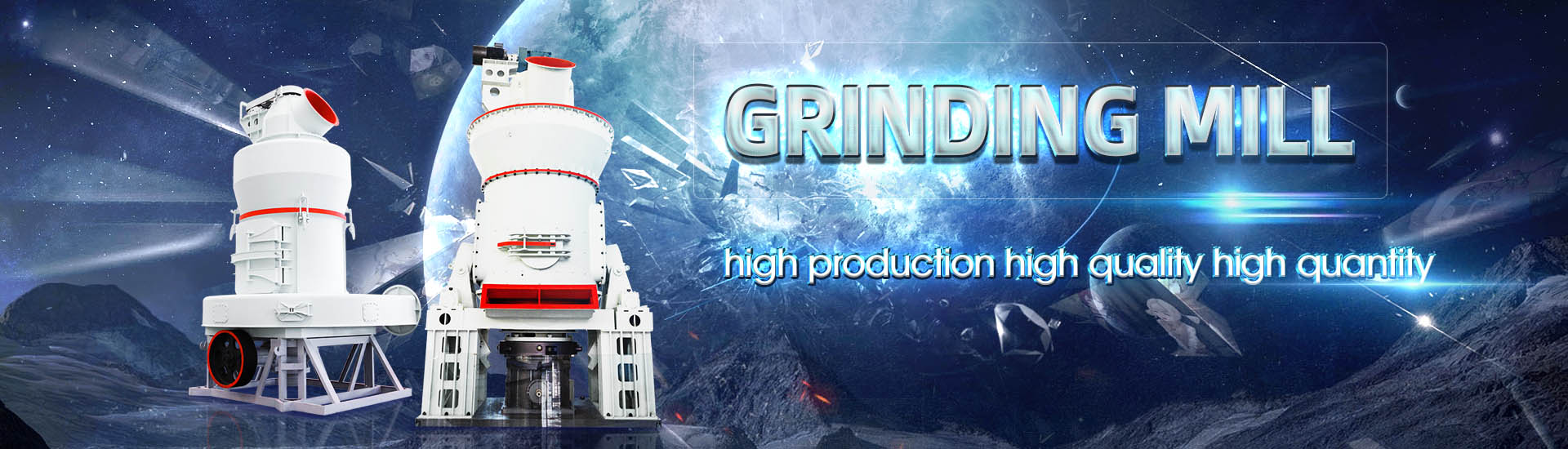
Stone ironmaking
-2.jpg)
Ironmaking Process an overview ScienceDirect Topics
Ironmaking is to convert iron ore or other ironbearing materials into a form that can be easily transformed into steel This is done primarily in a BF with other auxiliary facilities to smelt the 2014年1月1日 This chapter describes the ironmaking technology and outlines the process essentials The main focus was given to the blast furnace process, which is still the dominating Ironmaking ScienceDirect2015年1月1日 Mini steel mills normally use the EAF to produce steel from scrap and direct reduced iron (DRI) Since the EAF uses scrap and DRI instead of molten iron, cokemaking Quality requirements of iron ore for iron productionThe primary objective of iron making is to release iron from chemical combination with oxygen, and, since the blast furnace is much the most efficient process, it receives the most attention Iron processing Smelting, Refining, Alloying Britannica
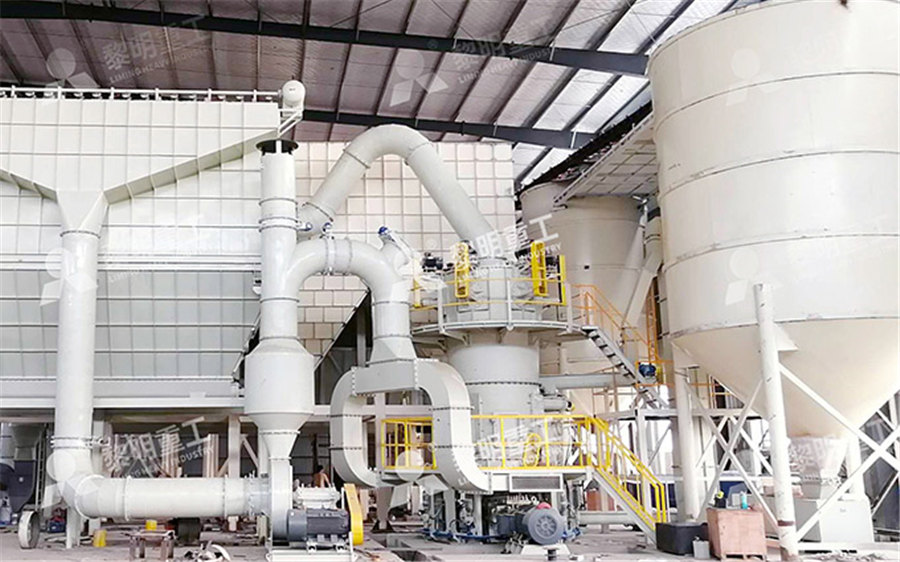
Production of Iron in the Blast Furnace SpringerLink
2020年8月19日 Analyzing the history of the ironmaking allows better understanding the current production technologies and their future developments Humans started to reduce iron ores in 2023年10月6日 Blast furnace ironmaking is a continuous metallurgical process in which iron ore is reduced to liquid pig iron in a blast furnace It is developed and improved from the ancient Blast Furnace Ironmaking SpringerLinkIron, one of the most fundamental elements on Earth, has played a pivotal role in shaping human civilization The journey of ironmaking techniques spans millennia, evolving from ancient Evolution of Ironmaking Techniques From Ancient to Modern 2017年10月17日 Ironmaking is a critical step in producing high performance steel because highquality raw materials reduce the time and energy to purify the iron to steel On the other hand, Ironmaking 101 – From Ore to Iron with Smelting and

Iron processing Definition, History, Steps, Uses,
Iron processing, use of a smelting process to turn the ore into a form from which products can be fashioned Included in this article also is a discussion of the mining of iron and of its preparation for smelting Iron (Fe) is a relatively dense How the history of ironmaking in Scunthorpe has shaped the town's future August 10: The foundation stone for Scunthorpe’s first library in High Street East (then Station Road) 150 Years of Ironmaking in Scunthorpe Issuu2013年5月8日 In ironmaking, limestone and dolomite are used in the production of sinter, pellets, and directly in blast furnace as fluxing materials In case of steelmaking limestone and dolomite are used as lime or calcined dolomite Limestone and Dolomite and their Use in Iron and The stone's analysis showed it to be calcareous, unlike the silicarich Northamptonshire ore with which the Frodingham stone later came to be associated The Lincolnshire stone varied considerably in its chemical composition, not only from seam to seam, but also at different points along the same seamScunthorpe and the Establishment of Ironmaking Go back
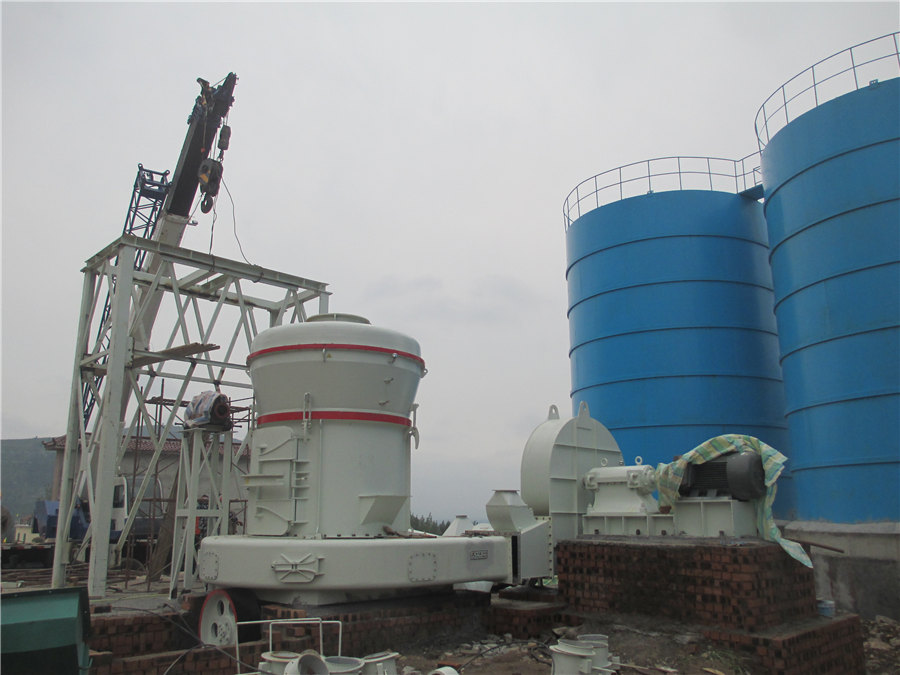
Ironmaking 101 – From Ore to Iron with Smelting and
2017年10月17日 Smelting Reduction Figure 2: The smelt reduction vessel (SRV) is the core technology component of the Hismelt process Source: RioTinto While years of ironmaking technology innovations have optimized blast furnace productivity, two alternative processes—smelting reduction and direct iron reduction— are growing in adoption The Iron processing Smelting, Refining, Alloying: The primary objective of iron making is to release iron from chemical combination with oxygen, and, since the blast furnace is much the most efficient process, it receives the most attention here Alternative methods known as direct reduction are used in over a score of countries, but less than 5 percent of iron is made this wayIron processing Smelting, Refining, Alloying Britannica2023年5月19日 Ironmaking sites in Han Dynasty also included the casting workshops located near urban area, eg, the ironmaking site from the Han Dynasty in Nanyang, The stone sculpture from the Han Dynasty unearthed at the Hongdao Monastery in Tengzhou, Shandong, depicts the leather bag (around 06 m diameter and 1 m length) used for forgingHistory of Metallurgy SpringerLink2014年1月1日 This chapter describes the ironmaking technology and outlines the process essentials The main focus was given to the blast furnace process, which is still the dominating technology for ironmaking The early blast furnace had about a 6 m × 6 m square formed stone foundation and 6–8 Ironmaking ScienceDirect
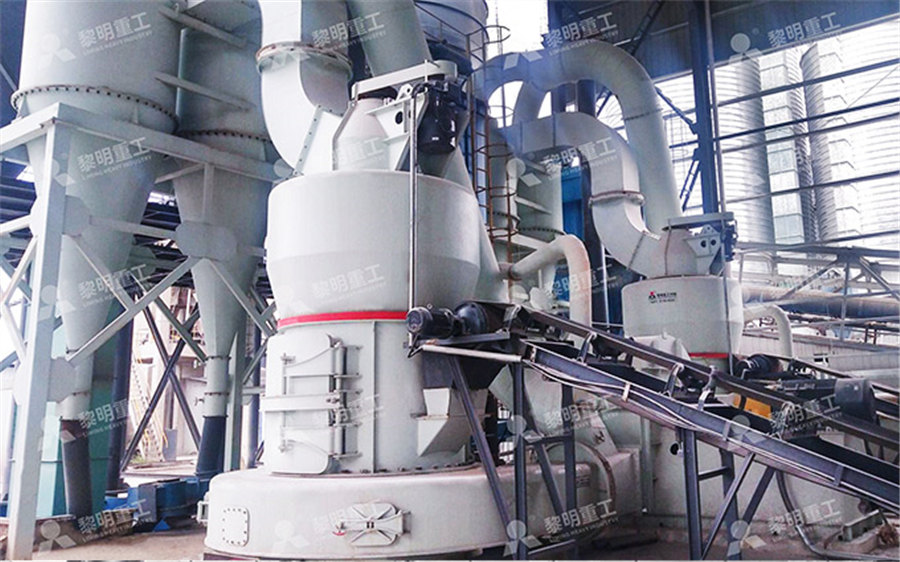
NPTEL :: Metallurgy and Material Science NOC:Ironmaking and
Lecture 05: Thermodynamics of BF Ironmaking (continued) Download Verified; 6: Lecture 06: Overall Heat Material Balance in Blast Furnace: Download Verified; 7: Lecture 07: RIST Diagram based on overall heat and material balance: Download Verified; 8:As mined, limestone requires refinement prior to use in the steelmaking and ironmaking processes to react properly Limestone fines are also used in the production of sinter and directreduced iron To be useful in the steelmaking and ironmaking processes, limestone is heated in a rotary lime kiln to create what is called “burnt” lime, or calcium oxide (CaO)Turning Limestone into Lime Reibus International2023年6月10日 In the process of blast furnace ironmaking, Slagforming in blast furnace ironmaking is the solvent that interacts with the gangue in the ore and the ash of coke to dissolve, collect, and melt the substances that do not enter pig iron and gas, so that the liquid slag is formed In the blast furnace, slag and pig iron are formed at the same timeSlagForming in Blast Furnace Ironmaking SpringerLink学术期刊 Ironmaking and Steelmaking:期刊短名:J Iron Steel Inst (London),期刊 ISSN: 03019233, 17432812。Ironmaking Steelmaking: Processes, Products and Applications monitors international technological advances in the industry with a strong element of engineering and product related material First class refereed papers from the international iron and steel Ironmaking and Steelmaking J Iron Steel Inst (London) 期刊影
.jpg)
(PDF) An Overview of the ReductionSmelting Process
2022年8月23日 Preliminary studies have revealed that there are tendencies to achieve more than a 90 % metallization degree from the direct reduction of iron ore/oxides using noncoking coal or charcoal as a 2015年1月1日 The integrated iron and steelmaking route involves blast furnace (BF) ironmaking followed by basic oxygen steelmaking (BOS) The BF uses sinter, pellet, and lump ore as the ironbearing raw materials and coke and pulverized coal as reducing agents to produce hot metal with consistent quality for the BOS processQuality requirements of iron ore for iron productionA blast furnace reduces iron ore into pig iron, also called hot metal, in the ironmaking process, which is the chief ingredient used in the steelmaking process A blast furnace primarily utilizes metallurgical coke, iron ore, and “burnt” lime to produce pig ironWhat is a Blast Furnace? Reibus International2023年11月10日 These factors have contributed to the development of alternative technologies of ironmaking, of which Direct Reduction (DR) processes are expected to emerge as preferred alternatives in the futureA REVIEW OF IRONMAKING BY DIRECT REDUCTION PROCESSES:
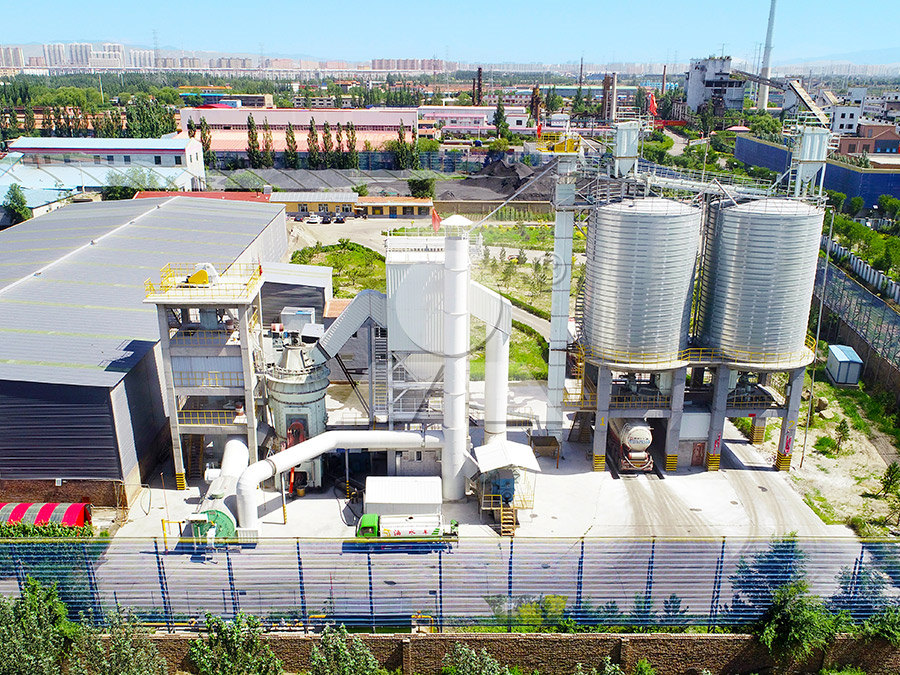
Review on the Application and Development of Biochar in Ironmaking
2023年11月3日 Applying it to ironmaking production is not only conducive to energy conservation and emission reduction in the ironmaking process but also can achieve efficient The results showed that the appropriate ratio of fruit stone charcoal to replace coke powder was 40%, which had little impact on the production and quality of Ironmaking Business and Industry Manufacturing Sign in or create a free account to curate your search content With an abundance of iron ore, timber for charcoal, limestone for flux, and water power, it is not surprising that iron making was one of Western Virginia's earliest industries Iron making began in eWV Ironmaking wvencyclopedia2023年6月10日 Nonblast Furnace Ironmaking It is also known as noncoking ironmaking, mainly including directreduction ironmaking and smeltingreduction ironmaking Directreduction ironmaking is a production process where solid porous ironcontaining materials (commonly called sponge iron) are reduced by iron ore below the melting temperatureIronmaking SpringerLinkstone, dolomite, and silica are widespread throughout the world, although there are examples where an adequate flux source was not available and this affected the process selection Limestone and Dolomite Limestone and dolomite fluxes used for ironmaking and steel making in the United States originate primarily from MichiganMETALLURGICAL USES FLUXES FOR METALLURGY
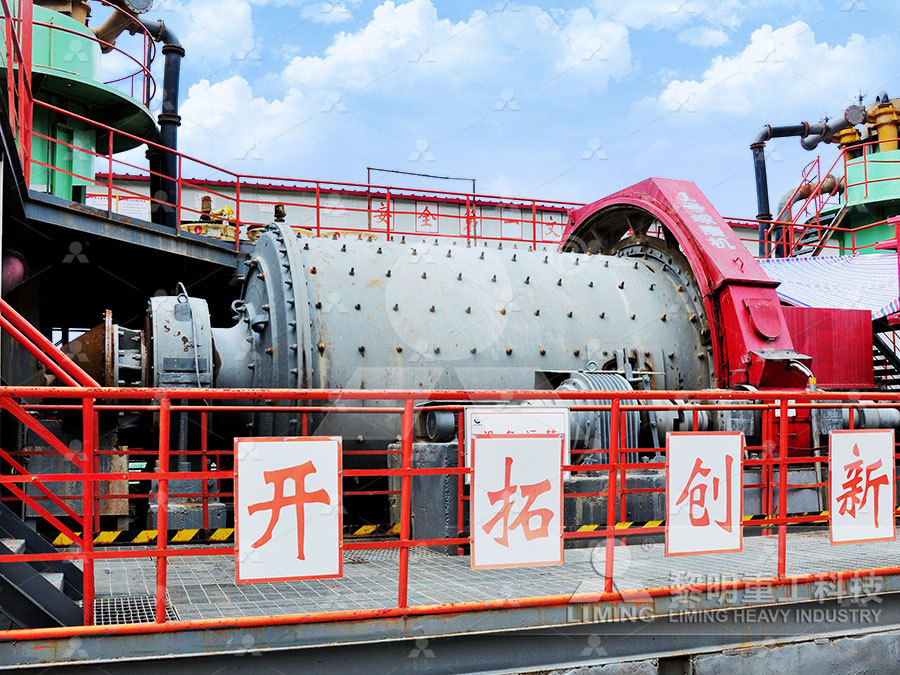
Production of Iron in the Blast Furnace SpringerLink
2020年8月19日 Analyzing the history of the ironmaking allows better understanding the current production technologies and their future developments Humans started to reduce iron ores in around 1500 BC in clay or stone recipients using charcoal 2023年12月11日 The traditional ironmaking technologies (including coking, sintering, pelletizing, and BF ironmaking process) are carbonintensive, which makes the industry a significant contributor to global CO2 emissions Hydrogen replacement of carbon in steelmaking processes is a sustainable way to reduce CO2 emissions First, the reduction thermodynamics and HydrogenBased Reduction Technologies in LowCarbon 2023年10月9日 Comprehensive control of greenhouse gas emissions and response to climate change are concerns of countries around the world to protect living homes The steel industry is responsible for over 10% of global CO2 emissions, with approximately 80% of these emissions coming from the ironmaking process Great efforts have been made in both blast furnace (BF) Development and Problems of Fluidized Bed Ironmaking Process: 2021年7月16日 HTCSLM The HTCSLM is an insitu observation tool consisting of a goldcoated elliptical chamber positioned below a UV imaging laser The chamber has the ability to reach 1700°C at the heating rate of up to 700°C min −1 and cooling rates of up to 3000°C min −1 (in the higher temperature range) Within the chamber, a halogen bulb is located in one focal Full article: Observation of the reactions between iron ore and
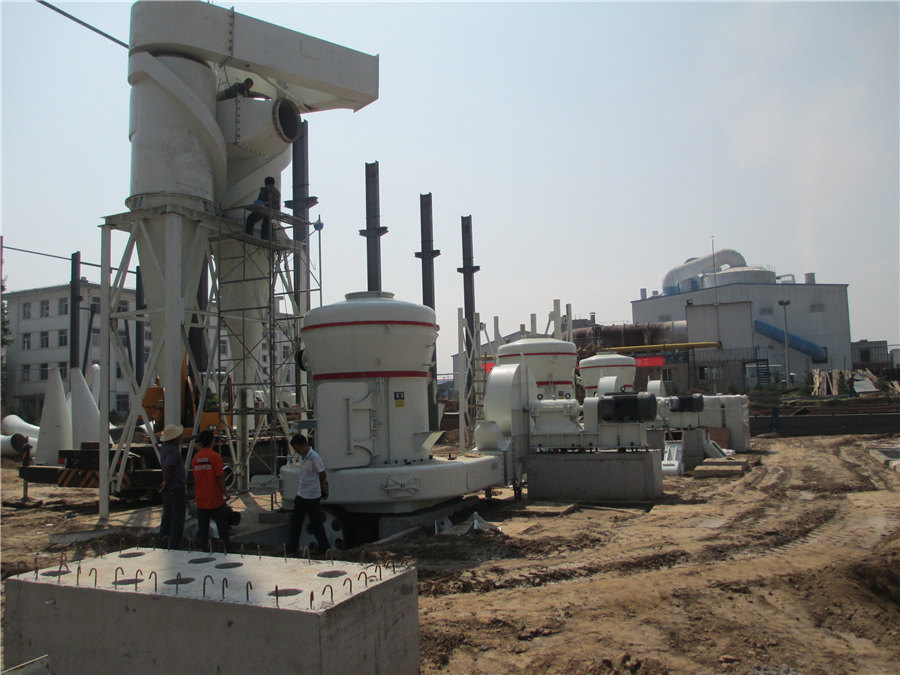
Ironmaking Steelmaking Taylor Francis Online
2023年11月23日 Published by Sage from 2024 Ironmaking Steelmaking: Processes, Products and Applications monitors international technological advances in the industry with a strong element of engineering and product related material First class refereed papers from the international iron and steel community cover all stages of the process, from ironmaking and its 2023年2月23日 By the time the blast furnace arrived in England in the late 15th century, it had "developed into a stone tower, roughly square in plan and about 67 meters high" To give access to the top for adding the charge, blast furnaces would often be built near a hill or embankment, with a bridge connecting the hill to the top of the furnaceThe Blast Furnace: 800 Years of Technology Improvement2006年7月1日 According to the method, for certain parts of the country, the wearing course can be constructed with local aggregates that have minimum polished stone value (PSV) of 40 (PSV ≥ 40), but, in this Utilization of Ironmaking and Steelmaking Slags ResearchGateStone coal was successfully used to synergistically treat stainless steel slag (SSS) to recover both chromium (Cr) and vanadium (V) The alloy with a Cr grade of 7084% and a V grade of 236% can be obtained by keeping SSS and stone coal at a ratio of 50 : 31 at 1600 °C for 120 min The corresponding recovery rates of Cr and V are as high as 9951% and 8125%, respectively Detoxification and synergistic recovery of Cr and V from stainless
.jpg)
Slovenian ironmaking museum Gornjesavski muzej Jesenice
SLOVENIAN IRONMAKING MUSEUM Permanent exhibition on the owners of iron foundries and the history of ironmaking in Jesenice Permanent exhibition Rise and various quality construction and art elements have been preserved, such as stone frames, portals and documented paintings with Renaissance, historical and Secession motifs Opening 2017年5月17日 Coal is conveyed to coal/flux stone pulverizers for sizing to 80 % minus 200 mesh size Fig 6 General process flow during the ironmaking in RHF The reduction of iron ore/coal agglomerates in a RHF is a cokefree, environmentally friendly ironmaking processIronmaking in Rotary Hearth Furnace – IspatGuruIron processing, use of a smelting process to turn the ore into a form from which products can be fashioned Included in this article also is a discussion of the mining of iron and of its preparation for smelting Iron (Fe) is a relatively dense Iron processing Definition, History, Steps, Uses,How the history of ironmaking in Scunthorpe has shaped the town's future August 10: The foundation stone for Scunthorpe’s first library in High Street East (then Station Road) 150 Years of Ironmaking in Scunthorpe Issuu
.jpg)
Limestone and Dolomite and their Use in Iron and
2013年5月8日 In ironmaking, limestone and dolomite are used in the production of sinter, pellets, and directly in blast furnace as fluxing materials In case of steelmaking limestone and dolomite are used as lime or calcined dolomite The stone's analysis showed it to be calcareous, unlike the silicarich Northamptonshire ore with which the Frodingham stone later came to be associated The Lincolnshire stone varied considerably in its chemical composition, not only from seam to seam, but also at different points along the same seamScunthorpe and the Establishment of Ironmaking Go back2017年10月17日 Smelting Reduction Figure 2: The smelt reduction vessel (SRV) is the core technology component of the Hismelt process Source: RioTinto While years of ironmaking technology innovations have optimized blast furnace productivity, two alternative processes—smelting reduction and direct iron reduction— are growing in adoption The Ironmaking 101 – From Ore to Iron with Smelting andIron processing Smelting, Refining, Alloying: The primary objective of iron making is to release iron from chemical combination with oxygen, and, since the blast furnace is much the most efficient process, it receives the most attention here Alternative methods known as direct reduction are used in over a score of countries, but less than 5 percent of iron is made this wayIron processing Smelting, Refining, Alloying Britannica
.jpg)
History of Metallurgy SpringerLink
2023年5月19日 Ironmaking sites in Han Dynasty also included the casting workshops located near urban area, eg, the ironmaking site from the Han Dynasty in Nanyang, The stone sculpture from the Han Dynasty unearthed at the Hongdao Monastery in Tengzhou, Shandong, depicts the leather bag (around 06 m diameter and 1 m length) used for forging2014年1月1日 This chapter describes the ironmaking technology and outlines the process essentials The main focus was given to the blast furnace process, which is still the dominating technology for ironmaking The early blast furnace had about a 6 m × 6 m square formed stone foundation and 6–8 Ironmaking ScienceDirectLecture 05: Thermodynamics of BF Ironmaking (continued) Download Verified; 6: Lecture 06: Overall Heat Material Balance in Blast Furnace: Download Verified; 7: Lecture 07: RIST Diagram based on overall heat and material balance: Download Verified; 8:NPTEL :: Metallurgy and Material Science NOC:Ironmaking and As mined, limestone requires refinement prior to use in the steelmaking and ironmaking processes to react properly Limestone fines are also used in the production of sinter and directreduced iron To be useful in the steelmaking and ironmaking processes, limestone is heated in a rotary lime kiln to create what is called “burnt” lime, or calcium oxide (CaO)Turning Limestone into Lime Reibus International