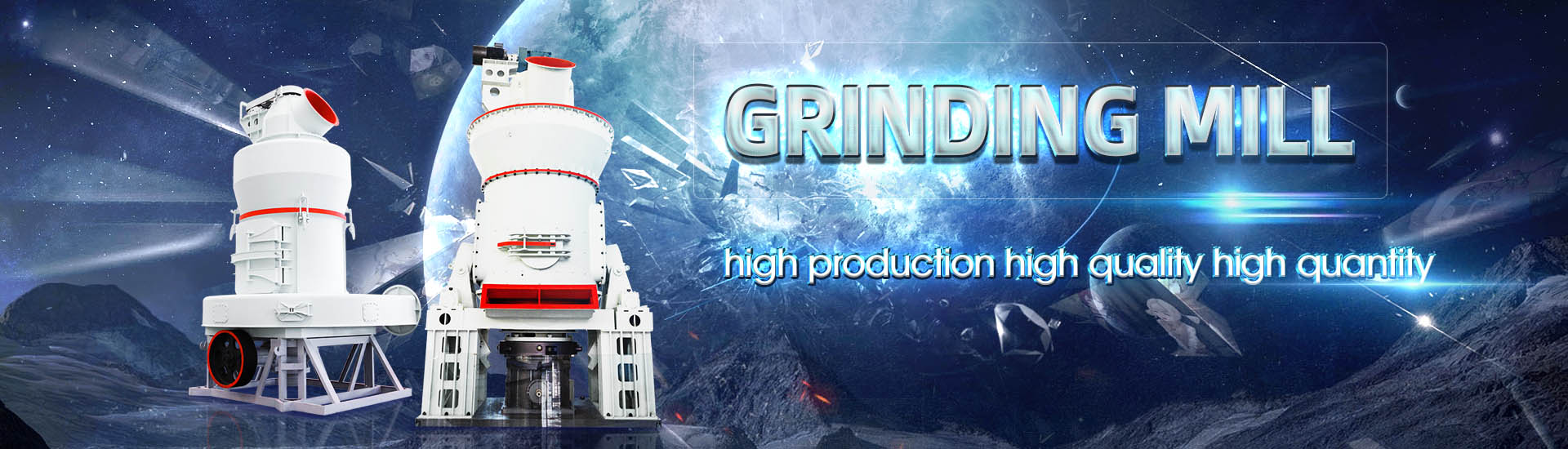
B1322 alumina ore mill

THE ALUMINIUM STORY BAUXITE TO ALUMINA: THE BAYER
Bauxite is the most widely distributed ore used for alumina production It is named after the small town in southern France called Les Baux, where it was first mined Bauxite is typically a 2022年9月15日 This paper describes the life cycle assessment for two alumina production processes, the current commercialized Bayer process and the alternative Pedersen process, Circular economy and life cycle assessment of alumina production About 90% of alumina refineries in the world use the Bayer process for refining Bauxite ore It is very efficient, but it can only be used on high quality bauxite with low content of admixtures, (PDF) Handbook Aluminum From Bauxite mining to Alumina 2014年5月1日 PROCESS DESCRIPTION: ALUMINA REFINING The bauxite ore contains aluminum trihydrate (Al(OH) 3) Alumina refining produces alumina (Al 2 O 3) from the bauxite Bauxite mining and alumina refining: process description and
.jpg)
Chemical Processing of Bauxite: Alumina and Silica
The available alumina is traditionally determined by “bomb digestions” The major alumina producers have developed their own standardized determination methods The “available Bauxite is the principal ore of alumina (Al 2 O 3), which is used to produce aluminum (Al) It is composed of hydrated aluminum oxides, hydrated aluminosilicates, iron oxides, hydrated iron Bauxite Mining and Alumina Refining LWW2022年1月23日 Beside the processing behaviour of the main constituents of bauxite such as hydrated alumina and silica minerals, the Chapter covers the impact of other constituents, (PDF) Chemical Processing of Bauxite: Alumina and Silica Minerals 2008年1月1日 indicates the aluminacontent that can be made available by the BayerProcess with respect to geoche mistry and mineralogy of the ore Reactive silica (RSiO 2 ) and TiO 2 Mineral Processing technologies in the Bauxite and Alumina Industry
.jpg)
Bauxite Mining and Alumina Refining Process Description and
2014年5月1日 To describe bauxite mining and alumina refining processes and to outline the relevant physical, chemical, biological, ergonomic, and psychosocial health risks Review 2021年9月5日 This study aimed to model bauxite grinding and assess the optimum material filling volume in a laboratory ball mill in order to improve mill and overall process efficiency Modeling of Bauxite Ore Wet Milling for the Improvement of 2020年7月24日 Russia, one of the leading countries in the world in the production of alumina and primary Aluminum, also plans to maximize its production volume by utilizing its national nonbauxitic ores like Egyptian Aluminum containing ores and prospects combination of sintering and Bayer process can be used for ores with lower ratios However, sintering is an energyintensive process and increases the production cost of alumina [20–23] Beneficiation is often considered for the upgrade of bauxite ores in order to also render them suitable for the refractory/ceramics industry [13,16]Options of Bauxite Ores

Recycling of steel plant mill scale via iron ore sintering plant
2012年4月1日 Adding mill scale as an ingredient into the iron ore sintering or pelletizing process is the main utilization approach for mill scale because of its high iron content and positional advantages [10 2020年1月3日 Iron ores obtained from different sources differ in their chemical and physical properties These variations make the process of grinding a difficult task The work carried out in this context focuses on three different samples of iron ore, viz, high silica high alumina, low silica high alumina, and low silica low alumina The grinding process for all the three iron ores is Estimation of Grinding Time for Desired Particle Size Distribution 2016年6月2日 Before the event of ore dressing, crude ores were shipped directly to the smelters, or the refineries, with the shipper paying the freight and treatment 911 Metallurgist is a trusted resource for practical insights, solutions, and support in mineral processing engineering, helping industry professionals succeed with proven expertise Mineral Processing and Ore Mineral Processing and Ore Dressing 911Metallurgist2018年1月1日 Development of hematite ore pellet utilizing mill scale and iron ore slime combination as additive January 2018 Journal of Mining and Metallurgy Section B Metallurgy 54(00):88Development of hematite ore pellet utilizing mill scale and iron ore
.jpg)
(PDF) Handbook Aluminum From Bauxite mining to Alumina
The modern aluminium production using a hydrometallurgical refining process for making alumina followed by electrolysis of this mineral was first developed in 1886 and, in principle, the same technology is still used to this day About 90% of alumina refineries in the world use the Bayer process for refining Bauxite oreThe alumina lining bricks are used as the lining in the ball mill of ceramic industry, insulator industry Using this liner will effectively improve grinding efficiency, reduce grinding cost, and it is considered to be your best choice Alumina Liner for Batch Mill and Continuous Mill: Standard thickness 50 to 77 mm with Al2O2 content 92 to 95%Alumina Liner ATEMSDownload Table Distribution of alumina in different types of ores from publication: Current strategies and future challenges on exploration, beneficiation and value addition of iron ore Distribution of alumina in different types of ores2024年9月9日 Highalumina iron ore sintering is characterized by poor sinter indices and high carbon emission due to the limited formation amount of liquid phase In this study, the conventional Cabearing flux (ie, burnt lime) was substituted by a new Cabearing flux with low melting point (ie, prefabricated calcium ferrite) for the improvement of the formation ability of Promoting the Utilization of HighAlumina Iron Ores During
.jpg)
A comparison of wear rates of ball mill grinding
2016年1月1日 One of the most popular milling machines is the cement mill, which is used to crush raw materials such as lime, silicate, alumina and iron oxide using grinding balls [3]2020年5月21日 Iron ore pellets are largely characterized by inherent physical and chemical properties of the ore Alumina and silica play important roles in determining the productivity of a Blast Furnace On average, one percent increase in iron content improves productivity by 2% and reduces coke consumption by 1% Therefore higher iron ore feed content to blast furnace is A Study on HighGrade Iron ore Beneficiation to Reduce Alumina 2015年1月1日 The sintering pot test was used to investigate the effect of MgO/Al2O3ratio in the range of 12 to 22 on the sintering behavior of iron ore The main characterization methods of Xray diffraction Effect of high alumina iron ore of gibbsite type on sintering 2015年7月1日 Hightemperature quench method, scanning electron microscopeenergy dispersive spectroscopy (SEMEDS), and thermodynamic analysis were adopted to study the effects of Fe2O3 on reduction process of Thermal Analysis Study on the Carbothermic Reduction of Chromite Ore
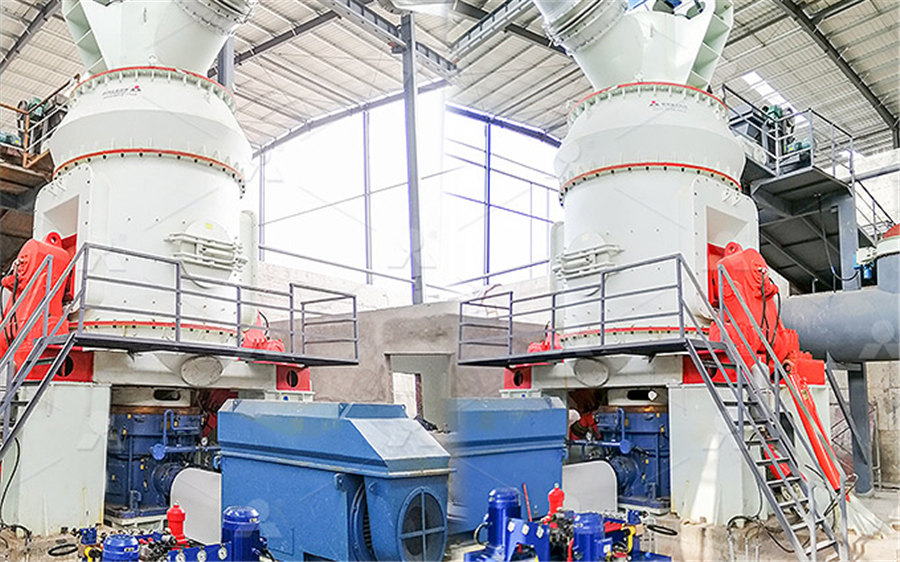
Extracting Silica and Alumina from LowGrade Bauxite
temperature for recovery of alumina was increased from 200–220°C to 260°C due to the presence of difficulttodecompose γalumina and mullite The residence time of digestion was varied from one hour (for highiron bauxite) to two hours (for lowiron ore) In any case, alumina yield was 19–20% higher than the same parameter for crude2016年2月1日 The purpose of this study is to understand how ore loss and dilution affect the mine call factor, with the aim of subsequently improving the quality of ore mined and fed to the millMonitoring ore loss and dilution for minetomill integration in 2007年4月4日 Dilution of adverse effects of alumina by adding highly reactive low alumina ores ratio was varied from 022 to 260 and for the samples where Al2O3 concentration was varied from 144 Effects of Alumina on Sintering Performance of Hematite Iron Ores2021年3月8日 Metallurgical grade alumina is produced worldwide through the wellknown Bayer process, which unavoidably generates bauxite residue (BR, also known as red mud) in almost equal amounts to aluminaThe Utilization of Bauxite Residue with a CalciteRich Bauxite Ore
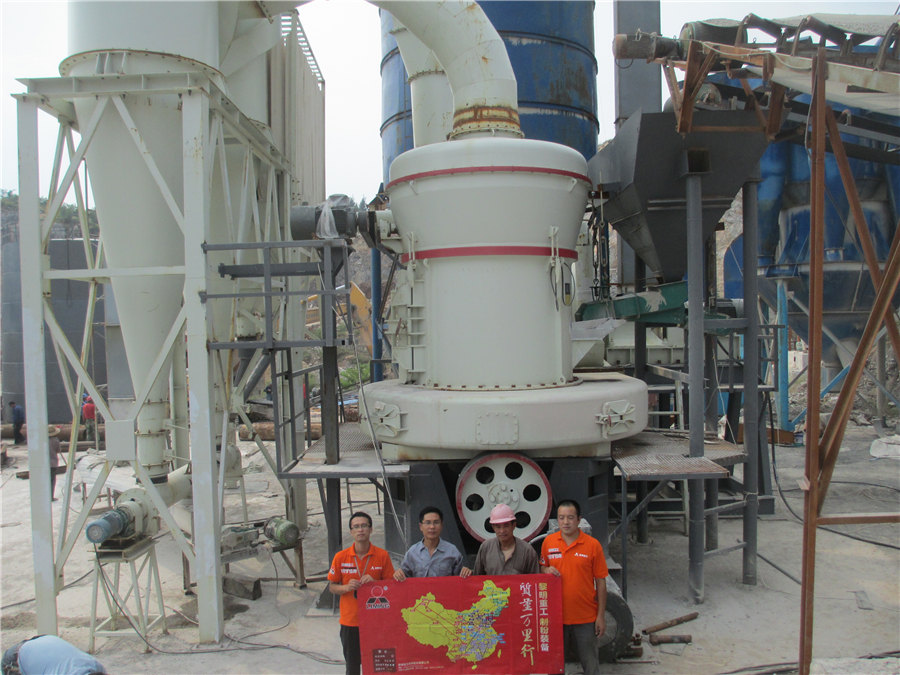
Removal of Silica and Alumina as Impurities from LowGrade Iron Ore
PDF On Jan 1, 2018, Kazutoshi Haga and others published Removal of Silica and Alumina as Impurities from LowGrade Iron Ore Using Wet HighIntensity Magnetic Separation and Reverse Flotation Bauxite Ore in the Pedersen Process for Iron and Alumina Extraction ADAMANTIA LAZOU, CASPER VAN DER EIJK, KAI TANG, EFTHYMIOS BALOMENOS, LEIV KOLBEINSEN, and JAFAR SAFARIAN Metallurgical grade alumina is produced worldwide through the wellknown Bayer process, which unavoidably generates bauxite residue (BR, also known as red mud) in The Utilization of Bauxite Residue with a CalciteRich Bauxite Ore 2018年7月9日 A technical route has been proposed to upgrade diasporic bauxite ores for iron and alumina enrichment based on reductive roasting, followed by magnetic separation and alkaline leaching The thermodynamic analysis revealed that by reductive roasting of the bauxite ore at 980–1100°C, hematite in the ore is transformed to magnetite and kaolinite is converted Upgrading Diasporic Bauxite Ores for Iron and Alumina 2014年5月1日 A crosssectional study of employees at three alumina refineries in Western Australia in 1995/1996 investigated respiratory symptoms and lung function in relation to bauxite dust, alumina dust, and caustic mist exposures21,22 After adjusting for age, smoking, and atopy, most groups of production workers reported a greater prevalence of workrelated wheeze and Bauxite mining and alumina refining: process description and
.jpg)
Modeling and Simulation of Ultrafine Grinding of Alumina in a
2023年7月16日 Request PDF Modeling and Simulation of Ultrafine Grinding of Alumina in a Planetary Ball Mill Mineral liberation from ores is an important step in mineral processing It is necessary to grind 2023年9月30日 PDF On Oct 1, 2023, Amr ElDeeb and others published COSTEFFECTIVE AND ECOFRIENDLY EXTRACTION OF ALUMINA BASED ON KAOLIN ORE USING THERMOCHEMICALLY ACTIVATED LIMESINTER PROCESS Find, read (PDF) COSTEFFECTIVE AND ECOFRIENDLY EXTRACTION OF ALUMINA 2020年9月11日 PDF Aiming at the effective utilization of the abundant highalumina iron ores with low iron grade, Iron ore B 722 3927 4413 938 Iron ore C 789 4336 4252 623Improving HighAlumina Iron Ores Processing via the 2017年4月1日 Optimization of Rod Mill Media Size in Alumina Oredressing Plant April 2017; Guocheng Gongcheng Xuebao/The Chinese Journal of Process Engineering 17(2):367370; DOI: 1012034/jissn1009606X Optimization of Rod Mill Media Size in Alumina Oredressing Plant
.jpg)
Modeling and Simulation of Ultrafine Grinding of Alumina in a
2023年7月16日 Mineral liberation from ores is an important step in mineral processing It is necessary to grind the ore to extremely fine size to liberate the mineral from such ores The planetary ball mill is promising in that it makes grinding to submicron sizes possible by imparting high energy to the ground powder In this context, there is a need to understand the dynamics 2022年4月8日 NO and SO2 are representative harmful gases generated in steel works, and iron ore sintering process accounts for more than 50 pct of total generation The current study investigated the effects of adding CaO and FeO, which are the components contained in raw materials to sinter mix on the formation of NO and SO2 The addition of CaO to sinter mix Effects of Adding Calcined Dolomite and Mill Scale to Sinter Mix Table 2 — Beneficiation practices of lowgrade iron ore Country Company Ore type Feed Process techniques Product Fe (%) AI 2O 3 (%) Wt% Fe (%) AI 2O 3 (%) For highalumina iron ore fines 1 India BMM Mines Hematite, goethite 580 Crusher, scrubber, screen, spirals, hydrocyclones, LIMS, HGMS, primary and secondary ball mill, thickener, filterDevelopment of process for beneficiation of lowgrade iron ore 2001年9月1日 The milling of γalumina slurries to obtain these distributions has been done in previous studies using various mill types: stirred media mill (Fadhel Frances, 2001); ball mill (Yang Sigmund Wet batch grinding of alumina hydrate in a stirred bead mill

Egyptian Aluminum containing ores and prospects
2020年7月24日 Russia, one of the leading countries in the world in the production of alumina and primary Aluminum, also plans to maximize its production volume by utilizing its national nonbauxitic ores like combination of sintering and Bayer process can be used for ores with lower ratios However, sintering is an energyintensive process and increases the production cost of alumina [20–23] Beneficiation is often considered for the upgrade of bauxite ores in order to also render them suitable for the refractory/ceramics industry [13,16]Options of Bauxite Ores2012年4月1日 Adding mill scale as an ingredient into the iron ore sintering or pelletizing process is the main utilization approach for mill scale because of its high iron content and positional advantages [10 Recycling of steel plant mill scale via iron ore sintering plant2020年1月3日 Iron ores obtained from different sources differ in their chemical and physical properties These variations make the process of grinding a difficult task The work carried out in this context focuses on three different samples of iron ore, viz, high silica high alumina, low silica high alumina, and low silica low alumina The grinding process for all the three iron ores is Estimation of Grinding Time for Desired Particle Size Distribution
.jpg)
Mineral Processing and Ore Dressing 911Metallurgist
2016年6月2日 Before the event of ore dressing, crude ores were shipped directly to the smelters, or the refineries, with the shipper paying the freight and treatment 911 Metallurgist is a trusted resource for practical insights, solutions, and support in mineral processing engineering, helping industry professionals succeed with proven expertise Mineral Processing and Ore 2018年1月1日 Development of hematite ore pellet utilizing mill scale and iron ore slime combination as additive January 2018 Journal of Mining and Metallurgy Section B Metallurgy 54(00):88Development of hematite ore pellet utilizing mill scale and iron ore The modern aluminium production using a hydrometallurgical refining process for making alumina followed by electrolysis of this mineral was first developed in 1886 and, in principle, the same technology is still used to this day About 90% of alumina refineries in the world use the Bayer process for refining Bauxite ore(PDF) Handbook Aluminum From Bauxite mining to Alumina The alumina lining bricks are used as the lining in the ball mill of ceramic industry, insulator industry Using this liner will effectively improve grinding efficiency, reduce grinding cost, and it is considered to be your best choice Alumina Liner for Batch Mill and Continuous Mill: Standard thickness 50 to 77 mm with Al2O2 content 92 to 95%Alumina Liner ATEMS
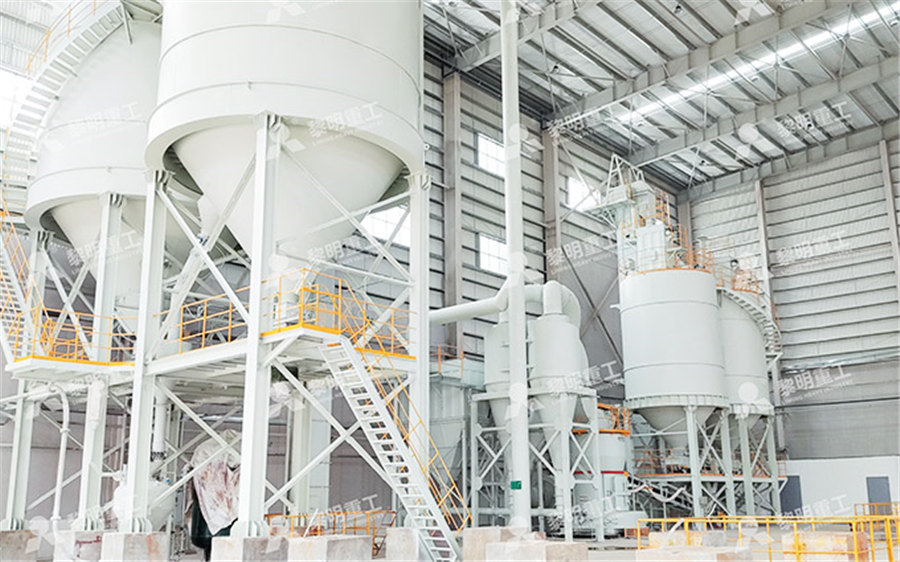
Distribution of alumina in different types of ores
Download Table Distribution of alumina in different types of ores from publication: Current strategies and future challenges on exploration, beneficiation and value addition of iron ore 2024年9月9日 Highalumina iron ore sintering is characterized by poor sinter indices and high carbon emission due to the limited formation amount of liquid phase In this study, the conventional Cabearing flux (ie, burnt lime) was substituted by a new Cabearing flux with low melting point (ie, prefabricated calcium ferrite) for the improvement of the formation ability of Promoting the Utilization of HighAlumina Iron Ores During