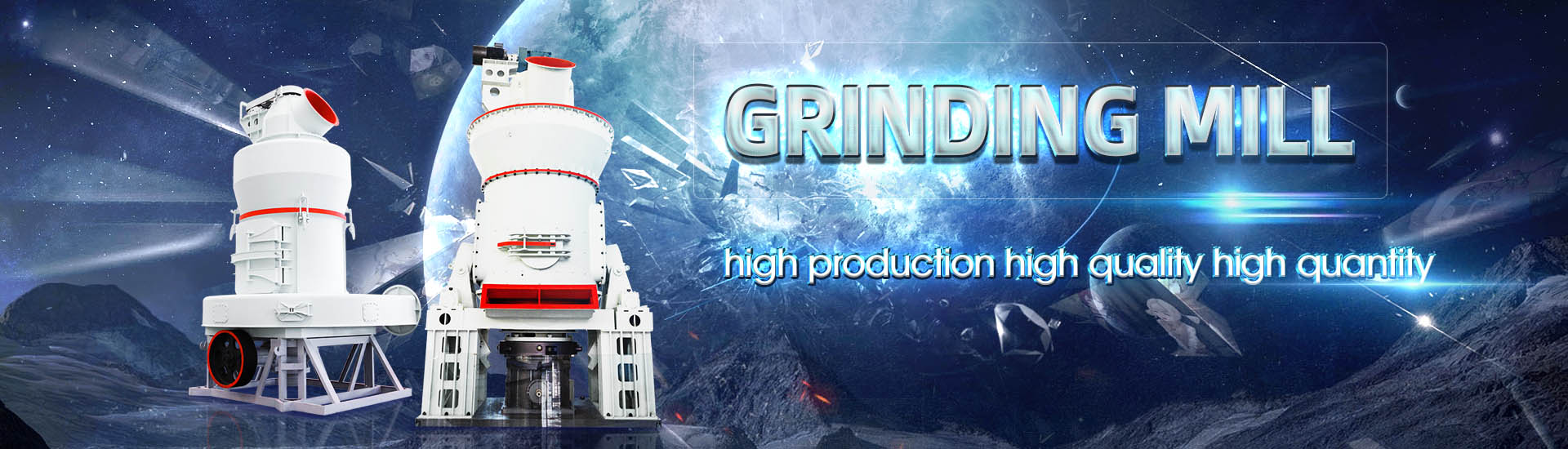
How to Handle Iron Oxide Processing Transfer Equipment
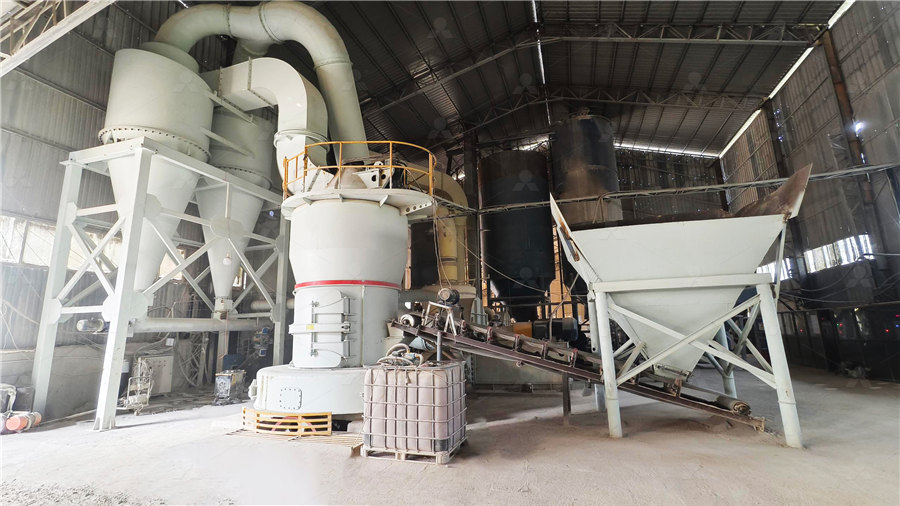
Direct Reduced Iron Fines: Guide for Shipping, Handling and Storage
12 Generation and Processing of Direct Reduced Iron Fines There are two principal sources of fines generation during the direct reduction process, as illustrated in the graphic below, based on the flowsheet of the Midrex process2017年10月17日 The Hismelt process employs a single smelt reduction vessel (SRV) where iron oxide fines are injected deep into hot metal melt, which instantly reduces the ore to produce iron and carbon monoxide Flux and coal are also From Ore to Iron with Smelting and Direct Iron 2024年4月26日 Iron ore, a naturally occurring mineral composed primarily of iron oxides, is mined and processed to extract iron for various industrial applications This article provides a comprehensive overview of the iron ore Iron Ore Processing: From Extraction to Manufacturingseveral ways: (1) on impact (eg, freefall drops from handling equipment in yards and into vessel holds, transfer points on conveyor belts, bins or other hard surfaces; (2) crushing of pellets Direct Reduced Iron (DRI): Guide to Shipping, Handling and Storage
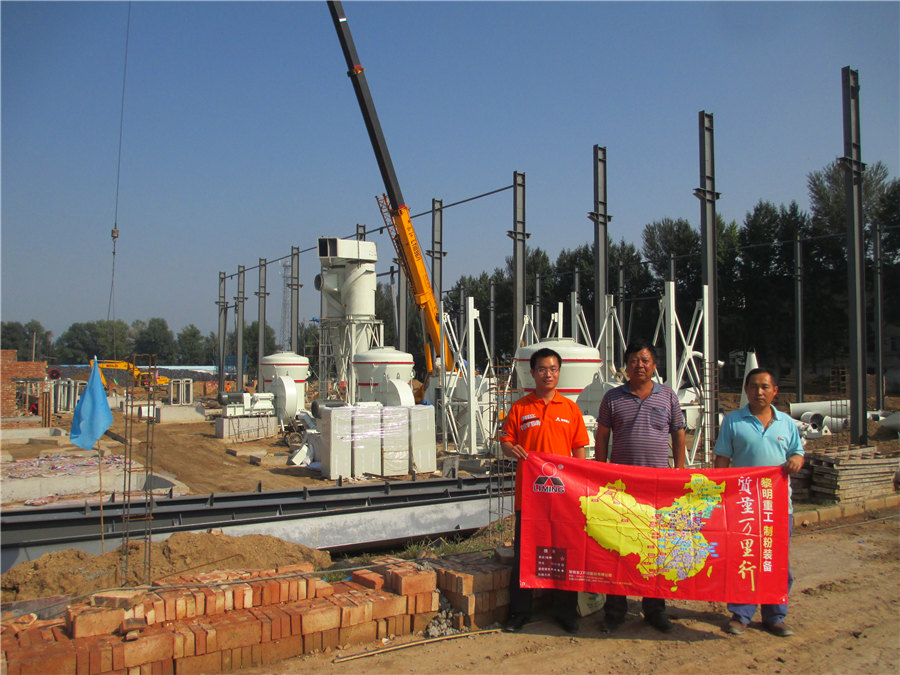
Direct Reduced Iron ByProduct Fines (DRI D): A Guide to Handling
There are several processes for direct reduction of iron ore, principally gasbased shaft furnaces (Midrex and ENERGIRON processes), accounting for 76% and coal based rotary kiln furnaces HDRI can be transported from a MIDREX® Shaft Furnace to a nearby steel mill at up to 650° C by one of three methods: enclosed and insulated conveyor, specially configured transport vessel or HOTLINK®, a system for direct feeding of HDRI Maximizing Iron Unit Yield from Ore to Liquid Steel Direct reduction of iron (DRI) forms an important subsector of the Indian steel sector, accounting for about 33% of the total steel production, which is about 3415 million tonne of steel produced inENERGYEFFICIENT TECHNOLOGY OPTIONS FOR DIRECT 2017年10月10日 Iron is made by reacting iron ore (iron oxide and impurities), coke (a reductant) and limestone (CaCO 3) in a blast furnace Iron ores with lower iron content such as taconite Ironmaking 101 – From Ore to Iron with Blast Furnaces
.jpg)
Iron Ore Processing, General SpringerLink
2022年10月20日 Making iron and steel from iron ore requires a long process of mining, crushing, separating, concentrating, mixing, agglomeration (sintering and pelletizing), and When iron ore is extracted from a mine, it must undergo several processing stages 1 Screening We recommend that you begin by screening the iron ore to separate fine particles below the The six main steps of iron ore processing MultotecAir in a hydronic HVAC system can be a problem, specifically when it comes to the development of corrosive iron oxide When system components, like pump volutes or expansion tanks, made of cast iron or steel are mixed with oxygen and water, corrosive iron oxide is formedHow to Combat Iron Oxide in Hydronic HVAC Systems Heat Transfer 2021年5月18日 21 Iron (III) Oxides Iron (III) oxide is, of course, a compound that exhibits four different crystalline polymorphs: αFe 2 O 3, βFe 2 O 3, γFe 2 O 3, and εFe 2 O 3Hematite and maghemite usually appear in nature, while beta and epsilon structures are generally synthetic oxides [10, 11]In general, the iron (III) oxides anions arrange in closepacked structures, Synthesis, Properties, and Applications of Iron Oxides: Versatility
.jpg)
The Ultimate Guide to the Black Oxide Process: Enhancing Metal
Before diving into the details of the process, let's first clarify what black oxide actually is Black oxide is a conversion coating used to blacken ferrous metals, such as steel or iron It creates a layer of black iron oxide on the surface, providing both aesthetic appeal and corrosion resistance 12 How Does the Black Oxide Process Work?Transfer into storage 6 Construction materials for storage 18 and handling Unsuitable materials Suitable materials Aluminium and its alloys Austenitic stainless steel Plastic tanks Other nonmetals Lubricants Pumps Valves Gaskets 7 Personnel safety instructions 22 Personnel protection Equipment First aid 8 Some common types of incidents 23HYDROGEN PEROXIDE HANDLING STORAGE Utah State iron ore burden is such that the ascending column of g ases interfaces with the maximum surface area of the iron ore the higher the content of iron ore fines in the feedstock, the lower the permeability of the burden The iron ore feedstock (pellets and lump ore) is therefore screened to remove fines before being charged to the furnaceDirect Reduced Iron ByProduct Fines (DRI D): A Guide to 2018年5月1日 Iron oxide bearing wastes (IOBS) are produced at every part of processing stage of sinter, molten iron and steel production They are hard to handle and in many cases are stockpiled only to be a Factors Affecting Ballability of Mixture Iron Ore Concentrates and Iron

Iron Oxide Drying Processing The ONIX Corporation
Iron Oxide Processing Systems Iron oxide, also known as ferric oxide, is an inorganic compound with the formula Fe 2 O 3 It is one of the three main oxides of iron, and occurs naturally as the mineral hematite It is the main source of iron in the steel industry Iron oxide is ferromagnetic, meaning it is attracted to magnetic sources, and is 2023年2月15日 Hematite, also spelled haematite, is a weakly magnetic iron ore with better floatability than magnetite and wide distributionIt is one of the most important raw materials for the extraction of iron Its composition is complex In addition to containing a small amount of magnetite, the impurity embedding of haematite has uneven particle size and high content of How to Extract Iron from Hematite: Methods and Plants2015年7月1日 Aggregation behaviour was observed within pH 3–45 for synthetic iron oxide NPs with a maximum particle size reading of 1398 ± 1173 dnm, while for natural iron oxide nano colloids, the Synthesis, Characterization and Applications of Iron Oxide 2024年4月26日 The final stage in iron ore processing is ironmaking, where the iron ore is transformed into molten iron through a process called reduction The most common method of ironmaking is the blast furnace route In a blast furnace, iron ore, coke (carbon), and fluxes (limestone or dolomite) are loaded into the furnace from the topIron Ore Processing: From Extraction to Manufacturing

(PDF) Flotation of Iron Ores: A Review ResearchGate
2019年11月19日 PDF A tremendous amount of research has been done on refining the flotation process for iron ore and designing the reagents which go into it This Find, read and cite all the research you 2017年2月16日 PDF Sintering is a thermal agglomeration process that is applied to a mixture of iron ore fines, recycled ironmaking products, fluxes, slagforming Find, read and cite all the research you (PDF) Iron Ore Sintering: Process ResearchGateDRI, also known as Sponge Iron, is the product of the direct redu or other ironction of iron orebearing materials while in the solid state, ie without melting, using “reducing agents” carbon monoxide and hydrogen, derived from reformed natural gas, syngas or coal It is a porous iron material which, due to itsHot Briquetted Iron (HBI): A Guide to Shipping, Handling Storage2022年1月23日 Beside the processing behaviour of the main constituents of bauxite such as hydrated alumina and silica minerals, the Chapter covers the impact of other constituents, such as titania, iron (PDF) Chemical Processing of Bauxite: Alumina and Silica Minerals
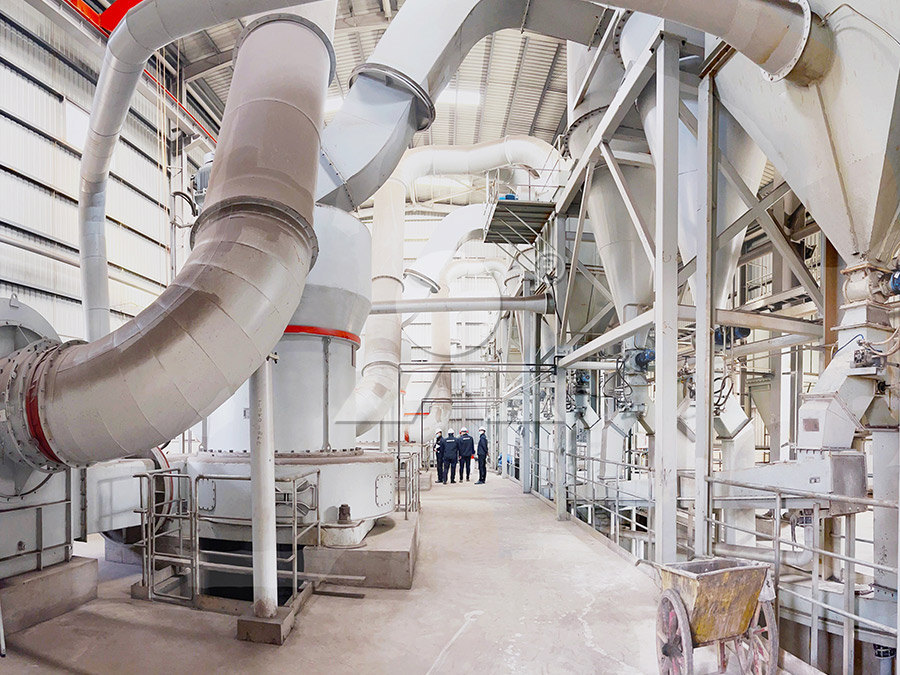
Spheroidization of Iron Powders by Radiative Heat Transfer
processing iron or other iron alloy powders however, this process can be easily adapted to produce larger quantities of material without significant changes in equipment configuration Thesis Supervisor: Thomas W Eagar Heganas, Sweden, and consists of the reduction of iron oxide, in particular, the reduction of iron ore by carbon2008年1月1日 Supercritical fluids possess unique characteristics that make them effective and environmentally friendly processing media for nanomaterials Of the nanomaterials of widespread applicative Processing of iron oxide nanoparticles by supercritical fluids2022年5月1日 Iron oxide nanoparticles are becoming progressively significant for the improvement of innovative biomedical and nanotechnology requests The keywords iron oxide nanoparticles, Fe 3 O 4 nanoparticles and magnetite nanoparticles have been utilized as a research object in the gross database of articles from the Web of Science The results of these Iron oxide nanoparticles: Preparation methods, functions, It is one of the three main oxides of iron, the other two being iron(II) oxide (FeO) the rarer form, and iron(II,III) oxide (Fe3O4) which naturally as magnetite DrugBank See also : Ferric cation (has active moiety); Ferric oxide red; sloe (component of); Ferric Oxide Red; Zinc Oxide (component of) Ferric Oxide Red Fe2O3 CID PubChem
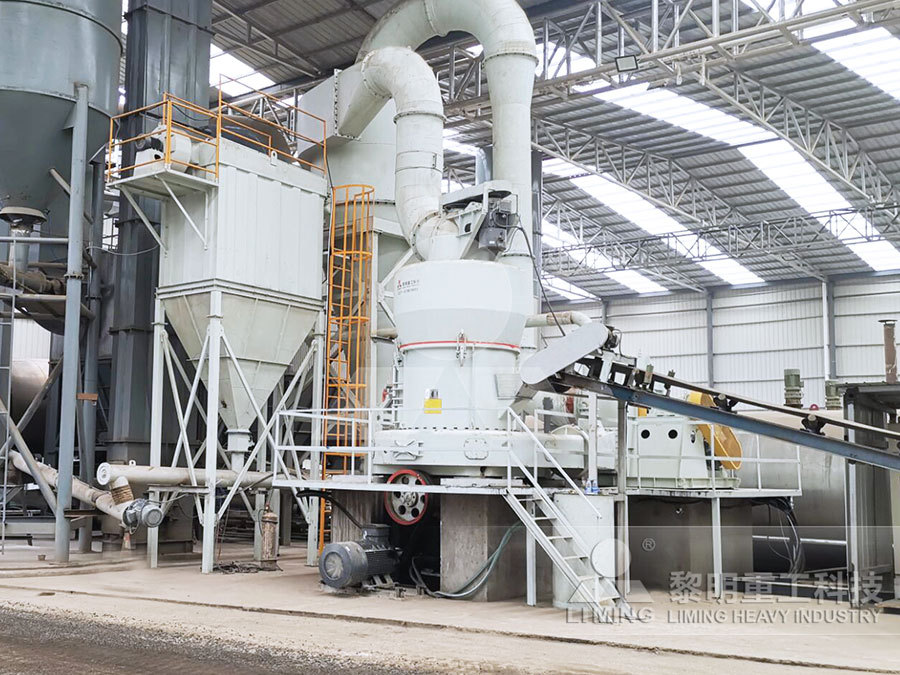
Granulating Iron Oxide Pigments for Use in Concrete
Iron oxide can be either natural or synthetic and as such, may be produced for use as a pigment in a variety of ways Some pigments may even utilize a blend of both natural and synthetic sources of iron oxide Natural Iron Oxide Natural iron oxides have long been used as a pigment, of which prehistoric cave paintings are a prime exampleIron residue may also be transferred to Stainless steel surfaces from materials which were previously used on steel or iron parts This includes blasting, grinding, and polishing abrasives; the iron parts they were previously used on may be the containers or the systems used to handle the abrasives, such as blasting cabinetsIron Residue / Contamination on Stainless Steel SurfacesThe term oxidation was first used to describe reactions in which metals react with oxygen in air to produce metal oxides When iron is exposed to air in the presence of water, for example, the iron turns to rust—an iron oxide When 45: OxidationReduction (Redox) Reactions2023年4月7日 Through the above process, the magnetite processing plant can obtain more than 65% of highquality iron ore concentrate, and the recovery rate is as high as 80% Of course, the specific beneficiation process needs to be How to Recover Iron from Magnetite: 4 Methods and
.jpg)
Extraction of iron IGCSE Chemistry Revision Notes
2024年11月4日 Carbon monoxide reduces the iron(III) oxide in the iron ore to form iron This will melt and collect at the bottom of the furnace, where it is tapped off iron(III) oxide + carbon monoxide → iron + carbon dioxide Limestone DIY InHouse black oxide finishing continues to grow in popularity With many reasons why inhouse blackening of iron, steel, and stainless steel is more attractive than sending parts out to a plater, they all come down to one simple concept: more effective control of quality, scheduling and costsSpecifically, manufacturers need faster turnaround on part finishing to satisfy customers DIY Black Oxide Coating And Finishing Birchwood Technologies2020年3月19日 Production of Iron Oxide Nanoparticles by CoPrecipitation method with Optimization Studies of Processing Temperature, pH and Stirring Rate(PDF) Production of Iron Oxide Nanoparticles by Co2017年6月21日 Iron is currently produced by carbothermic reduction of oxide ores This is a multiplestage process that requires largescale equipment and high capital investment, and produces large amounts of CO2(PDF) Hydrogen Plasma Processing of Iron Ore ResearchGate
.jpg)
Mitigating iron foulants in refinery processes DigitalRefining
Their decomposition temperature is >300°C At 282°C, iron acetate decomposes iron carbonate to form iron oxide (FeO) Once decomposed to iron oxide, abundant sulphur in the hydroprocessing allows for the generation of FeS As Figure 1 shows, these types of precipitation result in a beautiful, crystallographic agglomeration of iron sulphideNinetyeight percent of iron ore mined goes into producing steel, the world’s most common metal By definition, steel is the element iron (99%) combined with carbon (1%) The iron in iron ore comes from iron oxides found in deposits such as massive hematite (the most commonly mined), magnetite, titanomagnetite, and pisolitic ironstoneIron Ore: From Mining to Processing to Dust ControlFor instance, Fe 3 O 4 is a mixed iron oxide with Fe in different oxidation states as Fe 2 + and Fe 3 +Due to the flexible oxidation state of Fe, iron oxides can assume different phases and singlecrystalline structures with very different chemical and physical properties (cf Table 1 for an overview) This flexibility of their oxidation state makes iron oxides very interesting to be used Iron Oxide an overview ScienceDirect Topics2016年5月9日 Iron scale and foreign iron particles are also removed by the magnetic separator Summary of the Silica Sand Processing Plant Equipment In general most silica sands can be beneficiated to acceptable specifications by the flowsheet illustrated Reagent cost for flotation is low, being in the order of 5 to 10 cents per ton of sand treatedSilica Sand Processing Sand Washing Plant Equipment
.jpg)
How to Combat Iron Oxide in Hydronic HVAC Systems Heat Transfer
Air in a hydronic HVAC system can be a problem, specifically when it comes to the development of corrosive iron oxide When system components, like pump volutes or expansion tanks, made of cast iron or steel are mixed with oxygen and water, corrosive iron oxide is formed2021年5月18日 21 Iron (III) Oxides Iron (III) oxide is, of course, a compound that exhibits four different crystalline polymorphs: αFe 2 O 3, βFe 2 O 3, γFe 2 O 3, and εFe 2 O 3Hematite and maghemite usually appear in nature, while beta and epsilon structures are generally synthetic oxides [10, 11]In general, the iron (III) oxides anions arrange in closepacked structures, Synthesis, Properties, and Applications of Iron Oxides: Versatility Before diving into the details of the process, let's first clarify what black oxide actually is Black oxide is a conversion coating used to blacken ferrous metals, such as steel or iron It creates a layer of black iron oxide on the surface, providing both aesthetic appeal and corrosion resistance 12 How Does the Black Oxide Process Work?The Ultimate Guide to the Black Oxide Process: Enhancing Metal Transfer into storage 6 Construction materials for storage 18 and handling Unsuitable materials Suitable materials Aluminium and its alloys Austenitic stainless steel Plastic tanks Other nonmetals Lubricants Pumps Valves Gaskets 7 Personnel safety instructions 22 Personnel protection Equipment First aid 8 Some common types of incidents 23HYDROGEN PEROXIDE HANDLING STORAGE Utah State

Direct Reduced Iron ByProduct Fines (DRI D): A Guide to
iron ore burden is such that the ascending column of g ases interfaces with the maximum surface area of the iron ore the higher the content of iron ore fines in the feedstock, the lower the permeability of the burden The iron ore feedstock (pellets and lump ore) is therefore screened to remove fines before being charged to the furnace2018年5月1日 Iron oxide bearing wastes (IOBS) are produced at every part of processing stage of sinter, molten iron and steel production They are hard to handle and in many cases are stockpiled only to be a Factors Affecting Ballability of Mixture Iron Ore Concentrates and Iron Iron Oxide Processing Systems Iron oxide, also known as ferric oxide, is an inorganic compound with the formula Fe 2 O 3 It is one of the three main oxides of iron, and occurs naturally as the mineral hematite It is the main source of iron in the steel industry Iron oxide is ferromagnetic, meaning it is attracted to magnetic sources, and is Iron Oxide Drying Processing The ONIX Corporation2023年2月15日 Hematite, also spelled haematite, is a weakly magnetic iron ore with better floatability than magnetite and wide distributionIt is one of the most important raw materials for the extraction of iron Its composition is complex In addition to containing a small amount of magnetite, the impurity embedding of haematite has uneven particle size and high content of How to Extract Iron from Hematite: Methods and Plants
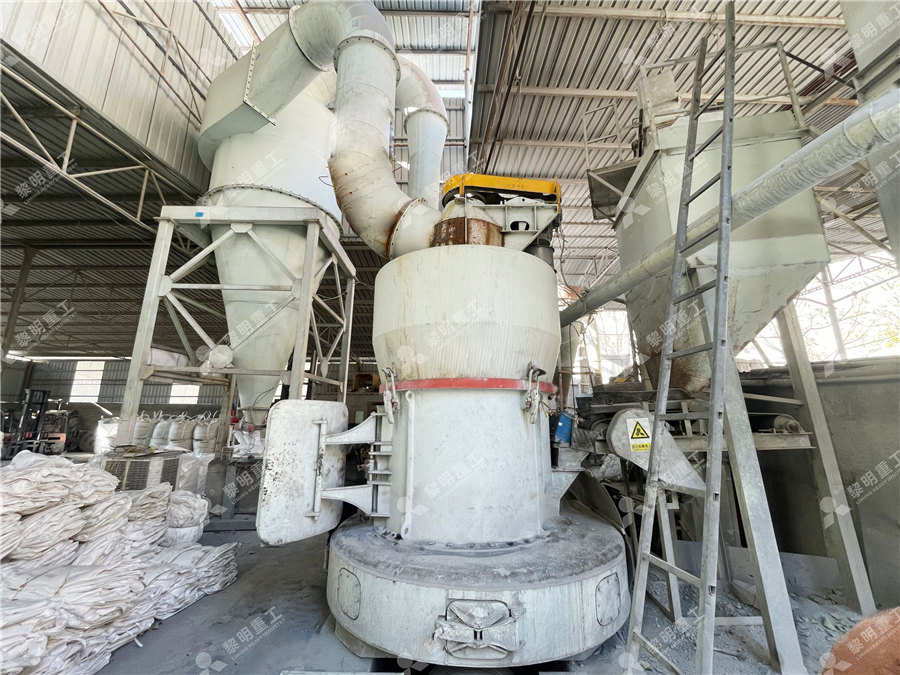
Synthesis, Characterization and Applications of Iron Oxide
2015年7月1日 Aggregation behaviour was observed within pH 3–45 for synthetic iron oxide NPs with a maximum particle size reading of 1398 ± 1173 dnm, while for natural iron oxide nano colloids, the 2024年4月26日 The final stage in iron ore processing is ironmaking, where the iron ore is transformed into molten iron through a process called reduction The most common method of ironmaking is the blast furnace route In a blast furnace, iron ore, coke (carbon), and fluxes (limestone or dolomite) are loaded into the furnace from the topIron Ore Processing: From Extraction to Manufacturing