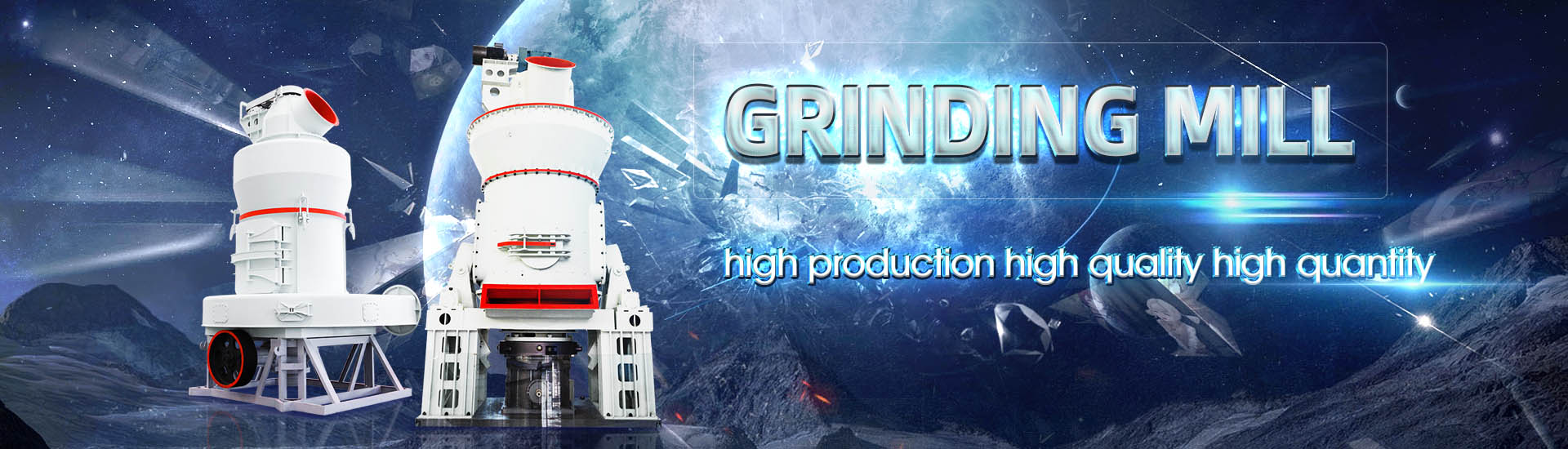
Factors affecting specific surface area of vertical mill operation
46.jpg)
Operational parameters affecting the vertical roller mill
2017年4月1日 In this study, pilot scale tests were performed with a mobile verticalrollermill grinding plant to investigate the relationships between operational parameters The 2016年9月1日 By initiating a CL for an industrial cement vertical roller mill (VRM), this study conducted a novel strategy to explore relationships between VRM monitored operational Operational parameters affecting the vertical roller mill As a result of the study, effects of operational parameters such as working pressure, and classifier rotor speed on product mass flow and product size were investigated In addition, correlations (PDF) Operational parameters affecting the vertical roller mill 2024年1月15日 Optimisation of the mill design has been carried out based on CFD modelling results Proposed reconfigurations produce a positive pressure upstream, suppressing air Optimisation of the performance of a new vertical roller mill by
.jpg)
Analysis and Optimization of Grinding Performance of
2022年1月23日 For design of experiments (DOE), the response surface method (RSM) was employed with the VRM experiments to systematically investigate the influence of operating parameters on the energy2022年1月23日 As reported by Boehm and by Altun , there are several factors affecting the grinding effect, among which the loading pressure and feed rate are more important, while the motor rotation speed and the moisture content of Analysis and Optimization of Grinding Performance of In this study, the effects of four grinding aids (Triisopropanolamine based (TIPA), Triethanolamine based (TEA), Hydroxylamine based (HA), and Calcium nitrate based (CN) grinding aids) in the clinker grinding process were evaluated on VERTICAL ROLLER MILL OPERATION PARAMETERS2021年9月1日 Vertical roller mill was separated into the two section as grinding and separation Grinding operation was defined by population balance model and breakage rate was Modelling of pilot scale vertical roller mill operated in overflow
.jpg)
Optimization of Milling Parameters for Energy Savings and Surface
2020年6月11日 This paper aims to optimize the machining inputs to enhance energy efficiency (EF) as well as the power factor (PO) and decrease the surface roughness (Ra) for the milling The share of windbased electricity generation is gradually increasing in the world energy market Wind energy can reduce dependency on fossil fuels, as the result being attributed to a decrease in global warming This paper discusses and reviews the basic principle parameters that affect the performance of wind turbines An overview presents the introduction and the background of Principle Parameters and Environmental Impacts that Affect 2021年1月29日 VRM Production Rate and Specific Power It can be clearly seen in Figure 3 that last 6 months average breakdown frequency Rate was 6016 tripping per month means per day more than 2 trippingIncrease productivity of vertical roller mill using seven 2013年9月9日 The advantages of size reduction are that it leads to increased surface area, which, in the pharmaceutical industry, leads to an increase in the therapeutic effectiveness of drugs (Sud Kamath METHODS OF SIZE REDUCTION AND FACTORS AFFECTING SIZE
.jpg)
Predicting the effect of operating and design variables in
2021年7月1日 Vertical stirred mills may be classified according to the speed of the stirrer in two groups: gravityinduced or fluidized mills [[1], [2], [3]]In the gravityinduced mills, the stirrer, generally of the screw type, turns so that the grinding charge exhibits an ascending convective motion at the center, descending from the edges of the screw and close to the mill shell, owing 2023年12月12日 [Show full abstract] disk mill It increases the Blaine specific surface area of the mixtures of 95 % clinker and 5 % gypsum by 16 and 76 % in ball and vibrating disk mills, respectively (PDF) Control of ball mill operation depending on ball load and 2018 In this chapter an introduction of widely applied energyefficient grinding technologies in cement grinding and description of the operating principles of the related equip‐ ments and comparisons over each other in terms of grinding efficiency, specific energy consumption, production capacity and cement quality are given(PDF) CEMENT RAW MATERIAL GRINDING ; VERTICAL ROLLER MILL OPERATION 2023年7月10日 The present literature review explores the energyefficient ultrafine grinding of particles using stirred mills The review provides an overview of the different techniques for size reduction and the impact of energy requirements on the choice of stirred mills It also discusses the factors, including the design, operating parameters, and feed material properties, EnergyEfficient Advanced Ultrafine Grinding of Particles Using
.jpg)
Some factors affecting sieving performance and efficiency
2009年7月25日 Download Citation Some factors affecting sieving performance and efficiency Sieving or screening has been the oldest yet most important unit operation for industrial separation of solid Table Energy saving effect of the vertical roller mill Ball mill Specific power Cost estimation About 14million US$ [Newlybuilt] and about 230 million US$ [retrofitted], including the cost of supplemental facilities [200tRM/h] [1US$=¥110] Related matters References Fig1 Vertical roller mill Vertical roller mill Effect(%) Production % 100 Vertical roller mill for raw Application p rocess materials2012年3月1日 the distributions of the ball mill and the vertical roller mill Fig 6a shows an example of the circularity of a ground granulated blastfurnace slag, produced with the LM 352+2Operating experience with a vertical roller mill for grinding 2021年12月5日 ANALYSIS OF THE FACTORS AFFECTING THE These two tables are presented together because all data can be seen easily in a single table and create ease of operation specific surface area(PDF) ANALYSIS OF THE FACTORS AFFECTING THE
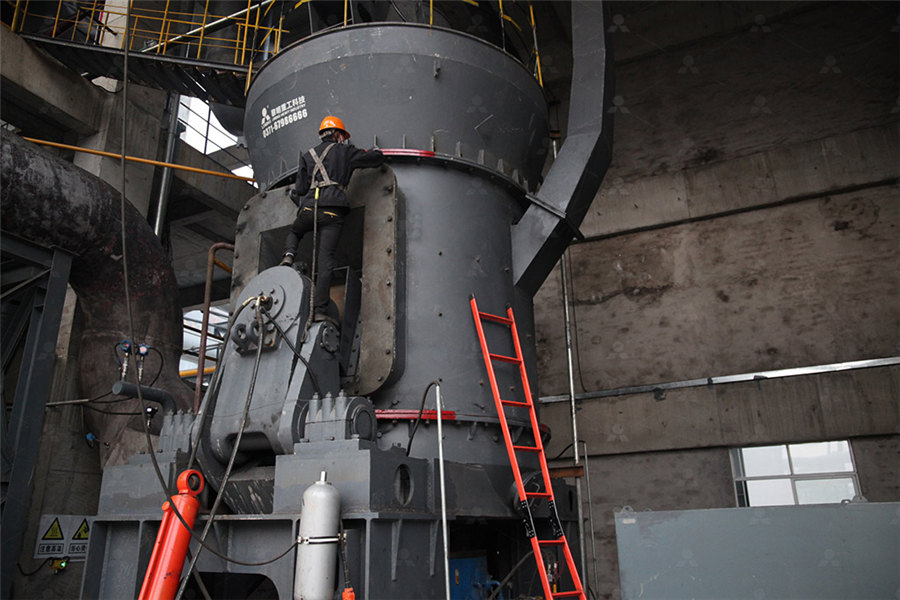
Analysis and Optimization of Grinding Performance of
2022年1月23日 This work concentrates on the energy consumption and grinding energy efficiency of a laboratory vertical roller mill (VRM) under various operating parametersof 80mm The raw materials are mixed in a certain proportion and fed into a vertical roller mill (LOESCHE mill) The vertical roller mill grinds the marital to D 85 of 90µm The ground product is calcined in a preheater to 850900℃ After calcination, the materials enter to a rotary kiln and heated to 1450℃ to become clinkerModeling and simulation of vertical roller mill using population 2018年9月20日 The specific surface area (SSA) of fly ash has a significant effect on its pozzolanic reactivity and on the performance of fly ashblended concreteA comparison of the specific surface area of fly ashThe surface completion of the processed workpiece is the nature of the surface that is made by the milling instrument The surface completion is impacted by various elements, including the apparatus calculation, feed rate, and profundity of cut The surface completion of a processed workpiece can be estimated utilizing various techniques,Investigation And Analysis Of Factors Affecting Milling Operation
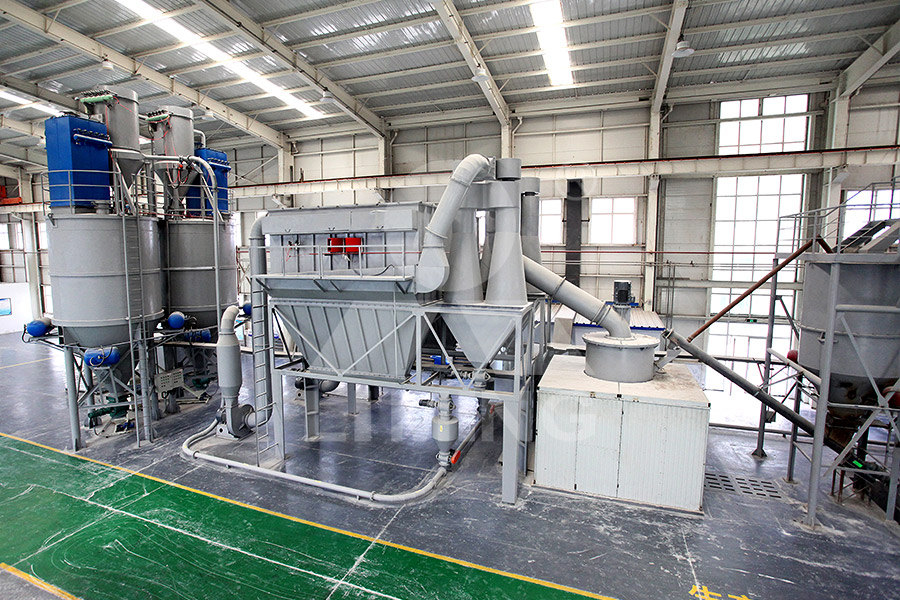
(PDF) Factors Affecting the Design and Operation of
2010年1月1日 Factors Affecting the Design and Operation of Biologically Active Filters actual mediaspecific surface area, BAF performance results typically are e xpressed as a function 2013年3月1日 This study investigated a mathematical model for an industrialscale vertical roller mill(VRM) at the Ilam Cement Plant in Iran The model was calibrated using the initial survey's data, and the Cements ground in the vertical roller mill fulfil the quality 2022年5月31日 Mineral crushing is the main source of energy consumption in mineral processing According to statistics, this consumption accounts for about 35–50% of the total cost of the mine (Curry et al, 2014), or even higherIt may also account for 18% of the global electrical energy consumption (NapierMunn, 2015)More efficient crushing equipment needs to be Analysis of vertical roller mill performance with changes in 2022年3月23日 Fine particles have large surface area Specific surface area is defined as the surface area per unit mass The other factors which affect the operation of roll crusher are rotational speed, diameter of rolls, This mill usually consists of a vertical rotor inside a circular screen enclosureSize Reduction SpringerLink
.jpg)
Effects of Mill Speed and Air Classifier Speed on Performance of
2021年6月29日 Special importance was assigned to the study of the specific surface area and the surface area production rate, both during the variation with the mill speed and the air classifier speed2023年8月5日 In summary, in fact, most of the factors affecting the output particle size of the highpressure roller mill are in the operation mode When the appropriate roller surface pressure and roller surface speed are selected, the output particle size of the highpressure roller mill can reach productionFactors affecting the particle size of the highpressure roller mill2022年1月23日 This work concentrates on the energy consumption and grinding energy efficiency of a laboratory vertical roller mill (VRM) under various operating parameters For design of experiments (DOE), the response surface method Analysis and Optimization of Grinding Performance of Prziwara et al studied grinding aids' effects on bulk properties such as product neness, particle size distribution, powder ow ability, surface area and surface energy [8] some studies on the Schematic operation principle of a verticalrollermill
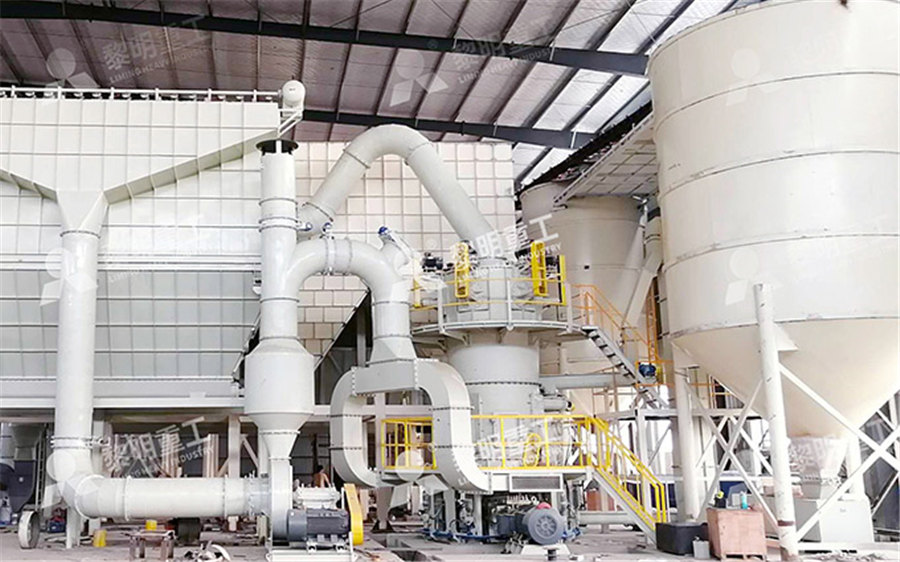
Factors Affecting the Performance of Vibrating Mills ball mills
Factors Affecting Vibrating Mills’ Performance Other factors to consider in mill design and operation include the use of liners to prevent wear and prolong the mill’s lifespan, vertical mill, rod mill and AG/SAG mill for grinding in a variety of industries and materials Contact : info@ballmillssupplier; Tel: +86 ;Larger media will create more impact and shear forces, resulting in more effective grinding, while smaller media will create more surface area, allowing for more efficient grinding The type of media can also impact the milling process, with ceramic media being more effective for grinding harder materials and steel media being more effective for grinding softer materialsFactors that Affect the Efficiency and Effectiveness of Attritor In vertical milling machines, the spindle is oriented vertically just as the name suggests, meaning that the cutting tool, usually a drill bit end mill, moves up and down along the Z axis Vertical milling machines are popular with tasks that require cutting and shaping materials in The Comparison Between Horizontal Milling And Vertical Milling2017年4月1日 Separation operation of verticalrollermill will be modelled by application of current models The model shall enable the prediction of the throughput, the particle size distributions around the verticalrollermill circuit, the specific energy consumption and in a later stage the wear to be expected in dependency of ore treatedOperational parameters affecting the vertical roller mill

A datadriven decisionmaking framework for online control of vertical
2020年5月1日 Vertical Vibration of Reducer: L0025: Mill Outlet Temperature: L0045: Specific Surface Area of Micropowder: L0006: Horizontal Vibration of Reducer: L0026: Mill Pressure Difference: L0046: Gas Pressure: L0007: Given Value of Main Roller Pressure: L0027: Dust Collector Outlet Pressure: L0047: Given Value of Gas Valve Opening: L0008: Feedback The parts of a ball mill Ball mills are used to grind various ores and other materials into a fine powder In order for the mill to function properly, it requires accurate and consistent grinding There are a number of factors that affect the grinding performance of ball mills, some of which are discussed belowFactors affecting ores grinding performance in ball mills2024年4月25日 Buildings 2024, 14, 1227 3 of 21 where: Ls is the luminance of the glare source(s) [cd/m2]; ω is the solid angle subtending each source [sr]; L b is the background luminance [cd/m2]; P is the Guth position index for each source; AP is apparent area of the glare source(s) [m2]; S is area of the glare source(s) [m2]; r is the distance from the observation Morphological and Position Factors of Vertical Surface Light The share of windbased electricity generation is gradually increasing in the world energy market Wind energy can reduce dependency on fossil fuels, as the result being attributed to a decrease in global warming This paper discusses and reviews the basic principle parameters that affect the performance of wind turbines An overview presents the introduction and the background of Principle Parameters and Environmental Impacts that Affect
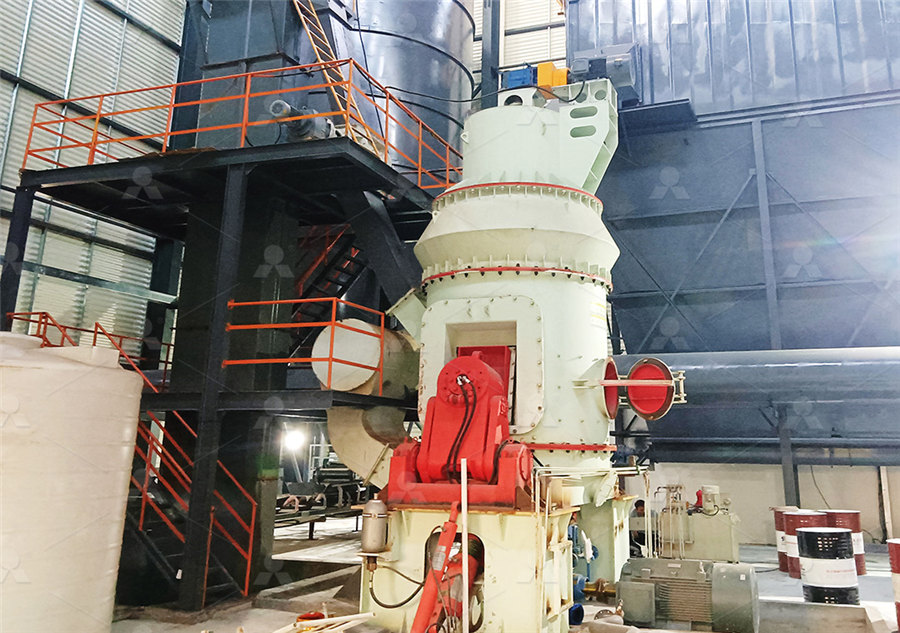
Increase productivity of vertical roller mill using seven
2021年1月29日 VRM Production Rate and Specific Power It can be clearly seen in Figure 3 that last 6 months average breakdown frequency Rate was 6016 tripping per month means per day more than 2 tripping2013年9月9日 The advantages of size reduction are that it leads to increased surface area, which, in the pharmaceutical industry, leads to an increase in the therapeutic effectiveness of drugs (Sud Kamath METHODS OF SIZE REDUCTION AND FACTORS AFFECTING SIZE 2021年7月1日 Vertical stirred mills may be classified according to the speed of the stirrer in two groups: gravityinduced or fluidized mills [[1], [2], [3]]In the gravityinduced mills, the stirrer, generally of the screw type, turns so that the grinding charge exhibits an ascending convective motion at the center, descending from the edges of the screw and close to the mill shell, owing Predicting the effect of operating and design variables in 2023年12月12日 [Show full abstract] disk mill It increases the Blaine specific surface area of the mixtures of 95 % clinker and 5 % gypsum by 16 and 76 % in ball and vibrating disk mills, respectively (PDF) Control of ball mill operation depending on ball load and
.jpg)
(PDF) CEMENT RAW MATERIAL GRINDING ; VERTICAL ROLLER MILL OPERATION
2018 In this chapter an introduction of widely applied energyefficient grinding technologies in cement grinding and description of the operating principles of the related equip‐ ments and comparisons over each other in terms of grinding efficiency, specific energy consumption, production capacity and cement quality are given2023年7月10日 The present literature review explores the energyefficient ultrafine grinding of particles using stirred mills The review provides an overview of the different techniques for size reduction and the impact of energy requirements on the choice of stirred mills It also discusses the factors, including the design, operating parameters, and feed material properties, EnergyEfficient Advanced Ultrafine Grinding of Particles Using 2009年7月25日 Download Citation Some factors affecting sieving performance and efficiency Sieving or screening has been the oldest yet most important unit operation for industrial separation of solid Some factors affecting sieving performance and efficiencyTable Energy saving effect of the vertical roller mill Ball mill Specific power Cost estimation About 14million US$ [Newlybuilt] and about 230 million US$ [retrofitted], including the cost of supplemental facilities [200tRM/h] [1US$=¥110] Related matters References Fig1 Vertical roller mill Vertical roller mill Effect(%) Production % 100 Vertical roller mill for raw Application p rocess materials
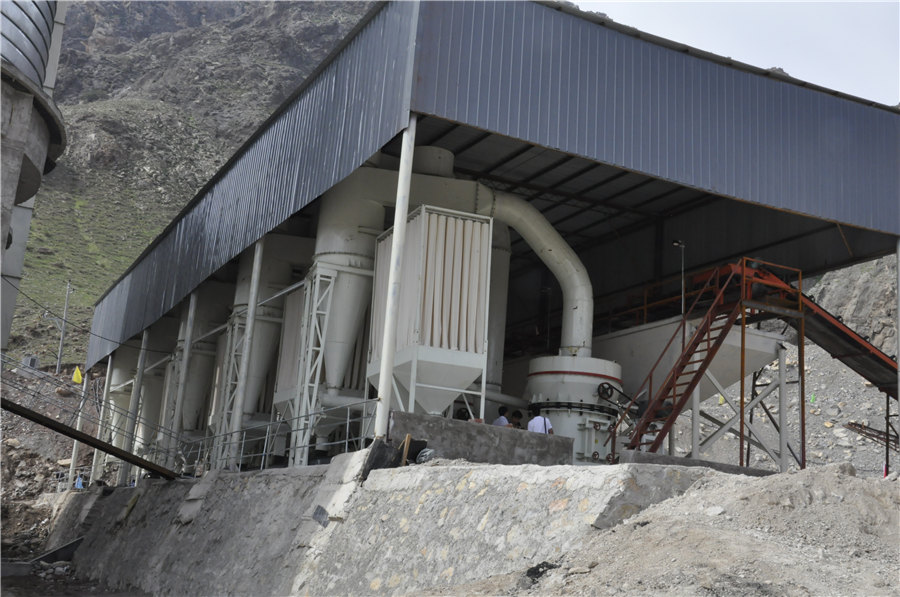
Operating experience with a vertical roller mill for grinding
2012年3月1日 the distributions of the ball mill and the vertical roller mill Fig 6a shows an example of the circularity of a ground granulated blastfurnace slag, produced with the LM 352+2