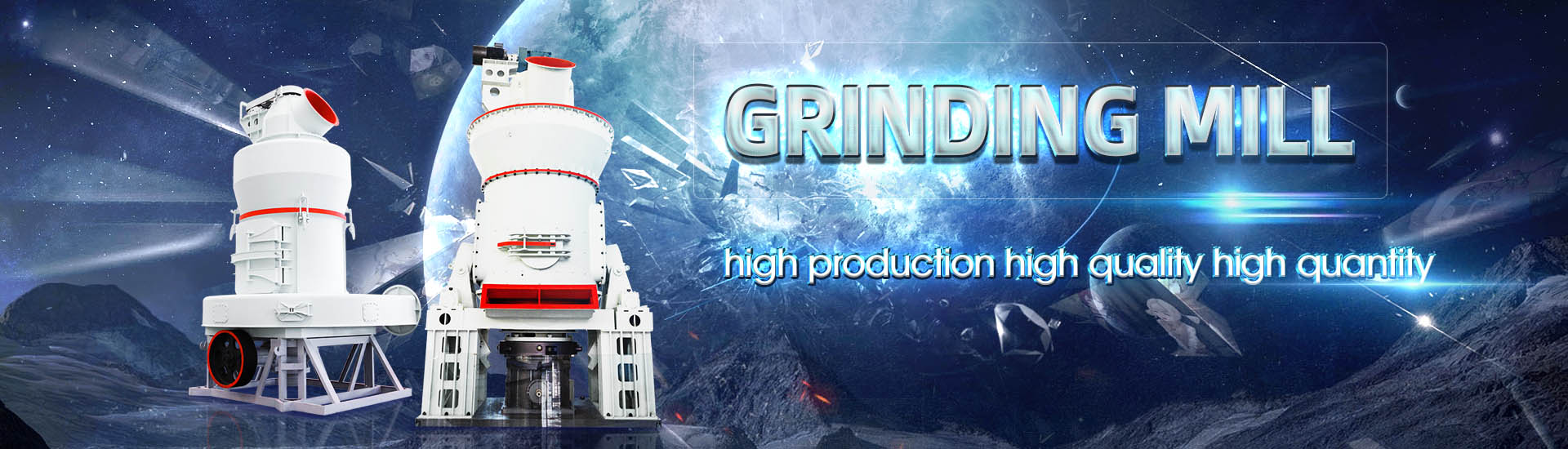
Sixroller ore mill is too big
.jpg)
Particle Size Reduction and Enlargement ScienceDirect
2019年1月1日 Materials are rarely found in the size range required, and it is often necessary either to decrease or to increase the particle size When, for example, the starting material is The roller mill’s ability to reduce materials to a uniform particle size provides more control of product characteristics and minimizes waste, as shown in Figure 1 The mill’s controlled Roller mills: Precisely reducing particle size with greater efficiency2022年10月4日 Ore heterogeneity could be a big problem in optimizing the mill feed and there is a great need to reduce the amount of waste materials before they enter the energy intensive Reduction of Fragment Size from Mining to Mineral Processing: A sixroller Loesche mills has justified the selected development concept, in which the grinding capacities of Loesche mills were boosted by increasing the number of rollers rather than the RAW MATERIAL GRINDING ITadipatri’s big sixer Loesche
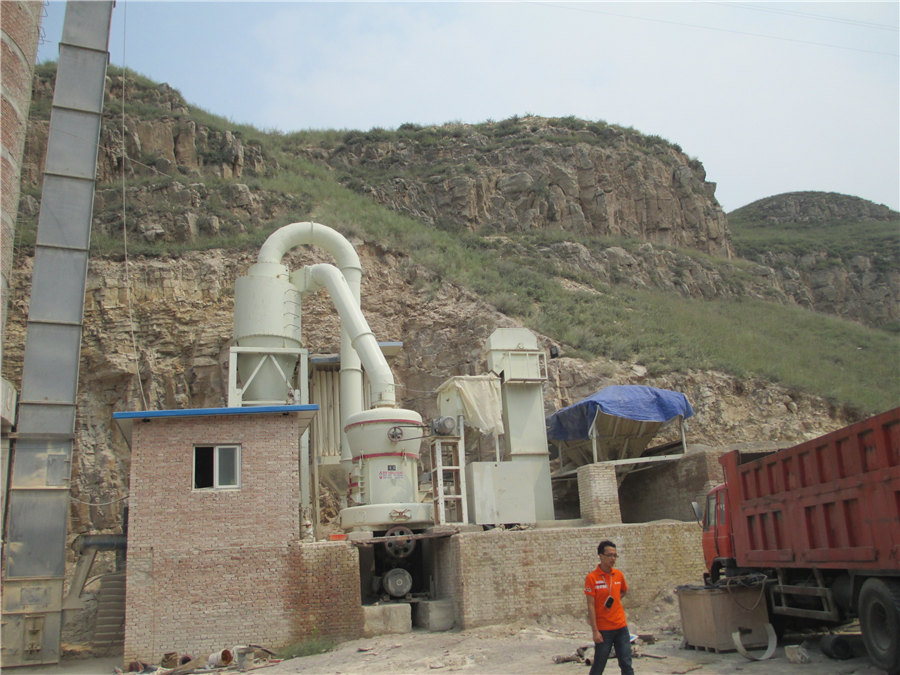
六辊轧机 百度百科
六辊 轧机,是一种辊 轧机,用于将粘性物质粉碎和均匀化,特别是用于使悬浮在粘合剂中的 固体 颗粒散布和均匀分布。 该辊轧机包括至少两个辊子和至少一个施压装置,所述辊子安装成可 2019年4月16日 The paper demonstrates why the Loesche VerticalRollerMill (VRM) is a serious alternative to conventional grinding technologies and where the limitations of the system are (PDF) LEARNING FROM OTHER INDUSTRIES; WHY THE VRM2001年10月1日 Recent research has shown, that the application of these vertical roller mills in dry grinding of ores and minerals can lead to significantly better recovery rates and higher Loesche vertical roller mills for the comminution of ores and 2023年7月4日 Roller mill is a type of grinding equipment for crushing materials by pressure between two or more rolling surfaces or between rolling grinding bodies (balls, rollers) and a Roller Mill SpringerLink
.jpg)
Redundancy and interchangeability – large vertical roller mills for
Based on these investigations Loesche GmbH has developed a mill for producing raw meal that has an arrangement of six rollers on the grinding table This mill, designated the LM 606 has a Wet grinding in an AG/SAG mill is accomplished in a slurry of 50 to 80 percent solids 2D and 3D simulations of particles in a SAG Mill red=fastest, blue=slowest moving particles [image: (13564)] The mill product can either be finished size AMIT 135: Lesson 6 Grinding Circuit – Mining Mill roller mill tests of your material in the manufacturer’s test facility with various roll corrugation styles and under conditions that duplicate your operating environment Figure 1 Particle size distributions: Roller mill versus other grinding methods Other grinding methods Roller mill Overs Target particle size Fines Figure 2Roller mills: Precisely reducing particle size with greater efficiencyOre mill Ore mills 21 companies 42 products My filters for ore Delete all Manufacturers C; Ceramic Instruments Srl (2) D; Dec Group (6) E; Eriez Magnetics Europe Limited (1) F; The POITTEMILL pendulum roller mill is a vertical mill that works by compressing the material bedOre mill, Ore grinding mill All industrial manufacturers

Study of the temperature rise of a roller mill C Mills Archive
Through research and analysis, mill roller heat source comes from three aspects: one is because of the heat released by the grinding wheat, namely after the wheat into the compression zone, as the roller run, wheat material layer thickness is more and more thin, wheat grinding roller pressure is more and more big, until the2020年9月8日 After technical development and improvement, the design of the blade of Raymond mill is reasonable, it can shovel up and make the material fully grind between the grinding roller and the grinding ring If Blade, grinding roller, grinding ring and other main wearing parts are seriously worn, the amount of powder production rate will be affectedSix Methods to Improve the Efficiency of Raymond Mill2024年1月8日 The roll deformation model of the sixhigh rolling mill is one of the core models of the strip shape control theory The influence function method (IFM) is a numerical method applied to solve the roll deformation problem This study aims to address the problems of slow calculation speed and insufficient calculation accuracy of IFM in calculating the roll deformation of the six An improved method for calculating roll deformation of sixhigh 2020年12月29日 6 Methods to Improve the Output of Raymond Mill Dec 29, 2020 As one of the commonly used milling equipment, stone Raymond roller mills are suitable for high fine milling processing of more than 280 kinds of materials in the mining, chemical, and construction industries The output of the Raymond mill grinder machine is directly related to the efficiency 6 Methods to Improve the Output of Raymond Mill
.jpg)
Modeling and simulation of vertical roller mill using population
1450℃ to become clinker The clinkers are cooled by six fans and entered the clinker bins The D 90 of clinkers are 32mm The clinkers and gypsum with a ratio of 97 to 3% are interred to a vertical roller mill (LOESCHE mill) The feed rate of the clinker VRM is 160t/h The VRM has four rollers including two big rollers (master rollers) and The rod mill is another type of grinding mill used in the copper ore mining process This machine uses steel rods as the grinding media instead of balls, which are commonly used in ball mills The rods grind the ore by tumbling within the mill, similar to the action of a rotating drumUnderstanding the SAG Mill in Copper Ore Mining Process2022年9月1日 All content in this area was uploaded by Zongxian Zhang on Aug 20, 2022(PDF) Towards waterless operations from mine to mill2017年1月1日 Schmitz, T: Quadropol QMCRD World's First Vertical Roller Mill with Driven Rollers Presentation 7 th International VDZ Congress 2013, 2527 September 2013, Düsseldorf/Germany(PDF) Drives for large vertical roller mills ResearchGate
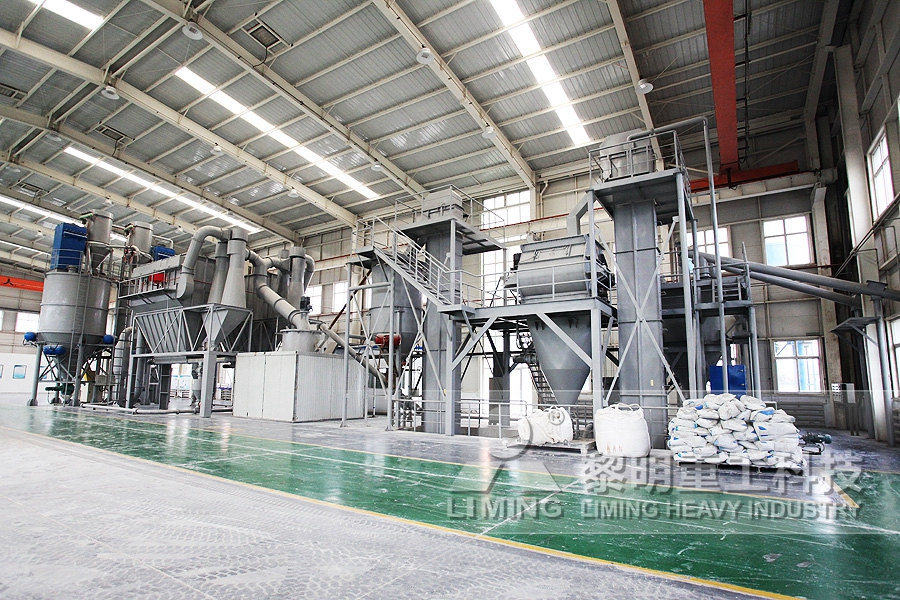
Monitoring ore loss and dilution for minetomill
However, ore below the pay limit adds variation to the mill grade as increased mill throughput will be required to make up for the loss of gold, and that impacts on the recovery in the plant It is against these perspectives and findings of this 2015年3月10日 Within the scope of the study ore grinding performance of the vertical roller mill was investigated with mobile pilot plant In this context, chalcopyrite ore of a plant having rod and ball milling circuit was ground under different operating modes eg, air swept and overflow, and process conditions, then samples were collected around the systemCopper ore grinding in a mobile vertical roller mill pilot plantthe mill structure, on the mill gearbox that supports the grinding table and on the mill foundation This challenge required a rigid design to ensure the longevity of the Loesche mill The decisive step for achieving The first sixroller Loesche mill for grinding cement raw material was successfully put into operation in July 2008 (see Figure 1)RAW MATERIAL GRINDING ITadipatri’s big sixer LoescheThe vertical roller mill grinds the marital to D85 of 90µm The ground product is calcined in a preheater to 850900℃ After calcination, the materials enter to a rotary kiln and heated to 1450℃ to become clinker The clinkers are cooled by six fans and entered the clinker bins The D90 of clinkers are 32mm The clinkers and gypsum with a Modeling and simulation of vertical roller mill using population
.jpg)
Rolling Mill Stands IspatGuru
2020年10月6日 Fig 2 Typical 4high stands showing various details Prestressed mill stand – In a conventional rolling mill, the roller separating force which arises when the work piece bar is passed through the rolls is transferred through the backup rolls and their bearings to the mill house In a prestressed mill stand, the two backup rolls are connected to each other by an 2022年9月1日 VRM has been widely researched in processing of cement (Ito et al, 1997, Jorgensen, 2005, Wang et al, 2009, Ghalandari et al, 2021)), coal (Tontu 2020), iron ore (Reichert et al 2015), zinc ore (van Drunick et al 2010), copper ore (Viljoen et al, 2001, Altun et al, 2015), gold (Erkan et al 2012; Altun et al 2017), nickel ore (Viljoen et al 2001), etc, and it Towards waterless operations from mine to mill ScienceDirect2015年4月9日 Typically this type of mill can deliver a product with a fineness of less than 01 mm Testing of material is needed before hand to determine the suitability of the ore for processing in an autogenous mill The rod mill (Fig 1) is a tumbling mill which is having a large percentage of its volume (30 % to 40 %) loaded with steel rodsGrinding Mills and Their Types – IspatGuruAn early 20thcentury oilseed rollermill from the Olsztyn district, Poland A late 19th century double roller mill displayed at Cook's Mill in Greenville, West Virginia in 2022 Closeup of Barnard's Roller Mill, New Hope Mills Complex, New York Cutaway drawing of a centrifugal roller mill for mining applications, 1913 Roller mills are mills that use cylindrical rollers, either in opposing Roller mill Wikipedia

Roller Mill SpringerLink
2024年1月1日 'Roller Mill' published in 'The ECPH Encyclopedia of Mining and Metallurgy' Skip to main content Advertisement Account Menu Find a The Raymond mill is mainly used to grind coal, nonmetallic ore, glass, ceramics, cement, gypsum, pesticide, chemical fertilizer, and other materials The product particle size is 0045–0125 2014年10月1日 In a test performed in the Loesche test center in Germany, copper slag grinding saved 229% energy in an airswept model and 344% energy in an overflow model [13,14]Copper Ore Grinding in a Mobile Vertical Roller Mill Pilot PlantIn some roller mills, the grist may be separated by size and some grist fractions may be sent through the mill a second or even third time The simplest, most common, but least efficient mill is a tworoller mill, which is usually found in small breweries or brewpubs Both rollers spin at the same speed The malt passes through the rollers only roller mill Craft Beer BrewingThree roller mill of this type is overall equally userfriendly in nature If you are interested in, you can read Graphene Sheet Films Applications SG Roll Mills They are the improved versions of the S triple roll Flexible wheels are used to Three Roll Mill and The Potential Applications

Vertical Roller Mill Magotteaux
Vertical roller mills have numerous applications in many different industriesAlthough they are widely used in the cement sector, for example, you are just as likely to find a vertical roller mill being used to handle ores in mining processing plantsThere again, vertical roller mills also have uses within the context of power stations where they are primarily used to pulverize coalWith a Dinnissen Roller Mill it is possible to reduce product, Sixfold increase of total production Production has gone from 35 tons per day to 30 tons per day No challenge is too big At Dinnissen, they think in terms of challenges, not problemsRoller Mill Contact us for your Solution Dinnissen2001年10月1日 This study investigated a mathematical model for an industrialscale vertical roller mill(VRM) at the Ilam Cement Plant in Iran The model was calibrated using the initial survey's data, and the LOESCHE vertical roller mills for the comminution of ores and minerals2016年9月1日 Furthermore, VRM separator speed (rpm) is one of the key operational parameters that determines product particle size Increasing the classi er rotor speed from 60 to 80 rpm decreases the particle Operational parameters affecting the vertical roller mill
.jpg)
PROCESS TRAINING for operators of Vertical RAW Mills
But the air also transport s the heat for the drying process Furtherrn ore the air fluidizes and stabilizes the grin ding bed or when big metal pieces are in the mill Also too low an outlet temperature can create a increased vibration level Power consumption of mill main drive2017年7月3日 (See fig 7) Any cylindrical mill may be lined in this fashion by using liners tapered in thickness If the liners are 2 feet long, a 12foot mill would have six truncated cones, end to end The mill would have the same capacity at the discharge end as at the feed end In some way, at least, this would be an advantage over the long coneWhy use Different Size Balls in a Mill 911MetallurgistOne contribution to minimise the increase is to use more efficient comminution equipment Verticalrollermills (VRM) are an energyefficient alternative to conventional grinding technology One reason is the dry inbed grinding principle Results of extensive test works with two types of magnetite iron ores in a Loesche VRM are presented hereResearch of iron ore grinding in a verticalrollermillWet grinding in an AG/SAG mill is accomplished in a slurry of 50 to 80 percent solids 2D and 3D simulations of particles in a SAG Mill red=fastest, blue=slowest moving particles [image: (13564)] The mill product can either be finished size AMIT 135: Lesson 6 Grinding Circuit – Mining Mill
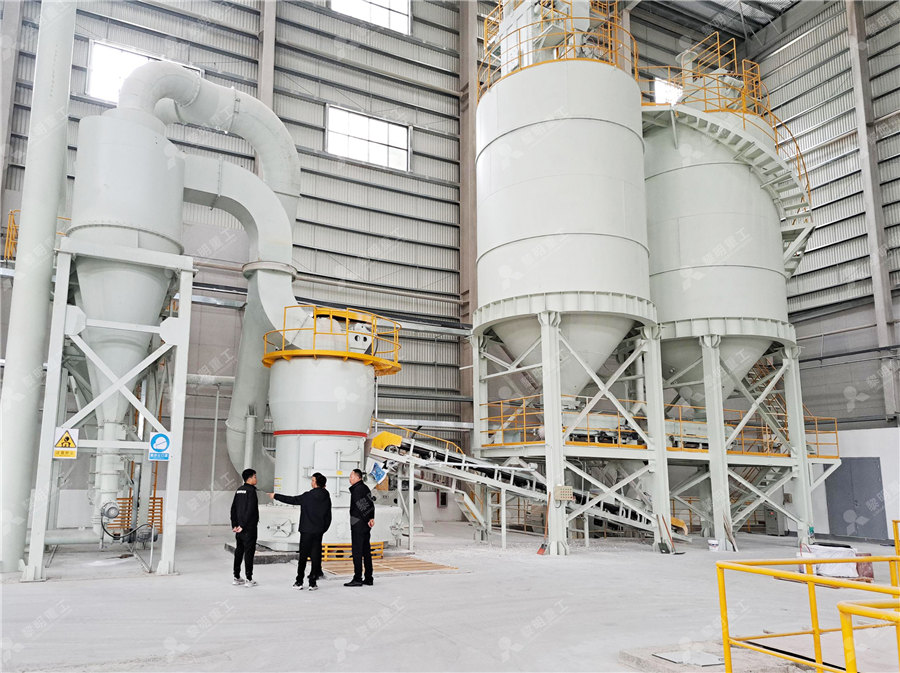
Roller mills: Precisely reducing particle size with greater efficiency
roller mill tests of your material in the manufacturer’s test facility with various roll corrugation styles and under conditions that duplicate your operating environment Figure 1 Particle size distributions: Roller mill versus other grinding methods Other grinding methods Roller mill Overs Target particle size Fines Figure 2Ore mill Ore mills 21 companies 42 products My filters for ore Delete all Manufacturers C; Ceramic Instruments Srl (2) D; Dec Group (6) E; Eriez Magnetics Europe Limited (1) F; The POITTEMILL pendulum roller mill is a vertical mill that works by compressing the material bedOre mill, Ore grinding mill All industrial manufacturersThrough research and analysis, mill roller heat source comes from three aspects: one is because of the heat released by the grinding wheat, namely after the wheat into the compression zone, as the roller run, wheat material layer thickness is more and more thin, wheat grinding roller pressure is more and more big, until theStudy of the temperature rise of a roller mill C Mills Archive2020年9月8日 After technical development and improvement, the design of the blade of Raymond mill is reasonable, it can shovel up and make the material fully grind between the grinding roller and the grinding ring If Blade, grinding roller, grinding ring and other main wearing parts are seriously worn, the amount of powder production rate will be affectedSix Methods to Improve the Efficiency of Raymond Mill
.jpg)
An improved method for calculating roll deformation of sixhigh
2024年1月8日 The roll deformation model of the sixhigh rolling mill is one of the core models of the strip shape control theory The influence function method (IFM) is a numerical method applied to solve the roll deformation problem This study aims to address the problems of slow calculation speed and insufficient calculation accuracy of IFM in calculating the roll deformation of the six 2020年12月29日 6 Methods to Improve the Output of Raymond Mill Dec 29, 2020 As one of the commonly used milling equipment, stone Raymond roller mills are suitable for high fine milling processing of more than 280 kinds of materials in the mining, chemical, and construction industries The output of the Raymond mill grinder machine is directly related to the efficiency 6 Methods to Improve the Output of Raymond Mill1450℃ to become clinker The clinkers are cooled by six fans and entered the clinker bins The D 90 of clinkers are 32mm The clinkers and gypsum with a ratio of 97 to 3% are interred to a vertical roller mill (LOESCHE mill) The feed rate of the clinker VRM is 160t/h The VRM has four rollers including two big rollers (master rollers) and Modeling and simulation of vertical roller mill using population The rod mill is another type of grinding mill used in the copper ore mining process This machine uses steel rods as the grinding media instead of balls, which are commonly used in ball mills The rods grind the ore by tumbling within the mill, similar to the action of a rotating drumUnderstanding the SAG Mill in Copper Ore Mining Process
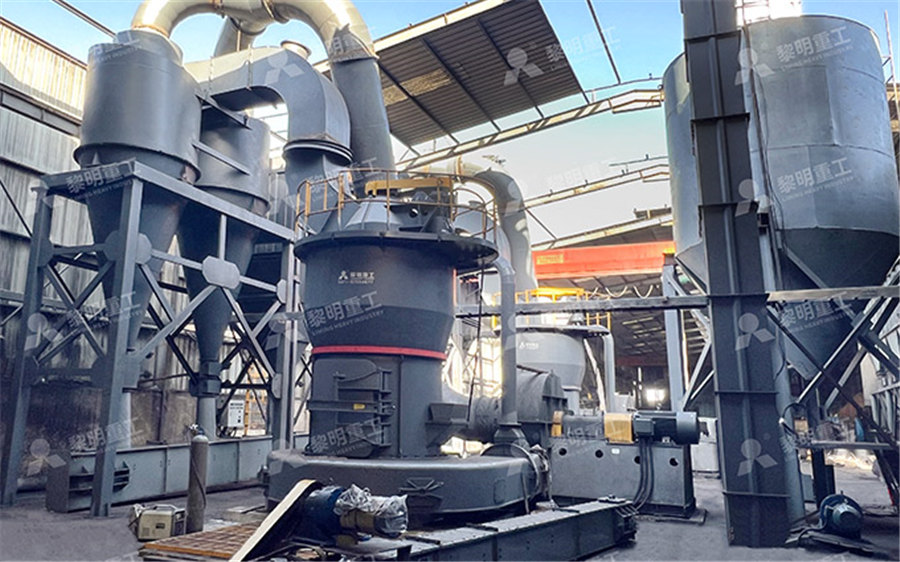
(PDF) Towards waterless operations from mine to mill
2022年9月1日 All content in this area was uploaded by Zongxian Zhang on Aug 20, 2022