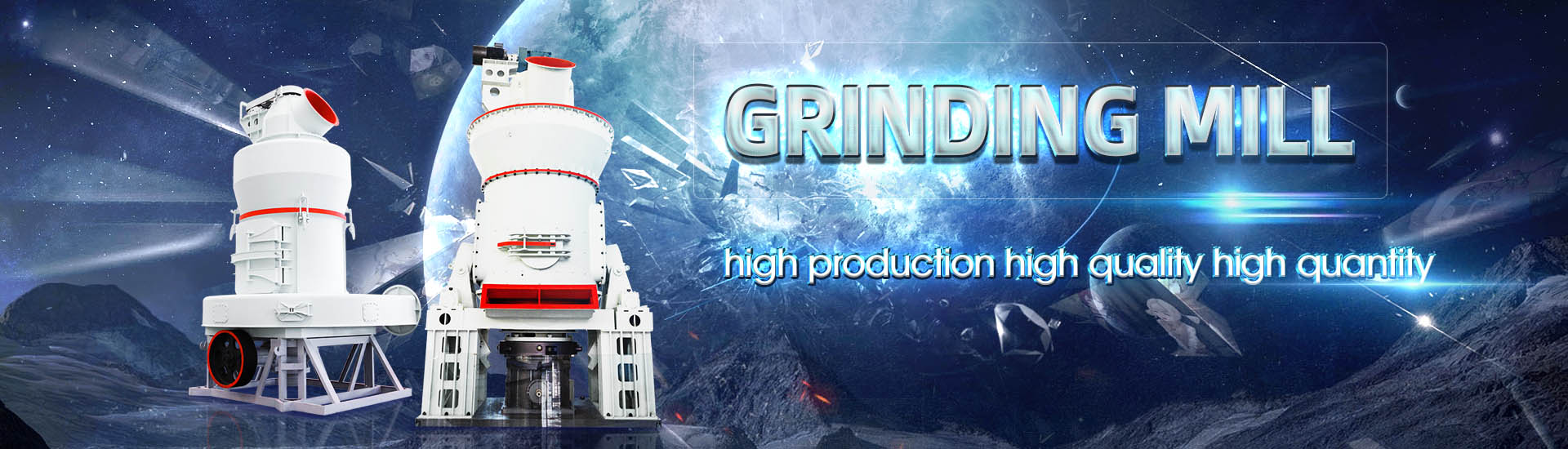
how much is the loss of iron ore powder processing plant stopping production
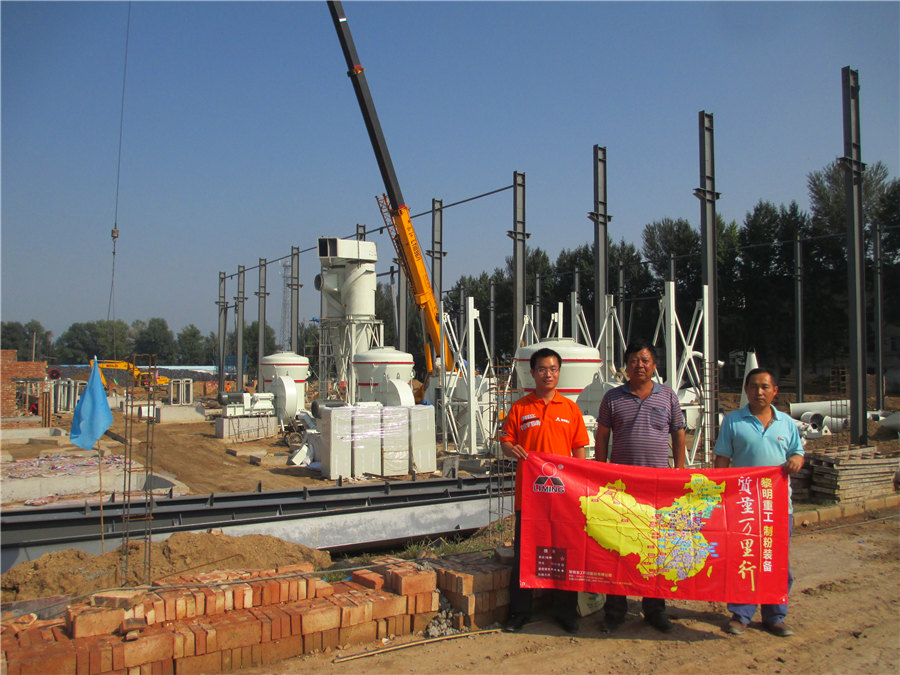
Full article: World mineral loss and possibility to
Taking iron ore as an example, if the percentage of iron ore loss in mining operation and mineral processing is together 372%, the total iron ore loss (final product as fines or pellets) in the world would be 1087 Mt in the year 2018 Taking iron ore as an example, if the percentage of iron ore loss in mining operation and mineral processing is together 372%, the total iron ore loss (final product as fines or pellets) in the World mineral loss and possibility to increase ore recovery ratio in eficiency (about 37%) due to highenergy losses through ofgases (41%) However, a large number of DRI plants with installed capacity of 200 tonne per day (tpd) or more have mENERGYEFFICIENT TECHNOLOGY OPTIONS FOR DIRECT 2021年5月20日 The potential iron loss during the scrap upgrading process in the form of shrapnel and dust is assumed to be in the range of 0105%, which is lost with the residue from the process A ruleofthumb figure discussed with Sicon Driving investments in ore beneficiation and scrap
.jpg)
A critical review on metallurgical recovery of iron from iron ore
2024年4月1日 Iron ore serves as an essential feedstock for steel manufacturers, with approximately 70% of the annual pig iron production from iron ore smelting relying on the 2022年1月1日 To meet the growing demand for steel products, world iron ore production has increased dramatically since 2000 As a result, traditional highgrade iron ore reserves are Introduction: Overview of the global iron ore industry2022年10月20日 The iron ore processing industry produces usable concentrations of ironbearing material by removing nonferrous rock (gangue) from lowgrade ore In the United Iron Ore Processing, General SpringerLink2024年3月12日 Iron ore production declined in 2019 to 2,450 million tonnes but rebounded to reach 2,474 million tonnes in 2020 and a decade high of 2,681 tonnes in 2021 before falling slightly to 2,611 million tonnes in 2022Iron ore facts Canada
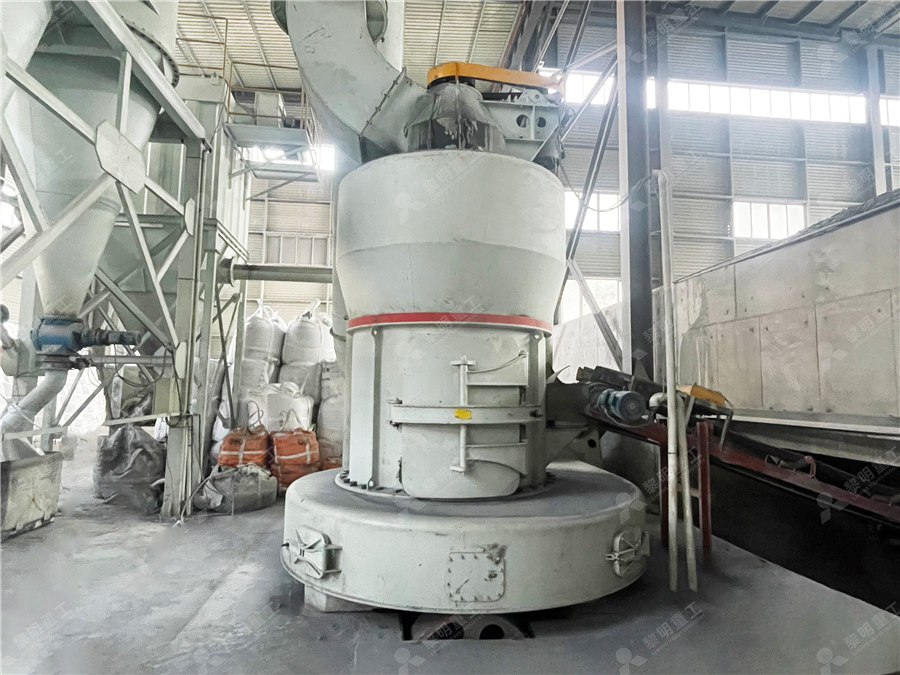
Overview of the Steel Production Process Springer
2020年5月26日 About 7% of global iron is produced as direct reduced iron (DRI) (also known as sponge iron) in a direct reduction furnace (DRF), an alternative to the BF route in which iron is reduced in the solid state by reacting lumps or 2016年3月21日 where R represents the ratio: % Pb in crude ore/% Cu in crude ore Formula (32) is very convenient for milling calculations on ores of this type Example: An ore contains 5% lead and 1% copper The ratio of perfect Common Basic Formulas for Mineral Processing Iron processing, use of a smelting but extraction of the metal from ores dates from about 2000 bc Production seems to have started in the copperproducing regions of Anatolia and early 19th century Furnace size has increased Iron processing Definition, History, Steps, Uses,Iron is currently produced by carbothermic reduction of oxide ores This is a multiplestage process that requires largescale equipment and high capital investment, and produces large amounts of CO2 An alternative to Hydrogen Plasma Processing of Iron Ore
.jpg)
Recent Trends in the Technologies of the Direct Reduction and
2023年4月5日 The blast furnace and direct reduction processes have been the major iron production routes for various iron ores (ie goethite, hematite, magnetite, maghemite, siderite, etc) in the past few decades, but the challenges of maintaining the iron and steelmaking processes are enormous The challenges, such as cumbersome production routes, scarcity of 2021年12月9日 Reduction degree as a function of time for iron ore pellet, sinter, and lump ore at 700, 800, 900, and 1000 C [ 44 ] “modified” Oxyhydroxides such as goethite have shown high reducibility A Review on the Kinetics of Iron Ore Reduction by HydrogenOre processing is the process of separating valuable minerals from its ores by ore beneficiation equipment Mineral processing plant is recovers or extracts minerals through a range of ore dressing solutions, including washing, crushing, grinding, gravity concentration, flotation magnetic separation, electrostatic separation and more JXSC provide full mining process Mineral Processing Plant Beneficiation Solutions JXSC 2023年9月15日 Iron powder is composed of small particles of iron that have been pulverized into a fine powder The particles are typically spherical or irregularly shaped and range in size from 10150 microns Iron powder is highly magnetizable and exhibits high permeabilityIron Powder: Characteristics,types,Specifications Additive
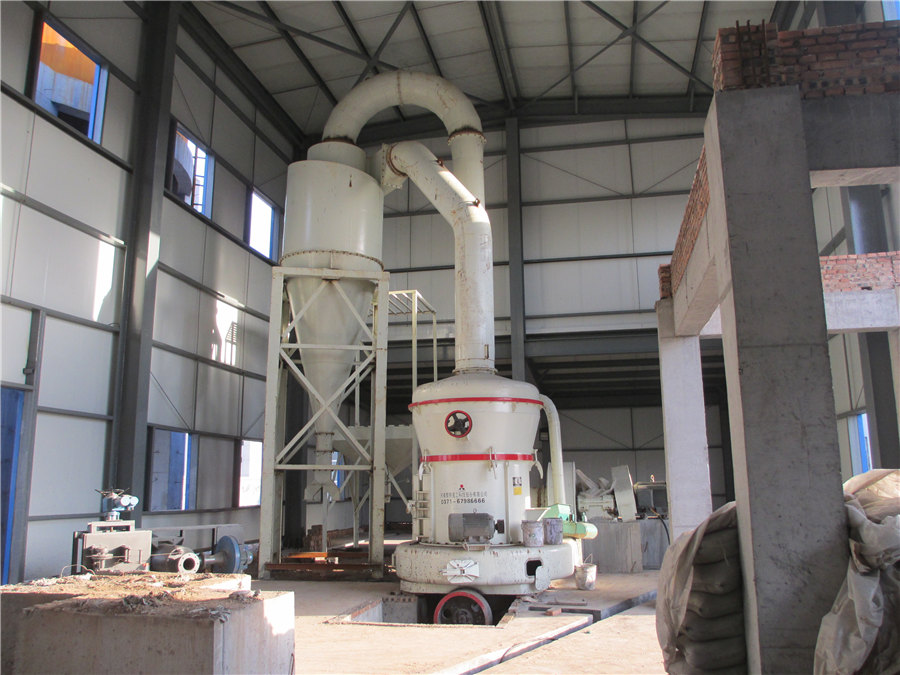
Iron Ore Tailings: Characterization and Applications
2021年1月1日 Brazilian iron ore production, in this same year, was around 450 million tons 5 According to the Brazilian mineral yearbook of the main metallic substances of 2020,Iron processing Ores, Smelting, Refining: Iron ores occur in igneous, metamorphic (transformed), or sedimentary rocks in a variety of geologic environments Most are sedimentary, but many have been changed by weathering, and so their precise origin is difficult to determine The most widely distributed ironbearing minerals are oxides, and iron ores consist mainly of Iron processing Ores, Smelting, Refining Britannica2023年11月20日 Discover the key factors and estimated expenses involved in establishing an iron processing plant for profitable operations +86 ; xlyin@xinhaimining; Follow us; Home; (Iron Ore Processing Plant) The size and capacity of the plant, site selection, production technology, raw material supply chain, How Much Is An Iron Ore Processing Plant Mining Pedia2020年5月14日 The concentration of lowgrade iron ores is vital to the continued availability of iron and steel in our everyday lives (Eisele and Kawatra, 2003;Kawatra and Claremboux, 2021a;Zhang et al, 2021)THE GROWING IMPORTANCE OF PELLETIZING FOR
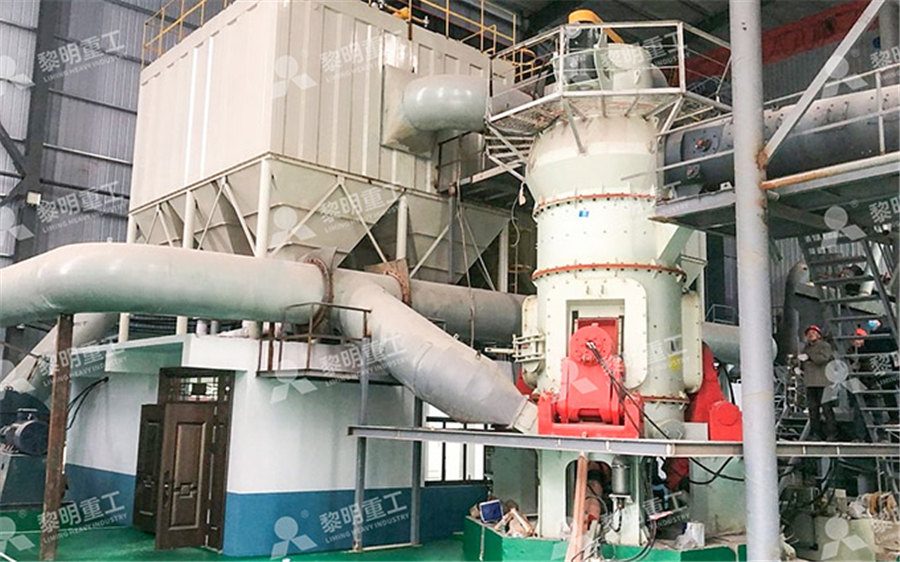
(PDF) Iron ore sintering Part 1 Theory and practice of
2013年8月1日 PDF Sintering is a process by which a mixture of iron ores, fl uxes and coke is agglomerated in a sinter plant to manufacture a sinter product of a Find, read and cite all the research you 2018年9月18日 21 Characterization Studies The fine sample used in the present study was collected from a typical dry processing plant of Khondbond region of India Head sample contains 5873% Fe (T), 554% Al 2 O 3, 66% SiO 2, and 437% loss on ignition (LOI)Further, the sample was subjected to particle size analysis, sizewise chemical analysis, and sizewise density Characterization and Beneficiation of Dry Iron Ore Processing Plant the costs of reprocessing those metals into final products • Production of metals from secondary raw materials significantly reduces CO 2 emissions compared to their primary production (ie, mining), and also reduces the derived impact on the water and the land Using recycled metal instead of finite virgin oresMetal Recycling Factsheet European Circular Economy Premium Statistic Global iron ore production iron content 20102023 Premium Statistic Global iron ore mining market value 20112023Global iron ore mining industry statistics facts Statista
.jpg)
Processing the ores of rareearth elements MRS Bulletin
2022年3月21日 Geology, deposit types, and ore minerals There are more than 200 minerals that contain REE 7,8 The most common rareearth minerals are monazite and bastnäsite (Figure 1a–b and Table II)Monazite exists as a group of arsenates, phosphates, and silicates, but the primary REEbearing monazite is a complex phosphate 5 Bastnäsite, also known as 2019年6月11日 World resources are estimated to be greater than 800 billion tons of crude ore containing more than 230 billion tons of iron The only source of primary iron is iron ore, but before all that iron ore can be turned into steel, it must go through the sintering process Sinter is the primary feed material for making iron and steel in a blast furnaceSintering: A Step Between Mining Iron Ore and Steelmaking2022年12月29日 Iron ore granulation is an indispensable process in the production of sinter that can influence and regulate the yield, efficiency and quality(PDF) Iron Ore Granulation for Sinter Production: Developments 2021年8月8日 The CO2lean direct reduction of iron ore with hydrogen is considered to offer a high potential to reduce CO2 emissions, and this direct reduction of Fe2O3 powder is investigated in this researchThe Direct Reduction of Iron Ore with Hydrogen ResearchGate
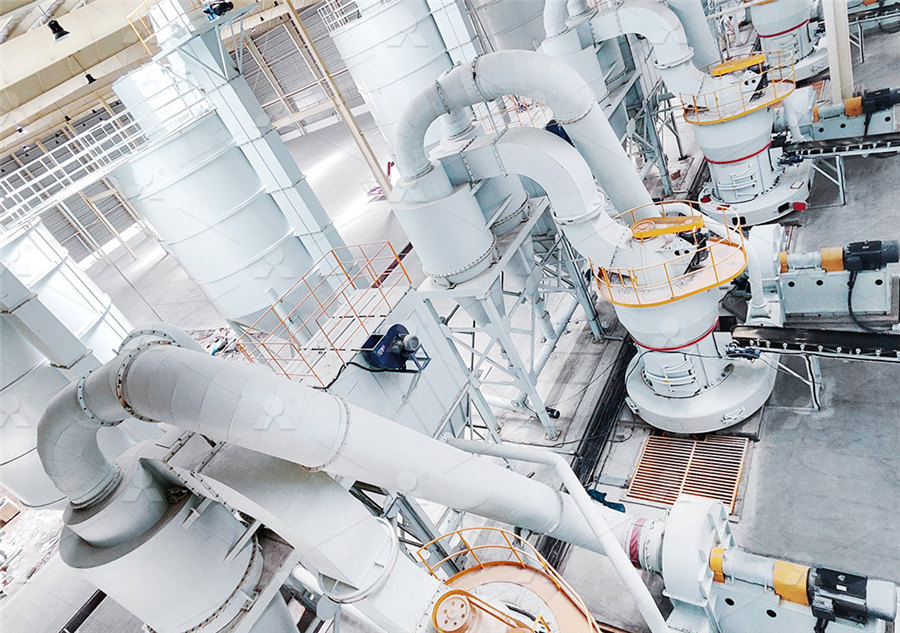
Gold Extraction Recovery Processes 911Metallurgist
2016年2月29日 Some of the metallurgical relationships that must be considered from the testwork program as follows: ore grade relationship to gold recovery, crushing and grinding parameters and their relationship to the ore variability in the ore body, effect of other minerals on the process, minerals and/compounds that negatively impact processing cost such as oxidized Others Low Grade Fe 65% 0 10 20 30 40 50 60 % Share Reserve [6] Fig 4 : Quality of iron ore in India Production in x 000 ton Iron Ore Quality in India (PDF) The utilisation of iron ore fines AcademiaIron Ore is a basic type of ore which is abundant in the world It is smelted into Iron Ingots or alloyed into Steel Ingots for further processing Its Resource Scanner is unlocked after the pioneer leaves the droppod Iron Ore can be harvested by hand (default E) in trace amounts from resource deposits scattered across the world, or from inexhaustible resource nodes on which Iron Ore Official Satisfactory Wikiof oxygen from iron ore in its solid form The iron used in the steelmaking process is currently chemically reduced from iron ore through the use of fossil resources – natural gas or coal This process is known as Direct Reduced Ironmaking (DRI) Carbon combines with the oxygen in the iron ore, producing metallic iron and a carbonrich Fact sheet Hydrogen (H2)based ironmaking
.jpg)
(PDF) Improving reducibility of iron ore pellets by optimization of
2016年1月1日 All content in this area was uploaded by Ammasi Ayyandurai on Jul 22, 年4月1日 Fig 2 illustrates the iron ore beneficiation process, particularly magnetic separation, resulting in the generation of inevitable tailings Due to the characteristics of iron ores and the conditions during beneficiation, it is inevitable that approximately 25–3 tons of IOTs are generated for every 1 ton of iron ore concentrate produced [7]A critical review on metallurgical recovery of iron from iron ore Iron processing Smelting, Refining, Alloying: The primary objective of iron making is to release iron from chemical combination with oxygen, and, since the blast furnace is much the most efficient process, it receives the most attention here Alternative methods known as direct reduction are used in over a score of countries, but less than 5 percent of iron is made this wayIron processing Smelting, Refining, Alloying BritannicaAustralia tops the list of iron ore production by country 2022 It is the leading producer of iron ore in the world The nation produces about 376% of total world production In 2020, it produced a whopping 900 million metric tons of iron ore It doubles its closest rival, BrazilIron Ore Production by Country 2024 World Population Review
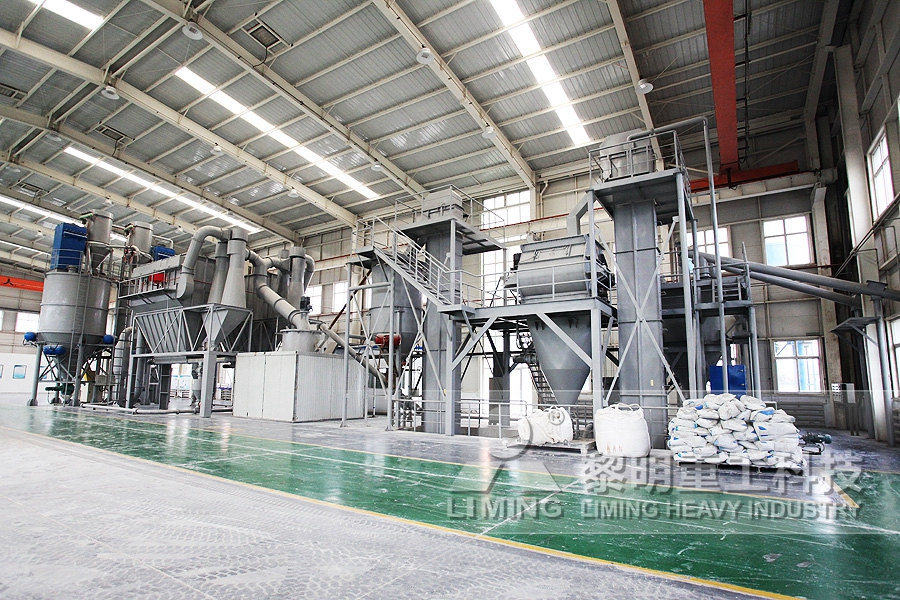
Iron Ore an overview ScienceDirect Topics
113212 IronBearing Materials Ore fines and iron concentrates make the main part of the sinter mix The grain size of ore fines and concentrates is typically 0–8 and 0–3 mm, respectivelyGrains smaller than 01 mm are not desired because they reduce the gas permeability of the bed and thus decrease the sintering efficiencyRecycled materials, such as 2021年4月21日 Nowhere is this challenge more evident than in the industrial sector, which has grown profoundly and rapidly over the last 20 years 3 Steel, a major sector from a commercial and emissions standpoint, is an essential material for the modern world and is a key component of many national economies (Figure 1)It is used in construction, military and defense, and Lowcarbon production of iron and steel: Technology options, economic Copper processing is a complicated process that begins with mining of the ore (less than 1% copper) and ends with sheets of 9999% pure copper called cathodes, which will ultimately be made into products for everyday useThe most common types of ore, copper oxide and copper sulfide, undergo two different processes, hydrometallurgy and pyrometallurgy, respectively, Copper Mining and Processing: Processing Copper Ores2016年3月21日 where R represents the ratio: % Pb in crude ore/% Cu in crude ore Formula (32) is very convenient for milling calculations on ores of this type Example: An ore contains 5% lead and 1% copper The ratio of perfect Common Basic Formulas for Mineral Processing
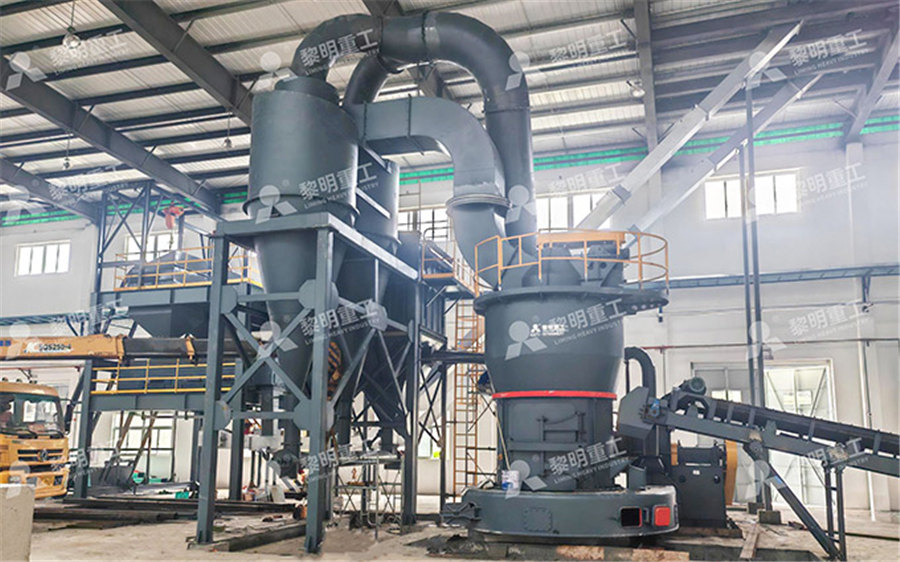
Iron processing Definition, History, Steps, Uses,
Iron processing, use of a smelting but extraction of the metal from ores dates from about 2000 bc Production seems to have started in the copperproducing regions of Anatolia and early 19th century Furnace size has increased Iron is currently produced by carbothermic reduction of oxide ores This is a multiplestage process that requires largescale equipment and high capital investment, and produces large amounts of CO2 An alternative to Hydrogen Plasma Processing of Iron Ore2023年4月5日 The blast furnace and direct reduction processes have been the major iron production routes for various iron ores (ie goethite, hematite, magnetite, maghemite, siderite, etc) in the past few decades, but the challenges of maintaining the iron and steelmaking processes are enormous The challenges, such as cumbersome production routes, scarcity of Recent Trends in the Technologies of the Direct Reduction and 2021年12月9日 Reduction degree as a function of time for iron ore pellet, sinter, and lump ore at 700, 800, 900, and 1000 C [ 44 ] “modified” Oxyhydroxides such as goethite have shown high reducibility A Review on the Kinetics of Iron Ore Reduction by Hydrogen

Mineral Processing Plant Beneficiation Solutions JXSC
Ore processing is the process of separating valuable minerals from its ores by ore beneficiation equipment Mineral processing plant is recovers or extracts minerals through a range of ore dressing solutions, including washing, crushing, grinding, gravity concentration, flotation magnetic separation, electrostatic separation and more JXSC provide full mining process 2023年9月15日 Iron powder is composed of small particles of iron that have been pulverized into a fine powder The particles are typically spherical or irregularly shaped and range in size from 10150 microns Iron powder is highly magnetizable and exhibits high permeabilityIron Powder: Characteristics,types,Specifications Additive 2021年1月1日 Brazilian iron ore production, in this same year, was around 450 million tons 5 According to the Brazilian mineral yearbook of the main metallic substances of 2020,Iron Ore Tailings: Characterization and ApplicationsIron processing Ores, Smelting, Refining: Iron ores occur in igneous, metamorphic (transformed), or sedimentary rocks in a variety of geologic environments Most are sedimentary, but many have been changed by weathering, and so their precise origin is difficult to determine The most widely distributed ironbearing minerals are oxides, and iron ores consist mainly of Iron processing Ores, Smelting, Refining Britannica
.jpg)
How Much Is An Iron Ore Processing Plant Mining Pedia
2023年11月20日 Discover the key factors and estimated expenses involved in establishing an iron processing plant for profitable operations +86 ; xlyin@xinhaimining; Follow us; Home; (Iron Ore Processing Plant) The size and capacity of the plant, site selection, production technology, raw material supply chain,