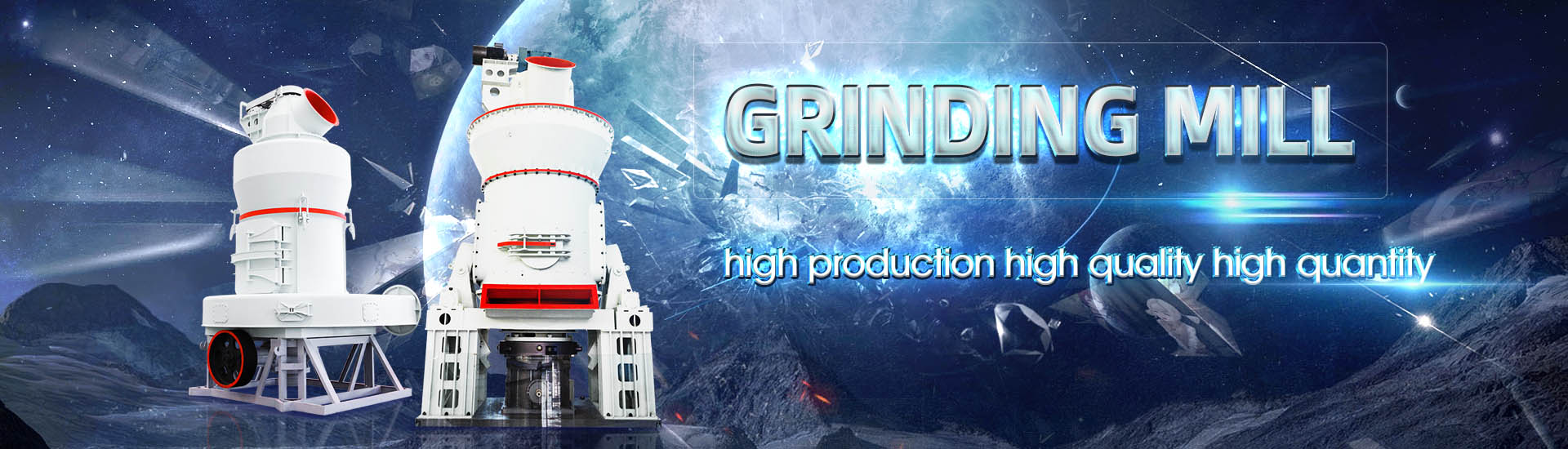
what ore grinding machine does the cement plant use

Cement Ball Mill Cement Grinding Machine Cement
Cement ball mill is a cement grinding machine used in the cement production line for cement clinker grinding AGICO supplies the cement ball mills for processing limestone, cement clinker, gypsum, slag, ore, etcThe cement roller press is a new kind of cement mill It is usually used as a pregrinding system to replace some functions of the ball mill so that the output of the ball mill can be increased by 3050% At the same time, it can also be Cement Manufacturing Machine Cement Making common solution to grind raw materials and cement Roller presses are used mainly in combination with a ball mill for cement grinding applications and as finished product grinding BALL MILLS Ball mill optimisation Holzinger ConsultingPrepare cement raw materials: The primary raw materials are limestone and clay, along with fly ash, iron ore, and coal 2 Grinding: The raw materials are ground into fine powder (1–25 mm) Overview of Cement Making Machine (with Price and Capacity)
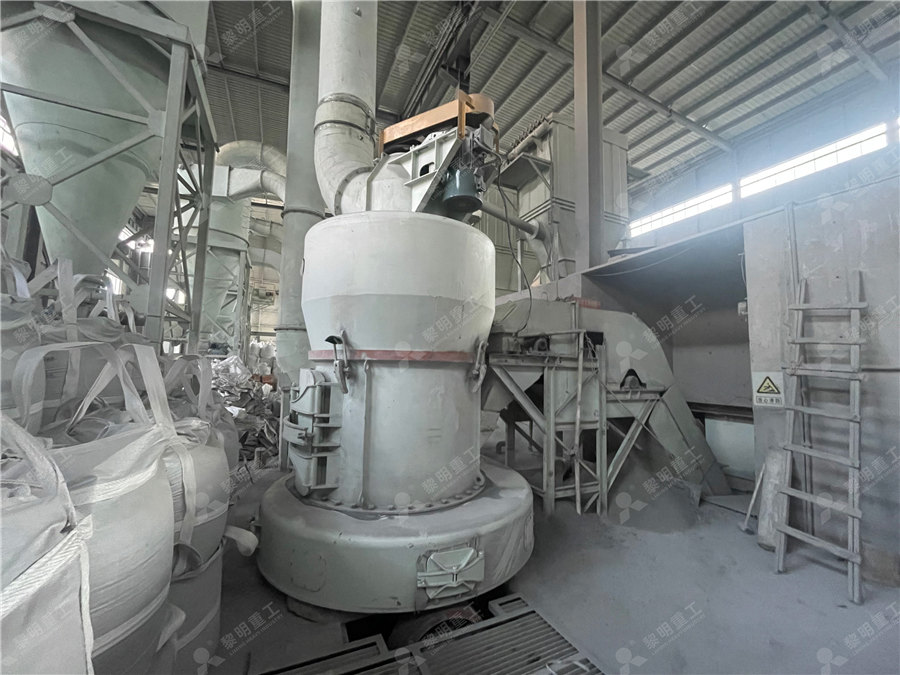
Vertical Cement Mill
The vertical cement mill is largescale cement grinding machine With advantages of energyefficient and stable quality, vertical roller mill is widely applied to many industries, such as All grinding work is done in the tube mill and the setup is: Tube Mill with Pregrinding Unit Part of the grinding work is done in a pregrinding unit, which can be: Depending on the selected CEMENT GRINDING SYSTEMS INFINITY FOR CEMENT EQUIPMENT2019年1月3日 Clinker grinding technology is the most energyintensive process in cement manufacturing Traditionally, it was treated as "low on technology" and "high on energy" as Clinker grinding technology in cement manufacturingEnduron® high pressure grinding rolls (HPGR) can handle a wide variety of ores and particle sizes from fine pellet feed all the way up to coarse grinding of 75mm magnetite iron oreOur Dynamic HPGR Technology for Mineral Grinding Weir
.jpg)
Everything you need to know about clinker/cement
Everything you need to know about clinker/cement Grinding if You read and understand this article , you will be ready to be a cement grinding area manager FEED AND FEED SYSTEM Feed Temperature Plants with satellite coolers Cement Grinding Plant Hot Sale; Modular Grinding Plant; Concrete Batching Plant; Generally, the proportion of components in cement raw materials is 6775% limestone, 1015% clay, 0515% iron ore and 8511% coal The How Is Cement Produced in Cement Plants Cement would be a length of 135 m and a diameter of 25 m, with a speed of approximately 20 revolutions per minute Such a mill would normally have a load of approximately 90 tons of grinding media, graduated from 90 mm to 60 mm An Introduction to Clinker Grinding and Cement StorageCement grinding unit is also called the cement grinding plant It consists of cement ball mill, dust collector, belt conveyor, bucket elevator, cement silo, powder concentrator, etc AGICO provides highquality clinker grinders and advanced cement grinding technologyCement Grinding Unit Clinker Grinder AGICO Cement
.jpg)
Cement mill Wikipedia
A 10 MW cement mill, output 270 tonnes per hour A cement mill (or finish mill in North American usage [1]) is the equipment used to grind the hard, nodular clinker from the cement kiln into the fine grey powder that is cementMost cement is currently ground in ball mills and also vertical roller mills which are more effective than ball mills2020年8月25日 Cement grinding: The clinker is taken from the clinker silo and sent to the feed bin where it is mixed with gypsum and additives before entering the cement grinding plant In the cement grinding process, the clinker is ground to a fine powder along with other materials, up to 5% gypsum or additional anhydrite is added to control the Cement Production Process Cement Manufacturing Process AGICO CEMENTPortland cement clinker was first made (in 1825) in a modified form of the traditional static lime kiln [2] [3] [4] The basic, eggcup shaped lime kiln was provided with a conical or beehive shaped extension to increase draught and thus obtain the higher temperature needed to make cement clinkerFor nearly half a century, this design, and minor modifications, remained the only Cement kiln WikipediaClinker is a nodular material produced in the kilning stage during the production of cement and is used as the binder in many cement products The lumps or nodules of clinker are usually of diameter 325 mm and dark grey in color It is produced by heating limestone and clay to the point of liquefaction at about 1400°C1500°C in the rotary kiln What is Cement Clinker? Composition, Types Uses
.jpg)
The essentials of electrical systems in cement plants EEP
2020年9月14日 The desired raw mix of crushed raw material and the additional components required for the type of cement, eg silica sand and iron ore, Power distribution system of a cement plant begins with the substation of the grid where power is received and ends with individual drives and Separator for cement mill: : 14: Packing machine:2023年10月19日 Types of Clinker Grinding Techniques used in cement manufacturing process Clinker grinders are an important part of the cement manufacturing process They are used to grind clinker into a fine powder and are typically located at the end of the cooler in a cement plantClinker Grinding Techniques in Cement Manufacturing JM Other materials used to manufacture cement include: shells, chalk, shale, slate, silica sand, iron ore, and blast furnace slag The Cement Manufacturing Process While each cement plant may differ in layout, equipment, and appearance, the How Cement is Made Portland Cement AssociationThe final manufacturing stage at a cement plant is the grinding of cement clinker from the kiln, mixed with 45% gypsum and possible additives, into the final product, cement In a modern cement plant the total consumption of electrical energy is about 100 kWh/t The cement grinding process accounts for approx 40% if this energy consumptionCEMENT GRINDING SYSTEMS INFINITY FOR CEMENT EQUIPMENT

Mineral Processing Plants: What You Need to Know
2024年8月15日 Widely used for fine grinding; can operate in dry or wet modes based on process requirements High Rod mill: Largersized ores Ideal for coarse ore grinding, preventing overgrinding Low Autogenous mill: Very hard, highly 2023年8月23日 A cement mill is a fundamental component of the cement manufacturing process, playing a vital role in breaking down and grinding cement clinker into fine powder This finely ground powder, when mixed with other materials, produces the building material we commonly know as cement To achieve this crucial transformation, a cement mill comprises What Are the Parts of a Cement Mills?2019年1月3日 Clinker grinding technology is the most energyintensive process in cement manufacturing Traditionally, it was treated as "low on technology" and "high on energy" as grinding circuits use more than 60 per cent of total energy consumed and account for most of the manufacturing cost Since the increasing energy cost started burning the benefits significantly, Clinker grinding technology in cement manufacturingMaintenance in the cement industry is one of the contributors to the production cost and represent typical 15 – 25 percent of total manufacturing expenditure Many companies have tried to use standard production methods to control maintenance costsMAINTENANCE IN THE CEMENT INDUSTRY
.jpg)
Grinding: Smarter Solutions Indian Cement Review
2022年8月10日 Equipment required for the cement grinding plant include cement roller press, cement silos, belt conveyors, cement mills, classifiers, bucket elevators, packing machines, etc The grinding mill and cement roller press are the core equipment of the cement grinding units These grinding mills directly decide the quality and cost of whole cement Cement Grinding Plant Hot Sale; Modular Grinding Plant; The hammer crusher is a kind of crushing machine which uses impact energy to crush materials It is mainly composed of limestone, gypsum, terrazzo, coal, slag, and other soft and hard ores The equipment can also adjust the gap between the screen strips, improve the discharge Cement Crusher Crushers for Cement Plant AGICO Cement 2017年5月19日 Grinding is an essential operation in cement production given that it permits to obtain fine powder which reacts quickly with water, sets in few hours and hardens over a period of weeks i Overview of cement grinding: fundamentals, additives, technologies2024年4月4日 Factors Affecting the Cost of Starting a Cement Manufacturing Plant Starting a cement manufacturing plant involves various costs that need to be carefully considered Understanding the factors that impact these costs is essential for effective financial planning and investment decisionmakingUnveiling Cement Manufacturing Plant Costs Osum

Cement Extraction, Processing, Manufacturing
2024年11月23日 Cement Extraction, Processing, Manufacturing: Raw materials employed in the manufacture of cement are extracted by quarrying in the case of hard rocks such as limestones, slates, and some shales, with the Stage 2: Grinding, Proportioning, and Blending The crushed raw ingredients are made ready for the cementmaking process in the kiln by combining them with additives and grinding them to ensure a fine homogenous mixture The composition of cement is proportioned here depending on the desired properties of the cement Generally, limestone is 80%, and the remaining 20% How Cement is Made Cement Manufacturing ProcessRaw Materials Crushing, Storing and Grinding Clinker calcination is the most crucial part of the whole process of cement manufacturing At this stage, ground raw materials will be sent into the cement kiln and be heated at a high Cement Clinker Calcination in Cement Production The vertical roller mill (VRM) is a type of grinding machine for raw material processing and cement grinding in the cement manufacturing processIn recent years, the VRM cement mill has been equipped in more and more cement plants around the world because of its features like high energy efficiency, low pollutant generation, small floor area, etc The VRM cement mill has a Vertical Roller Mill Operation in Cement Plant
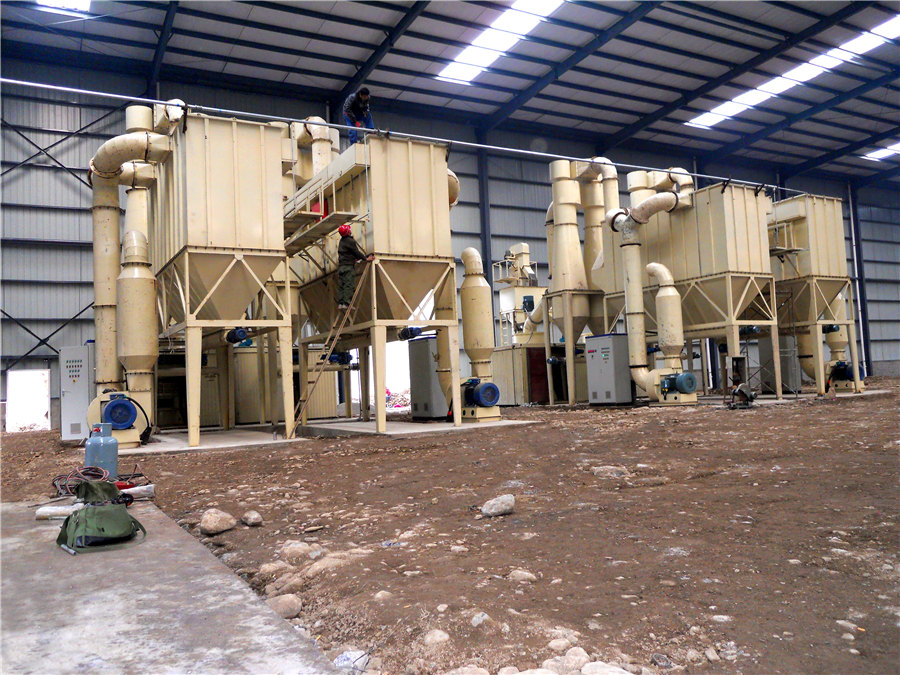
Cement Euipment Overview Cement Making Machines Cement Plant
2019年9月27日 AGICO offers cement making machines including cement mill, rotary kiln, cement crusher, cyclone preheater, cement dryer, clinker cooler etc any need? Skip to content Cement ball mill, vertical cement mill, and cement roller press are common types of cement grinding plant cement ball millCement manufacturing process The cement manufacturing plant can be divided into five steps: Crushing prehomogenization: cement crusher crush limestone and other materials and stacker and reclaimer homogenize them; Raw material preparation: use cement mill to process materials into required sizes for cement clinker production; Clinker production: In the cyclone preheater Cement Plant Cement Manufacturing Plant EPC ProjectMainly used for startup in all the cement plants Type Fuel oil Gas oil, LDO, Heavy fuel oil Heavy fuel oil is the mainly used oil in Cement kiln as it is comparatively cheaper Fuel oil Composition (% by weight) 85 % Carbon, 1117 % Hydrogen and 1 2 % SulphurCement Manufacturing Process INFINITY FOR CEMENT EQUIPMENTAs a leading cement plant builder, AGICO offers an expert cement grinding plant EPC service Cement Grinding Unit EPC Solution With a strong RD team, experienced engineers, and firstclass technical services, we aim to provide users with the most advanced and optimized cement production solutionsCement Grinding Plant Expert Cement Grinding Solutions from

Cement Grinding Plant Manufacturers NT Engitech
Cement Grinding plant The cement grinding unit manufactured by our company combines drying, grinding, powder classification, dust collection and cement packing It can grind cement clinker and process cement mixtures such as gypsum, fly ash, furnace slag, coal gangue, etc, realizing stable, highquality, and automatic cement productionBefore you send inquiry Please provide us with project information as much as possible: For a complete project: the material availability, the required output capacity, the process technology, your budgetary and financing status, the estimated starting time, etc For singular machinery: the model, the capacity, your budgetary information, other requirements, etcCement Equipment, Cement Plant Equipment Cement Plant Everything you need to know about clinker/cement Grinding if You read and understand this article , you will be ready to be a cement grinding area manager FEED AND FEED SYSTEM Feed Temperature Plants with satellite coolers Everything you need to know about clinker/cement Cement Grinding Plant Hot Sale; Modular Grinding Plant; Concrete Batching Plant; Generally, the proportion of components in cement raw materials is 6775% limestone, 1015% clay, 0515% iron ore and 8511% coal The How Is Cement Produced in Cement Plants Cement
.jpg)
An Introduction to Clinker Grinding and Cement Storage
would be a length of 135 m and a diameter of 25 m, with a speed of approximately 20 revolutions per minute Such a mill would normally have a load of approximately 90 tons of grinding media, graduated from 90 mm to 60 mm Cement grinding unit is also called the cement grinding plant It consists of cement ball mill, dust collector, belt conveyor, bucket elevator, cement silo, powder concentrator, etc AGICO provides highquality clinker grinders and advanced cement grinding technologyCement Grinding Unit Clinker Grinder AGICO CementA 10 MW cement mill, output 270 tonnes per hour A cement mill (or finish mill in North American usage [1]) is the equipment used to grind the hard, nodular clinker from the cement kiln into the fine grey powder that is cementMost cement is currently ground in ball mills and also vertical roller mills which are more effective than ball millsCement mill Wikipedia2020年8月25日 Cement grinding: The clinker is taken from the clinker silo and sent to the feed bin where it is mixed with gypsum and additives before entering the cement grinding plant In the cement grinding process, the clinker is ground to a fine powder along with other materials, up to 5% gypsum or additional anhydrite is added to control the Cement Production Process Cement Manufacturing Process AGICO CEMENT
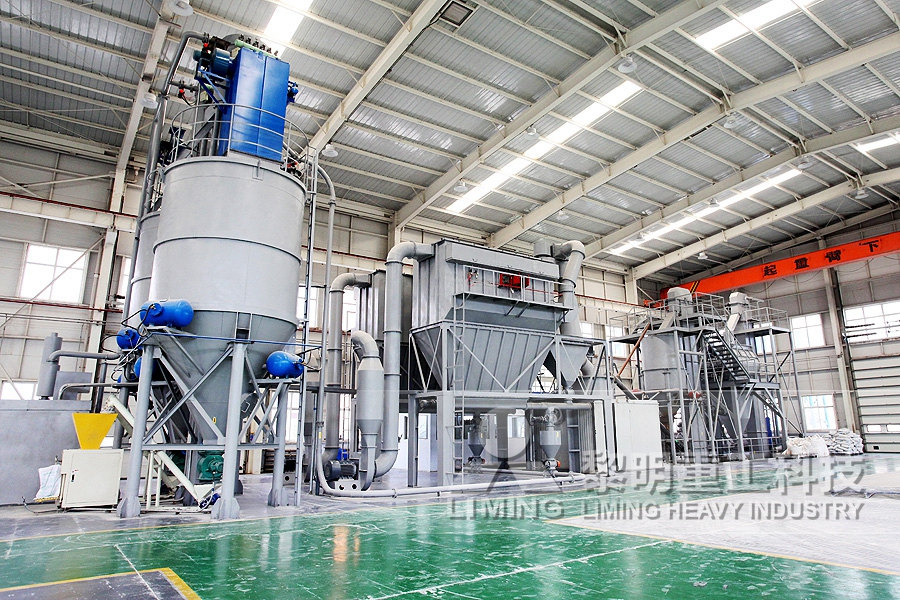
Cement kiln Wikipedia
Portland cement clinker was first made (in 1825) in a modified form of the traditional static lime kiln [2] [3] [4] The basic, eggcup shaped lime kiln was provided with a conical or beehive shaped extension to increase draught and thus obtain the higher temperature needed to make cement clinkerFor nearly half a century, this design, and minor modifications, remained the only Clinker is a nodular material produced in the kilning stage during the production of cement and is used as the binder in many cement products The lumps or nodules of clinker are usually of diameter 325 mm and dark grey in color It is produced by heating limestone and clay to the point of liquefaction at about 1400°C1500°C in the rotary kiln What is Cement Clinker? Composition, Types Uses2020年9月14日 The desired raw mix of crushed raw material and the additional components required for the type of cement, eg silica sand and iron ore, Power distribution system of a cement plant begins with the substation of the grid where power is received and ends with individual drives and Separator for cement mill: : 14: Packing machine:The essentials of electrical systems in cement plants EEP2023年10月19日 Types of Clinker Grinding Techniques used in cement manufacturing process Clinker grinders are an important part of the cement manufacturing process They are used to grind clinker into a fine powder and are typically located at the end of the cooler in a cement plantClinker Grinding Techniques in Cement Manufacturing JM