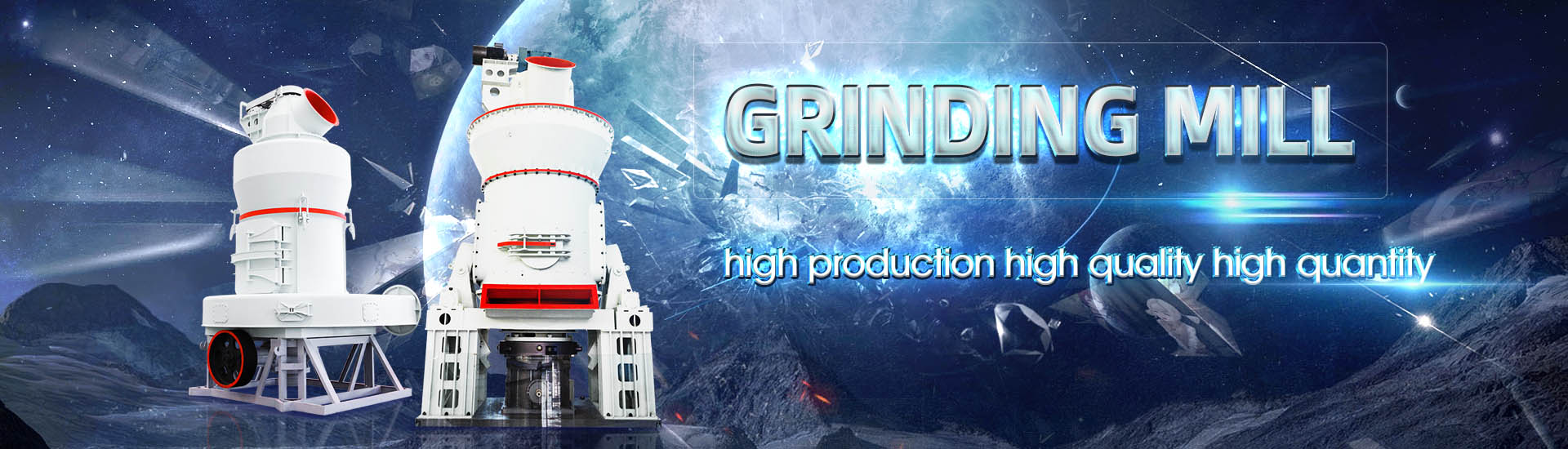
Anthracite pulverizing process
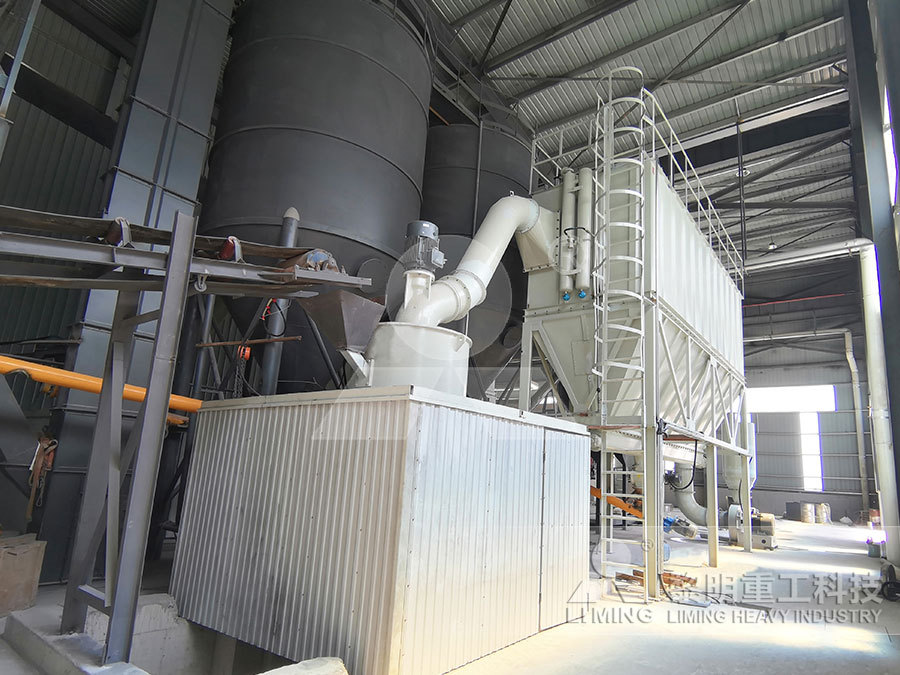
Advanced Development of Pulverized Coal Firing Technologies
lignite coals, subbituminous coals, semianthracite, oil coke, and other resources that heretofore have not been used as fuels to generate power In response to the diversification of fuels used 2017年6月1日 To investigate the process mechanism of airflow pulverization, the pulverization effects of Taixi anthracite, Shenfu coal and semicoke in the fluidized bed airflow crushing Air impact pulverization–precise classification process to support In a storage system (Fig 41), coal is pulverized and conveyed by air or gas to a suitable collector where the carrying medium is separated from the coal, which is then transferred to a storage Coal Preparation Systems for Boilers SpringerIt addresses the processes and their underlying mechanisms involved in pulverised coal combustion namely: drying and heating, devolatilisation, volatile oxidation and char oxidation Fundamentals of pulverised coal combustion ICSC
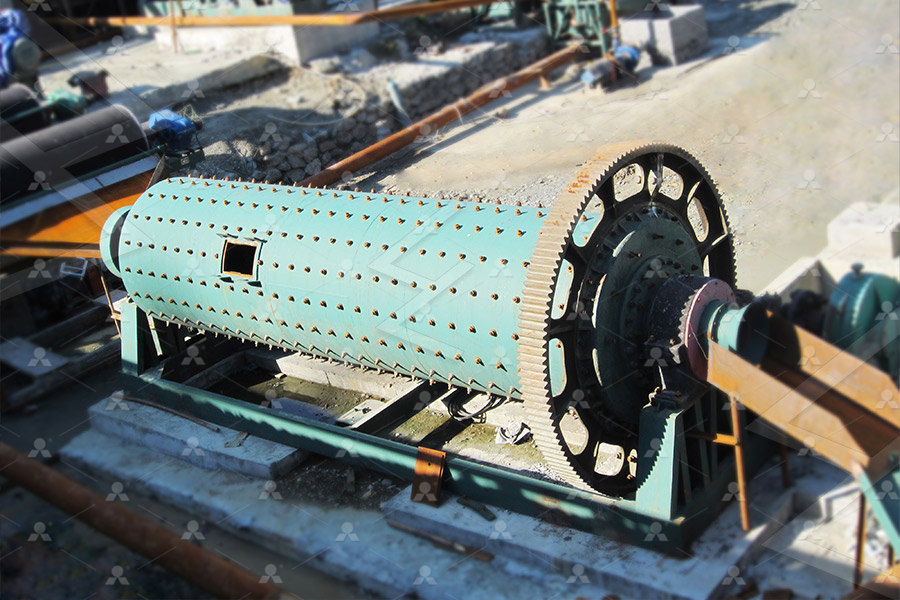
Pulverized Coal Injection of Blast Furnace Ironmaking
2024年1月1日 Its main task is to process raw coal into pulverized coal that meets the injection requirements The main particle size requirements are the volume of anthracite of less than Pulverized Coal Injection for Blast Furnaces (PCI) 1 Background and process overview The injection of pulverized coal into blast furnaces in Japan began at Nippon Steel Corp’s Oita No 3A2 Pulverized Coal Injection for Blast Furnaces (PCI)ignificantly improve the quality of lowreactive anthracite combustion As a result he optimum share of solid biomass of approximately 10% has been determined This share allows the Cocombustion of solid anthracitecoal firing boilers biomassIn the present investigation, pulverized coals with high volatile contents are used as deoxidizer in aluminum silicon smelting process using “Submerged Arc Furnace” (SAF) method SAF Coal Pulverization System: Explosion Prevention and Process Control
.jpg)
Gasification of Anthracite in a PilotScale CFB Gasifier and Pore
With the progress of activation, the pore structure of GFA presents a threestage evolution process: development, dynamic balance, and collapse Such a process can be divided and fuels, the kinetic characteristics of the pine sawdust for combustion process calculation, defined [8, 9] The purposes of the studies were the following: – to identify the optimum biomass/anthracite ratio for the most complete burnout of both fuels at residence time in the anthracite PC boiler furnace;Cocombustion of solid anthracitecoal firing boilers biomass2023年1月1日 Dry process, in which the raw materials are fed in ratios necessary to achieve the desired chemical composition to either a rotating ball mill or vertical spindle (roller) mill The raw materials are dried with waste process gases taken from the kiln system The target grind is the bulk of the product is less than 75 μmCoal utilization in the cement and concrete industriesa filter for recycling hack to feed bin 51 anthracite that is not passed by a 1A filter, so that the screening and pulverizing operation is repeated, ATTORNEYS United States Patent O M 3,460,925 ANTHRACITE T ACETYLENE CONVERSION PROCESS Maurice M Mitchell, Jr, Wallingford, Pa, assignor to Melpar, Ine, Falls Church, Va, Anthracite to acetylene conversion process Google Patents
.jpg)
Coal Preparation Systems for Boilers Springer
the furnace pressure drop Fuels like high ash anthracite are crushed to 3mm top size, while low ash bituminous can be crushed to 6mm top size (Singer, 1991) 42 Pulverizing Properties of Coal Coal properties have a great impact on the performance of the coal pulverizing system and the whole boiler2019年10月31日 This process is used for pulverization into medium and smallsized objects (10 cm or less) <Shear pulverization> An object is cut into small pieces by a wedge, such as a cutter It is suitable for pulverizing fragile objects <Friction grinding (pulverization by friction)>Pulverization 1: Definition and purpose THINKY MIXERThe dehydroxylation process is subjected to loamy materials within this temperature range In the final step, for temperatures above 600°C, there is a thermal swell of coal grains leading to absolute devolatilization and hence resulting in coke formation due to autoignition The total duration of this process is about 001–02 sPulverised Coal Combustion an overview ScienceDirect Topics2016年7月20日 The modern anthracite breaker or washery uses almost exclusively a wet method of preparation, which requires, roughly, 1 gal of water per minute per ton of production per dayThe entire anthracite industry uses about 320,000 gal per min of water for this purpose or 800,000 tons of water per day As this water leaves the breakers, it contains fine Anthracite Preparation 911Metallurgist
.jpg)
Impacts of Blending Semicoke in PCI Coal on Grinding Efficiency
2023年5月25日 Under the same pulverizing process and equipment conditions, the grinding efficiency is mainly influenced by the fuel properties and usually measured using the Hardgrove grindability index (HGI) 9The history of pulverization date back as early as 1824 and was envisaged by Carnot in a coal fired engine In 1890 Diesel made use of pulverized coal in his diesel engine The pulverized coal firing was first developed in cement industry which then migrated to power and process industries Pulverizing coal in boiler is an important factor the overall cycle efficiency There are many Coil Pulverizers for Boilers Bright Hub EngineeringTypically, anthracite has moisture contents between 2 and 45% Bituminous and subbituminous coals have typical values of 1–122% and 141–31%, respectively However, lignite and brown coal have values of 25–35% or The process of drying includes the evaporation of surface moisture and, subsequently, the loss of inherent moistureFundamentals of pulverised coal combustion ICSC2022年2月24日 Fineness: 200325 mesh, according to the process requirements Suitable for coal: bituminous coal, anthracite, etc Coalbased activated carbon has the characteristics of reasonable pore structure, good How is pulverized coal processed? SBM Ultrafine

Pulverised Coal an overview ScienceDirect Topics
Steps in the process are (1) mining of the coal from nearsurface or deep mines, (2) transporting crushed coal several centimeters in size to the power station, (3) pulverizing the coal to a powder predominantly less than 100 μ m in size, (4) pneumatically transporting this coal dust with combustion air into a large combustion chamber with steel walls cooled by water flowing in Vertical mill is widely used for pulverized coal preparation system in power plant, cement plant, metallurgy industry, chemical plant, etc It could be used to grind bituminite, meagre coal, and anthracite lignite with high moisture under Vertical mill for coal pulverizing in power plantThe Age of Steel: The Bessemer process, patented by Sir Henry Bessemer in 1856, marked a major breakthrough in steel production It involved blowing air through molten iron to remove impurities, resulting in the mass production of steel Electric Arc Furnaces: The 20th century saw the rise of electric arc furnaces, which useGuide to Modern Smelting Processes CED Engineering2024年4月12日 Some of this process' most significant benefits include the following Enhanced particle size: Wet pulverizing can achieve smaller particles than dry pulverization methods The final product is also often more uniform than dry pulverization products, which is essential for pharmaceuticals, cosmetics and other industries; Reduced fire hazards: The liquid within the Dry vs Wet Pulverization Key Differences Applications
.jpg)
Converting Slovianska TPP with the central coal pulverizing plant
2023年6月30日 Purpose To develop scientific foundations and technical solutions and to implement the converting of the anthracite boiler of the 800 MW unit of Slovianska TPP with central coal pulverizing plant to subbituminous coal combustion with maximum use of existing equipment, without stopping the unit’s operation Methodology Theoretical and calculational was examined by conducting parametric pulverizing tests using a test mill owned by IHI The pulverizing capacity at increased table speeds was evaluated using three types of coals with different Hardgrove Grindability Index (HGI) values Figure 6 shows the test results for two types of coal It was observed that capacity increased by 10% whenAdvanced Development of Pulverized Coal Firing TechnologiesSlim Box Anthracite Line Edition quantity Add to cart SKU: 42 Category Our grinder is made entirely of polished stainless steel and is perfect for pulverizing coarse soft material How it it’s a complex and timeconsuming process – taking years to master Before the product reaches your door, it goes through rigorous Snuffbox Slim Box Anthracite Line Edition oneGee2023年6月30日 Findings The technological features of coal pulverizing plant with steam panel dryers designed for anthracite and the peculiarities of the drying process of an individual coal particle were analyzedConverting Slovianska TPP with the central coal pulverizing plant
.jpg)
Process effluents and mine tailings: sources, effects and management
2016年12月19日 Increasing population levels, growing economies, rapid urbanization and changes in consumption patterns have increased the demand for raw materials such as base and precious metals, leading to growing concerns regarding their availability and the global efficiency of the mine supply chain Mine tailings, consisting of process effluents that are generated in a 2024年1月11日 The process of pulverizing coal involves several steps Each of these is essential to effectively and safely produce a fine powder that burns easily FTM Machinery, in this post, explains how to process coal into How to Process Coal into Pulverized Coal in 5 Steps?supply system and in the boiler unit burners Trial tests at the coal pulverizing plant and boiler unit Findings The technological features of coal pulverizing plant with steam panel dryers designed for anthracite and the pecu liarities of the drying process of an individual coal particle were analyzedSOLID STATE PHYSICS, MINERAL PROCESSING2013年9月15日 Fig 1 shows the working principles of the efficient power generation process developed here This process is mainly based on a boiler with an open pulverizing system and the recovery of water from millexhaust, in which boiler only the high temperature flue gas is used as the drying agent for the pulverizing systemAn environment friendly and efficient lignitefired power
.jpg)
Fire and Explosion Prevention in Coal Pulverizing Systems
dust This ignition and combustion process continues as a propagating flame front through the aircoal mix ture The combustion products formed are high temperature gases which expand seeking equilibrium; and as they do (Time = 1), they push the flame front away from the point of ignition As the flame front moves, itManufacturing Process The first step in the manufacture of Electrode Carbon Paste is screening the Calcined Petroleum Coke (CPC) and / or (ECA) to different fractions and pulverizing and storing it separately Following this, predetermined quantities of different fractions are weighed and transferred to a Sigma Mixer which is heated to about 150ºC by thermic fluidIndia Carbon Limited2020年7月27日 Catalytic coal gasification technology shows prominent advantages in enhancing coal gasification reactivity and is restrained by the cost of catalyst Two typical biomass ash additions, corn stalk ash (CSA, high K–Na and low Si) and poplar sawdust ash (PSA, high K–Ca and high Si), were employed to study the influence of biomass ash on pyrolysis process and Influence of different biomass ash additive on anthracite pyrolysis 2020年9月22日 The fifth paper compared influence of different biomass ash additive on anthracite pyrolysis process and char gasification reactivity It is concluded that abundant active AAEM (especially K and Na) contents of biomass ash and a lower graphitization degree of mixed chars could be responsible for the fact that the addition of corn Special issue on coal gasification: science and technology
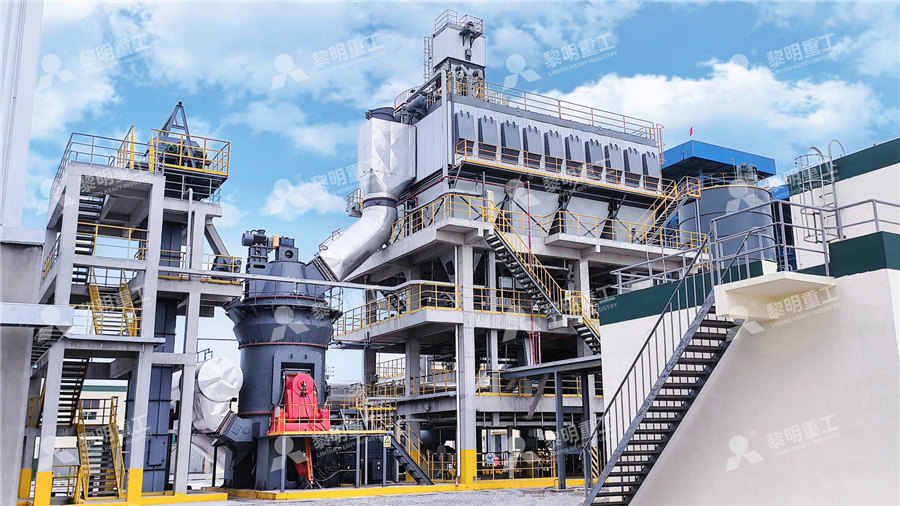
Grand Box Anthracite Slot Edition oneGee
Grand Box Anthracite Slot Edition + quantity Add to cart SKU: 43 Our grinder is made entirely of polished stainless steel and is perfect for pulverizing coarse soft material Don’t miss it How it’s a complex and timeconsuming process – taking years to master Before the product reaches your door, it goes through 2018年8月1日 Purpose To develop scientific foundations and technical solutions and to implement the converting of the anthracite boiler of the 800 MW unit of Slovianska TPP with central coal pulverizing plant Coal Slurry Drying Process ResearchUnder the same pulverizing process and equipment conditions, the grinding efficiency is mainly influenced by the fuel properties and usually measured using the Hardgrove grindability index (HGI)9–11) The HGI indicates how hard it will be to crush the material, which determines the energy consumption and grinding cost of material crushing12) AtImpacts of Blending Semicoke in PCI Coal on Grinding Efficiency fuels, the kinetic characteristics of the pine sawdust for combustion process calculation, defined [8, 9] The purposes of the studies were the following: – to identify the optimum biomass/anthracite ratio for the most complete burnout of both fuels at residence time in the anthracite PC boiler furnace;Cocombustion of solid anthracitecoal firing boilers biomass
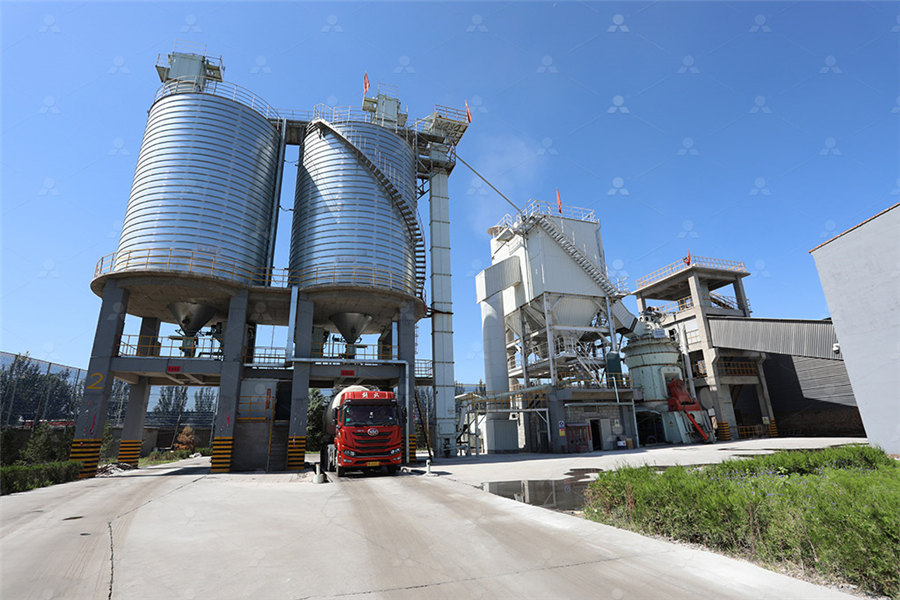
Coal utilization in the cement and concrete industries
2023年1月1日 Dry process, in which the raw materials are fed in ratios necessary to achieve the desired chemical composition to either a rotating ball mill or vertical spindle (roller) mill The raw materials are dried with waste process gases taken from the kiln system The target grind is the bulk of the product is less than 75 μma filter for recycling hack to feed bin 51 anthracite that is not passed by a 1A filter, so that the screening and pulverizing operation is repeated, ATTORNEYS United States Patent O M 3,460,925 ANTHRACITE T ACETYLENE CONVERSION PROCESS Maurice M Mitchell, Jr, Wallingford, Pa, assignor to Melpar, Ine, Falls Church, Va, Anthracite to acetylene conversion process Google Patentsthe furnace pressure drop Fuels like high ash anthracite are crushed to 3mm top size, while low ash bituminous can be crushed to 6mm top size (Singer, 1991) 42 Pulverizing Properties of Coal Coal properties have a great impact on the performance of the coal pulverizing system and the whole boilerCoal Preparation Systems for Boilers Springer2019年10月31日 This process is used for pulverization into medium and smallsized objects (10 cm or less) <Shear pulverization> An object is cut into small pieces by a wedge, such as a cutter It is suitable for pulverizing fragile objects <Friction grinding (pulverization by friction)>Pulverization 1: Definition and purpose THINKY MIXER
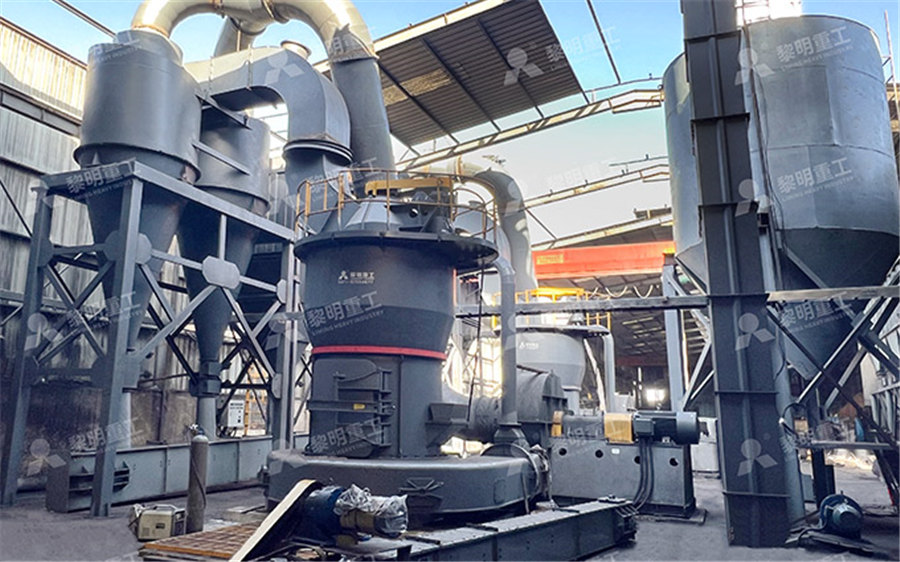
Pulverised Coal Combustion an overview ScienceDirect Topics
The dehydroxylation process is subjected to loamy materials within this temperature range In the final step, for temperatures above 600°C, there is a thermal swell of coal grains leading to absolute devolatilization and hence resulting in coke formation due to autoignition The total duration of this process is about 001–02 s2016年7月20日 The modern anthracite breaker or washery uses almost exclusively a wet method of preparation, which requires, roughly, 1 gal of water per minute per ton of production per dayThe entire anthracite industry uses about 320,000 gal per min of water for this purpose or 800,000 tons of water per day As this water leaves the breakers, it contains fine Anthracite Preparation 911Metallurgist2023年5月25日 Under the same pulverizing process and equipment conditions, the grinding efficiency is mainly influenced by the fuel properties and usually measured using the Hardgrove grindability index (HGI) 9Impacts of Blending Semicoke in PCI Coal on Grinding Efficiency The history of pulverization date back as early as 1824 and was envisaged by Carnot in a coal fired engine In 1890 Diesel made use of pulverized coal in his diesel engine The pulverized coal firing was first developed in cement industry which then migrated to power and process industries Pulverizing coal in boiler is an important factor the overall cycle efficiency There are many Coil Pulverizers for Boilers Bright Hub Engineering
.jpg)
Fundamentals of pulverised coal combustion ICSC
Typically, anthracite has moisture contents between 2 and 45% Bituminous and subbituminous coals have typical values of 1–122% and 141–31%, respectively However, lignite and brown coal have values of 25–35% or The process of drying includes the evaporation of surface moisture and, subsequently, the loss of inherent moisture