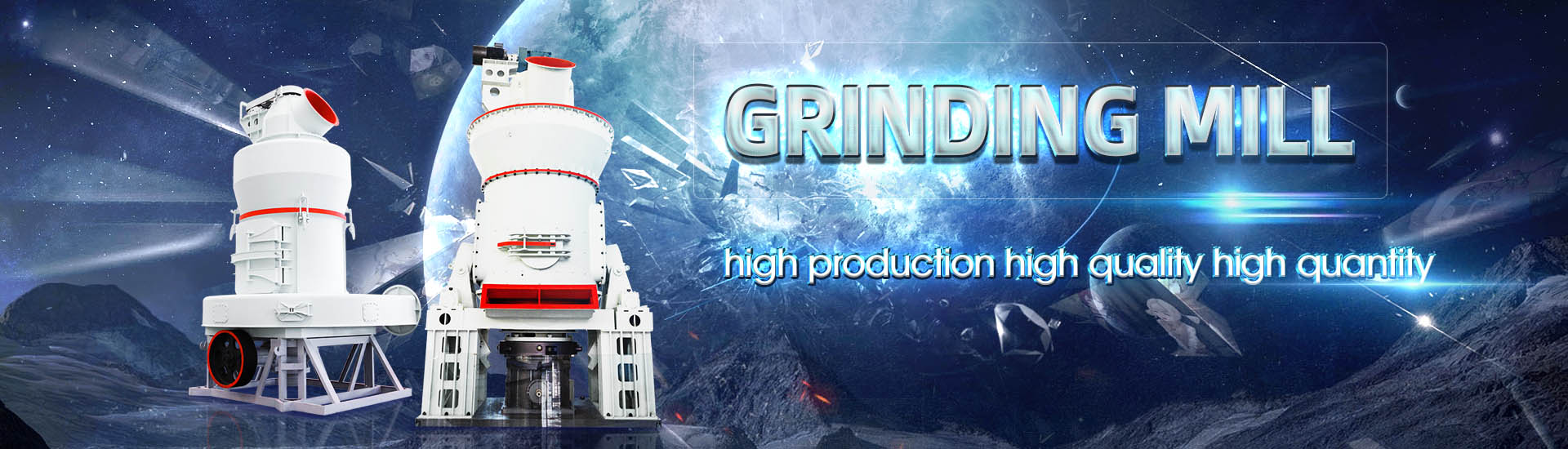
Cement plant grinding station pyrolysis carbon black room energy saving and emission reduction
.jpg)
An overview of energy savings measures for cement industries
2013年3月1日 In this paper, energy saving measures in the cement industry, such as energyefficiency measures for the preparation of raw materials, production of clinker, and the 2024年6月1日 Carbon Capture and Storage (CCS) is a promising technology for reducing carbon emissions in cement plants, which are significant contributors to greenhouse gas Decarbonising cement and concrete production: Strategies, experience in the cement sector and focus on specific technical measures that could be implemented by cement plants to reduce their operating costs and improve their carbon IMPROVING THERMAL AND ELECTRIC ENERGY EFFICIENCY AT 2021年9月20日 Methane pyrolysis is an emerging technology to produce lowercarbon intensity hydrogen at scale, as long as the coproduced solid carbon is permanently captured Partially Sequestration of solid carbon in concrete: A largescale enabler of
.jpg)
Benchmarking of Energy Consumption and CO2 Emissions in
2024年2月2日 The benchmarking analysis quantified the plant’s energy intensity and CO 2 emissions per tonne of cement produced across key process stages including raw material 2024年3月28日 Cement production is a main source of carbon emissions Decarbonization options exist, but their climate change mitigation potential, feasibility and environmental Paving the way for sustainable decarbonization of the European 2016年10月5日 In this chapter an introduction of widely applied energyefficient grinding technologies in cement grinding and description of the operating principles of the related EnergyEfficient Technologies in Cement Grinding IntechOpen2022年12月1日 Raw meal preparation, clinker manufacturing, and cement grinding recorded the highest thermal energy savings of 430 GJ/t, 24 GJ/t, and 029 GJ/t, respectively Gravitytype Review on energy conservation and emission reduction
.jpg)
Improving thermal and electric energy efficiency at cement plants
This report provides a summary of international best practice experience in the cement sector and focuses on specific technical measures that could be implemented by 2024年1月1日 In this study, the production behavior, characters, and mechanism of carbon black from pyrolysis of natural rubber (NR), butadiene rubber (BR), and styrenebutadiene rubber (SBR) were investigated The yield of carbon black was increased from 208%–244% to 479%–567% with the increase of pyrolysis temperature from 1100 to 1300°CCarbon black production characteristics and mechanisms from pyrolysis 2021年11月3日 Through routine energysaving monitoring, energy audit, energy efficiency benchmarking, internal audit, organizations’ energy consumption measurement, test and energy balance statistics, management review, selfevaluation, energysaving technical renovation, energysaving assessment, and other measures, we can improve the energy management Energy Conservation and Emission Reduction SpringerLink2023年12月20日 The demand for production of cements is ever increasing to meet the infrastructure development globally The energy and emission factors available for cements in most of the life cycle assessment (LCA) databases may not exactly suit for all the geographical locations The main challenge in Indian scenario is the absence of database for LCA study Study on energy use and carbon emission from manufacturing of
.jpg)
Carbon black and hydrogen production process analysis
2020年9月25日 Radiation from the plasma torch, as well as heat convection from the plasma gas, provides enough energy for the pyrolysis of hydrocarbons Temperature is the important parameter in cracking reactions [38]After the conversion of hydrocarbons into carbon black and hydrogen, a waste heat recovery system takes advantage of the heat of the products to 2021年11月30日 The second type of classification is based on the reaction scale and reactor type/size Laboratory scale heattreatment can be performed in a tube furnace, small reactors or chambers that can facilitate a controlled environment (eg inert gas or vacuum) [9, 11, 18, 63]In some cases, the size of the precursor sample may be extremely small (micro or even nano A comprehensive review of the pyrolysis process: from carbon 2011年5月1日 The typical electrical energy consumption of a modern cement plant is about 110–120 kWh per tonne of cement [19] The main thermal energy is used during the burning process, while electrical energy is used for cement grinding [20] Fig 1 shows electrical and thermal energy flow in a cement manufacturing processA critical review on energy use and savings in the cement industries1 1 Introduction As US manufacturers face an increasingly competitive global business environment, they seek opportunities to reduce production costs without negatively affecting product yield or qualityEnergy Efficiency Improvement and Cost Saving Opportunities for Cement
.jpg)
Chemical engineering solution for carbon neutrality in cement
2024年3月1日 Analysis along the carbon footprint of the cement production reveals processrelated CO 2 emissions from the decomposition of limestone (CaCO 3) (Eq 1) in the precalciner account for more than 60 % of total emissions and energyrelated CO 2 emissions from the combustion of fossil fuel for maintaining high temperatures of rotary kiln (1,450 °C1,500 °C) 2021年5月10日 They also estimated the cumulative costeffective fuel savings at 1029 PJ with a corresponding decrease in CO 2 emission of 97 Mt Tesema and Worrell (2015) estimated that in the 8 cement plants operating in Ethiopia in 2010, the potential costeffective electricity savings could reach 11 GWh with fuel savings of 12 PJ, resulting in a 01 Mt reduction in CO 2 Bottomup analysis of energy efficiency improvement and CO2 emission 2022年10月15日 “Saving resources and protecting the environment” is China's basic and national policy, and energy conservation is the key support in CO 2 emissions peaking and carbon neutrality China's 11th FiveYear Plan (2006–2010) for the first time set a 20 % reduction in energy consumption per unit of GDP as a target [6]In fact, China's energy intensity fell by Does energysaving and emission reduction policy affects carbon 2024年5月1日 Cement is a critical building material that can significantly contribute to driving future demand for infrastructure with an increase in the global population (GCCA, 2022)China's cement production was 236 billion metric tons in 2021, accounting for 56 % of the world's production (DC, 2009; CMIIT, 2022; USGS, 2022)Coal consumption in the cement industry Carbon and air pollutant emissions forecast of China's cement
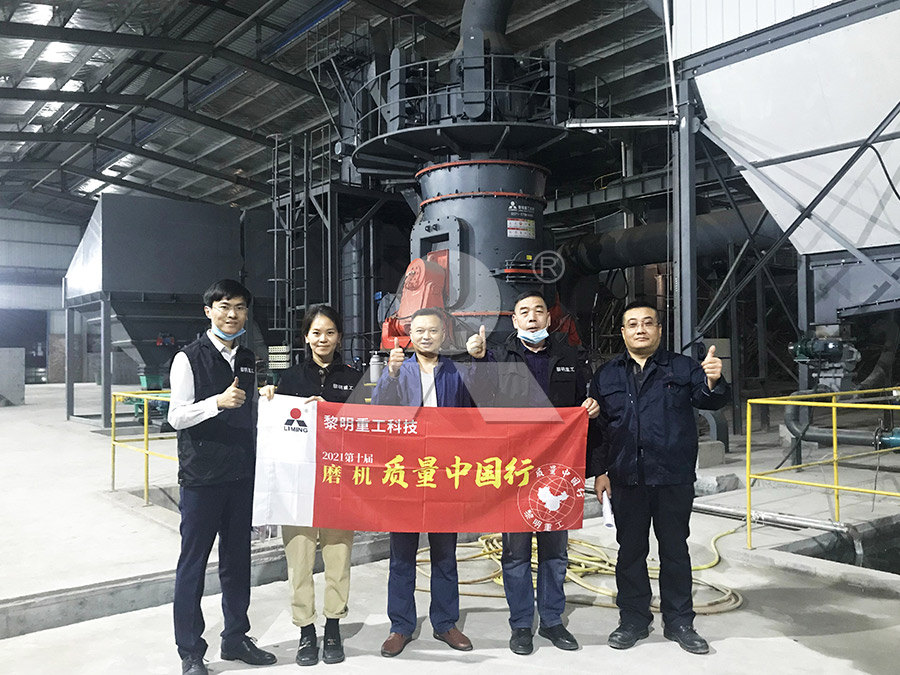
Global CO2 emissions from cement production,
Abstract Global production of cement has grown very rapidly in recent years, and, after fossil fuels and landuse change, it is the thirdlargest source of anthropogenic emissions of carbon dioxide The availability of the required 2023年3月6日 Thermal pyrolysis of waste tires is an industrially beneficial method for material and energy recovery Pyrolytic carbon black (CBp) is considered to be the secondary main product of this process In the present study, an ecofriendly and economically feasible autoclave reactorbased thermal pyrolysis method was employed for the pyrolysis of waste tire tread Recycling of waste tire by pyrolysis to recover carbon black: an 2016年10月18日 The steel industry is an energyintensive and CO 2intensive industry and the greenhouse gas (GHG) emission in the steel industry was more than 295 billion tons in 2012, which faces the great challenge of energy saving and CO 2 emission reduction in the context of global warming The heat recovery from high temperature slags (1450–1650 °C) from the Energy Saving and Emission Reduction from the Steel Industry: 2020年5月14日 Cement acts as the binder between aggregates (fine and coarse rocks) in the formation of concrete While cement makes up only a small percentage of the mix (approximately 12 percent by volume), it is almost exclusively responsible for the resulting CO 2 emissions In the cementmanufacturing process, raw materials are heated to high temperatures in a kiln in a Laying the foundation for zerocarbon cement McKinsey
.jpg)
Cement Technology Roadmap: Carbon Emissions Reductions
The cement energy technology roadmap outlines a possible transition path for the industry to make continued contributions towards a halving of global CO2 emissions by 2050 As part of this contribution, this roadmap estimates that the cement industry could reduce its direct emissions 18% from current levels by 20502023年12月1日 With the amount of waste tyres rising each year and currently standing at 15 billion worldwide (Xiao et al, 2022), there is now a significant amount stockpiled or disposed of in landfills (Bulai, 2022)It is estimated that approximately 4 billion ELTs are currently in stockpiles and landfills worldwide (WBCSD, 2008), and this will rise to 5 billion by 2030 (PachecoTorgal A comparative life cycle assessment of tyre recycling using pyrolysis 2024年1月1日 The cement production industry accounts for up to 15 % of the total industrial energy consumption and produces approximately 5 % of the total anthropogenic CO 2 emissions (IEA, 2019)The basic chemistry of cement production starts with the calcination of limestone (CaCO 3) that produces calcium oxide (CaO) and carbon dioxide (CO 2), followed by the Reducing carbon emissions in cement production through 2022年5月26日 The urge to reduce greenhouse gas emissions, in particular carbon dioxide, is a global problem, not only in spatial terms but also in terms of the scope of activities and sectors involved Nevertheless, some sectors/industries are more critical due to their overall contribution to the problem, which is the case of the Portland cement industry The present research Industrial production of recycled cement: energy consumption and carbon

Comparison of energy consumption and carbon emissions from
2021年7月15日 The high carbon emissions from cement production result from the combination of two of the three main sources of anthropogenic emissions of CO 2 to the atmosphere: i) carbonate decomposition; and ii) oxidation of fossil fuels With roughly 60% of the raw material comprising of carbonates (mostly limestone, CaCO 3), the production of the main component 2021年9月20日 Abstract Methane pyrolysis is an emerging technology to produce lowercarbon intensity hydrogen at scale, as long as the coproduced solid carbon is permanently captured Partially replacing Portland cement with pyrolytic carbon would allow the sequestration at a scale that matches the needs of the H2 industry Our results suggest that compressive strength, the Sequestration of solid carbon in concrete: A largescale enabler of 2020年7月29日 Cement plays a dual role in the carbon cycle like a sponge Here, the authors employ a dynamic model to quantify such sponge effect and concluded that deep decarbonization of the global cement The sponge effect and carbon emission mitigation potentials of Table 32 World consumption of carbon black by end use 11 Table 33 World consumption of carbon black by region and enduse market 12 Table 34 World consumption of hydrogen by region 15 Table 41 Indicative relative power consumption and product output by feedstock 17 Table 42 Particle range of rubbergrade carbon black 19Hydrogen and Carbon Black by Methane Pyrolysis IHS Markit
.jpg)
Options for switching UK cement production sites to near zero
Figure 23: MPA Cement Member Kiln, Grinding and Grinding and Blending Sites 10 Figure 24: Cement manufacturing process [source: “Technology Roadmap: LowCarbon transition in the Cement Industry”, International Energy Agency, Cement2022年8月15日 Controlling carbon emissions is a high priority for the Chinese government At the 75th UN General Assembly in 2020, the Chinese government pledged to peak its carbon emissions by 2030 and aim for carbon neutrality by2060 1 Achieving the two climate goals could meet China's Nationally Determined Contributions committed in the Paris Agreement, as well China's efforts towards carbon neutrality: Does energysaving 2022年3月1日 The cement industry emits 8% of global CO 2 emissions Representing over 50% of these emissions, China's Cement Industry (CCI) will play a key role towards achieving CO 2 emission peak and Carbon neutrality This study designed a bottomup Green Transition Roadmap model to assess the feasibility of China's newly proposed goal – achieve Carbon China's green deal: Can China's cement industry achieve carbon neutral 2020年11月1日 In the rubber industry, carbon black plays a significant role in its remarkable effects as a reinforcement filler, but it is manufactured from nonrenewable petrochemical materials [6, 7]From the perspective of sustainable and green chemistry, the customary status of carbon black has been severely challenged and many efforts have been devoted to the Recycling of waste tire by pyrolysis to recover carbon black

Investigation of Carbon Black Production from Coal Tar via
The chemical looping pyrolysis (CLP) process was used to produce reinforced carbon black (CB) in this paper, and the effects on energy conservation and emission reduction of the method were investigated The characteristics of the oxygen carrier (OC) type, particle size, and reaction temperature on the CB yield and the morphological structure were examined In addition, the Reduction Opportunities for the Cement Industry Prepared for: Industrial Technologies Cover: Rotary kilns represent the largest energy consumer and carbon dioxide emission source of the cement/concrete industry The cover diagram shows a thermal image of an plants manufactured over 88,900,000 tonnes of cement in the year 2001 Energy and Emission Reduction Opportunities for the Cement 2024年7月11日 Lowcarbon development of ordinary Portland cement industry is of great significance to China’s target “to peak carbon dioxide emissions before 2030 and to achieve carbon neutrality before Plantlevel intensity of energy and CO2 emissions for Portland cement 2024年1月1日 In this study, the production behavior, characters, and mechanism of carbon black from pyrolysis of natural rubber (NR), butadiene rubber (BR), and styrenebutadiene rubber (SBR) were investigated The yield of carbon black was increased from 208%–244% to 479%–567% with the increase of pyrolysis temperature from 1100 to 1300°CCarbon black production characteristics and mechanisms from pyrolysis
.jpg)
Energy Conservation and Emission Reduction SpringerLink
2021年11月3日 Through routine energysaving monitoring, energy audit, energy efficiency benchmarking, internal audit, organizations’ energy consumption measurement, test and energy balance statistics, management review, selfevaluation, energysaving technical renovation, energysaving assessment, and other measures, we can improve the energy management 2023年12月20日 The demand for production of cements is ever increasing to meet the infrastructure development globally The energy and emission factors available for cements in most of the life cycle assessment (LCA) databases may not exactly suit for all the geographical locations The main challenge in Indian scenario is the absence of database for LCA study Study on energy use and carbon emission from manufacturing of 2020年9月25日 Radiation from the plasma torch, as well as heat convection from the plasma gas, provides enough energy for the pyrolysis of hydrocarbons Temperature is the important parameter in cracking reactions [38]After the conversion of hydrocarbons into carbon black and hydrogen, a waste heat recovery system takes advantage of the heat of the products to Carbon black and hydrogen production process analysis2021年11月30日 The second type of classification is based on the reaction scale and reactor type/size Laboratory scale heattreatment can be performed in a tube furnace, small reactors or chambers that can facilitate a controlled environment (eg inert gas or vacuum) [9, 11, 18, 63]In some cases, the size of the precursor sample may be extremely small (micro or even nano A comprehensive review of the pyrolysis process: from carbon

A critical review on energy use and savings in the cement industries
2011年5月1日 The typical electrical energy consumption of a modern cement plant is about 110–120 kWh per tonne of cement [19] The main thermal energy is used during the burning process, while electrical energy is used for cement grinding [20] Fig 1 shows electrical and thermal energy flow in a cement manufacturing process1 1 Introduction As US manufacturers face an increasingly competitive global business environment, they seek opportunities to reduce production costs without negatively affecting product yield or qualityEnergy Efficiency Improvement and Cost Saving Opportunities for Cement 2024年3月1日 Analysis along the carbon footprint of the cement production reveals processrelated CO 2 emissions from the decomposition of limestone (CaCO 3) (Eq 1) in the precalciner account for more than 60 % of total emissions and energyrelated CO 2 emissions from the combustion of fossil fuel for maintaining high temperatures of rotary kiln (1,450 °C1,500 °C) Chemical engineering solution for carbon neutrality in cement 2021年5月10日 They also estimated the cumulative costeffective fuel savings at 1029 PJ with a corresponding decrease in CO 2 emission of 97 Mt Tesema and Worrell (2015) estimated that in the 8 cement plants operating in Ethiopia in 2010, the potential costeffective electricity savings could reach 11 GWh with fuel savings of 12 PJ, resulting in a 01 Mt reduction in CO 2 Bottomup analysis of energy efficiency improvement and CO2 emission
.jpg)
Does energysaving and emission reduction policy affects carbon
2022年10月15日 “Saving resources and protecting the environment” is China's basic and national policy, and energy conservation is the key support in CO 2 emissions peaking and carbon neutrality China's 11th FiveYear Plan (2006–2010) for the first time set a 20 % reduction in energy consumption per unit of GDP as a target [6]In fact, China's energy intensity fell by