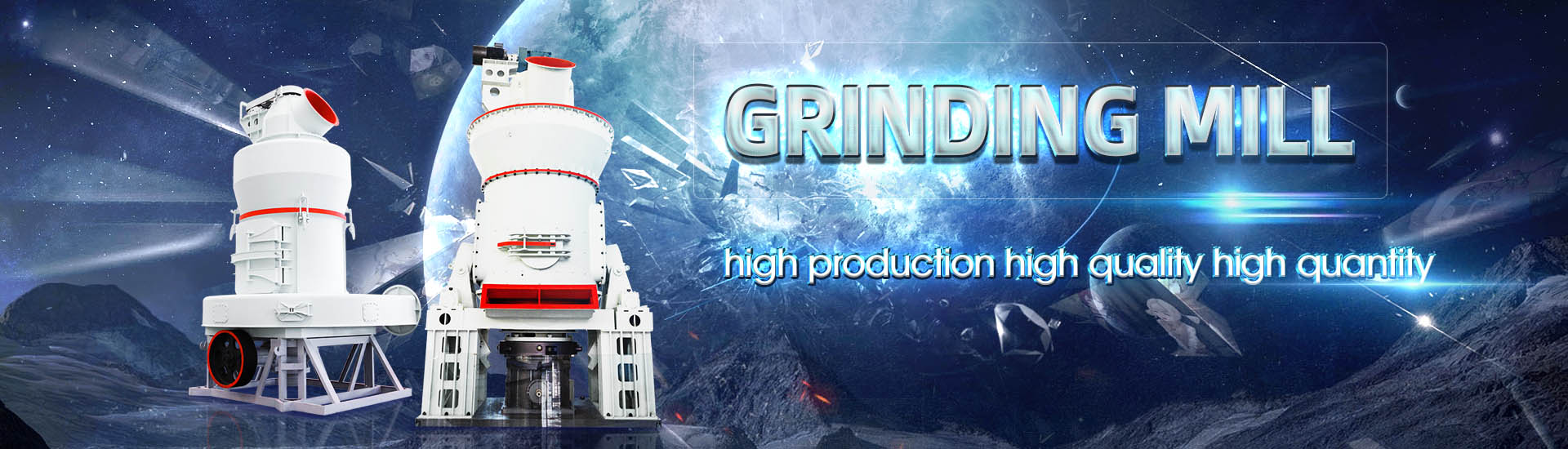
Ball mill output calculation method
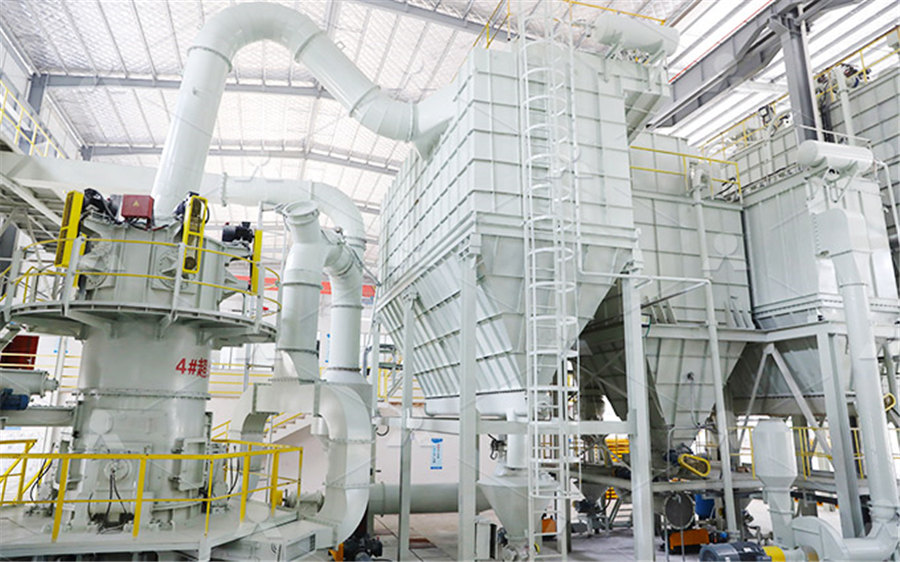
BALL MILLS Ball mill optimisation Holzinger Consulting
Ball mill optimisation As grinding accounts for a sizeable share in a cement plant’s power consumption, optimisation of grinding equipment such as ball mills can provide significant cost and COThe document contains formulas and examples for calculating key performance metrics for ball mills used in cement production It includes formulas to calculate power consumption, production rate, specific power, circulation factor, Ball Mill Calculations PDF Mill (Grinding) Industrial Define and calculate the grinding efficiency of the ball mill in a ball mill circuit Relate overall ball mill circuit output and circuit efficiency to specific design and operating variables Compare MODULE #5: FUNCTIONAL PERFOMANCE OF BALL MILLING2013年8月3日 In Grinding, selecting (calculate) the correct or optimum ball size that allows for the best and optimum/ideal or target grind size to be achieved by your ball mill is an important thing for a Mineral Processing Engineer AKA Calculate and Select Ball Mill Ball Size for Optimum
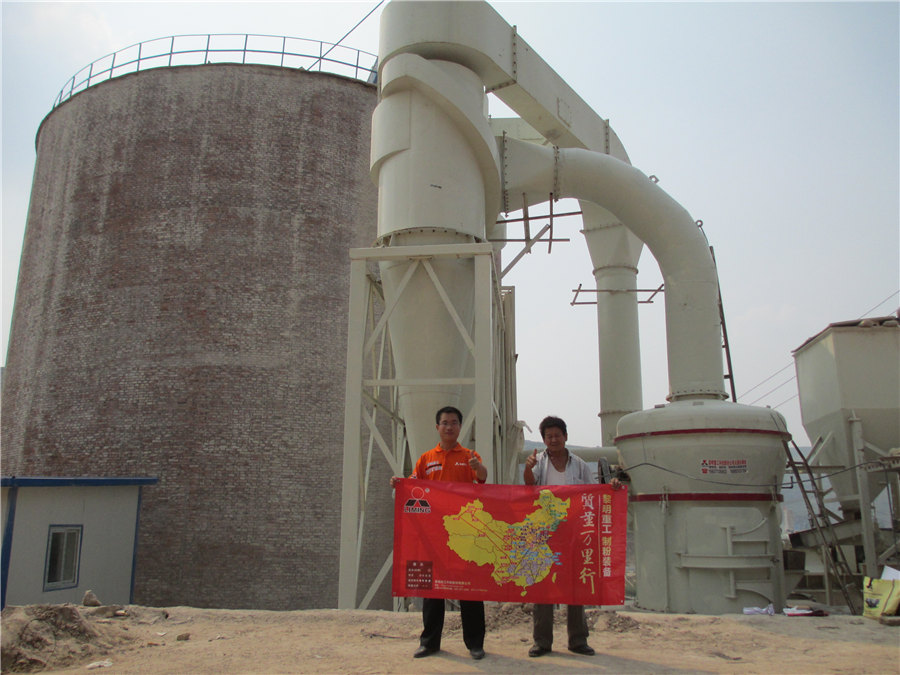
Ball Mill Design/Power Calculation 911Metallurgist
2015年6月19日 Ball Mill Power Calculation Example #1 A wet grinding ball mill in closed circuit is to be fed 100 TPH of a material with a work index of 15 and a size distribution of 80% passing ¼ inch (6350 microns) The required product 2023年10月1日 In this paper, a new method based on the Population Balance Model (PBM) is proposed and validated to estimate the results of the Bond ball mill work index test (Wi B) The Estimation methodology for Bond ball mill work index experiment Describe the components of ball mill Explain their understanding of ball mill operation Explain the role of critical speed and power draw in design and process control Recognize important considerations in ball mill selection Reading AMIT 135: Lesson 7 Ball Mills Circuits – Mining Mill 2022年4月21日 In actual industrial production, labeled sample data of a ball mill is difficult to obtain under variable working conditions Aiming to realize the soft measurement of ball mill Soft measurement of ball mill load under variable working
.jpg)
Grinding in Ball Mills: Modeling and Process Control ResearchGate
2012年6月1日 The paper presents an overview of the current methodology and practice in modeling and control of the grinding process in industrial ball mills Basic kinetic and energy 2022年3月15日 Various operational parameters, such as mill speed, the ball charge composition, charge filling, lifter type, and lifter number, significantly impact ball milling grinding efficiency [3](PDF) Power consumption management and simulation For “theory to practice”, the commercially available mill is taken to simulate kinematics of a onedimension mill E impact and cumulative energy E total are calculated based on known parameters: Diameter of the jar, length of the jar, amplitude of the jar, diameter of the ball, mass of the ball, total number of balls, frequency, and timeLungerich Group Tools2015年6月19日 The basic parameters used in ball mill design (power calculations), rod mill or any tumbling mill sizing are; material to be ground, characteristics, Bond Work Index, bulk density, specific density, desired mill Ball Mill Design/Power Calculation 911Metallurgist
.jpg)
Ball Mill Success: A StepbyStep Guide to Choosing
2024年8月8日 In the intricate dance of ball milling, where raw materials are transformed into finely milled particles, the choice of grinding media emerges as a pivotal performance lever This seemingly minor selection can dramatically 2023年10月1日 The inner diameter and the length are 0305 m, and the ball load is 194% of mill volume (equaling a total weight of 20125 kg) The mill has a frequency inverter with 220 V singlephase The mill design, operating conditions, and ball size distribution were based on Bond’s (1961 a,b) work index methodology and are shown in Table 2Estimation methodology for Bond ball mill work index experiment output 2020年2月26日 Measurement results of two ball mills in a real ceramic manufacturing plant showed that the proposed calculation models could achieve an accuracy of more than 96% for predicting the ball mill Calculation method and its application for energy consumption of ball 2017年2月13日 The apparent difference in capacities between grinding mills (listed as being the same size) is due to the fact that there is no uniform method of designating the size of a mill, for example: a 5′ x 5′ Ball Mill has a working diameter of 5′ inside the liners and has 20 per cent more capacity than all other ball mills designated as 5′ x 5′ where the shell is 5′ inside diameter and Ball Mills 911Metallurgist
.jpg)
Monitoring the fill level of a ball mill using vibration sensing and
2019年10月19日 Ball mills are extensively used in the size reduction process of different ores and minerals The fill level inside a ball mill is a crucial parameter which needs to be monitored regularly for optimal operation of the ball mill In this paper, a vibration monitoringbased method is proposed and tested for estimating the fill level inside a laboratoryscale ball mill A vibration Additionally, the actual position of the tool involved in cutting also changes, leading to uneven wear distribution on the ballend mill, making tool wear prediction and evaluation challenging In this paper, a discretization calculation method of tool path length for surface machining is proposed based on PowerMill postprocessing developmentA tool wear prediction method for freeform surface machining of ball 2016年2月14日 Do you need a quick estimation of a ball mill's capacity or a simple method to estimate how much can a ball mill of a given size (diameter/lenght) Ball mill design power example calculation Calculate Ball Mill Grinding Capacity David ; February 14, 2016; 6:03 pm; Prev Previous Hydrometallurgy ArticlesSmall Ball Mill Capacity Sizing Table 911Metallurgist2022年1月1日 The gear box is a collection of shafts, bearings, casing and gears in a systematic form to obtain the desired output The operating load in the ball mill is 200 kN, critical speeds range from 343 rpm and a power of 124 kW Introduction Ball mill is the size Calculation method and its application for energy consumption of ball Design and simulation of gear box for stone crushing ball mill
.jpg)
(PDF) Energy Efficient Ball Mill Circuit – Equipment
2013年7月15日 A ball mill circuit in closed circuit with scr eens can be designed using powerbased methods, similarly to circuits closed with cyclones These methodologies calculate the required mill specificCurrent methods of power consumption calculation of a mill drive do not allow determining the power consumption for ball drum mills with a crosslongitudinal motion of the grinding media A new calculation method has been developed taking into account different designs of integrated devices and modes of the grinding media motionThe Power Consumption Calculation of a Ball Drum Mill2015年10月9日 Calculating a grinding circuit’s circulating loads based on Screen Analysis of its slurries Compared to %Solids or Density based Circulating load equations, a more precise method of determining grinding Ball Mill Circulating Load Formula 911MetallurgistDownload Table Ball mill characteristics and test conditions Mill Diameter, D (cm) 204 Length, L (cm) 166 Volume, V (cm 3 ) 5,423 Operational speed, Ν (rpm) 66 from publication Ball mill characteristics and test conditions Mill Diameter, D
.jpg)
Modelling of the HighEnergy Ball Milling Process ResearchGate
M Mhadhbi DOI: 104236/ampc2021 33 Advances in Materials Physics and Chemistry Figure 1 Photograph of the highenergy planetary ball millA ball mill is a type of grinder filled with grinding balls, used to grind or blend materials for use in mineral dressing processes, paints, pyrotechnics, ceramics, and selective laser sintering It works on the principle of impact and attrition: size reduction is done by impact as the balls drop from near the top of the shellBall mill WikipediaBall Mill Calculations Free download as Excel Spreadsheet (xls), PDF File (pdf), Text File (txt) or view presentation slides online The document contains formulas and examples for calculating key performance metrics for ball mills used in cement production It includes formulas to calculate power consumption, production rate, specific power, circulation factor, separator efficiency, Ball Mill Calculations PDF Mill (Grinding) Scribd2021年7月26日 The common control methods, including model predictive control (MPC), disturbance observer (DO), and so on, show poor performance when strong external and internal disturbances exist In this paper, a composite control strategy based on MPCDO is put forward to realize the control of the threeinputthreeoutput ball mill systemProcess Control of Ball Mill Based on MPCDO Wiley Online
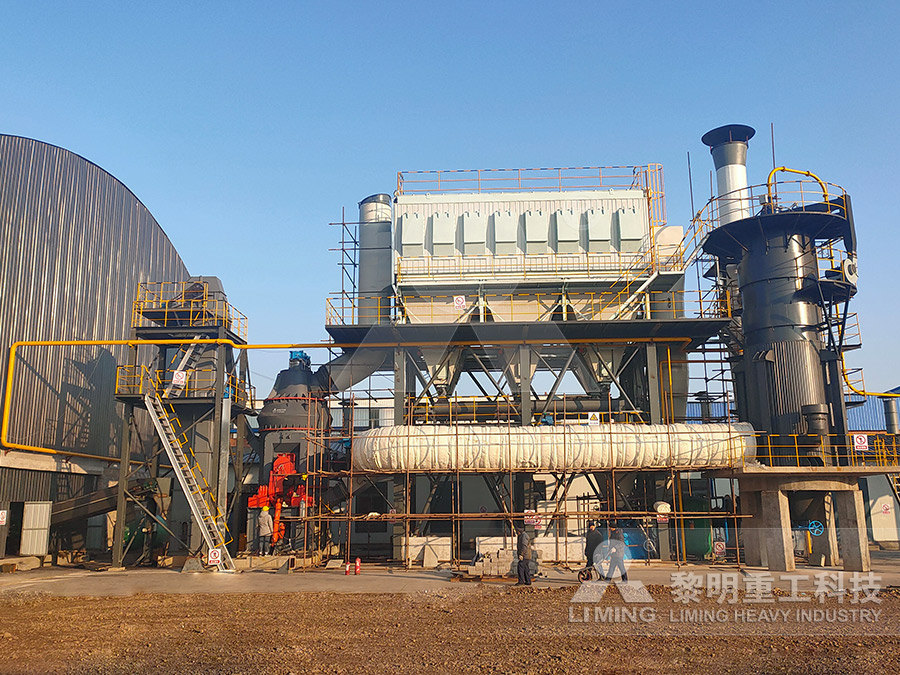
Intelligent optimal control system for ball mill grinding process
J Control Theory Appl 2013 11 (3) 454–462 DOI 101007/s1176801312103 Intelligent optimal control system for ball mill grinding process Dayong ZHAO 1†, Tianyou CHAI,2 1State Key Laboratory of Synthetical Automation for Process Industries, Northeastern University, Shenyang Liaoning , China;2017年7月26日 The finer you crush, the higher your ball mill tonnage and capacity will be 911 Metallurgist is a Here we described a method of designing a crushing plant using power drawn and power rate to define The rod mill was needed to reduce feed size to the ball mill because crushing plant output was normally coarser than 80% How Ball Mill Ore Feed Size Affects Tonnage CapacityPrevious Post Next Post Contents1 Ball charge optimization2 1 How to use the BP21 2 Description of the main indicators used in this BP2101 The residue on 2mm/4mm before partition wall2102 Material filling level and ball charge expansion211 Cement mill specific power 1st compartment 212 Raw mill specific power 1st compartment Ball charge Ball charge optimization INFINITY FOR CEMENT EQUIPMENT2014年1月1日 Optimization of ball mill operating parameters for their effect on mill output and cement fineness by using RSM method January 2014 International Journal of Applied Engineering Research 9(23 Optimization of ball mill operating parameters for their effect on mill
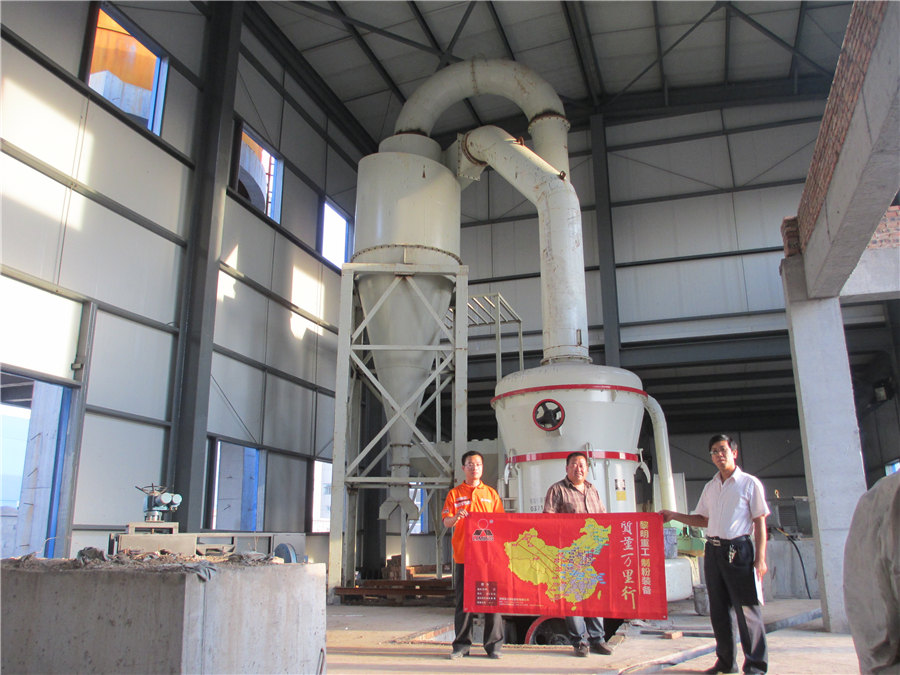
Ball Mill Grinding Process Handbook
Ball Mill Grinding Process Handbook Free download as PDF File (pdf), Text File (txt) or read online for free This document provides guidance on ball mill grinding processes It covers topics such as ball mill design including length to this work, the highenergy planetary ball mill process is modeled using the soft ware Automated Dynamic Analysis of Mechanical System MSC Adams[22] Figure 2 illustrates a schematic of a high Modelling of the HighEnergy Ball Milling Process2023年9月18日 Although not as popular as the Bond ball mill or the Bond rod mill work indices, the impact work index, also called Bond crushability index, continues to be much used for crusher selectionBond´s work index estimation using nonstandard ball mills2018年4月8日 Unlock the principles of ball mill design with 911 Metallurgist This guide offers detailed calculations and practical tips to ensure your mill is optimized for performance, efficiency, and effective mineral processingBall Mill Design Calculations How to 911Metallurgist
.jpg)
CALCULATION OF THE REQUIRED SEMIAUTOGENOUS MILL
(ball mills, autogenous and semiautogenous grinding mills) The basics of the described method were developed by S Morrel, an Australian expert in mineral material milling, and have not been published previously in Russia The RIVS experts have compared the new method and a few commonly used techniques andGrinding of ClassF fly ash using planetary ball mill: A simulation study to determine the breakage kinetics by direct and backcalculation method Dilip K Rajak, Atul Raj, Chandan Guria*, Akhilendra K Pathak Department of Petroleum Engineering, Indian Institute of Technology (Indian School of Mines), Dhanbad 826 004,Grinding of ClassF fly ash using planetary ball mill: A simulation techniques as a novel ball mill filllevel estimation method The ANN model is trained and tested using experimentally collected data 1502 Neural Computing and Applications (2020) The output of the ANN is used to estimate the percentage fill level of a ball mill 21 F Fi feature i Time domain signal xnðÞwas transformed into frequencyMonitoring the fill level of a ball mill using vibration sensing and 2023年4月23日 One of the most used tumbling mills is the ball mill method determine the h ardness of the grinding m edia In one study, oilquenched alloysteel balls heattreated at lower (PDF) Grinding Media in Ball MillsA Review ResearchGate
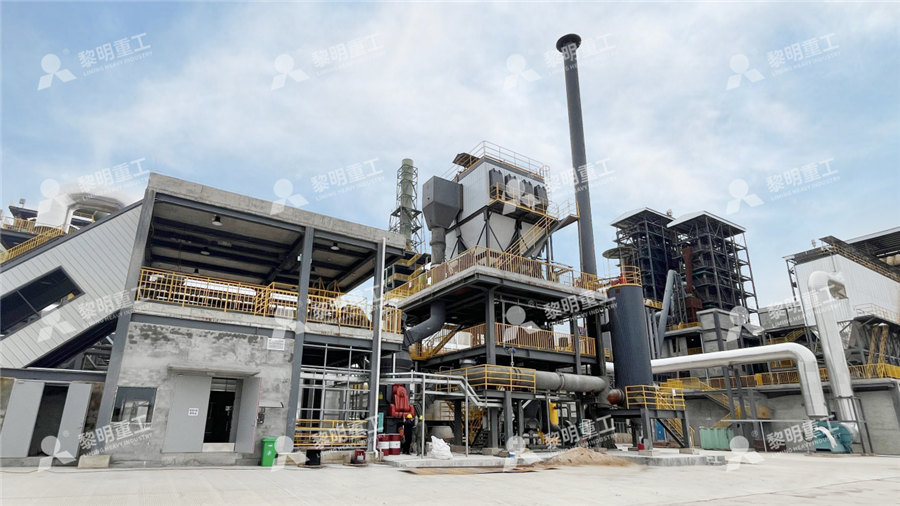
Lungerich Group Tools
For “theory to practice”, the commercially available mill is taken to simulate kinematics of a onedimension mill E impact and cumulative energy E total are calculated based on known parameters: Diameter of the jar, length of the jar, amplitude of the jar, diameter of the ball, mass of the ball, total number of balls, frequency, and time2015年6月19日 The basic parameters used in ball mill design (power calculations), rod mill or any tumbling mill sizing are; material to be ground, characteristics, Bond Work Index, bulk density, specific density, desired mill Ball Mill Design/Power Calculation 911Metallurgist2024年8月8日 In the intricate dance of ball milling, where raw materials are transformed into finely milled particles, the choice of grinding media emerges as a pivotal performance lever This seemingly minor selection can dramatically Ball Mill Success: A StepbyStep Guide to Choosing 2023年10月1日 The inner diameter and the length are 0305 m, and the ball load is 194% of mill volume (equaling a total weight of 20125 kg) The mill has a frequency inverter with 220 V singlephase The mill design, operating conditions, and ball size distribution were based on Bond’s (1961 a,b) work index methodology and are shown in Table 2Estimation methodology for Bond ball mill work index experiment output

Calculation method and its application for energy consumption of ball
2020年2月26日 Measurement results of two ball mills in a real ceramic manufacturing plant showed that the proposed calculation models could achieve an accuracy of more than 96% for predicting the ball mill 2017年2月13日 The apparent difference in capacities between grinding mills (listed as being the same size) is due to the fact that there is no uniform method of designating the size of a mill, for example: a 5′ x 5′ Ball Mill has a working diameter of 5′ inside the liners and has 20 per cent more capacity than all other ball mills designated as 5′ x 5′ where the shell is 5′ inside diameter and Ball Mills 911Metallurgist2019年10月19日 Ball mills are extensively used in the size reduction process of different ores and minerals The fill level inside a ball mill is a crucial parameter which needs to be monitored regularly for optimal operation of the ball mill In this paper, a vibration monitoringbased method is proposed and tested for estimating the fill level inside a laboratoryscale ball mill A vibration Monitoring the fill level of a ball mill using vibration sensing and Additionally, the actual position of the tool involved in cutting also changes, leading to uneven wear distribution on the ballend mill, making tool wear prediction and evaluation challenging In this paper, a discretization calculation method of tool path length for surface machining is proposed based on PowerMill postprocessing developmentA tool wear prediction method for freeform surface machining of ball
.jpg)
Small Ball Mill Capacity Sizing Table 911Metallurgist
2016年2月14日 Do you need a quick estimation of a ball mill's capacity or a simple method to estimate how much can a ball mill of a given size (diameter/lenght) Ball mill design power example calculation Calculate Ball Mill Grinding Capacity David ; February 14, 2016; 6:03 pm; Prev Previous Hydrometallurgy Articles2022年1月1日 The gear box is a collection of shafts, bearings, casing and gears in a systematic form to obtain the desired output The operating load in the ball mill is 200 kN, critical speeds range from 343 rpm and a power of 124 kW Introduction Ball mill is the size Calculation method and its application for energy consumption of ball Design and simulation of gear box for stone crushing ball mill