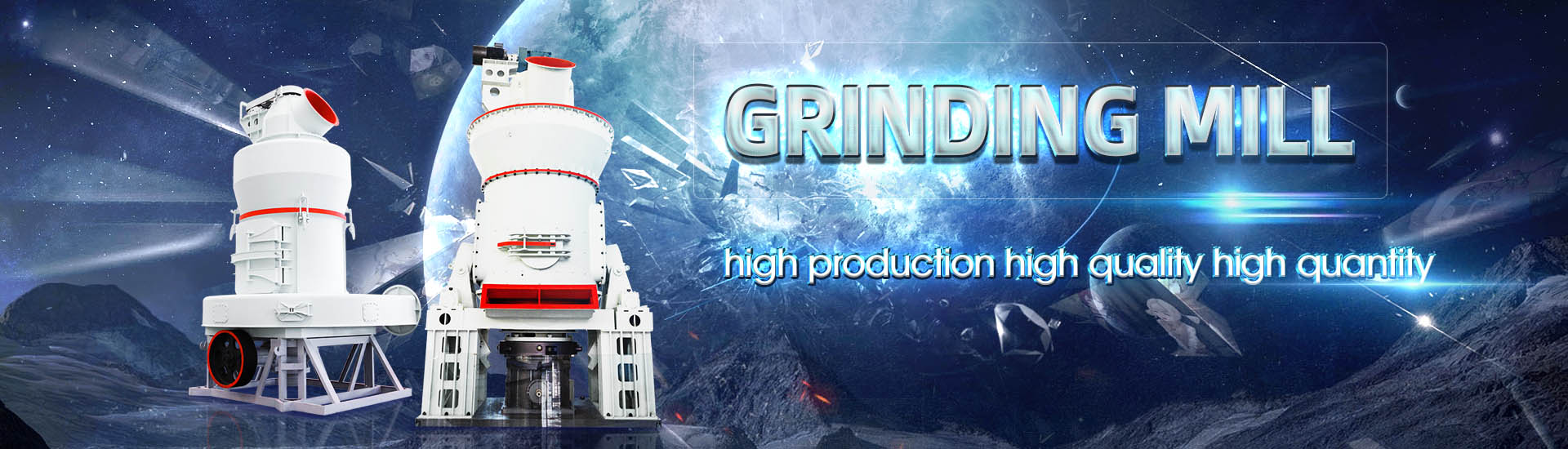
aluminum ash, overhaul slag, aluminum electrolyte processing
.jpg)
Research Progress of Electrolytic Aluminum Overhaul Slag Disposal
2023年4月25日 This article analyzes and summarizes the composition and hazards of the overhaul slag and the current development status of domestic and international electrolytic Coal gangue is a byproduct of the production of coalassociated minerals, Review of Research on the Pr2024年2月1日 The electrolytic aluminum industry generates a large amount lithium (Li)containing electrolytic aluminum slag (EAS) annually, and this can result in severe Efficient lithium recovery from electrolytic aluminum slag via an 2023年8月1日 Herein, a synergistic disposal strategy, ie, adopting the overhaul slag as a raw material together with aluminum oxide in the aluminum electrolysis process to produce Al–Si Dissolution behavior of overhaul slag from aluminum reduction
.jpg)
Comprehensive performance study of aluminum ash and calcium
2022年12月12日 In this paper, the first ultrahigh pressure contact molding technology was used to prepare highperformance building materials with aluminum ash and calcium carbide slag 2023年9月1日 This study employed hydrometallurgical processes to selectively leach lithium from Licontaining aluminum electrolyte slag, using sodium carbonate solution as the leaching agent A notable leaching efficiency of Clean Process for Selective Recovery of Lithium Aluminium ash and slag are produced from molten slag cooling in the electrolytic aluminium production process,the recycling and utilization of the electrolytic aluminium ash and slag is Recycling and Utilization of the Electrolytic Aluminium Ash and Slag2024年7月24日 The lithium was selectively recovered and enriched from spent aluminum electrolyte slag by using calcium salt roasting transformation followed by HBL121solvent extraction The new process realizes a high leaching Cleaner Process for the Selective Extraction of Lithium
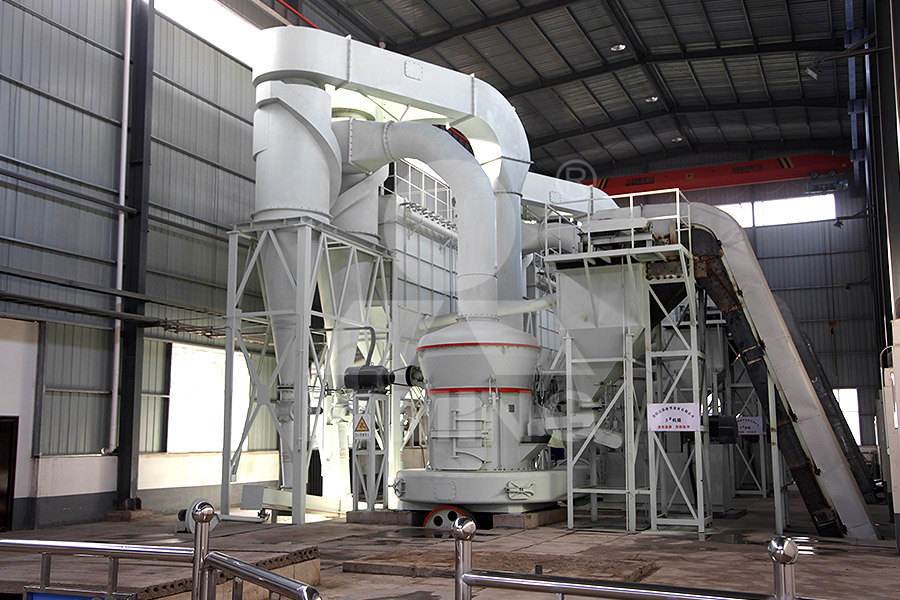
Assessing Environmental Impact of Aluminum Ash Disposal in
2024年6月4日 Based on the life cycle assessment method, this study examined the environmental impacts of four major aluminum ash treatment methods in four categories: 2021年10月1日 In this paper, a novel approach is developed for achieving the separation/recovery of lithium from spent lithiumcontaining aluminum electrolyte by a sodium A novel approach for lithium recovery from waste lithium 2023年4月25日 This article analyzes and summarizes the composition and hazards of the overhaul slag and the current development status of domestic and international electrolytic aluminum overhaul slag disposal, and points out the 电解铝大修渣处置研究进展2024年5月23日 16 Million metric tons of spent carbon electrodes modify carbonrich solid wastes from aluminum electrolysis are produced annually, threatening ecosystems by cyanide and fluoride pollution Here, we review carbonrich solid wastes with focus on sources and hazards, detoxification, separation, recovery, recycling and disposal Treatment techniques The recycling of carbonrich solid wastes from aluminum
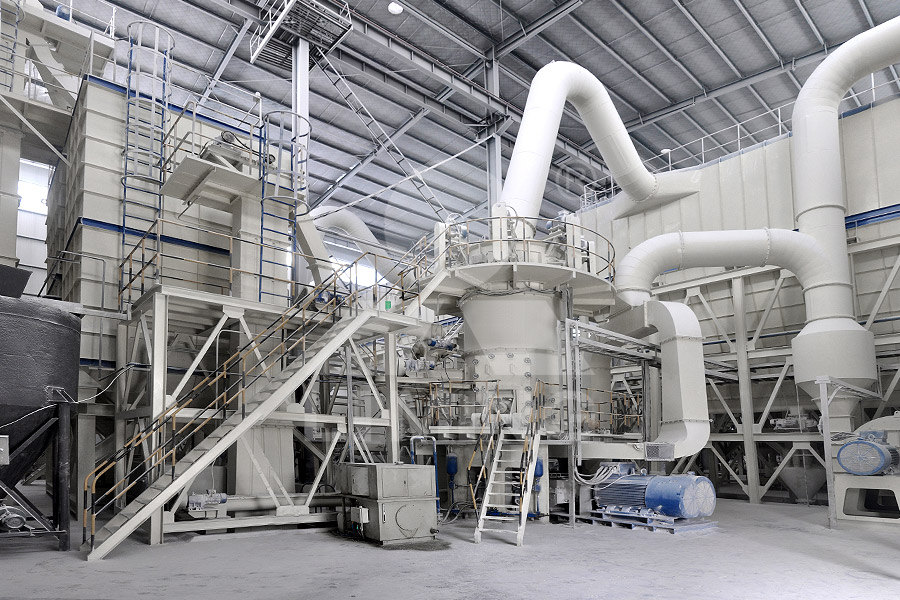
Dissolution behavior of overhaul slag from aluminum reduction
Download Citation On Aug 1, 2023, Jianping Yang and others published Dissolution behavior of overhaul slag from aluminum reduction cell in a cryolitebased molten salt system Find, read and 2023年10月1日 The main components of waste aluminum cryolite electrolyte are cryolite (Na 3 AlF 6), potassium cryolite (K 2 NaAlF 6), lithium cryolite (Na 2 LiAlF 6), fluorite (CaF 2), and approximately 2% carbon black (Wang et al, 2019)The main treatment methods of waste aluminum cryolite electrolyte can be divided into two categories: combined thermalwet Efficient extraction and recovery of lithium from waste aluminum 2024年6月4日 The main components of aluminum ash include single aluminum, aluminum oxide (Al 2 O 3), aluminum nitride (AlN), aluminum carbide (Al 4 C 3), fluoride and chlorinated salts, silicon, iron and other oxide (Kang et al 2022) Aluminum ash slag can be divided into primary aluminum ash and secondary aluminum ash according to the different degrees of Assessing Environmental Impact of Aluminum Ash Disposal in 2021年10月1日 To recover valuable elements such as lithium from waste aluminum electrolyte, Wu et al (2021) mixed Na 2 CO 3 with waste aluminum electrolyte and roasted them at 650 • C for 25 h, and Na 2 A novel approach for lithium recovery from waste lithium
.jpg)
A novel approach for ultrasonic assisted organic acid leaching of
2023年10月1日 Currently, the green resource utilization in the aluminum electrolysis industry mainly focuses on the solid waste treatment of aluminum electrolysis tank overhaul slag, the resource utilization of waste cathodes, and the recovery of electrolytic tank waste heat There are few reports on lithium recovery from waste aluminum electrolytes [16,17]2021年7月30日 The aluminum metal and molten salt flux are tapped after the process, where the cooled flux along with the mixture of nonmetallic components is called salt slag or salt cake54 Salt slag contains 5–7 wt% residual aluminum metal, 15–30 wt% aluminum oxide, 30–55 wt% sodium chloride, and 15–30 wt% potassium chloride and, depending upon the A Review of Secondary Aluminum Production and Its Byproducts2021年10月1日 A novel approach for lithium recovery from waste lithiumcontaining aluminum electrolyte by a roastingleaching the leaching toxicity was investigated The experimental results show that the best ratio of aluminum ash and calcium carbide slag is 1:9, the International Journal of Mineral Processing, Volume 160, 2017 A novel approach for lithium recovery from waste lithium aluminum, heat treatment or cold treatment processes are generally used to recover the 10% to 30% of metallic aluminum contained in the aluminum slag The secondary aluminum dross is accounting for approximately 70% to 90% of the aluminum slag, which the metal aluminum content remained is generally less than 5%Technical Report International Aluminium
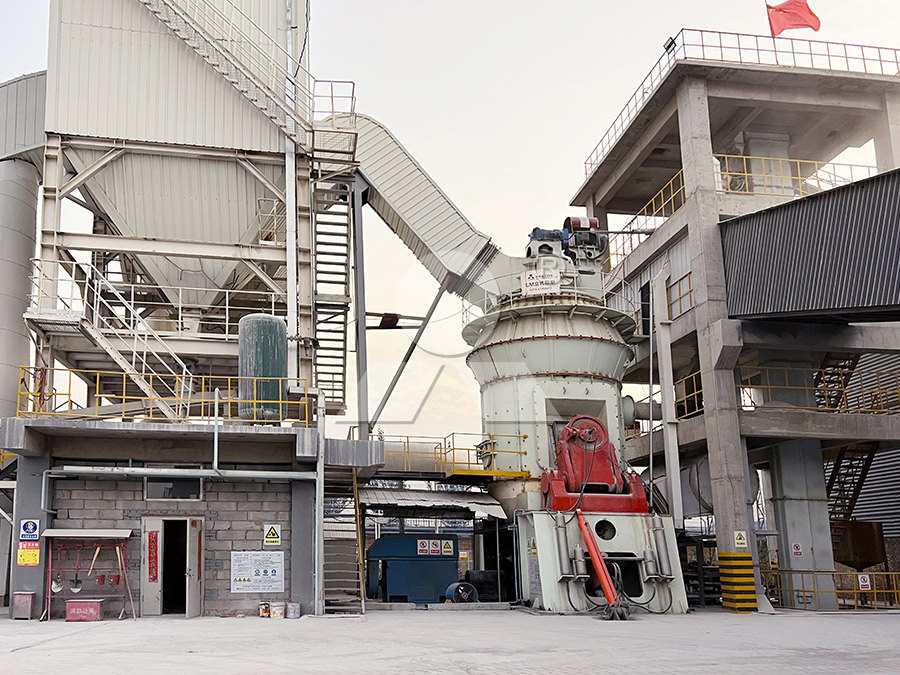
Novel process for the extraction of lithium carbonate from spent
2020年12月1日 The rapid development of the electrolytic aluminum industry in China and the increasing demand for aluminum products have led to the development of many lowgrade bauxite mines with an average Li 2 O content of at least 058% (Wang et al, 2013)Due to the use of this lowgrade bauxite in the electrolytic aluminum process, the content of lithium in the 2024年1月1日 Semantic Scholar extracted view of "Efficient lithium recovery from electrolytic aluminum slag via an environmentally friendly process: Leaching behavior and Green and efficient separation of fluorine from spent aluminum electrolyte by aluminum sulfate solution: Leaching behavior and mechanism Lingqi Meng Tianxiang Hao +5 Efficient lithium recovery from electrolytic aluminum slag via an 2020年1月2日 The invention discloses a fluorineretaining agent for overhaul slag of an aluminum electrolytic cell The fluorineretaining agent comprises the following components of, by mass, 80100 parts of calcium sulfate, 6080 parts of calcium oxide, 5070 parts of calcium hydroxide and 3060 parts of calcium chloride The invention further discloses a method for Fluorineretaining agent for overhaul slag of aluminum 2024年7月24日 Spent aluminum electrolyte slag is a byproduct produced during the electrolysis of aluminum and contains elements such as F, Al, Na, and Li It is a toxic and harmful substance with a stable and complex structure As a Cleaner Process for the Selective Extraction of Lithium
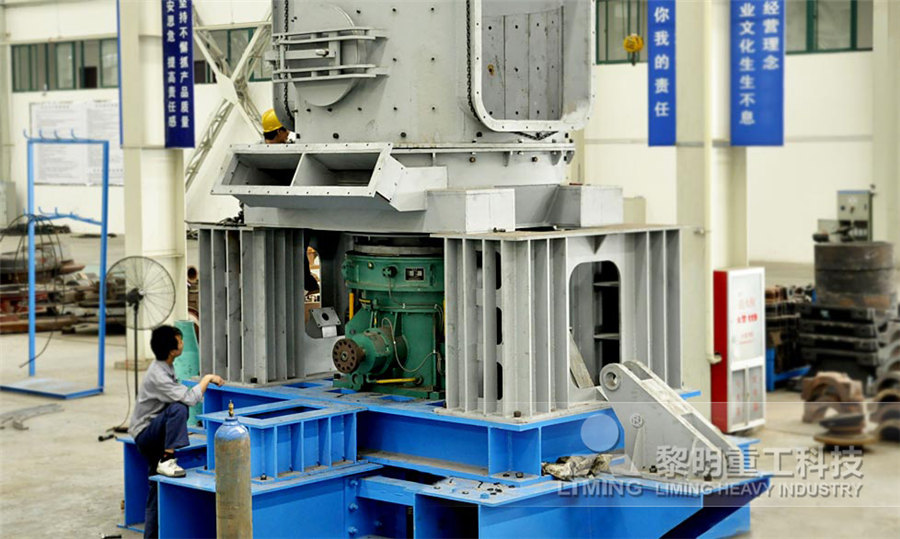
Novel process for the extraction of lithium carbonate from spent
2020年12月1日 A hydrometallurgical process was developed to extract lithium from a spent lithiumcontaining aluminum electrolyte, reduce the stacking of spent aluminum electrolyte, and recover the valuable elements In this study, we extracted lithium from an electrolyte using the following three steps: 1) leaching with HNO 3 − Al(NO 3) 3, 2) neutralizing the leachate 2024年2月1日 Overhaul slag, as one of the main hazardous solid wastes generated in the electrolytic aluminum, has high research value [12]The electrolytic cell lining is eroded by continuous chemical corrosion of hightemperature molten metal and salt, resulting in expansion and peeling off, leading to low production efficiency and degradation of performance [13]A novel approach for extracting lithium from overhaul slag by low 2018年10月1日 In the secondary aluminum industry (aluminum scrap recovery), about 200 kg of aluminum is produced per each ton of secondary aluminum (Seng et al, 2006) By 2020, annual global demand for aluminum will reach to about 97 million tons and almost 32% of which that equals to 31 million tons is expected to be supplied from scrap recycling ( Tsakiridis et al, 2013 )Hazardous aluminum dross characterization and recycling ALUMINUM ASH PROCESSING SYSTEM Processing capacity: 10,000200,000 t/a Processing materials: aluminum ash, aluminum slag, aluminum shavings and other hazardous waste Equipment configuration: rotary kiln, ball mill, dust collector and other equipmentAluminum Ash Processing Aluminum Ash Recovery Aluminum Ash
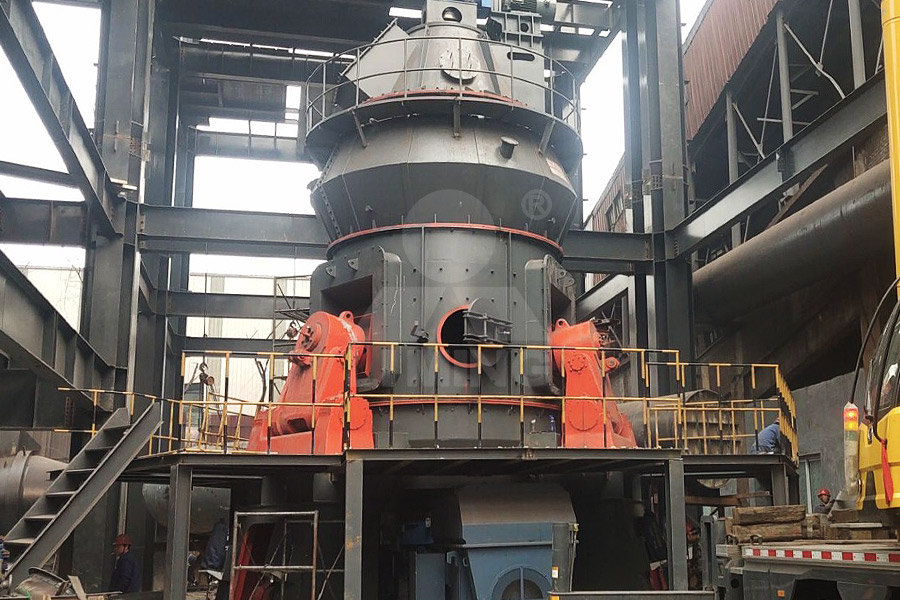
Comprehensive performance study of aluminum ash and calcium
2022年12月12日 Based on the research on bulk solid waste contact molding technology by our team [49], the comprehensive performance of pressed bricks with different ratios of aluminum ash and calcium carbide slag was investigated, the ratios of aluminum ash and calcium carbide slag are 9:1 ∼ 1:9 and pure aluminum ash and calcium carbide slag, the pressing pressure is 300 2023年10月1日 The aluminum electrolyte is the core part of the electrolytic production process of aluminum In contrast, lithiumrich aluminum electrolytes can cause problems such as reduced production temperature, decreased alumina solubility, increased precipitation at the bottom of the electrolytic cell, and poor stability in the aluminum electrolytic cell [ 7 , 8 ]Chemical Engineering and Processing Process Intensificationelectrolytic aluminum production process, including waste cathode carbon block, waste anode material Generally, electrolytic aluminum production enterprises will overhaul the electrolytic cell every five years, with a large amount of waste generated in this process Electrolytic aluminum scrap mainly contains NaF, Na 3 AlF 6, CaF 2Research on the Coprocessing of Mixed Electrolytic Aluminum Coal fly ash (CFA), an industrial byproduct of hightemperature combustion of coal in coalfired power plants, is one of the most complex and largest amounts of industrial solid wastes generated in China It is widely recognized that CFA should be considered as a potential alumina resource to substitute bauxite In this review, the features of highalumina fly ash and aluminum recovery Aluminum extraction technologies from high aluminum fly ash De Gruyter
.jpg)
Regeneration of raw materials for aluminum electrolysis from
2023年5月20日 Due to chemical corrosion and erosion by molten aluminum liquid and electrolyte, the carbon anode of the aluminum electrolytic cell would fall off into the electrolyte during the primary aluminum electrolysis process to produce spent anode carbon (SCA), which has been listed as one of the typical hazardous solid wastes in the National Hazardous Waste 2017年9月30日 To date, electrolyte compositions and processing regimes for a wide class of products made from various metals and alloys have been developed, as well as original technical solutions for (PDF) Electrolytic plasma processing of complex (4) Green and Safe Disposal Technology for Aluminum Electrolysis Pollutants This technology solves a number of technical problems in the green, safe disposal and resourceful use of aluminum electrolysis overhaul slag and secondary aluminum ash, The Development of Aluminum Industry and Technology in China2020年11月23日 According to the investigation, the production of aluminum ash and slag accounts for about 7% to 12% of the recycled aluminum output, and the metal aluminum content is between 10% and 30% Recycling aluminum ash and slag can not only reduce the waste of resources, but also produce considerable economic benefitsRecycling and utilization of the aluminum ash and slag Mineral
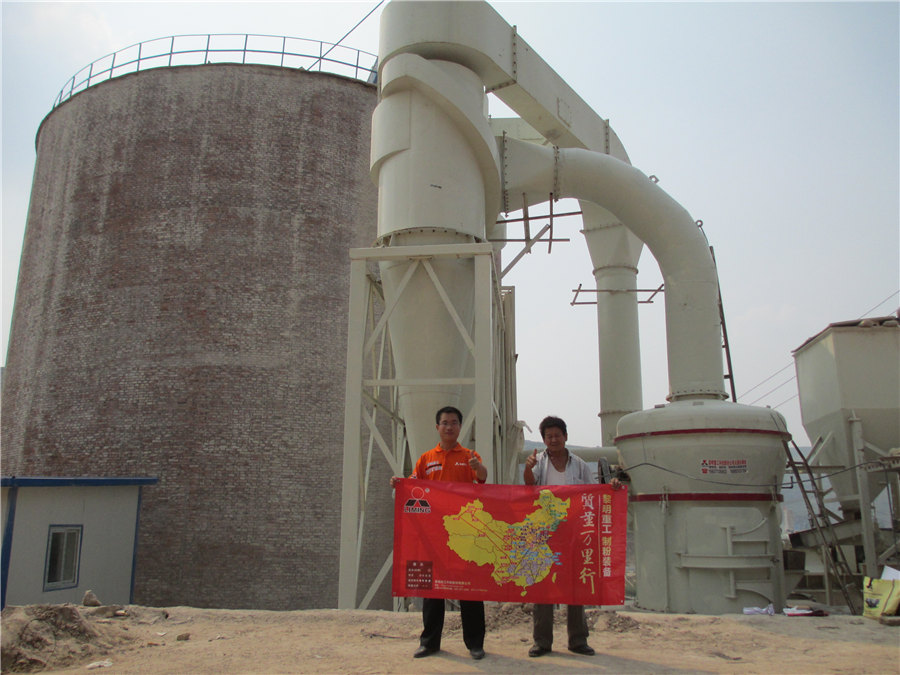
Industrial experimental research on coprocessing of spent
2023年2月1日 Request PDF Industrial experimental research on coprocessing of spent refractory materials in aluminum electrolytic cell To realize the harmlessness, reduction and resource utilization of 2024年5月1日 For example, in the collaborative disposal and recovery of valuable metals with red mud, the proportion of overhaul slag is only 10%, and the processing capacity is small (Mao et al, 2021) The above research is only limited to harmless disposal and the separation and recovery of high content elements, and has not yet paid attention to the high value of lithium in Selective preparation of lithium carbonate from overhaul slag by 2022年10月10日 One of the main electrolytic aluminum production costs is the consumption of carbon anodes, and carbon anode slag is a common hazardous waste in the aluminum industryRecovery of carbon and cryolite from spent carbon anode slag of 2021年7月30日 Sintering Aluminum dross and coal fly ash were used to prepare mullitebased ceramics through sintering and acid leaching methods At a sintering temperature of 1500 C, high mulliteA Review of Secondary Aluminum Production and Its Byproducts

(PDF) Preparation of Alumina from Aluminum Ash by
2019年2月26日 Aluminum ash is an industrial waste residue produced during alumina electrolysis and aluminum processing and casting In the experiment, alumina powder with a purity of 9897% was prepared by 2024年5月23日 16 Million metric tons of spent carbon electrodes modify carbonrich solid wastes from aluminum electrolysis are produced annually, threatening ecosystems by cyanide and fluoride pollution Here, we review carbonrich solid wastes with focus on sources and hazards, detoxification, separation, recovery, recycling and disposal Treatment techniques The recycling of carbonrich solid wastes from aluminum Download Citation On Aug 1, 2023, Jianping Yang and others published Dissolution behavior of overhaul slag from aluminum reduction cell in a cryolitebased molten salt system Find, read and Dissolution behavior of overhaul slag from aluminum reduction 2023年10月1日 The main components of waste aluminum cryolite electrolyte are cryolite (Na 3 AlF 6), potassium cryolite (K 2 NaAlF 6), lithium cryolite (Na 2 LiAlF 6), fluorite (CaF 2), and approximately 2% carbon black (Wang et al, 2019)The main treatment methods of waste aluminum cryolite electrolyte can be divided into two categories: combined thermalwet Efficient extraction and recovery of lithium from waste aluminum

Assessing Environmental Impact of Aluminum Ash Disposal in
2024年6月4日 The main components of aluminum ash include single aluminum, aluminum oxide (Al 2 O 3), aluminum nitride (AlN), aluminum carbide (Al 4 C 3), fluoride and chlorinated salts, silicon, iron and other oxide (Kang et al 2022) Aluminum ash slag can be divided into primary aluminum ash and secondary aluminum ash according to the different degrees of 2021年10月1日 To recover valuable elements such as lithium from waste aluminum electrolyte, Wu et al (2021) mixed Na 2 CO 3 with waste aluminum electrolyte and roasted them at 650 • C for 25 h, and Na 2 A novel approach for lithium recovery from waste lithium 2023年10月1日 Currently, the green resource utilization in the aluminum electrolysis industry mainly focuses on the solid waste treatment of aluminum electrolysis tank overhaul slag, the resource utilization of waste cathodes, and the recovery of electrolytic tank waste heat There are few reports on lithium recovery from waste aluminum electrolytes [16,17]A novel approach for ultrasonic assisted organic acid leaching of 2021年7月30日 The aluminum metal and molten salt flux are tapped after the process, where the cooled flux along with the mixture of nonmetallic components is called salt slag or salt cake54 Salt slag contains 5–7 wt% residual aluminum metal, 15–30 wt% aluminum oxide, 30–55 wt% sodium chloride, and 15–30 wt% potassium chloride and, depending upon the A Review of Secondary Aluminum Production and Its Byproducts
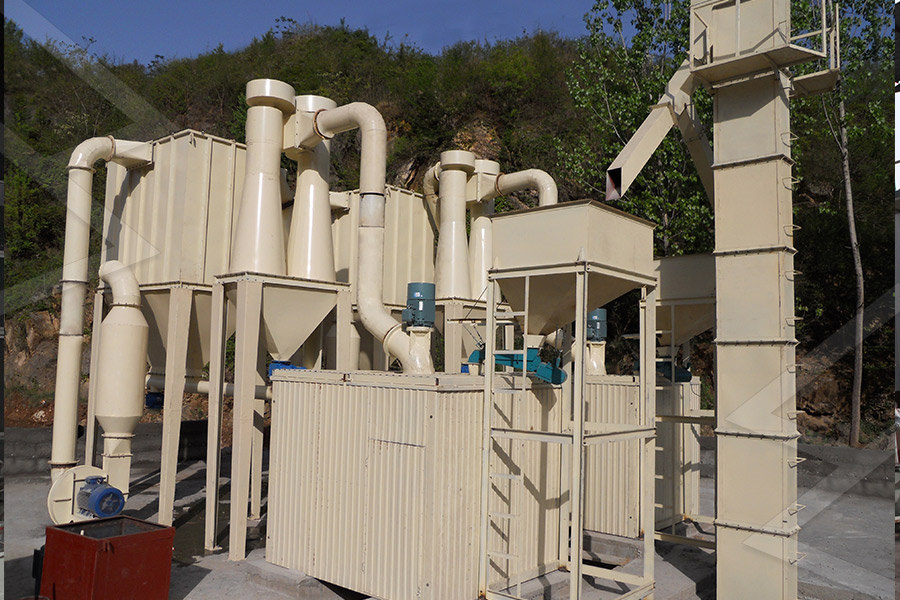
A novel approach for lithium recovery from waste lithium
2021年10月1日 A novel approach for lithium recovery from waste lithiumcontaining aluminum electrolyte by a roastingleaching the leaching toxicity was investigated The experimental results show that the best ratio of aluminum ash and calcium carbide slag is 1:9, the International Journal of Mineral Processing, Volume 160, 2017 aluminum, heat treatment or cold treatment processes are generally used to recover the 10% to 30% of metallic aluminum contained in the aluminum slag The secondary aluminum dross is accounting for approximately 70% to 90% of the aluminum slag, which the metal aluminum content remained is generally less than 5%Technical Report International Aluminium2020年12月1日 The rapid development of the electrolytic aluminum industry in China and the increasing demand for aluminum products have led to the development of many lowgrade bauxite mines with an average Li 2 O content of at least 058% (Wang et al, 2013)Due to the use of this lowgrade bauxite in the electrolytic aluminum process, the content of lithium in the Novel process for the extraction of lithium carbonate from spent