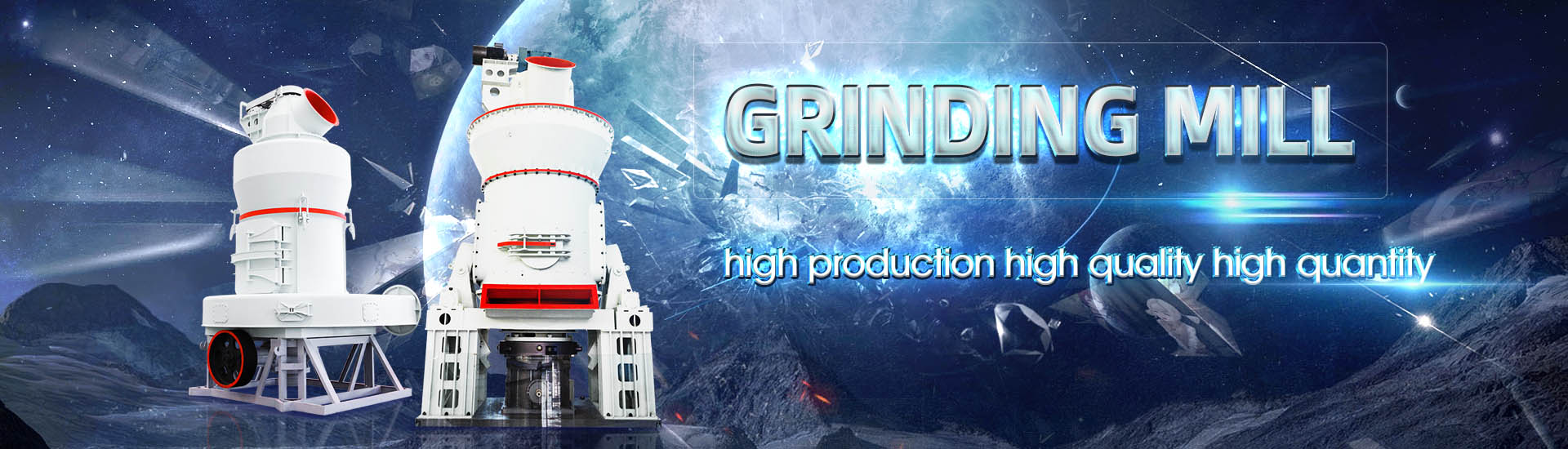
Qingbai Ni Ironmaking Plant
.jpg)
Plantbyplant decarbonization strategies for the global steel
2023年9月20日 Here, based on a newly developed database of individual iron and steel facilities worldwide, we explore the distinct differences in agetocapacity ratio and emissions intensity of primary2023年9月20日 Our results provide a detailed picture of CO 2 emission patterns associated with production processing of iron and steel plants, illustrating the decarbonization pathway to the Global iron and steel plant CO2 emissions and carbon NaturePedal to the Metal is an annual survey of the current and developing global iron and steel plant fleet The report examines the status of the iron and steel sector compared to global Pedal to the Metal 2024 Global Energy Monitor2019年7月19日 Coke making is responsible for the 10% of the energy consumption of the integrated ironmaking route; it is a materialintensive process, and it consumes enormous Coke Making: Most Efficient Technologies for Greenhouse
.jpg)
Review Article A review on CO2 mitigation in the Iron and Steel
2021年4月1日 In the Iron and Steel industry, the majority of the research to mitigate CO 2 emissions focuses on applying post combustion capture to the blast furnace (ie, applying 2019年1月1日 These factors have contributed to the development of alternative technologies of ironmaking, of which Direct Reduction (DR) processes are expected to emerge as preferred A review of ironmaking by direct reduction processes: Quality 2019年7月25日 Blast furnace (BF) ironmaking is the key production process in steel manufacturing The development of lowcarbon ironmaking technology based on the BF is an Review of green and lowcarbon ironmaking technology2023年11月10日 These factors have contributed to the development of alternative technologies of ironmaking, of which Direct Reduction (DR) processes are expected to emerge as preferred A REVIEW OF IRONMAKING BY DIRECT REDUCTION PROCESSES:
.jpg)
Decarbonizing China’s iron and steel industry from the supply and
2021年9月15日 Analyze lowcarbon pathways for Chinese iron steel industry towards carbon neutrality Both the supplyside and demandside contributions to decarbonization are 2019年7月19日 The traditional integrated ironmaking plant is based on blast furnace operations for the reduction of iron oxides to cast iron Seventy percent of the steel produced globally is Blast Furnace: Most Efficient Technologies for Greenhouse 2021年4月1日 In the Iron and Steel industry, the majority of the research to mitigate CO 2 emissions focuses on applying post combustion capture to the blast furnace (ie, applying mature carbon capture to the largest emitting source of the plant) [7]One of the best options within this topic is to combine vacuum pressure swing adsorption (VPSA) with top gas recycling oxygen Review Article A review on CO2 mitigation in the Iron and Steel 2023年11月3日 In recent years, the concept of green, lowcarbon and clean energy consumption has been deeply rooted in the hearts of the people, and countries have actively advocated the use of new energy In the face of Review on the Application and Development of Biochar
.jpg)
The Nickel Production Methods from Laterites and the
Primary world nickel production in 2020 was 24307 kt Ni; 69% (16777 kt) of them came from oxidized nickel ores (laterites) and 31% from sulfides Productionwise, 877% of the 16777 kt came from pyrometallurgical and Ni strips Diamond synthesis Antiseize lubricant Chemicals Powder Metallurgy Nickel plant in the 1920s and, in 1943, commercial nickel powder production began In 1973, Inco opened a second carbonyl plant in Sudbury, Canada, the site of its major nickel mining operations [5]The changing landscape of carbonyl iron and nickel powder production2020年7月9日 PDF A new route for making steel from iron ore based on the use of hydrogen to reduce iron oxides is presented, detailed and analyzed The main Find, read and cite all the research you need (PDF) Hydrogen Ironmaking: How It Works ResearchGate2021年3月10日 24 Environmental Effect of Pb and Zn Impurities In steel wastes, the main constituents that are classified under the hazardous classification are potentially toxic elements (eg, Pb and Zn) [] and alkali metals (eg, K) because of their concentration and potential environmental impact [] []Large amounts of BF dust are landfilled, some of which contain Ironmaking Process Encyclopedia MDPI
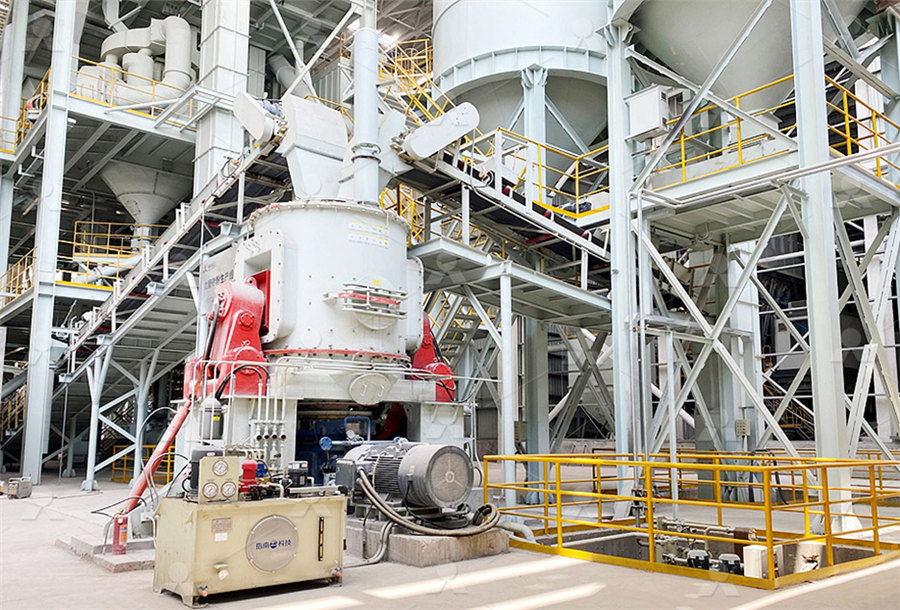
A REVIEW OF IRONMAKING BY DIRECT REDUCTION PROCESSES:
2023年11月10日 These factors have contributed to the development of alternative technologies of ironmaking, of which Direct Reduction (DR) processes are expected to emerge as preferred alternatives in the future2019年1月1日 Blast furnace ironmaking requires separate coke making and sintering plants and often has reduced operating flexibility (Lu, Pan and Zhu, 2015) Coking coal is regarded as premium quality coal that attracts relatively higher cost and there are concerns over the limited reserves (Chukwuleke, Iiuju and Chukwujekwu, 2009)A review of ironmaking by direct reduction processes: Quality Download scientific diagram Parts of an ironmaking blast furnace plant from publication: Prediction and Explanation Models for Hot Metal Temperature, Silicon Concentration and Cooling Capacity Parts of an ironmaking blast furnace plant ResearchGate2023年9月20日 The highly energyintensive iron and steel industry contributed about 25% (ref 1) of global industrial CO2 emissions in 2019 and is therefore critical for climatechange mitigation Despite Global iron and steel plant CO2 emissions and carbon Nature
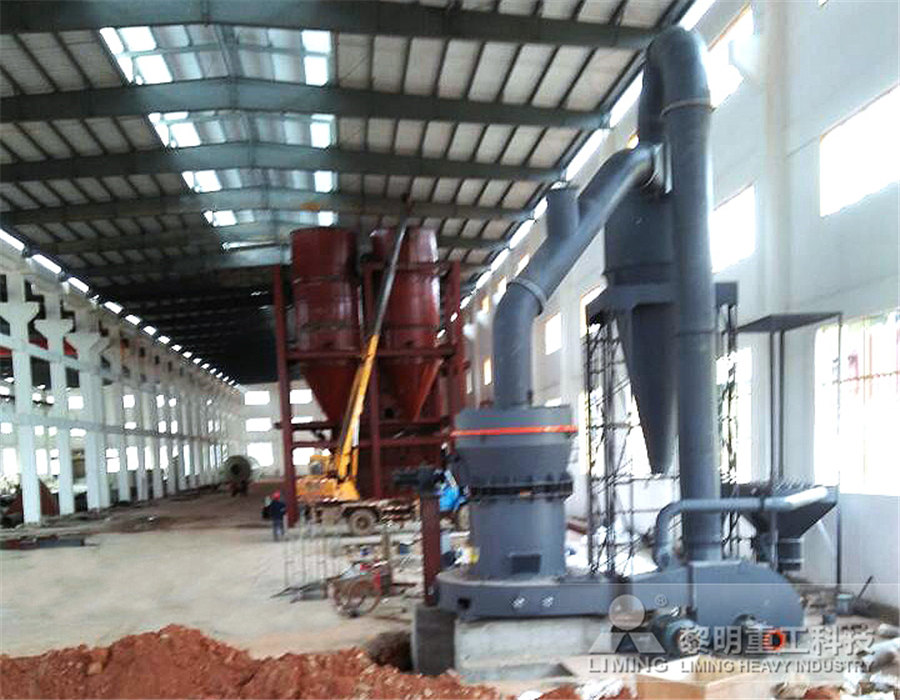
Expert Systems Controlling the Iron Making Process in
2010年1月1日 13 Expert systems Medical diagnosis systems were developed to support doctors in their work (eg MYCIN, Buchanan Shortliffe, 1984)The underlying ideas were adopted by the iron making industry and similar 2016年9月3日 Sinter plants contribute the largest share of pollutant emissions in the ironmaking plants and are the second largest emitter after municipal solid waste (MSW (NMVOCs) and PCDD/Fs but more heavy metals (such as Pb, Cd, Hg, Cr, Cu, Ni and Zn) and other hazardous nonmetal elements (such as As and Se) per unit mass of Risk Assessment and Control of Emissions from Ironmaking2019年2月26日 This content was downloaded from IP address 19110110598 on 26/02/2019 at 17:21(PDF) Recent Development of Energysaving 2019年2月6日 Studied area Figure 1 displays the flow sheet for the direct reduction ironmaking plant used in this study In this process, iron oxide pellets reduced to sponge iron in a gasbased shaft furnace The pellets are introduced at the top of the furnace through a hopper, and as the pellets descend by gravity flow, it is heatedReduction of CO2 emissions and energy consumption by
.jpg)
Selection of Ironmaking Technology: Principles and Risks
2013年7月2日 Due of limited availability of scrap, a steel company located in the European Part of Russian Federation, needed to review the available and emerging ironmaking technologies for the production of iron units for new minimills [capacity ~1 million tonne per annum (Mtpa) crude steel each] at two different cities (City 1 and City 2) as well as at their existing steel plants8 Digitalization and Automation: Ironmaking in the Industry 40 Era The integration of digital technologies and automation is reshaping ironmaking operations From advanced process control systems to predictive maintenance algorithms, digital solutions enhance efficiency, safety, and decisionmaking in steel plantsFrom Ore to Alloy: Navigating Ironmaking in Modern Steel 2016年4月1日 Microstructures displayed by the thermally treated for 10 minutes at 1200° C (A), 1300° C (B), 1400° C (C), 1500° C (D) and for 20 minutes at 1500° C (E) samplesUse of DRI/HBI in ironmaking and steelmaking furnaces2024年3月17日 Alternative ironmaking process; Lower CO2 emissions than traditional methods: Requires natural gas; Higher production costs: Continuous Casting: Improved yield and quality; Reduced energy consumption and waste: High initial investment; Maintenance is complex: Rolling Process: Versatility in producing various steel sections; Efficient in mass A Visual Guide: Steel Making Process Chart Cabaro Group
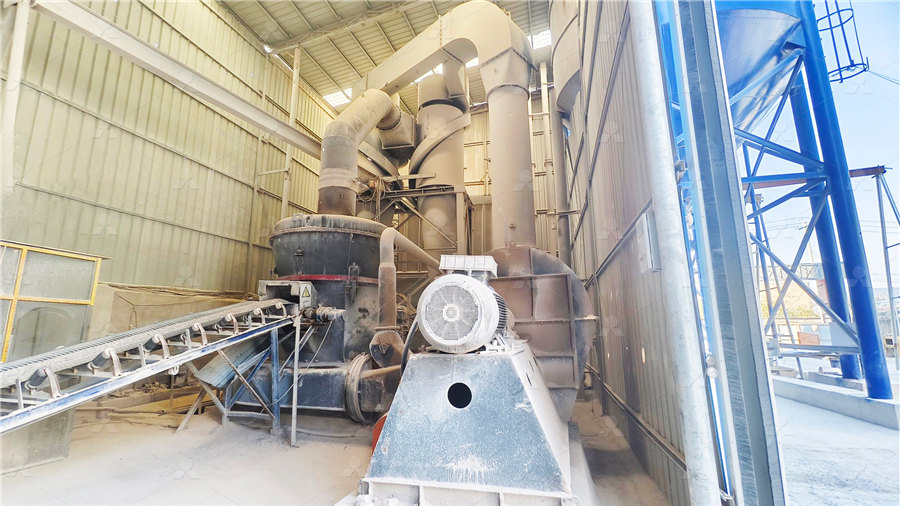
(PDF) Nickel Laterite Smelting Processes and Some ResearchGate
2019年9月3日 period of time (~2 years), plants producing lowgrade ferronickel grew to more than 300 The Ni grade in the concentrate was reported to increase from 233% to 948% with the use2017年10月17日 Smelting Reduction Figure 2: The smelt reduction vessel (SRV) is the core technology component of the Hismelt process Source: RioTinto While years of ironmaking technology innovations have optimized blast furnace productivity, two alternative processes—smelting reduction and direct iron reduction— are growing in adoption The Ironmaking 101 – From Ore to Iron with Smelting and Direct Iron 21 Introduction of Modern Ironmaking Technology Historically, iron was produced in Japan by a smallscale ironmaking method called the tatara 92) process with iron sand as the main raw material Use of the blast furnace Ironmaking Technology for the Last 100 Years: 2019年3月1日 This paper evaluates the use of portable xray fluorescence (pXRF) on glazes and pastes for sourcing Chinese porcelains from the 12 th13 th century Java Sea Shipwreck (JSW) collection at the Field Museum Three types of qingbai (bluishwhite) wares from the JSW collection were chosen for pXRF analysis Samples from four kiln complexes in Sourcing qingbai porcelains from the Java Sea Shipwreck:
.jpg)
Global iron and steel plant CO emissions and carbon neutrality
1 1 Global iron and steel plant CO 2 emissions and carbon 2 neutrality pathways 3 Tianyang Lei1, Daoping Wang2, Xiang Yu3, 4, Shijun Ma5, Weichen Zhao5, Can Cui1, Jing Meng5, Shu 4 Tao6, Dabo Guan1, 5, * 5 1 Department of Earth System Sciences, Tsinghua University, Beijing, , China 6 2 Department of Computer Science and Technology, University of 2021年12月20日 In July 2020, the energy company EWE and its subsidiary swb, and the steel constructor ArcelorMittal signed an intent letter for the cooperation of the “HyBit—Hydrogen for Bremen's industrial transformation” project; an electrolysis plant with a capacity of up to 24 MW is expected to be built at the Mittelsbüren power plant site in the first stage, with plans to use a Hydrogen direct reduction (HDR) in steel industry—An material Sinter plants are usually located within the integrated steelworks, because sinter can break up with excessive handling, and because of the availability of coke breeze which supplies the heat required for the process As ironmaking technology has developed, and the efficiency demanded of modem plant hasThe Making of Iron Steel SEAISI2019年7月19日 Size affects BF efficiency, with smaller furnaces in China emitting up to 25% more CO 2 than large ones The CO 2 intensity for Chinese BFs with a capacity >3000 m 3 is 109 tCO 2 /t compared to 131 tCO 2 /t for those with a capacity of 300–999 m 3A larger BF is usually more efficient because the heat losses are lower (larger surface/volume ratio) and it is Blast Furnace: Most Efficient Technologies for Greenhouse
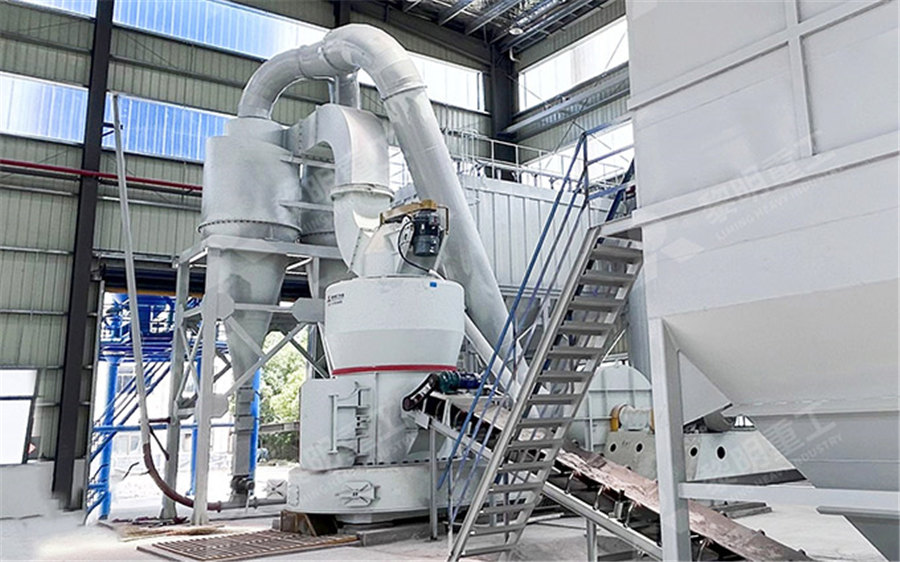
Cocombustion of semicoke and coal in an industry ironmaking
2019年12月1日 Lowrank coals can be upgraded to semicoke, and potentially used to partly replace expensive metallurgical coals in pulverised coal injection (PCI) in ironmaking blast furnaces (BFs)2023年10月9日 Comprehensive control of greenhouse gas emissions and response to climate change are concerns of countries around the world to protect living homes The steel industry is responsible for over 10% of global CO2 emissions, with approximately 80% of these emissions coming from the ironmaking process Great efforts have been made in both blast furnace (BF) Development and Problems of Fluidized Bed Ironmaking Process: BF/BOF vs EAF Comparing the properties of iron and steelmaking technologies: BF/BOF has consumption of equipment and emissions 24 times higher, and this requires more energy water consumption Moreover, it needs higher energy for production due to the cokemaking and sintering processesUse of DRI and HBI in steel making plants Arij TradingLearn about cuttingedge technologies for ironmaking and automation provided by Primetals Technologies ᐅ Over 300 successful ironmaking projects worldwide EN Corex plant emissions contain only insignificant amounts of NOx, SO2, dust, phenols, sulfides, and ammonia, so emission values come in below the maximum values permitted The World Leader in Ironmaking Solutions Primetals Technologies
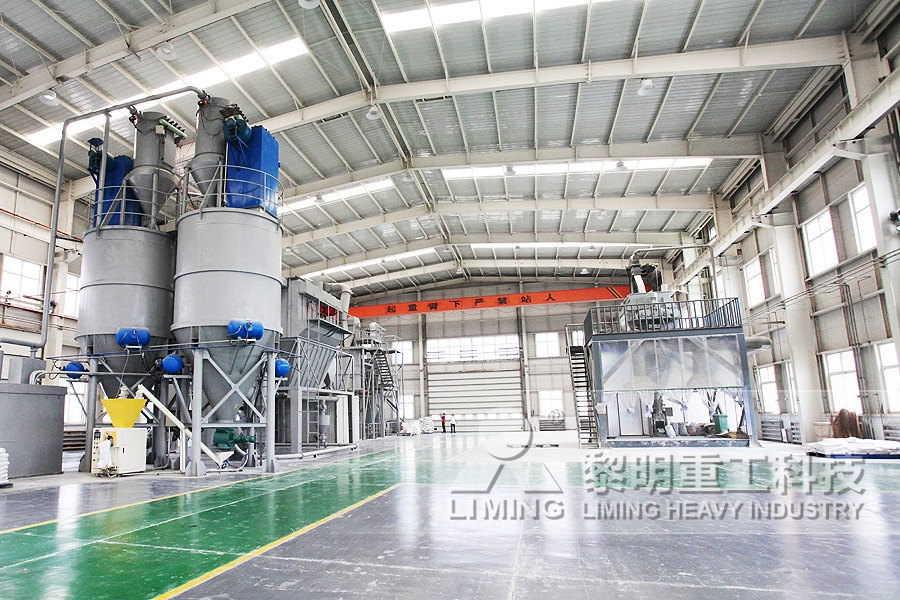
Review Article A review on CO2 mitigation in the Iron and Steel
2021年4月1日 In the Iron and Steel industry, the majority of the research to mitigate CO 2 emissions focuses on applying post combustion capture to the blast furnace (ie, applying mature carbon capture to the largest emitting source of the plant) [7]One of the best options within this topic is to combine vacuum pressure swing adsorption (VPSA) with top gas recycling oxygen 2023年11月3日 In recent years, the concept of green, lowcarbon and clean energy consumption has been deeply rooted in the hearts of the people, and countries have actively advocated the use of new energy In the face of Review on the Application and Development of Biochar Primary world nickel production in 2020 was 24307 kt Ni; 69% (16777 kt) of them came from oxidized nickel ores (laterites) and 31% from sulfides Productionwise, 877% of the 16777 kt came from pyrometallurgical and The Nickel Production Methods from Laterites and the Ni strips Diamond synthesis Antiseize lubricant Chemicals Powder Metallurgy Nickel plant in the 1920s and, in 1943, commercial nickel powder production began In 1973, Inco opened a second carbonyl plant in Sudbury, Canada, the site of its major nickel mining operations [5]The changing landscape of carbonyl iron and nickel powder production
.jpg)
(PDF) Hydrogen Ironmaking: How It Works ResearchGate
2020年7月9日 PDF A new route for making steel from iron ore based on the use of hydrogen to reduce iron oxides is presented, detailed and analyzed The main Find, read and cite all the research you need 2021年3月10日 24 Environmental Effect of Pb and Zn Impurities In steel wastes, the main constituents that are classified under the hazardous classification are potentially toxic elements (eg, Pb and Zn) [] and alkali metals (eg, K) because of their concentration and potential environmental impact [] []Large amounts of BF dust are landfilled, some of which contain Ironmaking Process Encyclopedia MDPI2023年11月10日 These factors have contributed to the development of alternative technologies of ironmaking, of which Direct Reduction (DR) processes are expected to emerge as preferred alternatives in the futureA REVIEW OF IRONMAKING BY DIRECT REDUCTION PROCESSES: 2019年1月1日 Blast furnace ironmaking requires separate coke making and sintering plants and often has reduced operating flexibility (Lu, Pan and Zhu, 2015) Coking coal is regarded as premium quality coal that attracts relatively higher cost and there are concerns over the limited reserves (Chukwuleke, Iiuju and Chukwujekwu, 2009)A review of ironmaking by direct reduction processes: Quality
.jpg)
Parts of an ironmaking blast furnace plant ResearchGate
Download scientific diagram Parts of an ironmaking blast furnace plant from publication: Prediction and Explanation Models for Hot Metal Temperature, Silicon Concentration and Cooling Capacity 2023年9月20日 The highly energyintensive iron and steel industry contributed about 25% (ref 1) of global industrial CO2 emissions in 2019 and is therefore critical for climatechange mitigation Despite Global iron and steel plant CO2 emissions and carbon Nature