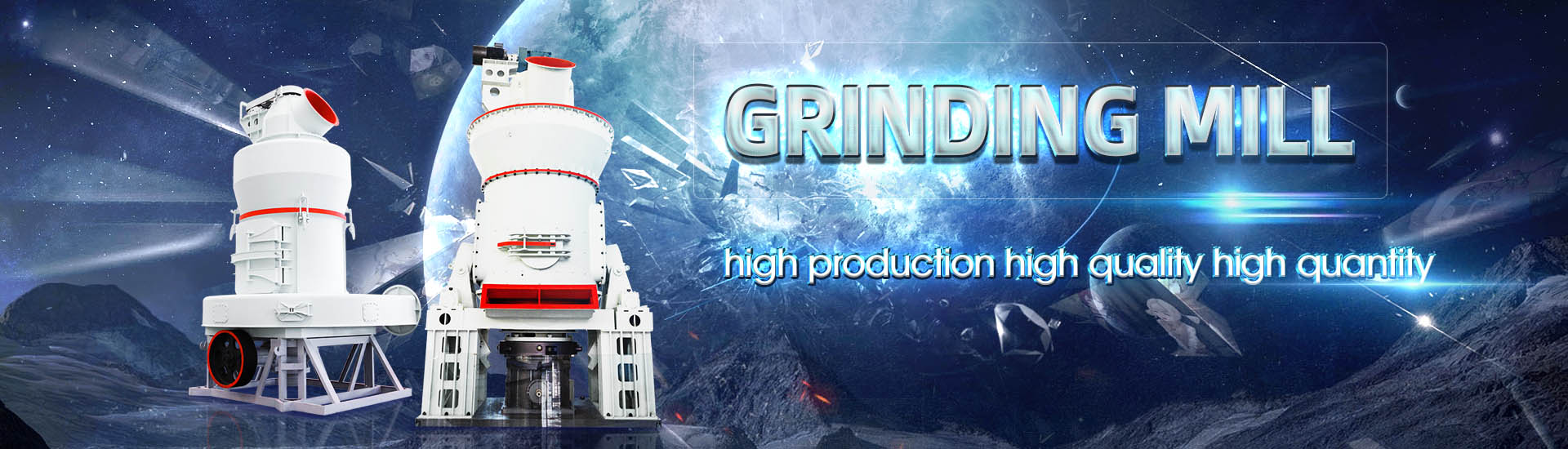
HOME→During the clinker calcination process, which chemical components of coal will affect the quality of clinker
During the clinker calcination process, which chemical components of coal will affect the quality of clinker
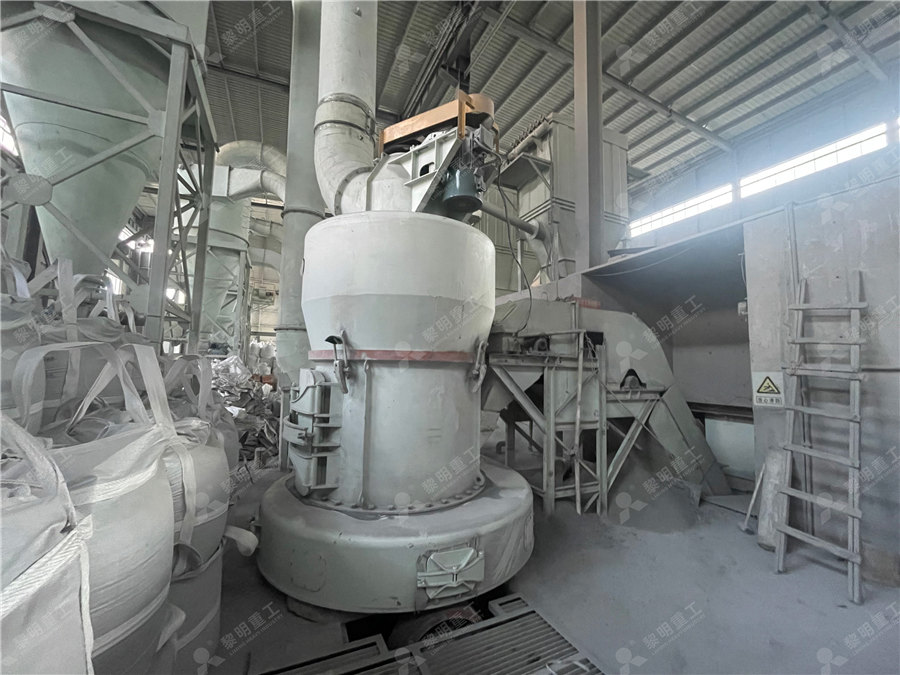
Clinker: reactions in the kiln Understanding Cement
This includes: 1 Water evaporation in the raw feed, if any 2 Loss of carbon dioxide from the limestone (ie: calcining) 3 Decomposition of the siliceous and aluminosilicate fractions of the feed 4 Formation of a sulfate melt phase The decomposition products react with lime to form intermediate 展开Calcination is the main process of clinker production, calcining calcium carbonate (CaCO 3) at about 900 °C to form calcium oxide, CaO, lime, and the release of carbon dioxide gas (CO 2) Clinker Production an overview ScienceDirect TopicsThey reported that the introduced trace elements in mixing sludge played an important role as mineralizers and cosolvents in cement sintering by reducing the eutectic point of the system Cement Clinker Production an overview ScienceDirect Topics2015年12月1日 The CaSiBi technology is characterized by a calcination process at temperatures between 400 and 500 °C after the autoclave without grinding The product of this Research review of cement clinker chemistry ScienceDirect
.jpg)
Process characteristics of clinker and cement production SINTEF
CaCO3 => CaO + CO2 ca 3510 MJ/t clinker (CSI GNR2014) ca 110 kWh/t cement (VDZ) tested in the second campaign showing streamlines coloured by temperature Considerably Abstract: In order to avoid environmental pollution from Coal gangue (CG) and copper tailings (CT), the utilization as cement clinker calcinations was experimentally investigated Low Utilization of Coal Gangue and Copper Tailings as Clay for Cement 2014年12月1日 In this research, energetic andexergetic analysis of calcium oxide formation, CO2 emissions, and environmental effects during the clinker production process in rotary Thermodynamic and Environmental Impact Assessment of Calcium Carbon dioxide (CO2) is a byproduct of a chemical conversion process used in the production of clinker, a component of cement, in which limestone (CaCO3) is converted to lime (CaO) CO2 31 CO2 Cement Production IGES
.jpg)
The properties and hydration of a calcined coal series metakaolin
2024年4月29日 To enhance the application of coal series kaolinite clay in the cement industry, the properties and hydration of ternary system based on calcined coal series metakaolin The calcination of limestone and the combustion of fossil fuels are the two major sources of carbon emissions during clinker production In the calcination process, calcium carbonate (CaCO 3) is decomposed to calcium oxide (CaO) and CO 2, a chemical reaction contributing to 60–65 % of carbon emissions related to clinker production [27, 28]Cement Clinker Production an overview ScienceDirect TopicsUpon addition of water, clinker minerals react to form different types of hydrates and "set" (harden) as the hydrated cement paste becomes concreteThe calcium silicate hydrates (CSH) (hydrates of alite and belite minerals) represent the main "glue" components of the concrete After initial setting the concrete continues to harden and to develop its mechanical strengthCement clinker Wikipedia2024年10月1日 Currently, the hightemperature heat source (550–1450 °C) during the decomposition and sintering process of Portland cement clinker is mainly provided by coal, the standard coal consumption in cement clinker production is between 92 kg/t and 128 kg/t [2, 8], and the average thermal energy intensity is 36GJ/t clinker in 2022, of which approximately Technology verification of Portland cement clinker production
.jpg)
Cement Clinker Manufacturing Process with Reactions
Extraction and Preparation of Raw Materials The main raw materials (limestone, clay chalk or basalt) are quarried from natural rocks They are crushed and transferred to preblending storage where other substances (such as sand, iron ore, bauxite, shale, slag, fly ash) are added to get the desired chemical compositionThe impact of coating layers on the clinker production process within a rotary kiln burning both coal and Refuse Derived Fuel (RDF) was investigated in one study [7], showing that a thin coating Clinker formation process in a modern plant rotary kilnDownload scientific diagram Calcination process of cement clinker from publication: A Synchronous Prediction Model Based on MultiChannel CNN with Moving Window for Coal and Electricity Calcination process of cement clinker ResearchGateproduct of a chemical conversion process used in the production of clinker, a component of cement, in which limestone (CaCO3) is converted to lime (CaO) CO2 is also emitted during cement production by fossil fuel combustion and is accounted for elsewhere However, the CO2 from fossil fuels is accounted for elsewhere in31 CO2 Cement Production IGES
.jpg)
Clinkerization Cement Plant Optimization
The overall process of conversion from raw meal to clinker being endothermic demands a theoretical heat of about 380420 kcal/kgclinker However, the rest of the specific heat consumption as tabulated above constitutes heat losses from preheater exhaust gases, clinker, cooler exhaust gases, preheater dust and radiation lossesreactions and distribution of chromium in clinkerproduced using steel slagduring calcination In this study, cement clinker was produced using steel slags with different chromium contents, and the relationships between the chromium content of the raw meal precursor, calcination temperature, and the Cr6+ contents of clinker were exploredReactions of Chromium during the Calcination of Cement Clinker 2024年6月1日 This transformation is achieved through a process called calcination During calcination, limestone, which contains a significant amount of calcium carbonate, is subjected to high temperatures in a kiln As a result, the limestone undergoes chemical decomposition, releasing carbon dioxide into the atmosphere [[70], [71], [72]]Decarbonising cement and concrete production: Strategies, Continuous high temperature process in the cement industry: Calcination and cement clinker burning Calcination of raw material CaCO 3 => CaO + CO 2 Process emissions of raw material: = 054 t CO 2 /t clinker Endotherm reaction at 950 °C ca 1700 MJ/t clinker ≈ 50% of energy Cement clinker burning at 1450 °C formation of hydraulicProcess characteristics of clinker and cement production SINTEF
.jpg)
Thermodynamic modelling of cements clinkering process as a tool
2023年10月16日 The valorisation of waste or byproducts in Portland clinker production is a promising alternative for developing sustainable cements The complexity of the chemical reactions during clinkering 2019年7月1日 Cement clinker calcination in rotary kiln is an energy intensive process Heat recovery from the kiln shell surface is a potential way to improve energy efficiency to make cement production cleaner and more sustainable In this work, methods were proposed to assess the heat loss through the kiln shell and its influencing factors, using an industrial cement kiln in Improving the sustainability of cement clinker calcination process Download scientific diagram Schematics of the clinker calcination process from publication: An Interval Type2 Fuzzy Controller Based on DataDriven Parameters Extraction for Cement Calciner Schematics of the clinker calcination process ResearchGateresponsible for 35% of clinker’s carbon footprint The other 65% are process emissions, released during the calcination reaction involved in the production of clinker Headlines Fossil fuel combustion to meet heat ing needs account s for 35% of cement’s CO 2 emissions The remaining 65% are due to direct processDeep decarbonisation of industry: The cement sector Europa
.jpg)
Portland Cement Clinker an overview ScienceDirect Topics
The process that cement raw materials is sintered in a kiln is the key to the quality of cement clinker In the sintering process of cement raw material, the useful components decomposed by various raw materials at 1000 °C are mainly: calcium oxide (CaO), silicon dioxide (SiO 2), aluminum oxide (Al 2 O 3), and ferric oxide (Fe 2 O 3)Calcination B Rand, in Concise Encyclopedia of Advanced Ceramic Materials, 1991 Publisher Summary This chapter explains calcination, which refers to the heating of inorganic materials to remove volatile componentsThe release of volatile matter during calcination minimizes internal shrinkage in later processing steps that can lead to the development of internal stresses and, Calcination an overview ScienceDirect Topics2024年7月21日 During calcination process of cement clinker, natural fluorapatite will decompose accompany with the existence of C2S at 1100 °C As a result, fluorine will react with CaO and Al2O3 to form C11A7 (PDF) Effects of Fineness and Morphology of Quartz in Siliceous 2022年4月12日 Carbon dioxide (CO2) emissions from China’s cement production process have increased rapidly in recent decades, comprising the secondlargest source of CO2 emissions in the country, next only to China’s provincial process CO2 emissions from cement production
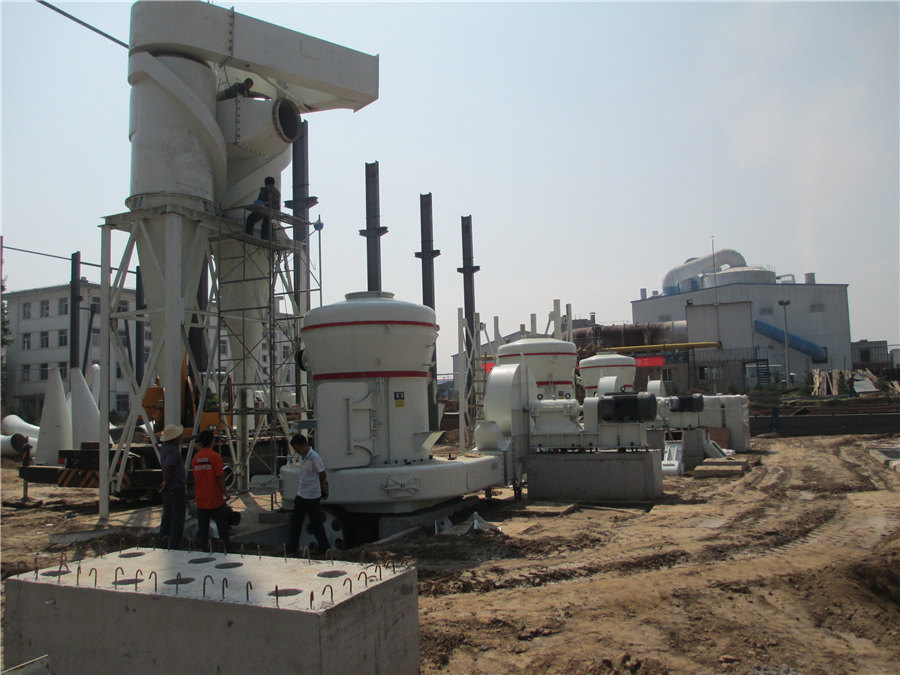
Cement Manufacturing Process and Its Environmental Impact
2023年7月10日 The cement manufacturing process involves the extraction and processing of raw materials, such as limestone, clay, and shale, which are then heated in a kiln at high temperatures to form clinker2023年1月1日 This paper proposes a modeling and optimization method for cement clinker calcination process based on gaussian process regression ensemble (EGPR) model and steadystate detectionResearch on Modeling and Optimization Method of 2015年12月1日 It is known that minor or trace components derived from raw materials or fuels affect both clinker formation and reactivity During the past years, continuous efforts have been made to study the incorporation of various foreign ions (alone or in combinations) in the cement clinker and their effects on the clinker formation and cement propertiesResearch review of cement clinker chemistry ScienceDirect2023年1月7日 The cement industry is undeniably critical for the global economy However, they are also the largest energy consumers in the world The clinker manufacturing process causes gaseous emissions like nitrogen oxides, sulfur dioxide, carbon dioxide and particulate matter There is scope for various technologies to be used in the cement manufacturing process for Emission reduction through process integration and exploration
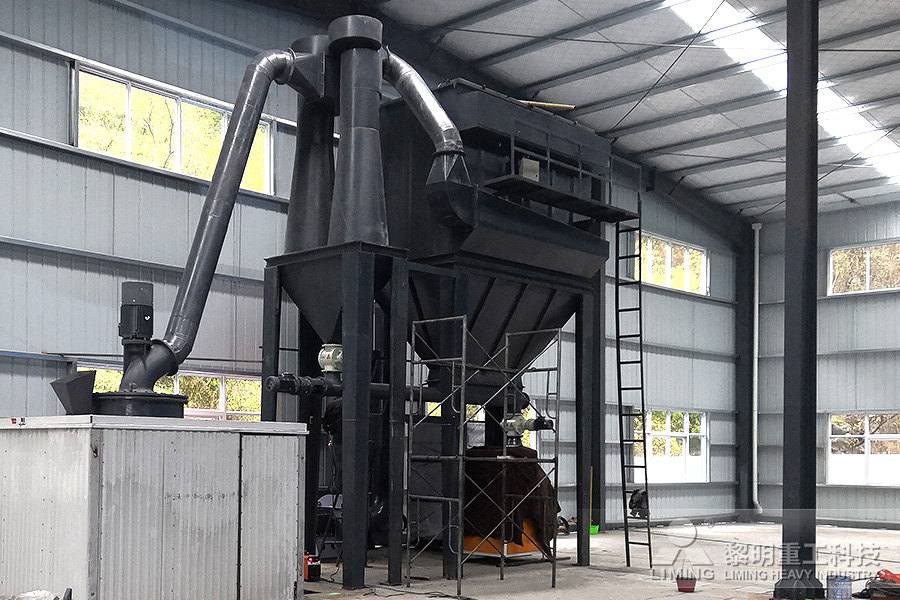
What is Calcination? FEECO International Inc
Calcination is the process of heating a solid material in order to cause chemical separation of its components The diversity of chemical separation lends calcination to accomplishing a range of objectives, from the removal of chemically bound (crystalline) water, to the volatilization of contaminants from a source material, thermal decomposition, and even phase changes2020年9月9日 The multivariable and nonlinear nature of the clinker production process has triggered a control challenge that, during the last years, has attracted the attention of researchers and practioneers In the control literature, different solutions for the clinker production phase control and optimization are present; different ways to model and manage the process Optimization of the Clinker Production Phase in a Cement Plant 2014年1月1日 Process is controlled by diffusion and during its progress two reaction regions are established: C 3 S + melt M a –M b and C 2 S + melt M b –M c –M d –M e nearby the ash liquid phase During the process the mean clinker composition is laying on the line linking the points C Portland Cement Clinker SpringerLinkand pulverized coal is the fuel typically used for this purpose in the cement industry Coal can in many cases be replaced by different types of alternative fuels, but this may impact process conditions, emissions or product quality In this study, CFD simulations were carried out to investigate the possibility to replace 50 %Numerical Modelling of the Calcination Process in a Cement
.jpg)
Effects of carbonaceous matter additives on kinetics, phase and
2018年12月1日 Unlike the calcination of natural kaolin, there is still a certain amount of carbon in coal gangue, which is another essential component that affects kaolinite activation during calcination [26]coal ash characteristics and its influence on kiln productivity and the clinker quality INTRODUCTION Coal is a major source of the fuel for the cement manufacture in India In recent years the coal quality has become severe constraint for the cement manufacturers To resolve this problem several aEFFECT OF COAL ASH CHARACTERISTICS ON KILN PERFORMANCE AND CLINKER QUALITY2021年1月1日 The results showed that the manufacture of cement clinker at 15% substitution of coal at 1300 o C obtained a CaO compound of 66384% and SiO2 of 22747% with sample results close to ASTM (PDF) The Effect of Addition Basalt Stone and Coal as Substitution The calcination of limestone and the combustion of fossil fuels are the two major sources of carbon emissions during clinker production In the calcination process, calcium carbonate (CaCO 3) is decomposed to calcium oxide (CaO) and CO 2, a chemical reaction contributing to 60–65 % of carbon emissions related to clinker production [27, 28]Cement Clinker Production an overview ScienceDirect Topics
.jpg)
Cement clinker Wikipedia
Upon addition of water, clinker minerals react to form different types of hydrates and "set" (harden) as the hydrated cement paste becomes concreteThe calcium silicate hydrates (CSH) (hydrates of alite and belite minerals) represent the main "glue" components of the concrete After initial setting the concrete continues to harden and to develop its mechanical strength2024年10月1日 Currently, the hightemperature heat source (550–1450 °C) during the decomposition and sintering process of Portland cement clinker is mainly provided by coal, the standard coal consumption in cement clinker production is between 92 kg/t and 128 kg/t [2, 8], and the average thermal energy intensity is 36GJ/t clinker in 2022, of which approximately Technology verification of Portland cement clinker production Extraction and Preparation of Raw Materials The main raw materials (limestone, clay chalk or basalt) are quarried from natural rocks They are crushed and transferred to preblending storage where other substances (such as sand, iron ore, bauxite, shale, slag, fly ash) are added to get the desired chemical compositionCement Clinker Manufacturing Process with ReactionsThe impact of coating layers on the clinker production process within a rotary kiln burning both coal and Refuse Derived Fuel (RDF) was investigated in one study [7], showing that a thin coating Clinker formation process in a modern plant rotary kiln
.jpg)
Calcination process of cement clinker ResearchGate
Download scientific diagram Calcination process of cement clinker from publication: A Synchronous Prediction Model Based on MultiChannel CNN with Moving Window for Coal and Electricity product of a chemical conversion process used in the production of clinker, a component of cement, in which limestone (CaCO3) is converted to lime (CaO) CO2 is also emitted during cement production by fossil fuel combustion and is accounted for elsewhere However, the CO2 from fossil fuels is accounted for elsewhere in31 CO2 Cement Production IGESThe overall process of conversion from raw meal to clinker being endothermic demands a theoretical heat of about 380420 kcal/kgclinker However, the rest of the specific heat consumption as tabulated above constitutes heat losses from preheater exhaust gases, clinker, cooler exhaust gases, preheater dust and radiation lossesClinkerization Cement Plant Optimizationreactions and distribution of chromium in clinkerproduced using steel slagduring calcination In this study, cement clinker was produced using steel slags with different chromium contents, and the relationships between the chromium content of the raw meal precursor, calcination temperature, and the Cr6+ contents of clinker were exploredReactions of Chromium during the Calcination of Cement Clinker
.jpg)
Decarbonising cement and concrete production: Strategies,
2024年6月1日 This transformation is achieved through a process called calcination During calcination, limestone, which contains a significant amount of calcium carbonate, is subjected to high temperatures in a kiln As a result, the limestone undergoes chemical decomposition, releasing carbon dioxide into the atmosphere [[70], [71], [72]]