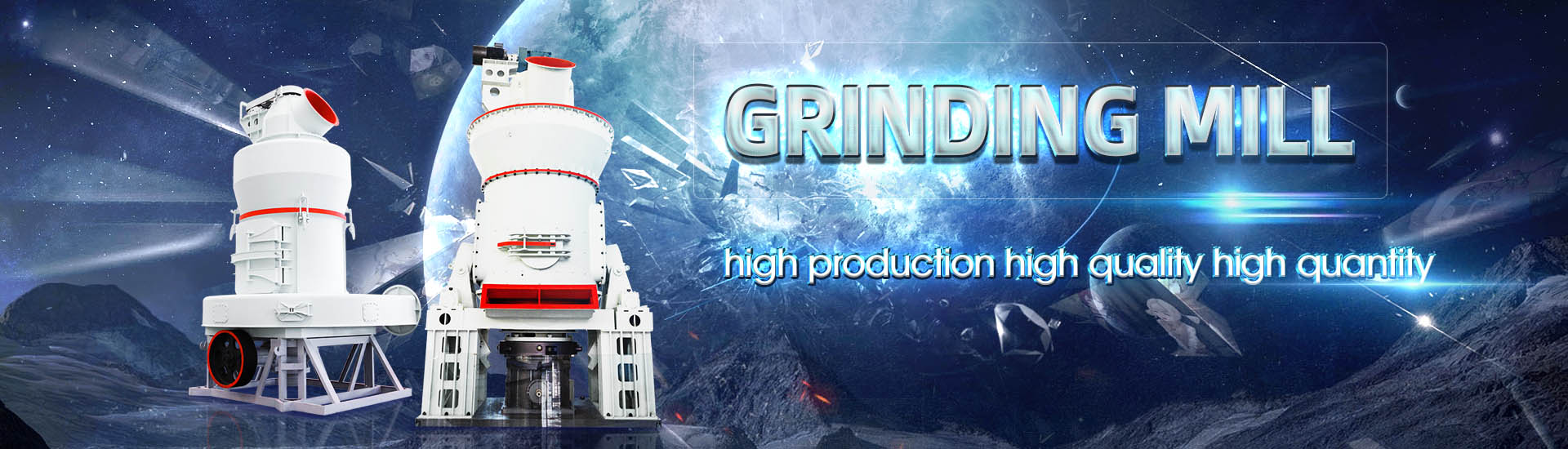
HOME→Annual summary of cement plant raw material workshop Annual summary of cement plant raw material workshop Annual summary of cement plant raw material workshop
Annual summary of cement plant raw material workshop Annual summary of cement plant raw material workshop Annual summary of cement plant raw material workshop

Online Database of Cement Plants International Cement Review
Welcome to The Global Cement Report™ online database of cement plants This resource contains listings of over 2618 facilities worldwide (excluding China), and is the most uptodate Vietnam Online Database of Cement Plants International Cement ReviewVietnam2023年10月13日 For instance, the US Geological Survey provides data on the production and consumption of cement in the United States, while the World Cement Association (WCA) Global database of cement production assets and upstream Cement is the most essential construction material that acts as a binding agent for concrete, laying bricks and more From limestone to clay and supplementary additives, each ingredient Explore Raw Material Used For Cement Production JK Cement
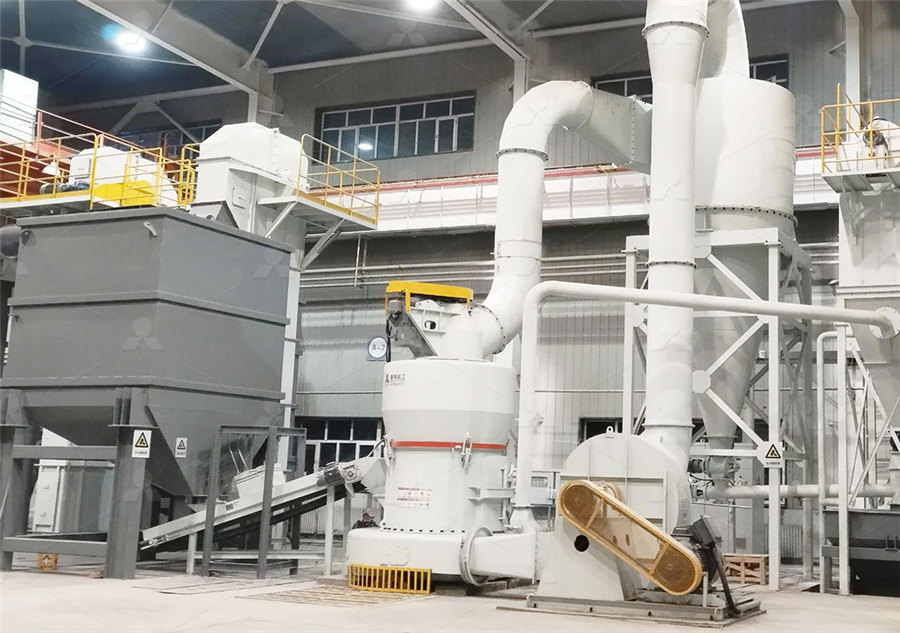
The Cement Plant Operations Handbook International Cement
The Cement Plant Operations Handbook is a concise, practical guide to cement manufacturing and is the standard reference used by plant operations personnel worldwide Providing a Learn about the raw mill in cement plants and the basic raw materials used in cement manufacturing Discover our efficient cement manufacturing process Contact us for more info!Raw Mill in Cement Plant Cement Manufacturing Raw MaterialsCement production is one of the largest industries in the world Annual world production in 2013 was approximately 4 GT (of which, about half was in China) It is produced in kilns at around Cement Production an overview ScienceDirect TopicsThe most important raw materials for making cement are limestone, clay, and marl These are extracted from quarries by blasting or by ripping using heavy machinery Extracting raw How cement is made Heidelberg Materials
.jpg)
How Cement is Made Portland Cement Association
Cement producers are constantly pursuing innovative, efficient, and environmentally responsible ways of producing highquality cement to realize carbon neutrality across the concrete value 2020年9月16日 Our reference plant is a fivestage preheatercalciner kiln with a vertical raw mill and two cement ball mills It has an annual production capacity of one million metric tons of Digitization and the future of the cement plant McKinseyPortland cement composition varies from plant to plant due to both cement specifications and the mineralogy of available materials A desirable raw mix is one that minimises both the heat input required for clinkering and total raw Cement Plant Raw materials INFINITY FOR CEMENT Introduction Setting up a cement plant involves numerous components and stages, each contributing significantly to the overall cost This detailed guide will break down the costs associated with each component and stage of a cement The Comprehensive Guide to Cement Plant Costs: An
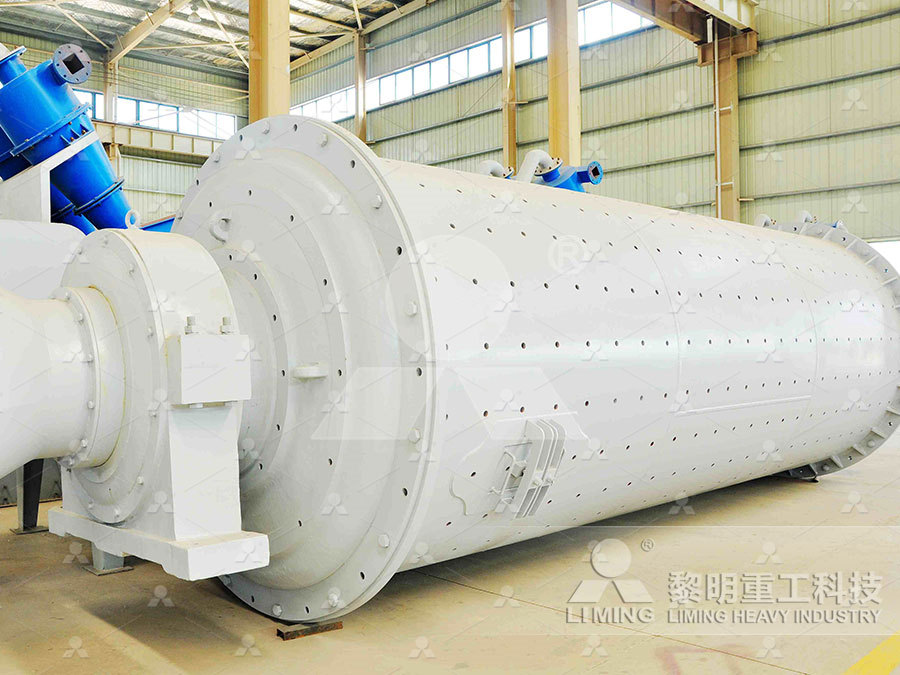
From raw materials Extracting raw materials Raw material
with the extraction of raw materials and ending with the finished product From raw materials to cement Extracting raw materials Crushing and transportation Raw material preparation I: Storage and homogenisation Raw material preparation II: Drying and raw grinding Burning The burning of the raw meal at approx 1,450°C is carried outIn the building and construction sector, Portland cement (PC) is the main binder in the production of concrete Its production uses 16 tonnes of raw materials, principally quartz and limestone TABLE 1 Summary of the main cement types, composition, and raw2015年8月1日 The results show that approximately 248t, 469t, and 341t of materials are required to produce a ton of the product in raw material preparation, clinker production, and cement grinding stages (PDF) Analysis of material flow and consumption in cement production 2024年11月23日 Cement Extraction, Processing, Manufacturing: Raw materials employed in the manufacture of cement are extracted by quarrying in the case of hard rocks such as limestones, slates, and some shales, with the aid of blasting when necessary Some deposits are mined by underground methods Softer rocks such as chalk and clay can be dug directly by Cement Extraction, Processing, Manufacturing Britannica
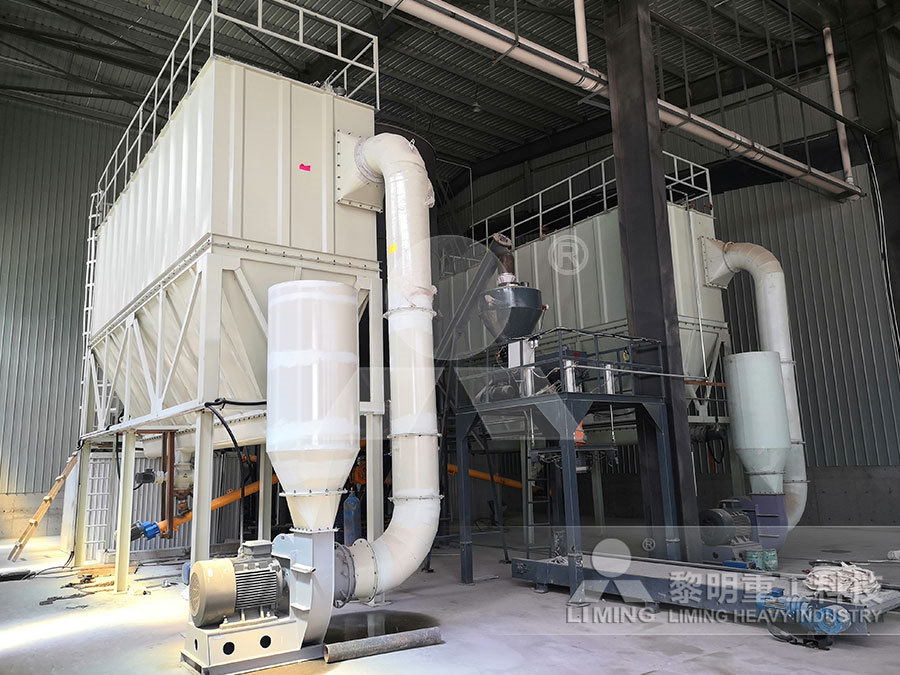
Explore Raw Material Used For Cement Production JK Cement
The production of raw cement involves the extraction and procurement of raw materials like limestone and clay or iron ore These materials are then crushed and finely ground to form the raw mix The raw mix is then subjected to hightemperature heating in a kiln, reaching temperatures around 1400°C in a process called clinker2020年9月16日 When envisioning the cement plant of the future, it is important to understand the reference for a typical plant today Our reference plant is a fivestage preheatercalciner kiln with a vertical raw mill and two cement ball mills It has an annual production capacity of one million metric tons of cement and produces several types of cementDigitization and the future of the cement plant McKinseyRaw material preparation I: storage and homogenisation The crushed material is transported into the raw material storage of the cement plant by conveyorbelts, cableways or railways and also in exceptional cases with trucks Once there it is stored in blending beds and homogenisedHow cement is made Heidelberg MaterialsRaw material blending is an important process affecting cement quality The aim of this process is to mix a variety of materials such as limestone, shale (clay), sandstone and iron to produce The cement raw material blending process and its control system
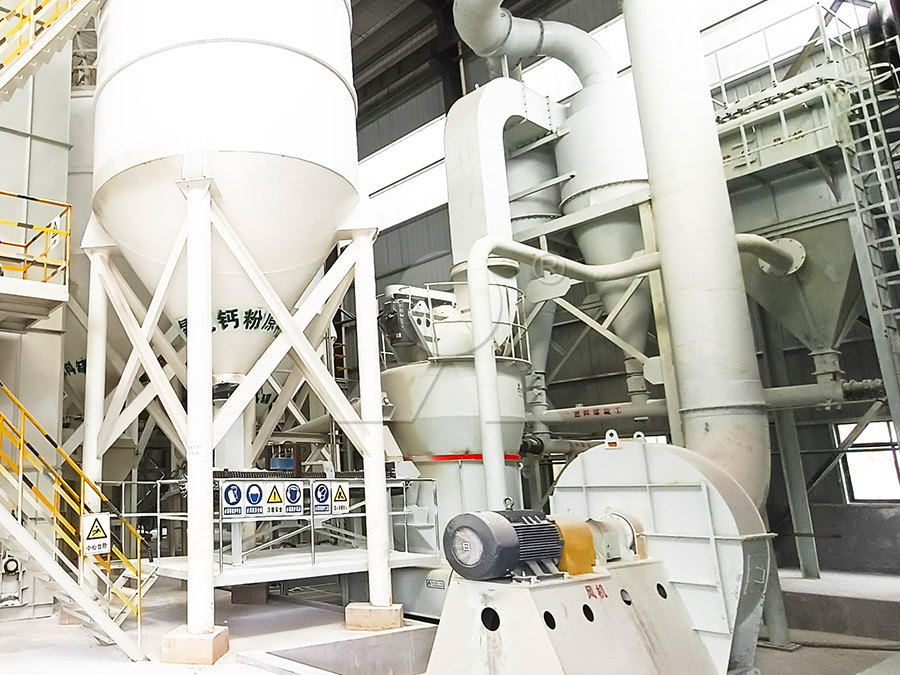
Linear Programming as a Tool to Design the MIX of Cement Plant Raw
This study uses linear programming to develop a methodology for selecting the best raw material mix in an ASCOM cement plant in Egypt In cement factories, this type adheres to Egyptian chemical composition criteria for raw feed (eg 825% calcium carbonate, 1408% silica, 25% alumina and 092% iron oxide)ESIA Summary: Greenfield Derba Cement Project: DMC, Ethiopia 2 OPC shall be produced as per CEMI 425 grade and shall contain 95% clinker and 5% gypsum PPC shall be produced as per CEMII 325 grade and shall contain 67% clinker, 28% pumice and 5% gypsum The annual cement capacity of the plant shall be 246 million tonnes per annumETHIOPIA ESIA Derba Midroc Cement Project African contractor for the cement plant The cement manufacturing process involves six steps, as shown diagrammatically in Erreur ! Source du renvoi introuvable: 1Raw material preparation, blending and storing: Raw material transported from the quarry will be crushed, blended in the required proportions and stockpiled in a storage area beforeDRC Nyumba Ya Akiba Cement Plant ESIA SummaryStage of Cement Manufacture There are six main stages of the cement manufacturing process Stage 1: Raw Material Extraction/Quarry The raw cement ingredients needed for cement production are limestone (calcium), sand and clay (silicon, aluminum, iron), shale, fly ash, mill scale, and bauxite The ore rocks are quarried and crushed into smaller pieces of about 6 inchesHow Cement is Made Cement Manufacturing Process
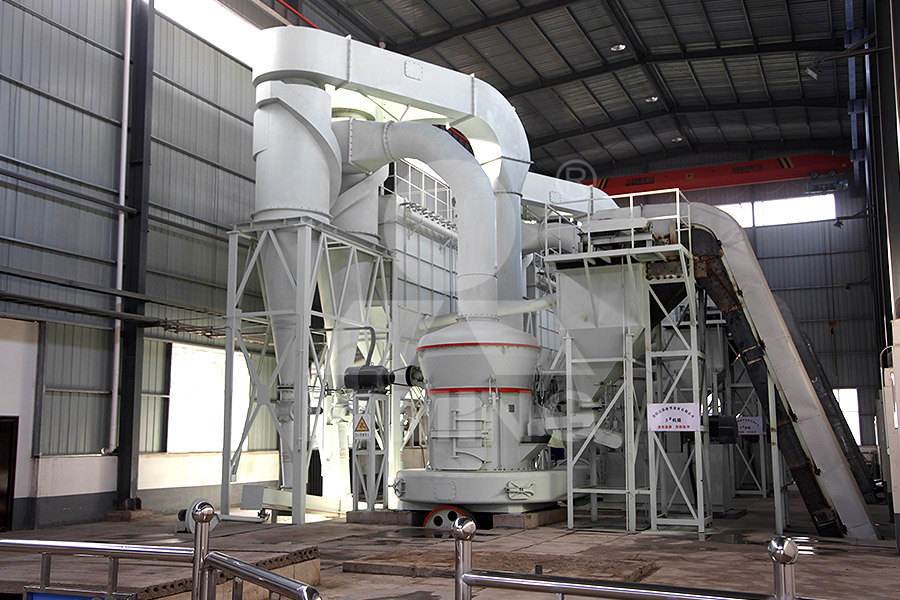
Cement Manufacturing Plant Report 2024: Setup and Cost
Report Overview: IMARC Group’s report titled “Cement Manufacturing Plant Project Report 2024: Industry Trends, Plant Setup, Machinery, Raw Materials, Investment Opportunities, Cost and Revenue” provides a complete roadmap for setting up a cement manufacturing plant It covers a comprehensive market overview to microlevel information such as unit operations involved, 2022年1月15日 Cement industry uses a number of wastes and byproducts as supplementary raw materials in cement raw mix which are referred to as alternative raw materials Industrial and mineral wastes from mineral processing industries, such as metallurgy, petrochemicals, chemicals, paper and pulp account for nearly 275 million tonnes per annumUtilisation of Alternative Fuels and Raw Materials in Indian Cement 2020年8月25日 Cement raw material preparation: Limestone is main raw materials for cement manufacturing, and most cement plants are located next to the quarry to reduce the transportation cost; Using explosion or getter loader to mine raw materials; sending raw materials to the cement crusher to crush or hammer; crushed raw materials are stored to prevent from environment Cement Production Process Cement Manufacturing Process AGICO CEMENT2019年4月23日 Introduction Portland cement underpins modern global development As such, it is the most abundantly produced material in the world (Deolalkar Citation 2016)The world has an abundance of the primary raw materials for cement manufacturing and, compared to other construction materials, cement’s cost is low and it has good durability (Hewlett Citation 2003)An overview of alternative raw materials used in cement and
.jpg)
Cement substitution with secondary materials can reduce annual
2022年9月30日 Cement production has more than doubled over the last two decades, from 180 Gt in 2002 to 405 Gt in 2018 (Fig 2), due mainly to socioeconomic development in China (064 Gt in 2002 to 22 Gt in TITAN Group Integrated Annual Report 2016 Summary 3 Cimento Apodi operates an integrated cement plant and a grinding plant in the state of Ceará in Northeast Brazil, with a production capacity of over 2 million tons of cement per year Current demand for building materials in Brazil is low; however, the fundamentals in terms of urbanIntegrated Annual Report 2016 SUMMARY Titan CementTop 10 cement groups in India Source: Survey of Cement Industry Directory Rank Company Cement Capacity MTPA Share % 1 Ultratech Cement Limited 11440 21% 2 Lafarge Holcim India (ACC + Ambuja) 6270 12% 3 Shree Cement Limited 4340 8% 4 Dalmia Bharat Limited 3075 6% 5 Nuvoco Vista Corp Limited 2232 4% 6 The Ramco Cements Limited 1940 4%The Ramco Cements Limited Corporate Presentation2016年11月30日 R Murthy and Santhosh Kumar M elaborate on the use of stackers and reclaimers used in cement industry for feeding raw materials Stacking raw materials/fuels and reclaiming them is an essential part of Raw material stacking and reclaiming Indian
.jpg)
(PDF) The Cement Industry in Ethiopia ResearchGate
2018年8月17日 According to an Ethiopian Ministry of Industry report, the country has a high expected cement consumption due to a rapid urbanization (43%), high rate of population growth (26%), a substantial Cement Kiln and Waste to Energy Incineration of Spent Media Craig Patterson1, Seyed A Dastgheib2 1US Environmental Protection Agency, Center for Environmental Solutions and Emergency Response 2Illinois State Geological Survey, University of Illinois at UrbanaChampaign THERMAL TREATMENT OF PFAS STATE OF THE SCIENCE WORKSHOP US Portland Cement Industry: Plant Information Summary2024年4月4日 When planning to start a cement manufacturing plant, estimating the cost is a crucial step However, the cost of setting up a cement manufacturing plant can vary widely depending on several factors, including the location, scale of production, raw material availability, technology used, and market demandUnveiling Cement Manufacturing Plant Costs OsumCement plants strive for consistent raw material quality with minimal chemistry deviation to ensure stable process operations, minimize production costs and meet product specification Continual monitoring and control of mining operations, stockpile blending and raw material proportioning helps cement producers optimize quarry lifetime, reduce waste, ensure quality product and Online Material Analysis for Cement Production FAQs

Characterization of raw materials and final product in the cement
2018年12月18日 Cement is a hydraulic binder formed by the grinding process of cement clinker, as intermediate product, which is produced by baking the limeclay raw material mixture to the sintering temperatureLimestone is the fundamental ore and basic raw material used in manufacturing cement Its significance lies in its high calcium content, essential for the chemical reactions that occur in the cementmaking process Limestone's composition makes it indispensable in the production of highquality cement 4 Which raw material provides calcium in A Complete Guide on Cement Raw Materials UltraTech CementLimited and Mustehkam Cement plant in District Haripur The annual production of cement in NWFP is about tons [5] All these cement plants produce high strength Portland cement and sulfate resisting cement Until now there is no plant in our province which is producing white cement due to the lack of raw material Therefore white Investigation of Raw Material for the Manufacturing of White Cement 2016年5月27日 4 PREFACE The first edition of this handbook appeared to find some use within the Industry and we are encouraged to revise and expand the material As previously noted, while there are a number of excellent books covering plant design, process engineering, and cement chemistry, there is a fair ly sparse literature addressing cement plant operations and little to cementplantoperationhandbook PDF SlideShare
.jpg)
Cement Plant Raw materials INFINITY FOR CEMENT
Portland cement composition varies from plant to plant due to both cement specifications and the mineralogy of available materials A desirable raw mix is one that minimises both the heat input required for clinkering and total raw Introduction Setting up a cement plant involves numerous components and stages, each contributing significantly to the overall cost This detailed guide will break down the costs associated with each component and stage of a cement The Comprehensive Guide to Cement Plant Costs: An with the extraction of raw materials and ending with the finished product From raw materials to cement Extracting raw materials Crushing and transportation Raw material preparation I: Storage and homogenisation Raw material preparation II: Drying and raw grinding Burning The burning of the raw meal at approx 1,450°C is carried outFrom raw materials Extracting raw materials Raw material In the building and construction sector, Portland cement (PC) is the main binder in the production of concrete Its production uses 16 tonnes of raw materials, principally quartz and limestone TABLE 1 Summary of the main cement types, composition, and raw
.jpg)
(PDF) Analysis of material flow and consumption in cement production
2015年8月1日 The results show that approximately 248t, 469t, and 341t of materials are required to produce a ton of the product in raw material preparation, clinker production, and cement grinding stages 2024年11月23日 Cement Extraction, Processing, Manufacturing: Raw materials employed in the manufacture of cement are extracted by quarrying in the case of hard rocks such as limestones, slates, and some shales, with the aid of blasting when necessary Some deposits are mined by underground methods Softer rocks such as chalk and clay can be dug directly by Cement Extraction, Processing, Manufacturing BritannicaThe production of raw cement involves the extraction and procurement of raw materials like limestone and clay or iron ore These materials are then crushed and finely ground to form the raw mix The raw mix is then subjected to hightemperature heating in a kiln, reaching temperatures around 1400°C in a process called clinkerExplore Raw Material Used For Cement Production JK Cement2020年9月16日 When envisioning the cement plant of the future, it is important to understand the reference for a typical plant today Our reference plant is a fivestage preheatercalciner kiln with a vertical raw mill and two cement ball mills It has an annual production capacity of one million metric tons of cement and produces several types of cementDigitization and the future of the cement plant McKinsey
.jpg)
How cement is made Heidelberg Materials
Raw material preparation I: storage and homogenisation The crushed material is transported into the raw material storage of the cement plant by conveyorbelts, cableways or railways and also in exceptional cases with trucks Once there it is stored in blending beds and homogenisedRaw material blending is an important process affecting cement quality The aim of this process is to mix a variety of materials such as limestone, shale (clay), sandstone and iron to produce The cement raw material blending process and its control system