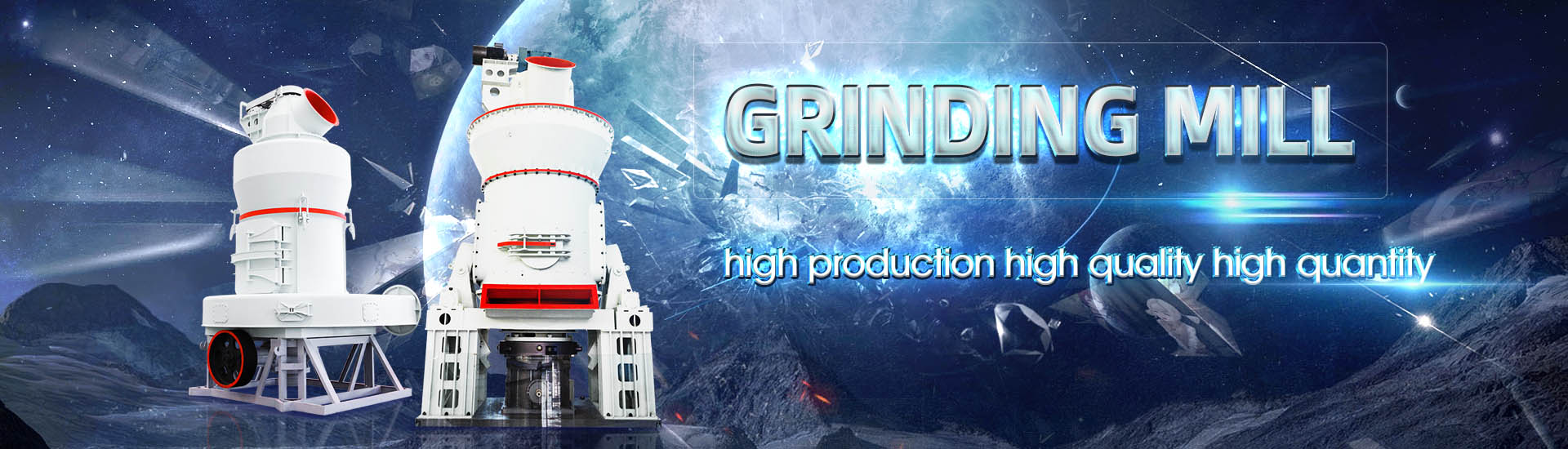
Cement Coal Mill CO Outlet Control Temperature
.jpg)
Modeling and Control of Coal Mill
In this paper, both the outlet temperature and pulverised coal flow is controlled with the help of MPC controller to overcome the drawbacks of PID The outlet temperature is controlled by manipulating the inlet primary air temperature and the pulverised coal flow is controlled by In this paper, we present a Model Predictive Control (MPC) based strategy to address the complex problem of coal mill outlet temperature control, which requires the collaborative Multiobjective Optimization of Coal Mill Outlet Temperature We propose an outlet temperature control strategy for coal mills, grounded in the MPC framework, utilizing the ARX for temperature prediction Its lower computational complexity alleviates the MultiObjective Optimization of Coal Mill Outlet Temperature Poor dynamic performance of coal mill causes difficulties in maintaining the frequency, boiler pressure and temperature of the plant This paper presents development and validation of coal Modeling and outlet temperature control of coal mill using Model
.jpg)
Modeling and outlet temperature control of coal mill using Model
2013年8月1日 Poor dynamic performance of coal mill causes difficulties in maintaining the frequency, boiler pressure and temperature of the plant This paper presents development and 2023年6月1日 Uniform coal feeding mass flow rate and required particle size and temperature at the outlet channel throughout with better classifier performance are crucial indicators that Multiobjective Optimization of Coal Mill Outlet Temperature 2015年11月1日 Coal mills are bottleneck in coal–fired power generation process due to difficulty in developing efficient controls and faults occurring inside the mills In this paper, a dynamic A unified thermomechanical model for coal mill operationIn this paper, a sliding mode control method for calciner outlet temperature via regression modeling is proposed, aiming at the problem of cement calciner outlet temperature control Sliding mode control for calciner outlet temperature via regression
.jpg)
An investigation of performance characteristics and
2020年8月12日 Obtained results indicate that grinding pressure, primary air (PA) temperature and mill motor current have a tendency to rise by increasing coal feeding mass flow rates for all used coal2020年9月9日 To achieve calcination temperature between 860 °C and 950 °C, according to (1), additional heat must be provided which is mostly (up to 70%) achieved by burning a primary Identification and Control of Precalciner in the Cement PlantExample Chekka, clinker temperature > 150°C with coal, Actions to control drying when no external heat source available For a cement mill: intermediate or outlet diaphragm For the case of; cement mills with a drying chamber see Everything you need to know about clinker/cement Download scientific diagram Effect of mill outlet temperature on the coal moisture content from publication: An investigation of performance characteristics and energetic efficiency of vertical Effect of mill outlet temperature on the coal
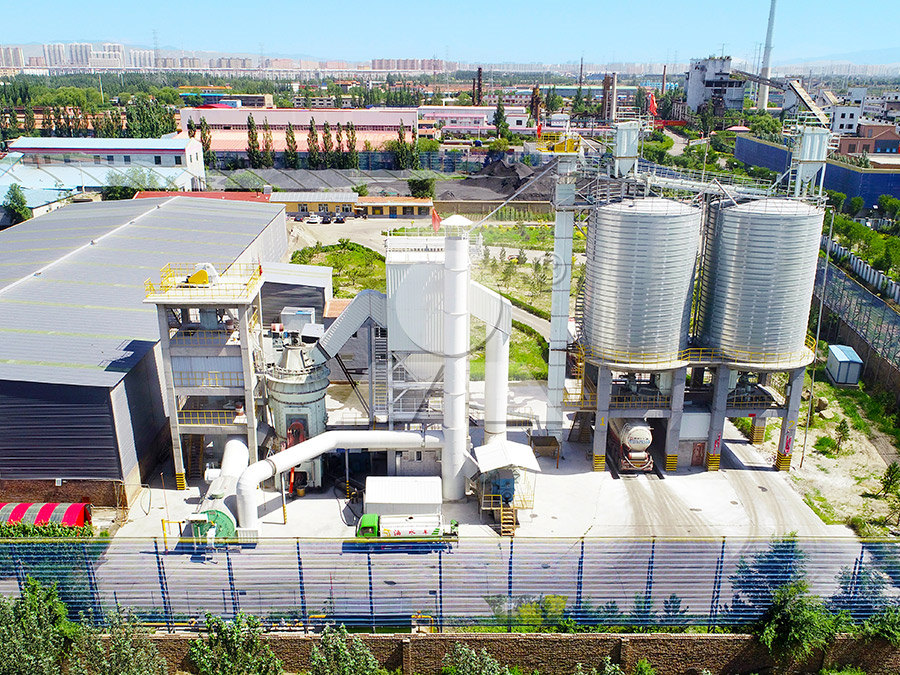
Modeling and outlet temperature control of coal mill using
Coal mills are used to grind and dry the raw coal containing moisture and to transport the pulverized coal air mixture to the boiler Poor dynamic performance of coal mill causes difficulties in maintaining the frequency, boiler pressure and temperature of the plant This paper presents development and validation of coal mill model for improved coal mill control The parameters Cement Plant Coal Mill Outlet Gas Temperature May 11 2015 coal mill is an important integral part of cement plant here large size of approx size 600mm is ground fine to the size of 90 micron coal from coal mill is used to feed kiln and calciner outlet temperature of coal from coal mill is different Chat Onlinecoal mill outlet temperature Sebocom Construction2020年8月12日 As one of the three major forces of coal mills, the grinding force exerts a significant impact on the working process of coal mills and parameters like mill current and outlet temperatureAn investigation of performance characteristics and energetic Previous Post Next Post Contents1 Kiln Control and Operation2 1 INTRODUCTION3 1 CONTROL PARAMETERS31 11 Location of the control parameters and variables311 111 Wet kiln312 111 Lepol kiln313 111 Preheater kiln314 111 Precalciner kiln32 11 Burning Zone Temperature (BZT)321 111 Pyrometer reading322 112 NOx of the exhaust Kiln Control and Operation INFINITY FOR CEMENT EQUIPMENT
.jpg)
Cement Mill Water Spray System Report
This project proposes installing a water cooling system in cement grinding units to control the temperature of cement below 115°C The system would spray water into the cement mill based on feedback from temperature sensors Water flow rates would be automatically adjusted to maintain the optimal temperature range and prevent issues caused by high temperatures like gypsum 2020年9月9日 In \( r{T} , r{CO} \) and \( r{c} \) are weighting factors, F c is mass flow of pulverized coal and C CO is CO concentration 4 RealTime Measurements and Responses Realtime responses of the precalciner temperature in the case of manual control and the case of automatic control are presented in Fig 8 and Fig 9 , respectivelyIdentification and Control of Precalciner in the Cement PlantA simple energy balance model of the coal mill is derived in (Odgaard and Mataji 2006), this model is based on a more detailed model found in (Rees and Fan 2003)In this model the coal mill is seen as one body with the mass m mThe following variables are defined: T(t) is the temperature in the coal dust flow in the mill, ṁ PA (t) is the primary air mass flow, T PA (t) is Coal Mill an overview ScienceDirect Topics2013年8月1日 The reliability of a coal mill's operation is strongly connected with optimizing the combustion process Monitoring the temperature of a dust–air mixture significantly increases the coal mill's Modeling and outlet temperature control of coal mill using
.jpg)
TEMPERATURE CONTROL IN CEMENT MANUFACTURING Peak
PEAK SENSORS Temperature Sensor Specialists peaksensors +44 (0) 1246 261 999 peaksensors pslsales@peaksensors TEMPERATURE CONTROL IN CEMENT MANUFACTURING Temperature management is essential in cement manufacturing to ensure process control and product consistency2023年1月9日 The pulverized coal reacts with the hightemperature oxygenenriched tertiary air in the fuel CO content (x 4), and outlet temperature (x 5) of primary cyclone C11 also reflect, to some extent, the operating T Control of Precalciner Temperature in the Cement The coal mass flow and the outlet temperature are modeled by reinvestigating the mass balance and heat balance models physically The archived data from a plant database are utilized to identify Modeling and Parameter Identification of Coal Mill ResearchGateto a global coal production of around 37 Gt in 1999, coal use in power and heat stations amounted to 23 Gt whereas the nonmetallic minerals industry, which includes cement production, used only about 05 Gt (IEA, 2001) The Clean Coal Centre has therefore published more reviews on power generation, including the coutilisation of coal with otherCoutilisation of coal and other fuels in cement kilns ICSC
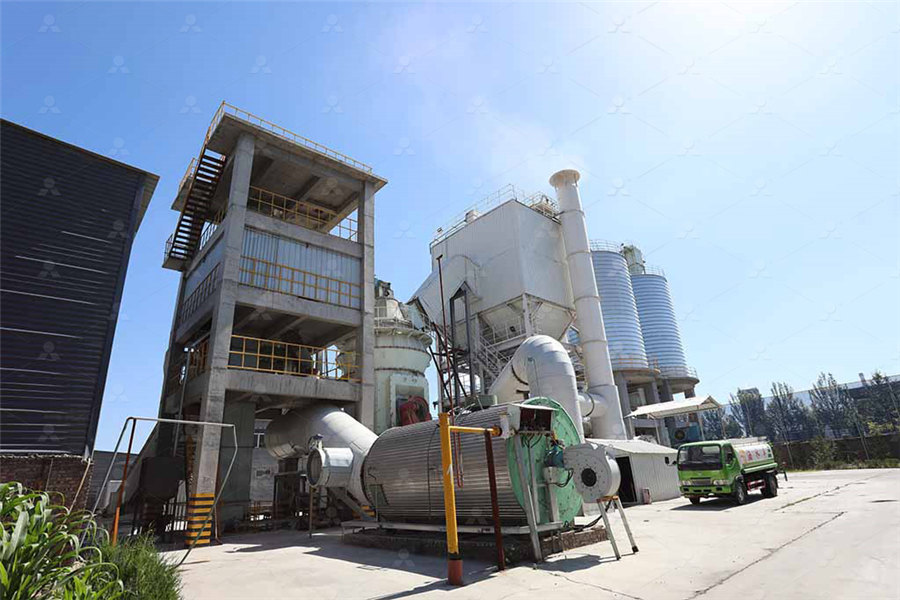
Important Operation Tips For Cement Vertical Mill
Mill System Operate Safety When the raw material is running in the vertical mill, the drying heat source of the material comes from the hot gas at the kiln tail Therefore, when the vertical mill is operated, the control of the inlet and outlet dampers should be balanced by the kiln millGROUP HEADQUARTER Viale Trento e Trieste 93 • 20853 Biassono (MB) • Italy T +39 039 22021 • F +39 039 Email: boldrocchi@boldrocchi • boldrocchi HEADQUARTERS SALES OFFICES WORLDWIDE FANS BLOWERS DIVISIONCEMENT PLANTS APPLICATIONS Boldrocchi GroupIdentification and Control of Precalciner in the Cement Plant Jakub Osmic1(B), Emir Omerdic2, Edin Imsirovic2, Tima O Smajlovic2, and Edin Omerdic3 1 University of Tuzla, 75000 Tuzla, Bosnia and Herzegovina jakubosmic@gmail 2 Cement Factory Lukavac, 75300 Lukavac, Bosnia and Herzegovina 3 University of Limerick, Limerick, Ireland Abstract Identification and Control of Precalciner in the Cement Plant1 Kiln gas outlet • Optimization of primary firing • Lower fuel consumption • Maintain clinker quality CO, O 2 • Control of false air in preheater CO, O 2 AO2000 System, LS25 Uras, Magnos ) AO2000 System, LS25 Uras, Magnos 5 Coal mill • Safety measurement • Prevention of smoldering (monitor of air entrance) CO, O 2 AO2000 ABB MEASUREMENT ANALYTICS Gas analysis in cement

EVERYTHING YOU NEED TO KNOW ABOUT CEMENT KILN FLAME
Previous Post Next Post Contents1 EVERYTHING YOU NEED TO KNOW ABOUT CEMENT KILN FLAME11 FLAME CHARACTERISTICS111 Group I12 LENGTH OF THE FLAME13 FLAME PROPAGATION SPEED14 IGNITION OF THE FUEL15 OXYGEN ENRICHMENT16 SHAPE OF THE FLAME17 DIRECTION OF THE FLAME18 ADJUSTMENT OF FLAME Two major parameters which decide the mill capacity and performance are the hardness of coal and the total moisture level in coal The mill outlet temperature of coalair mixture is maintained between 65 to 90 degree centigrade in the case of low and medium volatile coal In the case of high volatile coal while the lower limit generally remains as 65 degree centigrade, the upper Boiler Performance and Mill Outlet Temperature Bright Hub 2018年10月10日 EU’s cement sector and CO 2 gaseous emission reduction by 2030 decreasing the outlet gas temperature and and a coal mill, hot ue gases from the kiln are deployedHeat Integration in a Cement Production2023年1月9日 However, the cement calcination system is timedelayed, nonlinear, and multidisturbance, which makes it difficult to predict and control the precalciner temperatureControl of Precalciner Temperature in the Cement
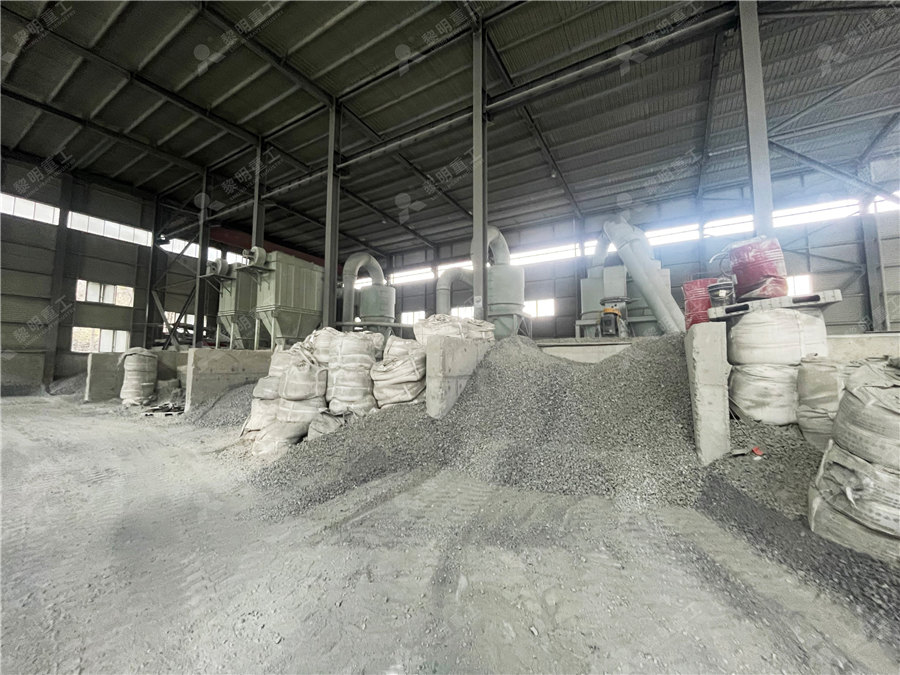
COAL GRINDING SYSTEMS SAFETY CONSIDERATIONS PEC
Coal mill hot air inlet temperatures never be more than 600should F and the outlet temperature should not exceed 200°F on Raymond coal mills If the flow of raw coal to the coal mill is interrupted for any reason (for example: plugging, failure of the coal feeder, etc), the outlet temperature of the coal mill can climb to dangerous levelsMaterial circulation inside the mill FSmidth Cement flsmidthcement 3 ATOX coal mill Proven technology Today the airswept vertical roller mill is the standard solution for coal grinding installations And thanks to our continuous refinement of the ATOX coal mill over the years, today’s leading airswept vertical roller mill is the ATOX COAL MILL2014年1月1日 The emission factors of kiln end, kiln head, coal mill, crushing and cement mill was 0156 clinker g/t, 3914 clinker g/t, 1538 coal g/t, 0016 stone g/t and 0056 cement g/t respectively, the (PDF) MPS mills for coal grinding ResearchGateControl scheme for outlet temperature is essential since improper control may lead to chances of explosion In the thermal power plant, the outlet temperature is maintained at 70 qC This temperature is required to remove the moisture content present in the coal Any further rise in temperature may lead to damage of the components in the mill Modeling and Control of Coal Mill
.jpg)
Modeling and outlet temperature control of coal mill using
DOI: 101109/CCA2013 Corpus ID: ; Modeling and outlet temperature control of coal mill using Model Predictive Controller @article{Pradeebha2013ModelingAO, title={Modeling and outlet temperature control of coal mill using Model Predictive Controller}, author={P Pradeebha and Natarajan Pappa}, journal={2013 IEEE International Conference on Control Cement Mill Common Issue: Higher cement temperature, Mill tripping under high cement temperature or mill outlet temperature is not an uncommon in cement mills It happens in majority of cases due to high clinker temperature and the other reasons could be insufficient mill venting and insufficient or faulty water spray systemCEMENT PLANT TALK001Cement Grinding p p p p p p p p p p p p p p p p p p p p p p p p p p p Raw Mill EFilter p p p p Cement Mill Fan Also in difficult and extreme operational conditions TLTfans secure troublefree operation to our customers p Raw Mill Fan Typical Data volume flow: 80350 m3/s temperature: 90100 °C mech design temperature: 250 °C pressure Fans in Cement Plants BrownleeMorrow CompanyExample Chekka, clinker temperature > 150°C with coal, Actions to control drying when no external heat source available For a cement mill: intermediate or outlet diaphragm For the case of; cement mills with a drying chamber see Everything you need to know about clinker/cement
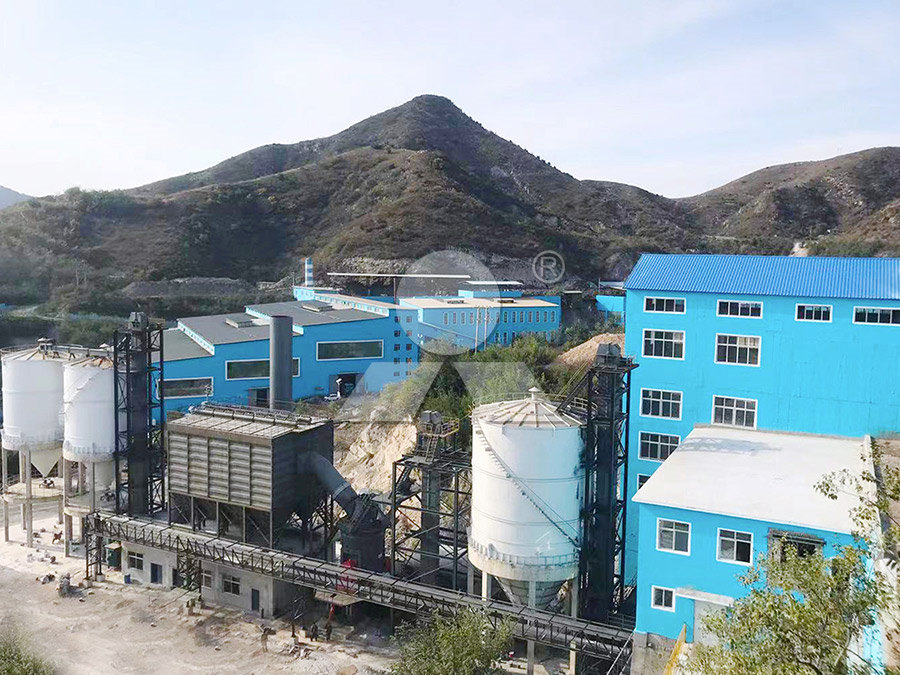
Effect of mill outlet temperature on the coal
Download scientific diagram Effect of mill outlet temperature on the coal moisture content from publication: An investigation of performance characteristics and energetic efficiency of vertical Coal mills are used to grind and dry the raw coal containing moisture and to transport the pulverized coal air mixture to the boiler Poor dynamic performance of coal mill causes difficulties in maintaining the frequency, boiler pressure and temperature of the plant This paper presents development and validation of coal mill model for improved coal mill control The parameters Modeling and outlet temperature control of coal mill using Cement Plant Coal Mill Outlet Gas Temperature May 11 2015 coal mill is an important integral part of cement plant here large size of approx size 600mm is ground fine to the size of 90 micron coal from coal mill is used to feed kiln and calciner outlet temperature of coal from coal mill is different Chat Onlinecoal mill outlet temperature Sebocom Construction2020年8月12日 As one of the three major forces of coal mills, the grinding force exerts a significant impact on the working process of coal mills and parameters like mill current and outlet temperatureAn investigation of performance characteristics and energetic
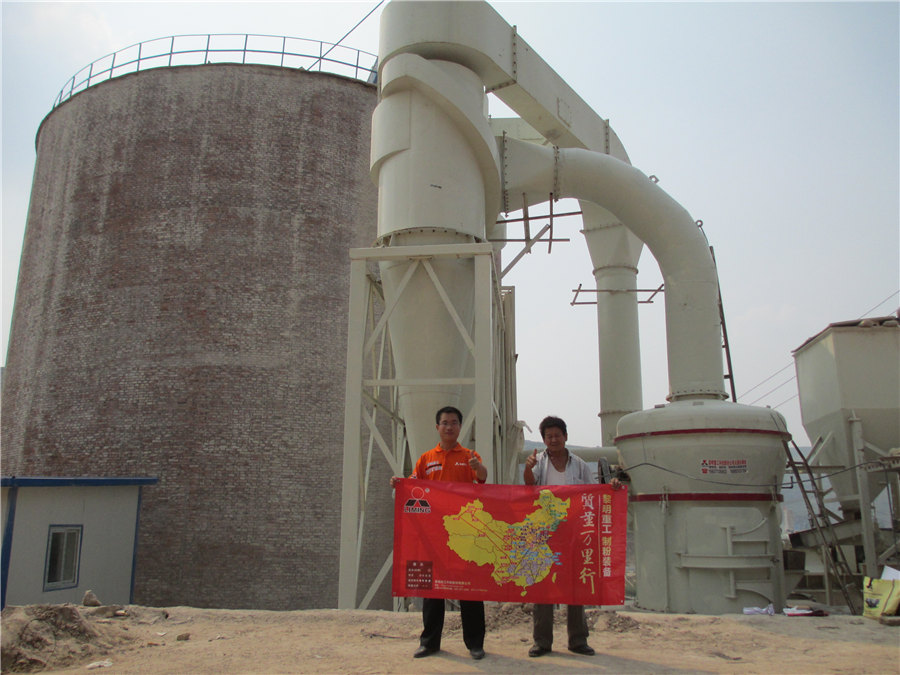
Kiln Control and Operation INFINITY FOR CEMENT EQUIPMENT
Previous Post Next Post Contents1 Kiln Control and Operation2 1 INTRODUCTION3 1 CONTROL PARAMETERS31 11 Location of the control parameters and variables311 111 Wet kiln312 111 Lepol kiln313 111 Preheater kiln314 111 Precalciner kiln32 11 Burning Zone Temperature (BZT)321 111 Pyrometer reading322 112 NOx of the exhaust This project proposes installing a water cooling system in cement grinding units to control the temperature of cement below 115°C The system would spray water into the cement mill based on feedback from temperature sensors Water flow rates would be automatically adjusted to maintain the optimal temperature range and prevent issues caused by high temperatures like gypsum Cement Mill Water Spray System Report2020年9月9日 In \( r{T} , r{CO} \) and \( r{c} \) are weighting factors, F c is mass flow of pulverized coal and C CO is CO concentration 4 RealTime Measurements and Responses Realtime responses of the precalciner temperature in the case of manual control and the case of automatic control are presented in Fig 8 and Fig 9 , respectivelyIdentification and Control of Precalciner in the Cement PlantA simple energy balance model of the coal mill is derived in (Odgaard and Mataji 2006), this model is based on a more detailed model found in (Rees and Fan 2003)In this model the coal mill is seen as one body with the mass m mThe following variables are defined: T(t) is the temperature in the coal dust flow in the mill, ṁ PA (t) is the primary air mass flow, T PA (t) is Coal Mill an overview ScienceDirect Topics