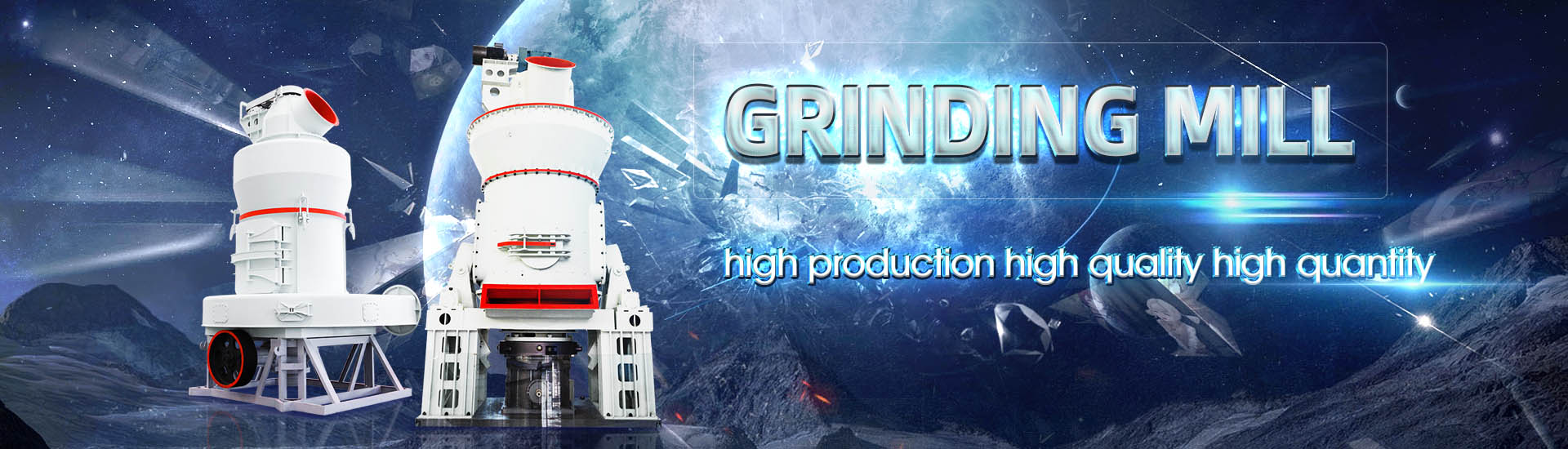
HOME→RM100 2 0 electrolytic aluminum waste slag grinding machine calcium carbonate powder grinding gypsum crushing system
RM100 2 0 electrolytic aluminum waste slag grinding machine calcium carbonate powder grinding gypsum crushing system
.jpg)
Efficient lithium recovery from electrolytic aluminum slag via an
2024年2月1日 This paper proposes a method for recovering Li from the slag using AlCl 3 as the leaching agent The effects of the leaching temperature, AlCl 3 concentration, pH, and solidtoliquid ratio (S/L) on the leaching efficiency of Li + were systematically examined2023年4月25日 This article analyzes and summarizes the composition and hazards of the overhaul slag and the current development status of domestic and international electrolytic aluminum overhaul slag disposal, and points out the development direction of hazardous waste disposal in China's electrolytic aluminum industryResearch Progress of Electrolytic Aluminum Overhaul Slag Disposal2023年10月1日 A cleaner and efficient process was proposed to recover LiF and Al 2 (SO 4) 3 from the waste cryolite electrolyte Under the optimum sulfated roasting conditions, 8755% of Li and 3030% of Al were leached The obtained cryolite residue with a low molecular ratio could be returned to the aluminum electrolysis systemEfficient extraction and recovery of lithium from waste aluminum 2020年8月1日 Here, we discuss the influence of different processing parameters on electrolytic refining of aluminum alloy and investigate the mechanism of extracting Al from coarse AlSi alloy in a lowtemperature molten salt system Aluminum is obtained with the use of coarse AlSi alloy as a soluble anode in the AlCl 3NaClKClRecovery of aluminum from waste aluminum alloy by low
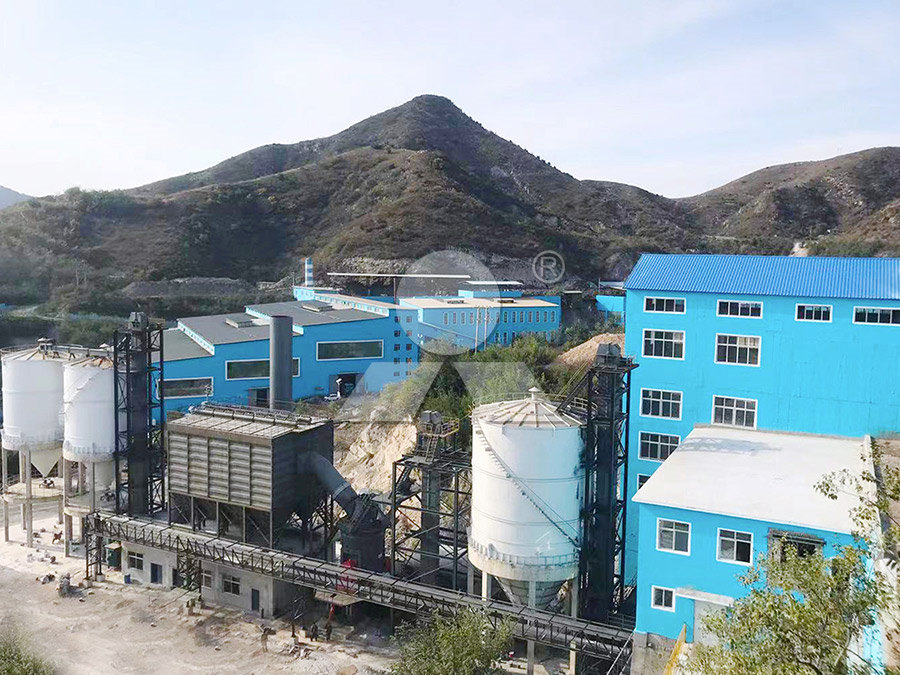
The recycling of carbonrich solid wastes from aluminum
2024年5月23日 Here, we review carbonrich solid wastes with focus on sources and hazards, detoxification, separation, recovery, recycling and disposal Treatment techniques include roasting, calcination, vacuum distillation, flotation, water leaching, acid leaching, alkali leaching, complexation leaching, and alkali fusion2023年9月1日 This study employed hydrometallurgical processes to selectively leach lithium from Licontaining aluminum electrolyte slag, using sodium carbonate solution as the leaching agent A notable leaching efficiency of 9912% is yielded for lithium, with minimal leaching observed for other elements such as calcium (Ca) and aluminum (Al)Clean Process for Selective Recovery of Lithium Carbonate from 2022年10月10日 In this work, electrolytic aluminum carbon anode slag was separated by flotation Using the selectivity index ( SI ) as an indicator, the influencing factors of the carbon slag flotationRecovery of carbon and cryolite from spent carbon anode slag of 2012年12月31日 The main mineral components of waste cathode carbon include sodium fluoride, cryolite, calcium fluoride, silicate minerals and so on, therein the fluorine content is about 986%, and the content Study on Harmless and Resources Recovery
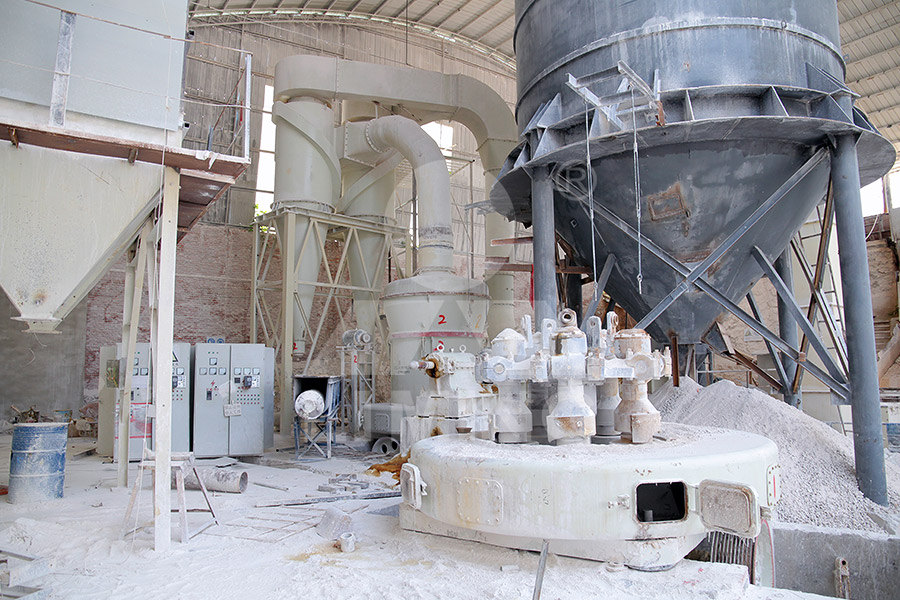
Ultimate Guide – Aluminum Fabrication, Grinding,
2021年6月16日 Aluminum and aluminum alloys are among the most used metals in fabrication,construction, and in the creation of good all around you It is such a useful and versatile metal, but there are some special 2022年5月1日 Most widely used acidic agents could react with these carbonates and release CO2 before they were recarbonated After the leaching step, alkaline reagents (eg, NH4OH, NaOH) are introduced to Preparation of calcium carbonate nanoparticles from waste carbide slag 2022年10月9日 1 Department of Mining Engineering, Shanxi Institute of Technology, Yangquan, China; 2 Department of Mining Engineering, Balochistan University of Information Technology, Engineering and Management Sciences (BUITEMS), Quetta, Pakistan; One of the main electrolytic aluminum production costs is the consumption of carbon anodes, and carbon Recovery of carbon and cryolite from spent carbon anode slag of 2023年3月12日 Recovery of Carbon and Cryolite from Spent Carbon Anode Slag Using a Grinding Flotation Process Based on unavoidable solid waste in the electrolytic aluminum industry, which 02 5 – 0 (PDF) Recovery of Carbon and Cryolite from Spent Carbon Anode Slag
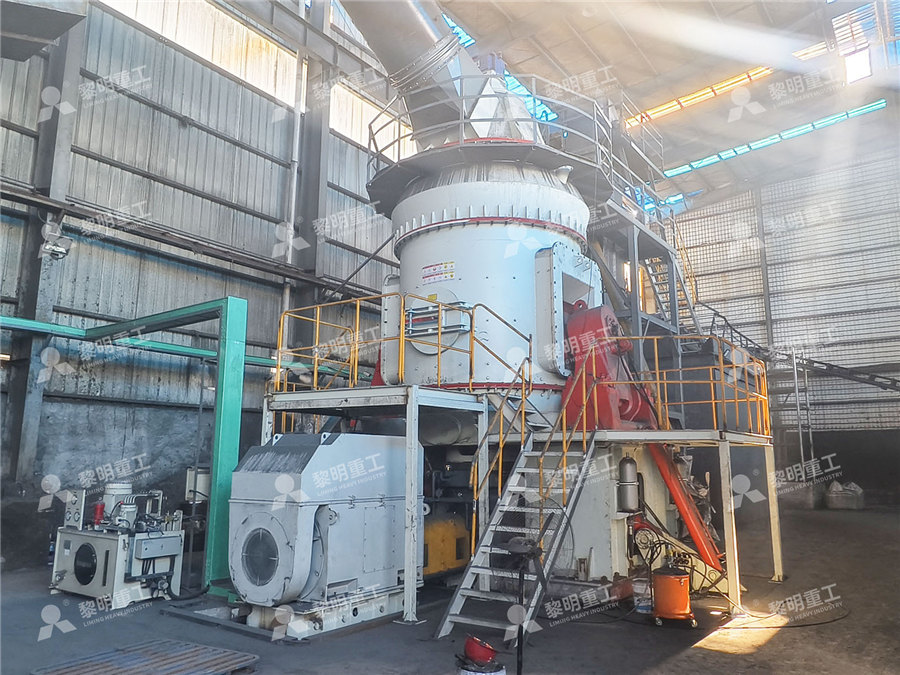
The recycling of carbonrich solid wastes from aluminum electrolytic
2024年5月23日 The main components include carbon, calcium fluoride (CaF 2), magnesium fluoride (MgF 2), aluminum fluoride (AlF 3), aluminum oxide (Al 2 O 3), and cryolitetype compounds such as cryolite (Na 3 AlF 6), simmonsite (LiNa 2 AlF 6), chiolite (Na 5 Al 3 F 14), elpasolite (K 2 NaAlF 6); the carbon content is 14–42% and the fluoride content is above 60% 2023年10月1日 The main components of waste aluminum cryolite electrolyte are cryolite (Na 3 AlF 6), potassium cryolite (K 2 NaAlF 6), lithium cryolite (Na 2 LiAlF 6), fluorite (CaF 2), and approximately 2% carbon black (Wang et al, 2019)The main treatment methods of waste aluminum cryolite electrolyte can be divided into two categories: combined thermalwet Efficient extraction and recovery of lithium from waste aluminum 2023年3月12日 Aluminum has a variety of uses in the building, transportation, electric power, packaging, national security, and hightech industries due to its unique chemical and physical properties []Cryolitealumina molten salt electrolysis is mainly applied in modern industrial aluminum production [2,3]As the aluminum production process continues, a large amount of Recovery of Carbon and Cryolite from Spent Carbon Anode Slag2023年9月1日 Lithium (Li)bearing aluminum electrolyte slag is an inevitable byproduct of the aluminum industry, and improper disposal or stacking it may lead to potential environmental hazards This study employed hydrometallurgical processes to selectively leach lithium from Licontaining aluminum electrolyte slag, using sodium carbonate solution as the leaching agent Clean Process for Selective Recovery of Lithium Carbonate from Waste
.jpg)
Research on the Coprocessing of Mixed Electrolytic Aluminum Waste
Research on the Coprocessing of Mixed Electrolytic Aluminum Waste in Circulating Fluidized Bed Test system 213 Blending electrolytic aluminum scrap, as follows: Table 1 Comparison table of four experimental conditions Blending ratio Calcium carbonate/g Condition 1 5:5 0 Condition 2 7:3 0 Condition 3 :7 0 Condition 4 7 : Whether soft rock, hard rock, nonmetallic minerals, or coal, FTM Machinery can provide costeffective grinding solutions Our powder milling machines are particularly suitable for producing clean coal powder, limestone powder, Powder Grinding Mills Engineered by FTM Fote 2024年5月23日 The aluminum electrolysis industry continually and unavoidably produces hazardous solid waste in the form of carbon anode slag Carbon anode slag poses a serious environmental pollution risk, and The recycling of carbonrich solid wastes from aluminum electrolytic 2024年1月23日 Initial Investment: Grinding machines, especially those used for precision applications, are costly Highend machines with advanced features like CNC systems are even more expensive Basic Grinding Machines: Entrylevel What is Grinding: Definition, Process, Types
.jpg)
Intelligent process control system for predicting operating
2024年1月31日 This study develops an intelligent datadriven approach for optimising slag grinding systems Slag grinding exhibits complex nonlinear 09 / 5Year Impact Factor: 13 Intelligent process control system for predicting operating conditions of slag grinding machines: a data mining approach for improved efficiency 2022年1月10日 Selective comminution and grinding mechanisms of spent carbon anode from aluminum electrolysis using ball and rod mills January 2022 Physicochemical Problems of Mineral Processing 58(3):Selective comminution and grinding mechanisms of spent carbon What Is Grinding Slag Removal? Slag is a specific type of sand that’s traditionally made from steel It often forms as a coarse waste product resulting from deburring or smelting processes To remove slag, metal processing facilities require grinding and slag removal Slag grinding processes efficiently remove all of the heavy slag produced Grinding Slag Removal Apex Machine GroupJune 2022; ARCHIVE Proceedings of the Institution of Mechanical Engineers Part C Journal of Mechanical Engineering Science 19891996 (vols 203210) 236(2):1107(PDF) A comprehensive review on the grinding process:
.jpg)
Resource utilization of solid waste carbide slag: a brief review of
Formation of calcium carbide The calcium carbide production technology in the industry was invented in 1892 Its production principle is that calcium oxide and coke react at a high temperature above 2000 °C generated by an arc to produce molten calcium carbide (CaC 2)This process is called the electrothermal method or arc method [] that is shown in EqRecycled ceramic tiles were prepared from electrolytic manganese slag( EM) and waste ceramic grinding fine powder( GP) The optimal mix proportion and firing system of the preparation of recycling ceramic tile were investigated with compressive strength,water absorption,porosity and bulk density as the main analysis indexes The effect of firing system on properties of ceramic Preparation of Recycled Ceramic Tiles by Using Electrolytic Stedman impact crushers, mills, and grinders are used in nearly every mineral, ore, and mining applicationWhether you are processing iron ore, coal, rock, salt, wood chips, or clay – to name a few – we have your solution to size reduction with our mineral crushing machines industrial ore slag crushersIndustrial Ore, Mineral, Slag Crusher Mineral Crushing Machines Calcium Carbonate (GCC industry achieves the highest quality available in the market by coating in a fully optimized Contraplex pin mill system with feed powder heating and top cut separations Superfine powders in the range d97 = 3 Calcium Carbonate (GCC) Hosokawa Alpine
.jpg)
A novel approach for lithium recovery from waste lithium
2021年10月1日 When CO 3 2− irons are added, it first reacts with Ca 2+ to form CaCO 3 but does not react with Li + (CaCO 3: K sp = 28 × 10 −9, Li 2 CO 3: K sp = 25 × 10 −2, 25 °C) (Li et al, 2014) After CaCO 3 precipitation, the solid phase and microstructure of the precipitation were observed from the XRD pattern and scanning electron micrograph2022年10月10日 221 Grinding experiments The grinding tests were conducted under dry conditions using a QM5 laboratoryscale ball mill (Changsha Tianchuang Powder Technology Co, Ltd Changsha, China) equipped with a 20 L stainless steel cylinder (Diameter 125 cm and length 160 cm) A total of 222 kg of stainless steel balls were used as milling mediaRecovery of carbon and cryolite from spent carbon anode slag of 2023年8月1日 The overhaul slag from the aluminum reduction cell is a hazardous waste The annual production of overhaul slag is above one million tons in China [1]The overhaul slag mainly consists of spent impervious materials and refractory bricks [2], [3]A large number of hazardous substances, such as fluorides and cyanides, are included in the overhaul slag [4]Dissolution behavior of overhaul slag from aluminum reduction 2022年12月12日 Calcium carbide slag is a waste slag produced after the hydrolysis of calcium carbide to obtain acetylene gas, with very fine particles, offwhite color due to the presence of trace carbon and sulfur impurities, slightly odorous, with Ca(OH) 2 as the main component, and a slag liquid pH value of 12 or more, thus often causing serious pollution to the environment [18]Comprehensive performance study of aluminum ash and calcium

Synergistic use of electrolytic manganese residue and barium slag
2022年4月4日 Electrolytic manganese residue (EMR) and barium slag (BS) are important industrial solid wastes EMR is a byproduct of the electrolytic manganesemetal process, which is produced by acid leaching, neutralization, and pressure filtration of manganese carbonate powder [1], [2]BS is a solid waste produced in the process of preparing barium salt from barite 2021年8月27日 The grinding wheel is the most important and unique part of the electrochemical grinding machine It is connected to the negative terminal of the power supply and acts as the cathode The grinding wheel is made of insulating materials such as diamond and aluminum oxide The wheels rotate and increase the flow of the electrolyteElectrochemical Grinding: Definition, Parts or Construction, 2021年10月6日 119 0725 0529 0491 0363 0322 0302 0229 Based on the results of the qualitative analysis, a subsequent quantitative analysis was carried out to obtain an accurate chemical compositionResearch on the Preparation Parameters and Basic Properties of RM 70GO! 20; RM 90GO! RM 100GO! RM 120X; RM V550GO! RM J110X; Screen units RM HS pre Weighing in at only 29 t when empty this is a particularly highcapacity machine which can crush up to The dieselelectric drive system reduces operating costs by up to 30% and the optimised impact plate geometry ensures not only high throughput but RM 100GO! RUBBLE MASTER Mobile Crushers
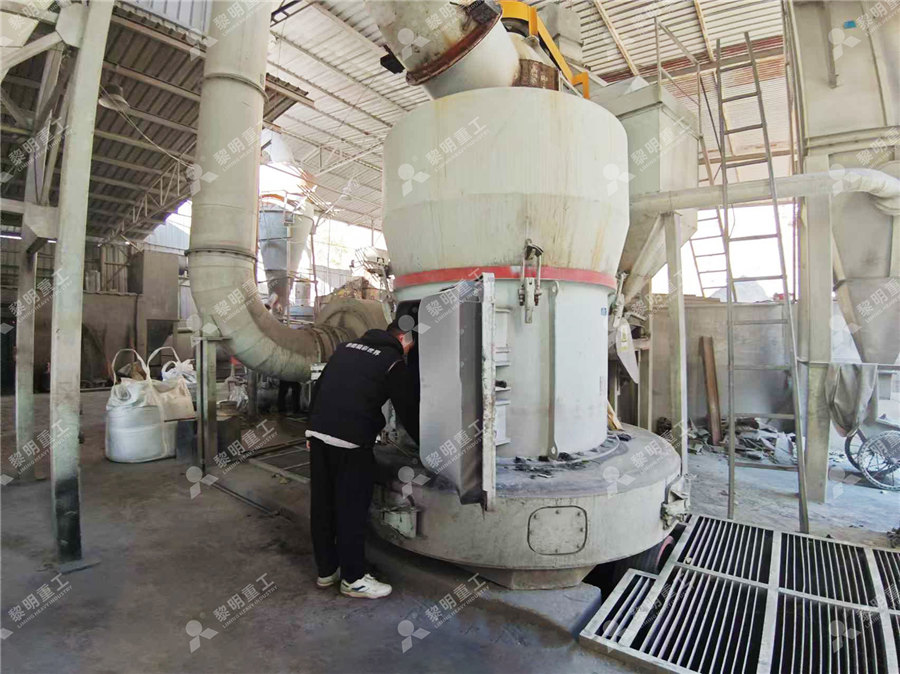
A novel approach for extracting lithium from overhaul slag by low
2024年2月1日 Lithium is the lightest alkali metal with interesting chemical properties such as electrochemical activity and high redox potential, and is an important energy storage in modern society [1], [2]Lithium is widely used in battery manufacturing, glass and ceramics, medicine and aluminum smelting [3], [4]At the same time, lithium as a strategic metal, the demand is 2012年12月31日 The main mineral components of waste cathode carbon include sodium fluoride, cryolite, calcium fluoride, silicate minerals and so on, therein the fluorine content is about 986%, and the content Study on Harmless and Resources Recovery 2021年6月16日 Aluminum and aluminum alloys are among the most used metals in fabrication,construction, and in the creation of good all around you It is such a useful and versatile metal, but there are some special Ultimate Guide – Aluminum Fabrication, Grinding, 2022年5月1日 Most widely used acidic agents could react with these carbonates and release CO2 before they were recarbonated After the leaching step, alkaline reagents (eg, NH4OH, NaOH) are introduced to Preparation of calcium carbonate nanoparticles from waste carbide slag
.jpg)
Recovery of carbon and cryolite from spent carbon anode slag of
2022年10月9日 1 Department of Mining Engineering, Shanxi Institute of Technology, Yangquan, China; 2 Department of Mining Engineering, Balochistan University of Information Technology, Engineering and Management Sciences (BUITEMS), Quetta, Pakistan; One of the main electrolytic aluminum production costs is the consumption of carbon anodes, and carbon 2023年3月12日 Recovery of Carbon and Cryolite from Spent Carbon Anode Slag Using a Grinding Flotation Process Based on unavoidable solid waste in the electrolytic aluminum industry, which 02 5 – 0 (PDF) Recovery of Carbon and Cryolite from Spent Carbon Anode Slag 2024年5月23日 The main components include carbon, calcium fluoride (CaF 2), magnesium fluoride (MgF 2), aluminum fluoride (AlF 3), aluminum oxide (Al 2 O 3), and cryolitetype compounds such as cryolite (Na 3 AlF 6), simmonsite (LiNa 2 AlF 6), chiolite (Na 5 Al 3 F 14), elpasolite (K 2 NaAlF 6); the carbon content is 14–42% and the fluoride content is above 60% The recycling of carbonrich solid wastes from aluminum electrolytic 2023年10月1日 The main components of waste aluminum cryolite electrolyte are cryolite (Na 3 AlF 6), potassium cryolite (K 2 NaAlF 6), lithium cryolite (Na 2 LiAlF 6), fluorite (CaF 2), and approximately 2% carbon black (Wang et al, 2019)The main treatment methods of waste aluminum cryolite electrolyte can be divided into two categories: combined thermalwet Efficient extraction and recovery of lithium from waste aluminum
.jpg)
Recovery of Carbon and Cryolite from Spent Carbon Anode Slag
2023年3月12日 Aluminum has a variety of uses in the building, transportation, electric power, packaging, national security, and hightech industries due to its unique chemical and physical properties []Cryolitealumina molten salt electrolysis is mainly applied in modern industrial aluminum production [2,3]As the aluminum production process continues, a large amount of 2023年9月1日 Lithium (Li)bearing aluminum electrolyte slag is an inevitable byproduct of the aluminum industry, and improper disposal or stacking it may lead to potential environmental hazards This study employed hydrometallurgical processes to selectively leach lithium from Licontaining aluminum electrolyte slag, using sodium carbonate solution as the leaching agent Clean Process for Selective Recovery of Lithium Carbonate from Waste Research on the Coprocessing of Mixed Electrolytic Aluminum Waste in Circulating Fluidized Bed Test system 213 Blending electrolytic aluminum scrap, as follows: Table 1 Comparison table of four experimental conditions Blending ratio Calcium carbonate/g Condition 1 5:5 0 Condition 2 7:3 0 Condition 3 :7 0 Condition 4 7 : Research on the Coprocessing of Mixed Electrolytic Aluminum Waste