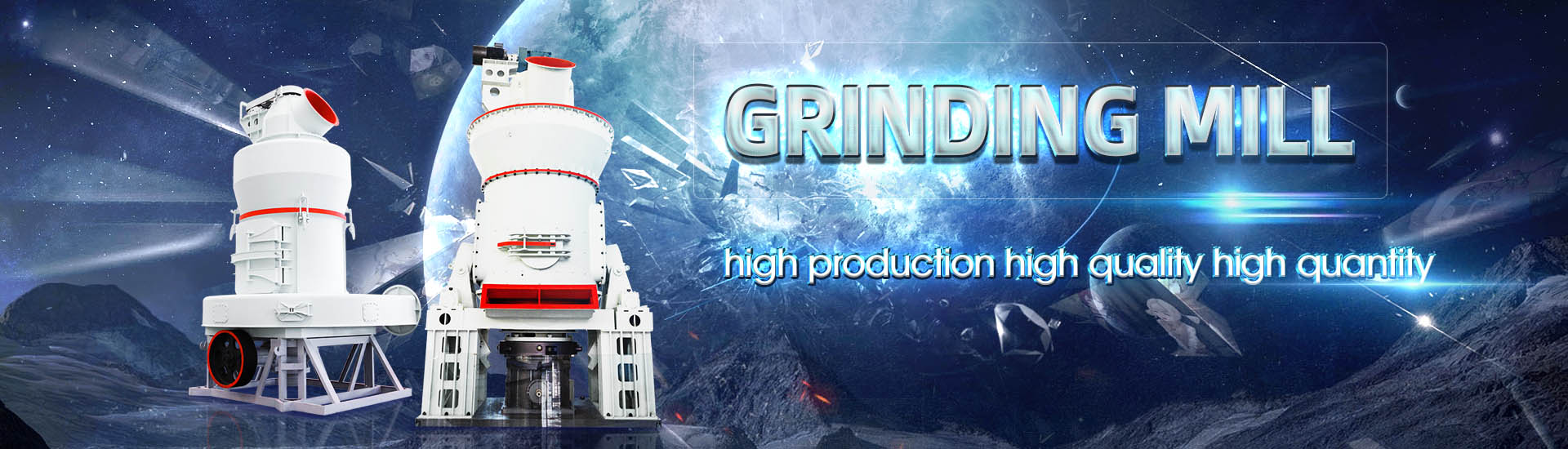
2 4X10 ore grinding steel ball ratio parameters
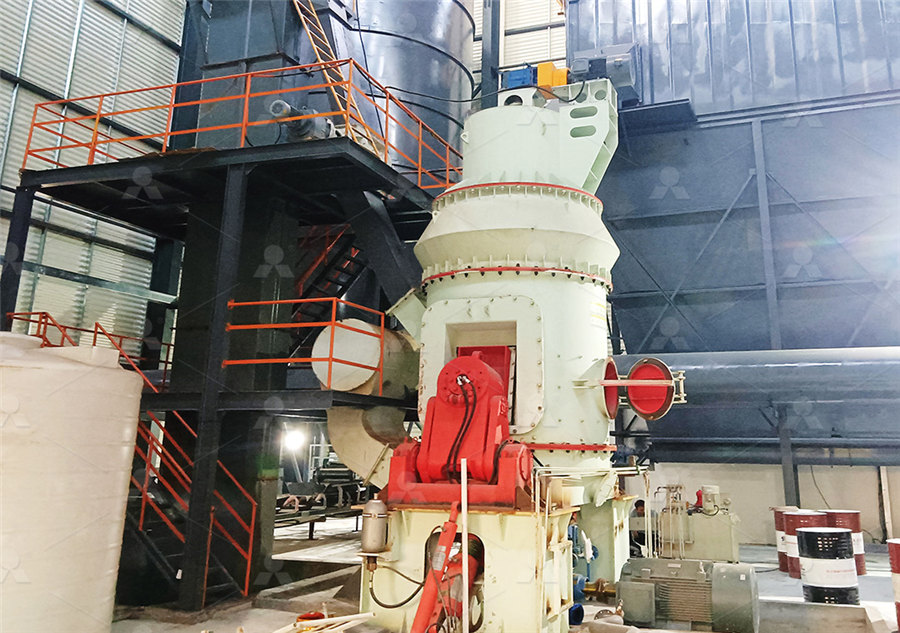
Effect of design and operational parameters on particle
2017年8月10日 With reducing the surface area of steel balls in constant volume, the ball size is increased and changing particleball engagement causes dominance of impact mechanism In 2023年10月27日 Grinding media play an important role in the comminution of mineral ores in these mills This work reviews the application of balls in mineral processing as a function of the A Review of the Grinding Media in Ball Mills for Mineral Processing 2024年8月27日 This study explores the effect of steel ball size and proportion on mineral grinding characteristics using Discrete Element Method (DEM) simulations Based on batch grinding kinetics, this paper analyzes the contact Investigating the Influence of Medium Size and Ratio 2018年6月1日 In this article, alternative forms of optimizing the milling efficiency of a laboratory scale ball mill by varying the grinding media size distribution and the feed material particle size Effect of ball and feed particle size distribution on the milling
.jpg)
Mill Load Measurement SpringerLink
2023年5月28日 The operating parameters related to mill load are as follows (1) Materialball ratio, the ratio of material volume to the void volume of steel balls in the static state (2) 2012年6月1日 There are three types of grinding media that are commonly used in ball mills: • steel and other metal balls; • metal cylindrical bodies called cylpebs;Grinding in Ball Mills: Modeling and Process Control ResearchGate2021年1月22日 Based on the specific productivity and grinding efficiency, the appropriate grinding parameters were ascertained as follows: material ball ratio of 07, ceramic ball An innovative approach for determining the grinding media 2012年12月1日 Analysis of variance (ANOVA) tests and response surface plots were used to set the optimal level for each input factor With compromise optimized values of 29% ball load (PDF) Optimization of inmill ball loading and slurry solids

Ore Grinding SpringerLink
2023年7月20日 There are several impact factors of the grinding operation (1) Structure parameters of grinding mill, including its specifications, model, aspect ratio, ore discharging 2023年4月24日 Grinding is the final stage of comminution, which reduces particle size to micron size level The size reduction is achieved by attrition, abrasion, and impact between the ore itself and between the ore particles and grinding media []According to Swart et al [], ball mills are mostly used because of their very high size reduction ratio, although they have a very low Grinding Media in Ball MillsA Review [v1] Preprints2015年6月1日 Al and C levels, 10% and 125% respectively, in FeAlMn grinding ball were kept constant while Mn content was varied by 15%, 20% and 25% Grinding ball of FeCrC alloy as a comparison was An investigation of the corrosive wear of steel balls 2004年12月1日 The grinding parameters were x 2 , x 3 , x 4, and x 5 are ingredient ratio of the limestone, sandstone, steel At present the main aggregates for fine grinding of gold ores are ball Optimization of continuous ball mills used for finishgrinding
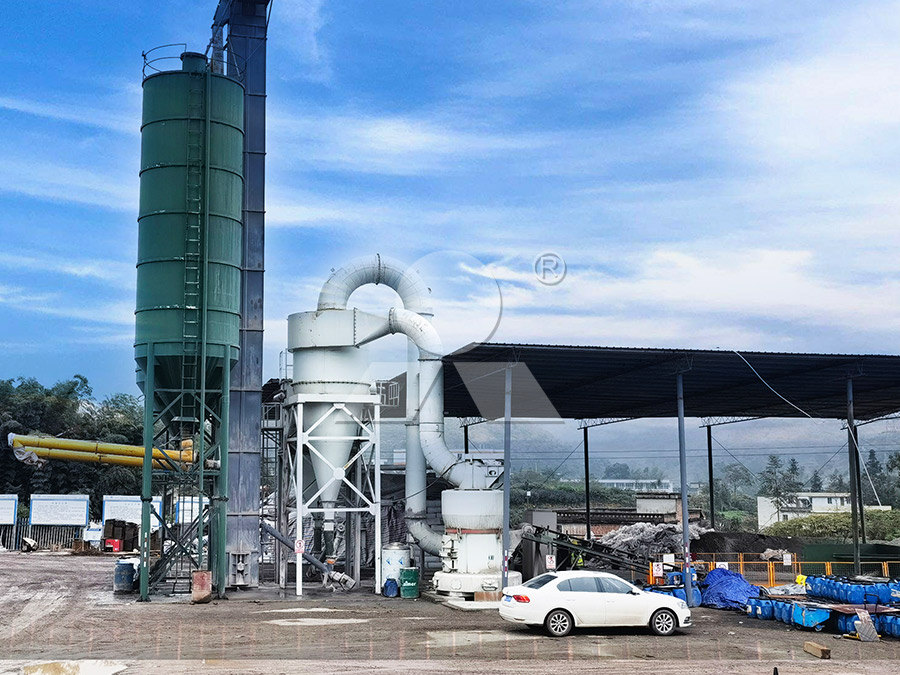
Enhancing the Grinding Efficiency of a Magnetite SecondStage
2024年1月31日 Ceramic ball milling has demonstrated remarkable energysaving efficiency in industrial applications However, there is a pressing need to enhance the grinding efficiency for coarse particles This paper introduces a novel method of combining media primarily using ceramic balls supplemented with an appropriate proportion of steel balls Three grinding media 2013年8月3日 In Grinding, selecting (calculate) the correct or optimum ball size that allows for the best and optimum/ideal or target grind size to be achieved by your ball mill is an important thing for a Mineral Processing Engineer AKA Metallurgist to do Often, the ball used in ball mills is oversize “just in case” Well, this safety factor can cost you much in recovery and/or mill liner Calculate and Select Ball Mill Ball Size for Optimum Grinding2022年2月28日 The particular rate of breakage ratio between dry and wet grinding varies from 1 Calkaya, M: Kinetics of fine wet grinding of zeolite in a steel ball mill in comparison to dry grinding Tangsathitkulchai, C, Austin, LG: The effect of slurry density on breakage parameters of quartz, coal and copper ore in a laboratory Grinding SpringerLink2024年9月1日 Improvement of mechanochemical leaching of zinc oxide ore — Optimization of grinding parameters for basket grinder Author links open overlay panel Yusen Yu a b, Lixue Cui a b, which included a liquid–solid ratio of 10:1, leaching time of 1 h, using 2 mm steel ball as the grinding medium results in the highest zinc Improvement of mechanochemical leaching of zinc oxide ore
.jpg)
Grinding in Ball Mills: Modeling and Process Control Sciendo
Keywords: Ball mills, grinding circuit, process control I Introduction Grinding in ball mills is an important technological process applied to reduce the size of particles which may have different nature and a wide diversity of physical, mechanical and chemical characteristics Typical examples are the various ores, minerals, limestone, etc2024年8月27日 This study explores the effect of steel ball size and proportion on mineral grinding characteristics using Discrete Element Method (DEM) simulations Based on batch grinding kinetics, this paper analyzes the contact behavior during grinding, discussing particle breakage conditions and critical breakage energy The results indicate that while increasing Investigating the Influence of Medium Size and Ratio on Grinding 2023年5月28日 where L b stands for steel ball load, L w for water load, L m for material load, φ mb for materialball ratio, φ mw for grinding concentration, φ bf for medium filling ratio, φ bmw for filling ratio, ρ b for steel ball density, ρ m for material density, ρ w for water density, μ for void content, generally 038, V mill for the effective volume of the mill, V m for the material volume Mill Load Measurement SpringerLinkThe stirred ball mill 222 The Milling Conditions The influences of operating parameters such as stirrer speed (rpm), ball filling ratio (J), powder filling ratio (fc), solid ratio (wt%) and grinding time were investigated In order to calculate the powder filling ratio (fc) and the ball filling ratio (J), Eqs 1 and 2 were used The wet Optimization of Wet Grinding Parameters of Calcite Ore in Stirred Ball

Potential of HighPressure Grinding Roll (HPGR) for Size
throughput, improved size reduction ratio and maximized energy efficiency In this study, emphasis has been given to study this aspect and the objective is to optimize the process parameters during grinding of hard banded hematite quartzite iron ore (BHQ) in HPGR 2 Materials and Methods A banded iron ore (BHQ) sample from Odisha was used in 2023年10月27日 The ball mill is a rotating cylindrical vessel with grinding media inside, which is responsible for breaking the ore particles Grinding media play an important role in the comminution of mineral ores in these mills This work reviews the application of balls in mineral processing as a function of the materials used to manufacture them and the mass loss, as A Review of the Grinding Media in Ball Mills for Mineral 2021年11月1日 Structure of the instrumented grinding media, showing (a) the measurement module, (b) structure of the instrumented ball and (c) rough surface of the spherical shell 1 Measurement module, 2 Power supply module, 3 Cover plate, 4 Sensor packages, 5 Clump weight, 6 Stainless steel shellAssessing load in ball mill using instrumented grinding media2020年10月9日 In order to obtain the optimal operation parameters of a SAG mill, in this paper, the discrete element method (DEM) is used to simulate the breakage process of the particles by controlling three Operation Analysis of a SAG Mill under Different Conditions Based on
.jpg)
Friction and wear of liner and grinding ball in iron ore ball mill
2017年6月15日 Tere has been extensive research on the ball milling of ore At present, the ball milling method focuses on the optimization of the grinding medium, roller rotation rate, steel ball or steel rod 2021年1月22日 Herein, an innovative approach for determining the grinding media system of ball mill based on grinding kinetics and linear superposition principle was proposed The optimal media ball size of −2 + 045 mm, −045 + 015 mm, and − 015 mm feeding samples were 40 mm, 30 mm, and 30 mm, respectivelyAn innovative approach for determining the grinding media 2024年9月26日 Energy savings and consumption reduction of ball mills are crucial for industrial production The grinding medium is an important component of a ball mill In theory, using higherdensity grinding media can yield better grinding results However, for materials with varying grindability, employing grinding media of different densities can reduce energy consumption Optimization and Experimental Study of Iron Ore Grinding ore and corresponds to the scheme, including medium and small stage ball grinding provides a comparative analysis of a wide range of ore processing steps and requires 515% energy in a selfgrinding mill [3] 1 Figure 2 Ball mill process control system using ACS (Adaptable Control System) Figure 2 shows that the input and output signalsControl of ball mill operation depending on ball load and ore
.jpg)
Effect on Fine Particles Output Characteristics of Ceramic Ball Grinding
2023年11月7日 Steel balls as traditional grinding media are prone to excessive fines generation and high energy consumption Therefore, in light of this problem, the authors investigated another media—ceramic balls based on the output characteristics of fine particles This study discusses the effect of ceramic balls on the change of the particle size distribution, zeroorder output 2015年12月1日 Firstly, the conventional ball mill parameters such as mill speed (% of critical speed), material filling ratio (Jb), ball filling ratio (fc), ball size distribution (10203040 mm, %), grinding An experimental study on the ultrafine grinding of gypsum ore the performance of dry ball mill grinding was investigated for a limestonetype brecciated uranium ore The optimum grinding was obtained with the combination of dierent balls (127–375 mm) and interstitial lling of 50% (20% ball lling ratio at xed material lling ratio= 4%) The net power consumption in a ball mill is proportional to theOptimization of Ball Mill Grinding of a Limestone‐Type Brecciated Optimization of Solids Concentration in Iron Ore Ball Milling through Modeling and Simulation Patricia M C Faria 1,2, Raj K Rajamani 3 and Luís M Tavares 2,* 1 Department of Development Engineering, Vale SA, Porto de Tubarão, VitóriaES CEP 29090900, Brazil; imization of Solids Concentration in Iron Ore Ball Milling
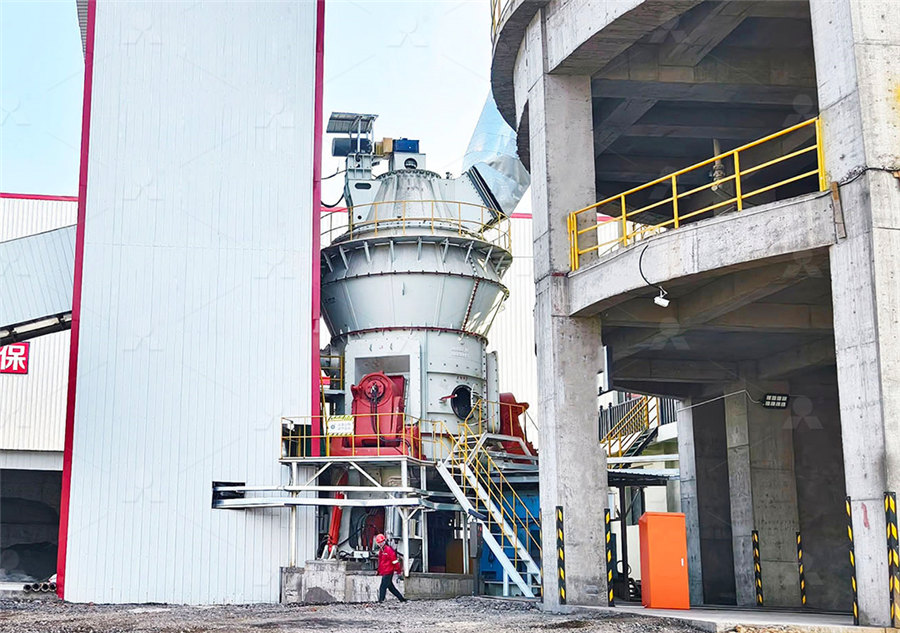
Grinding Media in Ball MillsA Review Academia
minerals Review A Review of the Grinding Media in Ball Mills for Mineral Processing Nyasha Matsanga 1, * , Willie Nheta 1 and Ngonidzashe Chimwani 2 1 2 * Mineral Processing and Technology Research Centre, Department of Metallurgy, University of Johannesburg, Doornfontein Campus, P O Box 17911, Johannesburg 2028, South Africa; 2019年8月30日 How to do Ball Mill Parameter Selection and Calculation from Power, Rotate Speed, Table 14 Ore Grinding Difficulty Coefficient (K’1) Ore hardness: Ore Grinding Difficulty Coefficient After calculating the maximum steel ball diameter, the steel ball ratio in the mill can be calculated with reference to Fig 21 Ball Mill Parameter Selection – Power, Rotate Speed, Steel Ball2014年1月1日 The data analysis showed that the ratio of grinding net powers between ball and vertical mills is approximately 135 for all samples tested View fulltext ArticlePopulation balance model approach to ball mill optimization in iron ore 2023年10月27日 The ball mill is a rotating cylindrical vessel with grinding media inside, which is responsible for breaking the ore particles Grinding media play an important role in the comminution of mineral A Review of the Grinding Media in Ball Mills for Mineral Processing
.jpg)
Effect of different parameters on grinding efficiency and its
2016年11月22日 The commonly used AE feature parameters for grinding AE are statistic parameters such as number of AE pulses, probability density of pulse amplitude, the peak of RMS values, crest factors analysis (ie the ratio of the peak to the RMS level of a signal), kurtosis, skew, autocorrelation, spectral density of AE and ratio of power at interested frequency ranges2022年10月13日 For Tongkeng ore, the optimized grinding conditions are grinding time 54 min, grinding concentration 67% and filling ratio 35% For Gaofeng ore, the optimized grinding conditions are grinding Research on Grinding Law and Grinding Parameters 2017年11月1日 Friction and wear of liner and grinding ball in iron ore ball mill Author links open overlay panel Yuxing Peng a b, Xu Ni a b, the slurry was obtained by mixing the water and the iron ore powder with a ratio of 1:1 Mn16 steel: Grinding ball: GCr15 steel (AISI52100) Particulates: Iron ore particulates (mesh number: Friction and wear of liner and grinding ball in iron ore ball mill2023年4月24日 Grinding is the final stage of comminution, which reduces particle size to micron size level The size reduction is achieved by attrition, abrasion, and impact between the ore itself and between the ore particles and grinding media []According to Swart et al [], ball mills are mostly used because of their very high size reduction ratio, although they have a very low Grinding Media in Ball MillsA Review [v1] Preprints
.jpg)
An investigation of the corrosive wear of steel balls
2015年6月1日 Al and C levels, 10% and 125% respectively, in FeAlMn grinding ball were kept constant while Mn content was varied by 15%, 20% and 25% Grinding ball of FeCrC alloy as a comparison was 2004年12月1日 The grinding parameters were x 2 , x 3 , x 4, and x 5 are ingredient ratio of the limestone, sandstone, steel At present the main aggregates for fine grinding of gold ores are ball Optimization of continuous ball mills used for finishgrinding 2024年1月31日 Ceramic ball milling has demonstrated remarkable energysaving efficiency in industrial applications However, there is a pressing need to enhance the grinding efficiency for coarse particles This paper introduces a novel method of combining media primarily using ceramic balls supplemented with an appropriate proportion of steel balls Three grinding media Enhancing the Grinding Efficiency of a Magnetite SecondStage 2013年8月3日 In Grinding, selecting (calculate) the correct or optimum ball size that allows for the best and optimum/ideal or target grind size to be achieved by your ball mill is an important thing for a Mineral Processing Engineer AKA Metallurgist to do Often, the ball used in ball mills is oversize “just in case” Well, this safety factor can cost you much in recovery and/or mill liner Calculate and Select Ball Mill Ball Size for Optimum Grinding
.jpg)
Grinding SpringerLink
2022年2月28日 The particular rate of breakage ratio between dry and wet grinding varies from 1 Calkaya, M: Kinetics of fine wet grinding of zeolite in a steel ball mill in comparison to dry grinding Tangsathitkulchai, C, Austin, LG: The effect of slurry density on breakage parameters of quartz, coal and copper ore in a laboratory 2024年9月1日 Improvement of mechanochemical leaching of zinc oxide ore — Optimization of grinding parameters for basket grinder Author links open overlay panel Yusen Yu a b, Lixue Cui a b, which included a liquid–solid ratio of 10:1, leaching time of 1 h, using 2 mm steel ball as the grinding medium results in the highest zinc Improvement of mechanochemical leaching of zinc oxide ore Keywords: Ball mills, grinding circuit, process control I Introduction Grinding in ball mills is an important technological process applied to reduce the size of particles which may have different nature and a wide diversity of physical, mechanical and chemical characteristics Typical examples are the various ores, minerals, limestone, etcGrinding in Ball Mills: Modeling and Process Control Sciendo2024年8月27日 This study explores the effect of steel ball size and proportion on mineral grinding characteristics using Discrete Element Method (DEM) simulations Based on batch grinding kinetics, this paper analyzes the contact behavior during grinding, discussing particle breakage conditions and critical breakage energy The results indicate that while increasing Investigating the Influence of Medium Size and Ratio on Grinding
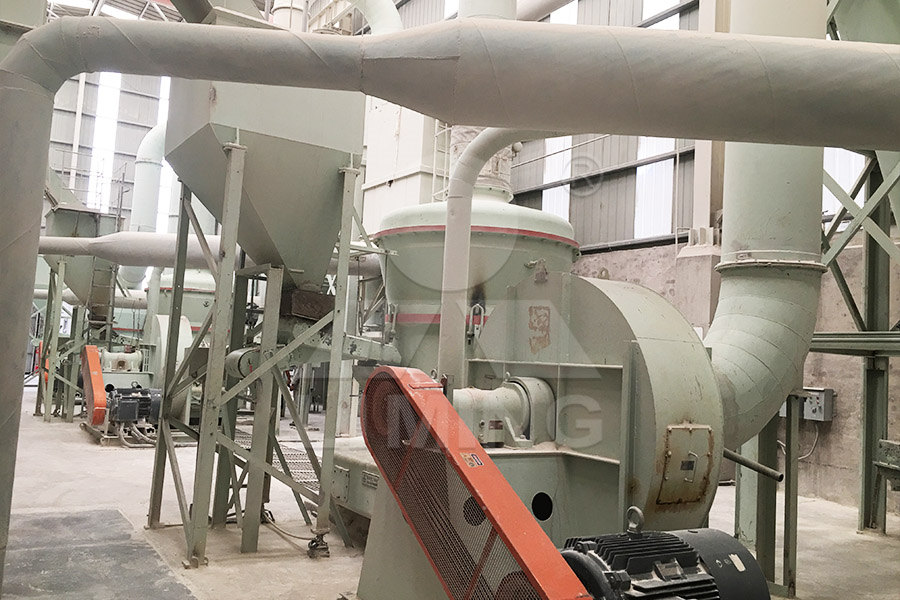
Mill Load Measurement SpringerLink
2023年5月28日 where L b stands for steel ball load, L w for water load, L m for material load, φ mb for materialball ratio, φ mw for grinding concentration, φ bf for medium filling ratio, φ bmw for filling ratio, ρ b for steel ball density, ρ m for material density, ρ w for water density, μ for void content, generally 038, V mill for the effective volume of the mill, V m for the material volume