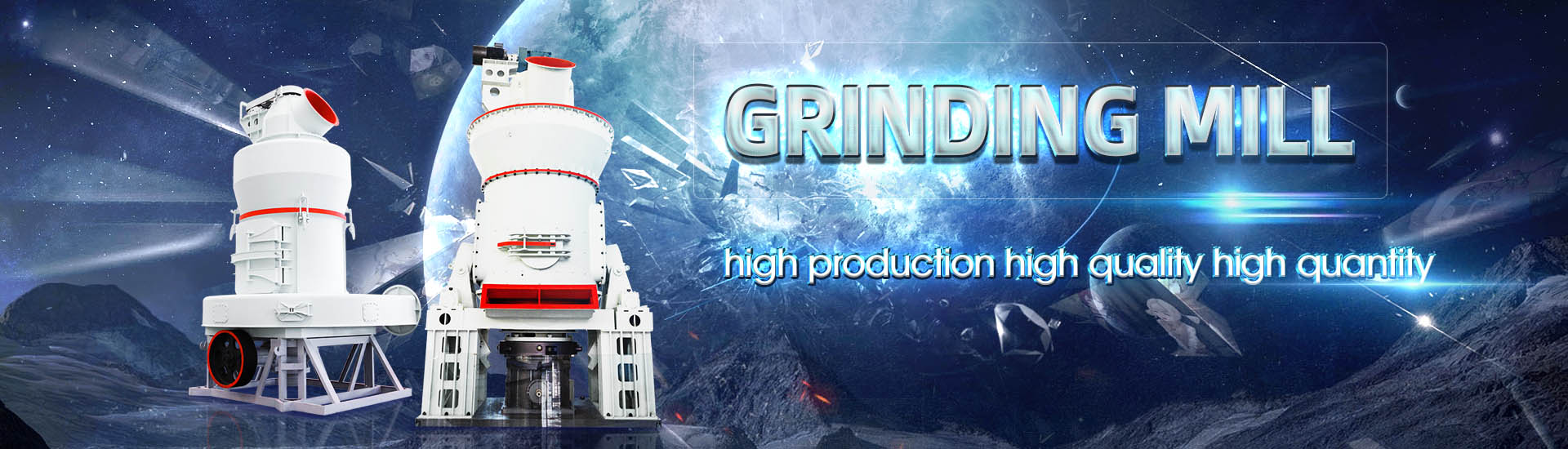
Lime kiln safety production responsibility system
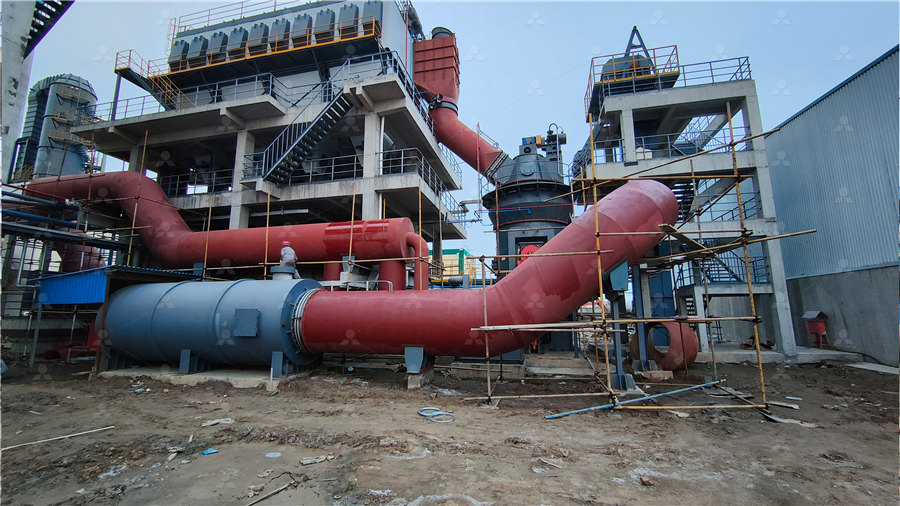
Lime Kiln Principles and Operations TAPPI
Lime Kiln Maintenance Refractory System • Monitor shell temperatures past refractory drilling records • Inspect for condition, drill/measure record thicknesses throughout kiln • Monitor Section 2 provides a detailed description of the production process for lime, with discussions of individual lime products, limestone inputs, and costs of production Section 3 describes the Lime Production: Industry ProfileIn some lime plants, the resulting lime is reacted (slaked) with water to form hydrated lime The basic processes in the production of lime are: (1) quarrying raw limestone; (2) preparing 1117 Lime Manufacturing US Environmental Protection AgencyThis paper presents some further information on the internals, potential for operational efficiency improvements and general maintenance aspects of the lime kiln Continuing the 25 Lime Kiln Equipment Operation and Maintenance TAPPI
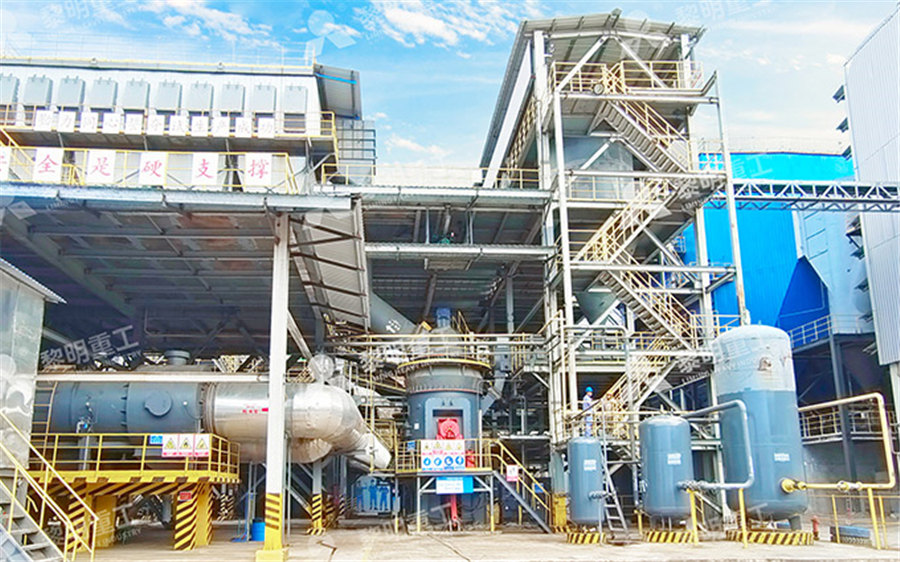
22 Lime Kiln Principles and Operations TAPPI
Lime Kiln Principles And Operations Terry N Adams Technical Consultant Seattle WA Slide 2 Outline • Lime kiln equipment – flames, chains, refractories – product coolers, external mud Lime production involves three main processes: stone preparation, calcination, and hydration During the calcination process, lime is sufficiently heated to generate processrelated CO2 as Technical Support Document for the Lime Manufacturing Sector2018年7月11日 The safety of a district’s kilns involves many choices and operations: choice of kiln for suitability to use, its location, its installation, commissioning, inspection, testing, Kiln Risk Management Best PracticesThis rule applies to commercial and captive (produced and utilized internally; not sold on the open market) lime manufacturing plants that are located at sources that emit enough toxic air FACT SHEET Final Rule to Reduce Toxic Air Emissions From Lime
.jpg)
New PFR lime kiln process with blast furnace gas and oxygen
A new and innovative Parallel Flow Regenerative lime kiln process using 100% blast furnace gas achieves the same performance as a natural gasfired PFR lime kiln; however, with Applying the most advanced technology, innovations and best practices, ANDRITZ helps companies in the lime industry to automate and modernize operations in order to increase Enhance the Value Generated by Your Plant: Automation AndritzShandong Wanda Environmental Protection Technology Co, LtdThe core products include advanced equipment represented by intelligent environmental protection lime kilns, providing customers with overall solutions for intelligent Shandong Wanda Environmental Protection o Because of the high carbon intensity of the lime production processes, pricing carbon directly causes higher costs for lime production Eg, an increase in carbon prices equivalent to €1/tonne CO 2 translates into a lime production average cost increase by €1,1/tonne quicklime (for comparison: EU production costs vary between €55 andA Competitive And effiCient Lime industry European Lime

Maintaining Your Lime Vertical Kiln
Inspecting the Kiln Regular inspections are essential for identifying potential issues early on and preventing equipment failure When inspecting a lime vertical kiln, it’s important to focus on the following common inspection Present paper attempts to review the literature related to various strategies to design the control system for the Lime kiln industrial process Lime Kiln is multivariable process with complex interactions of variables It has higher degree of coupling, severe non linearities, and frequent disturbances This paper covers the modeling and control aspects of Lime Kiln process The Modeling, Control and Instrumentation of Lime Kiln Process: A 8 Slide 15 Lime Kiln Heat Rate • Heat rate is a measure of energy efficiency – Units are MM Btu/ton CaO or GJ/tonne CaO – Often stated as MM Btu/ton “product” • Typical range – 5 to 9 MM Btu/ton CaO – 58 to 105 GJ/tonne CaO – Lower is better Slide 16 Lime Kiln Energy Balance Components • Drying • Calcining : CaCO3 + heat ÄCaO + CO2 • Losses – Heat loss through 22 Lime Kiln Principles and Operations TAPPI76 Hannes Piringer / Energy Procedia 120 (2017) 75–95 2 Hannes Piriner/ Energy Procedia 00 (2017) 000–000 The idea of this paper is to illustrate the following topics: impact of market Lime Shaft Kilns ResearchGate
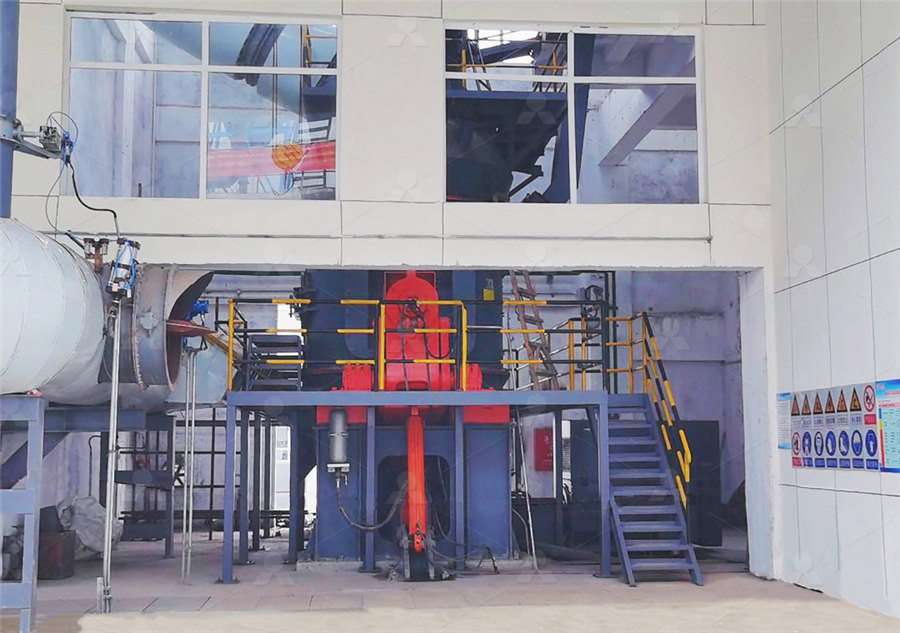
Lime Shaft Kilns ScienceDirect
2017年8月1日 Published by Elsevier Ltd Peerreview under responsibility of the organizing committee of INFUB11 101016 000–000 13 533 Limitations of the HPS kiln The main application of the HPS lime kiln is the production of low Example of a rotary hopper charging system For kiln shafts with a large cross section area a Increasing lime production while decreasing kiln pluggage through installation of the first LimeFlash lime kiln feed system in North America, TAPPI JOURNAL August 2012Increasing lime production while decreasing kiln pluggage By choosing the right type of igniter Sintrol can significantly improve combustion gas ignition reliability, lime kiln safety and production efficiency Continuous emission management systems CEMS Measuring emissions and caring for the environment are important issues for all of us, Sintrol lime and cement kiln instrumentationUsing Rotary Kilns in Lime Production Rotary kilns account for 90% of lime production in the United States A rotary kiln consists of a long, cylindrical, slightly inclined, refractorylined furnace The limestone and combustion gases pass through the kiln in a countercurrent flow As the limestone moves down the kiln, the limestonePROCESSING • CHARACTERISTICS • PRODUCTION • KILNS • SOLUTIONS
.jpg)
New PFR lime kiln process with blast furnace gas and oxygen
rate and lower thermal efficiency of the lime kiln Table 1 exemplarily shows a comparison of three different cases on a modern 500 t/d PFR lime kiln, operating in accordance with the convention 2 Flowsheet of stateoftheart PFR lime kiln 3 Flowsheet of BFGfired PFR lime kiln according to the new processDolomitic Lime Kiln Dust Safety Data Sheet According to the Hazard Communication Standard (CFR29 19101200) HazCom 2012 and the Hazardous Products Regulations (HPR) WHMIS 2015 10/18/2022 EN (English) 5/15 SECTION 8: Exposure controls/personal protection 81 Control parameters Dolomitic Lime Kiln Dust No additional information availableDolomitic Lime Kiln Dust GraymontWhen lime or water quality is poor and/or when lime consumption rates are high, Carmeuse Systems designs slaking systems utilizing a vertical ball mill The total grinding process of a vertical ball mill utilizes all residual reaction value, Lime Slaking Systems CarmeuseLime Kiln Dust; Kiln Dust; Baghouse Dust CAS REGISTRY NO CAS No N/A DATE REVISED 7/1/2010 Previous versions obsolete Section I – Contact Information MANUFACTURER Greer Lime Company HC 78 Box 93A Riverton, West Virginia 26814 24 Hr Emergency Contact No In WV: (800) 3445133 Outside WV: (800) 5383100 HMIS III SAFETY RATING Health 3GREER LIME COMPANY MATERIAL SAFETY DATA SHEET
.jpg)
Intelligent control system of an industrial lime kiln process
and the "rst lime kiln control system based on fuzzy logic was installed in a Swedish pulp mill in the following year (Ostergaard, 1993) Other industrial, fuzzy logic based kiln control applications have since been reported (Scheuer Principato, 1995; Nilsson, 1997) The "rst rulebased expert system for kiln control was developedAt the invitation of the Dannenfelsbased Schwab GmbH, more than 50 experts from the lime industry met at the headquarters of the MGroup in Lemgo on the occasion of the workshop “New kiln type QualiCal Syn 85” from 10 th to 11 th May 2012 (Fig1)On their completion at Calcis Warstein GmbH Co KG, currently two QualiCal kilns are waiting to be commissioned – one Modern lime kiln technology Cement Lime Gypsum24 Vertical kiln system for lime production 27 25 Parallel flow kiln with left shaft calcining and right shaft preheating 210 26 Fluidized bed kiln responsibility to develop National Emission Standards for Hazardous Air Pollutants (NESHAP) Lime Production: Industry Profilethe final product quality but also in terms of kiln performance n by Pierangelo Bresciani, Valerio Colombari, Gabriele Vola and Luca Sarandrea, Cimprogetti Srl, Italy ICR OCTOBER 2016 I ndustrial lime production needs highgrade limestone and/or pure dolomite resources in widely and longterm available mineral deposits PreliminaryLIME MANUFACTURING Analyse to excel Cimprogetti
.jpg)
An Expert System Application for Lime Kiln Automation Andritz
less than optimal kiln operation and lime quality, and production efficiency suffers The lack of kiln automation cansignificantly limit kiln performance This paper describes a new approach to lime kiln automation that combines the experience of lime kiln operators in an expert system program with a unique adaptive process loop2022年10月1日 The thermal treatment of limestone (mainly CaCO 3) to produce lime (CaO) is a major contributor to CO 2 emissions and the literature on decarbonising the lime industry is scarce Subsequent hydration of lime would lead to the synthesis of slaked/hydrated lime Ca(OH) 2; the production of a tonne of Ca(OH) 2 emits ∼12 tonnes of CO 2 arising mainly from the Decarbonising the lime industry: Stateoftheart ScienceDirectKnowledge of lime kiln operations and safety procedures; What are the working conditions for a Lime Kiln Operator? Lime Kiln Operators usually work in industrial settings such as lime production facilities The working conditions may include: Exposure to high temperatures and dust; Shift work, including nights and weekendsLime Kiln Operator: The Complete Career Guide RoleCatcherproduction process In general, the output method is less certain, as it involves multiplying production data by default emission factors and correction factors for lime kiln dust and hydrated lime based on purity (ie percentage of input that is a carbonate) assumptions In contrast, theTechnical Support Document for the Lime Manufacturing Sector
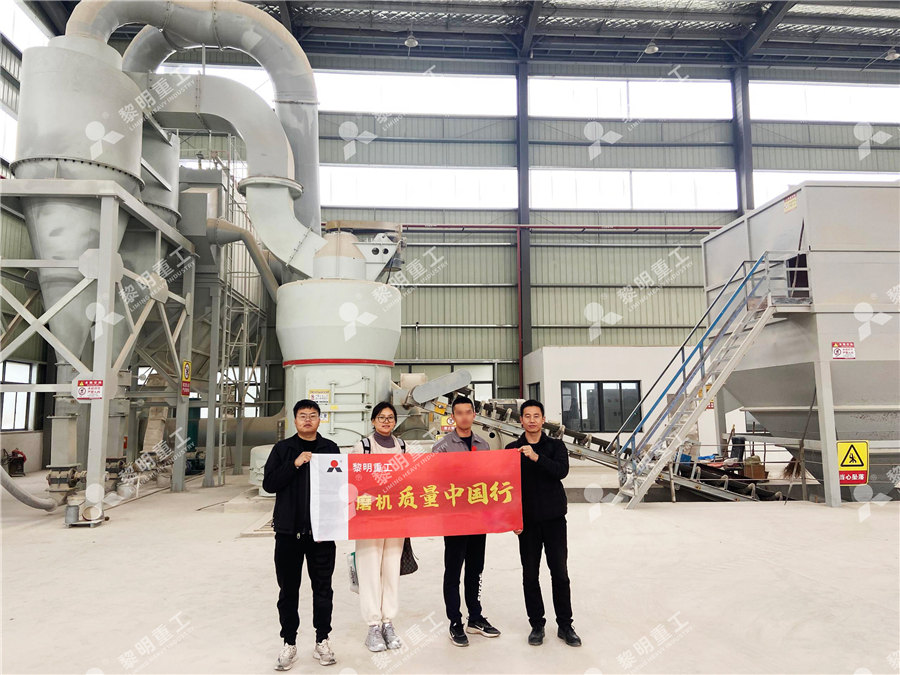
Valmet to deliver a modern lime kiln to Kuantum Papers Limited
2024年11月21日 Valmet is to deliver a modern lime kiln to Kuantum Papers Limited in Punjab, India After the installation of the lime kiln and a satellite cooler, the lime kiln production capacity will increase to 200 tonnes per day The order is included in Valmet's orders received of the fourth quarter 2024 The value of the order will not be disclosedalso be used Lime is also used to improve the properties of soil/aggregate mixtures in “full depth recycling” 2 Lime percentages should be determined by an engineer using a mix design and test protocol A chart to convert lime percentages to weight appears in Appendix D Page 6LIMETREATED SOIL CONSTRUCTION MANUAL2017年3月20日 Synthesis lime kiln with easy and simple lime discharging solution #NEVERSTOPINNOVATING is QualiCal Corporate vision focused on the RD activities driving the progress in the lime field QualiCalLime Kilns – QualiCal – Medium2001年6月1日 The first experiments in applying fuzzy logic to rotary kiln control were carried out at a cement plant in 1978, and the first lime kiln control system based on fuzzy logic was installed in a Swedish pulp mill in the following year (Ostergaard, 1993)Other industrial, fuzzy logic based kiln control applications have since been reported (Scheuer Principato, 1995; Nilsson, 1997)Intelligent control system of an industrial lime kiln process
.jpg)
QualiCal Stateoftheart lime production by Synthesis PFR kiln
2022年7月4日 Actually Synthesis® Kilns are worldwide in operation from the smallest Synthesis®40 with a capacity from 100tpd to the biggest Synthesis®145 with a capacity till 800tpd: n8 of these kilns ABSTRACT: This paper is the first of a twopart series on “green” lime kiln fuels The first part of this work reviews the use of pulp mill and recovery byproducts as either full or partial Alternative “green” lime kiln fuels: Part I—Pulping/recovery 2020年10月28日 One key driver for lime kiln’s energy efficiency is the cooling process where the heat in the hot burned lime is recuperated and heatsup the combustion air For decades, lime kiln coolers were based on satellitebased coolers design where the hot burnt lime is transported through cooler satellite tubes uphill on the periphery on the kiln shellImproved performance with Valmet's new 2stage Lime Kiln CoolerHigh Calcium Lime Kiln Dust Safety Data Sheet According to the Hazard Communication Standard (CFR29 19101200) HazCom 2012 and the Hazardous Products Regulations (HPR) WHMIS 2015 10/18/2022 EN (English) 5/14 SECTION 8: Exposure controls/personal protection 81 Control parameters High Calcium Lime Kiln Dust No additional information availableHigh Calcium Lime Kiln Dust Graymont
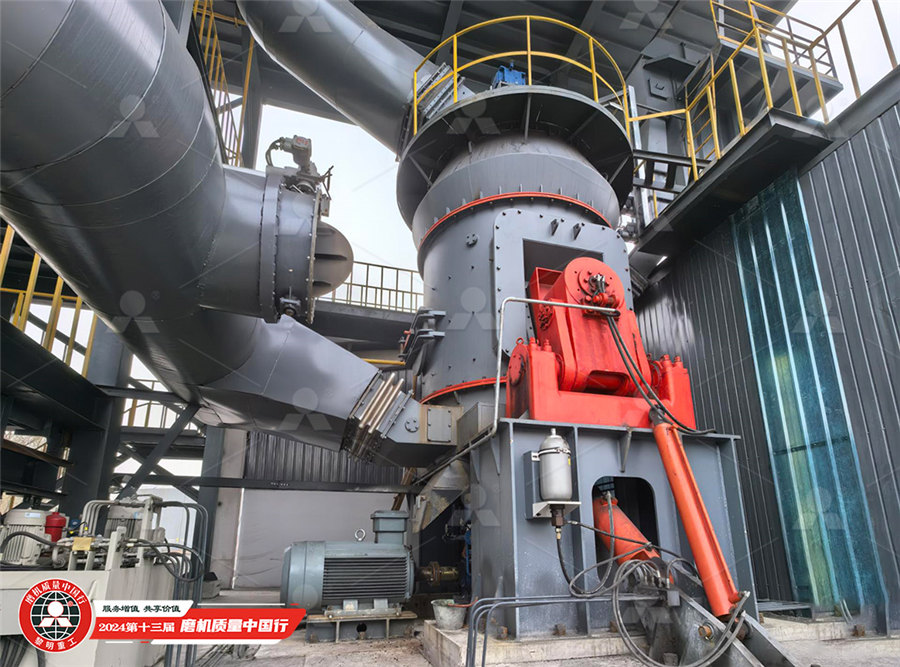
Shandong Wanda Environmental Protection
Shandong Wanda Environmental Protection Technology Co, LtdThe core products include advanced equipment represented by intelligent environmental protection lime kilns, providing customers with overall solutions for intelligent o Because of the high carbon intensity of the lime production processes, pricing carbon directly causes higher costs for lime production Eg, an increase in carbon prices equivalent to €1/tonne CO 2 translates into a lime production average cost increase by €1,1/tonne quicklime (for comparison: EU production costs vary between €55 andA Competitive And effiCient Lime industry European Lime Inspecting the Kiln Regular inspections are essential for identifying potential issues early on and preventing equipment failure When inspecting a lime vertical kiln, it’s important to focus on the following common inspection Maintaining Your Lime Vertical KilnPresent paper attempts to review the literature related to various strategies to design the control system for the Lime kiln industrial process Lime Kiln is multivariable process with complex interactions of variables It has higher degree of coupling, severe non linearities, and frequent disturbances This paper covers the modeling and control aspects of Lime Kiln process The Modeling, Control and Instrumentation of Lime Kiln Process: A
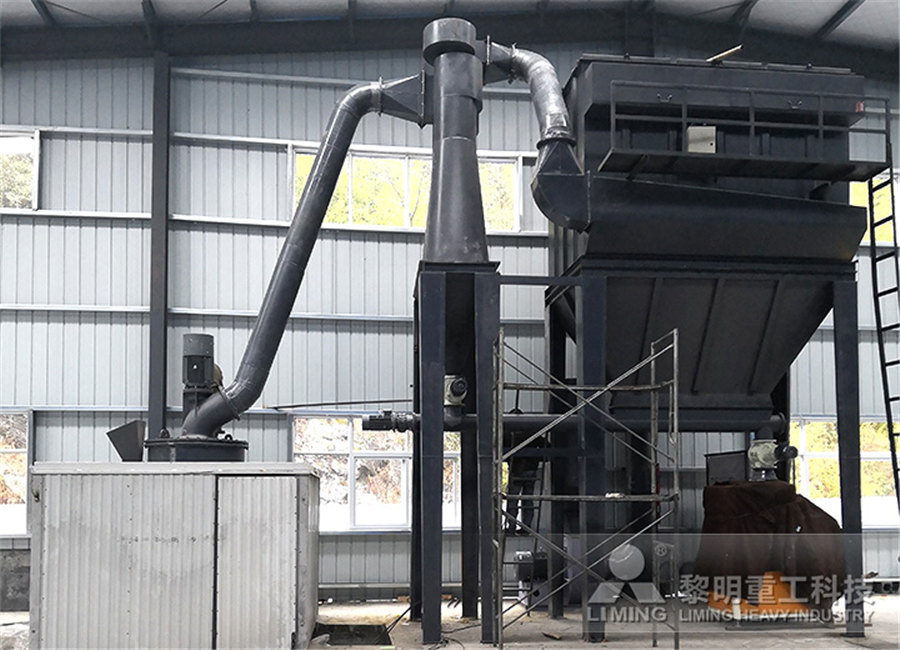
22 Lime Kiln Principles and Operations TAPPI
8 Slide 15 Lime Kiln Heat Rate • Heat rate is a measure of energy efficiency – Units are MM Btu/ton CaO or GJ/tonne CaO – Often stated as MM Btu/ton “product” • Typical range – 5 to 9 MM Btu/ton CaO – 58 to 105 GJ/tonne CaO – Lower is better Slide 16 Lime Kiln Energy Balance Components • Drying • Calcining : CaCO3 + heat ÄCaO + CO2 • Losses – Heat loss through 76 Hannes Piringer / Energy Procedia 120 (2017) 75–95 2 Hannes Piriner/ Energy Procedia 00 (2017) 000–000 The idea of this paper is to illustrate the following topics: impact of market Lime Shaft Kilns ResearchGate2017年8月1日 Published by Elsevier Ltd Peerreview under responsibility of the organizing committee of INFUB11 101016 000–000 13 533 Limitations of the HPS kiln The main application of the HPS lime kiln is the production of low Example of a rotary hopper charging system For kiln shafts with a large cross section area a Lime Shaft Kilns ScienceDirectIncreasing lime production while decreasing kiln pluggage through installation of the first LimeFlash lime kiln feed system in North America, TAPPI JOURNAL August 2012Increasing lime production while decreasing kiln pluggage
.jpg)
Sintrol lime and cement kiln instrumentation
By choosing the right type of igniter Sintrol can significantly improve combustion gas ignition reliability, lime kiln safety and production efficiency Continuous emission management systems CEMS Measuring emissions and caring for the environment are important issues for all of us, Using Rotary Kilns in Lime Production Rotary kilns account for 90% of lime production in the United States A rotary kiln consists of a long, cylindrical, slightly inclined, refractorylined furnace The limestone and combustion gases pass through the kiln in a countercurrent flow As the limestone moves down the kiln, the limestonePROCESSING • CHARACTERISTICS • PRODUCTION • KILNS • SOLUTIONS