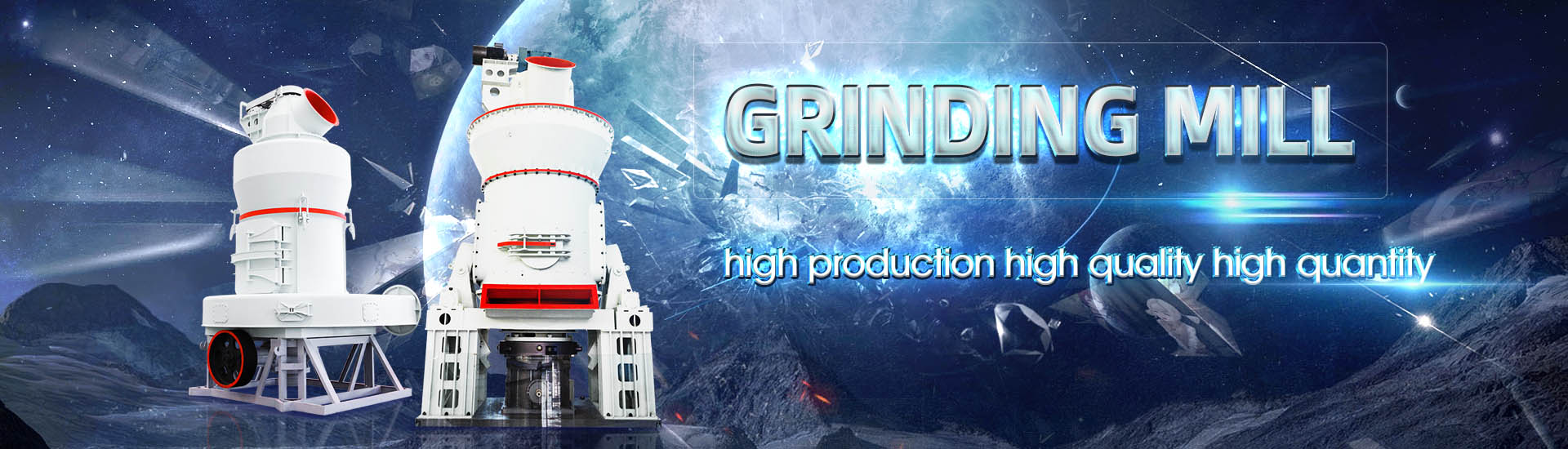
Sintering flue gas desulfurization gas
.jpg)
Summary of research progress on industrial flue gas
2022年1月15日 Through the purification technology of flue gas desulfurization, ultralow emissions of SO 2 flue gas in industrial flue gas can be achieved This article involves dry 2024年4月1日 Semidry desulfurization technology has gained prominence in sintering flue gas desulfurization due to its notable advantages such as minimal equipment corrosion, dry waste Resource utilization of semidry flue gas desulfurization ash by 2023年2月11日 Industrial flue gas desulfurization can effectively reduce sulfur dioxide emissions to atmosphere, but emits large amounts of desulfurization byproducts Calciumbased Resource utilization of flue gas calciumbased desulfurization ash: 2019年3月1日 Firstly, it summarizes the existing desulfurization and denitration technologies, then summarizes the research progress of the combined desulfurization and denitration Progress of Desulfurization and Denitration Technology of Flue
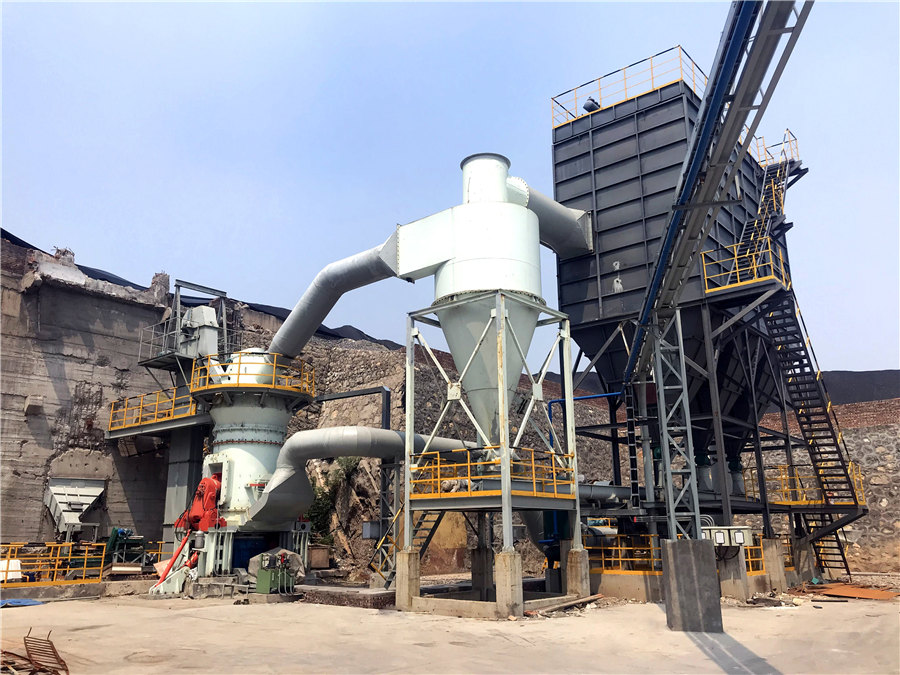
Structure Optimization Research Based on Numerical
2022年10月20日 Although more and more desulfurization equipment has been put into use in sintering plants, how to effectively remove sulfur dioxide from sintering flue gas in a desulfurization tower is still a great challenge in China Based on the analysis of the main principle of deep desulfurization of sintering flue gas, a deep desulfurization system of sintering flue gas is constructed, which is composed of an absorption washing unit and a washing solution treatment Deep desulfurization of sintering flue gas in iron and 2 天之前 Flue gas desulfurization (FGD) technologies play a critical role in the reduction of oxides of sulfur (SO x) emissions from coalfired power plants, a significant source of air Performance Evaluation of SemiDry Flue Gas Desulfurization in 2022年12月28日 Under the simulated sintering flue gas condition, the effect of CO 2 concentration, temperature and relative humidity on the desulfurization of calciumbased adsorbent were carried out The mechanism of CaCO 3 Effect of CO 2 on the Desulfurization of Sintering Flue
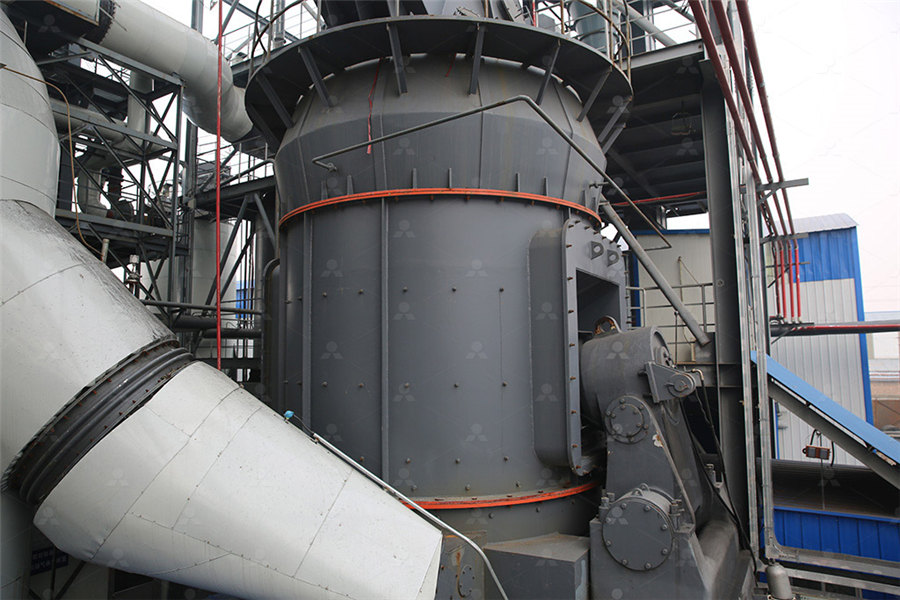
Particle Conditioning for Improving Blockage Resistance of
2024年10月8日 After particle conditioning, the pressure drop across the catalyst is stabilized at values below 600 Pa, effectively mitigating the blockage issue in the denitrification catalyst for 2022年12月28日 The effect of carbon dioxide (CO2) on the desulfurization of sintering flue gas with hydrate (Ca(OH)2) as an absorbent was investigated, and the formation of calcium carbonate (CaCO3) and its effect on the Effect of CO 2 on the Desulfurization of Sintering 2024年10月8日 This research provides critical technical support for the stable ultralow emission of NOx from sintering flue gas (ESP) at a steel plant in Shandong The conditioning agent was an alkaline absorbent from a specific flue gas desulfurization project The absorbent was added to the sintered fly ash in different ratios (1:0, 1:0 Particle Conditioning for Improving Blockage Resistance of 2017年9月8日 The removal of thallium ions in flue gas desulfurization wastewater from ferrous metallurgic industry was studied by emulsion liquid membrane (ELM) method using 2ethylhexyl phosphoric acid2ethylhexyl ester (P507) as carrier, aviation kerosene (AK) as organic solvent, polyisobutylene succinimide (T154) as surfactant, polyisobutylene (PIB) as additive, and The efficient removal of thallium from sintering flue gas
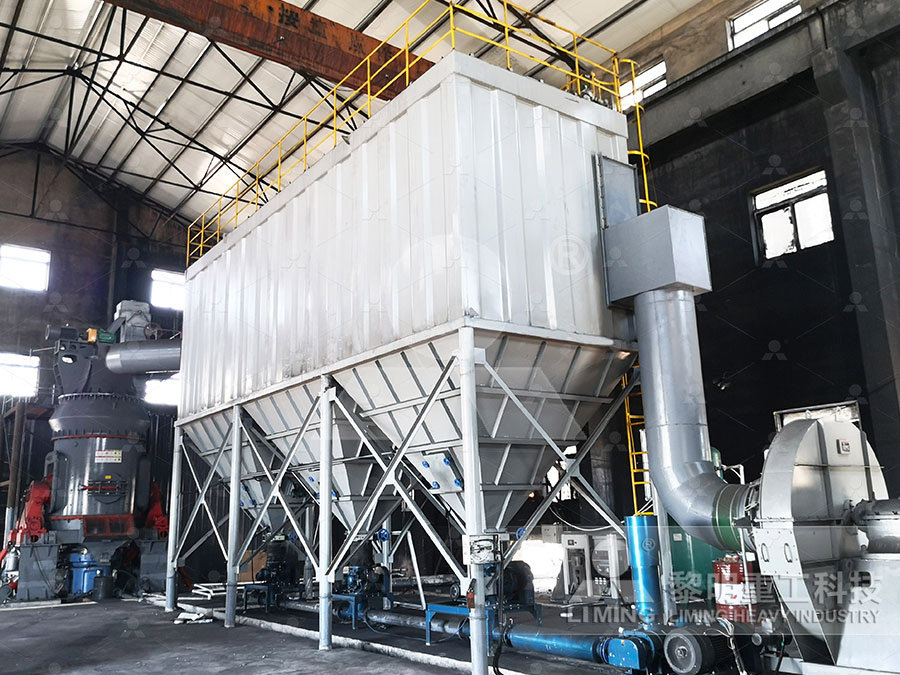
Structure Optimization Research Based on Numerical Simulation
2022年10月20日 Based on the comprehensive analysis, these optimized structures are recommended in the design of an ammoniabased wet sintering flue gas desulfurization towerPDF On Oct 15, 2018, Cara Niu published Comparison of flue Gas Desulfurization Technologies Find, read and cite all the research you need on ResearchGateComparison of flue Gas Desulfurization Technologies2021年3月17日 Iron ore sintering is an important part of a long steelmaking process with sulfur dioxide emissions accounting for 40%–80% of the total sulfur dioxide emissions in steel companies [1,2,3,4]Semidry flue gas desulfurization technology combines the characteristics of wet and dry flue gas desulfurization processes, and it has significant advantages such as low Lowtemperature oxidation behavior and mechanism of semi Abstract Read online The new flue gas desulfurization system of 108m2 sintering machine is reformed, combined with the applicable scope of common desulfurization and dust removal process and the basic principles of desulfurization and dust removal process selection, the advanced and reliable rotary spray dryer absorber(SDA) technology is selected for flue gas Study on sintering flue gas desulfurization process selection
.jpg)
STUDY ON SINTERING FLUE GAS DESULFURIZATION PROCESS
The new flue gas desulfurization system of 108m 2 sintering machine is reformed, combined with the applicable scope of common desulfurization and dust removal process and the basic principles of desulfurization and dust removal process selection, the advanced and reliable rotary spray dryer absorber(SDA) technology is selected for flue gas desulfurization Taking the 2021年6月1日 O 3 oxidation combined with semidry process is proposed for simultaneous desulfurization and denitrification of sintering/pelletizing flue gas Some factors affecting the efficiency of denitrification and desulfurization are introduced • The reaction mechanism of desulfurization and denitrification is expounded explicitlyO3 oxidation combined with semidry method for simultaneous DOI: 101016/JCJCHE201604005 Corpus ID: ; Simultaneous desulfurization and denitrification of sintering flue gas via composite absorbent @article{Wang2016SimultaneousDA, title={Simultaneous desulfurization and denitrification of sintering flue gas via composite absorbent}, author={Jie Wang and Wenqi Zhong}, journal={Chinese Journal of Chemical Simultaneous desulfurization and denitrification of sintering flue gas 2020年9月10日 The properties of activated coke (AC) for sintering flue gas purification greatly affect the efficiency of desulfurization and denitration, but they gradually change during cycles The change in properties of coalbased AC during cycles was studied to clarify the change law and AC optimization index The AC oxygen content rapidly increases from 1349 to 1787 wt% Properties change of activated coke for sintering flue gas
.jpg)
Subcritical hydrothermal oxidation of semidry ash from iron ore
2023年4月1日 Realization of low temperature and high efficiency oxidation of CaSO 3 is the key to solve the issue of ecological hazards caused by semidry sintering flue gas desulfurization ash The subcritical hydrothermal technology was employed for the oxidation of CaSO 3, achieving 8983% of CaSO 3 at 180 °C, 2 MPa for 120 min with a solidtoliquid ratio of 1:202023年7月29日 The semidry flue gas desulfurization ash (SFGDA) is an industrial waste generated by the semidry desulfurization process, and its resources have been continuously attracted attention Through the method of heat decomposition, the SFGDA decomposed into CaO and SO2 has emerged as a prominent research topic This paper summarizes various of Advances on resource utilization of semidry desulfurization ash 2021年7月1日 From another perspective, more and more studies about NO x removal from sintered flue gas focus on the integration of desulfurization and denitrification technologies, such as a combination of active coke desulfurization and denitrification, semidry desulfurization + medium or lowtemperature SCR, as well as semidry desulfurization + ozone oxidation Emissions of air pollutants from sintering flue gas in the Beijing 2016年6月5日 The semidry desulfurization ash obtained from sintering flue gas contains a large amount of CaSO3, which has an important stabilizing influence on desulfurization ash, and thereby restricts its Oxidation modification of semidry desulfurization ash from sintering
.jpg)
3D simulation of sintering flue gas desulfurization and
2016年9月28日 The result was then further verified by an industrial scale test on a 2 × 220 m² sintering flue gas desulfurization tower Discover the world's research 25+ million members;2016年8月1日 At present, wet flue gas desulfurization (FGD) is a relatively mature and most widely applied technology in iron and steel industry to control the SO 2 emission However, it is not much effective for the absorption of NO X because NO X from the sintering flue gas mainly exists in the form of NO which is poorly soluble in water [3]Simultaneous desulfurization and denitrification of sintering flue gas 2022年12月1日 At present, the typical treatment technologies for the removal of SO 2 and NO x from sintering flue gas can be classified into two types, namely wet process and dry process (Cheng and Zhang, 2018a)The wet processes are commonly subdivided into oxidation adsorption methods and complexing adsorption methods, which have positive effects on desulfurization Performance on desulfurization and denitrification of onestep 2019年3月1日 [9] Wang X H and Fang X C 2008 Progress in Simultaneous Removal of SO2 and NOX from Flue Gas Contemporary Chemical Industry 37 197200 Google Scholar [10] Li H, Niu M and Miao Y 2013 Analysis of LimestoneGypsum Flue Gas Desulfurization Technology for Sintering Machine Science Technology Information 138138 Google ScholarProgress of Desulfurization and Denitration Technology of Flue Gas
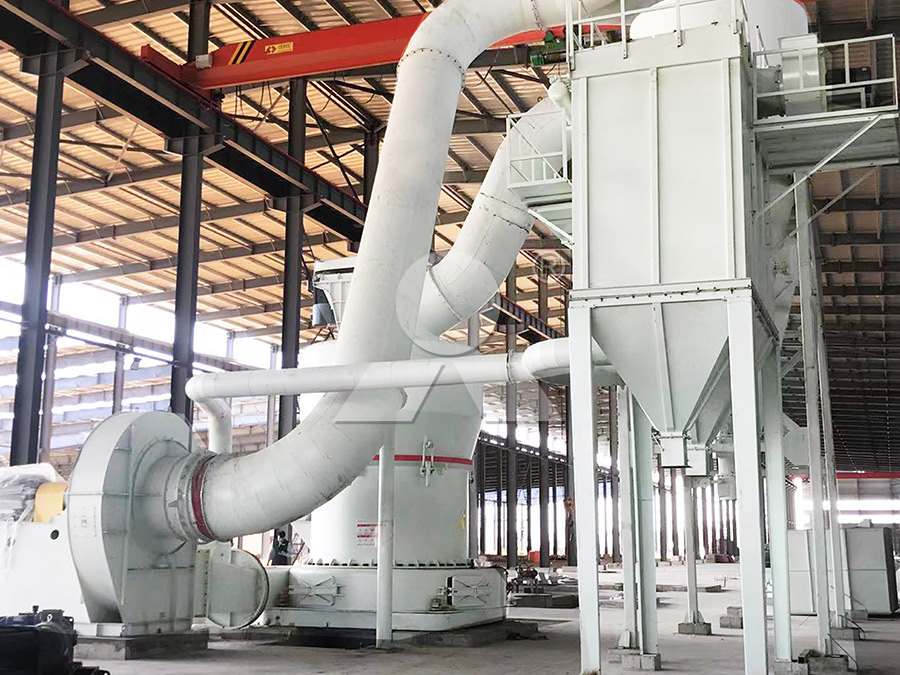
Experimental Investigation of Sintering Flue Gas Desulfurization with
SO2 Emission of sintering flue gas accounts for more than 70% of total SO2 emission of steel industry The purpose of this paper was to use steel slag for desulfurization of sintering flue gas Based on traditional circulating fluidized beds (CFB) for flue gas desulfurization (FGD), a new dry digestion CFBFGD process was developed The new process eliminated the traditional 2021年3月5日 At present, the continuous accumulation of the flue gas desulfurization (FGD) gypsum in steel plants leads to the serious environmental issues and resource waste To achieve green and sustainable development for the steel industry, it is significant to improve the usage of byproduct gypsum Employing the sintering FGD gypsum, ferric oxide, and graphite carbon Preparation of calcium ferrite by flue gas desulfurization gypsum2022年10月20日 Although more and more desulfurization equipment has been put into use in sintering plants, how to effectively remove sulfur dioxide from sintering flue gas in a desulfurization tower is still a great challenge in China Structure Optimization Research Based on Numerical 2011年7月1日 SO2 Emission of sintering flue gas accounts for more than 70% of total SO2 emission of steel industry The purpose of this paper was to use steel slag for desulfurization of sintering flue gasExperimental Investigation of Sintering Flue Gas Desulfurization
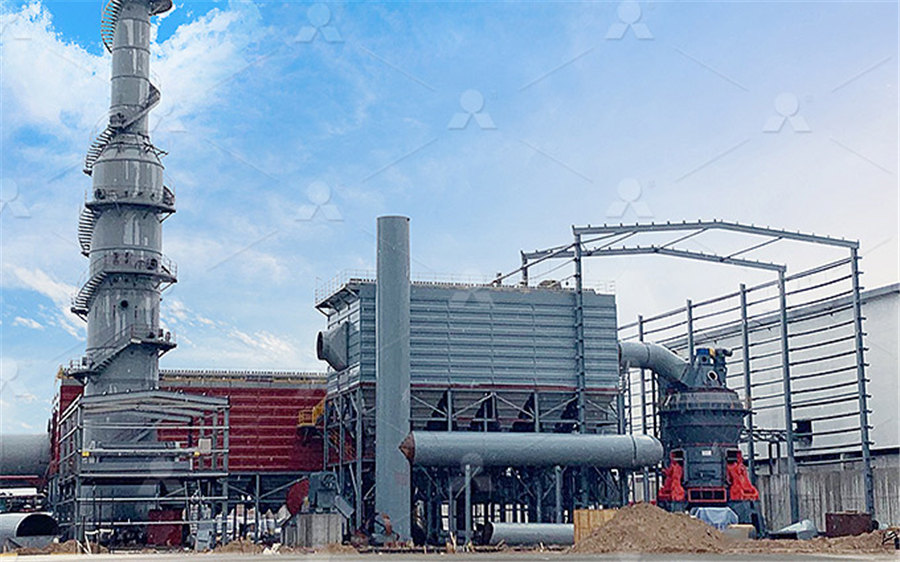
Carbothermal reduction of flue gas desulfurization ash through
2024年11月1日 Wei et al [17], [18] explored the use of subcritical hydrothermal oxidation to oxidize semidry desulfurization ash derived from iron ore sintering flue gas Under the conditions of an initial pressure of 4 MPa, a reaction temperature of 240 °C, a solid–liquid mass ratio of 1:20, and a reaction time of 90 min, the oxidation rate of CaSO 3 reached 9226 %It can be seen from Figure 1 that in the process of deep desulfurization of sintering flue gas, sodium hydroxide complex is first used to adsorb NO, O 2, and SO 2, and the adsorbed substance has the properties of H 2 O 2 and strong oxidant Then, NO 3 and SO 2 are converted to NO and SO 3 through oxidation treatment Finally, nitrite, nitrate, and sulfate ions can be Deep desulfurization of sintering flue gas in iron and steel works 2015年1月21日 The semidry desulfurization ash obtained from sintering flue gas contains a large amount of CaSO3, which has an important stabilizing influence on desulfurization ash, and thereby restricts its disposal and comprehensive utilization In order to solve this problem, lowtemperature static oxidation and hightemperature dynamic roasting were adopted for studying Oxidation modification of semidry desulfurization ash from sintering 2021年8月15日 Increasingly stringent pollutant emission standards pose a new challenge to the control of air pollutants in China's iron and steel industry (ISI) This study quantified and compared the environmental and economic effects of three typical sintering flue gas ultralow emission treatment technologies in China's ISI, namely, semidry flue gas desulfurization + semidry flue Environmental and economic impact assessment of three sintering flue
.jpg)
Recent advances in process and materials for dry desulfurization
Currently, desulfurization technologies can be categorized into three main types: wet flue gas desulfurization (FGD) [11], [12], [13], semidry desulfurization [14] and dry desulfurization [15]Wet flue gas desulfurization is widely employed in largescale desulfurization processes due to its high efficiency and low energy consumption [16]However, it poses a significant environmental 2017年11月1日 To effectively solve the problem of reutilizing semidry sintering flue gas desulfurized ash (SSFGDA) from steel plants, a new technology is proposed in this paper in which ash is added to a boiling furnace to obtain SO 2 during sulfuric acid production Using thermodynamics and simulation calculations, the hightemperature characteristics of CaSO 3 Utilization of semidry sintering flue gas desulfurized ash for SO2 2022年12月1日 Coal is widely used by energy, chemical and other enterprises as the main fuel Due to technical or management deficiencies, currently a large amount of coal is directly burned without pretreatment, which produces lots of industrial flue gas containing SO 2 and NO x (Lv et al, 2021; Sun et al, 2019; Xiaohe et al, 2021)It will cause environmental pollution and lead Simultaneous desulfurization and denitrification of flue gas 2022年12月28日 The effect of carbon dioxide (CO2) on the desulfurization of sintering flue gas with hydrate (Ca(OH)2) as an absorbent was investigated, and the formation of calcium carbonate (CaCO3) and its effect on the Effect of CO 2 on the Desulfurization of Sintering
.jpg)
Particle Conditioning for Improving Blockage Resistance of
2024年10月8日 This research provides critical technical support for the stable ultralow emission of NOx from sintering flue gas (ESP) at a steel plant in Shandong The conditioning agent was an alkaline absorbent from a specific flue gas desulfurization project The absorbent was added to the sintered fly ash in different ratios (1:0, 1:0 2017年9月8日 The removal of thallium ions in flue gas desulfurization wastewater from ferrous metallurgic industry was studied by emulsion liquid membrane (ELM) method using 2ethylhexyl phosphoric acid2ethylhexyl ester (P507) as carrier, aviation kerosene (AK) as organic solvent, polyisobutylene succinimide (T154) as surfactant, polyisobutylene (PIB) as additive, and The efficient removal of thallium from sintering flue gas 2022年10月20日 Based on the comprehensive analysis, these optimized structures are recommended in the design of an ammoniabased wet sintering flue gas desulfurization towerStructure Optimization Research Based on Numerical Simulation PDF On Oct 15, 2018, Cara Niu published Comparison of flue Gas Desulfurization Technologies Find, read and cite all the research you need on ResearchGateComparison of flue Gas Desulfurization Technologies
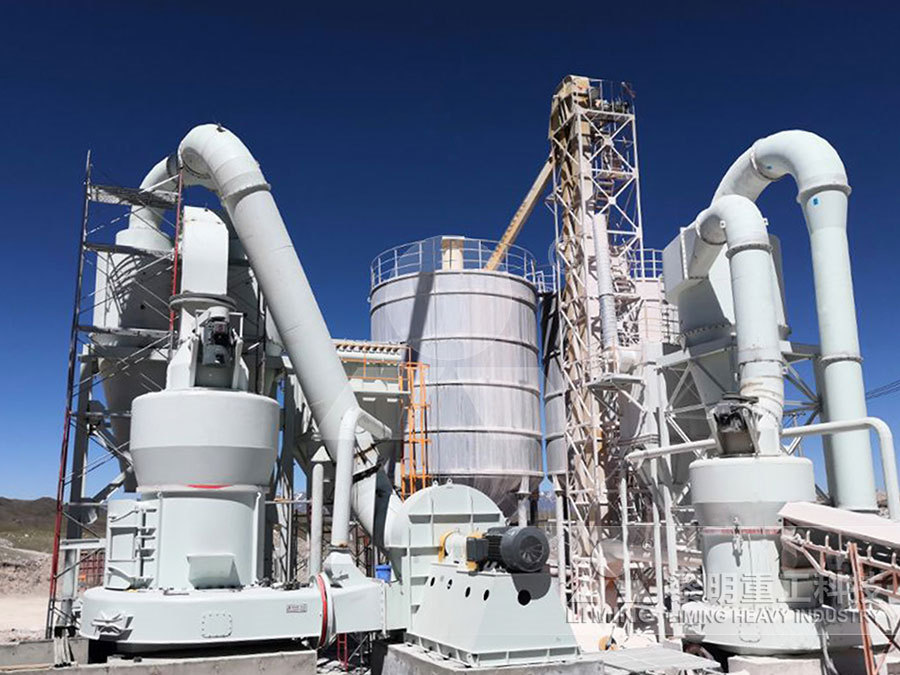
Lowtemperature oxidation behavior and mechanism of semi
2021年3月17日 Iron ore sintering is an important part of a long steelmaking process with sulfur dioxide emissions accounting for 40%–80% of the total sulfur dioxide emissions in steel companies [1,2,3,4]Semidry flue gas desulfurization technology combines the characteristics of wet and dry flue gas desulfurization processes, and it has significant advantages such as low Abstract Read online The new flue gas desulfurization system of 108m2 sintering machine is reformed, combined with the applicable scope of common desulfurization and dust removal process and the basic principles of desulfurization and dust removal process selection, the advanced and reliable rotary spray dryer absorber(SDA) technology is selected for flue gas Study on sintering flue gas desulfurization process selectionThe new flue gas desulfurization system of 108m 2 sintering machine is reformed, combined with the applicable scope of common desulfurization and dust removal process and the basic principles of desulfurization and dust removal process selection, the advanced and reliable rotary spray dryer absorber(SDA) technology is selected for flue gas desulfurization Taking the STUDY ON SINTERING FLUE GAS DESULFURIZATION PROCESS 2021年6月1日 O 3 oxidation combined with semidry process is proposed for simultaneous desulfurization and denitrification of sintering/pelletizing flue gas Some factors affecting the efficiency of denitrification and desulfurization are introduced • The reaction mechanism of desulfurization and denitrification is expounded explicitlyO3 oxidation combined with semidry method for simultaneous
.jpg)
Simultaneous desulfurization and denitrification of sintering flue gas
DOI: 101016/JCJCHE201604005 Corpus ID: ; Simultaneous desulfurization and denitrification of sintering flue gas via composite absorbent @article{Wang2016SimultaneousDA, title={Simultaneous desulfurization and denitrification of sintering flue gas via composite absorbent}, author={Jie Wang and Wenqi Zhong}, journal={Chinese Journal of Chemical