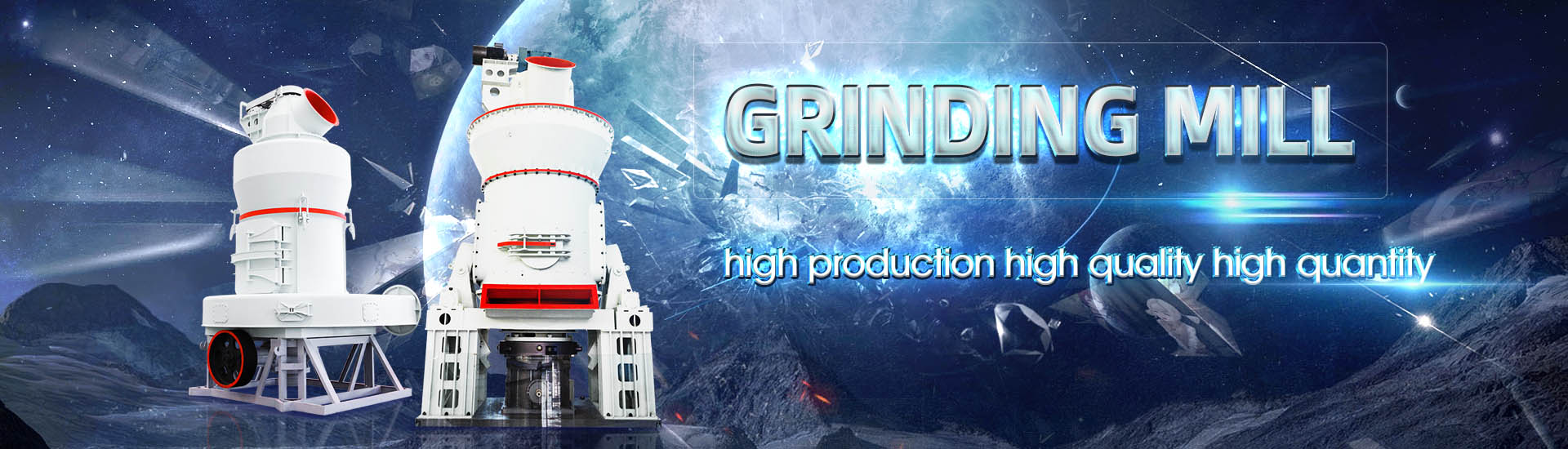
Coalfired reverberatory furnace masonry method

Reverberatory Furnace University of Technology, Iraq
Today, reverberatory furnaces are widely used to melt secondary aluminium scrap for eventual use by diecasting industries Reverberatory smelting has recently been giving way to such 2023年11月25日 In the smelting of nonferrous metals, reverberatory furnaces are used for drying, roasting, smelting, refining, melting, heat preservation, slag processing, and other Reverberatory Furnace SpringerLinkThe air furnace was a reverberatory furnace (fuelled with mineral coal) that was similar to the cupolas used for smelting lead and copper This is a completely different technology from the modern foundry cupola which is a sort of small 18thcentury ironfounding: coke iron, air furnaces and In 25 the metallurgical field, this designation precisely defines a furnace where there is a separation between 26 the production of heat, its use and the evacuation of gases A The reverberatory furnace for ore smelting: An experiment on a
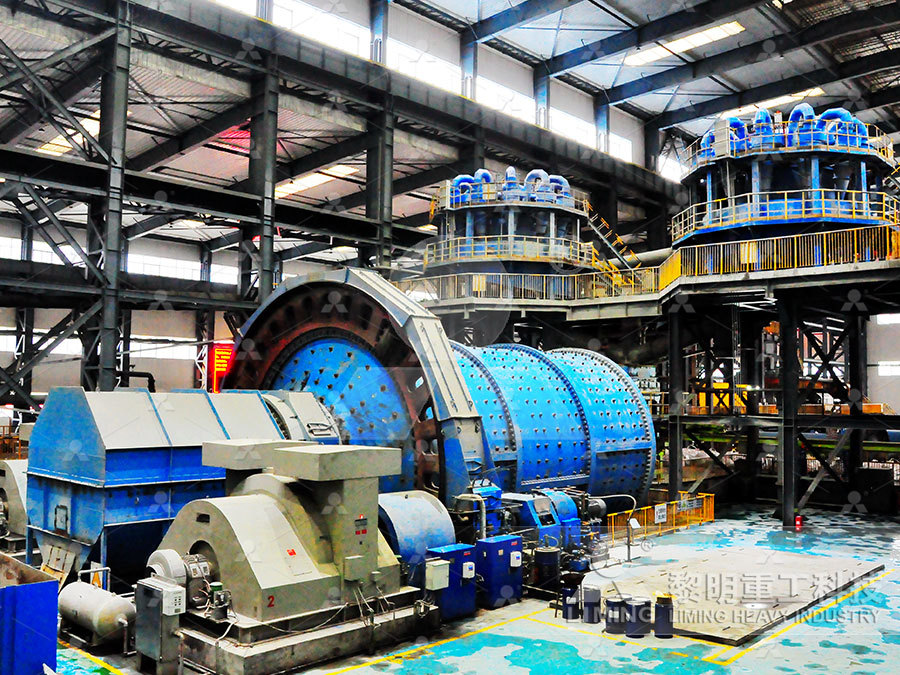
RedalycAn approach to optimal control of the combustion system
In this work an optimal control technique is applied to control the excess air in the combustion process of a reverberatory furnace by the monitoring of O 2Until the introduction of electric furnaces in the 1930's, the fuelfired reverberatory furnace was the sole process for melting cathode copper, and it is still widely used today During the first half of Melting cathode copper—A case study in process energy efficiencyThe earliest description in the English language of a reverberatory furnace was found in a work published in 1613 by John Rovenson, while the earliest drawing of any value of a coalburningEarly History of the Reverberatory Furnace Naturefurnace designs enhanced smelting capabilities The Roman Influence: The Romans, renowned for their engineering prowess, made significant contributions to smelting technology They Guide to Modern Smelting Processes CED Engineering
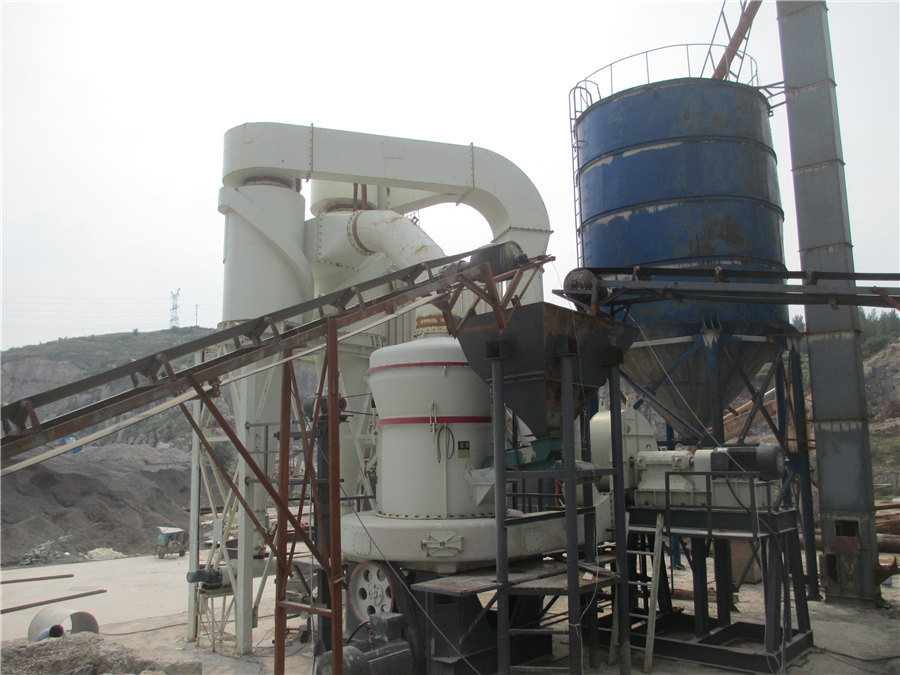
Reverberatory Furnace SpringerLink
2023年11月25日 Since the 19th century, copper smelting reverberatory furnace has developed rapidly Modern large copper smelting reverberatory furnace (Fig 1) is rectangular, and its internal dimensions are: 3036 meters long, 711 meters wide, 345 meters highIt is built with high quality refractory materials, and its roof can be divided into sprung roof and suspended roof2024年2月3日 Kg Furnace Equipped with Linde Hydrogen LTOF Burner The furnace utilized in this study is depicted in Fig 1 Originally, this furnace was an electric furnace supplied by Borel (model FI 1250) For these trials, the electric heating system was not employed The furnace's maximum capacity for these trials was 60 kg of aluminumReverberatory Furnaces Decarbonization—The Case of Hydrogen Shandong An Yutian General Equipment Co, Ltd In addition to factors such as furnace congestion and slow melting of charge, another important reason that affects lead smelting in a reverberatory furnace is lead leakage from the fire wall When adding charge, the lead liquid level at the bottom of the furnace rises and exceeds the height of the water jacket of the fire wallFactors Affecting Lead Smelting in Reverberatory FurnaceReverberatory furnaces consisted of a wide concave hearthbed, partially separated from an adjacent fireplace by a low partition wall (called the fire bridge), with a low arched roof (the fire arch) over all Thus the main difference in the design of reverberatory and shaft furnaces was the separation of ore and fuelReverberatory Furnace Design The classification and 1Library
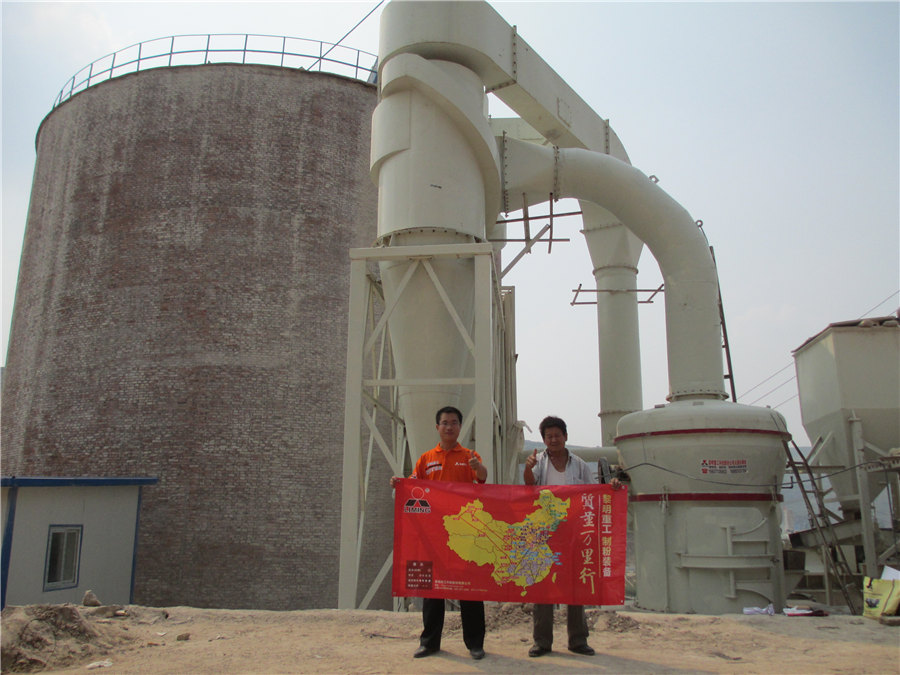
Copper Smelting Furnace 911Metallurgist
2017年3月5日 The early development of the reverberatory furnace for smelting copper ores was the work of the Welsh smelters hearth, using oil for fuel The Steptoe plant, at McGill, Hev, followed with five furnaces with hearths 110 ft long, coalfired, changed to oilfiring in 1911 The Cananea Copper Co put in one furnace with 2016年10月31日 The construction of the ordinary reverberatory furnace is too well known to need detailed description here It consists of a vaulted chamber, containing the ore; through this chamber, the flames and products of combustion from a reverberatory furnace and a current of air are made to pass in a horizontal direction above the ore, which is thus heatedReverberatory Furnace 911Metallurgistand the anthracite coal charged reverberatory furnace This device is affordable, user The gas fired reverberatory furnace is made up of the following main chambers; Design and Development of a Gas Fired Reverberatory Furnace: A reverberatory furnace for nickel refining is an open flame furnace that comes from a burner, which uses natural gas as fuel; and which working temperatures vary from 1450°C to 1550°CIsometric View of Gas Fired Reverberatory Furnace
.jpg)
Reverberatory Furnace: Working, Applications, Construction,
A Reverberatory Furnace is a furnace that isolates the material being treated, from contact with the fuel but not with combustion gases A reverberatory furnace is primarily used in the extraction of metals such as copper, tin, nickel and aluminium, as well as to manufacture certain types of cement and concrete The processes of refining and smelting are carried out in a 2021年8月1日 X Zhang et al fired the coal and the biogas product at the same time in a coalfired boiler Fuel consumption, NO, and SO 2 emissions have been reduced There was a very small (02%) decrease in the boiler efficiency [19] X LI et al experimented with high ash and lowcalorie fuel in a 350 MW boilerInvestigation of factors affecting thermal performance in a coal THE REVERBERATORY FURNACE Until the introduction of electric furnaces in the 1930's, the fuelfired reverberatory furnace was the sole process for melting cathode copper, and it is still widely used today During the first half of this century Melting cathode copper—A case study in process energy efficiency2023年1月5日 However, converting pig iron to wrought iron still required the use of charcoal This was solved by the puddling process, invented by Henry Cort in 1784 [10] In the puddling process, pig iron would be placed in a coalfired The Rise of Steel, Part I by Brian Potter Construction
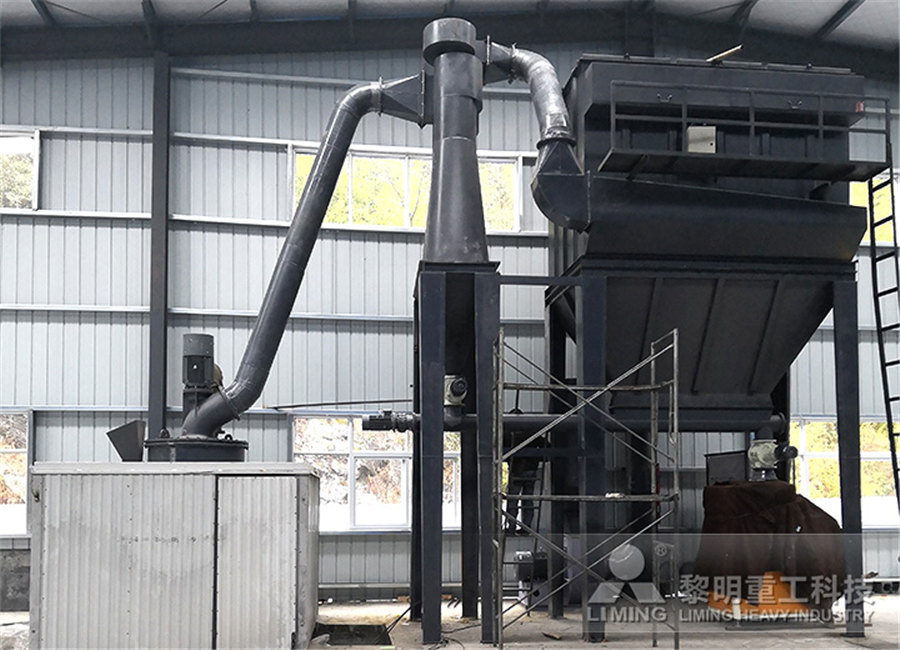
Reverberatory Furnace Construction, Operation And
Today, the reverberatory furnace mostly consists of a rectangular steel box which is lined with castables processing nonwetting properties or refractory bricks The main method of heat transfer is through the radiation from the refractory 2017年3月6日 The furnace in Fig 1 having a long hearth per se, there is no discrepancy of size between furnace and boiler; but in the case of a smaller furnace, this boiler (a 2firetube boiler, from 8 to 9 m long) would seriously overbalance the furnace, or else the boiler would have to be shortened, with a considerable diminution of heatingsurfaceHow to Generate Steam Energy from Furnace Waste Heat2024年1月1日 Since the 19th century, copper smelting reverberatory furnace has developed rapidly Modern large copper smelting reverberatory furnace (Fig 1) is rectangular, and its internal dimensions are: 30–36 meters long, 7–11 meters wide, 3–45 meters highIt is built with high quality refractory materials, and its roof can be divided into sprung roof and suspended roofReverberatory Furnace SpringerLink2021年11月8日 The foundry trade developed as a separate branch of the iron industry in the first half of the 18th century It mostly used coke pig iron, which was produced at Coalbrookdale and in a small number of other furnaces This was rendered possible by Sir Clement Clerke’s development of the air furnace for remelting pig iron and of Abraham Darby’s patented method 18thcentury ironfounding: coke iron, air furnaces and cupolas
.jpg)
Guide to Modern Smelting Processes CED Engineering
furnace designs enhanced smelting capabilities The Roman Influence: The Romans, renowned for their engineering prowess, made significant contributions to smelting technology They developed advanced furnace designs, including the reverberatory furnace, which improved efficiency and reduced emissions2018年1月1日 Design and implementation of furnace temperature measurement system for power plant coalfired boiler in acoustic method January 2018 MATEC Web of Conferences 232:04031(PDF) Design and implementation of furnace temperature 2022年2月15日 A programmed O 2 flow should be used to be set based basically on the furnace’s fire demand A small safety margin (3 to 4% excess air) is added to cope with variations in a reverberatory furnace or burner operation regarding the test bustion optimization in gas burners of reverberatory Semantic Scholar extracted view of "A prediction method for coalfired furnaces" by F Lockwood et al The furnace of a pulverised coalfired utility boiler with an electrical output of 550 MW, the dimensions of 19m x 15m x 48m and 32 swirl burners located on four elevations is consideredA prediction method for coalfired furnaces Semantic Scholar
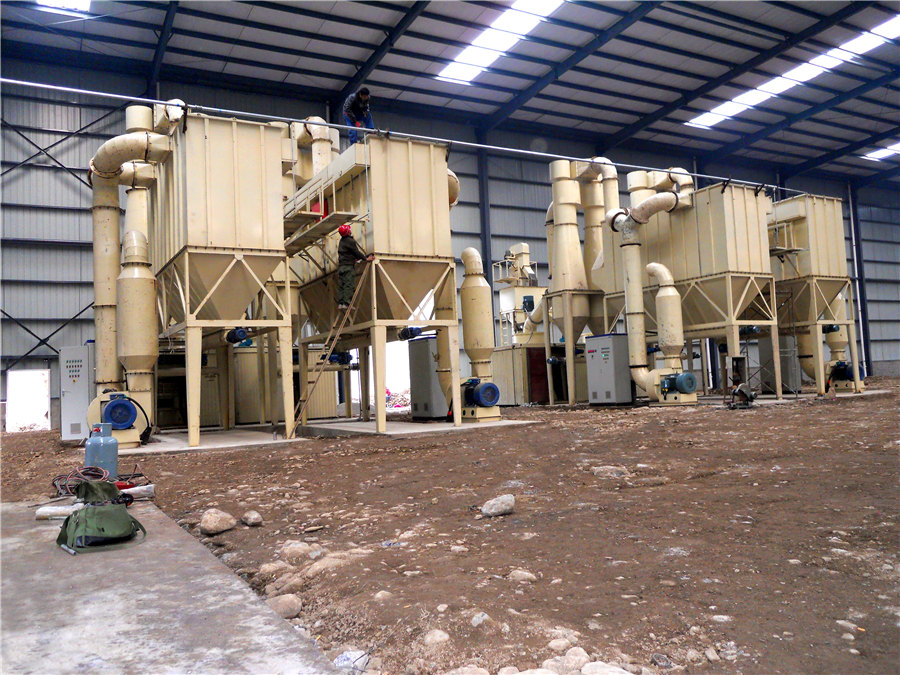
(PDF) Influence of the natural gas composition and flue gas
2020年9月26日 A reverberatory furnace for nickel refining is an open flame furnace that comes from a burner, which uses natural gas as fuel; and which working temperatures vary from 1450°C to 1550°Cwarm air furnace coal only for parallel installation with existing forced airgas or oil fired furnace (us only) for installation as a central furnace the 1500 hotblast furnace has been approved for us installations only all models certified under ul 391 the 1300 model is also certified under can/csab3661m91 n1901g caution:OWNER'S MANUAL SOLID FUEL WARM AIR FURNACE COAL 2020年12月31日 Smelting furnace production is continuous, the smelting process in the oxidizing atmosphere and furnace temperature is about 1500~1550℃, slag by iron, silicon, calcium, aluminum oxide composition, molten dust slag sputtered on the furnace wall and top of the refractory masonry, so that the refractory masonry suffered by slag erosion and damageRefractory for blast furnace and reverberatory furnaceOther articles where puddling furnace is discussed: iron processing: History: Henry Cort, who patented his puddling furnace in 1784 Cort used a coalfired reverberatory furnace to melt a charge of pig iron to which iron oxide was added to make a slag Agitating the resultant “puddle” of metal caused carbon to be removed by oxidation (together with silicon, phosphorus, andPuddling furnace metallurgy Britannica
.jpg)
Early History of the Reverberatory Furnace Nature
AT a meeting of the Newcomen Society held on January 17, Mr Rhys Jenkins read a paper on “The Reverberatory Furnace with Coal Fuel, 1612–1712” The term reverberatory, he said, came from 2010年12月22日 It does appear that coal fired reverberatory furnaces were used I am still not convinced that a box on top of a coal forge will be sufficient to burn off all the coal crud In 'dry' puddling (in a furnace with a sand bottom and no oxide addded) about 30 percent of puddling furnace Smelting, Melting, Foundry, and Casting I 2 Combustion system for reverberatory furnaCe The gas – fired reverb furnace consists simply of three parts: a fireplace at one end, a stack or chimney at the other end and a bed between both on which the aluminum is heated (McKenna, 1998) Heat is supplied in a space between the charge and the roof and transferred by radiation and convectionan approaCh to optimal Control of the Combustion in a reverberatory furnaCeNirayama reverberatory furnace in Izunokuni city, Hashino blast furnace in Kamaishi city, Mie Tsu Naval Training Center in Saga city, Hashima Coal Mine and Glover House in Nagasaki city, Miike Coal Mine in Arao city and Omuta city and Yahata Steel Works in Kitakyushu city SomeWorld Cultural Heritage Solving 10 Mysteries of Nirayama Reverberatory
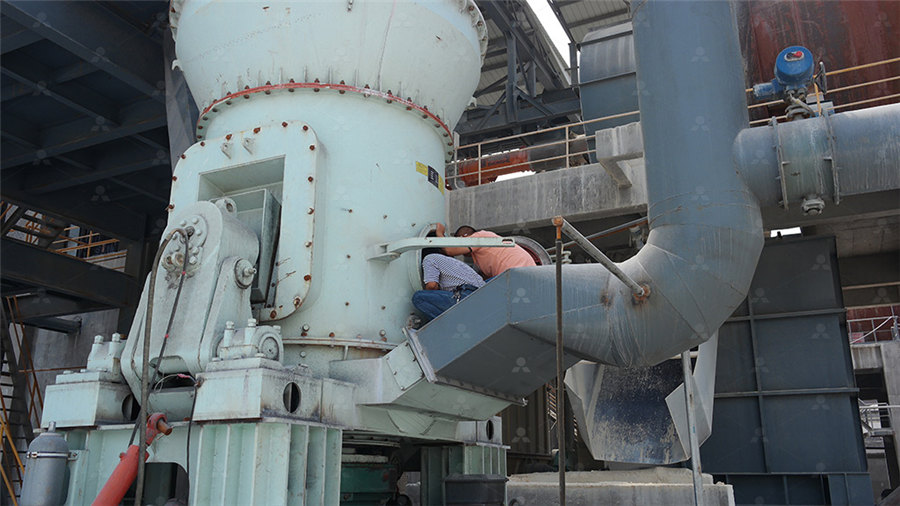
Smelting Northern Mine Research Society
They burnt coal on a separate fire grate and the heat was reflected onto the ore, which was in a lowarched compartment, by a brick firebridge This kept the coal smoke away from the lead and allowed more ore to be smelted at once Because they were built of fire brick and their temperature could be controlled, reverberatory furnaces could that of the ordinary pulverizedcoal fired rever beratory smelting method, except that concen trate instead of pulverized coal is fed into the burner See Fig la PETRI BRYK, JOHN RYSELIN, JORMA HONKASALO, and ROLF MALMSTROM, are FLASH SMELTING COPPER CONCENTRATES2023年11月25日 Since the 19th century, copper smelting reverberatory furnace has developed rapidly Modern large copper smelting reverberatory furnace (Fig 1) is rectangular, and its internal dimensions are: 3036 meters long, 711 meters wide, 345 meters highIt is built with high quality refractory materials, and its roof can be divided into sprung roof and suspended roofReverberatory Furnace SpringerLink2024年2月3日 Kg Furnace Equipped with Linde Hydrogen LTOF Burner The furnace utilized in this study is depicted in Fig 1 Originally, this furnace was an electric furnace supplied by Borel (model FI 1250) For these trials, the electric heating system was not employed The furnace's maximum capacity for these trials was 60 kg of aluminumReverberatory Furnaces Decarbonization—The Case of Hydrogen
.jpg)
Factors Affecting Lead Smelting in Reverberatory Furnace
Shandong An Yutian General Equipment Co, Ltd In addition to factors such as furnace congestion and slow melting of charge, another important reason that affects lead smelting in a reverberatory furnace is lead leakage from the fire wall When adding charge, the lead liquid level at the bottom of the furnace rises and exceeds the height of the water jacket of the fire wallReverberatory furnaces consisted of a wide concave hearthbed, partially separated from an adjacent fireplace by a low partition wall (called the fire bridge), with a low arched roof (the fire arch) over all Thus the main difference in the design of reverberatory and shaft furnaces was the separation of ore and fuelReverberatory Furnace Design The classification and 1Library2017年3月5日 The early development of the reverberatory furnace for smelting copper ores was the work of the Welsh smelters hearth, using oil for fuel The Steptoe plant, at McGill, Hev, followed with five furnaces with hearths 110 ft long, coalfired, changed to oilfiring in 1911 The Cananea Copper Co put in one furnace with Copper Smelting Furnace 911Metallurgist2016年10月31日 The construction of the ordinary reverberatory furnace is too well known to need detailed description here It consists of a vaulted chamber, containing the ore; through this chamber, the flames and products of combustion from a reverberatory furnace and a current of air are made to pass in a horizontal direction above the ore, which is thus heatedReverberatory Furnace 911Metallurgist
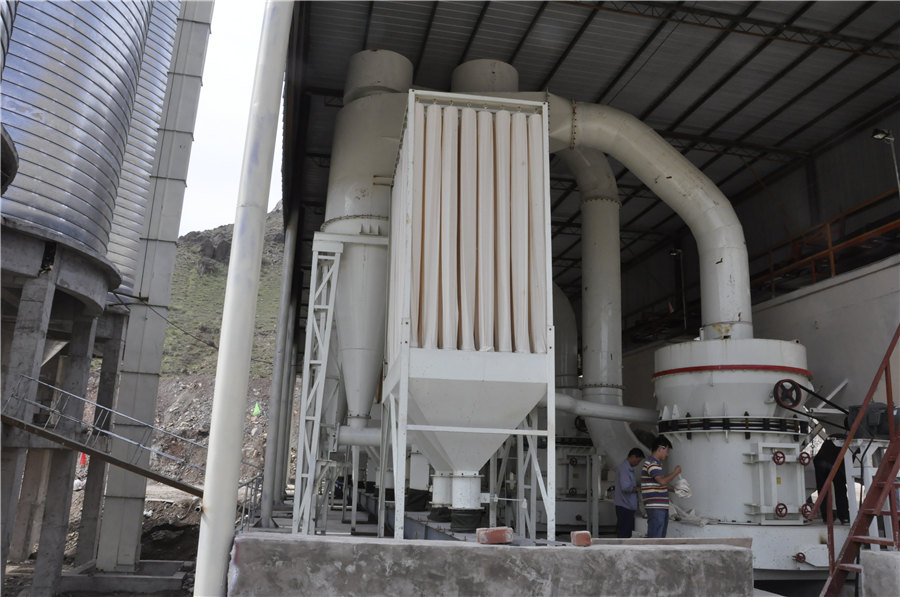
Design and Development of a Gas Fired Reverberatory Furnace:
and the anthracite coal charged reverberatory furnace This device is affordable, user The gas fired reverberatory furnace is made up of the following main chambers; A reverberatory furnace for nickel refining is an open flame furnace that comes from a burner, which uses natural gas as fuel; and which working temperatures vary from 1450°C to 1550°CIsometric View of Gas Fired Reverberatory FurnaceA Reverberatory Furnace is a furnace that isolates the material being treated, from contact with the fuel but not with combustion gases A reverberatory furnace is primarily used in the extraction of metals such as copper, tin, nickel and aluminium, as well as to manufacture certain types of cement and concrete The processes of refining and smelting are carried out in a Reverberatory Furnace: Working, Applications, Construction, 2021年8月1日 X Zhang et al fired the coal and the biogas product at the same time in a coalfired boiler Fuel consumption, NO, and SO 2 emissions have been reduced There was a very small (02%) decrease in the boiler efficiency [19] X LI et al experimented with high ash and lowcalorie fuel in a 350 MW boilerInvestigation of factors affecting thermal performance in a coal