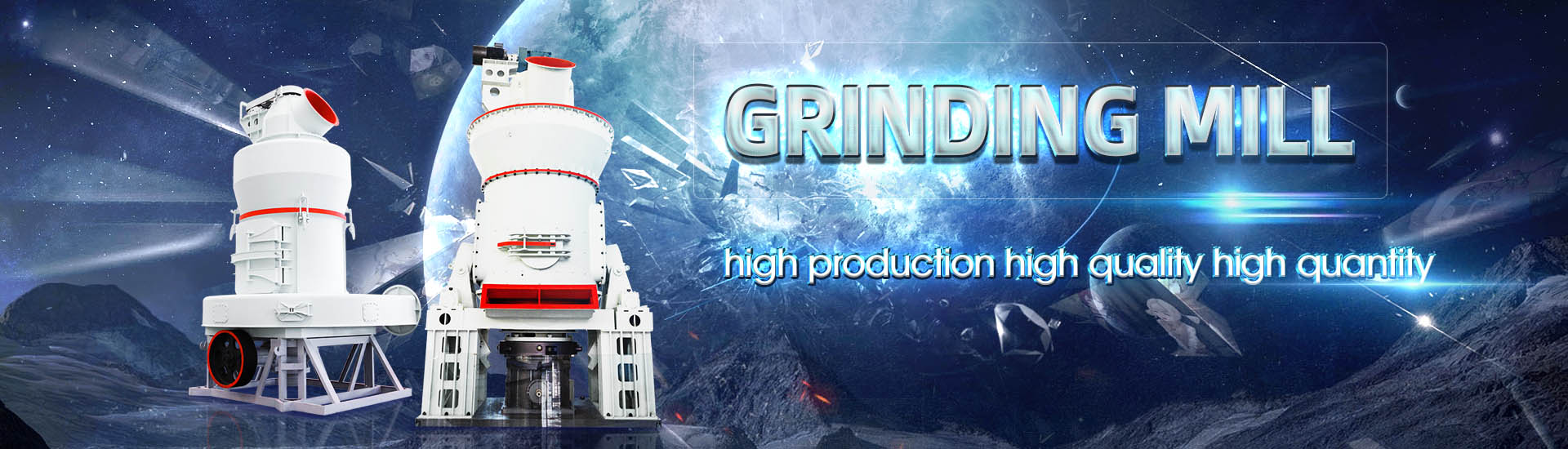
Process flow of black iron oxide production line
.jpg)
Coprecipitation synthesis of stable iron oxide nanoparticles with
2020年11月1日 Early reaction stages of a coprecipitation synthesis were studied via insitu synchrotron XRD and SAXS A stabilisation procedure was developed, not requiring any ultra A process for the production of iron oxide black pigments by reaction or aromatic nitro compounds with metallic iron, optionally with addition of control chemicals, to form finelyEPB1 Manufacturing process for black iron oxide 2020年6月1日 Coprecipitation is by far the most common synthesis for magnetic iron oxide nanoparticles (IONPs), as cheap and environmentally friendly precursors and simple experimental procedures(PDF) CoPrecipitation Synthesis of Stable Iron Oxide 2024年8月7日 To tackle the limitations of translating high temperature IONP synthesis to high scale flow, Besenhard et al 1 have introduced an innovative modular hightemperature flow Translating batch to flow: New procedures for optimizing iron
.jpg)
Primary Metal Production Michigan Technological University
General Principles of Production of Metals by Pyrometallurgy In pyrometallurgy, metals are extracted by converting sulfides into oxides and then reducing oxides into metals, using To tackle the limitations of translating high temperature IONP synthesis to high scale flow, Besenhard et al1have introduced an innovative modular hightemperature flow reactor de Translating batch to flow: New procedures for optimizing iron oprecipitation and reduction reactions using iron (III) nitrate precursor and sodium hydroxide as reducing agents The iron oxide NPs were characterized using tranSynthesis of iron oxide nanoparticles in a continuous flow spiral 2024年8月7日 To tackle the limitations of translating high temperature IONP synthesis to high scale flow, Besenhard et al have introduced an innovative modular hightemperature flow Translating batch to flow: New procedures for optimizing iron
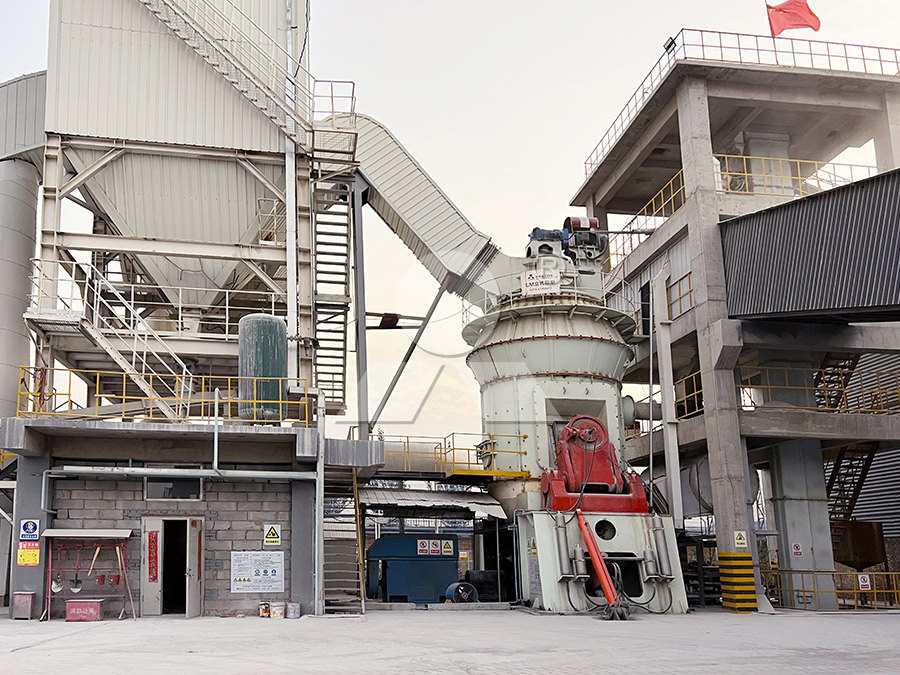
Black Oxide Finishing for Gears Gear Solutions Magazine Your
2010年3月1日 Ruggedly designed for high volume continuous service, a CNC low temperature black oxide line usually consists of eight process tanks and 10 stations overall For example, in one installation the operator of the deburring station loads parts onto the black oxide racks and then wheels them into the pickup station2013年3月16日 Degree of metallization of DRI is the extent of conversion of iron oxide into metallic iron during DRI production process The DRI production process involves the intimate ranging from 800 deg C to 1050 deg C is Direct Reduced Iron and its Production Processes – Fig 1 Integration of the chloriron process with lowcarbon electricity, Cl 2, and electric arc furnace markets (A) Iron ore electrolysis, fed by abundant iron oxide, seawater, and zerocarbon electricity, can support further deployment of infrastructure for a netzeroemissions energy system (B) Colocation ofElectrochemical ChlorIron Process for Iron Production from Iron Oxide 2016年3月30日 In book: Encyclopedia of Iron, Steel, and Their Alloys (pppp 10821108) Chapter: i) Direct Reduced Iron: Production; Publisher: CRC Press, Taylor and Francis Group, New York(PDF) i) Direct Reduced Iron: Production ResearchGate
.jpg)
Synthesis, Properties, and Applications of Iron Oxides: Versatility
2021年5月18日 21 Iron (III) Oxides Iron (III) oxide is, of course, a compound that exhibits four different crystalline polymorphs: αFe 2 O 3, βFe 2 O 3, γFe 2 O 3, and εFe 2 O 3Hematite and maghemite usually appear in nature, while beta and epsilon structures are generally synthetic oxides [10, 11]In general, the iron (III) oxides anions arrange in closepacked structures, The production of iron from its ore involves a redox reaction carried out in a blast furnace The furnace is filled at the top with the iron ore oxide most commonly hematite (\(Fe2O3\)) but can also magnetite (\(Fe3O4\)), As the process continue the molten iron flow down through the furnace and collects at the bottom, Iron Production Chemistry LibreTexts2023年4月5日 The blast furnace and direct reduction processes have been the major iron production routes for various iron ores (ie goethite, hematite, magnetite, maghemite, siderite, etc) in the past few decades, but the challenges of maintaining the iron and steelmaking processes are enormous The challenges, such as cumbersome production routes, scarcity of Recent Trends in the Technologies of the Direct Reduction and 2024年6月11日 Sustainable and highly efficient production of highpurity iron from oxide ores by acidic electrowinning in anionrich electrolytes June 2024 DOI: 1026434/chemrxiv2024stwdnSustainable and highly efficient production of highpurity iron
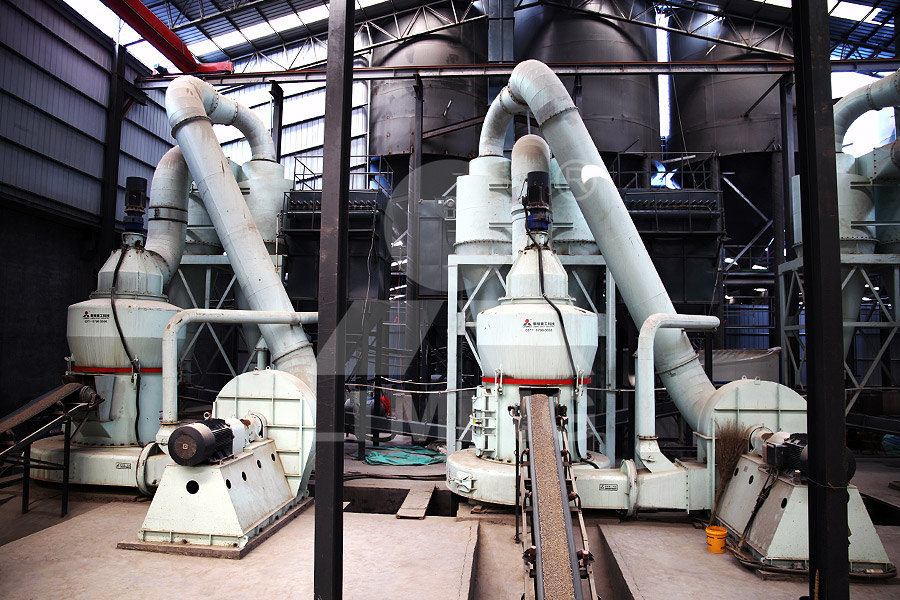
Electrochemical chloriron process for iron production from iron oxide
2024年2月5日 Electrochemical chloriron process for iron production from iron oxide and salt water Berkley B Noble, 1,2Anastasiia Konovalova, Louka J Moutarlier, 1,2 Valerie Brogden, 3 and Paul A Kempler1 ,2 4 * region used to compare market size are shown by a dotted line ll 716 Joule 8, 714–727, March 20, 2024 Article2018年7月11日 Iron Ores and Iron Oxide Materials 50 Bentonite, an inorganic binder, has been the main binder used in the iron ore pelletizing process since the beginning of pellet production in the 1950sIron Ore Pelletizing Process: An Overview ResearchGateA NEW BENCHMARK FOR IRON OXIDE PRODUCTION LANXESS Inorganic Pigments Group represents a consistent combination of environmental responsibility, efficiency and quality In line with these objectives, and based on our 90 years of experience, we have once again set a milestone in the production of synthetic iron oxide pigments atCONQUER NEW TERRITORIES Palmer Holland2011年4月19日 This novel technology electrolyzes iron oxide into metallic iron that is of crude steel quality (Allanore, Ortiz and Sadoway, 2011; Allanore, 2014;Wiencke et al, 2018)Molten Oxide Electrolysis for Iron Production:
.jpg)
Black Oxide: All You Need to Know okdor
Home Black Oxide: All You Need to Know The process of black oxide treatment has been a trendy yet underappreciated metal finishing technique used to protect and add aesthetic value to various components, parts, and devices In this 1 A process for the production of iron oxide black pigments by reaction or aromatic nitro compounds with metallic iron, optionally with addition of control chemicals, to form finely divided pigments consisting predominantly of Fe3 O4 , characterized in that the finely divided pigments thus produced are subjected to a heat treatment at 200 to 800 degrees C in a nonoxidizing EPB1 Manufacturing process for black iron oxide 2024年11月4日 Carbon monoxide reduces the iron(III) oxide in the iron ore to form iron This will melt and collect at the bottom of the furnace, where it is tapped off iron(III) oxide + carbon monoxide → iron + carbon dioxide Limestone (calcium carbonate) is added to the furnace to remove impurities in the oreExtraction of iron IGCSE Chemistry Revision Notes Save My A process for the production of a black iron oxide pigment from Fe 2 O 3 hematite iron oxide which may be an impure oxide produced by the “Ruthner” process or by other means, or which may be a mineral hematite The process may be used to upgrade poor quality synthetic or natural hematite, or to improve their performance as red pigments, by conversion to black pigment Process for the production of black iron oxide pigments
%3C1PGHL[2}HK_]YT.jpg)
Lithiumion Battery Cell Production Process ResearchGate
2019年2月6日 PDF The first brochure on the topic "Production process of a lithiumion battery cell" is dedicated to the production process of the lithiumion cell Find, read and cite all the research A process for the production of iron oxide yellow pigments by the PennimanZoph process from the raw materials iron (II) sulfate, sodium hydroxide and metallic iron, is disclosed in which iron (II) is oxidized to iron (III) by gassing with air in the presence of goethite nuclei, the iron (III) sulfate is dissolved to form iron (II) and the goethite nuclei are built up to iron oxide yellow Process for the production of iron oxide yellow pigments2022年4月30日 Iron oxide nanoparticles have been of great interest due to their physical and chemical properties, and the coprecipitation method is among the main ways to produce them Despite being the cheapest and most straightforward method, its main disadvantage during the scaleup process is the increase in the nanoparticle’s polydispersity and the reactor’s Automation of a lowcost device for flow synthesis of iron oxide 2022年9月1日 The predominant component of the black powder was iron oxide or iron sulfide, according to certain early studies [14], [15], and the black powder also contained ferric hydroxide, ferrous carbonate, and sulfur, according to some reports [16]The presence of these components indicates that the black powder results from internal corrosion occurring in the pipeline [10], [17]Generation causes of black powder in the east line of the gas
.jpg)
Molten Oxide Electrolysis for Iron Production: Identification of
The minimum specific electrical energy need for an autothermal cell is the1 ien 6 1805 MJtFe"0 kWhtFe"1, for a faradaic efficiency of unityTwo key process parameters are then needed to reach 2024年8月7日 The precise tuning of iron oxide nanoparticles (IONPs) to achieve controlled sizes is crucial for numerous applications High temperature synthesis is most appropriate to achieve small, uniform sizes but suffers from challenges with reproducibility and scaleup Flow chemistry/engineering approaches are gaining popularity to address nanoparticle (NP) Translating batch to flow: New procedures for optimizing iron oxide 2011年11月1日 The behaviour of an iron oxide sample (Fe2O3) during successive reduction–oxidation cycles (steam–iron process) has been investigated by means of a thermobalance system acting as a Oxidation reaction kinetics for the steamiron process in 2020年3月19日 Iron Oxide Nanoparticle, maghemite (γFe2O3) has received great interest and extensively used in biomedical field Optimization studies were carried out in the production of γFe2O3 Production of Iron Oxide Nanoparticles by CoPrecipitation
.jpg)
Development of technology for the production of natural red iron oxide
2017年1月1日 The most common inorganic pigment is red iron oxide World production of iron oxide pigments is about 600 thousand tons per year and greatly exceeds the production of other color pigments, with 2023年4月5日 Recent Trends in the Technologies of the Direct Reduction and Smelting Process of Iron Ore/Iron Oxide in the Extraction of Iron and Steelmaking April 2023 DOI: 105772/intechopen(PDF) Recent Trends in the Technologies of the Direct2021年1月4日 Until the late 19th century iron oxide pigments were obtained wholly from natural materials, generally with little alteration other than physical purification In some cases roasting or calcination was also carried out However, beginning in the first part of the 20th century, chemical methods were developed for synthetic production of commercial iron oxidesIron Oxide Pigments 911Metallurgist2017年4月9日 Midrex is an ironmaking process, developed for the production of direct hot DRI (HDRI) and/or hot briquetted iron (HBI) The process flow sheet is en givat Fig 2 Fig 2 and converted to DRI The reducing gas, which is primarily hydrogen (H2) and carbon mono oxide (CO), reacts with the iron oxide (Fe2O3) to reduce ie to Midrex Process for Direct Reduction of Iron Ore – IspatGuru
.jpg)
1A Manufacturing Process for Iron and Steel
The figure shows a flowchart of the integrated manufacturing process for iron and steel using the blast furnace and basic oxygen furnace hereinafter, respectively), which is presently the most commonly used method (51% of world steel production) After the BFBOF process, and iron oxide (Fe 2 O 3) The residual oxygen, 2023年4月27日 Static magnetic properties of various samples of silicairon oxide systems: (a)Hysteresis loop and backfield demagnetization curve of a sample containing εFe 2 O 3 (PDF) Diversity of Iron Oxides: Mechanisms of Formation, Physical 2010年3月1日 Ruggedly designed for high volume continuous service, a CNC low temperature black oxide line usually consists of eight process tanks and 10 stations overall For example, in one installation the operator of the deburring station loads parts onto the black oxide racks and then wheels them into the pickup stationBlack Oxide Finishing for Gears Gear Solutions Magazine Your 2013年3月16日 Degree of metallization of DRI is the extent of conversion of iron oxide into metallic iron during DRI production process The DRI production process involves the intimate ranging from 800 deg C to 1050 deg C is Direct Reduced Iron and its Production Processes –
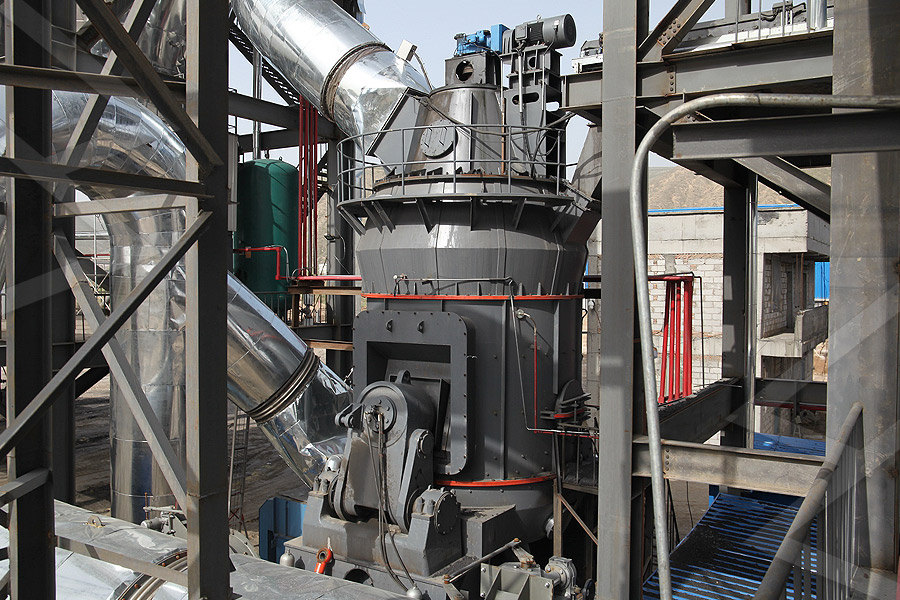
Electrochemical ChlorIron Process for Iron Production from Iron Oxide
Fig 1 Integration of the chloriron process with lowcarbon electricity, Cl 2, and electric arc furnace markets (A) Iron ore electrolysis, fed by abundant iron oxide, seawater, and zerocarbon electricity, can support further deployment of infrastructure for a netzeroemissions energy system (B) Colocation of2016年3月30日 In book: Encyclopedia of Iron, Steel, and Their Alloys (pppp 10821108) Chapter: i) Direct Reduced Iron: Production; Publisher: CRC Press, Taylor and Francis Group, New York(PDF) i) Direct Reduced Iron: Production ResearchGate2021年5月18日 21 Iron (III) Oxides Iron (III) oxide is, of course, a compound that exhibits four different crystalline polymorphs: αFe 2 O 3, βFe 2 O 3, γFe 2 O 3, and εFe 2 O 3Hematite and maghemite usually appear in nature, while beta and epsilon structures are generally synthetic oxides [10, 11]In general, the iron (III) oxides anions arrange in closepacked structures, Synthesis, Properties, and Applications of Iron Oxides: Versatility The production of iron from its ore involves a redox reaction carried out in a blast furnace The furnace is filled at the top with the iron ore oxide most commonly hematite (\(Fe2O3\)) but can also magnetite (\(Fe3O4\)), As the process continue the molten iron flow down through the furnace and collects at the bottom, Iron Production Chemistry LibreTexts
.jpg)
Recent Trends in the Technologies of the Direct Reduction and
2023年4月5日 The blast furnace and direct reduction processes have been the major iron production routes for various iron ores (ie goethite, hematite, magnetite, maghemite, siderite, etc) in the past few decades, but the challenges of maintaining the iron and steelmaking processes are enormous The challenges, such as cumbersome production routes, scarcity of 2024年6月11日 Sustainable and highly efficient production of highpurity iron from oxide ores by acidic electrowinning in anionrich electrolytes June 2024 DOI: 1026434/chemrxiv2024stwdnSustainable and highly efficient production of highpurity iron 2024年2月5日 Electrochemical chloriron process for iron production from iron oxide and salt water Berkley B Noble, 1,2Anastasiia Konovalova, Louka J Moutarlier, 1,2 Valerie Brogden, 3 and Paul A Kempler1 ,2 4 * region used to compare market size are shown by a dotted line ll 716 Joule 8, 714–727, March 20, 2024 ArticleElectrochemical chloriron process for iron production from iron oxide 2018年7月11日 Iron Ores and Iron Oxide Materials 50 Bentonite, an inorganic binder, has been the main binder used in the iron ore pelletizing process since the beginning of pellet production in the 1950sIron Ore Pelletizing Process: An Overview ResearchGate