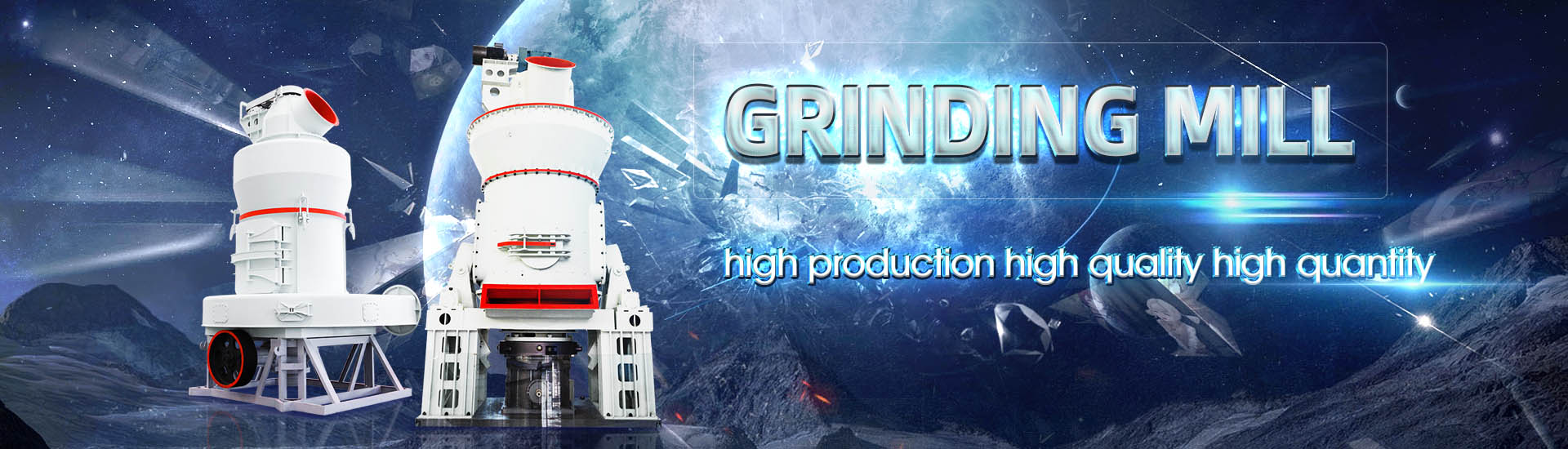
Coal mill installation plan
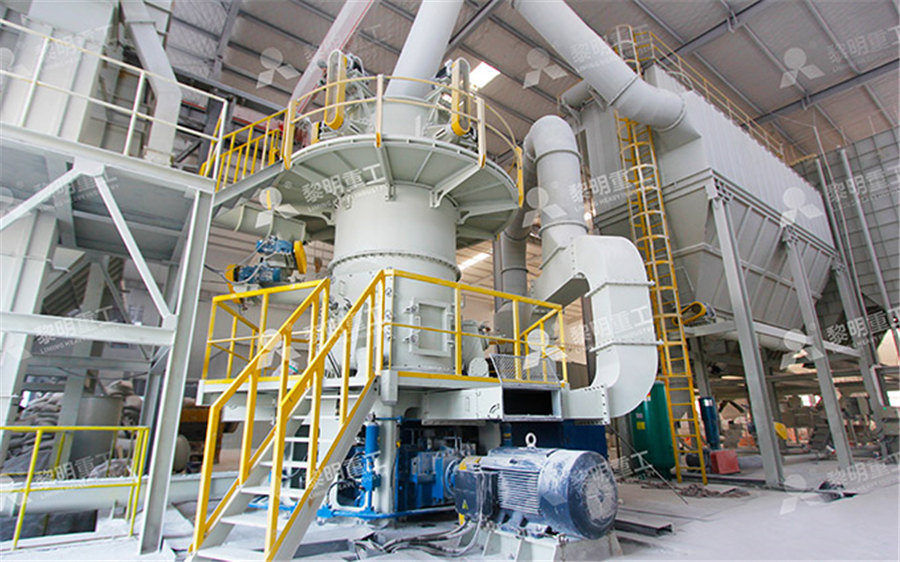
010Method Statement of Coal Mill Instattalation PDF
This document provides a method statement for installing a coal mill at a project site It outlines the general components and purpose of the coal mill It then describes the responsibilities of personnel overseeing the installationLoesche coal grinding mills are distinguished by other characteristics that improve efficiency, safety and environmental protection, from the standard version to topoftherange LOESCHEMILLSOfering high reliability, low installation costs and a wide range of sizes, the ATOX grinds and dries all types of coal – while providing excellent economy in terms of specific energy consumption ATOX COAL MILLContribute to lbsid/en development by creating an account on GitHuben/162/vertical coal mill installation planmd at main
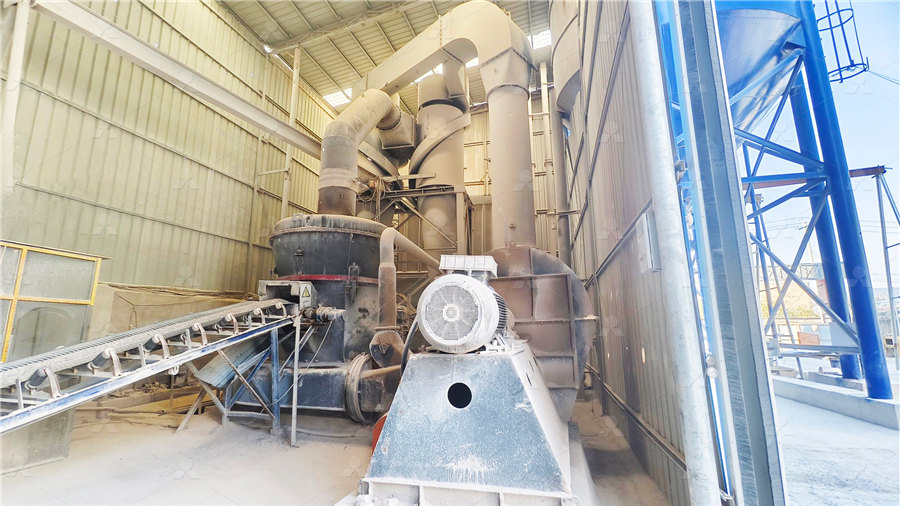
PROCESS OPTIMISATION FOR LOESCHE GRINDING PLANTS
Loesche plants are specifically planned for the required process steps and equipped with the associated techno logy This technology comprises: Loesche Automation combines cutting Vertical roller mills are not only used for grinding cement raw materials but also find an application in grinding a wide variety of coal types in cement and power plants Gebr Pfeiffer SE (GPSE) COAL GRINDING IMPS: more than meets the eye Gebr PfeifferCoalfired plants are the most widely used power plant today They involve the combustion of coal producing high pressure (typically 2400–3500 psig, ~165–240 bar) and high temperature Instrumentation and control in coalfired power plant ICSCLOESCHE coal grinding mills are distinguished by characteristics that improve efficiency, safety and environmental protection, from the standard version to topoftherange installations Special versions are available with characteristics Coal Mills for Cement Plants Loesche
.jpg)
(PDF) MPS mills for coal grinding ResearchGate
2014年1月1日 Two mill systems are employed for most coal grinding applications in the cement industry These are, on the one hand, vertical roller mills (VRM) that have achieved a share of almost 90% and,Loesche has been involved in processing solid fuels since 1925 Some key events include delivering their first coal mill in 1927 and introducing hydraulic systems in 1961 Their mills are 132 Loesche Mills For Solid Fuels Coal Mill E 2016The four most common coal pulverizers types are: BallTube Mills This type of mill consists of a rotating tube filled with cast alloy balls Coal is introduced through two hollow trunnions on each side of the tube As the tube rotates, the balls tumble onto the coal, crushing and pulverizing it Coal Pulverizer – Power Plant Pall CorporationCoal grinding is a critical process in various industries, particularly in power generation and cement production However, the process involves significant safety risks due to the combustible nature of coal dust and the mechanical hazards posed by the operation of the mill Ensuring safety during coal grinding is essential to prevent accidents, exAspects of Coal Mill Safety Coal Mill Safety, Explosion and Fire
.jpg)
Pulverizers 101: Part I POWER Magazine
2011年8月1日 A FourStep Plan Blueprinting a That means using the original design grinding profiles for your mill The majority of coal pulverizers sized around 120,000 pph use three grinding elements, MINISTRY OF COAL 101 SAFETy IN COAL MINES Coal mining poses several inherent, Management Plan is prepared for each mine CIL always Mill Te Per 3 Lac Manshifts 197579 157 196 1224 1278 218 044 1424 289 198084 122 143 1018 1065 129 030 975 226SAFETY IN COAL MINESIn a nonreversible hammer mill with screen bars, shown in above figure, material is broken first by impact between hammers and breaker plates and then by a scrubbing action (shear and attrition) of material against screen bars Attrition crushing is most useful in the following two circumstances When material is friable or not too abrasiveConstruction, Working and Maintenance of Crushers for Crushing 2 IEA Coal Research A/C air to cloth ratio BACT Best Available Control Technology 414 Mill inerting 26 42 Coal and air distribution system 27 5 Primary pollution control 30 51 Process optimisation 30 Retrofitting is limited to the installation ofProspects for upgrading coalfired power plants ICSC
.jpg)
Ball Mill Maintenance Installation Procedure 911Metallurgist
2016年10月20日 On Mill Installation and Maintenance Before starting the erection of the mill, adequate handling facilities should be provided or made available, bearing in mind the weights and proportions of the various parts and subassemblies This information can be ascertained from the drawings and shipping papersSection 2 : Coal Handling Plant 21 Introduction 2 1 22 Brief description of coal handling plant system 2 2 23 Design criteria and broad features 2 5 24 Performance requirements 2 17 25 Codes and standards 2 19 Annexure2A Typical scope of work for coal handling plant 2 STANDARD DESIGN CRITERIA/ GUIDELINES FOR BALANCE OF 2020年4月2日 A differential pressure measurement was install ed Coal mill motor power (kW) 0 4171 4548 4390 4586 The key input to the coal fired power plan t is the coalAnalysis of the Coal Milling Operations to the Boiler ParametersThe information gained will include coal pipe balance, coal fineness, air/coal ratios, as well as the condition of the grinding components, mill throat, classifier, springs, and other components This information is then provided to the Power Plant in a comprehensive report and is used as a tool to determine which modifications are required to meet their specific target or performance goalsCE RB Coal Mill Modernization Components and Services
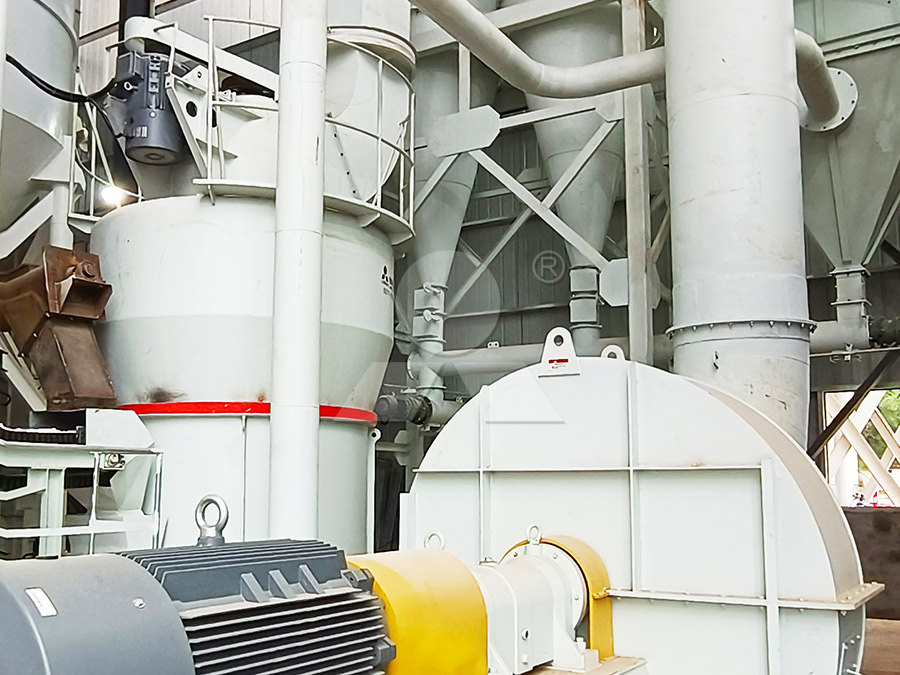
Ball Mill Installation Essential Work and Precautions
In this article, we will discuss the work that needs to be done after the installation of a ball mill and the precautions that need to be taken to ensure safe and efficient operation Inspection of the ball mill After installing a ball mill, it is important to conduct a thorough inspection of the equipment to ensure everything is in order1927 First Loesche coal mill delivered for the Klingenberg power station in Berlin 1953 500th coal mill plant sold worldwide 1961 Introduction of hydraulic spring assembly system 1965 Construction of first pressure mill (LM 122 D) 1980 Delivery of first modular coal mill (LM 263 D) 1985 Delivery of first selfinerting coal grinding plant (LM 212 D) for the steel industry (PCI LOESCHEMILLS2019年5月8日 7 Maintenance Strategy Maintenance Significant Item Inspection / Execution Task Coal Measure HGI (hard grove index), moisture content, abrasiveness and size of coal fed to mill Pulverised fuel (PF) Measure particle TPS Coal Mills and Fan Performance PPT SlideShare2014年1月1日 Two mill systems are employed for most coal grinding applications in the cement industry These are, on the one hand, vertical roller mills (VRM) that have achieved a share of almost 90% and, on (PDF) MPS mills for coal grinding ResearchGate
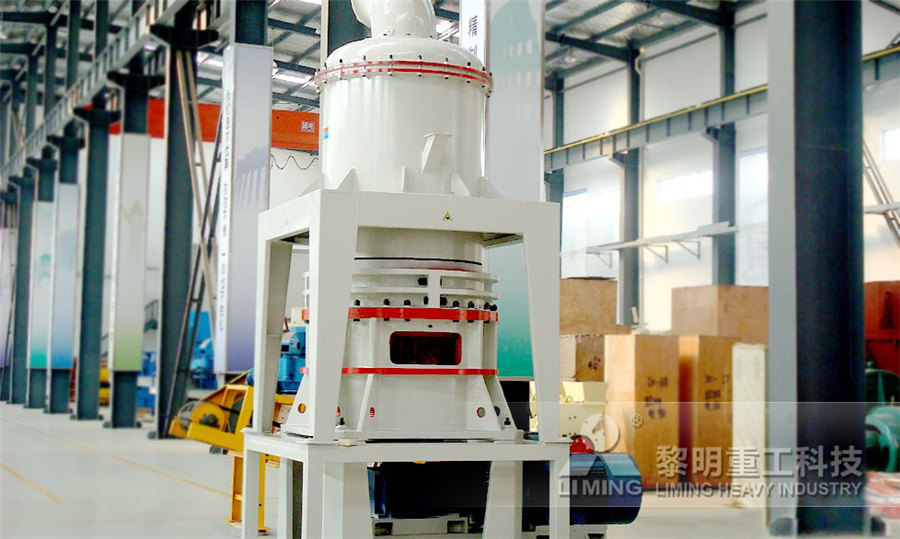
Coal mill pulverizer in thermal power plants PPT SlideShare
2012年11月17日 20 131Fineness Fineness is an indicator of the quality of the pulverizer action Specifically, fineness is a measurement of the percentage of a coal sample that passes through a set of test sieves usually designated at 50, 100, and 200 mesh A 70% coal sample passing through a 200 mesh screen indicates optimum mill performance The mill wear and 2016年3月11日 To reduce runofmine to mill feed requires reduction in a series of stages The physical size and power requirements of a crusher capable of reducing hard rock vary depending on the application Extended experience in most crushing plants show that a minus 19MM (¾”) rod mill feed can be and is being produced in three stages of crushingCrushing Plant Flowsheet DesignLayout 911Metallurgist2024年10月25日 Looming over LGE and KU and other coalreliant utilities are new regulations from the US Environmental Protection Agency that require coalfired power plants and new natural gasfired power plants to curb 90% of their carbon dioxide emissions by 2032 if utilities plan to operate them past 2039Less power from coal, more from natural gas in Kentucky’s future Coal grinding is a critical process in various industries, particularly in power generation and cement production However, the process involves significant safety risks due to the combustible nature of coal dust and the mechanical hazards posed by grinding machinery Ensuring safety during coal grinding is essential to prevent accidents, explosionSafety Aspects of Coal Grinding Coal Mill Safety, Explosion and

COAL MILL Land Instruments International
COAL MILL Derek Stuart, AMETEK Land, and Todd Collins PE, Hoosier Energy, US, discuss available techniques for detecting early signs of mill fires and explosions concentration of coal dust An installation location at the classifier outlet was preferred, since this allowedTotal Renewable energy is planned to install 5570 MW of renewable capacity by 2030 Coal India Limited (CIL) is currently installed 11 MW as rooftop solar power Coal India, a fossil fuel producer has aligned itself and is committed to become a Net Zero Energy Company and is in the process of implementing 3 GW solar power program by 202526Ministry of Coal, Government of IndiaSince the first application using an MPS mill to process pulverized coal in Germany in the mid 1960s, there have been over 2,000 different MPS mill installations operating in coalfired power plants worldwide As one of the most popular coal pulverizers in the utility industry, the MPS mill was first introduced into the US in the early 1970sCOAL PULVERIZER DESIGN UPGRADES TO MEET THE DEMANDS 2021年3月12日 1 Introduction Two mill systems are employed for most coal grinding applications in the cement industry These are, on the one hand, vertical roller mills (VRM) that have achieved a share of almost 90% and, on the other MPS mills for coal grinding AYS Engineering
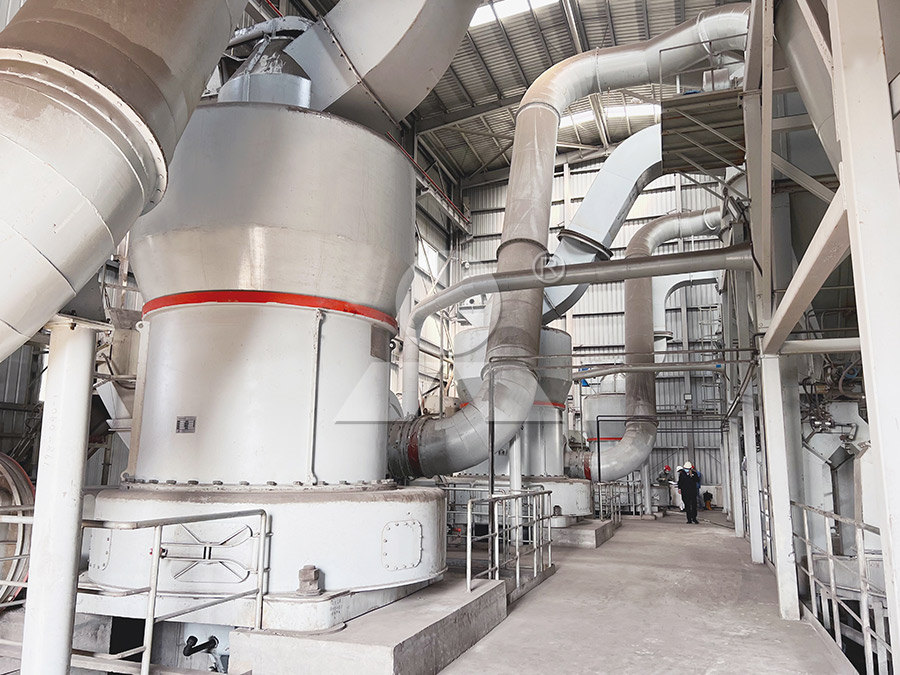
Reliable Coal Pulverizers and Mills » Babcock Wilcox
Reliable coal pulverizer performance is essential for sustained fullload operation of today's power plants An effective pulverizer must be capable of handling a wide variety of coals and accommodating load swings in utility boilers as large Certainly inadequate drying of coal in a ball mill Installation will reduce output and may lead to blockage of the mill However, it has been shown in many installations that if the exit gas temperature of the mill Is maintained at 70750C, satIsfactory COAL PREPARATION AND FIRING INFINITY FOR CEMENT EQUIPMENTThe information gained will include coal pipe balance, coal fineness, air/coal ratios, as well as the condition of the grinding components, mill throat, classifier, springs, and other components This information is then provided to the Power Plant in a comprehensive report and is used as a tool to determine which modifications are required to meet their specific target or performance goalsMPS Coal Mill Modernization Components and ServicesThe ball mill is a traditional coal pulverizer machine, which has been widely used since it was invented In the cement plant, the new dry process cement manufacturing requires the moisture content of coal powder to be 05% ~ 15%, while that of raw coal is 15% ~ 40%Coal Mill in Cement Plant
.jpg)
Coal Mill PDF Mill (Grinding) Industries
Coal Mill Free download as PDF File (pdf), Text File (txt) or view presentation slides online This dissertation examines technologies to enhance the maintenance performance of coal pulverizers through new technologies It presents the results of testing modifications to rotating throat assemblies, spider and guide wear plates, ball loading cylinders, classifier cones, and This manual and data base has been funded by the Coal Services Health and Safety Trust The project is designed to assist in developing a more cohesive and sophisticated understanding of risk management and risk communications within the coal mining industryRisk Management Manual Coal Services2023年10月12日 The present Indian annual demand of 120 Mt is expected to go up to 310 Mt by the end of this century Although the major share of this is expected to come from opencast mines, underground coal (PDF) INSTALLATION OF HIGH CAPACITY BELT CONVEYOR 2019年9月28日 Detecting classifiercoal mill damage using a signal repair plan Table 1 Vibration contribution to efforts to improve the performance of industrial installations, (PDF) Detecting classifiercoal mill damage using a
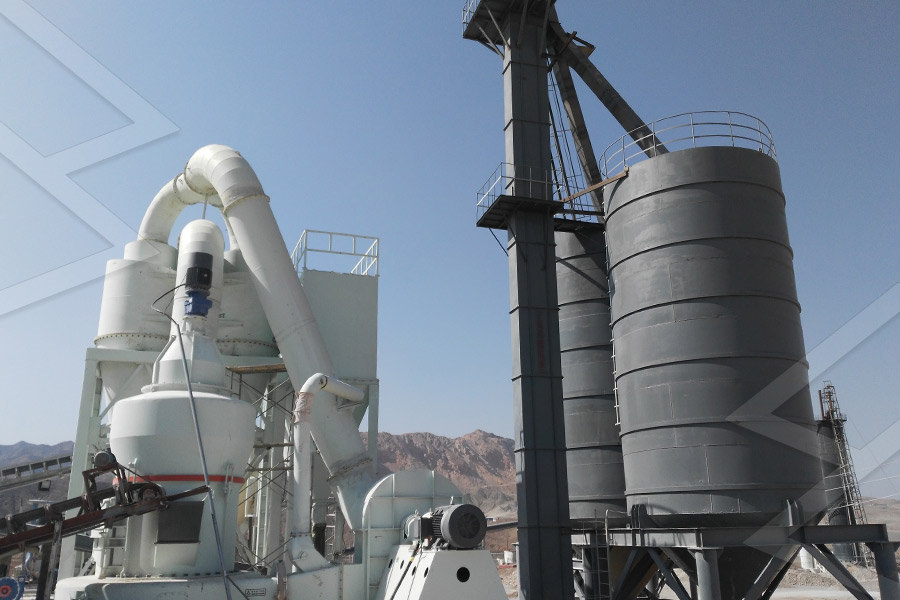
Coal Pulverizer – Power Plant Pall Corporation
The four most common coal pulverizers types are: BallTube Mills This type of mill consists of a rotating tube filled with cast alloy balls Coal is introduced through two hollow trunnions on each side of the tube As the tube rotates, the balls tumble onto the coal, crushing and pulverizing it Coal grinding is a critical process in various industries, particularly in power generation and cement production However, the process involves significant safety risks due to the combustible nature of coal dust and the mechanical hazards posed by the operation of the mill Ensuring safety during coal grinding is essential to prevent accidents, exAspects of Coal Mill Safety Coal Mill Safety, Explosion and Fire 2011年8月1日 A FourStep Plan Blueprinting a That means using the original design grinding profiles for your mill The majority of coal pulverizers sized around 120,000 pph use three grinding elements, Pulverizers 101: Part I POWER MagazineMINISTRY OF COAL 101 SAFETy IN COAL MINES Coal mining poses several inherent, Management Plan is prepared for each mine CIL always Mill Te Per 3 Lac Manshifts 197579 157 196 1224 1278 218 044 1424 289 198084 122 143 1018 1065 129 030 975 226SAFETY IN COAL MINES
.jpg)
Construction, Working and Maintenance of Crushers for Crushing
In a nonreversible hammer mill with screen bars, shown in above figure, material is broken first by impact between hammers and breaker plates and then by a scrubbing action (shear and attrition) of material against screen bars Attrition crushing is most useful in the following two circumstances When material is friable or not too abrasive2 IEA Coal Research A/C air to cloth ratio BACT Best Available Control Technology 414 Mill inerting 26 42 Coal and air distribution system 27 5 Primary pollution control 30 51 Process optimisation 30 Retrofitting is limited to the installation ofProspects for upgrading coalfired power plants ICSC2016年10月20日 On Mill Installation and Maintenance Before starting the erection of the mill, adequate handling facilities should be provided or made available, bearing in mind the weights and proportions of the various parts and subassemblies This information can be ascertained from the drawings and shipping papersBall Mill Maintenance Installation Procedure 911MetallurgistSection 2 : Coal Handling Plant 21 Introduction 2 1 22 Brief description of coal handling plant system 2 2 23 Design criteria and broad features 2 5 24 Performance requirements 2 17 25 Codes and standards 2 19 Annexure2A Typical scope of work for coal handling plant 2 STANDARD DESIGN CRITERIA/ GUIDELINES FOR BALANCE OF
.jpg)
Analysis of the Coal Milling Operations to the Boiler Parameters
2020年4月2日 A differential pressure measurement was install ed Coal mill motor power (kW) 0 4171 4548 4390 4586 The key input to the coal fired power plan t is the coalThe information gained will include coal pipe balance, coal fineness, air/coal ratios, as well as the condition of the grinding components, mill throat, classifier, springs, and other components This information is then provided to the Power Plant in a comprehensive report and is used as a tool to determine which modifications are required to meet their specific target or performance goalsCE RB Coal Mill Modernization Components and Services