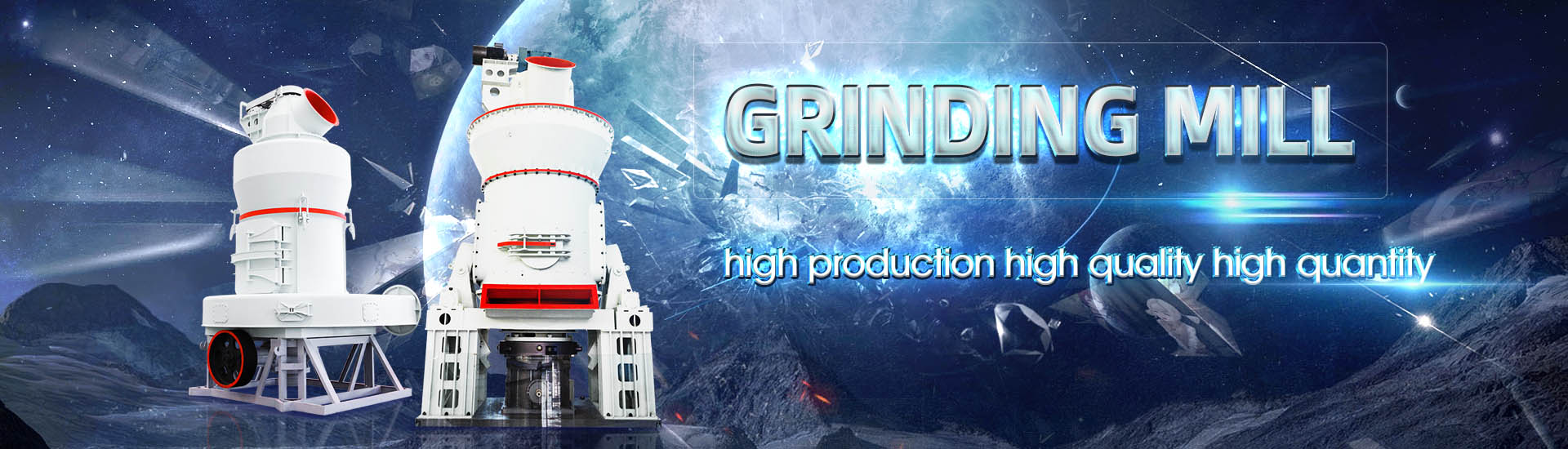
Grinding mill output 420TH
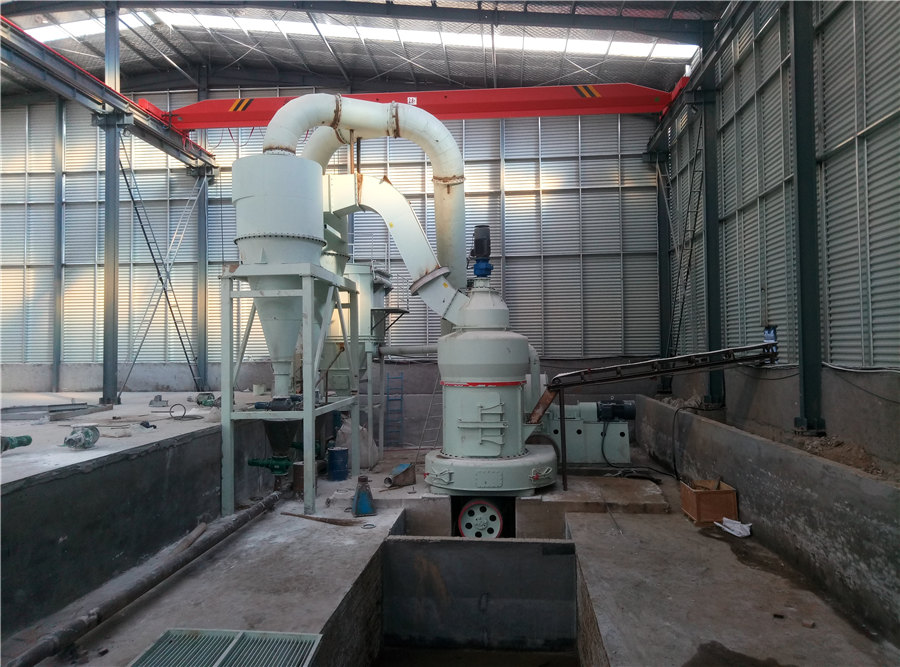
Horizontal Grinding Mill Overflow Type, Gratedischarge Type, and
The Ball Mill is designed to grind materials by turning the cylindrical shell with grinding medium (eg steel balls, cylpeb, and pebbles) put in the shell, and has a simple structure and ease of 展开2020年6月15日 Grind curves give the steadystate values of the performance variables throughput, power draw, and grind in terms of the mill filling and critical mill speed The grind Steadystate and dynamic simulation of a grinding mill using grind Ball mill optimisation As grinding accounts for a sizeable share in a cement plant’s power consumption, optimisation of grinding equipment such as ball mills can provide significant cost BALL MILLS Ball mill optimisation Holzinger ConsultingVertimill® is an energy efficient grinding machine They tend to grind more efficiently than, for example, ball mills with feeds as coarse as 6 mm to products finer than 20 microns This provides up to a 40% higher energy efficiency Vertimill® Metso
.jpg)
OPTIMIZATION OF CEMENT GRINDING OPERATION IN BALL MILLS
Optimization addresses the grinding process, maintenance and product quality The objective is to achieve a more efficient operation and increase the production rate as well as improve the run The quadropol® concept for coal or pet coke grinding, with adapted table speed and high efficiency separator sepol®, ensures a safety mill operation and serves reliable the kiln burning process Mombasa Cement Ltd ordered a QMK² quadropol® thyssenkrupp Polysius Grinding Our roller mills consistently and safely grind wheat, corn, rye, barley, spelt and other grains We offer a wide range of roller mills and optional functions to match the milling solutions you need The Arrius MRRA is the first fully integrated Roller Mills Milling Bühler Group2013年1月1日 Principles of Modern Grinding Technology explains the principles that led to rapid improvements in modern grinding technology over recent decades Removal rates and quality standards havePrinciples of Modern Grinding Technology

Development of an expert system for optimal design of the
2021年7月12日 A pilot system was built considering three main grinding outputs, including surface roughness, material removal rate and normal grinding force Based on the primary 2022年6月1日 A semiautogenous grinding mill is simulated with gradient and nongradient based extremum seeking controllers to maximize the mill performance using grind curves Extremum seeking control for optimization of an openloop Increasing Output Of Cement Grinding In Ball MillCase Study 5 INCREASING OUTPUT OF CEMENT GRINDING IN BALL MILLCASE STUDY 1MOHAN SINGH PANWAR, 2AJAY KUMAR BANSAL, 3HEMANI PALIWAL 1Student, 2Guide, 3External Guide Email: l, 2ajaykumarbansal@poornima, 3hemani8588@gmailINCREASING OUTPUT OF CEMENT GRINDING IN BALL MILLOutput: 6 t/h 350 t/h Motor power: 75 kW 3,300 kW Machine length: 2,400 mm 7,200 mm WTM intelligent vertical mill is dedicated to the highefficiency dissociation of minerals, providing users with energysaving, consumption Stone mill, Stone grinding mill All industrial
.jpg)
LM Vertical Grinding Mill SBM Mill Crusher
2023年3月15日 Comprehensive Optimization, Lower Operating Costs From aspects of grinding efficiency, powder drying, abrasion of vulnerable parts and maintenance replacement of spare parts, SBM’s LM Vertical Grinding Mill Ball mill grinding machines are valuable tools in various industries, offering efficient and reliable grinding and mixing capabilities Understanding their working principle, different types, parts, applications, advantages, and recent developments helps to appreciate their significance and wideranging applications in industries such as cement, mining, pharmaceuticals, chemicals, Ball Mill Grinding Machines: Working Principle, Types, Parts Analysis of the efficiency of the grinding process in closed circuit ball mills Valery I Telichenko1, Rashid R Sharapov1*, Svetlana YLozovaya2 and Vladimir ISkel1 1Moscow State University of Civil Engineering, Moscow, Russia 2Belgorod State Technological University named after VG Shukhov, Belgorod, Russia Abstract Ball mills for fine grinding cement clinker and additives areAnalysis of the efficiency of the grinding process in closed circuit The heavy duty mill, aimed for industrial purposes, has a strong frame, hardwearing shaft and bearings The adjustment of the stones has an adjustment gear for fine tuning All in all an industrial mill used for grinding whole grain into grits or healthy and good whole meal flour or for grinding of flour grits into high class flour as the lastGrindmaster 950 Perfect for professional Grinding Engsko
.jpg)
380V threephase mill, 380V threephase grinding mill
Output: 200 kg/h Motor power: 17 kW Machine length: 180 cm 1General Specifications Modern Stone Sesame Grinding Mill Capacity is up to 200 kg/h 2 Heads for Grinding Stone 7,5Kw 10Hp 380V 50Hz Motor Performance evaluation results of vertical roller mill in cement grinding application are presented SAMPLING STUDIES In this study, a new sampling method developed byPerformance Evaluation of Vertical Roller Mill in Cement Grinding2013年1月1日 PDF Principles of Modern Grinding Technology explains the principles that led to rapid improvements in modern grinding technology over recent decades Find, read and cite all the research Principles of Modern Grinding Technology ResearchGate2013年8月3日 In Grinding, selecting (calculate) the correct or optimum ball size that allows for the best and optimum/ideal or target grind size to be achieved by your ball mill is an important thing for a Mineral Processing Engineer AKA Metallurgist to do Often, the ball used in ball mills is oversize “just in case” Well, this safety factor can cost you much in recovery and/or mill liner Calculate and Select Ball Mill Ball Size for Optimum Grinding
.jpg)
Improvement of cement performances through the use of grinding
Mill output 57 t/h Compressive strengths 2days 11 MPa 7days 30 MPa 28 days 43 MPa After introducing MAGA/VM 10 at a dosage of 400 g/t (0,04%) directly sprayed on the grinding bed, the following positive effect have been observed: Mill output increase by 12%: from 57 to 64 t/h Energy saving by 9%: from 30 to 27,6 kWh/tFinal grain size: 74 µm 400 µm Rotational speed: 21 rpm Output: 16 t/h 50 t/h Ball mill is common used grinding plant in the industry, and it is key equipment used for milling after materials are crushed This machine can be can grind all kinds of ores and other materials, which is widely used Mill, Grinding mill All industrial manufacturersFinal grain size: 250 µm 800 µm Rotational speed: 1,500 rpm 6,000 rpm Output: 650 kg/h 13,000 kg/h any type of dry of soft products with average hardness THEORY OF OPERATION: The product is loaded in the center of Centrifugal mill, Centrifugal grinding mill AllIn the mill the grinding chamber is an oval loop of pipe 25 to 200 mm in diameter and 12 to 24 m high Feed enters through a venturi injector which is situated near the bottom of the loop At the upper end of the loop classification of the ground particles takes placeSize Reduction1: Grinding – Unit Operations in Food Processing
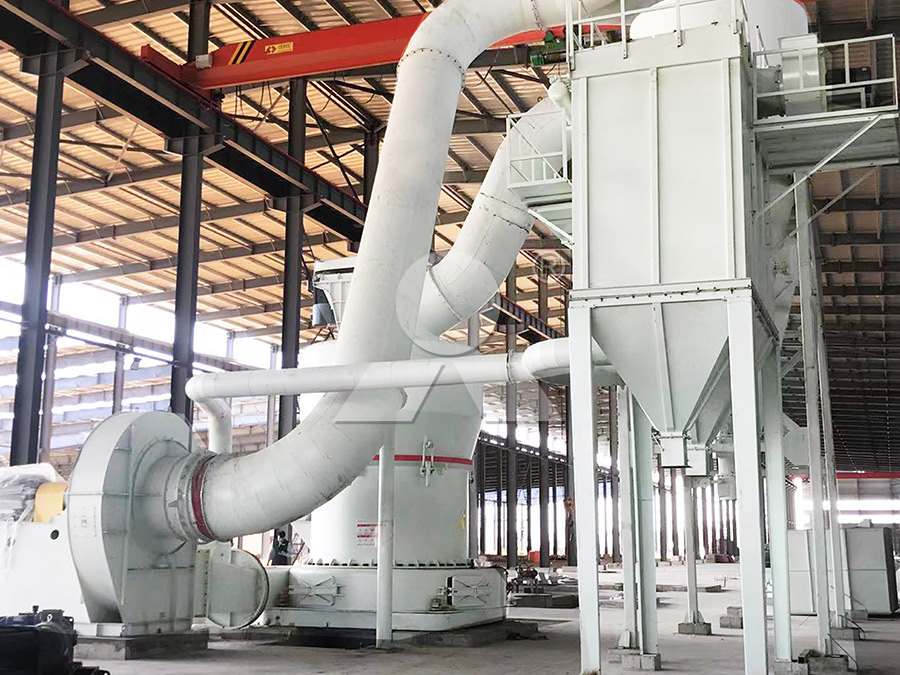
Factors Affecting Ball Mill Grinding Efficiency
2017年10月26日 The following are factors that have been investigated and applied in conventional ball milling in order to maximize grinding efficiency: a) Mill Geometry and Speed – Bond (1954) observed grinding efficiency to be a function of ball mill diameter, and established empirical relationships for recommended media size and mill speed that take this factor into According to one study, the grinding process alone accounts for approximately 40% of total power consumption in a mine complex (Ballantyne et al, 2012) A ball mill employs steel balls to generate a grinding action, ie ore particle comminution via impact and abrasion with steel balls, and is a key component of beneficiation plant productionEfect of grinding media on the milling eficiency of a ball millOutput: 16 t/h 50 t/h Ball mill is suitable to grind various mineral and other materials, which is widely used in various industries such as benefication, The Metso Outotec® Open Ended Discharge Grinding Mill (OED Mill) is a large grinding mill solution that enables innovative and efficient high capacityLarge mill, Large grinding mill All industrial manufacturers2020年5月25日 46 For a similar treatment of the energy equilibrium in a water mill, see Holdsworth et al (2015), where the kinetic energy is added to the energy required for grinding the wheat; also Υong et al (1984, p138): Input Energy = Output Energy (useful traction work)+Work Energy (energy for compacting the soil)+Interfacial Energy (energy for overcoming the slippage)The Vertical Olive Crushing Mill as a Machine and its Energy
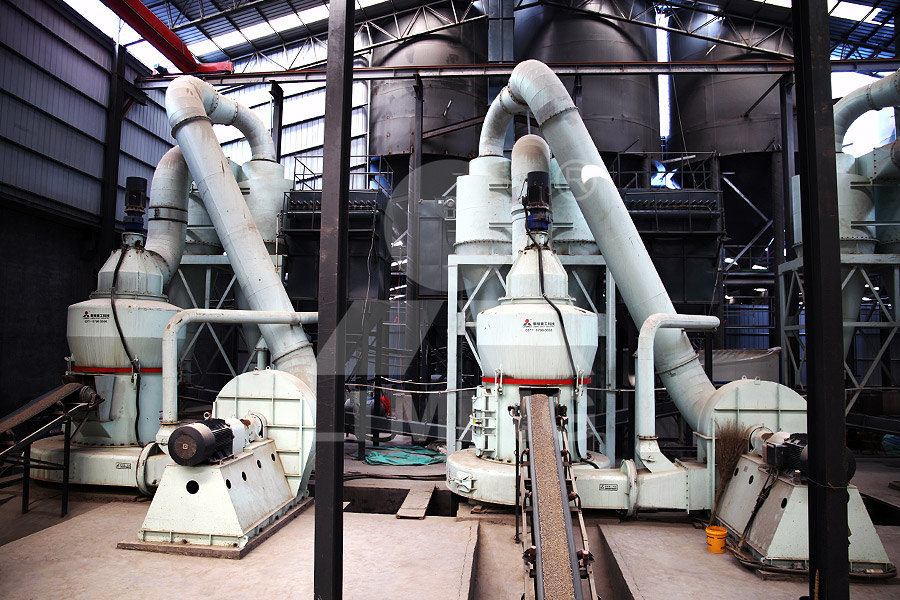
Ball mill characteristics and test conditions Mill Diameter, D (cm
Download Table Ball mill characteristics and test conditions Mill Diameter, D (cm) 204 Length, L (cm) 166 Volume, V (cm 3 ) 5,423 Operational speed, Ν (rpm) 66 from publication 2022年6月1日 Grinding mill performance (throughput or grind) is maximized using grind curves • Grind curves map the essential performance measures of a grinding mill • The need for a plant operator to manually select operating conditions is reduced • The grinding mill can be optimized without the need for a detailed process modelExtremum seeking control for optimization of an openloop grinding mill A 15 mio t/a cement plant is having a closed circuit ball mill for cement grinding: The mill has been operating with satisfactory performance interms of system availability and output, however power consumption was on higher side 31 System Description Mill Rated capacity 150 t/h OPC at 2800 blaine I chamber linersPROCESS DIAGNOSTIC STUDIES FOR CEMENT MILL 2024年8月8日 This seemingly minor selection can dramatically influence the efficiency of the milling process, the quality of the output, and, ultimately, the bottom line Whether in the realm of pharmaceuticals, ceramics, or materials Ball Mill Success: A StepbyStep Guide to Choosing
.jpg)
The 20TH limestone desulfurization grinding production line in a
Grinding Mill: The grinding mill, often a vertical roller mill or ball mill, is responsible for grinding the limestone into a fine powder Efficient Grinding: The production line ensures a high output of fine limestone powder, which is essential for effective desulfurization d2012年6月1日 As the cylinder starts to rotate, the grinding balls inside the cylinder crush and grind the feed material, generating mechanical energy that aids in breaking bonds, activating the catalyst, and Grinding in Ball Mills: Modeling and Process Control2020年6月15日 Since grinding mills have a significant impact on the final economic performance of a mineral processing plant (McIvor and Finch, 1991, SosaBlanco et al, 2000), it is important to operate them at the point which will optimize the economic performance of the plant (Cramer, 2008, Matthews and Craig, 2013)Grinding mill processes are difficult to control as the control Steadystate and dynamic simulation of a grinding mill using Hammer Mill Grinding With over 160 years of industry experience and continued cutting edge research and development, Bühler is proud to present the next generation grinding portfolio, with all new and updated equipment to provide the highest performance and value for your businessHorizontal Hammer Mill Grinding System Bühler Group
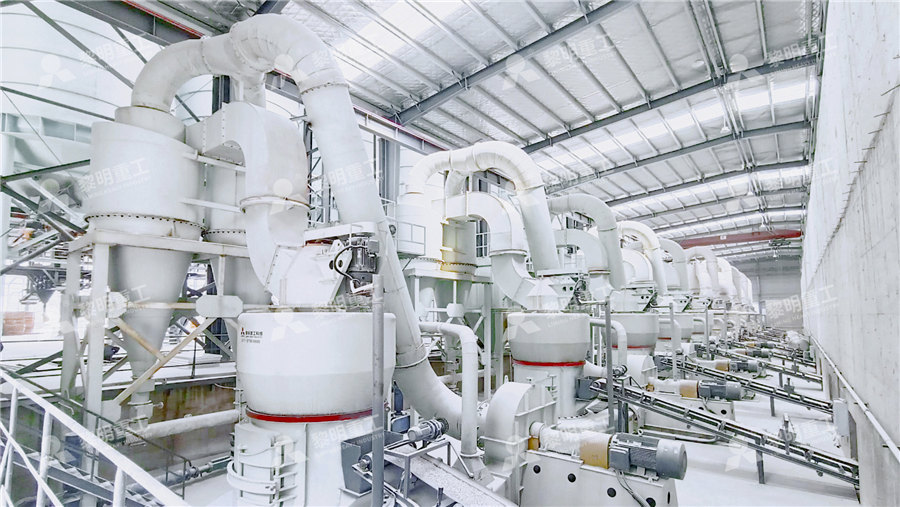
The F H Benning Company Grinding Mill: A Case Study
The E H Benning Company Grinding Mill: A Case Study Justine Christianson At the turn of the 20th century, huge piles of oyster shells could be found outside the numerous seafood packinghouses to 80% of the total world output14 The New England region and New York State were the leading producers in the US from 180727, with New Haven 2023年5月22日 Test rig—grinding installation with electromagnetic mill The grinding installation used in this research is shown in Fig 1Feed material is supplied with a screw feeder and enters the working Model and simulator of inlet air flow in grinding installation with 6 Du et al Applied Mathematics and Nonlinear Sciences (aop)1–8 Fig 7 Pressure ratio in coal mill 1 It can be seen from Figure 4 that the output of the ball grinder first increases and then Applied Mathematics and Nonlinear Sciences ResearchGateOutput Capacity: 10 lbs per hr Maximum Fineness: 75 to 100 mesh: Output 4F Hand Mill Brochure; The original Quaker City Grinding Mill (QCG) Over 100 years in service The F4 manual, disk grinding mill is used in fine testing labs around the worldModel 4F Hand Mill Quaker City Grinding Mills QCG Sys
.jpg)
INCREASING OUTPUT OF CEMENT GRINDING IN BALL MILL
Increasing Output Of Cement Grinding In Ball MillCase Study 5 INCREASING OUTPUT OF CEMENT GRINDING IN BALL MILLCASE STUDY 1MOHAN SINGH PANWAR, 2AJAY KUMAR BANSAL, 3HEMANI PALIWAL 1Student, 2Guide, 3External Guide Email: l, 2ajaykumarbansal@poornima, 3hemani8588@gmailOutput: 6 t/h 350 t/h Motor power: 75 kW 3,300 kW Machine length: 2,400 mm 7,200 mm WTM intelligent vertical mill is dedicated to the highefficiency dissociation of minerals, providing users with energysaving, consumption Stone mill, Stone grinding mill All industrial 2023年3月15日 Comprehensive Optimization, Lower Operating Costs From aspects of grinding efficiency, powder drying, abrasion of vulnerable parts and maintenance replacement of spare parts, SBM’s LM Vertical Grinding Mill LM Vertical Grinding Mill SBM Mill CrusherBall mill grinding machines are valuable tools in various industries, offering efficient and reliable grinding and mixing capabilities Understanding their working principle, different types, parts, applications, advantages, and recent developments helps to appreciate their significance and wideranging applications in industries such as cement, mining, pharmaceuticals, chemicals, Ball Mill Grinding Machines: Working Principle, Types, Parts
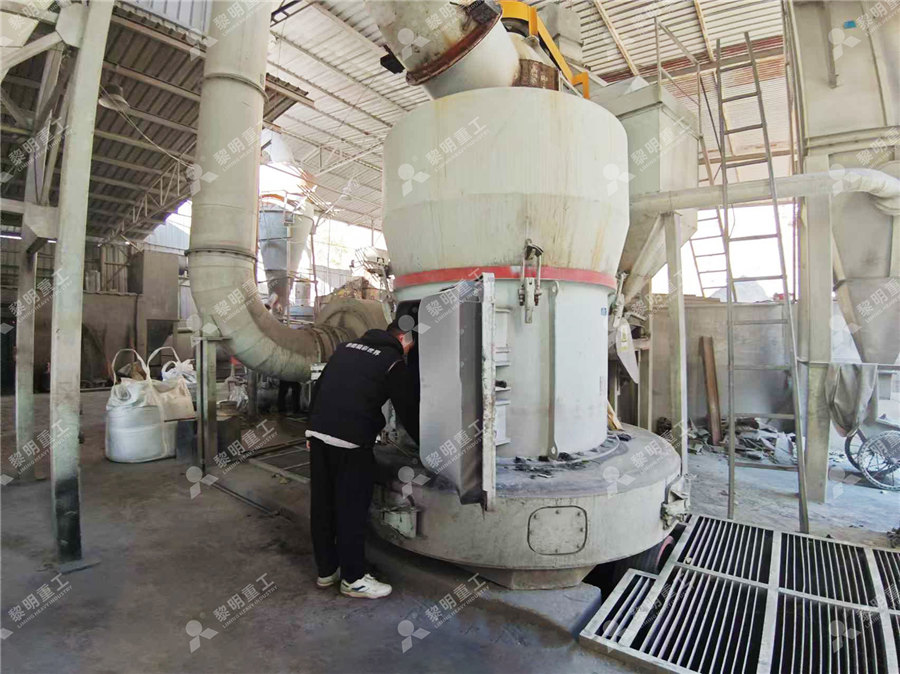
Analysis of the efficiency of the grinding process in closed circuit
Analysis of the efficiency of the grinding process in closed circuit ball mills Valery I Telichenko1, Rashid R Sharapov1*, Svetlana YLozovaya2 and Vladimir ISkel1 1Moscow State University of Civil Engineering, Moscow, Russia 2Belgorod State Technological University named after VG Shukhov, Belgorod, Russia Abstract Ball mills for fine grinding cement clinker and additives areThe heavy duty mill, aimed for industrial purposes, has a strong frame, hardwearing shaft and bearings The adjustment of the stones has an adjustment gear for fine tuning All in all an industrial mill used for grinding whole grain into grits or healthy and good whole meal flour or for grinding of flour grits into high class flour as the lastGrindmaster 950 Perfect for professional Grinding EngskoOutput: 200 kg/h Motor power: 17 kW Machine length: 180 cm 1General Specifications Modern Stone Sesame Grinding Mill Capacity is up to 200 kg/h 2 Heads for Grinding Stone 7,5Kw 10Hp 380V 50Hz Motor 380V threephase mill, 380V threephase grinding millPerformance evaluation results of vertical roller mill in cement grinding application are presented SAMPLING STUDIES In this study, a new sampling method developed byPerformance Evaluation of Vertical Roller Mill in Cement Grinding
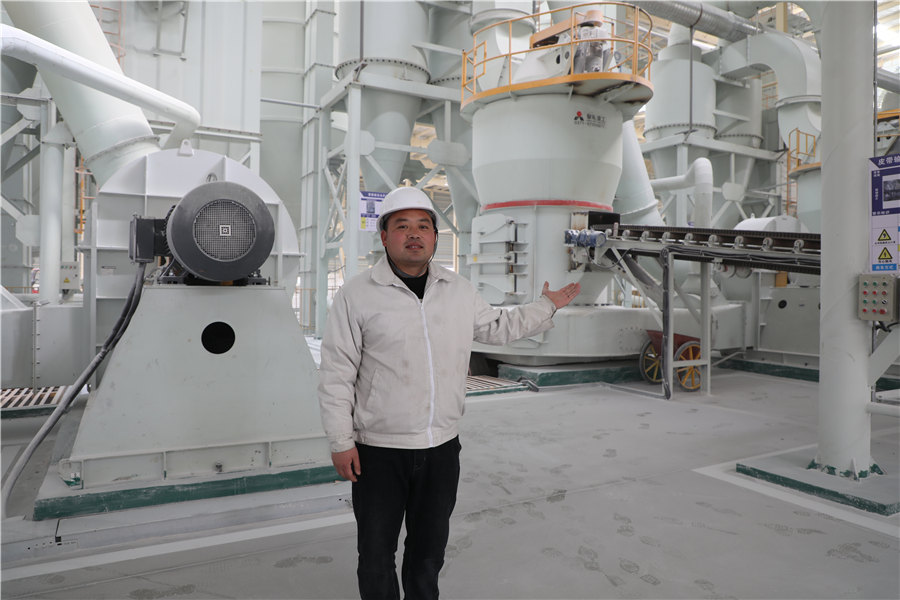
Principles of Modern Grinding Technology ResearchGate
2013年1月1日 PDF Principles of Modern Grinding Technology explains the principles that led to rapid improvements in modern grinding technology over recent decades Find, read and cite all the research 2013年8月3日 In Grinding, selecting (calculate) the correct or optimum ball size that allows for the best and optimum/ideal or target grind size to be achieved by your ball mill is an important thing for a Mineral Processing Engineer AKA Metallurgist to do Often, the ball used in ball mills is oversize “just in case” Well, this safety factor can cost you much in recovery and/or mill liner Calculate and Select Ball Mill Ball Size for Optimum Grinding