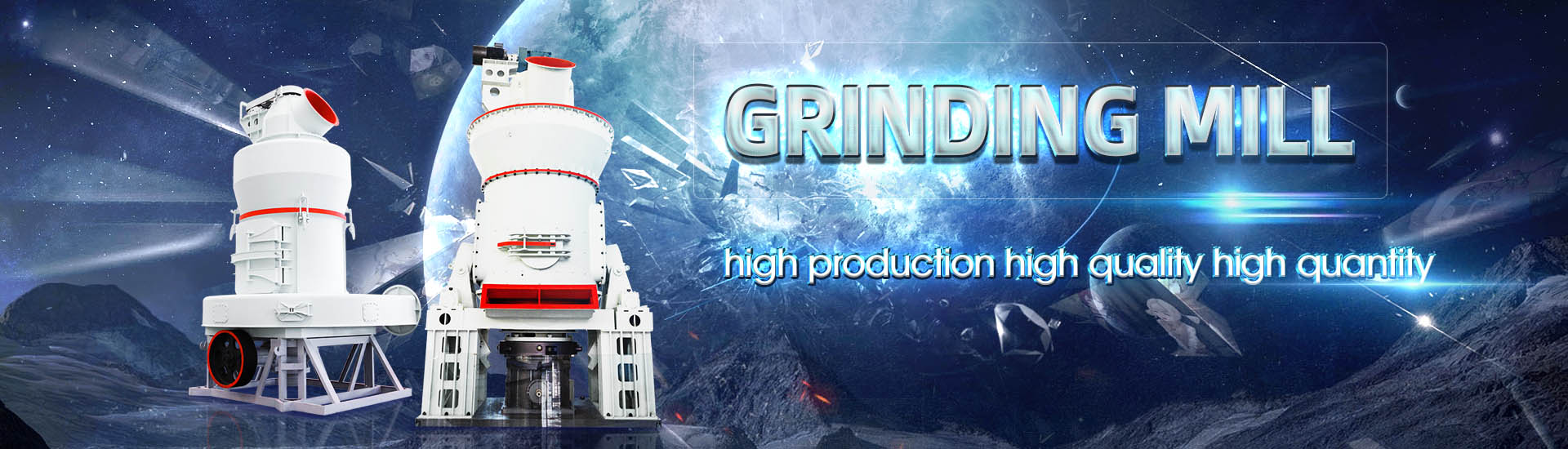
The birth of highefficiency ore mill eased the market demand for wollastonite
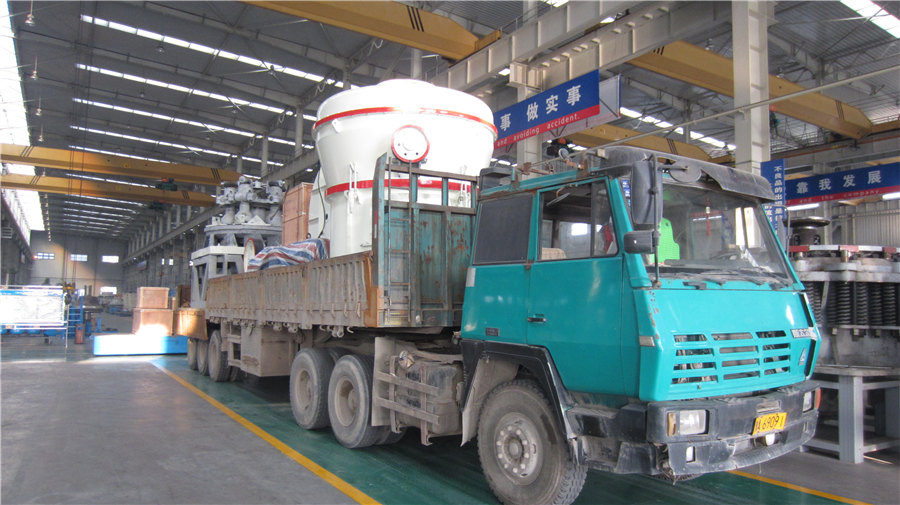
Future of Mining, Mineral Processing and Metal Extraction Industry
Mining operations are tailormade for electrification and autonomy The mines are often located in remote areas, and the operations are often hazardous This requires high level of investments in 展开2020年7月1日 Rising productivity, alongside exploration, is the principal means by which mining can combat resource depletion Over the past one hundred and fifty years, the mining industry Mining productivity and the fourth industrial revolution2023年9月1日 As mentioned earlier, the decreasing ore grade of certain minerals in mines may result in a capacity shortage to meet market demand (Calvo et al, 2016b, Northey et al, Limit of recovery: How future evolution of ore grades could With demand for ultrafine grades for automotive plastics on the rise and steady growth forecast for all its enduser segments, the global market for wollastonite looks promising indeed And with Wollastonite Imerys
.jpg)
Evolution of iron ore mining in the world and in the countries
Due to discovery and development, including construction of a costly transport infrastructure, of huge deposits of rich iron ore in Australia and Brazil, the countries became the largest2020年7月23日 Technological progress has also been crucial to allow the exploitation of new deposits in more complex scenarios: lower ore grades, extreme weather conditions, deeper Innovation in the Mining Industry: Technological Trends and a 2014年10月15日 The goal of ore sorting is to reduce the total amount of material sent to the high energy milling circuit, while not significantly impacting total metal recovery In general, ore Development of ore sorting and its impact on mineral processing 2012年10月13日 In 2010 the big miners abandoned the benchmark and began to sell their ore on shortterm contracts, at prices set on a nascent spot market The ironore price has since The lore of ore The Economist
.jpg)
Mining productivity and the fourth industrial revolution
2019年2月18日 Rising productivity, alongside exploration, is the principal means by which mining can combat resource depletion Over the past one hundred and fifty years, the mining 2023年12月1日 Results show that even when using the high bound of mineral demand due to the energy transition, the rest of the economy remains responsible for a very large majority of Global energy consumption of the mineral mining industry: Introduction The mining of high gold grades is obviously very beneficial for the economic viability of an operation, but optimum recovery of the product is required to maximize profits (Chapman and Bindoff, 2010, p 13)Monitoring ore loss and dilution for minetomill 2014年1月1日 With the increasing depletion of highgrade ore deposits, smarter mineral processing solutions are required to achieve sustainable and economic methods for mining and processing lowgrade deposits(PDF) The economics of large scale ore sorting
.jpg)
Monitoring ore loss and dilution for minetomill
2016年2月1日 The purpose of this study is to understand how ore loss and dilution affect the mine call factor, with the aim of subsequently improving the quality of ore mined and fed to the mill2020年12月21日 which creates a demand for accurate and realtime assessments of a mill’s load and its behavior [13] Circuit retrofitting is the most difficult and costly appr oach to the grinding process Increasing Energy Efficiency and Productivity of the 2021年2月26日 Milling is among the most energyconsuming technological stages of copper ore processing It is performed in mills, which are machines of high rotational masses The start of a mill filled to capacity requires appropriate solutions that mitigate the overloading One method for increasing the energy efficiency of ball mills is to optimize their drive systems This article Energy Efficiency Analysis of Copper Ore Ball Mill Drive The ores tested include relatively competent porphyry, diorite, chlorite and serpentine ores with Bond ball mill work indices ranging between 15 kWh/t and 18 kWh/t However, Bond ball mill work index alone was not an effective determinate of primary mill power requirementOre Competency and the Design of AG/SAG Circuits
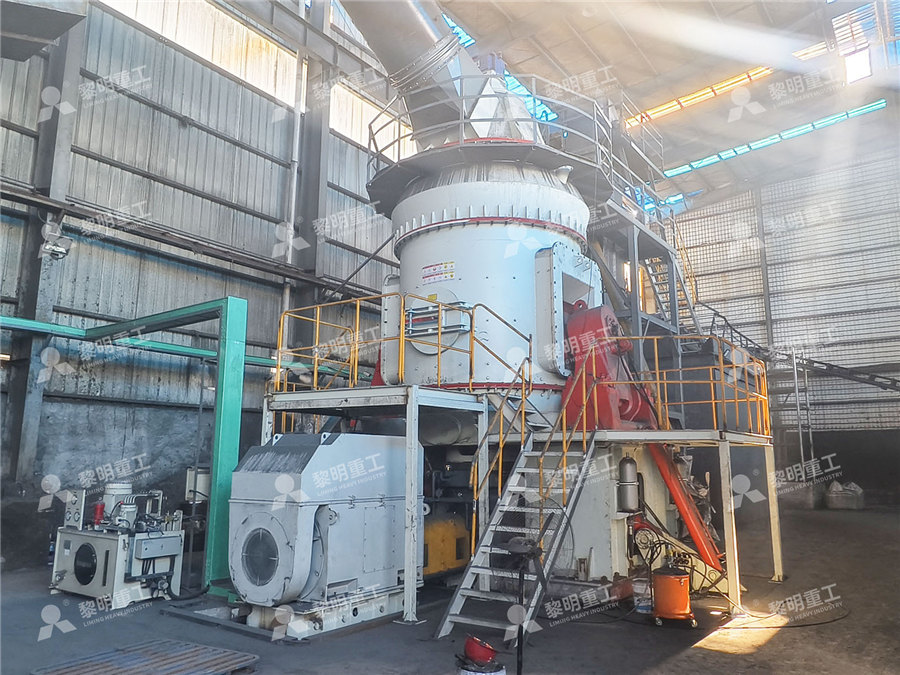
History of Oil: The Birth of the Modern Oil Industry (1859–1939)
2021年3月30日 On 27th August 1859, a railroad man called “Colonel” Edwin L Drake drilled the first commercial, dedicated oil well in the United States near Titusville, Pennsylvania, in the Appalachian Basin using an early form of cabletool rig (Fig 1)Drake was not really a colonel, but a retired railroad conductor in need of a job, a little prestige, and was new to the fledgling oil I Introduction In the early years of the nineteenth century, Americans’ endless commercial ambition—what one Baltimore paper in 1815 called an “almost universal ambition to get forward”—remade the nation 1 Between the Revolution and the Civil War, an old subsistence world died and a new morecommercial nation was born Americans integrated the 8 The Market Revolution American Yawp2021年9月5日 Size reduction is a necessary operation in mineral processing plants and provides the desired size for separation operations and the liberation of the valuable minerals present in ores Estimations on energy consumption indicate that milling consumes more than 50 % of the total energy used in mining operations Despite the fact that ball milling is an efficient Modeling of Bauxite Ore Wet Milling for the Improvement of 2002年11月1日 Unfortunately, the energy efficiency is extremely low in mining operations For instance, the energy efficiency is about 10% in percussive rock drilling (Carrol 1985), 35% in rock crushing The energy efficiency of ball milling in comminution
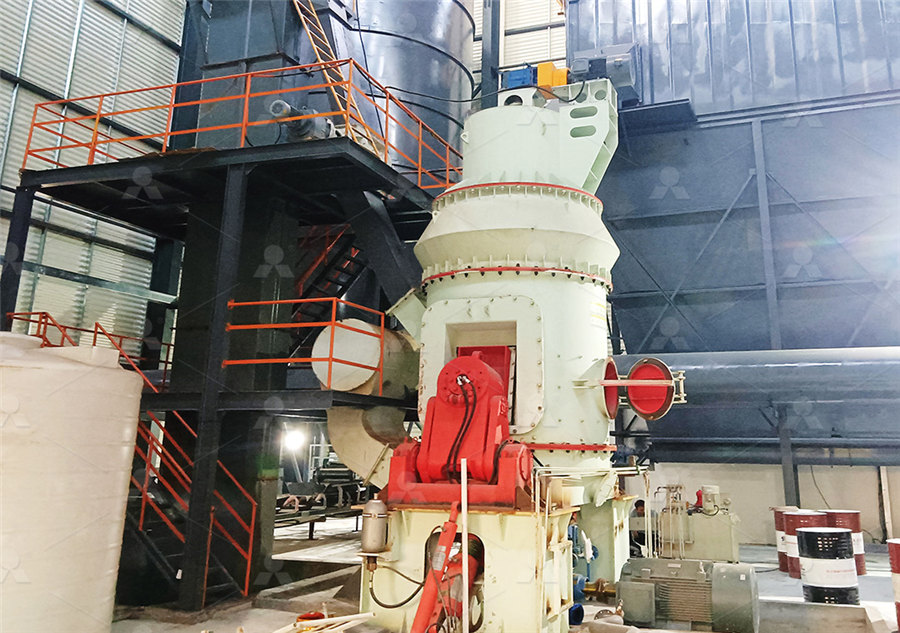
Wollastonite Imerys
With demand for ultrafine grades for automotive plastics on the rise and steady growth forecast for all its enduser segments, the global market for wollastonite looks promising indeed And with reserves at our Mexican wollastonite operations until well into the 22 nd century, Imerys is all set to lead the way2011年3月8日 Surface modification of wollastonite particles using titanate as a modification agent incorporated by simultaneous wet ultrafine grinding in a laboratory stirred mill was investigated The physical, physicchemical and application properties of the modified wollastonite were measured and evaluated The results showed that grinding intensity markedly influences Surface modification of wollastonite by the mechanoactivated Figure 5 Startup of the LSPMSM SMH1732T motor with a filled ball mill after two hours of downtime: (a) active power, (b) current intensity, (c) voltage "Energy Efficiency Analysis of Copper Ore Ball Mill Drive Systems"Energy Efficiency Analysis of Copper Ore Ball Mill Drive Systemsdemand for all kinds of mineral resources, of which the most important is iron ore By 2024, mineral extraction in Russia will have increased by 10–15% and demand for iron ore will rise from 331 to 380 million t (by 148%), according to the predictions in [1] Enrichment plants process iron ore and produced concentrate with high iron contentPredicting the Operational Efficiency of HighPressure Roller
.jpg)
EcoEfficient and CostEffective Process Design for Magnetite Iron Ore
2013年9月16日 In 1996, China manufactured just over 100 Mt of steel and became the world's largest steel producer Official Chinese energy consumption statistics for the steel industry include activities not 2022年2月17日 In openpit mines, the blast operation should be effectively optimized, leading to minimization of production costs through the application of specific technical specifications However, there is inadequate information in the literature to link blasting to comminution stages To this end, the effective parameters for the performance of mining unit operations were An Evaluation on the Impact of Ore Fragmented by Blasting on2020年1月16日 The combination of energy intensive and poor performance of comminution process implies that there is a great opportunity for significant energy and economic savings by the improvement of this (PDF) Optimization and performance of grinding circuits: the 2014年10月20日 The comminution energy consumption could be over 30 kWh/t, an order of magnitude higher than for hematite ores However, with the depletion of highgrade deposits and strong demand for steel, a Regrind of metallic ores with vertical mills: An overview of the
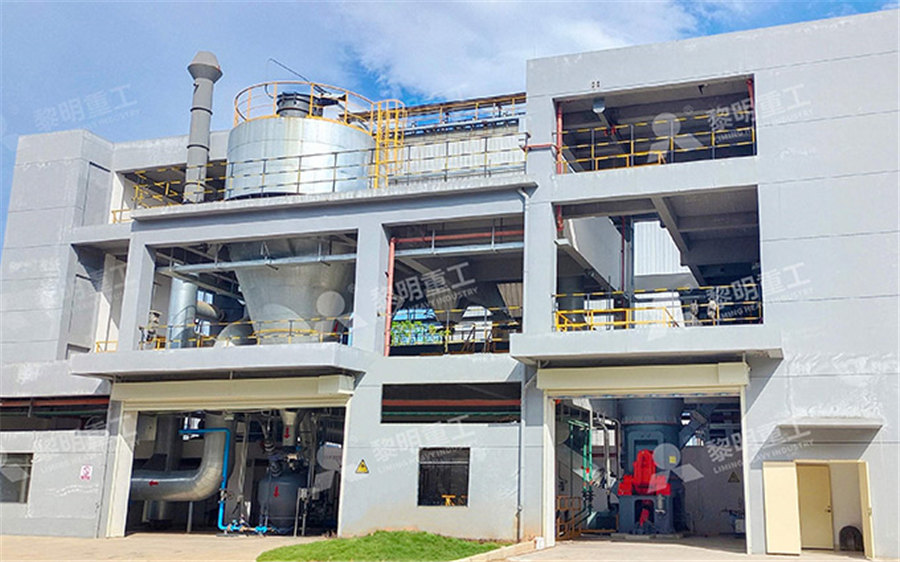
Energy Efficiency Analysis of Copper Ore Ball Mill Drive Systems
Milling is among the most energyconsuming technological stages of copper ore processing It is performed in mills, which are machines of high rotational masses The start of a mill filled to capacity requires appropriate solutions that mitigate the overloading One method for increasing the energy efficiency of ball mills is to optimize their drive systems This article looks at two 2018年7月11日 demand market, mineral processing and iron ore metallurgy technology For years, the Chi nese iron industry is highly dependent on the foreign mines due its quick development on(PDF) The Chinese Iron Ore Deposits and Ore Production2015年9月1日 Fig 1 shows the MinasRio regrinding plant and Fig 2 shows the layout of one of the two banks, containing eight VTM1500 mills and four hydrocyclone batteries(PDF) THE GRINDING EFFICIENCY OF THE CURRENTLY 2024年6月1日 (grinding media and mill liners) standpoint, with mines able to achieve high equipment availability and productivity “Since their early application in the 1960s, SAG mills have provided the modern mining industry with workhorses used for most high throughput grinding applications,” Bianca Foggiatto, director of Comminution and ProcessingTHE FUTURE OF SAG MILLS Ausenco
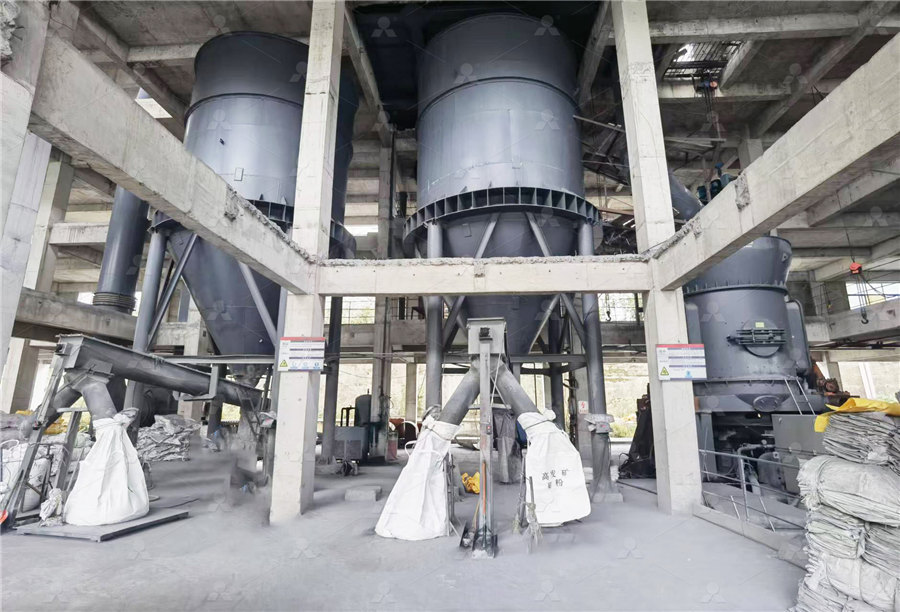
Limit of recovery: How future evolution of ore grades could
2023年9月1日 As mentioned earlier, the decreasing ore grade of certain minerals in mines may result in a capacity shortage to meet market demand (Calvo et al, 2016b, Northey et al, 2014) While it is impossible to predict the future of resource availability in each mine, it is possible to estimate the behavior of specific energy for concentration for each extracted metal2019年8月16日 Mining, mineral processing and metal extraction are undergoing a profound transformation as a result of two revolutions in the making—one, advances in digital technologies and the other, availability of electricity from renewable energy sources at affordable prices The demand for new metals and materials has also arisen concurrently This necessitates Future of Mining, Mineral Processing and Metal Extraction 2024年6月5日 SAG mills are well established in the mining industry with several possible flowsheets featuring them But these circuits consume significant amounts of energy and water With alternative grinding options providing a means to decrease energy and water use, North American Mining asked a group of leading experts for their opinion of the future of theseThe future of SAG mills North American Mining Magazine2023年12月7日 Maintaining the mill control within tight parameters showed not only increased stability and throughput but also reduced issues downstream The system showed an increased throughput of 17 per cent and was able to keep the mill stable in this high efficiency condition A: Basecase, BC: LoadIQ (Blue is throughput and Yellow is mill power)Case study: Industry 40 – Advanced mill optimisation AusIMM
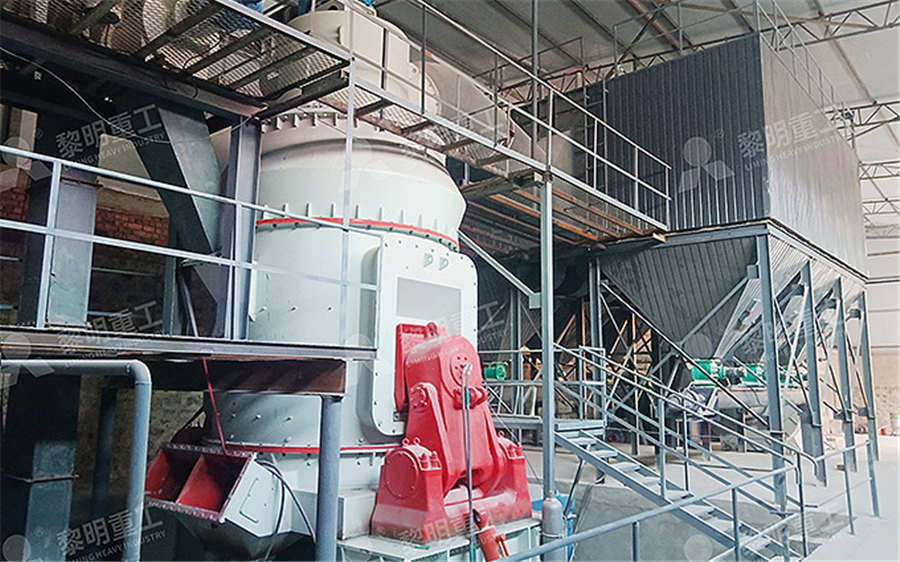
Beneficiation of Gold and Silver Ores SpringerLink
2019年12月15日 429 VertiMills Vertical mills were first designed in the 1950s for applications in fine and ultrafine grinding in Japan Lately, the vertical mill is making progress toward primary grind application and shown promise in energy reduction relative to ball mills, typical to what is normally seen in regrinding applications (Mazzinghy et al 2014)2014年1月1日 Conference: Proceedings of the 23rd International Mining Congress and Exhibition of Turkey IMCET 2013; At: Kemer, Antalya, Turkey, April 1619, 2013, pp 293301Factors affecting the performance of crushing plant operations2019年8月29日 Belttype sorter: (I) Material presentation by vibrating feeder and belt; (II) sensors; (III) ejection nozzle array; (IV) central processing unit (CPU); (V) drop fraction; and (VI) ejected fraction(PDF) Sensor‐Based Ore Sorting Technology in Mining—Past, PDF On Jan 1, 2014, Cecilia Lund published Geometallurgy A tool for better resource efficiency Find, read and cite all the research you need on ResearchGate(PDF) Geometallurgy A tool for better resource efficiency
.jpg)
Monitoring ore loss and dilution for minetomill
Introduction The mining of high gold grades is obviously very beneficial for the economic viability of an operation, but optimum recovery of the product is required to maximize profits (Chapman and Bindoff, 2010, p 13)2014年1月1日 With the increasing depletion of highgrade ore deposits, smarter mineral processing solutions are required to achieve sustainable and economic methods for mining and processing lowgrade deposits(PDF) The economics of large scale ore sorting2016年2月1日 The purpose of this study is to understand how ore loss and dilution affect the mine call factor, with the aim of subsequently improving the quality of ore mined and fed to the millMonitoring ore loss and dilution for minetomill 2020年12月21日 which creates a demand for accurate and realtime assessments of a mill’s load and its behavior [13] Circuit retrofitting is the most difficult and costly appr oach to the grinding process Increasing Energy Efficiency and Productivity of the
.jpg)
Energy Efficiency Analysis of Copper Ore Ball Mill Drive
2021年2月26日 Milling is among the most energyconsuming technological stages of copper ore processing It is performed in mills, which are machines of high rotational masses The start of a mill filled to capacity requires appropriate solutions that mitigate the overloading One method for increasing the energy efficiency of ball mills is to optimize their drive systems This article The ores tested include relatively competent porphyry, diorite, chlorite and serpentine ores with Bond ball mill work indices ranging between 15 kWh/t and 18 kWh/t However, Bond ball mill work index alone was not an effective determinate of primary mill power requirementOre Competency and the Design of AG/SAG Circuits2021年3月30日 On 27th August 1859, a railroad man called “Colonel” Edwin L Drake drilled the first commercial, dedicated oil well in the United States near Titusville, Pennsylvania, in the Appalachian Basin using an early form of cabletool rig (Fig 1)Drake was not really a colonel, but a retired railroad conductor in need of a job, a little prestige, and was new to the fledgling oil History of Oil: The Birth of the Modern Oil Industry (1859–1939)I Introduction In the early years of the nineteenth century, Americans’ endless commercial ambition—what one Baltimore paper in 1815 called an “almost universal ambition to get forward”—remade the nation 1 Between the Revolution and the Civil War, an old subsistence world died and a new morecommercial nation was born Americans integrated the 8 The Market Revolution American Yawp
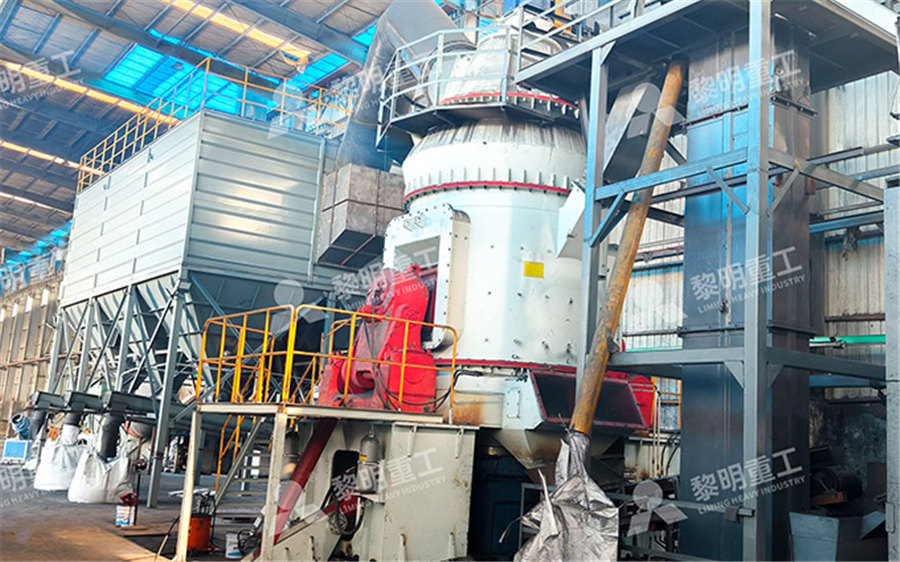
Modeling of Bauxite Ore Wet Milling for the Improvement of
2021年9月5日 Size reduction is a necessary operation in mineral processing plants and provides the desired size for separation operations and the liberation of the valuable minerals present in ores Estimations on energy consumption indicate that milling consumes more than 50 % of the total energy used in mining operations Despite the fact that ball milling is an efficient 2002年11月1日 Unfortunately, the energy efficiency is extremely low in mining operations For instance, the energy efficiency is about 10% in percussive rock drilling (Carrol 1985), 35% in rock crushing The energy efficiency of ball milling in comminution