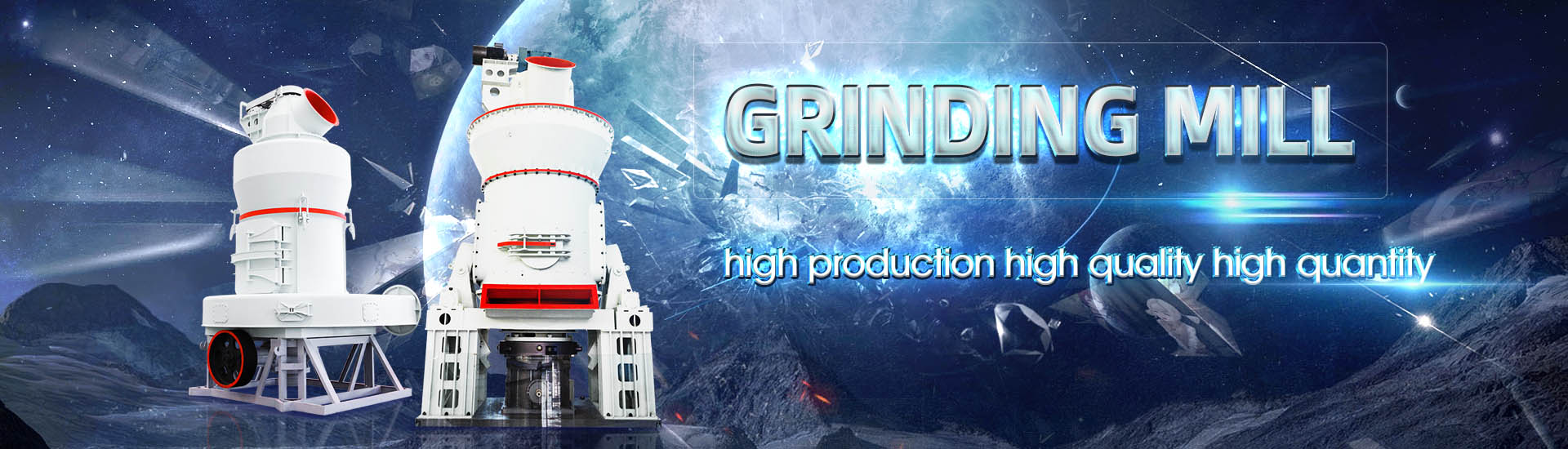
Performance parameters of NC EDM EDAC1 machine
.jpg)
INVESTIGATION OF ELECTRIC DISHARGE MACHINING
oelectric process due to the occurrence of successive discharge between workpiece and electrode BoxBehnken design (BBD) involving four parameters discharge current (I), Pulse 2023年9月15日 In this study, the optimization of processing parameters of Inconel 718 using electrical discharge machining (EDM) with three kinds of renewable dielectrics (soybean oil, Optimization of process parameters and performance for 2023年3月4日 In particular, input parameters, such as peak current, pulse on time, and pulse off time, are studied, along with the effect of dielectrics against the output parameters, such as A review of electrical discharge machining (EDM) and its Several research works have been discussed which provide optimization of EDM performance measures such as high MRR, low TWR, and suitable SQ This section studies each of the A review on optimization of machining performances and recent
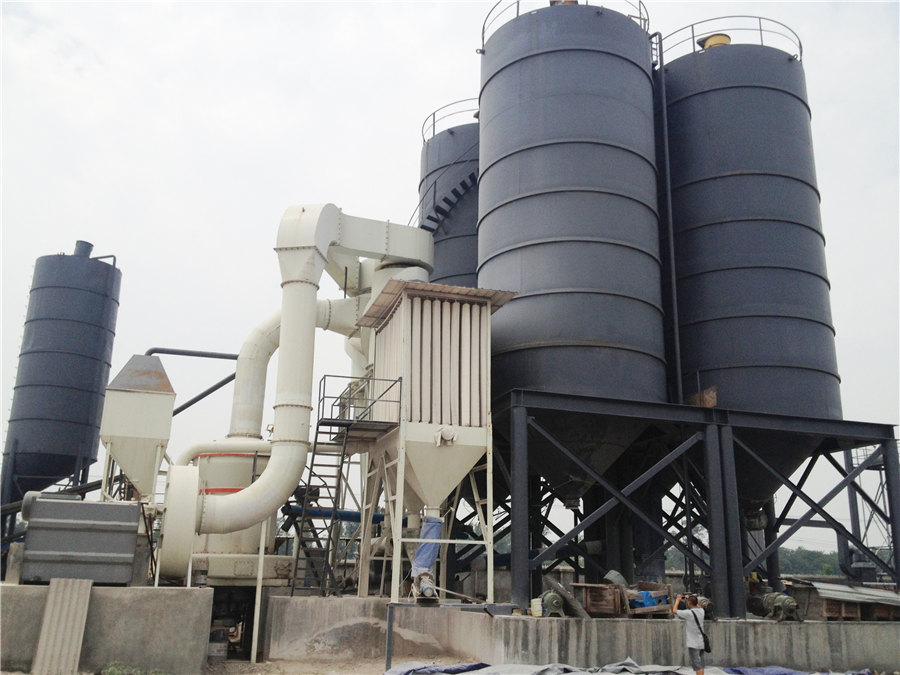
Optimization of machining parameters of EDM for performance
In this paper described EDM of Titanium alloy (Ti6Al4v) in which best process setting has been determined to satisfy efficiency of copper electrode The new mathematical model based on the2023年4月11日 Some researchers performed comparative analysis to predict the performance parameters by developing statistical and soft computing prediction model such as artificial A review of modeling and simulation techniques in EDM process2018年1月30日 In this paper described EDM of Titanium alloy (Ti6Al4v) in which best process setting has been determined to satisfy efficiency of the copper electrode The new technique is based on theOptimization of machining parameters of EDM for During the experiments, parameters such as dielectric type, abrasive size, concentration of abrasive in the dielectric fluid, discharge peak current and pulse duration were changed to Optimization of Multiple Performance Characteristics in EDM: A
.jpg)
Electric discharge machining performance measures and
2023年1月29日 In this review, a proper study has been done to find the process controlling parameters and the relationship between process parameter variables and optimisation of rate The most influential process parameters of EDM process are discharge voltage, peak current, pulse duration (pulse on time and pulse off time), duty factor, polarity, type of dielectric flushing Process parameters and performance measures of EDMChapter 4: Who Are The Leading EDM Machine Manufacturers A variety of EDM (Electrical Discharge Machining) machines are available today, crucial for their ability to precisely and intricately machine hard materials and complex EDM Machining: Components, Types, Applications, 2015年6月13日 Input parameters of WEDM viz pulseon time, pulseoff time, spark gap voltage, wire tension, peak current, wire feed and performance was measured in terms of material removal rate (MRR) and (PDF) Multi response optimization of wireEDM process parameters
]@S0{UDKK%G24F3JGHC.jpg)
Strategic Optimization and Investigation Effect Of Process Parameters
2012年6月1日 The WireEDM process parameters (arc on time, on time, open voltage, off time and servo voltage) were optimized with considerations of multiple performance characteristics, ie, recast layer 2020年10月11日 In the present work, multiresponse optimization of electrodischarge machining (EDM) process is carried out based on an experimental analysis of machining superalloy Inconel718(PDF) EDM process parameter optimization for efficient machining 2019年8月9日 The double ball bar (DBB), based on circular test (Archenti et al 2012a), is a device that can be used for quick tests of machine tools, developed in the early 1980s (Bryan 1982), and it is adopted by ISO 2304 and ANSI B5542005 as an instrument for circular test (ANSI/ASME B554 2005; ISO 2304:2005)This ensures unified practice in ball bar Accuracy and Performance Analysis of Machine ToolsArjun Biloria et al Optimizing the Parameters Influence the Performance of Wire cut EDM Machining 3371 International Journal of Current Engineering and Technology, Vol4, No5 (Oct 2014) EDM works by eroding material in the path of electrical discharges Figure2 Optimizing the Parameters Influence the Performance of Wire cut EDM
.jpg)
Effect of electrical pulse parameters on the machining performance in EDM
INDIAN J ENG MATER SCI, DECEMBER 2011 414 pulse parameters results in increased tool wear Figure 4 shows the image of the tool working surface2022年3月31日 Die sinking EDM processes are widely employed in advanced aerospace applications where part quality and machining time are main concerns The aim of this research work is to develop an advanced (PDF) Investigation of Optimum EDM Die Sinking Parameters in 2022年10月4日 This includes the NC wire cut machine by Charmilles SA in 1969, the CNC wire EDM machine in 1972 by Seibu, and the primitive CNC wire EDM machine by Dulebohn in 1974 How EDM Machining Is Used EDM (electric discharge machining) is used in making molds for plastic injection molding and metal die casting3 Types of EDM Machining and Their Differences Xometry2021年8月1日 The key parameters on the estimation of tunnelboring machine (TBM) performance are rock strength, toughness, discontinuity in rock mass, type of TBM and its specificationsEmpirical Models for Estimating Performance and Operational Parameters

Optimization of Machine Process Parameters in EDM for EN 31
technique in terms of computational time, best parameters obtained, less percentage errors, etc 5 Experimental Setup DieSinking EDM machine (Electronica EMT43 Machine) was used to conduct the experiments EDM process was carried out on the work piece EN 31 material having cylindrical crosssection having dimension of 25 mm 15 mm2009年12月1日 The present paper emphasizes the development of mathematical models for correlating the various machining parameters, such as pulse on time, peak current, average gap voltage and the percent volume fraction of SiC present in the aluminum matrix on the most dominant machining criteria, ie the metal removal rate, electrode wear ratio, gap size and the Study of the parameters in electrical discharge machining through The world’s most accurate Ram EDM, Makino’s EDAC1, is capable of producing corner radii of 000019 inches (0005mm) and surface finish quality of 0 inches (06 micron) Ry This machine achieves positional and pitch accuracies of ±000004 inches (10 micron) through new mechanical and electronic designs, including a cubic structure and removal of overhangs at MAKINO EDAC1 EDM Sinkers MachineTools2020年3月19日 Sinha [40] applied rotaryEDM to machine A ISI D2 t ool steel using a copper electrode M RR, TWR, the performance parameters in EDM of En31 tool steel were studied(PDF) Principles and Characteristics of Different EDM Processes
.jpg)
7 CNC Parameters You Should Know Modern Machine Shop
2019年7月4日 Knowing (or suspecting) that a parameter affects a given issue is just the beginning of correcting the issue You must be able to find the parameter in question Most CNC manufacturers document related parameters in a group, but since there are so many of them, it still can be difficult to find the one that is related to your particular issue2014年12月31日 In 2014, in two different studies, Mohanty et al optimized MRR and SR outputs for Inconel 718 [15], and then, Sultan et al did the same for MRR and electrode wear rate (EWR) [16], both using the Process Optimization and Estimation of Machining Performances Using 2013年3月17日 Machining process parameters (MPP) directly affect the machining quality and efficiency of heavyduty CNC machine tools (HCMT) The selection of MPP is very important to effectively improve machining performance Machining performance has been closely related to the HCMT running state In order to maintain HCMT sustainably manufacturing with high Machining process parameters optimization for heavyduty CNC machine PDF On Dec 20, 2022, Neha Verma and others published A Study on Wire EDM with Parameters Find, read and cite all the research you need on ResearchGate(PDF) A Study on Wire EDM with Parameters ResearchGate
.jpg)
Optimization of Electro Discharge Machining Process Parameters
electrical and nonelectrical parameters [2,5] In all viewed literature, the researchers try to optimize the EDM process by studying the effect of process parameters on the performance measures but2018年12月21日 An EDM machine is the piece of equipment used to carry out this manufacturing process The principle behind EDM was first observed in 1770 by Joseph Priestley, who was experimenting with electrical discharges He EDM Machine types working principles2022年12月19日 Enhancement Material Removal Rate Optimization of Sinker EDM Process Parameters Using a Rectangular Graphite Electrode December 2022 Jurnal Optimasi Sistem Industri 21(2):8796Enhancement Material Removal Rate Optimization of 2019年1月8日 However, many functions are multimodal, discontinuous, and nondifferenName: Christopher R Houck Address: North Carolina State University, Box 7906, Raleigh, NC, 276957906,USA,(919) OPTIMIZATION OF PROCESS PARAMETERS OF WIRE

Performance Analysis of Wire Electric Discharge Machining (WEDM)
optimal combination of WEDM parameters for proper machining of Skd 61 alloy to achieve better surface finish In addition the importance of the cutting parameters on the cutting performance outputs is determined by using analysis of variance (ANOVA) Key words: Wire EDM, MRR, Surface roughness, Taguchi method, ANOVA 1 Introduction:2019年8月1日 The material removal rate (MRR) of electrical discharge machining (EDM) is low when machining difficulttomachine materials; to address this issue, a novel highspeed electrical machining (EM The research of effect of various parameters on processing performance 2022年3月7日 AMCsLM5/3,6,9% ZrO2 fabricated by stir casting process are machined in Wire EDM to choose the optimum parameters by changing the Pulse on Time, Pulse off Time, Gap Voltage and Wire FeedOptimization of Machining Parameters for Wire EDM of AMCs Authors/year Workpiece Tool electrode Process parameters Performance parameters Sharma et al [8] Inconel600 Rotary brass hollow tubular Ip, Vg, Ton, Toff Fp MRR, EWR, OC TA Shah et al [9] Inconel 600 Molybdenum Wire Ip, Ton, Toff fw MRR Jerald et al [10] Inconel 600 Copper OCV, F, MRR TWR Singh et al [11] Inconel 600 Brass, Copper Optimization of EDM process parameters for TWR on machining
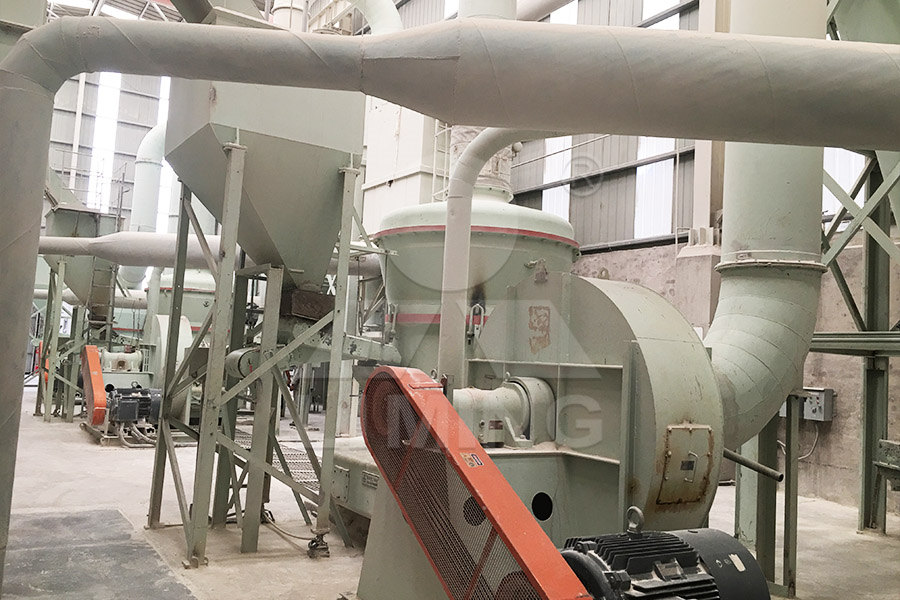
Research on the Influence of PM Controller Parameters on the
DOI: 103901/JME201118186 Corpus ID: ; Research on the Influence of PM Controller Parameters on the Performance of Hydrostatic Slide for NC Machine Tool @article{Gao2011ResearchOT, title={Research on the Influence of PM Controller Parameters on the Performance of Hydrostatic Slide for NC Machine Tool}, author={Dianrong Gao}, 2018年5月7日 Electrical discharge machining (EDM) is a nonconventional machining process that is used for machining of hardtomachine materials, components in which length to diameter ratio is very high or products with a very complicated shape The process is commonly used in automobile, chemical, aerospace, biomedical, and tool and die industries It is very important Optimization of Machine Process Parameters in EDM for EN 31 Due to the inherent properties of the process, wire EDM can easily machine complex parts and precision components out of hard conductive materials Page 5 Figure1 3 Die sinking wire cut EDM Process 15 Important parameters of EDM (a) Spark Ontime (pulse time or Ton): The duration of time (µs) the current is allowed to flow per cycleExperimental Investigation of Machining Parameters for EDM The most influential process parameters of EDM process are discharge voltage, peak current, pulse duration (pulse on time and pulse off time), duty factor, polarity, type of dielectric flushing Process parameters and performance measures of EDM
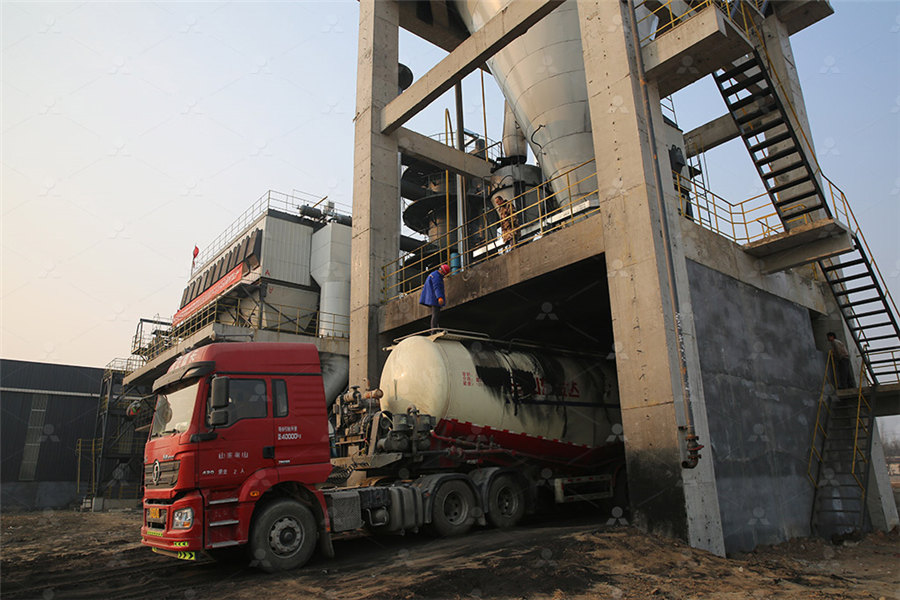
EDM Machining: Components, Types, Applications,
Chapter 4: Who Are The Leading EDM Machine Manufacturers A variety of EDM (Electrical Discharge Machining) machines are available today, crucial for their ability to precisely and intricately machine hard materials and complex 2015年6月13日 Input parameters of WEDM viz pulseon time, pulseoff time, spark gap voltage, wire tension, peak current, wire feed and performance was measured in terms of material removal rate (MRR) and (PDF) Multi response optimization of wireEDM process parameters 2012年6月1日 The WireEDM process parameters (arc on time, on time, open voltage, off time and servo voltage) were optimized with considerations of multiple performance characteristics, ie, recast layer Strategic Optimization and Investigation Effect Of Process Parameters 2020年10月11日 In the present work, multiresponse optimization of electrodischarge machining (EDM) process is carried out based on an experimental analysis of machining superalloy Inconel718(PDF) EDM process parameter optimization for efficient machining
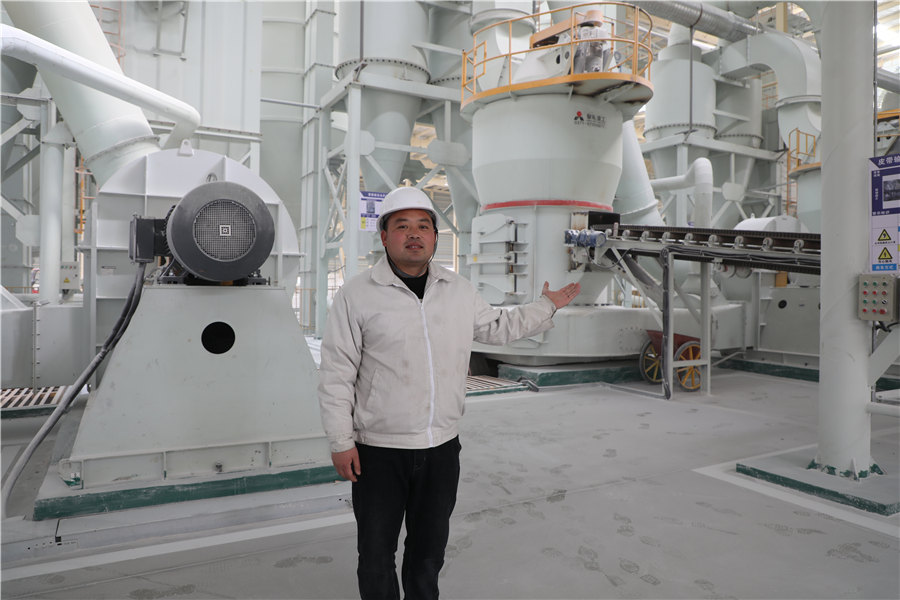
Accuracy and Performance Analysis of Machine Tools
2019年8月9日 The double ball bar (DBB), based on circular test (Archenti et al 2012a), is a device that can be used for quick tests of machine tools, developed in the early 1980s (Bryan 1982), and it is adopted by ISO 2304 and ANSI B5542005 as an instrument for circular test (ANSI/ASME B554 2005; ISO 2304:2005)This ensures unified practice in ball bar Arjun Biloria et al Optimizing the Parameters Influence the Performance of Wire cut EDM Machining 3371 International Journal of Current Engineering and Technology, Vol4, No5 (Oct 2014) EDM works by eroding material in the path of electrical discharges Figure2 Optimizing the Parameters Influence the Performance of Wire cut EDM INDIAN J ENG MATER SCI, DECEMBER 2011 414 pulse parameters results in increased tool wear Figure 4 shows the image of the tool working surfaceEffect of electrical pulse parameters on the machining performance in EDM2022年3月31日 Die sinking EDM processes are widely employed in advanced aerospace applications where part quality and machining time are main concerns The aim of this research work is to develop an advanced (PDF) Investigation of Optimum EDM Die Sinking Parameters in
.jpg)
3 Types of EDM Machining and Their Differences Xometry
2022年10月4日 This includes the NC wire cut machine by Charmilles SA in 1969, the CNC wire EDM machine in 1972 by Seibu, and the primitive CNC wire EDM machine by Dulebohn in 1974 How EDM Machining Is Used EDM (electric discharge machining) is used in making molds for plastic injection molding and metal die casting