSN 22222839 (Online) Vol13, No10 2023年1月25日 Abstract An improved differential evolutionary cement mill operation index decision algorithm based on constraint control and selection strategy is proposed to address the problem that the operation index is usually decided by manual experience in the cement mill operation process, which causes unqualified cement specific surface area and excessive The Decision Algorithm of Cement Mill Operation Index Based2021年11月17日 A 33grade cement concrete mortar made with cement, water, and sand in the ratio of 1:1:3 cured for 28 days under controlled conditions achieves a minimum compressive strength of 33 N/mm 2 A 33grade cement is used in plain cement concrete (PCC) where it is not subjected to stress It complies with the specifications set out in BIS 269 standardsFundamentals of Cement Chemistry, Operations, and Quality The desired target for the free lime content in the cement clinker is 05% 15% [10] or below 2% [12] Lower values of free lime indicates an overburn, consuming more energy both in the clinker Effect of kiln feed on lime saturations factor

(PDF) Cement Quality Control By Using Modern
2019年3月1日 An essential part of modern quality management system in cement production is stateoftheart radiation measurement technologies based on methods of neutron activation, Xray fluorescence and X 即时翻译文本完整的文档文件。为个人和团队提供准确的翻译。每天有数百万人使用DeepL进行翻译。DeepL翻译:全世界最准确的翻译 DeepL Translate2019年6月13日 Overview: Cement Milling / Finish grinding is the last unit operation in the cement manufacturing process (Excluding Cement Packing) However, is most critical not only with regard to power Cement Mills Optimization The Quality Perspective LinkedIn—The aim of the present research is to improve the manufacturing conditions of cement and therefore its quality For this purpose, various reference samples of clinker were produced in the normal manufacture's conditions considered by the Company of Cement of Gabes, then compared to other samples which are variable in the Lime Saturation Factor and the raw The Effect Of Raw Material's Fineness And Lime Saturation Factor
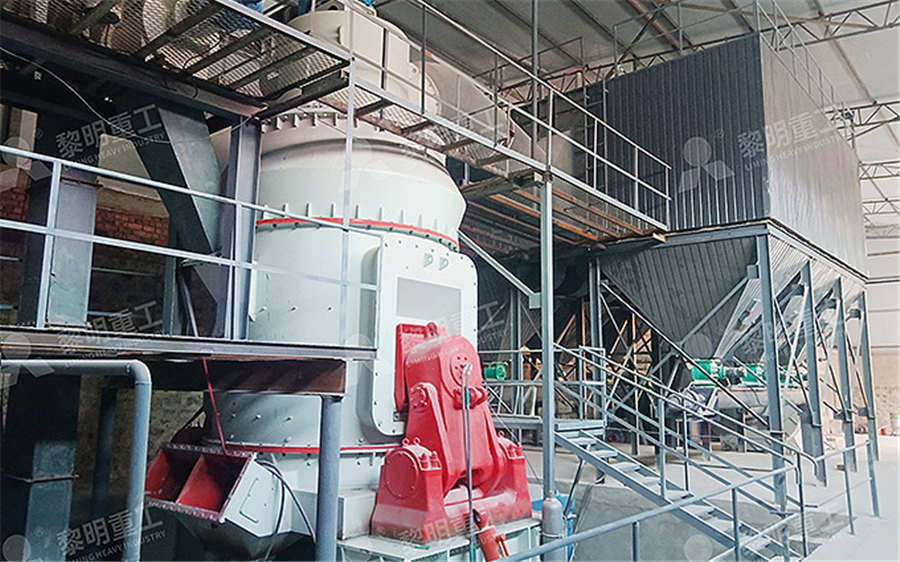
Cement mill Wikipedia
A cement mill (or finish mill in North American usage [1]) crystallization of gypsum on their rehydration causes "false set" a sudden thickening of the cement mix a few minutes after mixing, which thins out on remixing High milling temperature causes this For this reason, 14 cu cm of water in order for all the cement to become hydrated* The reason for this is that 24 cu cm is the least volume that 1 cu cm of cement can occupy after it has become per g of cement, provided that a state of saturation or near saturation of the paste is maintained The strongest materials yet made with portland cement A DISCUSSION OF CEMENT HYDRATION IN RELATION TO THE 2020年5月30日 The machines used in cement production at the factory include raw mill machines, kiln machines, and cement mill machines The more often a machine is damaged, the average time between failures of Analysis of Raw Mill Machines Maintenance in Cement Industry 2011年1月31日 The pinion from the drive of the cement mill was failed; the teeth cracked and spall occurred on the sides of several teeth The failure was only located on one side of the pinionFailure of the pinion from the drive of a cement mill
.jpg)
Cements ground in the vertical roller mill fulfil the
2013年3月1日 This study investigated a mathematical model for an industrialscale vertical roller mill(VRM) at the Ilam Cement Plant in Iran The model was calibrated using the initial survey's data, and the 6 The mill hot air inlet temperature should not exceed 315°C on systems using ambient air 7 The mill outlet temperature should not exceed 95°C on direct fired systems; the maximum outlet temperature on indirect systems is generally Everything you need to know about Kiln System About 30% of the energy are required to manufacture one ton of cement is used up in grinding It sums up to a substantial percentage of the over all cost of cement The consumption of energy in cement mill varies within, 165 to 635 KWh/ton, having an average of Effect of Free Lime and Lime Saturation Factor on Grindability of 2021年4月1日 In cement industry process control, extended efforts have been dedicated to raw meal homogeneity as it is the main factor affecting clinker activityInfluence of raw meal composition on clinker reactivity and cement
.jpg)
Optimization of continuous ball mills used for finishgrinding of
2004年12月1日 During the last decade, semifinishgrinding plants have been used more and more for the energy efficient grinding of highquality cement In 1999, it was found that by decreasing the ball charge 2022年4月6日 6 Grinding of Clinker: • Cooled clinker is ground along with 3 5 % gypsum in a cement grinding mill (ball mill / VRM/ Roll press combined with a ball mill) to a fine powder, known as cement 7 Storage of Cement: • The ground cement is stored in cement silos (having different compartments) from where it is fed to packer machines 8From raw materials to 8 steps of cement manufacturing, read2016年3月1日 The reason is that the conductivity of cementbased materials depends on the pore characteristics (porosity, pore connectivity, etc), and the pore characteristics are important factors that The effect of water saturation degree on the electrical 2016年9月1日 Cement production is one of the most energyintensive manufacturing industries, and the milling circuit of cement plants consumes around 4% of a year's global electrical energy productionOperational parameters affecting the vertical roller mill
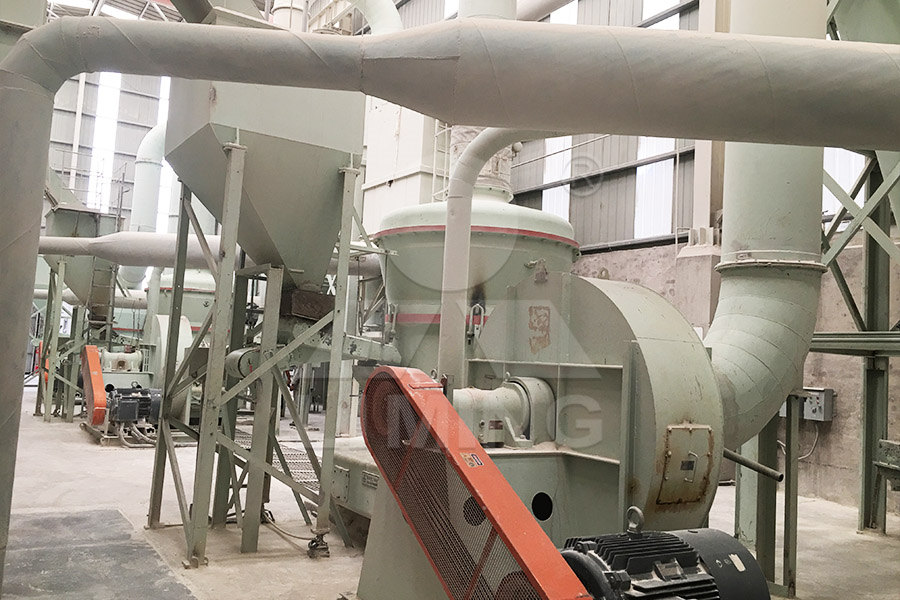
Analytical method for determining the saturation point of
2019年6月6日 The optimum dosage of superplasticizer (SP) additives is determined by the saturation point of SP (SPS), obtained on cement paste by the utilization of the Marsh cone Limestone and gypsum (additions) are taken from a cement mill doser (BK IV) and they dried in an oven at 105°C and 60°C, respectively to facilitate crushing and to prevent clogging in the mill Fly ash is taken from a cement mill doser (BK IV) They have a dry fine nature and they don't need any grinding or dryingEffect of clinker free lime and cement fineness on the cement