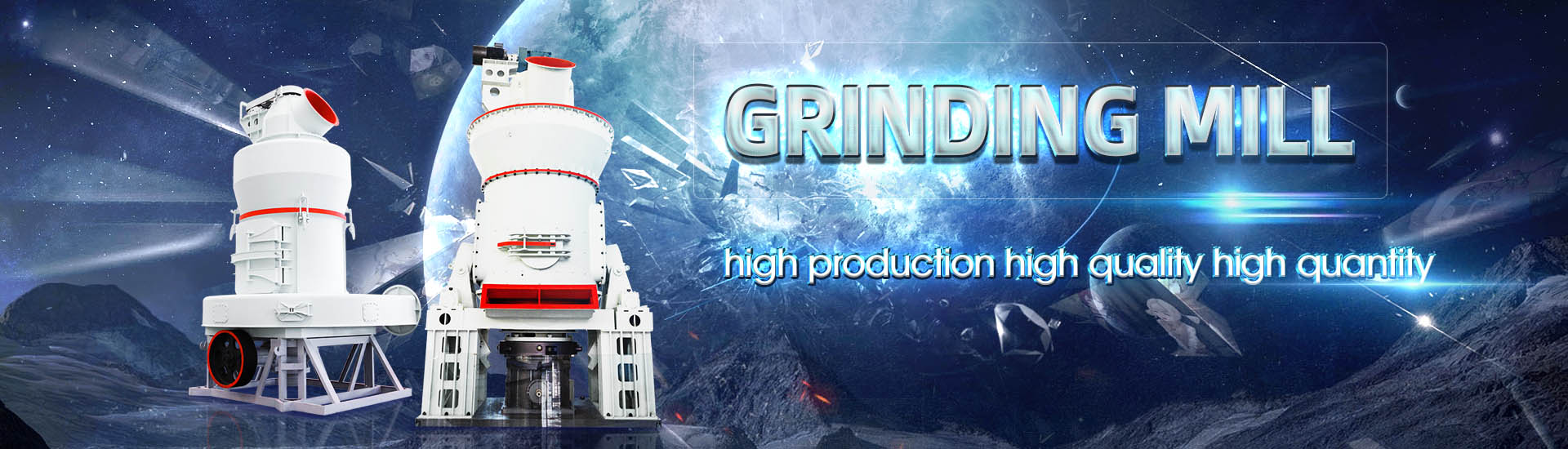
How to control the fineness of ball mill

BALL MILLS Ball mill optimisation Holzinger Consulting
in combination with a ball mill for cement grinding applications and as finished product grinding units, as well as raw ingredient grinding equipment in mineral applications This paper will focus on the ball mill grinding process, its tools and optimisation possibilities (see Figure 1) The ball 2024年10月28日 Method of fineness adjustment of ball mill 1 Adjust the grinding medium Change the type of medium: choose the appropriate type of grinding medium according to the How to adjust the fineness of the mine ball mill2012年6月1日 The paper presents an overview of the current methodology and practice in modeling and control of the grinding process in industrial ball mills Basic kinetic and energy Grinding in Ball Mills: Modeling and Process Control ResearchGateGrinding in ball mills is an important technological process applied to reduce the size of particles which may have different nature and a wide diversity of physical, mechanical and chemical Grinding in Ball Mills: Modeling and Process Control Sciendo
.jpg)
How to Control Grinding Fineness of Ball Mills
2015年11月4日 To sum up,there are five methods to control the grinding fineness of ball mills: 1In the actual production process, we can do reasonable arrangement of all kinds of minerals in order to2020年1月11日 After consulting Fote engineers and having a reference, here five methods are sorted out for the improvement of ball mill efficiency and the materials utilization rate This can reduce the energy consumption and the use 5 Ways to Improve the Ball Mill Efficiency FTM2022年7月7日 Understanding the factors that affect the grinding fineness of a ball mill is a necessary prerequisite for controlling the grinding fineness Here are 9 factors that affect the 9 factors that affect the grinding fineness of ball mill2019年4月22日 Here are ten ways to improve the grinding efficiency of ball mill 1 Change the original grindability The complexity of grindability is determined by ore hardness, toughness, dissociation andTen Ways to Improve the Grinding Efficiency of Your
.jpg)
10 Ways to Improve the Grinding Efficiency of Your Ball
Here are the 10 ways for your to improve the ball mill performance: Step#1 Change the original grindability Step#2 More crushing and less grinding to reduce the feed size into mill Step#3 Reasonable filling rate of steel ball 2017年10月25日 Ball Mill Breakage Efficiency Consider a ball mill circuit processing material of a given feed size and at a given throughput rate to a target product size, the latter which once How to Improve Ball Mill Performance 911Metallurgist2018年2月1日 In another study to investigate ball size distribution on ball mill efficiency by Hlabangana et al [50] using the attainable region technique on a silica ore by dry milling, a threeball mix of Effect of ball and feed particle size distribution on 2012年6月1日 The process control in a ball mill grinding circuit faces severe difficulties due Conditions on Fineness and Shape of Particle Size Distribution of Produc t in a Ball Mill –Grinding in Ball Mills: Modeling and Process Control
36.jpg)
5 Ways to Improve the Ball Mill Efficiency FTM
2020年1月11日 According to the industrial tests, the capacity varies with the ball mill types; Even from the same type of ball mill, the energy consumption and milling efficiency are different One of the factors is the function of the 2024年2月20日 In the example shown, it is easy to see that the Planetary Ball Mill PM 300 offers advantages in terms of power, final fineness and maximum jar volume compared to the Mixer Mill MM 500 control The latter in terms offers easier handling, versatility and the ability to control the temperature during the processHow Ball Mills Contribute to Battery Technology AZoMThe PM 100 can be found in virtually all industries where the quality control process places the highest demands on purity, speed, fineness and reproducibility The mill is ideally suited for tasks in research like mechanochemistry (cocrystal screening, In the Ball Mill PM 100 this counterweight can be adjusted on an inclined guide railPlanetary Ball Mill PM 100 RETSCH highest fineness2015年11月4日 To sum up,there are five methods to control the grinding fineness of ball mills: 4The size of the ball mill’s discharge hole plays an important role in the ore beneficiation processHow to Control Grinding Fineness of Ball Mills
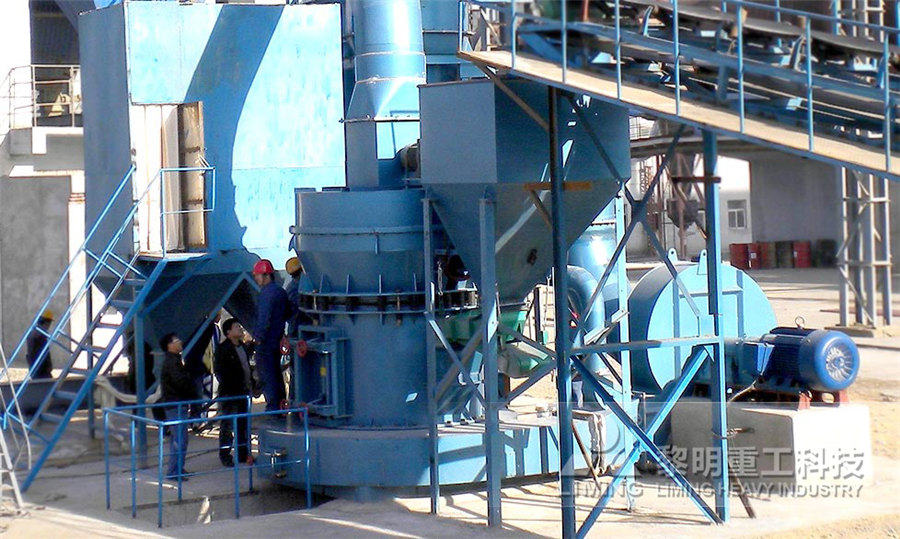
The Ultimate Guide to Ball Mills Miningpedia
2019年8月14日 Ball mill is a common grinding equipment in concentrator Common Types of Ball mill back to top The common industrial ball mills mainly include cement ball mill, tubular ball mill, ultrafine laminating mill, cone ball mill, ceramic ball mill, intermittent ball mill, overflow ball mill, grid ball mill, wind discharge ball mill, double bin ball mill, energy saving ball mill2013年8月3日 In Grinding, selecting (calculate) the correct or optimum ball size that allows for the best and optimum/ideal or target grind size to be achieved by your ball mill is an important thing for a Mineral Processing Engineer AKA Metallurgist to do Often, the ball used in ball mills is oversize “just in case” Well, this safety factor can cost you much in recovery and/or mill liner Calculate and Select Ball Mill Ball Size for Optimum Grinding2024年10月3日 The cylinder is the container that holds the ball mill grinding process together We size cylinders by their total volume when empty When selecting a cylinder, it’s important to pick a size that could potentially hold all of your grinding media, raw materials, and 25% of your total volume for processing space—what we consider the "working" area of the ball millUnderstanding the Parts of a Ball Mill Economy Ball Mill2023年10月20日 7 Control System Many modern ball mills are equipped with a control system that regulates various parameters such as mill speed, material feed rate, and temperature The control system ensures optimal operation, improves efficiency, and allows for remote monitoring and adjustments (1864 Overflow Ball Mill)Comprehensive Guide on Operating a Ball Mill Miningpedia
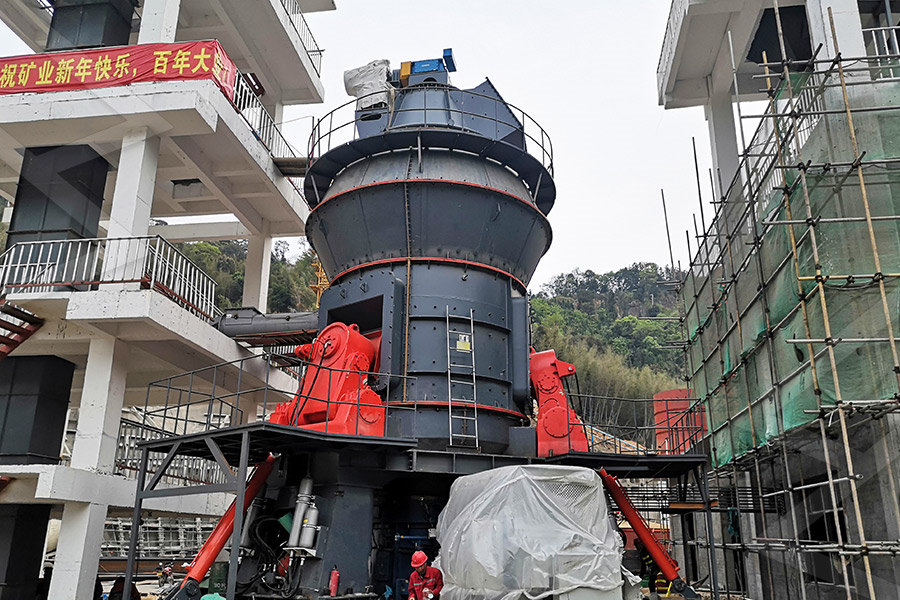
Process Training Ball Mill INFINITY FOR CEMENT
Control of ball mills Mill Feed; of different Blaine cements in one mill often install automatically adjustable guide vanes in order to be able to control the product fineness not only with the airflow through the separator and rotor For ball mill, reasonable ball internal structure of ball mill and product fineness requirements, the characteristics of grinding materials (grindability, particle size, etc) should also be considered The steel ball should have the ability to How to choose the ball loading and loading ratio of To find the suitable ball size for the desired final fineness, usually a factor of approximately 1000 can be applied If a grind size of 30 µm (D90) is the objective, the most suitable ball size would be between 20 mm and 30 mm If smaller Planetary Ball Mills RETSCH fine grinding of materialsChemical process industries are running under severe constraints, and it is essential to maintain the endproduct quality under disturbances Maintaining the product quality in the cement grinding process in the presence of clinker heterogeneity is a challenging task The model predictive controller (MPC) poses a viable solution to handle the variability This paper addresses the Predictive Controller Design for a Cement Ball Mill Grinding
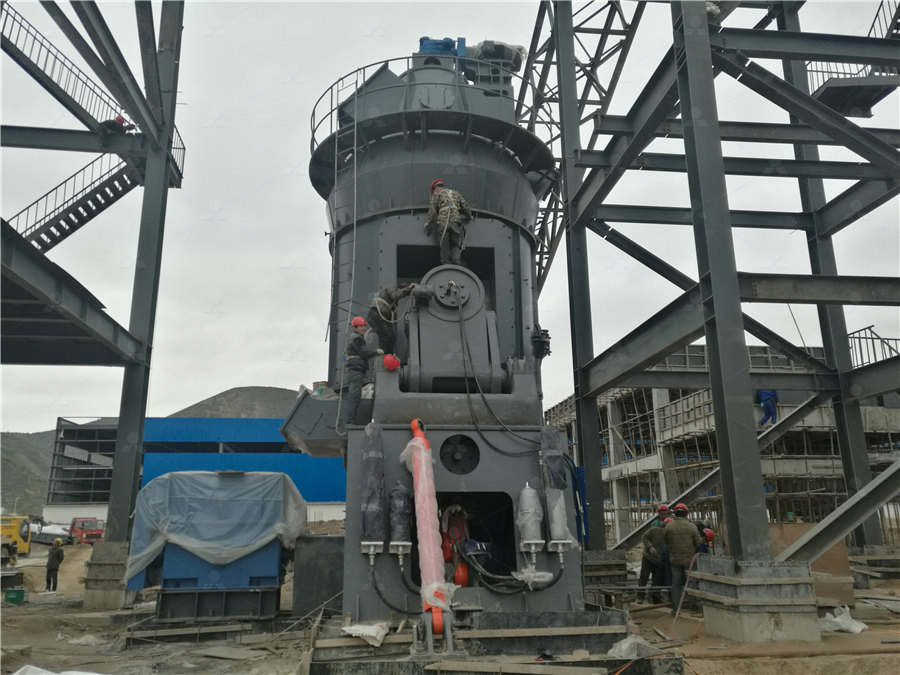
Factors Affect The Output and Quality of Ball Mills And How to
2023年12月28日 3 The ball mill is of good quality The better the quality of the ball mill, the more stable the performance of the ball mill will be during operation In addition, as for the lining plate of the ball mill’s wearing parts, the quality of the lining plate affects the overall production efficiency of the ball mill As we all know, the lining 2024年8月8日 Unlock the secrets to ball mill efficiency with our comprehensive guide on choosing the right grinding media Learn how material composition, size, shape, Conversely, larger media offer faster size reduction but may not achieve the desired fineness The shape of the media also plays a role, Ball Mill Success: A StepbyStep Guide to Choosing the Right 2021年5月11日 How to control grinding fineness of ball mill The grinding fineness of ball mill is mainly achieved by grinding operation The influencing factors of grinding fineness are: raw ore hardness, crushing particle size, mesh screen hole, ore feeding amount, ball mill model, Grinding Fineness Of Ball Mill Knowledge News CIC Luoyang ONLINE COAL FLOW MEASURING AND BALANCING (CONTROL) AND ONLINE COAL FINENESS MEASURING SYSTEM FOR COMBUSTION OPTIMISATION IN A THERMAL BOILER Suresh G Chandwani1, Dr Francesco Turoni2, Reinhardt Kock2, Dr Michael Haug2, Dr Michael Schreiber2 1NSGuzder Company Pty Ltd, Neville House, Currimbhoy Road, CPRI Online Coal Flow Balancing and Fineness Adjustment
.jpg)
How to Adjust Cement Mill Fineness?
2023年9月22日 The cement mill is undoubtedly an important piece of equipment in the cement grinding station, and its quality directly determines the quality of the cementRecently, a customer wrote to inquire about the cement mill upgrade solution The customer said that his cement mill has only been used for two years, and the fineness of the finished cement appears to be coarse2019年4月22日 For example, control the ore feed of the ball mill, control the water supply of the ball mill, adjust the classifying effect, and control the particle size composition and moisture of the sand returnTen Ways to Improve the Grinding Efficiency of Your Ball Mill2020年3月21日 Ball mill's low grinding efficiency, low processing capacity, high production energy consumption, unstable product fineness, etc are problems that many customers will encounter How to effectively improve the grinding Top 10 tips to improve the grinding efficiency of ball 2020年7月2日 A comprehensive investigation was conducted to delineate the effect of ball size distribution, mill speed, and their interactions on power draw, charge motion, and balls segregation in a (PDF) Effects of Ball Size Distribution and Mill Speed and Their
.jpg)
Temperature Reduction for Ball Mill Optimization
Therefore, the ventilation methods of many ball mill grinders are restricted by that fineness Air vents must be no larger than the small material you are attempting to create Additional issues with proper ventilation are created by system Cement Ball Mill A ball mill is a type of grinder used to grind, blend and sometimes for mixing of materials for use in mineral dressing processes, paints, pyrotechnics, ceramics and selective laser sintering Ball mill in the cement industry is used to reduce the size of clinker into fine particles also called as cementEffects of Mill Speed and Air Classifier Speed on Performance of 2014年3月1日 With a view to developing a sound basis for the design and scaleup of ball mills, a large amount of data available in the literature were analyzed for variation of the two key mill performance (PDF) Analysis of ball mill grinding operation using mill power 2024年10月28日 In the open circuit system, the mill product has the fineness required for the next stage Local control stations (local control panels, emergency stop switches, safety lanyards) Sensors and detectors Ball Mill Dust CollectorBALL MILL MAINTENANCE The Cement Institute

Effects of Mill Speed and Air Classifier Speed on Performance of
2021年6月29日 Nowadays, ball mills are widely used in cement plants to grind clinker and gypsum to produce cement The research focuses on the mill speed as well as air classifier speed effect on the two 2022年6月24日 The ball mill is the key equipment for the material to be body, main reducer lubrication station, hydraulic station, PLC electrical control cabinet and other parts composition When the vertical mill is working, the main motor drives the Clum ultrafine vertical mill Fineness: 1503000mesh Yield: 120t/h see More >> GET IN How to choose between ball mill and vertical roller mill?2023年3月1日 This led to an improvement of the mill control and monitoring by the operator in the control room Blaine's fineness prediction with kernel principal component regression showed a great prediction accuracy when online monitoring in an industrial ball mill is carried out [6]Efficient machine learning model to predict fineness, in a vertical Retsch visualises the features and strengths of each ball bill model in a diagram to help finding the right model for a specific application In the example shown it is easy to see that the Planetary Ball Mill PM 300 offers advantages in terms of power, final fineness and maximum jar volume compared to the Mixer Mill MM 500 controlBall Mills Suitable for every application Retsch
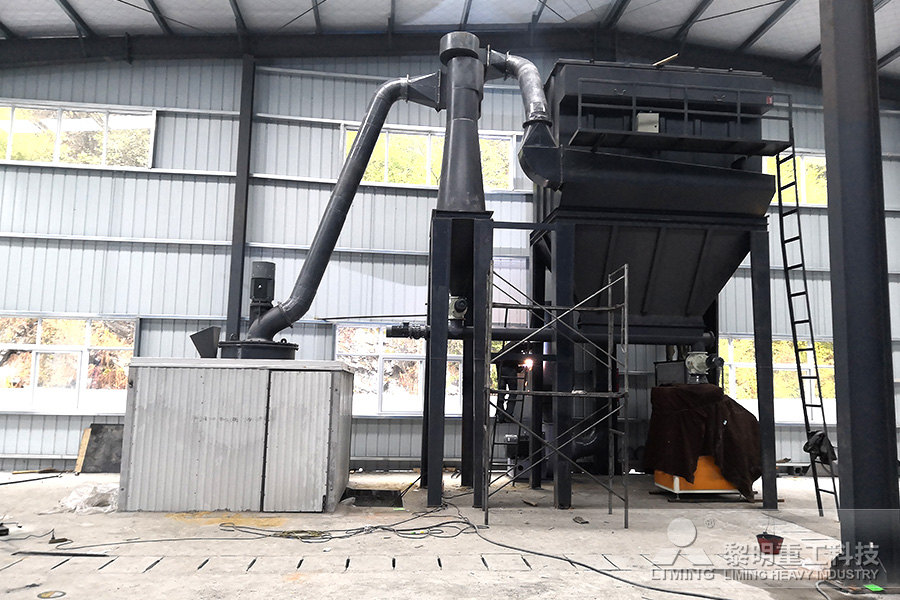
Effect of ball and feed particle size distribution on
2018年2月1日 In another study to investigate ball size distribution on ball mill efficiency by Hlabangana et al [50] using the attainable region technique on a silica ore by dry milling, a threeball mix of 2012年6月1日 The process control in a ball mill grinding circuit faces severe difficulties due Conditions on Fineness and Shape of Particle Size Distribution of Produc t in a Ball Mill –Grinding in Ball Mills: Modeling and Process Control2020年1月11日 According to the industrial tests, the capacity varies with the ball mill types; Even from the same type of ball mill, the energy consumption and milling efficiency are different One of the factors is the function of the 5 Ways to Improve the Ball Mill Efficiency FTM2024年2月20日 In the example shown, it is easy to see that the Planetary Ball Mill PM 300 offers advantages in terms of power, final fineness and maximum jar volume compared to the Mixer Mill MM 500 control The latter in terms offers easier handling, versatility and the ability to control the temperature during the processHow Ball Mills Contribute to Battery Technology AZoM

Planetary Ball Mill PM 100 RETSCH highest fineness
The PM 100 can be found in virtually all industries where the quality control process places the highest demands on purity, speed, fineness and reproducibility The mill is ideally suited for tasks in research like mechanochemistry (cocrystal screening, In the Ball Mill PM 100 this counterweight can be adjusted on an inclined guide rail2015年11月4日 To sum up,there are five methods to control the grinding fineness of ball mills: 4The size of the ball mill’s discharge hole plays an important role in the ore beneficiation processHow to Control Grinding Fineness of Ball Mills2019年8月14日 Ball mill is a common grinding equipment in concentrator Common Types of Ball mill back to top The common industrial ball mills mainly include cement ball mill, tubular ball mill, ultrafine laminating mill, cone ball mill, ceramic ball mill, intermittent ball mill, overflow ball mill, grid ball mill, wind discharge ball mill, double bin ball mill, energy saving ball millThe Ultimate Guide to Ball Mills Miningpedia2013年8月3日 In Grinding, selecting (calculate) the correct or optimum ball size that allows for the best and optimum/ideal or target grind size to be achieved by your ball mill is an important thing for a Mineral Processing Engineer AKA Metallurgist to do Often, the ball used in ball mills is oversize “just in case” Well, this safety factor can cost you much in recovery and/or mill liner Calculate and Select Ball Mill Ball Size for Optimum Grinding
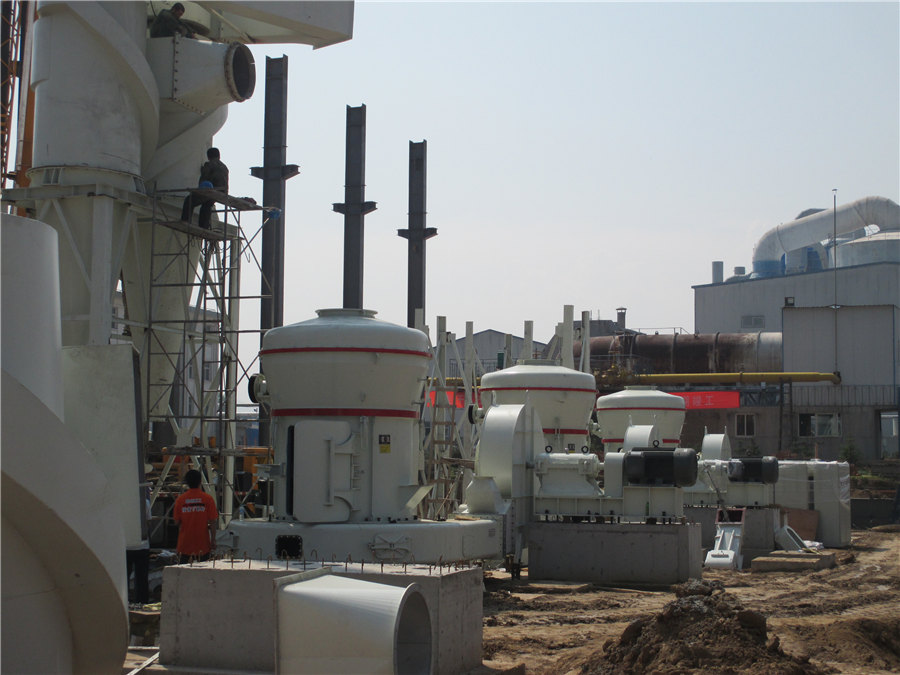
Understanding the Parts of a Ball Mill Economy Ball Mill
2024年10月3日 The cylinder is the container that holds the ball mill grinding process together We size cylinders by their total volume when empty When selecting a cylinder, it’s important to pick a size that could potentially hold all of your grinding media, raw materials, and 25% of your total volume for processing space—what we consider the "working" area of the ball mill2023年10月20日 7 Control System Many modern ball mills are equipped with a control system that regulates various parameters such as mill speed, material feed rate, and temperature The control system ensures optimal operation, improves efficiency, and allows for remote monitoring and adjustments (1864 Overflow Ball Mill)Comprehensive Guide on Operating a Ball Mill Miningpedia