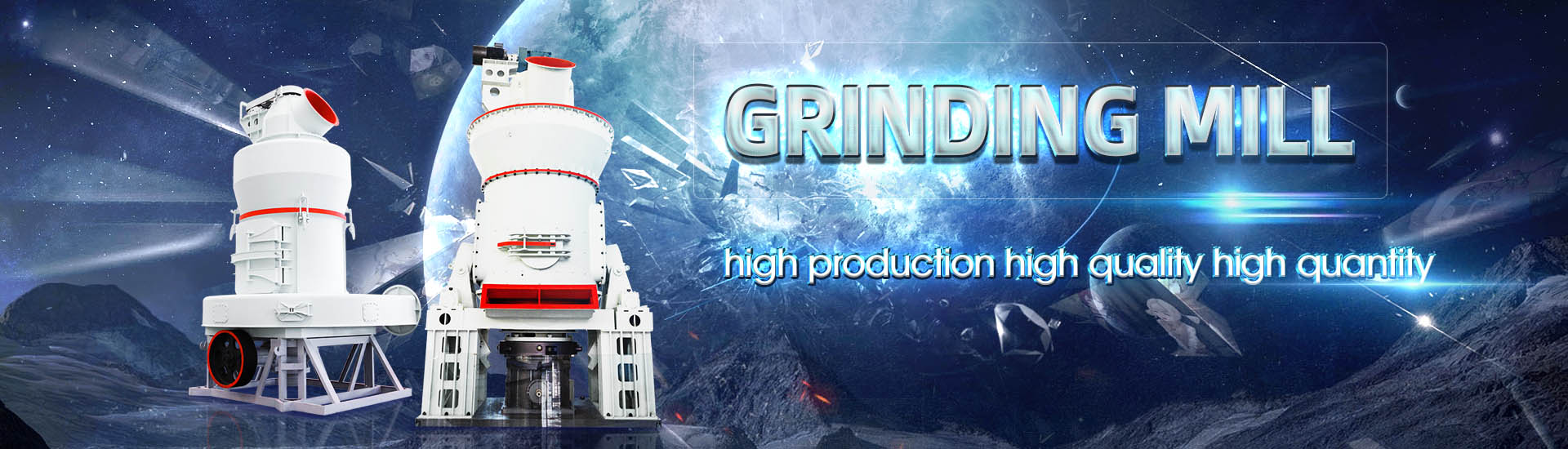
Lithium carbonate kaolin processing equipment
.jpg)
Lithium processing technology Complete solutions that FLSmidth
Impurity removal from the salar brine is a critical step in the process flowsheet for production of batterygrade lithium Our MaxRTM technology provides the most advanced method in the industry, combining precipitation reactors with solidliquid separation, which allows the seeding Bepex has been supplying processing technology for lithium carbonate or lithium hydroxide production since the early 1990s Now, with lithium producers straining to fulfill ever increasing demand, Bepex is pioneering systems to streamline Lithium Processing Systems and Equipment BepexKTS offers integrated engineering and equipment design to produce a concentrated lithium chloride ready for final conversion into a lithium carbonate or hydroxide As your one source partner, we can also leverage the expertise LiPro™ Direct Lithium Extraction TechnologyKBR has developed PureLiSM a unique lithium conversion and refining process to cater to the growing lithiumion battery demand for electric vehicles and stationary energy storage KBR’s HighPurity Lithium Production Technology
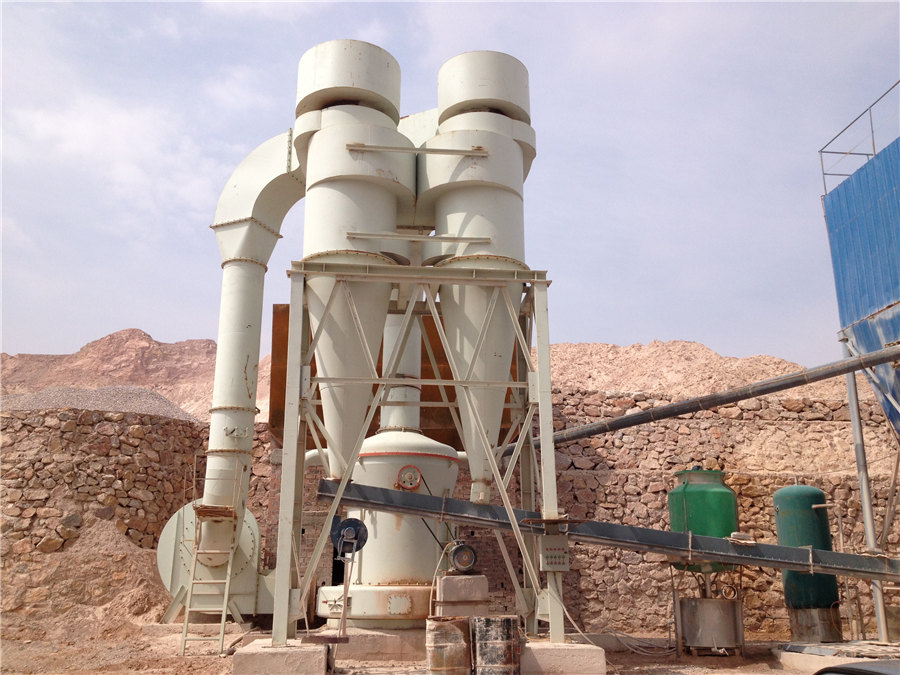
Recent advances in lithium extraction from lithiumbearing clay
2023年3月1日 Future researchers are expected to put more effort into the elucidation of actual chemical reactions involving minerals and interim/final products, process optimization, and the Working with the lithium concentrate, SGS’ team uses a standardized flowsheet to produce high grade lithium products such as lithium carbonate or lithium hydroxide These are reagents for Hard Rock Lithium Processing SGSWe concentrate, refine, and convert lithium chloride solutions to technical or battery grade lithium carbonate or lithium hydroxide solids We offer robust, modular, wellautomated, and Lithium: Processing Saltworks Technologies2021年5月1日 Some specific techniques of lithium extraction from ores and minerals are systematized Autoclave methods seem the most promising for poor alkaline Li Processing of lithium ores: Industrial technologies and case studies

Lithium extraction from a Lirich kaolin resource through Na2SO4
2024年11月1日 In this study, lithium extraction from a Lirich kaolin is performed by roasting with Na 2 SO 4 and water leaching The thermal analysis of the Lirich kaolin is characterized by Lithium carbonate in distilled water (a) and power form of lithium carbonate after drying (b) Purity of recovered Li 2 CO 3 was measured by analyzing the contents of the elements of 40 minerals in ICPOES analysis, and Table 2 displays 50 elements that are analyzed for purity As a result of purity analysis, 7 elements of impurities wereCarbonation Process to Manufacture Lithium Carbonate from Lithium As a worldwide leader in the supply of lithium brine treatment technologies and chemical processing systems, Veolia Water Technologies helps lithium producers and recyclers meet the technical challenges associated with the rising Lithium Processing Battery Recycling SolutionsDownload scientific diagram Overview of main processing options for production of lithium carbonate from rock minerals from publication: Minerometallurgical processes for lithium recovery from Overview of main processing options for
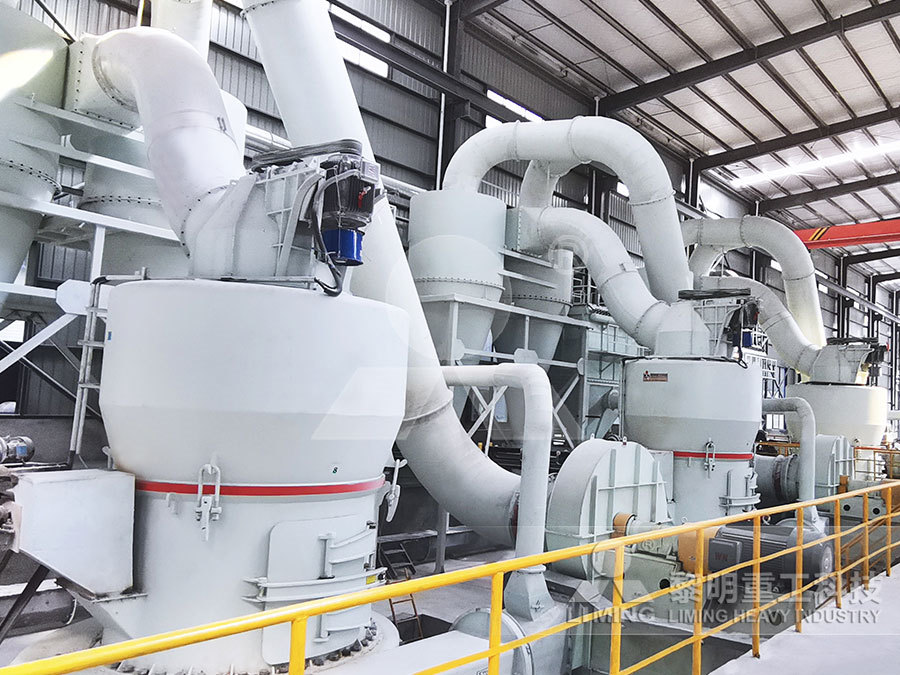
Lithium Processing Capabilities Veolia Water Tech
Lithium Processing Experience lithium chloride Solids handling equipment, including a centrifuge and dryer, were integrated into the overall process design • Lithium Chloride (LiCl) • Lithium Carbonate (Li 2 CO 3) • Lithium Hydroxide anhydrous and monohydrate (LiOH)Extensive work has gone into designing the most efficient and costeffective processing route for producing lithium hydroxide from ore We use nontoxic additives and our lowwaste process is designed to ensure that as much as possible of what comes out can be used commercially to support local industriesThe Process Germany's Lithium Hydroxide Production RouteDuring the evaporation process, a slurry of hydrated lime (Ca(OH) 2) is added to the brine to precipitate out unwanted elements, particularly magnesium and boron (as magnesium hydroxide and calcium boron salts)When lithium concentration reaches a certain point, the brine is pumped to a recovery facility to extract the metal, a process that usually includes the following stepsLithium handling Carmeuse SystemsThe process is undertaken at atmospheric pressure and modest temperature, followed by a series of impurity removal steps at progressively higher pH levels and the subsequent precipitation of lithium carbonate The process contrasts with the far more energy intensive processing of spodumene concentrates, which requires high temperature Processing Technology Cornish Lithium Plc
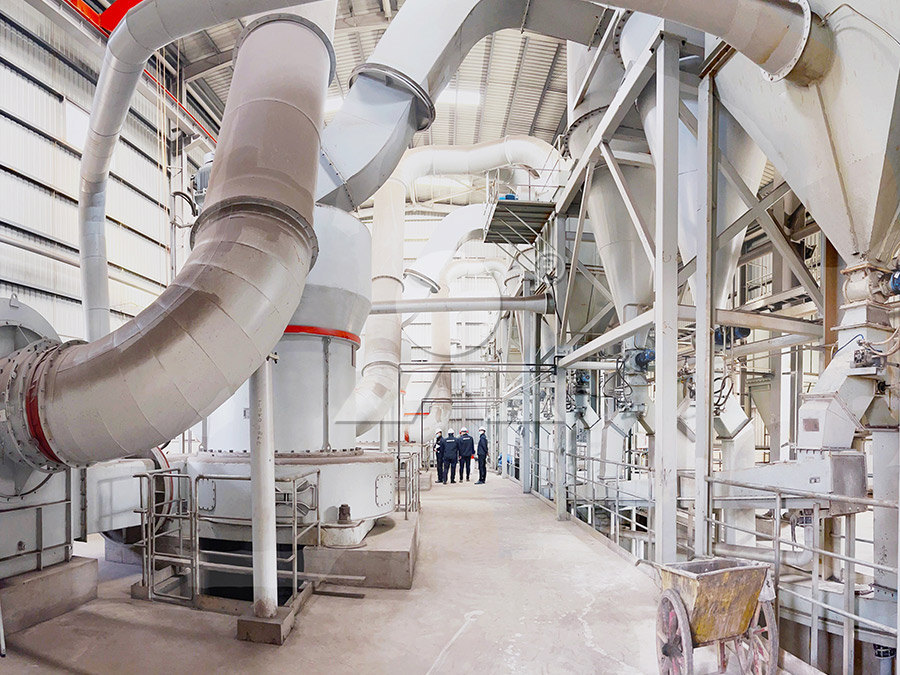
KBR’s HighPurity Lithium Production Technology
KBR has developed PureLiSM a unique lithium conversion and refining process to cater to the growing lithiumion battery demand for electric vehicles and stationary energy storage systems PureLi is capable of transforming a wide range of lithium feedstocks into batterygrade lithium carbonate or lithium hydroxide monohydrateAfter the lithium brine solution is concentrated to the specifications you desire, it is transferred to the mixing tank Soda ash is added to lithium brine in order to precipitate lithium carbonate (Li₂CO₃)The solution is processed by the Filter Press where the lithium carbonate is captured between the plates, and the remaining liquid is dischargedLithiumion Battery Recycling Process Equipment MetChem2023年3月15日 Treated with sodium carbonate, known also as soda ash, to remove lithium carbonate Lithium carbonate is then washed and dried into end product This lithium mining process also tends to consume large quantities of fresh water This water is largely drawn from aquifers, rivers, wells, or other water sources used for drinking or irrigationThe Lithium Mining Process2023年10月9日 The machinery and equipment used in a lithium ore processing plant may vary depending on the (eg, spodumene, brine, or clay) and the desired end product (eg, lithium carbonate, lithium Lithium ore processing plant machinery and equipment LinkedIn
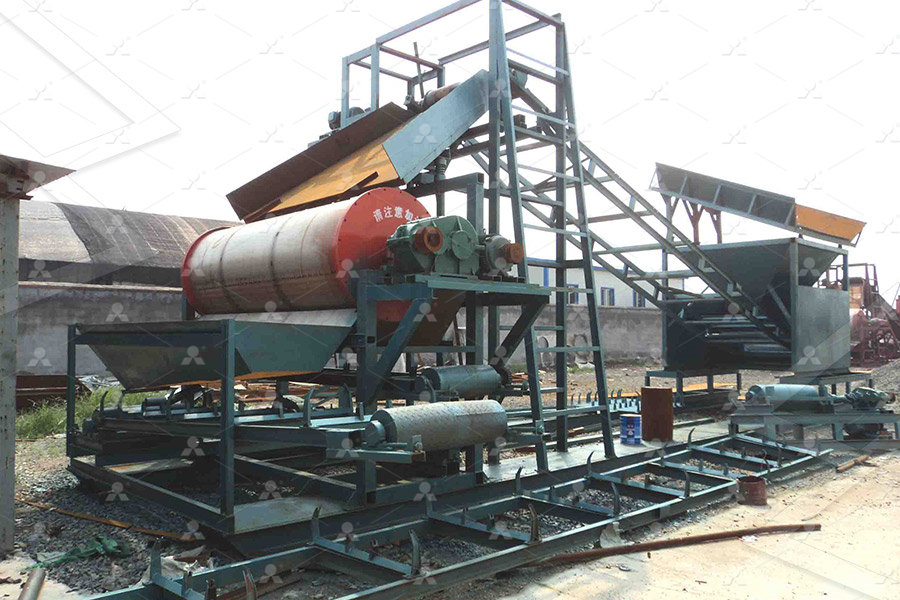
Lithium Ore Mining Process JXSC Mineral
Spodumene has a theoretical Li2O content of 803% Due to its high lithium content, spodumene is the most important lithium ore mineral A typical run of mine ore can contain 12% Li2O, while a typical spodumene concentrate 2024年2月8日 Liu, H Azimi, G Process analysis and study of factors affecting the lithium carbonate crystallization from sulfate media during lithium extraction Hydrometallurgy 199 , (2021)Reevaluation of batterygrade lithium purity toward NatureThis is in keeping with the Company’s strategy of enabling a decarbonisation of the lithium supply chain Resource drilling in 2021 led to the publication of a maiden JORCcompliant Inferred Resource of 517 million tonnes at a grade of 024% lithium oxide equating to over 300,000 tonnes of contained Lithium Carbonate EquivalentTrelavour Cornish Lithium Plc2021年2月1日 Request PDF Processing of lithium ores: Industrial technologies and case studies – A review Recently, there has been a steady increase in demand for lithium (Li) and its compounds Processing of lithium ores: Industrial technologies and case studies
.jpg)
Ball Mill Is Indispensable For Lithium Ore Processing
2024年11月21日 The grinding and grading stage of lithium ore is to ensure that lithium minerals are fully dissociated from gangue mineral monomers Therefore, lithium ore extraction is inseparable from ore grinding, and the common equipment for lithium ore grinding is ball mill Onestage closedcircuit grinding and grading process can be adopted, and the onestage 2019年10月27日 a Fluid bed dryer is equipment used extensively in the bulk industry to reduce the moisture content of powder and granules Lithium hydroxide and lithium carbonate Fluid Bed Dryers; Published On: 27 October 2019 Categories: Products Tags: Lithium hydroxide dryer Lithium is mainly destined for the fastgrowing lithiumion battery Lithium hydroxide and lithium carbonate Fluid Bed Dryers Tema ProcessLithium Processing The Spodumene concentrate ore is converted into either Lithium Carbonate or Lithium Hydroxide for use as an essential component to make LithiumIon Batteries The process for making Lithium Carbonate is illustrated in Figure 2 A similar flow schematic with different chemical reagents can be used to make Lithium HydroxideLithium Processing Spodumene filtration solutionOur lithium processing capabilities are reinforced by a global team of scientists and engineers that design solutions for the production of high purity lithium System Designs Veolia has a wide range of evaporation and crystallization system designs specific for lithium processing Filtration and membrane, ion exchange, lithium brine concentrationLithium Processing Solutions Services Veolia Water
.jpg)
Lithium Processing Plant, Equipment JXSC Machinery
Crushing screening: In the crushing and screening stage of lithium ore, a threestage and one closedcircuit crushing and screening process, or a twostage and one closedcircuit crushing and screening process can be adoptedSpecifically, it is necessary to refer to the particle size of the raw ore and equip a reasonable lithium ore crushing process2022年12月13日 The following is the process flow of lithium ore processing to obtain lithium carbonate: After the mining of lithium ore, the bulk material is first crushed by electromagnetic dressing equipment; Then under the action of belt conveyor, it is evenly sent to the grinding machine for deep grinding treatment; After grinding, lithium ore powder should be reasonably How to mine lithium ore, mineral processing, crushing, grindingWhile we do not provide equipment for processing lithium brines, FEECO is a leader in advanced thermal processing and agglomeration equipment and supporting services for the processing of lithiumbearing ores, most notably Lithium Processing Equipment FEECO International Lithium Carbonate and Lithium Hydroxide Transfer Systems Whether transferring battery grade lithium powder from a dryer to a storage silo or from a silo to packaging equipment or a bulk truck, Schenck Process can provide a complete transfer solution RT filter RT filter MD airlock Flex tube diverter Flex tube diverter RT filter MD airlock MDBulk Material Handling Processing Solutions for Lithium
.jpg)
Research of lithium carbonate threephase reactive crystallization process
2021年9月13日 The gasliquidsolid reactive crystallization process of lithium carbonate includes two consecutive steps, which are the carbonization reaction process of lithium carbonate and the thermal decomposition process of lithium bicarbonate solution First, the factors of the lithium carbonate carbonization reaction rate were investigatedPDF On Jan 1, 2022, Tianming Gao and others published Lithium extraction from hard rock lithium ores: technology, resources, environment and cost Find, read and cite all the research you need (PDF) Lithium extraction from hard rock lithium ores: technology A high lithium ore, containing approximately 6% lithium, is the main raw material used in the production of lithium salts (lithium hydroxide or lithium carbonate) from hard rock sources Building on globally diverse lithium conversion sites in the Americas, Australia and China, Albemarle has invested in both added capacity as well as new strategic processing locations around the worldLithium Resource Processing Albemarle2023年6月29日 High lithium carbonate solubility (15 g/L) and high liquid to solid leaching ratios require costly and avoidable operations to be implemented in order to enhance lithium concentrationLithium Production and Recovery Methods: Overview of Lithium
.jpg)
Commercial Lithium Production and Mining of Lithium
2020年8月21日 Processing From Brine Much of the lithium produced today is extracted from brine reservoirs called salars that are located in highelevation The conversion ratio of lithium carbonate to lithium metal is about 53 to 1 Global Lithium Production The top five countries for lithium production in 2018 were Australia, Chile, China 2023年11月15日 Conventional processing of a lithiumion battery cell consists of three steps: (1) elec trode manufacturing, (2) cell assembly , and (3) cell finishing (formation) [ 8LithiumIon Battery Manufacturing: Industrial View on Processing 2023年12月27日 In step 1, to convert spodumene into lithium sulfate (Li 2 SO 4), the raw ore is crushed and separated both mechanically and via floatationNext, the concentrate undergoes energy and chemically intensive hot acidroasting This process (as shown in Figure 1 below) sees concentrated spodumene powder roasted at 1050°C, cooled, mixed with sulfuric acid, Hard Rock Spodumene Lithium Processing Saltworks Lithium carbonate in distilled water (a) and power form of lithium carbonate after drying (b) Purity of recovered Li 2 CO 3 was measured by analyzing the contents of the elements of 40 minerals in ICPOES analysis, and Table 2 displays 50 elements that are analyzed for purity As a result of purity analysis, 7 elements of impurities wereCarbonation Process to Manufacture Lithium Carbonate from Lithium
.jpg)
Lithium Processing Battery Recycling Solutions
As a worldwide leader in the supply of lithium brine treatment technologies and chemical processing systems, Veolia Water Technologies helps lithium producers and recyclers meet the technical challenges associated with the rising Download scientific diagram Overview of main processing options for production of lithium carbonate from rock minerals from publication: Minerometallurgical processes for lithium recovery from Overview of main processing options for Lithium Processing Experience lithium chloride Solids handling equipment, including a centrifuge and dryer, were integrated into the overall process design • Lithium Chloride (LiCl) • Lithium Carbonate (Li 2 CO 3) • Lithium Hydroxide anhydrous and monohydrate (LiOH)Lithium Processing Capabilities Veolia Water TechExtensive work has gone into designing the most efficient and costeffective processing route for producing lithium hydroxide from ore We use nontoxic additives and our lowwaste process is designed to ensure that as much as possible of what comes out can be used commercially to support local industriesThe Process Germany's Lithium Hydroxide Production Route

Lithium handling Carmeuse Systems
During the evaporation process, a slurry of hydrated lime (Ca(OH) 2) is added to the brine to precipitate out unwanted elements, particularly magnesium and boron (as magnesium hydroxide and calcium boron salts)When lithium concentration reaches a certain point, the brine is pumped to a recovery facility to extract the metal, a process that usually includes the following stepsThe process is undertaken at atmospheric pressure and modest temperature, followed by a series of impurity removal steps at progressively higher pH levels and the subsequent precipitation of lithium carbonate The process contrasts with the far more energy intensive processing of spodumene concentrates, which requires high temperature Processing Technology Cornish Lithium PlcKBR has developed PureLiSM a unique lithium conversion and refining process to cater to the growing lithiumion battery demand for electric vehicles and stationary energy storage systems PureLi is capable of transforming a wide range of lithium feedstocks into batterygrade lithium carbonate or lithium hydroxide monohydrateKBR’s HighPurity Lithium Production TechnologyAfter the lithium brine solution is concentrated to the specifications you desire, it is transferred to the mixing tank Soda ash is added to lithium brine in order to precipitate lithium carbonate (Li₂CO₃)The solution is processed by the Filter Press where the lithium carbonate is captured between the plates, and the remaining liquid is dischargedLithiumion Battery Recycling Process Equipment MetChem

The Lithium Mining Process
2023年3月15日 Treated with sodium carbonate, known also as soda ash, to remove lithium carbonate Lithium carbonate is then washed and dried into end product This lithium mining process also tends to consume large quantities of fresh water This water is largely drawn from aquifers, rivers, wells, or other water sources used for drinking or irrigation