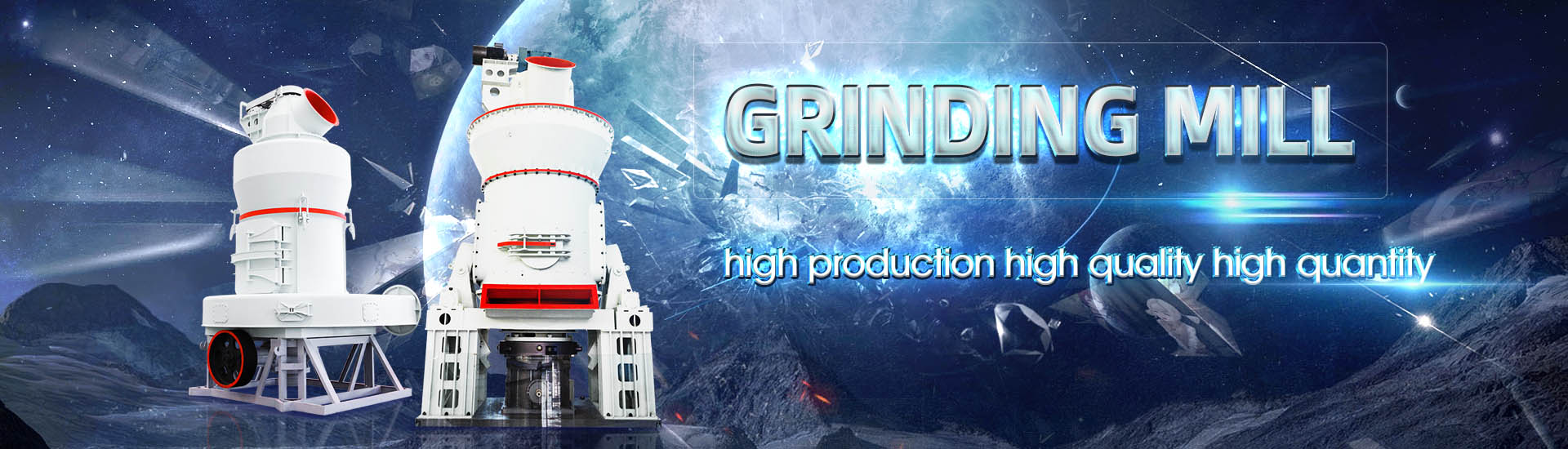
Industrial grinding mill Energysaving measures for manufacturers' equipment
.jpg)
Energy efficiency of stateoftheart grinding processes
2018年1月1日 Grinding is an essential technology used for finishing operations of many precision components, especially such made of hard and brittle materials This work presents This paper reports the results of an investigation targeting two objectives: (1) characterising energy outputs in industrial grinding mill circuits, and (2) identifying the potential for recovering Breaking Down Energy Consumption in Industry Grinding Mills2023年2月2日 These studies aim to find machining parameters that can reduce energy on the one hand (37% of researchers), including SEC, SCE, net cutting energy (NSCE), active Optimization techniques for energy efficiency in machining 2020年1月1日 Based on an energy demand breakdown of typical metal cutting machine tools, critical components with a high energy savings potential are identified These units are Energy efficient machine tools ScienceDirect
.jpg)
A review of energy consumption and minimisation
2021年8月31日 In this paper, we shall examine the review of energy consumption by machine tools and energy minimisation strategies in the manufacturing process The aim is to review the existing stateoftheart Lang, T A, “Energy Savings Potential in the Cement Industry and Special Activities of the ‘Holderbank’ Group,” in Industrial Energy Efficiency: Policies and Programmes Conference Proceedings, (May 2627, 1994), International Everything you need to know about Energy Efficiency Rotational speed: 7,500, 5,550, 12,000 rpm Output: 5 kg/h 500 kg/h Motor power: 3 kW 15 kWPrinciple Advantages The material is evenly sent to the grinding chamber by the feeding system, and receives the strong impact of the highspeed rotating grinding movable disk At the same time, it receives the action Impact mill, Impact grinding mill All industrial manufacturersThe industrial pin mill (also known as a universal mill, turbo mill, and impact mill) is a one pass grinding equipment ideal for achieving the micronization of bulk materials and powdered products Common applications involve the fine Grinding mill Palamatic Process
.jpg)
Large mill, Large grinding mill All industrial manufacturers
Other Manufacturing Equipment > Large mill Large mills 34 companies 47 products My filters large Delete all What providing users with energysaving, consumptionreducing, qualityenhancing and efficiencyenhancing solutions, The Metso Outotec® Open Ended Discharge Grinding Mill (OED Mill) Our industrial food grinding equipment reduces the size of dry foods and spices to uniform sizes, resulting in high yields and cost savings at rates up to 10,000 Kg/Hr Contact; MPE food grinding equipment and granulation equipment are the leading choice of food manufacturers who need sanitary, Industrial Food Grinding and Granulation Equipment MPEFor over 60 years, CITIC Heavy Industries (CITIC HIC) has focused on providing global customers with reliable, energysaving and highefficiency mineral grinding equipment relying on its advantages of technological development strength, core manufacturing expertise, strict quality control measures and excellent customer serviceGrinding Mills Mineral Processing Equipment CITIC HIC2023年9月18日 We're talking about the improvement of energy efficiency in feed mill grinding systems What feed mills should be on the lookout for when they're selecting this equipment, and what kind of savings they can expect by implementing a more energyefficient grinding processSustainable grinding and energy savings in feed mills [Podcast]
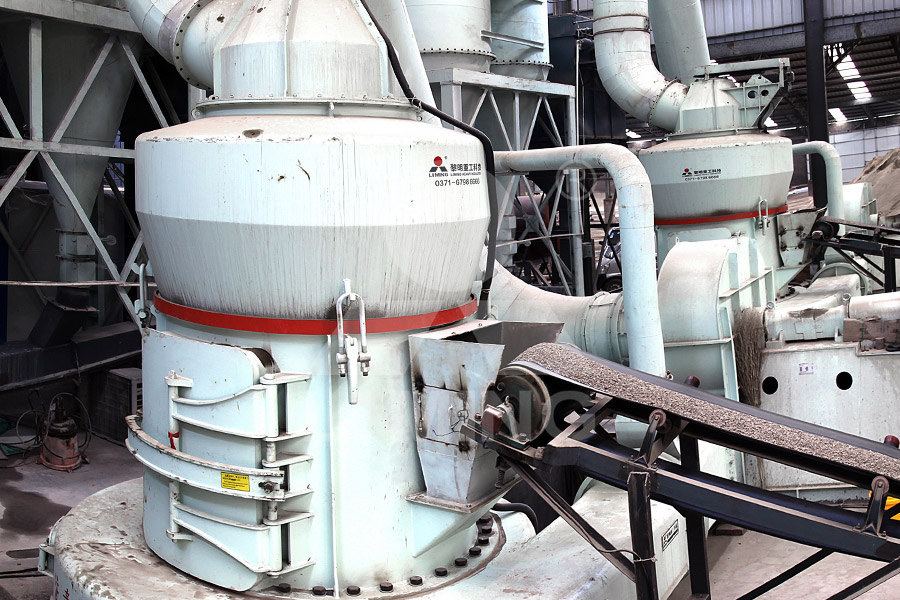
ENERGY SAVINGS AND TECHNOLOGY COMPARISON USING SMALL GRINDING
A regrind ball mill with a mix of small grinding media can be as energy effi cient as an Isa Mill charged with 25 and 35 mm beads In vertical stirred mills, energy savings vary from 30 per cent to 60 per cent To carry out the same fi nal grind, a vertical stirred mill with Millpebs will consume at least 60 per cent less energy than a ball BREAKING DOWN ENERGY CONSUMPTION IN INDUSTRIAL GRINDING MILLS *Jocelyn Bouchard1, Gilles LeBlanc2, Michelle Levesque3, Peter Radziszewski4, and David GeorgesFilteau1 1 Université Laval BREAKING DOWN ENERGY CONSUMPTION IN INDUSTRIAL GRINDING MILLSsmall grinding media represents the best potential to improve grinding efficiency How do the small grinding media perform in industrial grinding mills? The use of small grinding media in regrind mills proved that finer grinding can be achieved at lower energy consumption In ball mills, smaller grinding media versus 25 mm media generate aEnergy Savings and Improved Recovery with Small Grinding MediaThis document provides an overview of energy savings measures that can be implemented in cement industries It reviews previous studies on reducing energy consumption, carbon dioxide emissions, and improving energy efficiency in An Overview of Energy Savings Measures For Cement
.jpg)
Making Your Cement Grinding Plant Energy Saving
The grinding mill has a small length to diameter ratio, poor wear resistance, long grinding time, and low work efficiency The working efficiency of the cement separator is low so that the micro powder with particle size between 3 and Final grain size: 74 µm 400 µm Rotational speed: 21 rpm Output: 16 t/h 50 t/h Ball mill is common used grinding plant in the industry, and it is key equipment used for milling after materials are crushed This machine can be can grind all kinds of ores and other materials, which is widely used Mill, Grinding mill All industrial manufacturers2023年11月1日 Grinding operation is the last preparation stage before beneficiation In this stage, the material undergoes the combined action of impact and grinding, so that the ore particle size is diminished and the qualified materials is provided for succeeding beneficiation operations [1, 2]Generally, the quality of the grinding product is also an important factor to determine the Energy conservation and consumption reduction in grinding 2013年3月10日 Download Citation An overview of energy savings measures for cement industries Due the advances in the industrial processes, in which the cement industry is a major contributor, energy An overview of energy savings measures for cement industries
.jpg)
Energy Saving: A Quick Start Guide for Small and Medium Manufacturers
More than onethird of the energy consumed in the United States (more than $200 billion a year) is used to power our manufacturing plants and industrial factories Saving energy can lead to cost savings and strengthen the company’s manufacturing competitiveness2022年6月20日 Our guide to 13 energysaving tips for manufacturers explores how manufacturers can make small changes which can have a big impact on our energy usage Read Our Reviews Units 5/6 Drake Mill Business Park, Estover Road, Plymouth, PL6 7PS13 Energy Saving Tips for Manufacturers Trends Rowse2016年5月7日 The measures include process optimisation through inhouse modifications of equipment for the enhancement of energy efficiency, the use of medium voltage drives and gridresistance regulators in all high tension motors of most of the process fans (that is, preheater fans, ESP fans, coal mill fans), arresting of leakages to reduce fan electrical loads and process Power Savings: Cement manufacturers take measures to reduce energy Both energy efficiency and energy conservation are important to saving energy While different plants can save energy through oneoff conservation and efficiency efforts, we recommend developing an energy management system The DOE’s approach to energy management is aligned with the ISO 50001:2018 Energy Management StandardSaving Energy: A QuickStart Guide for Small to Medium Manufacturers
.jpg)
Energy Conservation Measures In Kiln For Clinker Production
Abstract:This study was aim to identify and explain the energy conservation measures in kiln for clinker production For better energy efficiency in kiln, requires the implementation of energy conservation measures in kiln in order for optimum performance and energy saving of kiln The cement process, have three stages andproductivity and greater reduction in energy costs for grinding by about 40 % Therefore we define these new grinding bodies as energy saving bodies Keywords—innovative grinding bodies, spherical grinding bodies, Drum Mill, energy saving bodies 1Introduction Since 1864 in the USA and since 1867 in Germany has began grinding ofIndustrial Tests with Innovative Energy Saving Grinding Bodies2022年1月30日 The Morrell method for predicting the specific energy consumption of conventional crushing, High Pressure Grinding Rolls (HPGRs), and tumbling mill equipment is well known and widely applied in TheMorrellMethodtoDeterminetheEfficiencyof 2013年7月15日 The energy saving resulting from the replacement of cyclones with screens in a closed ball mill circuit was estimated to be in the range of 10 to 25% (Jankovic and Valery, 2012a) An analysis of the(PDF) Energy Efficient Ball Mill Circuit – Equipment
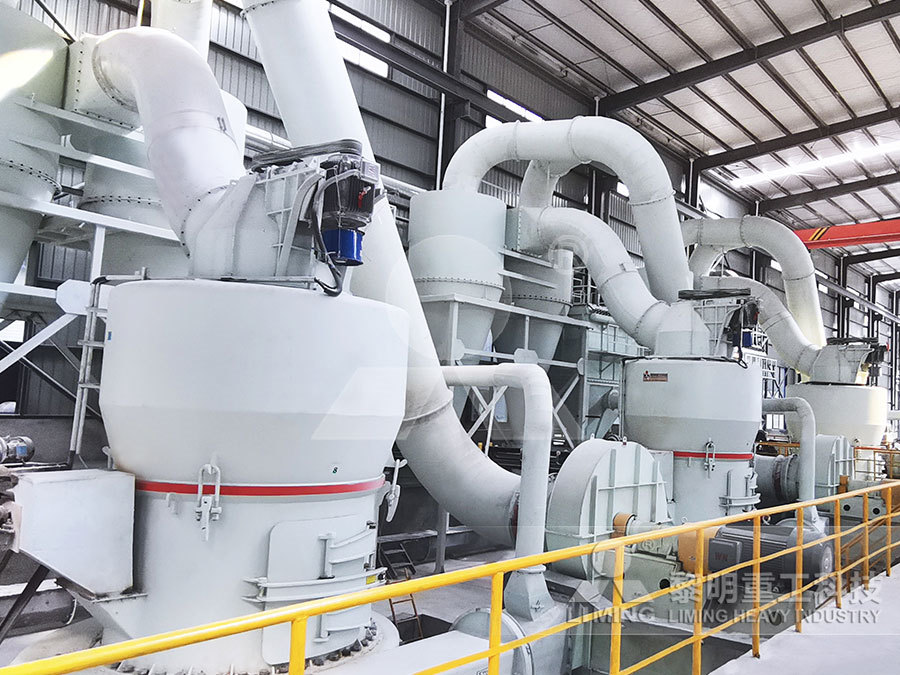
High Pressure Grinding Roll and Magnetic Separation for Energy Saving
2024年5月31日 This paper presents an industrial verification test, adding a high pressure grinding roll and magnetic separation operation after the thirdstage fine crushing operation to reduce the particle size of ball mill feed and improve the processing capacity of grinding operation The optimal process parameters of high pressure grinding roll and magnetic separation were 3RZGHU 7HFKQRORJ\ t directly measure the work of the mill from the data The specific productivity was calculated by EqEnergy conservation and consumption reduction in grinding Energy Pricing CAD/kWh 0045 0045 Grinding Media Pricing CAD/t 1,000 1,250 Energy Cost kCAD/year Grinding Media Cost kCAD/year Total Cost kCAD/year Annual Savings of nearly 143,000 CAD/year 2,736 3,078 1,215 729 3,951 3,807Energy Efficiency Comparison in Fine Grinding in the Mining Conclusions Comparisons between different energyefficient grinding technologies and applications were presented for production of cement with energy savings Industrialscale data related to Horomill® and Polysius® HPGR/twocompartment ball mill circuit provided insights in‐ to the operational and sizereduction characteristics of Horomill EnergyEfficient Technologies in Cement Grinding Academia
.jpg)
Industrial validation of the functional performance equation for
mill Then, the ratio of the plant mill specific grinding rate (SGRC) of coarse material to the standardized lab millgrinding rate (LabGr) of coarse material will be a relative measure of the efficiency of usage of this energy that is being applied to coarse material (the efficiency of the mill grinding environment)Find your roller mill easily amongst the 185 products from the leading brands (WAMGROUP, Brabender, LONGI, ) on DirectIndustry, the industry specialist for your professional purchasesRoller mill, Roller grinding mill All industrial manufacturers2012年1月1日 The industrial sector accounts for 40% of global energy use In 1995, developing countries used an estimated 48 EJ for industrial production, over onethird of world total industrial primary Energy Savings Measures for Clinker Production in Cement IndustryLang, T A, “Energy Savings Potential in the Cement Industry and Special Activities of the ‘Holderbank’ Group,” in Industrial Energy Efficiency: Policies and Programmes Conference Proceedings, (May 2627, 1994), International Everything you need to know about Energy Efficiency
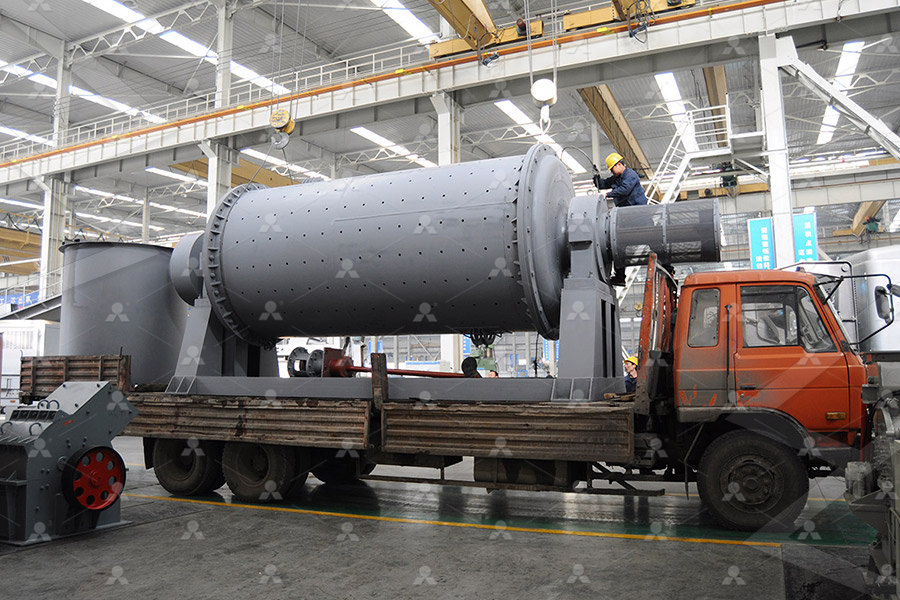
Impact mill, Impact grinding mill All industrial manufacturers
Rotational speed: 7,500, 5,550, 12,000 rpm Output: 5 kg/h 500 kg/h Motor power: 3 kW 15 kWPrinciple Advantages The material is evenly sent to the grinding chamber by the feeding system, and receives the strong impact of the highspeed rotating grinding movable disk At the same time, it receives the action The industrial pin mill (also known as a universal mill, turbo mill, and impact mill) is a one pass grinding equipment ideal for achieving the micronization of bulk materials and powdered products Common applications involve the fine Grinding mill Palamatic ProcessOther Manufacturing Equipment > Large mill Large mills 34 companies 47 products My filters large Delete all What providing users with energysaving, consumptionreducing, qualityenhancing and efficiencyenhancing solutions, The Metso Outotec® Open Ended Discharge Grinding Mill (OED Mill) Large mill, Large grinding mill All industrial manufacturersOur industrial food grinding equipment reduces the size of dry foods and spices to uniform sizes, resulting in high yields and cost savings at rates up to 10,000 Kg/Hr Contact; MPE food grinding equipment and granulation equipment are the leading choice of food manufacturers who need sanitary, Industrial Food Grinding and Granulation Equipment MPE
.jpg)
Grinding Mills Mineral Processing Equipment CITIC HIC
For over 60 years, CITIC Heavy Industries (CITIC HIC) has focused on providing global customers with reliable, energysaving and highefficiency mineral grinding equipment relying on its advantages of technological development strength, core manufacturing expertise, strict quality control measures and excellent customer service2023年9月18日 We're talking about the improvement of energy efficiency in feed mill grinding systems What feed mills should be on the lookout for when they're selecting this equipment, and what kind of savings they can expect by implementing a more energyefficient grinding processSustainable grinding and energy savings in feed mills [Podcast]A regrind ball mill with a mix of small grinding media can be as energy effi cient as an Isa Mill charged with 25 and 35 mm beads In vertical stirred mills, energy savings vary from 30 per cent to 60 per cent To carry out the same fi nal grind, a vertical stirred mill with Millpebs will consume at least 60 per cent less energy than a ball ENERGY SAVINGS AND TECHNOLOGY COMPARISON USING SMALL GRINDING BREAKING DOWN ENERGY CONSUMPTION IN INDUSTRIAL GRINDING MILLS *Jocelyn Bouchard1, Gilles LeBlanc2, Michelle Levesque3, Peter Radziszewski4, and David GeorgesFilteau1 1 Université Laval BREAKING DOWN ENERGY CONSUMPTION IN INDUSTRIAL GRINDING MILLS
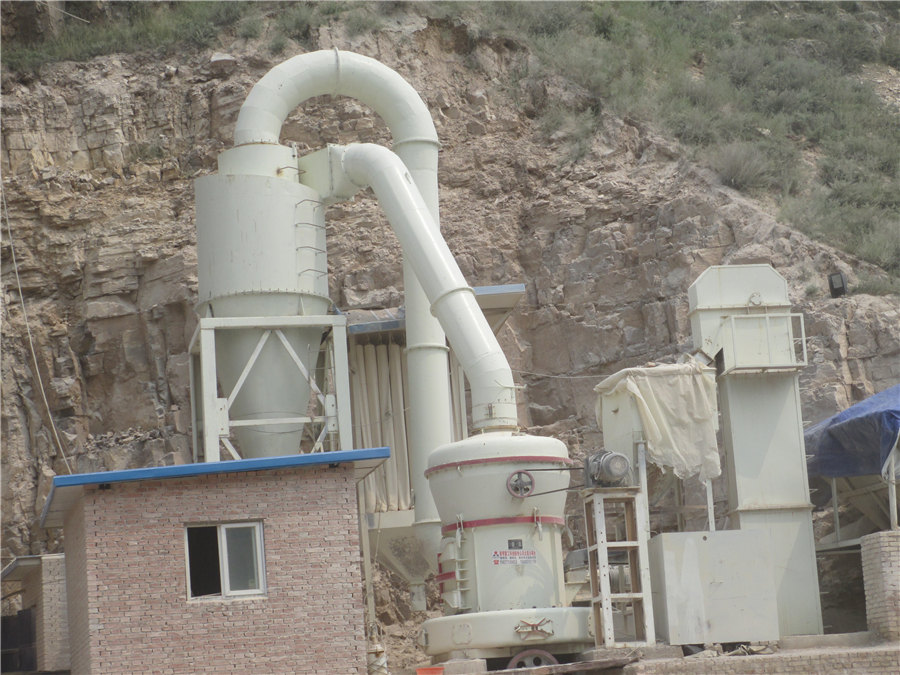
Energy Savings and Improved Recovery with Small Grinding Media
small grinding media represents the best potential to improve grinding efficiency How do the small grinding media perform in industrial grinding mills? The use of small grinding media in regrind mills proved that finer grinding can be achieved at lower energy consumption In ball mills, smaller grinding media versus 25 mm media generate a