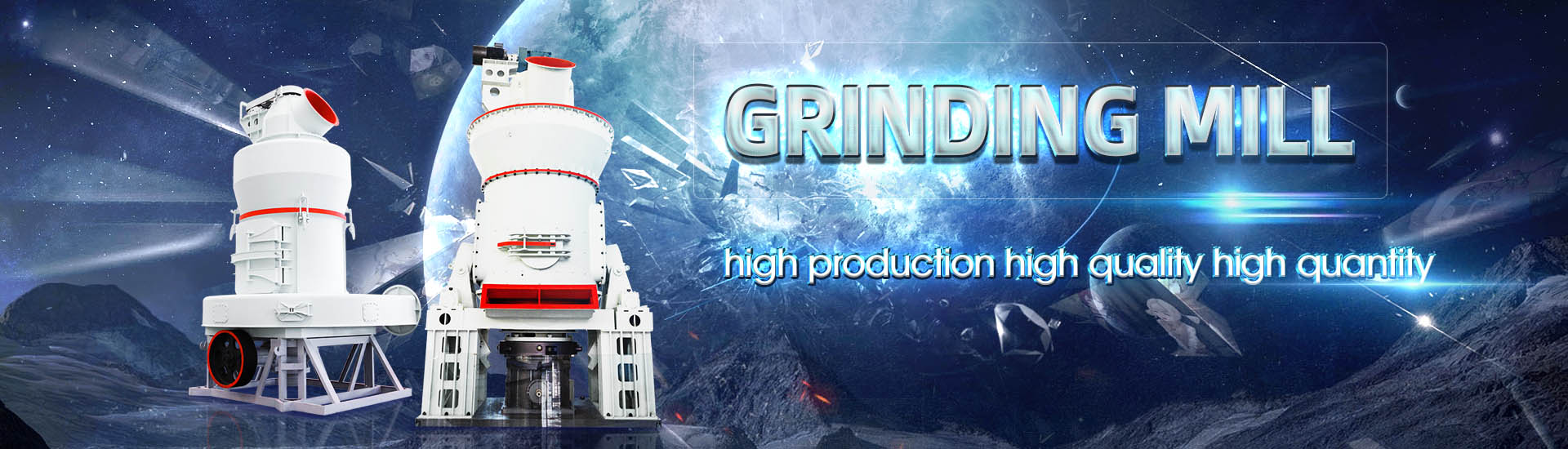
Lithium carbonate processing and milling
.jpg)
Lithium processing technology Complete solutions that FLSmidth
Impurity removal from the salar brine is a critical step in the process flowsheet for production of batterygrade lithium Our MaxRTM technology provides the most advanced method in the industry, combining precipitation reactors with solidliquid separation, which allows the seeding Hosokawa’s Air Classifying Mills are a proven technology for processing lithium materials for nearly 20 years The ACM also has numerous applications with food, pharmaceutical, mineral, chemical and cosmetic materialsLithium Carbonate Milling Hosokawa Micron Powder Bepex has been supplying processing technology for lithium carbonate or lithium hydroxide production since the early 1990s Now, with lithium producers straining to fulfill ever increasing demand, Bepex is pioneering systems to streamline Lithium Processing Systems and Equipment BepexSGS Minerals Services has experience with complete flowsheet development to recover high grade lithium products from hard rock lithium minerals SGS offers a multidisciplinary team Hard Rock Lithium Processing SGS
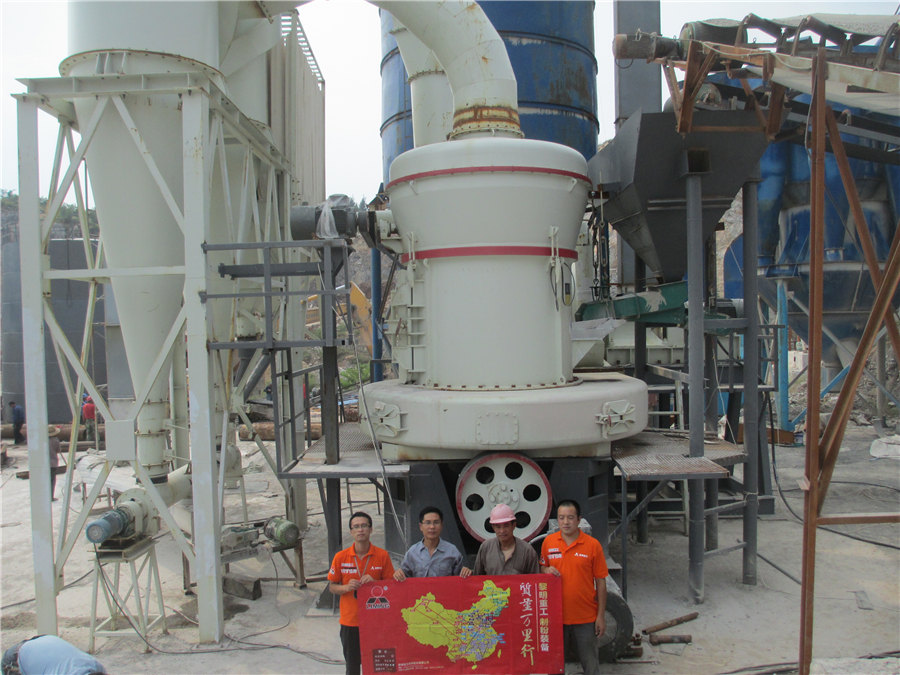
Process analysis and study of factors affecting the lithium
2021年2月1日 Lithium carbonate is the primary product of the lithium extraction process and is an important compound for the battery making industry A major step in the conventional 2019年8月23日 When the lithium chloride reaches optimum concentration, the liquid is pumped to a recovery plant and treated with soda ash, precipitating lithium carbonate, which is then Lithium Processing Equipment, Process Flow, Cases JXSC Machine2023年1月1日 Therefore, this paper presents a comparative life cycle assessment (LCA) to quantify the environmental impact of selected lithium production routes: brine (Chile), Comparative Life Cycle Assessment of Lithium Mining, Extraction, 2024年8月15日 The process flow of the lithium carbonate production from sedimentary deposits can be generalised into three stages: mining, mineral processing (ie, comminution and Life cycle assessment of lithium carbonate production: Comparing
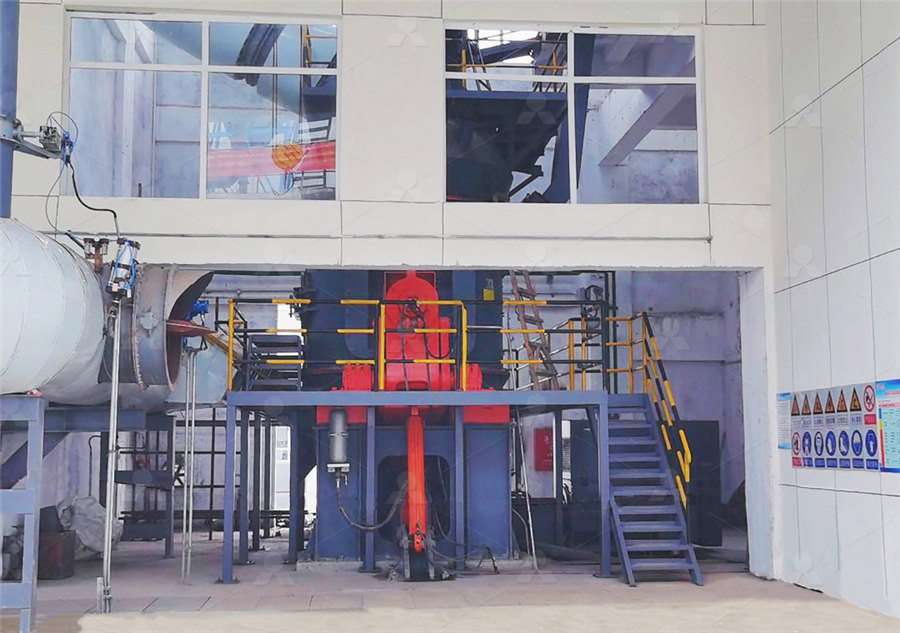
Processing Technology Cornish Lithium Plc
The process is undertaken at atmospheric pressure and modest temperature, followed by a series of impurity removal steps at progressively higher pH levels and the subsequent precipitation of lithium carbonate The process contrasts We have more than 20 years’ experience providing marketleading lithium processing solutions We have thousands of pyroprocessing references worldwide in the mining industry where Lithium processing technology FLSmidth2021年2月1日 In this study, the crystallization process of lithium carbonate is investigated thoroughly The effect of several operating parameters, including initial salt concentration, reaction However, after dry ball milling, the particle size is significantly reduced, and crystal surfaces become more porous and rougher due to the Process analysis and study of factors affecting the lithium carbonate At 31 December 2023, the Keliber project had an attributable (7982%) Mineral Resource of 158 Mt grading at 12% Lithium Oxide (Li 2 O), containing 471kt of lithium carbonate equivalent (LCE); and Mineral Reserves of 77 Mt grading at Lithium project SibanyeStillwater
.jpg)
Aspects of Spodumene Lithium Extraction Techniques
2024年9月30日 Lithium (Li), a leading cathode material in rechargeable Liion batteries, is vital to modern energy storage technology, establishing it as one of the most impactful and strategical elements Given the surge in the electric car 2021年2月1日 Request PDF Processing of lithium ores: Industrial technologies and case studies – A review Recently, there has been a steady increase in demand for lithium (Li) and its compounds Processing of lithium ores: Industrial technologies and case studies 2023年3月28日 Ballmilling is the process where powder particles are treated by repeated deformation, fracture, To transform the lithium compounds into carbonate in process 2, Universal and efficient extraction of lithium for lithiumion ores, including mineralogical and process testing facilities Engineering services Our fulltime engineering team o–er process flowsheet, plant layout and design to achieve bestpossible performance of your spodumene processing operation Calcining and Acid Roasting Crystallisation Leaching Impurity Removal Lithium Carbonate Milling and Lithium processing technology FLSmidth
.jpg)
Recovery of lithium carbonate by acid digestion and
2018年1月1日 Recently, an alternative process for extracting lithium from a lepidolite ore, constituted by mechanical activation and sulphuric acid digestion, avoiding the calcination step, was proposed and studied in detail (Vieceli et al, 2017b)The effects of several factors on the structural transformations of the mineral phases were evaluated in this study2023年12月11日 The recycling of cathode materials from spent lithiumion battery has attracted extensive attention, but few research have focused on spent blended cathode materials In reality, the blended materials of lithium iron phosphate and ternary are widely used in electric vehicles, so it is critical to design an effective recycling technique In this study, an efficient method for Hydrometallurgical recovery of lithium carbonate and iron 2023年5月27日 The role of ball milling in lithium ore processing is to break down the lithiumcontaining minerals and release the lithium ions into the solution This is achieved through the mechanical grinding of the ore, which helps to increase the surface area of the material, making it easier for the leaching solution to penetrate and dissolve the lithium ionsBall Milling in Lithium Ore Processing: A Comprehensive Guide2019年5月29日 The process allows the recovery of lithium but not the production of technical lithium hydroxide of lithium carbonate Another step, such as carbonation or electrodialysis is needed ( Figure 11 ) Concerning the lithium production from brines, the process revolves around concentrating the brines up to 6 wt% Li and removing the impurities one after the other ( Spodumene: The Lithium Market, Resources and Processes
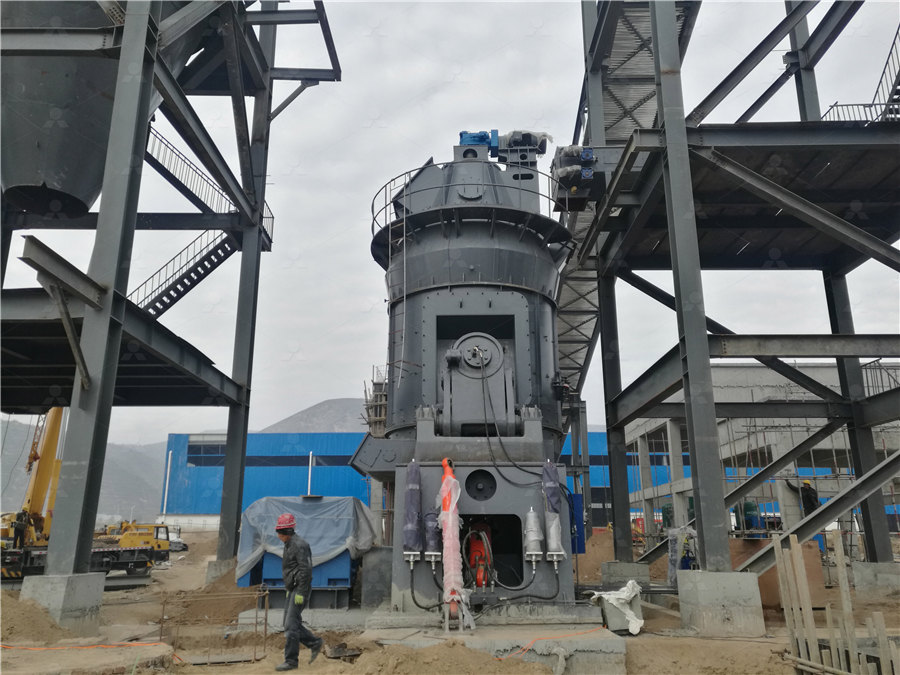
Earlystage recovery of lithium from spent batteries via CO
2024年7月29日 Schwich et al 18 investigated an effective ecofriendly “EarlyStage Lithium Recovery” (ESLR) method involving Li leaching through carbonation with supercritical CO 2 in a costintensive 2015年4月1日 PDF This paper examines the structural and particle size characteristics of lithium carbonate after mechanical processing in an AGO2 planetary (05 min) milling of lithium carbonate led toStructural and particle size characteristics of lithium 2018年8月21日 SepSol Partner, Sturtevant, successfully completed a milling application for lithium carbonate company in Argentina using their FCM Classifier Mill Skip to content OFFICE HOURS: Monday Friday 8:00 18:00 EST Lithium Carbonate Milling; Just One of Many Exciting 2021年9月28日 The lithium carbonate spot price has more than tripled in the past two years, from $6,000 a tonne to $20,000 a tonne for battery grade material We could be on the cusp of a massive new industry At current prices there are enormous profits to be had in the mining and production of lithium concentrates for chemicals or batteriesLithium Processing METS Engineering

Critical Review of Lithium Recovery Methods: Advancements
2024年10月10日 The integration of lithium into technological applications has profoundly influenced human development, particularly in energy storage systems like lithiumion batteries With global demand for lithium surging alongside technological advancements, the sustainable extraction and recovery of this critical material have become increasingly vital This paper 2022年2月2日 The financial and economic model developed for comprehensive processing of the tailings from Yaroslavsky GRK to obtain fluorite concentrate that can be used for producing fluorites by dry methods and other commercially successful products (lithium carbonate, potassium sulfate, rubidium and cesium formates, and aluminum sulfate) proved the Comprehensive Processing of Mica Concentrate from Yaroslavsky This can be great news or notso great news Until now, it has been not so great news Dealing with product size fines has added greatly to both CAPEX OPEX in the processing of lithium carbonate Processing lithium carbonate with a high percentage of product sized fines adds greatly to the energy cost of processing lithiumPreClassifying Before Milling or Micronizing LithiumWorking with the lithium concentrate, SGS’ team uses a standardized flowsheet to produce high grade lithium products such as lithium carbonate or lithium hydroxide These are reagents for the lithium battery industry The multistep process involves atmospheric leaching, liquidsolid separation and impurity removal via precipitation and ionHard Rock Lithium Processing SGS
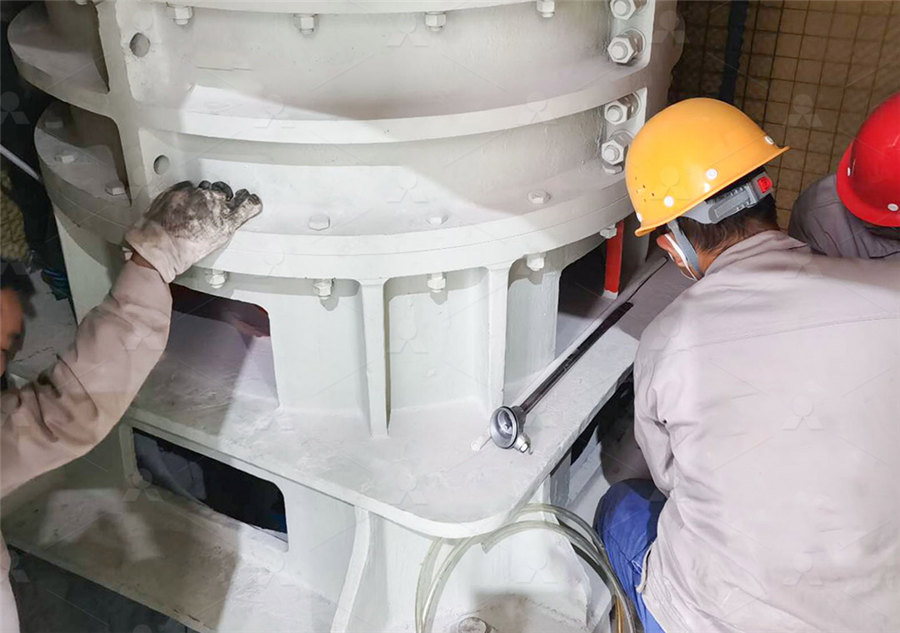
Lithium Processing Equipment, Process Flow, Cases JXSC
2019年8月23日 Mining for Lithium: Lithium is often recovered from brine, or water with a high concentration of lithium carbonate Subsurface brines trapped in the Earth’s crust are major source material for lithium carbonate These sources are less expensive to mine than from rock such as spodumene, petalite, and other lithiumbearing minerals2023年3月1日 Lithium carbonate with 995% purity was finally obtained by redissolving the Li 2 SO 4 crystals in water, followed by precipitation and washing (Sitando and Crouse, 2012) In the second route, CO 2 was used to adjust the pH value of the original pregnant leach solution from pH of about 13 to 68, shown by Eqs 18 – 19 in Table 14 ( Chen et al, 2011 ), before the Recent advances in lithium extraction from lithiumbearing clay 2017年10月1日 Request PDF Recovery of lithium carbonate by acid digestion and hydrometallurgical processing from mechanically activated lepidolite Lithium extraction from hardrock ores has regained Recovery of lithium carbonate by acid digestion and Impact Mill Grinding Process Material include: Lithium cobaltate (LCO), Li(OH), lithium manganate, lithium iron phosphate (LFP), ternary materials (NCM), lithium carbonate (Li 2 CO 3), lithium nickel cobalt manganate (NCM), lithium nickel Cathode Materials Processing Technology Lithium
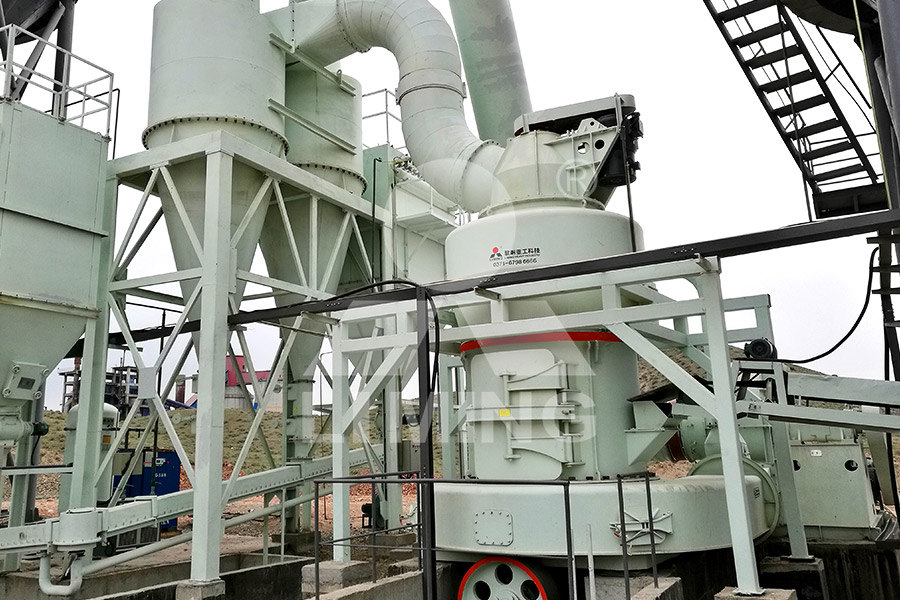
Enhancing lithium leaching by mechanical
2018年12月28日 Preparation of lithium carbonate from spodumene concentrate was carried out by a sodium carbonate autoclave process The ball millinginduced reduction of MoS2 by Al has been investigated2023年12月27日 In step 1, to convert spodumene into lithium sulfate (Li 2 SO 4), the raw ore is crushed and separated both mechanically and via floatationNext, the concentrate undergoes energy and chemically intensive hot acidroasting This process (as shown in Figure 1 below) sees concentrated spodumene powder roasted at 1050°C, cooled, mixed with sulfuric acid, Hard Rock Spodumene Lithium Processing Saltworks 2019年4月28日 The reactive crystallization of lithium carbonate (Li2CO3) from lithium sulfate (Li2SO4) and sodium carbonate (Na2CO3) solutions is a key process in harvesting solid lithium, whether from ores, brines, or clays However, the process kinetics and mechanism remain poorly understood and the modelling of the reactive crystallization of Li2CO3 is not available Hence, Mechanism and Modelling of Reactive Crystallization Process of Lithium 2023年6月29日 High lithium carbonate solubility processing, since lithium passes into slag during pyrometallurgical processing, and only metals such as Ni, Co, Mn, Cu, and their alloys are recovered [38]Lithium Production and Recovery Methods: Overview of Lithium
.jpg)
USA1 Process for producing lithium carbonate
Disclosed are methods for a simplified process for preparing lithium carbonate from concentrated lithium brine which can be used for battery grade, pharmaceutical and other high purity grade applications Impure lithium carbonate is precipitated from lithium concentrated brine, preferably lowered in magnesium, subsequently suspended in aqueous solution and reacted with carbon 2021年5月1日 Discovery and development of the richest brine and lacustrine deposits in South America revolutionized the lithium market due to a sharp reduction in the processing cost of this type of raw material into commercial lithium salts (in Processing of lithium ores: Industrial technologies and case 2024年9月23日 Lithium iron phosphate (LiFePO4, LFP) has long been a key player in the lithium battery industry for its exceptional stability, safety, and costeffectiveness as a cathode material Major car makers (eg, Tesla, Volkswagen, Ford, Toyota) have either incorporated or are considering the use of LFPbased batteries in their latest electric vehicle (EV) models Despite Status and prospects of lithium iron phosphate manufacturing in Lithium Titanate Oxide (LiTiO3); aka LTO as well as Lithium Carbonate, Li2CO3; aka LCO The beneficial properties of LTO LCO are directly related to its size and purity JP’s jet milling technology provides a distinct processing advantage using its dry, highpurity processing, with fine particle generation in the singleJet Milling’s Indispensable Value in Lithium Ion Batteries
.jpg)
Process analysis and study of factors affecting the lithium carbonate
2021年2月1日 In this study, the crystallization process of lithium carbonate is investigated thoroughly The effect of several operating parameters, including initial salt concentration, reaction However, after dry ball milling, the particle size is significantly reduced, and crystal surfaces become more porous and rougher due to the At 31 December 2023, the Keliber project had an attributable (7982%) Mineral Resource of 158 Mt grading at 12% Lithium Oxide (Li 2 O), containing 471kt of lithium carbonate equivalent (LCE); and Mineral Reserves of 77 Mt grading at Lithium project SibanyeStillwater2024年9月30日 Lithium (Li), a leading cathode material in rechargeable Liion batteries, is vital to modern energy storage technology, establishing it as one of the most impactful and strategical elements Given the surge in the electric car Aspects of Spodumene Lithium Extraction Techniques2021年2月1日 Request PDF Processing of lithium ores: Industrial technologies and case studies – A review Recently, there has been a steady increase in demand for lithium (Li) and its compounds Processing of lithium ores: Industrial technologies and case studies
.jpg)
Universal and efficient extraction of lithium for lithiumion
2023年3月28日 Ballmilling is the process where powder particles are treated by repeated deformation, fracture, To transform the lithium compounds into carbonate in process 2, ores, including mineralogical and process testing facilities Engineering services Our fulltime engineering team o–er process flowsheet, plant layout and design to achieve bestpossible performance of your spodumene processing operation Calcining and Acid Roasting Crystallisation Leaching Impurity Removal Lithium Carbonate Milling and Lithium processing technology FLSmidth2018年1月1日 Recently, an alternative process for extracting lithium from a lepidolite ore, constituted by mechanical activation and sulphuric acid digestion, avoiding the calcination step, was proposed and studied in detail (Vieceli et al, 2017b)The effects of several factors on the structural transformations of the mineral phases were evaluated in this studyRecovery of lithium carbonate by acid digestion and 2023年12月11日 The recycling of cathode materials from spent lithiumion battery has attracted extensive attention, but few research have focused on spent blended cathode materials In reality, the blended materials of lithium iron phosphate and ternary are widely used in electric vehicles, so it is critical to design an effective recycling technique In this study, an efficient method for Hydrometallurgical recovery of lithium carbonate and iron
.jpg)
Ball Milling in Lithium Ore Processing: A Comprehensive Guide
2023年5月27日 The role of ball milling in lithium ore processing is to break down the lithiumcontaining minerals and release the lithium ions into the solution This is achieved through the mechanical grinding of the ore, which helps to increase the surface area of the material, making it easier for the leaching solution to penetrate and dissolve the lithium ions2019年5月29日 The process allows the recovery of lithium but not the production of technical lithium hydroxide of lithium carbonate Another step, such as carbonation or electrodialysis is needed ( Figure 11 ) Concerning the lithium production from brines, the process revolves around concentrating the brines up to 6 wt% Li and removing the impurities one after the other ( Spodumene: The Lithium Market, Resources and Processes