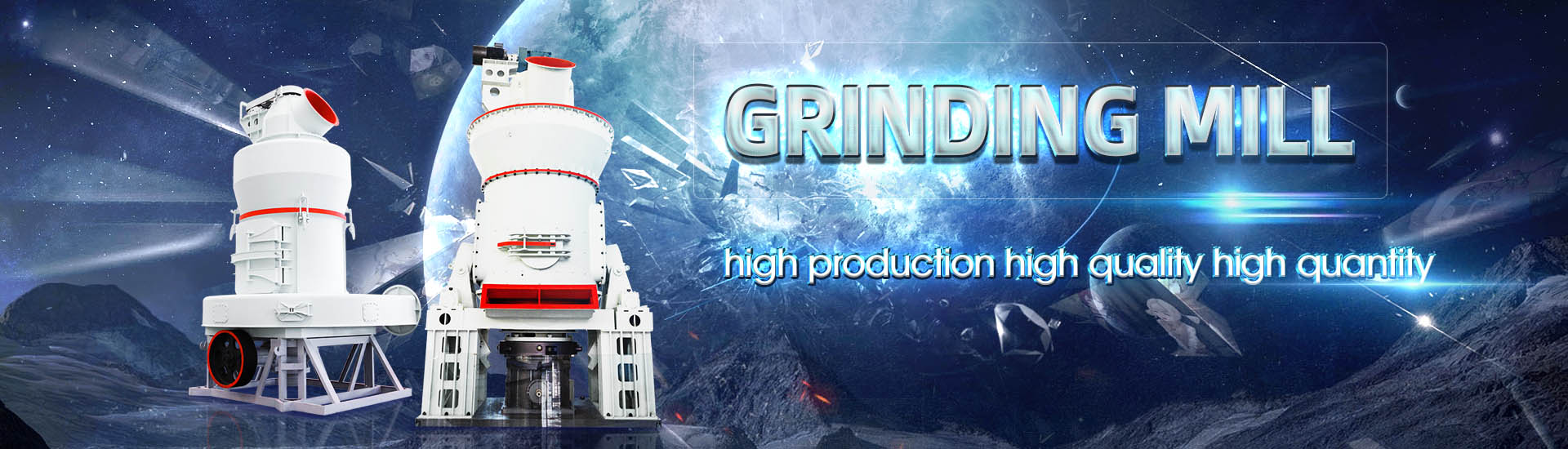
Central control of raw material vertical mill

Intelligent Control System Design for Vertical Mill Based on Data
Abstract—It is difficult to effectively control the vertical grinding process of raw materials due to its characteristics of strong coupling, nonlinearity and large hysteresis This paper proposes a 2020年5月1日 Vertical roller mill (VRM) is a largescale grinding equipment, which is used to grind raw materials from block/granule into powder Due to harsh production environment and A datadriven decisionmaking framework for online control of Mixed raw materials are fed using the feeding belt conveyer through feeding mouth along with feed pipe With the help of louver ring, a rising air current at the periphery is directed; while the PROCESS CONTROL FOR CEMENT GRINDING IN VERTICAL Vertical raw mills are widely used in the cement industry due to their high efficiency, low energy consumption, and compact design The Role of Vertical Raw Mills in Cement Production: 1 Grinding Limestone: The primary function of a vertical raw mill is to grind limestone, the main raw material in cement production, into a fine powderThe vertical raw mill: A key component in cement production

Raw Material DryingGrinding Cement Plant Optimization
Dry Grinding: Open circuit Ball mill, closed circuit Ball mill, vertical roller mill, Roll Press or Roll press in circuit with ball mill However, it would be seen that the most significant process and types used for raw material grinding operations in modern cement industry are: Process: Dry Closed circuit drygrinding Type of mill: Ball and Vertical raw mill is one kind of raw mill, generally used to grind bulk, granular, and powder raw materials into required cement raw meal in the cement manufacturing plantVertical raw mill is an ideal grinding mill that crushing, drying, grinding, Vertical raw mill Cement PlantFeeding Amount Control of Verticle Roller Mill Mainteining material laye thicknessr is the main content of the operation control The stability of the material layer is a prerequisite for safe operation of the verticle roller mill The amount of feed in the mill can be tested by 3 methods: Grinding roller limit device clearance;How to Improve Grinding Efficiency of Vertical Roller Mill2022年10月3日 This article was compiled as a result of practical work at PT Semen Baturaja (Persero) Tbk The focus of the discussion is on evaluating the performance of the vertical raw mill tool through the (PDF) ANALISA KINERJA ALAT VERTICAL RAW MILL PABRIK II PT

Optimizing Raw Mills Performance ; the Materials WAY
2019年6月22日 Introduction: Raw milling is one of the most important and integral component of cement production process; it is the stage which produces the most important intermediate product ieAdaptive Dynamic Programming in Raw Meal Fineness Control of Vertical Mill Grinding Process Based on Extreme Learning Machine Abstract Abstract: The grinding process of vertical mill raw meal in cement industry features nonlinear, strong coupling and long timedelay, which is difficult to model precisely and implement stable control for rawAdaptive Dynamic Programming in Raw Meal Fineness Control of Vertical Globally, cement plants are striving to improve their energy efficiency Therefore, it is critical for cement plant operations to increase the monitoring and control of a vertical raw mill energy process This technology has attracted the interest of the cement industry with its proven benefitAssessment of the thermodynamics efficiency of a cement vertical raw Group CCR tuban 12 mengendalikan dan mengkoordinasikan kegiatan pengoperasian Roller Vertical mill Tuban 12 secara terpusat dari central control room, agar peralatan beroperasi dengan lancar, efektif, efisien dan aman sesuai instruksi kerja (IK) dan rencana mutu sehingga menghasilkan produk dengan kuantitas dan kualitas sesuai dengan rencana yang ditetapkan Proses Raw Mill (Penggilingan Raw Material) 123dok
.jpg)
Vertical raw mill pradeep kumar PPT Free
2013年5月15日 Exception handling • 21 vertical roller mill vibration is too large: (1) Feed uneven, when the mixture into the vertical roller mill over the powder, the vertical roller mill's loading rate, leading to the vertical roller mill on the thin 2012年12月31日 a Distributed Control System(DCS) of cement raw materials is presented for the vertical roller mill by the application of ABB's IndustrialIT The results demonstrate the practical application of Design and Realization Of Roller Mill Control 2016年9月1日 In contrast, increasing the separator speed from 60 to 80 rpm at a constant grinding pressure results in a reduced raw material production rate from 240,000 kg/h to 230,000 kg/h and which Operational parameters affecting the vertical roller mill For the operation of the Raw Mill (Vertical Roller Mill), existing system was 2fan circuit The existing system consisted of Gas Conditioning Tower (GCT) followed by Electrostatic Precipitator (ESP) for the control of particulate emissions from the kiln and raw millRaw Mill – Kiln Application in Cement Industry Thermax
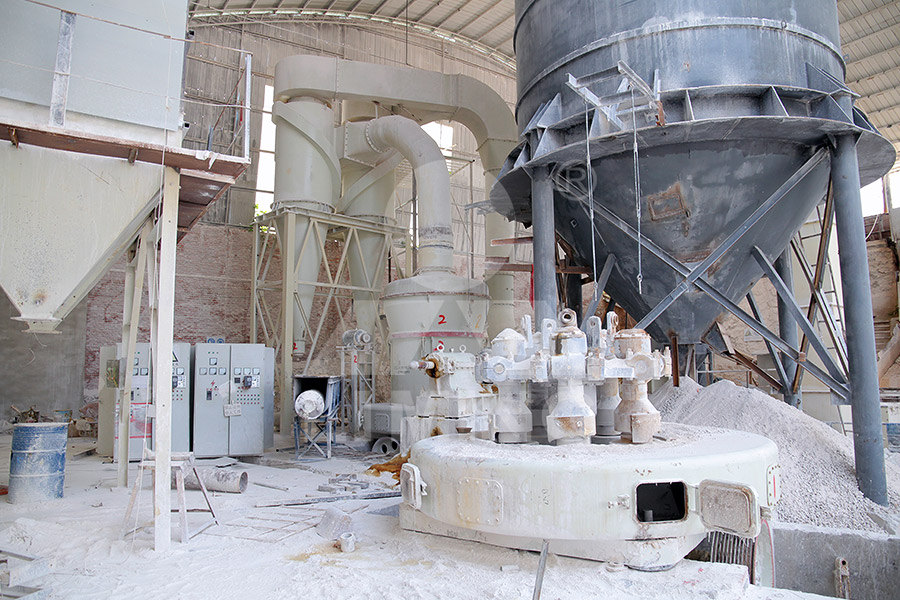
A datadriven decisionmaking framework for online control of vertical
2020年3月1日 Vertical roller mill (VRM) is a largescale grinding equipment, which is used to grind raw materials from block/granule into powder Due to harsh production environment and inconsistent raw 2021年1月1日 Stacking Reclaiming of Raw material: Swing type stacker Reclaimer: Limestone other raw material are stored in open area into a longitudinal storage unit called stockpile through Stacker These are then extracted transversely from the stockpile through reclaimer: 3: Raw Meal Grinding Homogenization: Grinding Mill Vertical Roller Mill Review on vertical roller mill in cement industry its 2017年9月11日 Due to the compact design and material transportation system of vertical roller mills (VRM), some important streams (total mill feed and discharge, dynamic separator feed and reject) remain in the (PDF) Performance Evaluation of Vertical Roller Mill in Cement Providing a comprehensive guide to the entire cement production process from raw material Finish mill – 12 Cement – 13 Quality control – 14 Packing and distribution – 15 Emission abatement (dust, NO x, SO 2, etc) – 16 mentioned in Chapter 3 for dry raw milling – ball mills, vertical roller mills, roll presses, The Cement Plant Operations Handbook International Cement
.jpg)
Everything you need to know about cement Materials Preparation and Raw
material in the mill is not affected by the material moisture, although some loss in grinding efficiency was observed when the fresh material at the mill inlet had moisture of more than 68% The Horomill used as a raw mill is claimed to combine the effectiveness of the vertical roller mill and the roller press with a very low pressure drop in the circuit2020年5月1日 Vertical roller mill (VRM) is a largescale grinding equipment, which is used to grind raw materials from block/granule into powder Due to harsh production environment and inconsistent raw material quality, VRM requires timely regulationA datadriven decisionmaking framework for online control of vertical 2021年1月22日 In the whole process of cement production, the electricity consumption of a raw material mill accounts for about 24% of the total Based on the statistics of the electricity consumption of the raw A Survey and Analysis on Electricity Consumption of Raw Material Mill Mill System Operate Safety When the raw material is running in the vertical mill, the drying heat source of the material comes from the hot gas at the kiln tail Therefore, when the vertical mill is operated, the control of the inlet and outlet Important Operation Tips For Cement Vertical Mill

PROCESS OPTIMISATION FOR LOESCHE GRINDING PLANTS
– Control Parameters for Loesche Vertical Mills Variable clocking • 50 / 100 ms: Signal detection • 1 second – 10 minutes: Signal evaluation • Material grindability • Material temperature • Material moisture • Mixture composition • Composition of raw material • Grinding roller wear • Fineness (Blaine) or residue (VOA)The vertical mill allows the installation area to be decreased, leading to a reduction of construction cost 3 Easy operation Material feed, grinding force, air volume and separator feed can be adjusted through a remote control system, which makes the operation easier 4 UBE Vertical Mill UBE Machinery Corporation, LtdOptimizationofVerticalRawMillOperationpdf Free download as PDF File (pdf), Text File (txt) or view presentation slides online The document discusses optimization and operation of vertical roller mills (VRMs) Key points include: 1) Continuously monitor and adjust process parameters to find the optimum operating conditions of highest capacity and lowest power consumptionOptimization of Vertical Raw Mill Operation PDFThe mill will not run at this time The feed group is stopped when there is sufficient material in the mill The material is then distributed in the mill manually with a shovel When the mill is too full the mill main drive can be overloaded and it will be necessary to remove some material from the mill Preparations for mill start upPROCESS TRAINING for operators of Vertical RAW Mills
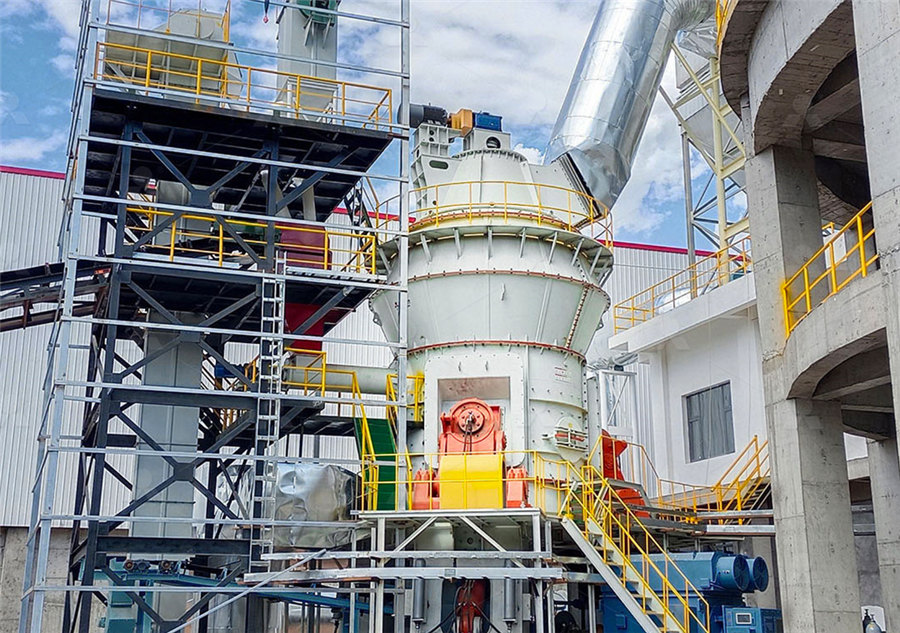
Intelligent Control System Design for Vertical Mill Based on Data
accurately establish the model of raw material grinding process in vertical mill to optimize the control of key parameters during the process[5] The model of raw material grinding process for vertical mill has been studied indepth both at home and abroad Cai X[6] established a soft sensing model of the materialThis mill, designated the LM 606 has a grinding table with a diameter of 600 m and an installed drive rating of 4 650 kW Even with poor grindability of the raw material this mill is expected to produce an output of 640 t/h at a raw meal fineness corresponding to a residue of about 15 % on a 009 mm sieve The first Loesche mill equipped with sixRedundancy and interchangeability – large vertical roller mills 2024年11月1日 Numerical Study of Flow Field and Particle Motion Characteristics on Raw Coal Vertical Roller Mill Circuits the MMLM2550 VRM and the central control platform Changing the thickness of helical guide blade had little effect on the outlet ventilation and pressure drop of the mill Supplementary Material Figure S2 and S3 Numerical Study of Flow Field and Particle Motion Characteristics Roller; Roller pada Vertical Raw Mill berfungsi sebagai media penggilingan material ke meja Roller Vertical Raw Mill berjumlah empat buah dengan diameter 2,5 mANALISA KINERJA ALAT VERTICAL RAW MILL PABRIK II PT
.jpg)
The vertical raw mill: A key component in cement production
Vertical raw mills are widely used in the cement industry due to their high efficiency, low energy consumption, and compact design The Role of Vertical Raw Mills in Cement Production: 1 Grinding Limestone: The primary function of a vertical raw mill is to grind limestone, the main raw material in cement production, into a fine powderDry Grinding: Open circuit Ball mill, closed circuit Ball mill, vertical roller mill, Roll Press or Roll press in circuit with ball mill However, it would be seen that the most significant process and types used for raw material grinding operations in modern cement industry are: Process: Dry Closed circuit drygrinding Type of mill: Ball and Raw Material DryingGrinding Cement Plant OptimizationVertical raw mill is one kind of raw mill, generally used to grind bulk, granular, and powder raw materials into required cement raw meal in the cement manufacturing plantVertical raw mill is an ideal grinding mill that crushing, drying, grinding, Vertical raw mill Cement PlantFeeding Amount Control of Verticle Roller Mill Mainteining material laye thicknessr is the main content of the operation control The stability of the material layer is a prerequisite for safe operation of the verticle roller mill The amount of feed in the mill can be tested by 3 methods: Grinding roller limit device clearance;How to Improve Grinding Efficiency of Vertical Roller Mill
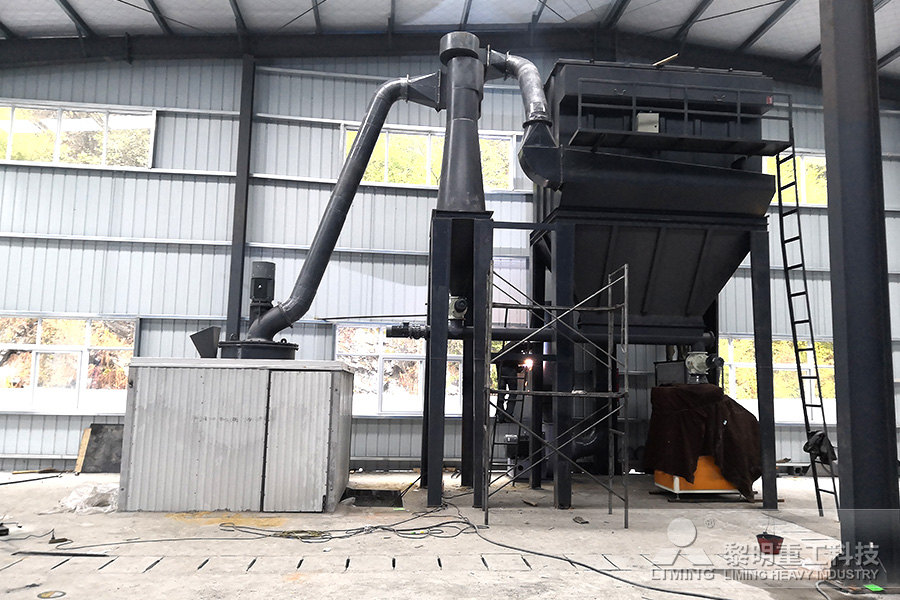
(PDF) ANALISA KINERJA ALAT VERTICAL RAW MILL PABRIK II PT
2022年10月3日 This article was compiled as a result of practical work at PT Semen Baturaja (Persero) Tbk The focus of the discussion is on evaluating the performance of the vertical raw mill tool through the 2019年6月22日 Introduction: Raw milling is one of the most important and integral component of cement production process; it is the stage which produces the most important intermediate product ieOptimizing Raw Mills Performance ; the Materials WAYAdaptive Dynamic Programming in Raw Meal Fineness Control of Vertical Mill Grinding Process Based on Extreme Learning Machine Abstract Abstract: The grinding process of vertical mill raw meal in cement industry features nonlinear, strong coupling and long timedelay, which is difficult to model precisely and implement stable control for rawAdaptive Dynamic Programming in Raw Meal Fineness Control of Vertical Globally, cement plants are striving to improve their energy efficiency Therefore, it is critical for cement plant operations to increase the monitoring and control of a vertical raw mill energy process This technology has attracted the interest of the cement industry with its proven benefitAssessment of the thermodynamics efficiency of a cement vertical raw
.jpg)
Proses Raw Mill (Penggilingan Raw Material) 123dok
Group CCR tuban 12 mengendalikan dan mengkoordinasikan kegiatan pengoperasian Roller Vertical mill Tuban 12 secara terpusat dari central control room, agar peralatan beroperasi dengan lancar, efektif, efisien dan aman sesuai instruksi kerja (IK) dan rencana mutu sehingga menghasilkan produk dengan kuantitas dan kualitas sesuai dengan rencana yang ditetapkan