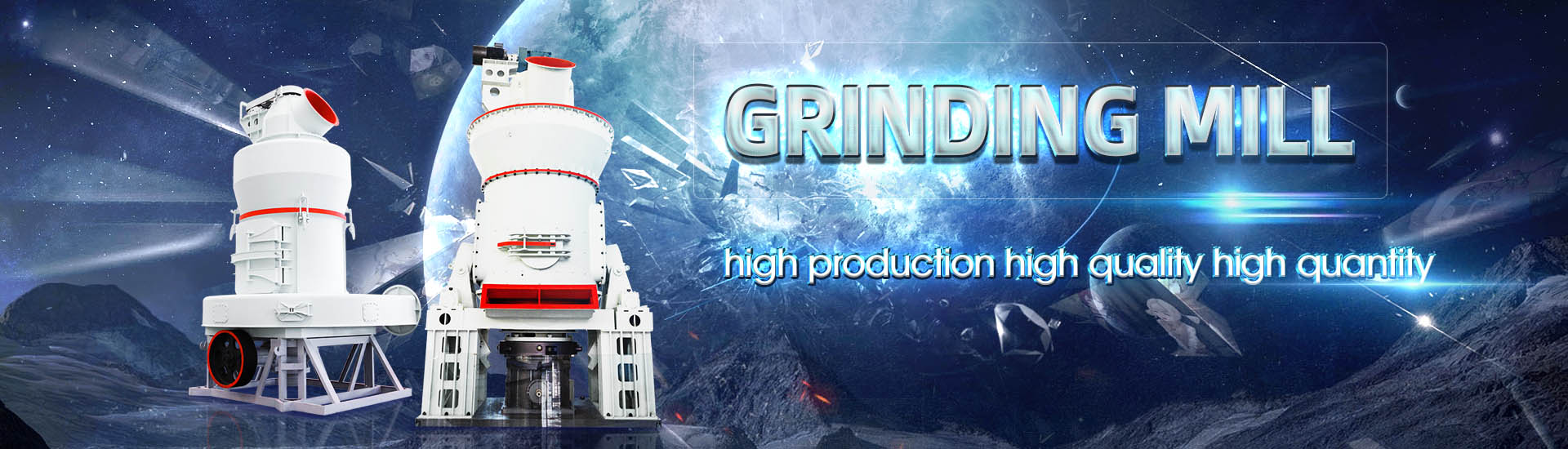
Parameters of 1250 diameter coal mill
.jpg)
LOESCHEMILLS
The Loesche coal grinding mill range is divided into two serial types: Small twin mills constructed to individual specifications (LM 122 D to LM 202 D), with table diameters from 1,200 to 2,000 mm Larger mills with two, three and four rollers and modular structures (LM 212 D to LM ZGM type medium speed roller mill is widely used in coal powder preparation system of electric power, metallurgy, cement, chemical industry and other industries, as well as coal pulverizing ZGM type Mediumspeed Rolling coal millpower plant equipmentThe final determination of the type and output of the coal mill depends on the following parameters: ① the drying dose of the pulverizer population; ② the temperature of the HP Bowl type millspower plant equipmentCoal mill is an important component of the thermal power plant It is used to grind and dry the moisturized raw coal and transport the pulverized coal – air mixture to the boiler Poor dynamic Modeling and Control of Coal Mill
.jpg)
Technical specifications of vertical roller coal mill
Vertical Coal Mill (VCM) is equipment for grinding and pulverizing coal into micron size Rotary kilns then use the powders as fuel burners The VCM has a housing section equipped with aIn this paper, the coal mill is modeled based on physical insight and the model parameter values are obtained by using the grey nonlinear model in Matlab System Identification Toolbox The Modeling and Parameter Identification of Coal Mill2009年9月20日 The major measurement parameters of coal pulverizers are typically pulverizer outlet temperature, coal mass flow, primary air flow, inlet primary air temperature, motor Modeling and Parameter Identification of Coal Mill ResearchGate2009年9月1日 Development and validation of coal mill model for improved coal mill control is presented and the parameters required to validate the model is estimated using Genetic Modeling and Parameter Identification of Coal Mill
.jpg)
An investigation of performance characteristics and energetic
2020年8月12日 To understand the performance of a vertical roller coal mill, the real operational tests have been performed considering three different coal sources Obtained results indicate 2012年5月1日 The paper presents development and validation of a coal mill model to be used for improved mill control, which may lead to a better load following capability of power plants Derivation and validation of a coal mill model for control1250 parameter diameter mill hotelbarecu Roller Mill Dolomit Group Parameter Diameter Mill The end mill speed is calculated with the following formula n rpm vc mmin 1000 314 ø d1 mm Example calculation vc 500 mmin selected from chart d ø 8 mm 19904 rpm 500 1000 314 8 If the maximum speed of the milling motor is lower than the Diameter 1250 Coal Mill ParametersRequest PDF On Sep 1, 2016, Deniz Altun and others published Operational parameters affecting the vertical roller mill performance Find, read and cite all the research you need on ResearchGateOperational parameters affecting the vertical roller mill
.jpg)
(PDF) The influence of rolling mill process parameters on roll
2019年6月1日 PDF This study analyzes the impact of operational parameters of hot rolling mill in the degradation process of a roll surface by thermal fatigue A Conclusion All proposed formulae for determining the ball diameter, depending on the diameter of the grain size material being ground, fit into the general form given in the equation: db Kd n , where db is the ball diameter, d is the diameter of the grain size material being ground, K and n are parameters, for which all authors say, depend on mill characteristics, 338 N Magdalinovic THE OPTIMAL BALL DIAMETER IN A MILL Academia2022年5月31日 Mineral crushing is the main source of energy consumption in mineral processing According to statistics, this consumption accounts for about 35–50% of the total cost of the mine (Curry et al, 2014), or even higherIt may also account for 18% of the global electrical energy consumption (NapierMunn, 2015)More efficient crushing equipment needs to be Analysis of vertical roller mill performance with changes in 2021年6月29日 Under optimum conditions of +60 mm material suitable for a 100 mm ball diameter, −60 + 20 mm material suitable for an 80 mm ball diameter, −20 mm material suitable for a 70 mm ball Effects of Mill Speed and Air Classifier Speed on Performance of
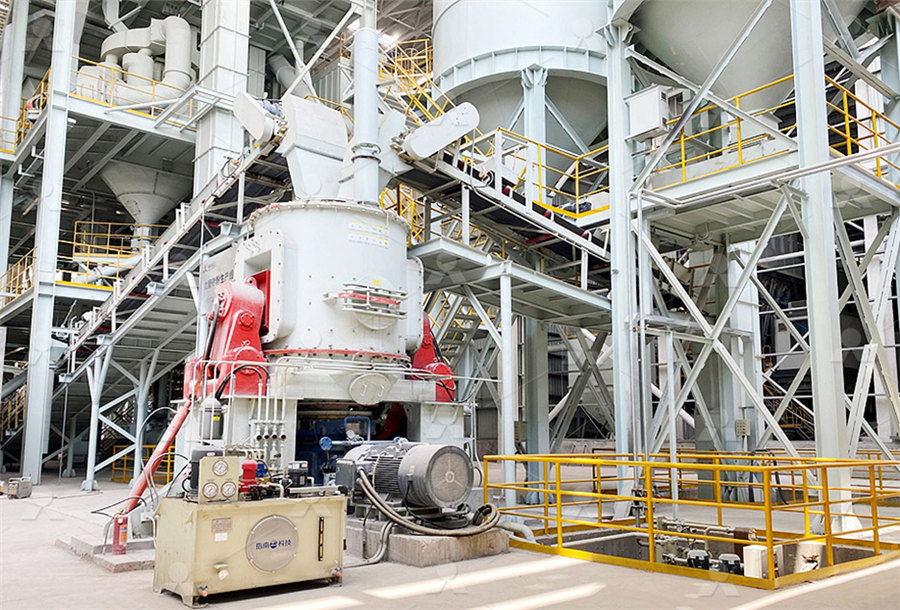
Modeling and Parameter Identification of Coal Mill ResearchGate
Modeling and Parameter Identification of Coal Mill 701 Fig 1 Sectional view of MBF coal mill It can be seen in the literature that modeling theneed improvement to achieve milloptimal performance Coal feed to the mill is important, this was observed to be a limiting constraint on mill capacity when the coal required exceed nominal load requirement KEYWORDS: Air fuel ratio; pulverised fuel distribution; classifier; elutriation; heat balance; isokineticPerformance optimisation of vertical spindle coal pulverisers2012年1月1日 Determine Design Parameters of Fan Mill System 31 Determine The Terminal coal water should be slightly lower than water air dried basis when coal mill outlet temperature is above 100 ć for Select air leakage coefficient as 01 or 02 as a supplement calculated to account for the cold gas diameter when designing The Research on Design Parameters of Fan Mill Direct Pulverizing System 2017年4月1日 In this study, pilot scale tests were performed with a mobile verticalrollermill grinding plant to investigate the relationships between operational parameters The identification and quantification of the grinding parameter relationships was carried out to implement these relationships into a computational verticalrollermill performance modelOperational parameters affecting the vertical roller mill
.jpg)
Breakage and separation mechanism of ZGM coal mill based on parameters
2014年3月1日 The factors included specific mill technologies, grindability of coal, drying capacity, residues and safety parameters Roller mills were stated to be the established and preferred equipment for 2020年10月9日 In order to obtain the optimal operation parameters of a SAG mill, in this paper, the discrete element method (DEM) is used to simulate the breakage process of the particles by controlling three Operation Analysis of a SAG Mill under Different 1927 First Loesche coal mill delivered for the Klingenberg power station in Berlin 1953 500th coal mill plant sold worldwide 1961 Introduction of hydraulic spring assembly system 1965 Construction of first pressure mill (LM 122 D) 1980 Delivery of first modular coal mill (LM 263 D) 1985 Delivery of first selfinerting coal grinding plant (LM 212 D) for the steel industry (PCI LOESCHEMILLS2012年12月31日 This phenomenon reveals that during combustion the emission of fine PM, especially the PM 25 , is greatly affected by coal fineness, which is consistent with the work by Ninomiya et al (2004)The Research on Design Parameters of Fan Mill Direct Pulverizing
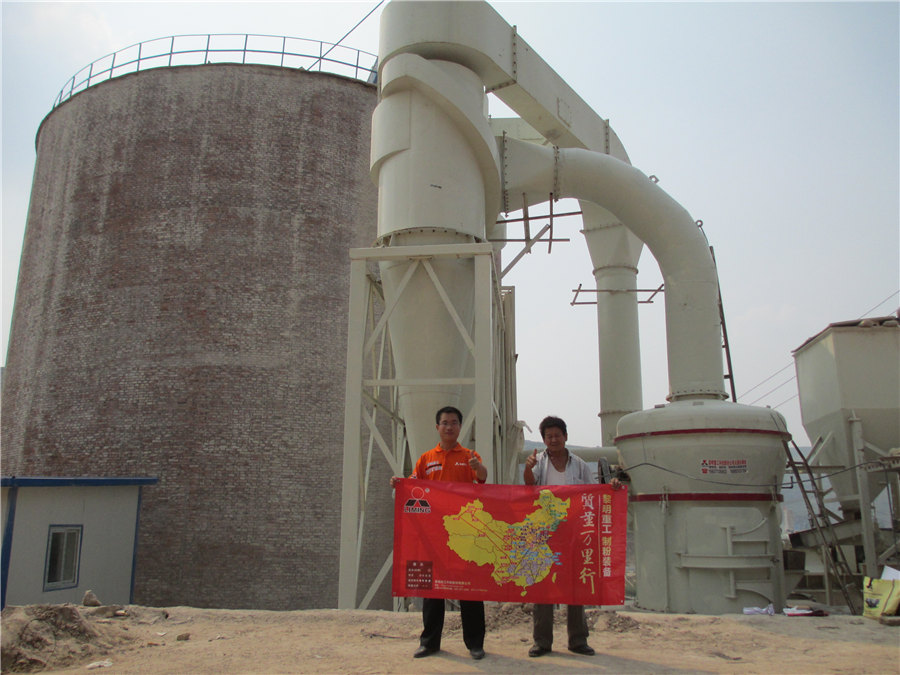
Wet and dry grinding of coal in a laboratoryscale ball mill: Particle
2019年10月1日 Firstly, the conventional ball mill parameters such as mill speed (% of critical speed), material filling ratio (Jb), ball filling ratio (fc), ball size distribution (10203040 mm, %), grinding Optimal parameters for drilling explosions when developing coal deposits by openpit method Pavel Afanasev1,*, Andrey Pasynkov1, Ivan Kurta2 1SaintPetersburg Mining University, 2, 21 Line VO, , St Petersburg, Russia 2Ukhta State Technical University, 13, Pervomayskaya St, , Ukhta, Republic of Komi, Russia Abstract The article discusses two deposits of Optimal parameters for drilling explosions when developing coal 2020年7月2日 A comprehensive investigation was conducted to delineate the effect of ball size distribution, mill speed, and their interactions on power draw, charge motion, and balls segregation in a (PDF) Effects of Ball Size Distribution and Mill Speed and Their Section of coal bowl mill Table 1 Guaranteed coal conditions for mill performance evaluation Coal Moisture % 20 Coal HGI 55 Mill Outlet Temperarure °C 80 Mill Air Flow T/hr 102 Coal Fineness (% passing trough 200 mesh) 70% passing through 200 mesh and 90% passing through 50 mesh Differental Pressure 300 mmwc Coal Output from Mill 609 t/hrA Study on 500 MW Coal Fired Boiler Unit’s Bowl Mill
.jpg)
LM Vertical Grinding Mill SBM Mill Crusher
2023年3月15日 Comprehensive Optimization, Lower Operating Costs From aspects of grinding efficiency, powder drying, abrasion of vulnerable parts and maintenance replacement of spare parts, SBM’s LM Vertical Grinding Mill achieves lower energy consumption, stronger drying capacity, as well as lower abrasion and easier checks of core parts, saving the operating costs From the coal yard, the coal is transfer to the mill bunkers through conveyor belt The bunkers are sized for an effective capacity of twelve (12) hours at BMCR with design coal Each mill bunker has one hopper, connected to the feeders Mills operate when the bunker coal gate valves are opened, coal is allowed to flow to the gravimetric feedersAnalysis of the Coal Milling Operations to the Boiler ParametersA simple energy balance model of the coal mill is derived in (Odgaard and Mataji 2006), this model is based on a more detailed model found in (Rees and Fan 2003)In this model the coal mill is seen as one body with the mass m mThe following variables are defined: T(t) is the temperature in the coal dust flow in the mill, ṁ PA (t) is the primary air mass flow, T PA (t) is Coal Mill an overview ScienceDirect Topics2018年5月4日 Sieves configuration: The sieves (or screens) of the hammer mills are usually perforated steel sheets of 2 3 mm thickness, with holes whose diameter is usually equal to or less than the diameter of the pelletLarger holes Hammer mill: parameters that affect grinding La
.jpg)
Ball Mill Parameter Selection Calculation JXSC
2019年8月30日 1 Calculation of ball mill capacity The production capacity of the ball mill is determined by the amount of material required to be ground, and it must have a certain margin when designing and selecting There are many The final determination of the type and output of the coal mill depends on the following parameters: ① the drying dose of the pulverizer population; ② the temperature of the desiccant at the inlet of the pulverizer (generally up to 400 ℃); ③ the moisture content of the pulverized coal at the outlet of the pulverizer; ④ the outlet temperature of the pulverizer (at least 55 ℃ HP Bowl type millspower plant equipmentPARAMETER INFLUENCE ANALYSIS OF BALL MILL BASED ON DEM Jinfeng ZHANG 1, Tie QU 2 *, Bijuan YAN 1, Chunjiang ZHAO , Qiang BIAN , Zhangda ZHAO 1 1250 Effective inner diameter /mm D 2 7166 Critical speed r/min n c 1584 Media fill rate φ 029 Liner thickness /mm d 77 Steel ball quality /kg m 1PARAMETER INFLUENCE ANALYSIS OF BALL MILL BASED ON DEM2014年3月1日 The operation parameters were adjusted for analyzing the breakage and separation characteristics in the industrial mill under the normal working condition The schematic diagram of the sampling ports is shown in Fig 1 The new feed drops on the rotatable grinding disc of the coal mill by gravity and mixes with the circulating loadBreakage and separation mechanism of ZGM coal mill based on parameters
.jpg)
ZGM type Mediumspeed Rolling coal millpower plant equipment
Under the same disc diameter, the roller diameter of ZGM medium speed coal mill is large, the width is large, and the speed is low Therefore, 1250: Grinding roll working diameter (mm) 1300: 1600: 1900: 2250: 2450: 2650: 2900: Grinding roll speed(r/min) 319: 287: 264: (omitted) to further determine the detailed parameters and size of Download scientific diagram Sectional view of MBF coal mill from publication: Modeling and Parameter Identification of Coal Mill The coal mill used in the coalfired power plants is modeled Sectional view of MBF coal mill Download Scientific DiagramCoal Mill Safety parameters: Position of Explosion vents Operational readiness of quick shutoff dampers Inertization section readiness (N2, CO2 pressure in bars) Feed size can be as large as 75 to 100 mm Feed size can be as large as 5% of roller diameter PreviousCoal Grinding Cement Plant OptimizationOptimization of some parameters of stirred mill for ultrafine grinding of of response surface method (RSM) The grinding process was carried out in a cylindrical ball mill with a diameter and length of 186 cm Application of Box–Behnken design and response surface methodology for modelling of some Turkish coals, Fuel 86 (2007) 90 (PDF) Optimization of some parameters of stirred mill for ultra
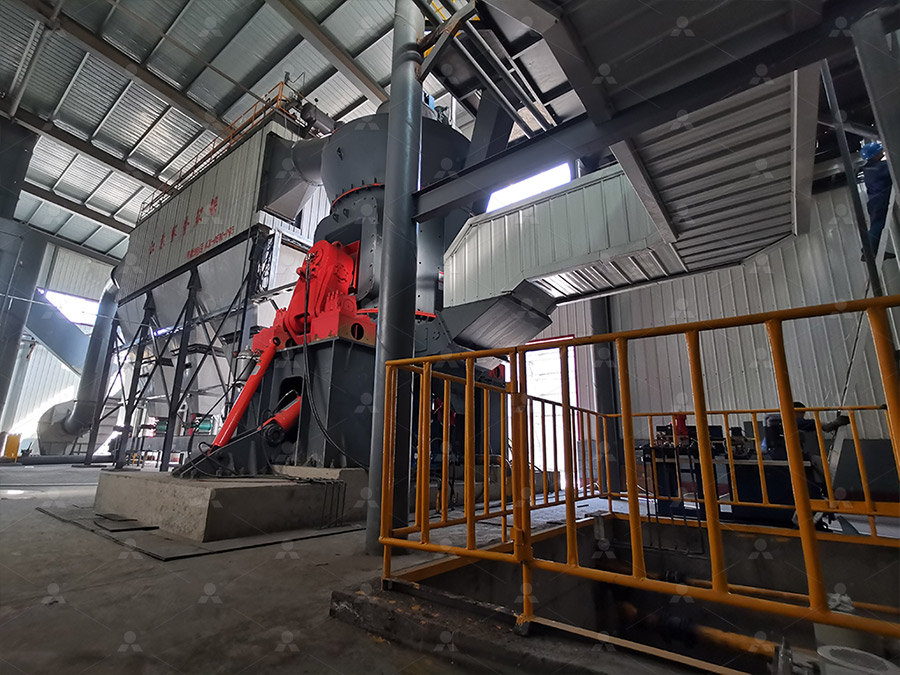
Diameter 1250 Coal Mill Parameters
1250 parameter diameter mill hotelbarecu Roller Mill Dolomit Group Parameter Diameter Mill The end mill speed is calculated with the following formula n rpm vc mmin 1000 314 ø d1 mm Example calculation vc 500 mmin selected from chart d ø 8 mm 19904 rpm 500 1000 314 8 If the maximum speed of the milling motor is lower than the Request PDF On Sep 1, 2016, Deniz Altun and others published Operational parameters affecting the vertical roller mill performance Find, read and cite all the research you need on ResearchGateOperational parameters affecting the vertical roller mill 2019年6月1日 PDF This study analyzes the impact of operational parameters of hot rolling mill in the degradation process of a roll surface by thermal fatigue A (PDF) The influence of rolling mill process parameters on roll Conclusion All proposed formulae for determining the ball diameter, depending on the diameter of the grain size material being ground, fit into the general form given in the equation: db Kd n , where db is the ball diameter, d is the diameter of the grain size material being ground, K and n are parameters, for which all authors say, depend on mill characteristics, 338 N Magdalinovic THE OPTIMAL BALL DIAMETER IN A MILL Academia
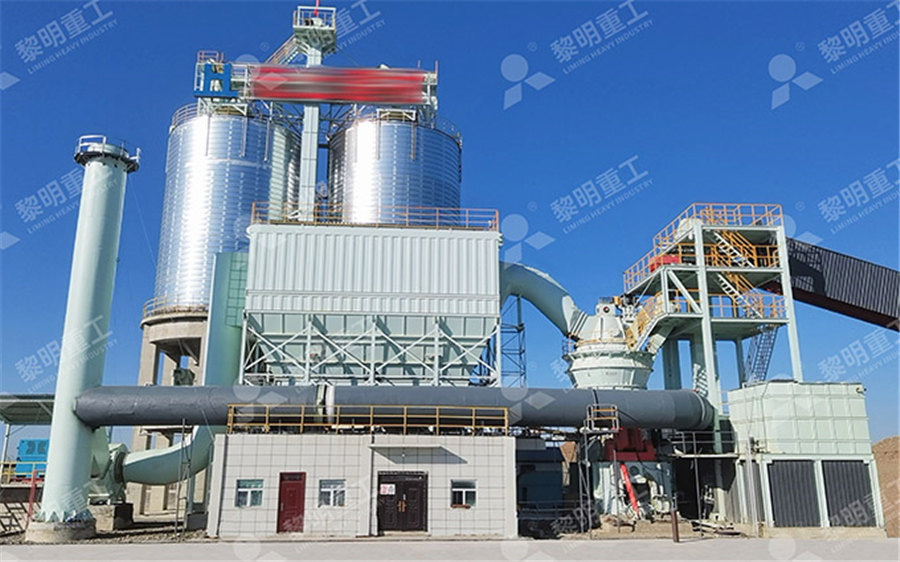
Analysis of vertical roller mill performance with changes in
2022年5月31日 Mineral crushing is the main source of energy consumption in mineral processing According to statistics, this consumption accounts for about 35–50% of the total cost of the mine (Curry et al, 2014), or even higherIt may also account for 18% of the global electrical energy consumption (NapierMunn, 2015)More efficient crushing equipment needs to be 2021年6月29日 Under optimum conditions of +60 mm material suitable for a 100 mm ball diameter, −60 + 20 mm material suitable for an 80 mm ball diameter, −20 mm material suitable for a 70 mm ball Effects of Mill Speed and Air Classifier Speed on Performance of Modeling and Parameter Identification of Coal Mill 701 Fig 1 Sectional view of MBF coal mill It can be seen in the literature that modeling theModeling and Parameter Identification of Coal Mill ResearchGateneed improvement to achieve milloptimal performance Coal feed to the mill is important, this was observed to be a limiting constraint on mill capacity when the coal required exceed nominal load requirement KEYWORDS: Air fuel ratio; pulverised fuel distribution; classifier; elutriation; heat balance; isokineticPerformance optimisation of vertical spindle coal pulverisers
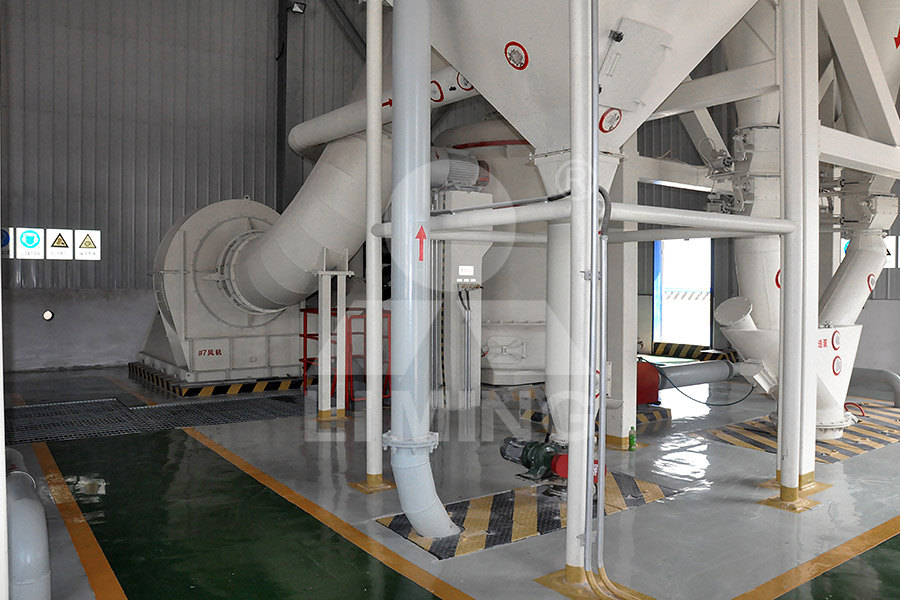
The Research on Design Parameters of Fan Mill Direct Pulverizing System
2012年1月1日 Determine Design Parameters of Fan Mill System 31 Determine The Terminal coal water should be slightly lower than water air dried basis when coal mill outlet temperature is above 100 ć for Select air leakage coefficient as 01 or 02 as a supplement calculated to account for the cold gas diameter when designing 2017年4月1日 In this study, pilot scale tests were performed with a mobile verticalrollermill grinding plant to investigate the relationships between operational parameters The identification and quantification of the grinding parameter relationships was carried out to implement these relationships into a computational verticalrollermill performance modelOperational parameters affecting the vertical roller mill