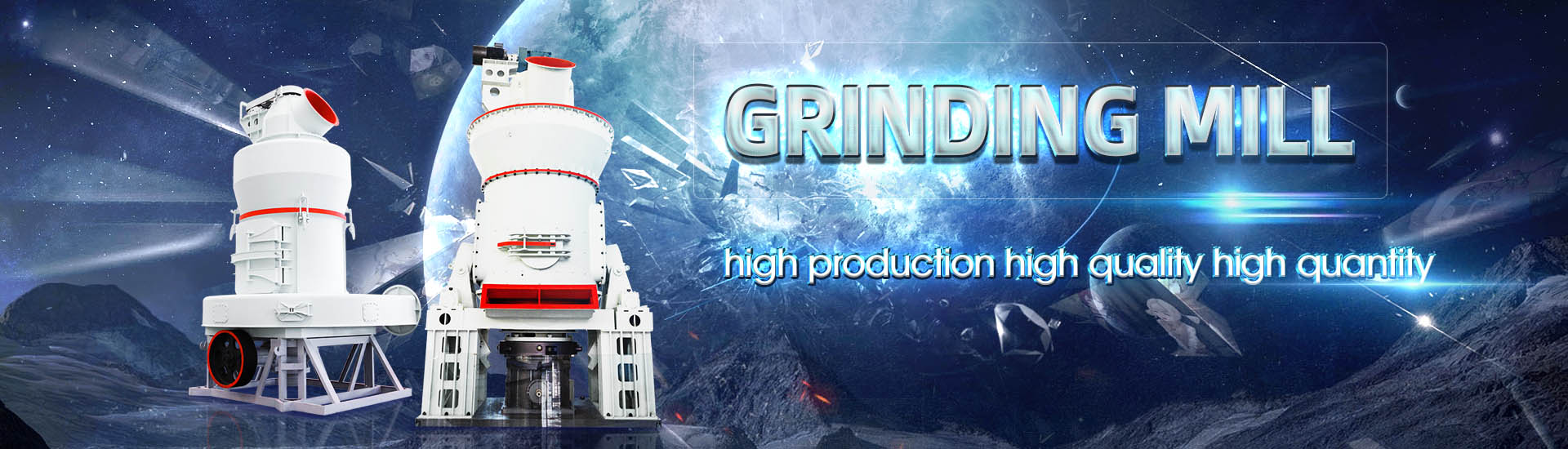
Oil soft stone oil coke processing and utilization technology
.jpg)
12 The development of cokemaking technology based on the
2019年1月1日 This chapter explains the technological principles behind semisoft coking coal utilization from the viewpoint of the mechanism of carbonization and reviews the development 2019年1月1日 Depending on the temperature, the process of carbonization can be classified into two types: lowtemperature carbonization (LTC) and hightemperature carbonization (HTC) Industrial perspective of the cokemaking technologies2024年1月2日 The various attempts to determine the end of the carbonization cycle and its importance in improving coke quality have been explained in detail Furthermore, Technological Advancements in Cokemaking: Mineral Processing 2021年7月22日 There are three proven processes for the manufacture of metallurgical coke: the byproduct process, the heatrecovery process and the beehive process The heatrecovery Comparison of Byproduct and HeatRecovery Cokemaking
.jpg)
Leading Edge of Coal Utilization Technologies for Gasification and
The expansion of raw coal brands for producing metallurgical coke is very important In Japan, improvement of coke quality is strongly demanded to smoothly operate large inner volume The Lurgi process uses the pressurized fixed bed gasifier The Winkler process uses the fluidized bed type gasifier developed in German, and the KoppersTotzek process uses the entrained Leading Edge of Coal Utilization Technologies for Gasification and In this study, we studied the feasibility of preparing highquality needle coke from coal liquefaction pitch Nine types of blending pitch (coal liquefaction pitch and anthracene oil mixed with Generation and characterization of coalbased needle coke 2015年8月19日 A novel process integrated with oil shale retorting, oil shale/semicoke combustion, shale oil and retorting gas upgrading and ash comprehensive utilization Research progress on utilization and systemic integration
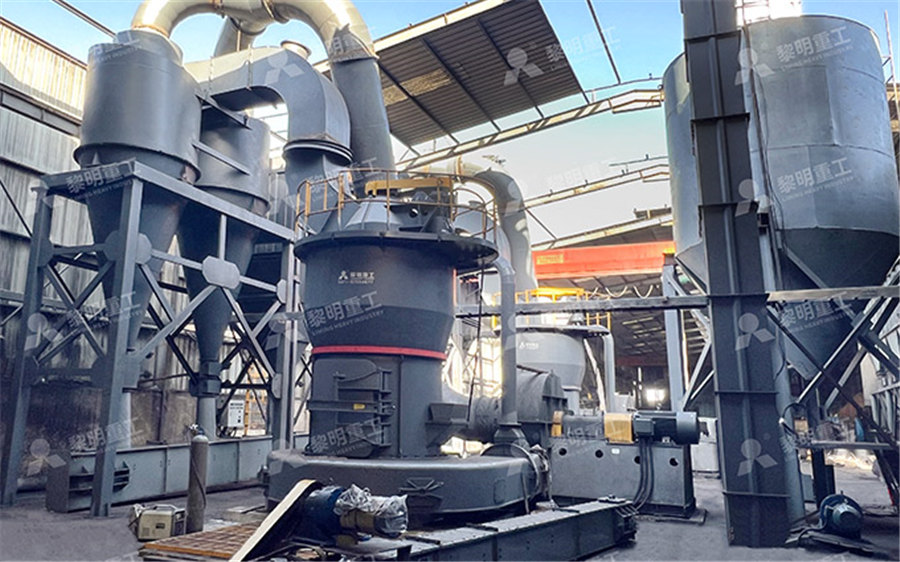
A review on copyrolysis of coal and oil shale to produce coke
2019年11月29日 This review focuses on the potential utilization of oil shale (OS) as a feedstock for coalblending coking, in which the initial and basic step is pyrolysis However, OS has a 2019年7月19日 The goals of coking process control are realizing steady heating of coke oven, enhancing production of coke oven and quality of coke, reducing energy consumption and Coke Making: Most Efficient Technologies for Greenhouse 2020年6月6日 It is found from Table 73 that when VR is processed by solvent deasphalting, delayed coking and the combination of the two processes, the yield of 360 °C + product of the combined process is increased by about 25% and the yield of coke is reduced by about 30% Compared with the delayed coking process, slurry bed hydrocracking process can produce Effective Processing Technology of Heavy Oil SpringerLink2024年9月1日 Crude oil holds an important position in the field of energy However, larges amount of oil sludge would generate during the process of crude oil production, transportation, storage and refining (Gan et al, 2022, Niu et al, 2022)According to statistics, 60×10 5 t of oil sludge would generated in the world each year, and this quantity is still rising (Santiago et al, Research progress on formation mechanism and reutilization
.jpg)
Research progress on utilization and systemic integration
2015年8月19日 A novel process integrated with oil shale retorting, oil shale/semicoke combustion, shale oil and retorting gas upgrading and ash comprehensive utilization technologies, can increase energy efficiency and improve economic performance This integrated process meets the needs of Chinese energy development strategy2018年12月13日 The fluid catalytic cracking (FCC) technology is one of the pillars of the modern petroleum industry which converts the crude oil fractions into many commodity fuels and platform chemicals, such Fluid catalytic cracking technology: current status and recent 2014年6月1日 1, 2 Shale oil in China is mainly distributed in the Ordos Basin, Songliao Basin, Bohai Bay Basin, and Junggar Basin 3 The recoverable reserves of shale oil in Jimusaer of the Juggar Basin are Review of oil shale semicoke and its combustion utilization2019年11月29日 In this study, two shale samples with different maturities, from Geniai, Lithuania (Ro = 07%), and Wenjiaba, China (Ro = 27%), were selected for opensystem pyrolysis experiments at 400 °C and A review on copyrolysis of coal and oil shale to produce coke

Upgrading of Canadian Oil Sand Bitumen via Cracking and Coke
Table 2 The FCC catalyst was mainly composed of matrix, binder, and Yzeolite (ultrastable Yzeolite) The BFC catalyst with moderate cracking activity and catalytic effects of coke 2017年8月11日 The integrated residue cracking and coke gasification–combustion (RCGC) process was proposed to make hierarchical and valueadded utilization of Venezuela vacuum residueDeep Conversion of Venezuela Heavy Oil via Integrated Cracking and Coke 2012年12月31日 The oil shale retorting, the refinery oil, the semicoke combustion power generation and the ash residue utilization organic union in the together theory realizes the comprehensive utilization of Comprehensive Utilization of Oil Shale and Prospect Analysis2007年1月1日 Semicoke is a solid waste material left after oil shale retorting in oil shale chemical industry During more than 80 years of operation more than 110 million tonnes of semicoke have been Mineral composition of Estonian oil shale semicoke sediments
.jpg)
Oil Sludge Treatment Processes Chemistry and Technology of
2015年11月12日 This review considers effective modern methods for oil sludge and acid resid treatment We analyze in detail the technologies for dewatering, solidification, solvent extraction, thermal treatment (including in the presence of catalysts), and modern oil sludge and solid fuel (oil shales, coals) treatment methods We note that the dominant criteria for the effectiveness of 2022年12月1日 Ye et al (2017) prepared an oilinwater nanoemulsion (NAR), which achieved a 957% oil removal efficiency after cleaning at 40 °C for 30 min Jiang et al (2021) used sodium dodecyl benzene sulfonate, nbutanol, water, and white oil to prepare a singlephase microemulsion to form a thermodynamically stable dispersion system, and the oil removal Regional distribution, properties, treatment technologies, and 2024年8月18日 A plasmachemical method is proposed for processing fuel oil, at a rate of 1000 kg/h Mild plasmachemical treatment results in considerable cracking of the highboiling fueloil component In plasmachemical processing of fuel oil and subsequent distillation of the liquid components, the products are 67% gas, 480% residue, 112% solvent (from the onset of PlasmaChemical Processing of Fuel Oil Coke and Chemistry2020年1月3日 The above books and reviews also cover a number of other important topics associated with oil shale processing, such as availability of oil shale reserves [60, 69, 107], oil shale mining [69, 72], research and development needs [60, 69], socioeconomical problems , environmental impact [60, 69, 107], oil shale upgrading economics and shale oil cost Oil Shale Processing, Chemistry, and Technology
.jpg)
Technical and economic analysis of an oil shale comprehensive
2018年12月1日 To relieve the shortage of oil, exploration of oil shale attracts increasingly attention from different countries, especially in China Facing with the disadvantages of conventional oil shale retorting technology, more and more attention has been paid to the comprehensive utilization of oil shale for utilizing oil shale efficiently and in an environment 2023年10月23日 Abstract This paper provided an overview of various coke oven gas (COG) heat utilization technologies in the coke oven ascension pipe The prevailing technology currently used is the distributed sensible heat recovery method, specifically waterjacketed and coiltype waste heat utilization technologies However, it still faces challenges such as coking and low The Research on Waste Heat Utilization Technology of Coke2022年7月11日 Carbon capture storage and utilization is not a new technology, but its application to reduce CO2 emissions from the refinery sector is just now emerging as promising mitigation This study will look closely at opportunities to match CO2 sources with potential sinks by matching carboncapturing projects at Indian oil refineries with Enhanced Oil Recovery Potential matching of carbon capture storage and utilization 2013年4月1日 Catalytic hydroprocessing of white pine pyrolysis biooil over cobaltmolybdenum (CoMo) carbide supported on biochar was carried out in a continuous fixedbed reactor at a temperature between 350 Hydroprocessing BioOil and Products Separation for Coke Production
.jpg)
Apricot kernel characterization, oil extraction, and its utilization: a
2023年1月7日 Apricot kernel is the innermost part of the apricot fruit Most of the time, apricot fruit seeds are discarded as waste or byproduct in the food processing units (Gezer et al, 2011), but it has good potential source of oil, protein, vitamins, fibre, essential minerals, and many bioactive components (Akhone et al, 2022)Stone/pit are obtained after the separation of fruit 2022年12月1日 Carbon capture and storage (CCS) technology refers to the process of separating CO 2 from relevant emission sources, then transporting it to the storage site and isolating CO 2 from the atmosphere for a long time This technology can reduce CO 2 emissions from the source, and can remove the existing CO 2 in the atmosphere on a large scale, which Research progress on CO2 capture and utilization technology2000年1月1日 With 05–10% of the world's oil shale reserves, Estonia mines more than 48% of the total world oil shale output Electricity, thermal energy and shale oil are produced from oil shale in EstoniaOil shale processing in Estonia and Russia ResearchGate2019年1月1日 This chapter explains the technological principles behind semisoft coking coal utilization from the viewpoint of the mechanism of carbonization and reviews the development and commercialization of technologies, such as briquette blending carbonization process, coal moisture control, drycleaned and agglomerated precompaction system, formed coke process, The development of cokemaking technology based on the utilization
}@~3SRDG`IA1KP_ICWAA.jpg)
Obtaining needle coke from coal liquefaction residue
2012年11月18日 Solvent separation can be used to separate coal liquefaction products into several pitch fractions, which can be used to produce needle coke, carbon fibers, binder in electrode fabrication and impregnating pitch [1–5]Needle coke, having a low coefficient of thermal expansion (CTE) and an isotropic structure, is widely used in making electrodes for smelting ore2020年8月1日 The main technical and technological problems in the LNB FCCU before the revamp were: High catalyst losses; Increased APS of equilibrium catalyst (from 90 to 108 µm)FCC Unit Performance dependence on H‐Oil Severity2018年3月2日 Coke making process is strictly connected with formation of coke oven wastewater, highly loaded and contaminated stream, proper treatment and utilization of which requires sophisticated methods COKE OVEN WASTEWATER FORMATION, TREATMENT AND UTILIZATION 2014年6月15日 Oil shale, one of the most important potential crude oil substitute resources, is widespread in the world According to data reported by Qian et al [1], shale oil (calculated based on the in situ oil shale) accounts for about 400 billion tons of oil, worldwide, which is higher than the total for traditional crude oil (which is more than 300 billion tons)Review of oil shale semicoke and its combustion utilization
.jpg)
Membrane technology for vegetable oil processing—Current status
2021年8月24日 Vegetable oil processing has been identified as one of the potential nonaqueous applications of membrane technology Membranebased processing has been largely attempted on individual steps of the conventional refining process with reasonable success2015年8月7日 The pyrolysis process of blends of petroleum coke and coal accords with mechanism model (1−α)15 well, and the combustion process accords with mechanism model w15 wellGrinding Characteristics of Coal and Petroleum Coke/Coal 2018年7月1日 After oilfield development enters middle and late period, the increasingly highwater content in the oil produced would cause a large accumulation of oil sludge in the transportation system To solve this problem, three kinds of sludge profile control agent to be used through slug composition in the profile control plugging for heavy oil steam huffpuff wells have Research and application of oil sludge resource utilization technology 2020年6月6日 It is found from Table 73 that when VR is processed by solvent deasphalting, delayed coking and the combination of the two processes, the yield of 360 °C + product of the combined process is increased by about 25% and the yield of coke is reduced by about 30% Compared with the delayed coking process, slurry bed hydrocracking process can produce Effective Processing Technology of Heavy Oil SpringerLink
.jpg)
Research progress on formation mechanism and reutilization
2024年9月1日 Crude oil holds an important position in the field of energy However, larges amount of oil sludge would generate during the process of crude oil production, transportation, storage and refining (Gan et al, 2022, Niu et al, 2022)According to statistics, 60×10 5 t of oil sludge would generated in the world each year, and this quantity is still rising (Santiago et al, 2015年8月19日 A novel process integrated with oil shale retorting, oil shale/semicoke combustion, shale oil and retorting gas upgrading and ash comprehensive utilization technologies, can increase energy efficiency and improve economic performance This integrated process meets the needs of Chinese energy development strategyResearch progress on utilization and systemic integration 2018年12月13日 The fluid catalytic cracking (FCC) technology is one of the pillars of the modern petroleum industry which converts the crude oil fractions into many commodity fuels and platform chemicals, such Fluid catalytic cracking technology: current status and recent 2014年6月1日 1, 2 Shale oil in China is mainly distributed in the Ordos Basin, Songliao Basin, Bohai Bay Basin, and Junggar Basin 3 The recoverable reserves of shale oil in Jimusaer of the Juggar Basin are Review of oil shale semicoke and its combustion utilization
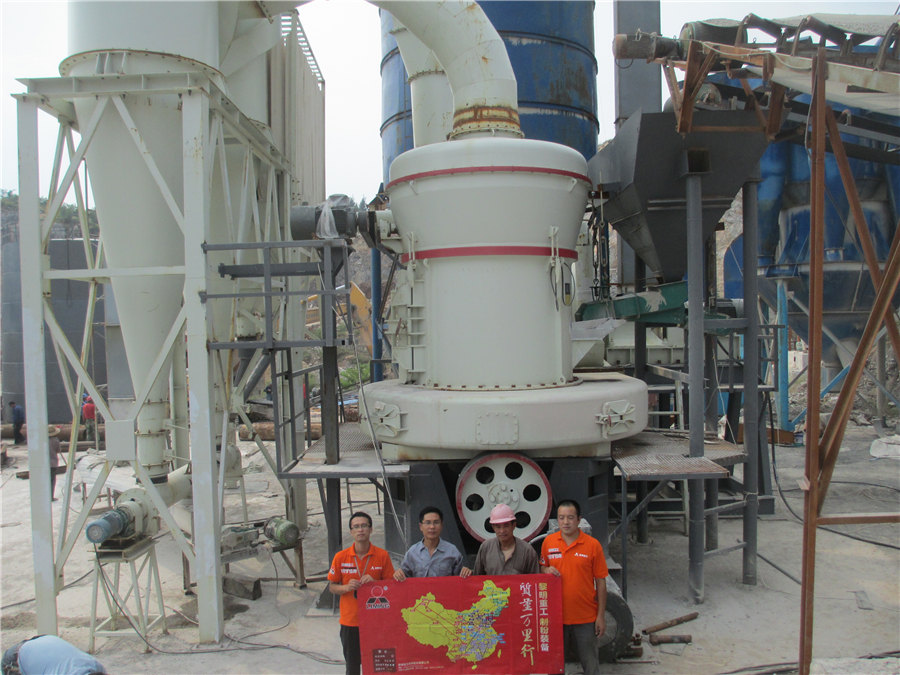
A review on copyrolysis of coal and oil shale to produce coke
2019年11月29日 In this study, two shale samples with different maturities, from Geniai, Lithuania (Ro = 07%), and Wenjiaba, China (Ro = 27%), were selected for opensystem pyrolysis experiments at 400 °C and Table 2 The FCC catalyst was mainly composed of matrix, binder, and Yzeolite (ultrastable Yzeolite) The BFC catalyst with moderate cracking activity and catalytic effects of coke Upgrading of Canadian Oil Sand Bitumen via Cracking and Coke 2017年8月11日 The integrated residue cracking and coke gasification–combustion (RCGC) process was proposed to make hierarchical and valueadded utilization of Venezuela vacuum residueDeep Conversion of Venezuela Heavy Oil via Integrated Cracking and Coke 2012年12月31日 The oil shale retorting, the refinery oil, the semicoke combustion power generation and the ash residue utilization organic union in the together theory realizes the comprehensive utilization of Comprehensive Utilization of Oil Shale and Prospect Analysis
.jpg)
Mineral composition of Estonian oil shale semicoke sediments
2007年1月1日 Semicoke is a solid waste material left after oil shale retorting in oil shale chemical industry During more than 80 years of operation more than 110 million tonnes of semicoke have been