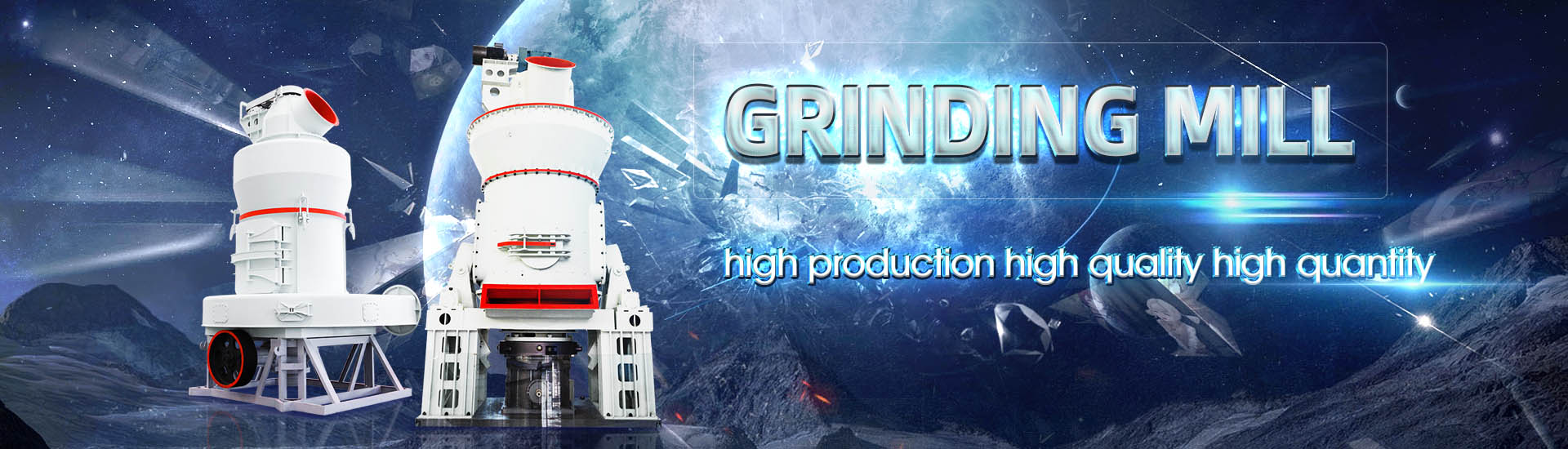
What is the particle size of limestone used for desulfurization
.jpg)
Modeling of Limestone Dissolution for Flue Gas
2020年11月24日 For this investigation, the dissolution of limestone samples was performed into a beaker containing 05 L of deionized water The particle size distribution (PSD) was measured by laser diffractometry (Malvern Mastersizer 2015年10月30日 Limestonebased desulfurizing agent is one of the superior elements which are optimal at around 850950^{\circ}C on high temperature desulfurization(PDF) A Review of Desulfurization Technology using 2024年11月12日 Lime D, which had a particle size of 10 μm, exhibited enhanced desulfurization reactivity, resulting in the highest rate of conversion into CaSO 3 and CaSO 4 These results Effects of the surface properties and particle size of hydrated lime achieve a particle size of ~325 mesh followed by pressing the sample into a pellet with a diameter of 40 mm using a pressure of 200 kN Two excitation conditions are used which are shown in Analysis of limestone for flue gas desulfurization in a power plant
.jpg)
Applications of Ultrafine Limestone Sorbents for the
2019年10月29日 Therefore, in this paper, the application of natural ultrafine limestone, with a Sauter mean diameter of less than 20 μm, was tested by conducting benchscale, pilotscale, and commercialscale experiments to The results showed that the particle characteristics changed after desulfurization and new particles of CaSO 4 may be generated The scrubbing of the desulfurization slurry generated Fine Particle Transformation during the Limestone Gypsum The fine particles formed during the limestone–gypsum flue gas desulfurization process are related to the particles in desulfurization slurry The main composition ofFine Particle Characteristics from Limestone– Gypsum 2005年12月7日 This work presents a practical result of experimental investigation of the limestone particle size effect on deSO x from a circulating fluidized bed combustion (CFBC) Desulfurization with a Modified Limestone Formulation in an
.jpg)
Insights into the desulfurization mechanism of lowgrade
2021年12月1日 In this study, a promising approach of employing lowgrade limestone with different particle sizes as absorbent in wet flue gas desulfurization technique was investigated, Fig 2 Fine particle concentrations after desulfurization Fig 3 Size distribution after desulfurization a Number concentration b Mass concentration Fine Particle Characteristics from Limestone–Gypsum 517 on the limestone particle surface firstly, and then it goes into the inner parts gradually along with the change in particle Fine Particle Characteristics from Limestone– Gypsum Desulfurization 2021年3月17日 The performance of a wet FGD system is greatly influenced by gas–liquidphase mass transfer, ieof Ca 2+ ions in the liquid phase and of SO 2 from the gas phase to the aqueous phase (Hrdlička and Dlouhý 2019)This is further influenced by the rate of dissolution of limestone in the system, directly affecting the concentration of dissolved ions in the slurry Spray drying absorption for desulphurization: a review of 2023年3月15日 The performance of the limestone slurry scrubbing process is determined by various factors, including the purity and particle size of the limestone, temperature, and pH [7], [8] Particularly, the efficiency of desulfurization is chemically limited by two pH extremes [9] Desulfurization characteristics of limestone slurry with added
.jpg)
Evaluation of limestone impurities in the desulfurization process
2017年1月1日 The conversions versus time of calcined limestone, ranging in particle size from 25 to 450 μm, were measured over the temperature range 9731173 K and a gas rate of 0046 m/s2021年12月1日 Limestone particle size has a significant influence on the desulfurization effect in CFB boilers However, Red mud was first used in flue gas desulfurization (FGD), Insights into the desulfurization mechanism of lowgrade limestone 2007年9月6日 Limestone particle size has a crucial influence on SO2 capture efficiency, it was possible for CFB boilers to reach over 99% desulfurization efficiency with limestone injected into furnace, ParticleSize Optimization for SO2 Capture by Limestone in a 2020年5月16日 Numerous mitigation techniques have been incorporated to capture or remove SO2 with flue gas desulfurization (FGD) being the most common method Regenerative FGD method is advantageous over other methods due to high desulfurization efficiency, sorbent regenerability, and reduction in waste handling The capital costs of regenerative methods are Sulfur dioxide removal: An overview of regenerative flue gas
.jpg)
THE CAUSATION OF HIGH LIMESTONE CONSUMPTION IN COAL DESULFURIZATION
Keywords: Limestone, Fluidized bed boilers, Flue gas desulfurization Laboratory research of the reactivity of limestone used for desulfurization of coal fluidized bed boilers have shown that reactivity of CaO after limestone calcination process in boiler is significantly influenced by reactions of CaO with SiO2, Al2O3 and Fe2O3 contained in ashThe particle density is 1080 kg/m3 TRAP model was used therefore particles in contact with wall run down the wall, not bounce 3 Results The kinetics of chemical reactions in a wet scrubber is influenced by many parameters The most important are Numerical simulation of flow in the wet scrubber for desulfurization2015年12月30日 Request PDF A Study on Desulfurization Efficiency of Limestone Sludge with Particle Size Flue gas desulfurization(FGD) is the technique to remove SO2 gas from stack gases of coalfired plantsA Study on Desulfurization Efficiency of Limestone Sludge with Particle DOI: 101016/S00092509(00)000907 Corpus ID: ; Use of limestone for SO2 removal from flue gas in the semidry FGD process with a powderparticle spouted bed @article{Ma2000UseOL, title={Use of limestone for SO2 removal from flue gas in the semidry FGD process with a powderparticle spouted bed}, author={Xiaoxun Ma and Takao Kaneko Use of limestone for SO2 removal from flue gas in the semidry
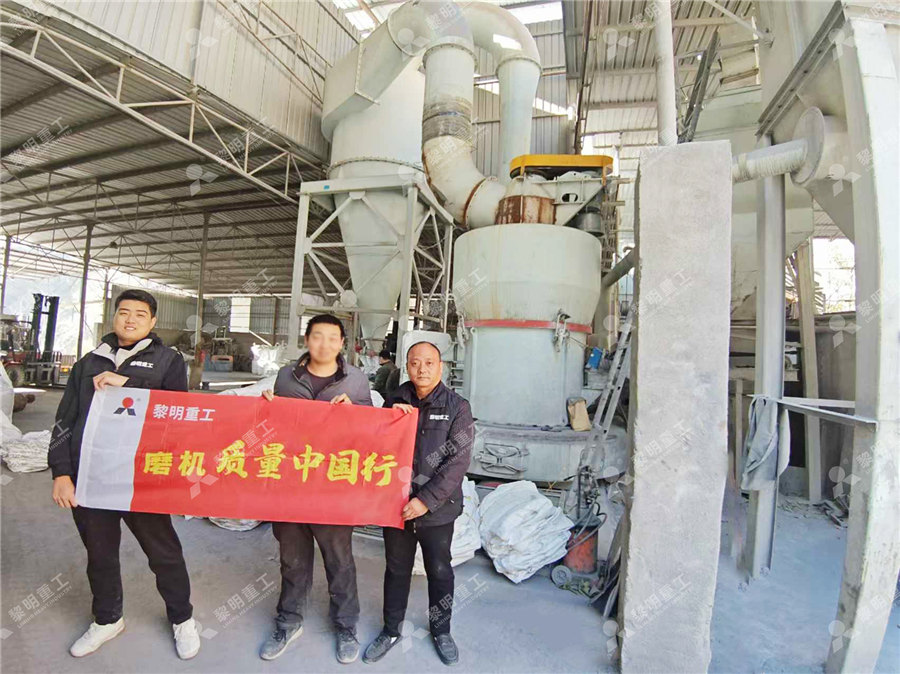
Use of limestone for SO2 removal from flue gas in the
Ewect of sorbent particle size In the present study three di!erent sizes of limestone particle (35, 54 and 89 lm) were used to investigate the Fig 4 E!ect of Ca/S molar ratio on SO removal 2 Fig 5 E!ect of particle size of the 2006年8月1日 Spray nozzle efficiency, scrubber vessel configuration, limestone reactivity and particle size are all factors that influence these processes Adequate mixing of the flue gas and slurry is criticalWetLimestone Scrubbing Fundamentals Power 2019年10月29日 In a 3MW(th) pilotscale CFB boiler, desulfurization using the ultrafine limestone with a 10μm cut size and the coarse limestone with a 310μm cut size was comparedApplications of Ultrafine Limestone Sorbents for the Desulfurization 2012年2月1日 Keywords: flue gas desulfurization, limestone, reactivity, modeling 1 It is well established that particle size and shape substantially influence the bulk properties of powdered materialsUse of Carbonate Rocks for Flue Gas Desulfurization Reactive
.jpg)
Fine Particle Transformation during the Limestone Gypsum
Special attention is required on the fine particle control after desulfurization because a large quantity of fine particles are emitted into the atmosphere from the coalfired power plants In an attempt to figure out the transformation of fine particles during the limestone gypsum desulfurization, the physical properties of fine particles before and after the desulfurization 2001年5月19日 A detailed process model of the wet limestone flue gas desulfurization system has been presented This model can be used to calculate indispensable parameters for estimating costs and next to Model of the Wet Limestone Flue Gas Desulfurization2020年8月1日 Within the fluidised bed, bauxite (mainly composed of Al 2 O 3) with a particle size of 106–180 μm was used as bed material because it was less likely to cause agglomeration than sand (SiO 2), and limestone with a particle size of 200–400 μm for desulfurization (at a 2:1 mol ratio of Ca:S, about 3 wt% of sludge) was added in the sludgeDesulfurization using limestone during sludge incineration in 2015年3月15日 Kikkawa et al [22] used granular limestone of 1 mm particle size directly as desulfuring reagent Kinetics of limelimestone sulfation: review of lime reactivity and sulfation kinetics in the dry limestone desulfurization processes High Temp–High Pressures, 13 (1981), pp 333345 Google Scholar [26]Status of Flue Gas Desulphurisation (FGD) systems from coal
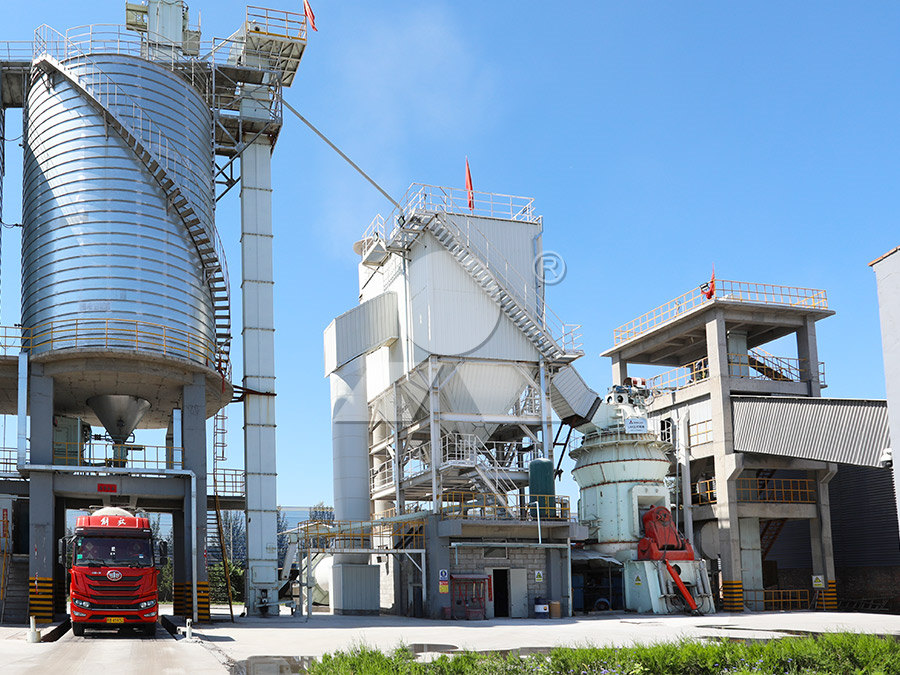
Effect of particle size on insitu desulfurization for oxyfuel CFBC
2021年5月1日 The effect mechanism of particle size on simultaneous calcination and sulfation of limestone is mainly due to the change of reaction specific surface area, heat transfer, and mass transfer from 2016年7月1日 There are many factors that influence the sulfation characteristics of limestone, such as temperature, geological characteristics of the limestone, SO 2 concentration and particle size Temperature has a strong influence on sulfur capture of limestone, typically the best sulfur capture performance is obtained at about 850 °C under airfired CFBB conditions in laboratory The effect of steam on simultaneous calcination and sulfation of 2020年7月22日 To investigate the mechanism of SO2 absorption with the chemical reaction in the limestonegypsum process, the effect of limestone concentration and particle size on the SO2 absorption rate in Dissolution Reactivity and Kinetics of LowGrade Limestone for 2009年4月1日 In this article, the influence of temperature, stirring speed, limestone type, particle size, and desulfurization additives on the limestone dissolution rate was investigated The dissolution Dissolution rate of limestone for wet flue gas desulfurization in
.jpg)
Recent advances in process and materials for dry desulfurization
Too small a particle size can affect the separation efficiency, while too large a particle size can lead to insufficient utilization of limestone, reducing the desulfurization performance [66], [67] For circulating fluidized bed technology, desulfurization by adding limestone to the furnace is a lowcost and simple strategy, and its efficiency is almost comparable to that of traditional 2019年12月1日 Kikkawa et al (2002) tried to scrub SO 2 from FGD without limestone size reduction Beyond the energy savings, The particle size and the amount of silicate clinker added affected the block properties use of wet flue gas desulfurization waste streams as sulfur source Water Res, 47 (2013), Recent advances in flue gas desulfurization gypsum processes 2015年7月27日 The energy required to grind limestone to a size suitable for subsequent feeding to the FGD plant is a function of the initial size of the limestone and its hardness 42 Lime Lime (CaO) is produced by calcination (1 kg of lime is produced from 18 kg of limestone) of limestone in kilns of various designs—for example, rotary or vertical shaft kilnsReview of Design, Operating, and Financial Considerations in 2024年8月1日 The particle size of limestone slurry (or limestone slurry fineness) directly impacts the process of flue gas desulfurization and the gypsum quality, and the reaction efficiency of the slurry and flue gas is improved with the decrease in particle size; however, overgrinding may lead to increased energy consumption [7], [8]Online measurement of particle size in highconcentration limestone
.jpg)
A Study on the Desulfurization Efficiency of Limestone Sludge
2015年11月30日 The flue gas desulfurization (FGD) process is one of the most effective methods to reduce the amount of SO₂ gas (up to 90%) generated by the use of fossil fuel Limestone is usually used as a desulfurizing agent in the wettype FGD process; however, the limestone reserves of domestic mines have become exhausted In this study, limestone sludge In the experiments, limestone was used as SO 2 absorbent to simulate the desulfurization processes in the spray scrubber The flue gas temperature at the inlet of spray scrubber was 120 °C and the liquid to gas ratio was 20 L/m 3 22 Measurement Technique The particle concentration and size distribution were measured in real time by means of an electrical low Fine Particle Characteristics from Limestone–Gypsum Desulfurization This article discusses the analysis of limestone for flue gas desulfurization in a power plant using an EDXRF spectrometer In sample preparation, the powder is ground to obtain a particle size of ~325 mesh, and then, the sample is pressed into a pellet with a diameter of 40 mm at a pressure of 200 kNDetermination of Flue Gas Desulfurization by Analyzing Limestone Fig 2 Fine particle concentrations after desulfurization Fig 3 Size distribution after desulfurization a Number concentration b Mass concentration Fine Particle Characteristics from Limestone–Gypsum 517 on the limestone particle surface firstly, and then it goes into the inner parts gradually along with the change in particle Fine Particle Characteristics from Limestone– Gypsum Desulfurization
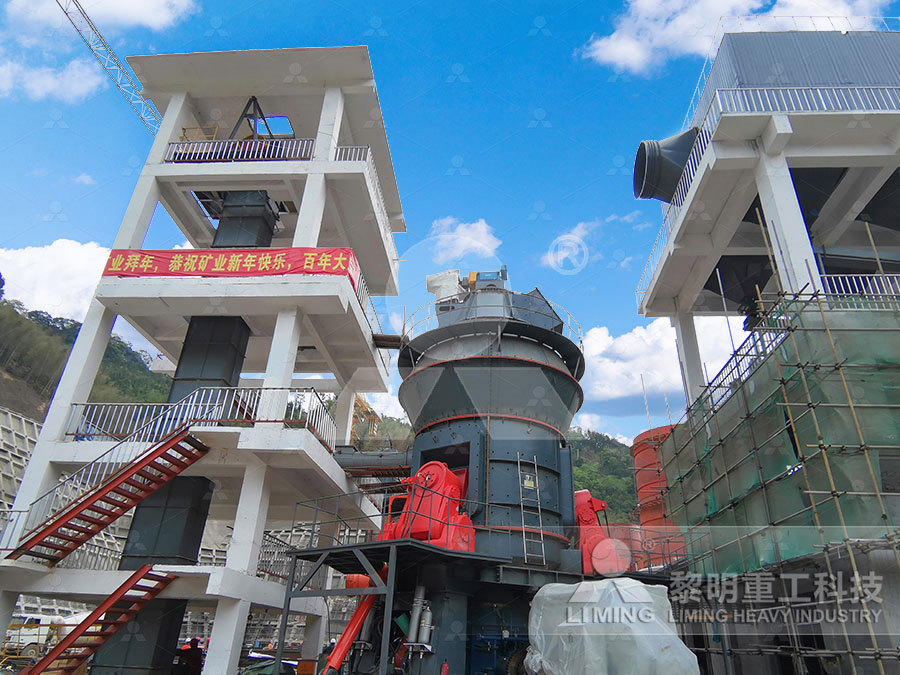
Spray drying absorption for desulphurization: a review of
2021年3月17日 The performance of a wet FGD system is greatly influenced by gas–liquidphase mass transfer, ieof Ca 2+ ions in the liquid phase and of SO 2 from the gas phase to the aqueous phase (Hrdlička and Dlouhý 2019)This is further influenced by the rate of dissolution of limestone in the system, directly affecting the concentration of dissolved ions in the slurry 2023年3月15日 The performance of the limestone slurry scrubbing process is determined by various factors, including the purity and particle size of the limestone, temperature, and pH [7], [8] Particularly, the efficiency of desulfurization is chemically limited by two pH extremes [9] Desulfurization characteristics of limestone slurry with added 2017年1月1日 The conversions versus time of calcined limestone, ranging in particle size from 25 to 450 μm, were measured over the temperature range 9731173 K and a gas rate of 0046 m/sEvaluation of limestone impurities in the desulfurization process 2021年12月1日 Limestone particle size has a significant influence on the desulfurization effect in CFB boilers However, Red mud was first used in flue gas desulfurization (FGD), Insights into the desulfurization mechanism of lowgrade limestone
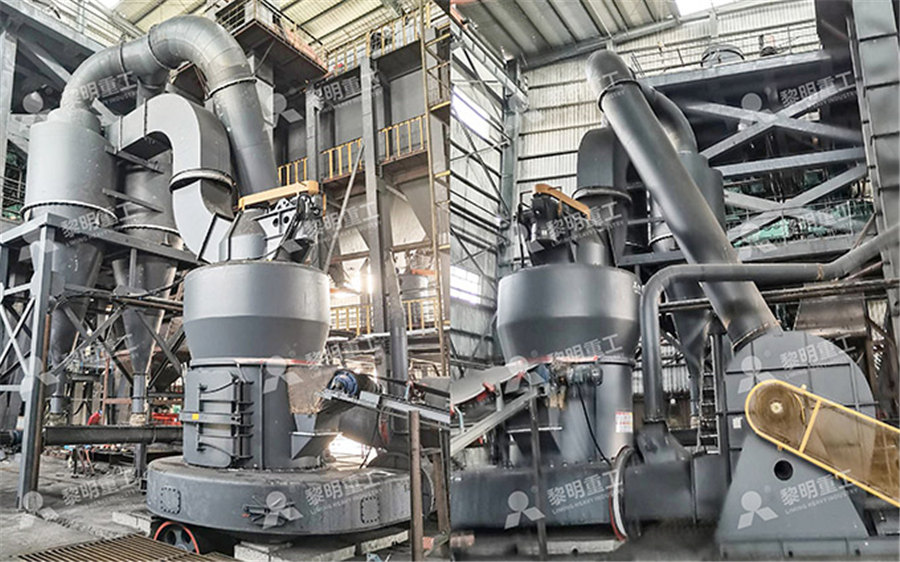
ParticleSize Optimization for SO2 Capture by Limestone in a
2007年9月6日 Limestone particle size has a crucial influence on SO2 capture efficiency, it was possible for CFB boilers to reach over 99% desulfurization efficiency with limestone injected into furnace, 2020年5月16日 Numerous mitigation techniques have been incorporated to capture or remove SO2 with flue gas desulfurization (FGD) being the most common method Regenerative FGD method is advantageous over other methods due to high desulfurization efficiency, sorbent regenerability, and reduction in waste handling The capital costs of regenerative methods are Sulfur dioxide removal: An overview of regenerative flue gas Keywords: Limestone, Fluidized bed boilers, Flue gas desulfurization Laboratory research of the reactivity of limestone used for desulfurization of coal fluidized bed boilers have shown that reactivity of CaO after limestone calcination process in boiler is significantly influenced by reactions of CaO with SiO2, Al2O3 and Fe2O3 contained in ashTHE CAUSATION OF HIGH LIMESTONE CONSUMPTION IN COAL DESULFURIZATION The particle density is 1080 kg/m3 TRAP model was used therefore particles in contact with wall run down the wall, not bounce 3 Results The kinetics of chemical reactions in a wet scrubber is influenced by many parameters The most important are Numerical simulation of flow in the wet scrubber for desulfurization
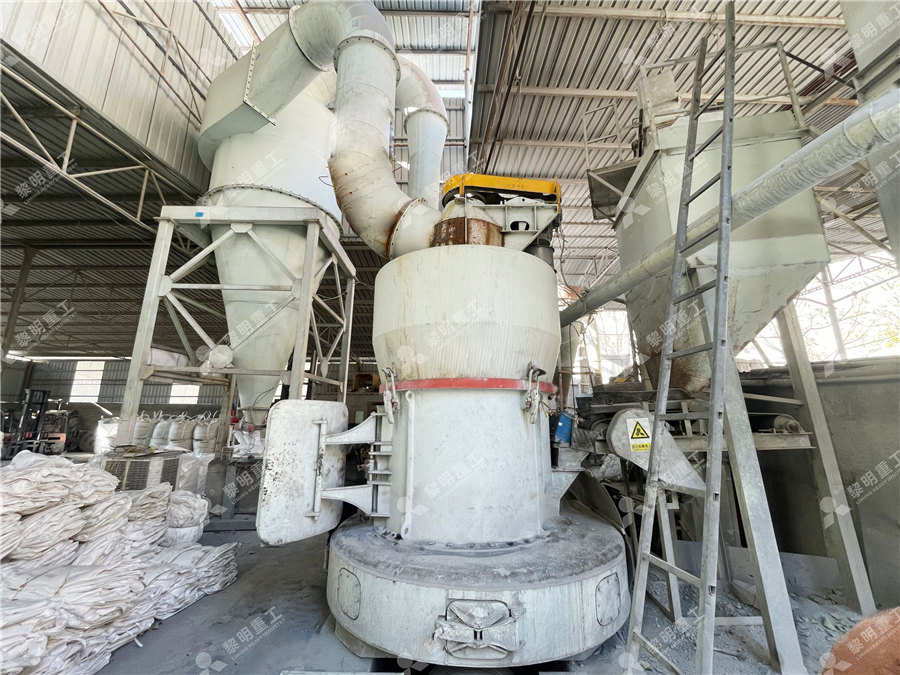
A Study on Desulfurization Efficiency of Limestone Sludge with Particle
2015年12月30日 Request PDF A Study on Desulfurization Efficiency of Limestone Sludge with Particle Size Flue gas desulfurization(FGD) is the technique to remove SO2 gas from stack gases of coalfired plants