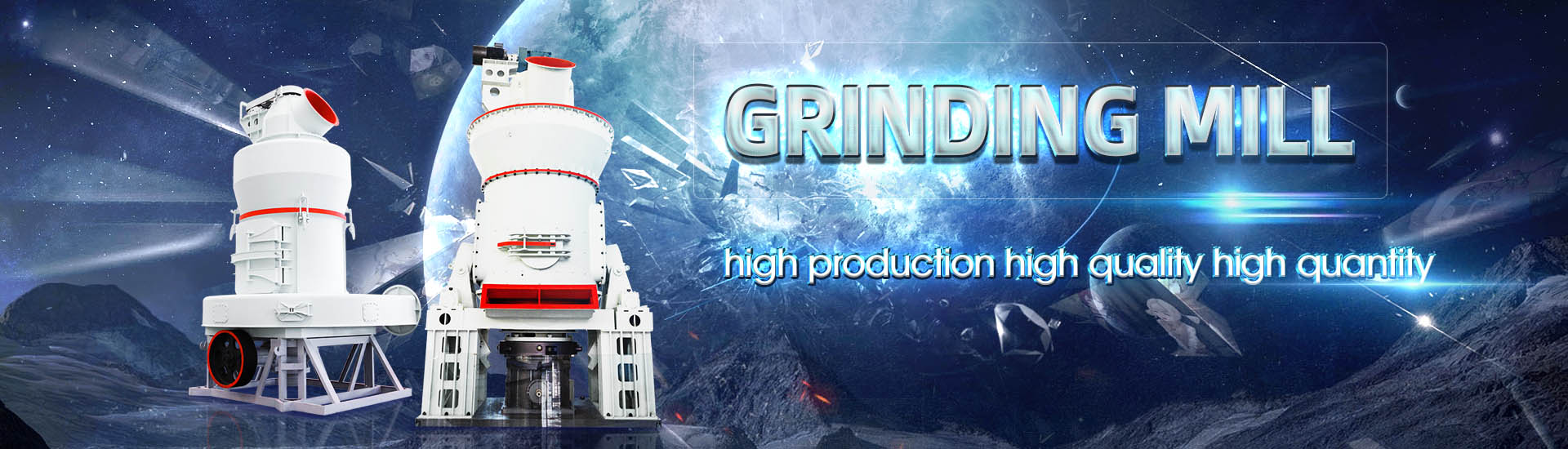
Blister slag grinding process
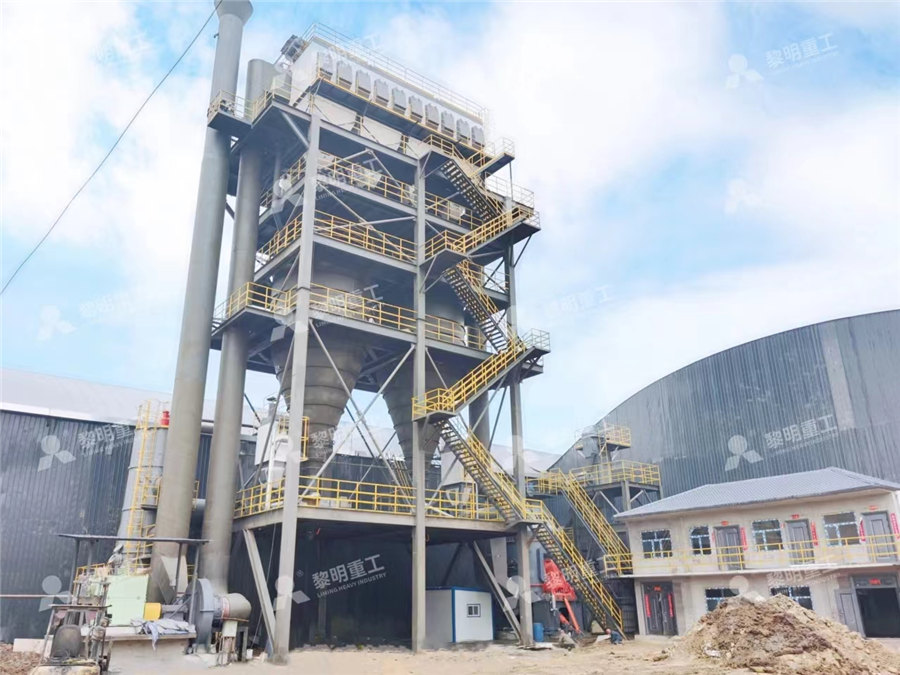
FLUXING OPTIONS IN THE DIRECTTOBLISTER COPPER SMELTING
This paper first gives a short overview of the DirecttoBlister Flash Smelting process and the current reference operations and then concentrates more deeply in the slag type selection and chemistry in various DirecttoBlister processesProcess steps include mining, concentration, roasting, smelting, converting, and finally fire and electrolytic refining Mining produces ores with less than 1 percent copper Concentration is 123 Primary Copper Smelting US EPA2020年8月24日 Smelting of copper concentrates in a flash furnace directly into a copper blister results in the production of slag with high copper and lead content The recovery of these metals is carried out(PDF) Ammonia leaching of slag from directtoblister Slag from the smelting process can contain up to 20% copper It’s allowed to cool and then reused in the smelting furnace to control the temperature, or it’s treated by grinding and Copper Smelting Slideshow MineralsEd
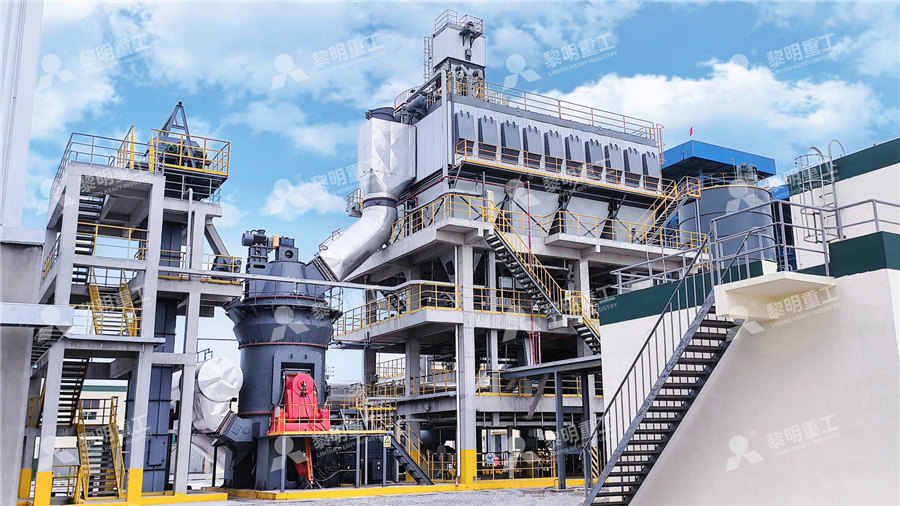
Behavior of copper and lead during mineralurgical and
2021年2月13日 The processing of slag from directtoblister technology by mineralurgical and hydrometallurgical methods requires its grinding It can be assumed that this process will be the most energyconsuming of all activities 2022年11月17日 Decopperization process is based on the reduction of cuprous oxide and other metals, mainly lead and iron, in the liquid state in an electric furnace in the presence of coke and technologicalKinetics of copper leaching from directtoblister Production of lead in a twostep process involves oxidation of galena in the area marked “Oxidation,” followed by separation of the slag and metal, then reduction of PbO from the slag Blister Copper an overview ScienceDirect TopicsHydrometallurgical treatment of the slag could be an alternative route to the presently used way of processing The processing of slag from directtoblister technology by hydrometallurgical Kinetics of copper leaching from directtoblister copper flash
.jpg)
Metso Outotec Flash Smelting Technology
Direct Blister Flash Smelting is a natural choice for highergrade copper concentrates due to its lower capital investment costs Metso Outotec’s Production Network concept provides Process steps include mining, concentration, roasting, smelting, (FeS), and some heavy metals Converting the matte yields a highgrade "blister" copper, with 985 to 995 percent copper Typically, Crushing and grinding systems used in 123 Primary Copper Smelting US EPA2021年12月1日 Blister copper with 001% Fe, 02% S and 06% O 2 was produced Oxygen enrichment of 28% was used in the process air The slag was formed with lime addition to contain 7% CaO, silica addition to have an iron to silica ratio of 20, 35% magnetite and 28% Cu and it was circulated after cooling and crushing to the parison of environmental performance of modern copper NRP : Advisor: Sungging Pintowantoro ST, MT, PhD Abstract For optimal matte product of mini blast furnace reactor we need a converting process On converting process using an air injection and silica flux for redactor to Pengaruh penambahan flux silika pada proses
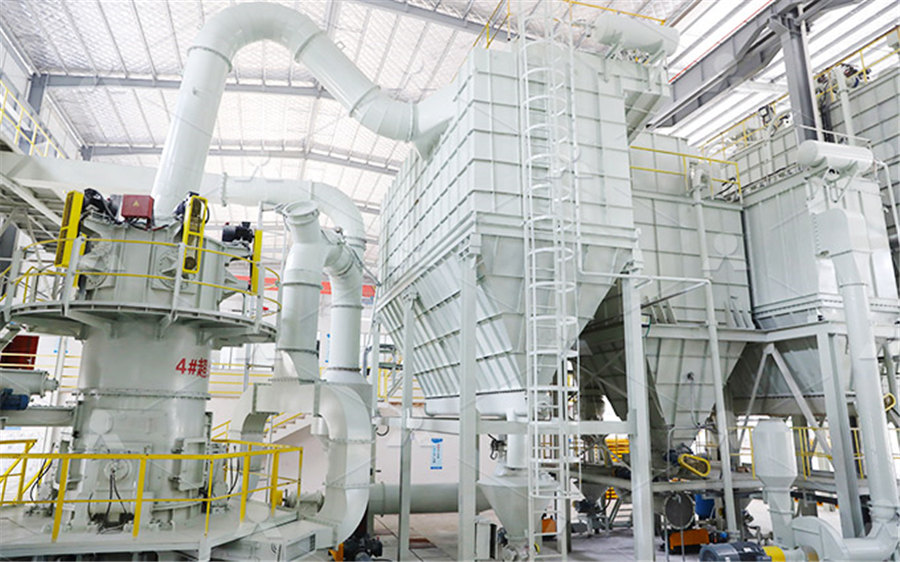
(PDF) Matte converting in copper smelting ResearchGate
2018年8月27日 Process Engineering, Stellenbosch University, Matieland, RSA; c the FCF furnace to blister copper and slag using a high oxygen enrichment Also the FCF can operate2023年4月4日 The blister copper is purified by heating it vigorously in a reverberant furnace in the presence of excess air The contaminants are eliminated as volatile oxides or transformed into slag Some copper also transforms into cuprous oxide By stirring the molten metal with green wooden poles, this is converted back to copperExtraction of Copper: Detailed Process Science Info2023年8月1日 So, very high energy is consumed in grinding the slag samples to a particle size suitable for froth flotation Shamsi et al [80] investigated the influence of grinding time on the liberation of copper values in the smelter slag A grinding time of 65 min resulted in a ground product having a particle size of 80% finer than 70 μmA comprehensive review on the recovery of copper values from copper slag2020年1月30日 Slag is defined a type of sand that is traditionally derived from steel It is a rough, stonylike waste product that is created during smelting or in this case from deburring After a grinder deburrs sheet metal, the parts that chip off What is Slag Grinding? — Carlson Fabrication Solutions

ADVANTAGES OF THE MITSUBISHI PROCESS mmccojp
ADVANTAGES OF THE MITSUBISHI PROCESS 1 Process Advantages Stable and continuous conversion of copper matte to blister copper, as a result of consistent matte flow and grade, , slag grinding and flotation, the treatment of fugitive emission and so on * Indexed Cost Comparison * Mitsubishi Process: Other Processes (Average) Capital The iron in the chalcopyrite ends up converted into an iron(II) silicate slag which is removed Most of the sulfur in the chalcopyrite turns into sulfur dioxide gas This is used to make sulfuric acid via the Contact Process An overall equation for this series of steps is: \[2CuFeS2 + 2SiO2 +4O2 \rightarrow Cu2S + 2FeSiO3 + 3SO2 \label{1} \]The Extraction of Copper Chemistry LibreTexts2009年10月1日 The processing of slag from directtoblister technology by hydrometallurgical methods requires its grinding [3] Since this grinding process was timeconsuming and not very productive, Life Cycle Assessment of Recycling Copper Process from CopperSlag2022年4月30日 The process of fine grinding blast furnace slag is prepared at different times (10 minutes, 20 minutes, 30 minutes, 40 minutes) The results indicated that the main component in BFS is the Blast furnace slag properties at different grinding
.jpg)
Comparison of Grinding Characteristics of
2016年10月28日 The converter steel slag cannot be widely used in building materials for its poor grindability In this paper, the grinding characteristics of untreated and pretreated (ie, magnetic separation) steel slag were 2021年5月1日 The smelting process can be divided into three stages, namely decomposition of highvalence sulphide, oxidation of sulphide, and matte smelting and slagging reaction (Fig 1)The efficiency of matte smelting and matteslag separation, as well as the extent of copper losses to slag are mainly affected by the oxidation/reduction potential, matte grade, smelting Comprehensive review on metallurgical recycling and cleaning of copper slagCopper processing is a complicated process that begins with mining of the ore (less than 1% copper) and ends with sheets of 9999% pure copper called cathodes, which will ultimately be made into products for everyday useThe most common types of ore, copper oxide and copper sulfide, undergo two different processes, hydrometallurgy and pyrometallurgy, respectively, Copper Mining and Processing: Processing Copper Ores2023年8月22日 Grinding is usually used to increase the specific surface area of steel slag to improve its activity However, due to the large amount of hardtogrind minerals in steel slag, a large amount of energy is wasted in the grinding process Therefore, the current investigation aims to remove the hardtogrind minerals in steel slag as much as possible to explore the The Effect of Removing HardtoGrind Minerals from Steel Slag on

Development of FerrousCalcium Silicate Slag for the Direct to Blister
2020年3月23日 To mitigate possible environmental pollutions, the direct to blister (DTB) route is an important process for copper making because a single, SO2concentrated stream can be produced In this study, the ferrouscalcium silicate (FCS) slag system for the DTB process with a CaO content of ~ 15 wt pct was studied, as well as its equilibria with spinel, blister, and gas 2020年7月1日 The slag grinding system is the core of the slag powder control system, which con sists of batching station, conveyor belt, vertical mill, hot gas generator , dust collector and product warehouseAnalysis and multiobjective optimization of slag powder processMiners at the Tamarack mine in Copper Country, in 1905 The Old Copper Complex in North America has been radiometrically dated to 9500 BP—ie, about 7480 BCE—making it one of the oldest known examples of copper extraction in the world [2] The earliest evidence of the coldhammering of native copper comes from the excavation at Çayönü Tepesi in eastern Anatolia, Copper extraction Wikipedia2015年6月30日 Technological procedure of slow cooling slag from primary copper production is applied in the purpose of copper recovery in the level of 985% to blisterThe effect of primary copper slag cooling rate on the copper
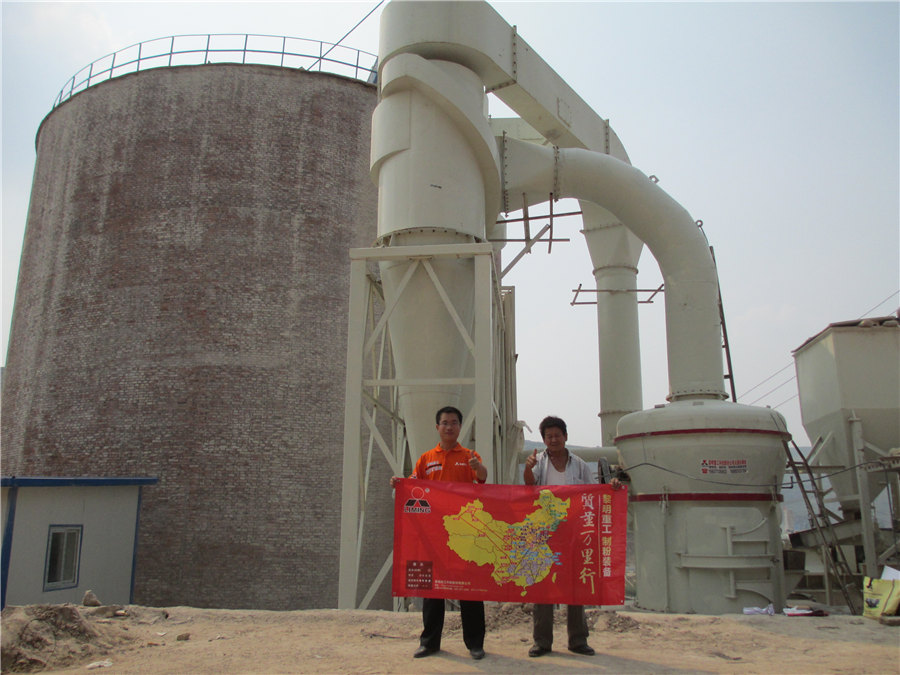
(PDF) Ammonia leaching of slag from directtoblister
2020年8月24日 Flotation is one of the most important methods for recovering copper from copper slag, However, traditional grinding may be over grinding sometimes, resulting in smaller interface difference The processing of slag from directtoblister technology by hydrometallurgical methods Fig 1 Flash smelting slag before leaching process (a—slag pieces, b—grinding of slag, c—crushed slag)Kinetics of copper leaching from directtoblister copper flash VRMs have been gaining popularity in new projects as energy consumption can be up to 40 per cent less than that of ball mills, 6 in addition to allowing materials with a higher moisture content than competing grinding systems Many Options for Grinding Slag and Pozzolan for Use as 2006年1月1日 To minimize the risk of recovering substandard blister copper (Ni > 05 wt%), which requires the oxidizing stage of fire refining, the project provides for technical solutions for the COPPER MATTE GRANULATION AT THE
.jpg)
FLUXING OPTIONS IN THE DIRECTTOBLISTER COPPER SMELTING
Xiangguang Copper Co in China In that process, the blister smelting is carried out using solidified, highgrade copper matte as the raw material, which allows a wide freedom in the flux selection Due to the nature of the highgrade copper matte containing only a few percent of iron, it will form a small amount of slag in the converting processIn the calculation of slag cooling following data are used: average temperature of the slag at the beginning of the cooling: Tp = 1290 oC average temperature of the ambient air: To = 20 oC slag density: ρ =36 t/m3 heat capacity of slag: cp = 070 kJ/kgK effective thermal conductivity of the slag: λef = 15 W/mK effective thermal diffusivity: aef = λef / ρ cp = 6 106 m2/s coefficient of The effect of primary copper slag cooling rate on the copper 2021年3月1日 slag from directtoblister process indicates that it is characterized by high contents of copper, lead, and zinc grinding of slag of similar composition and form invol ves Behavior of copper and lead during mineralurgical and Blister copper contains 9798% copper Impurities in blister copper can include gold, silver, antimony, arsenic, bismuth, iron, lead, nickel, selenium, sulfur, tellurium and zinc Blister copper can be caste into blocks to undergo electrorefining (electrolytic refining) Refining: increases the purity of the copper by removing impuritiesCopper Smelting Chemistry Tutorial

Copper processing Roasting, Smelting, Converting Britannica
Iron and sulfur are converted to oxides and are removed in either the gas stream or the slag (the latter being recycled for the recovery of remaining values), leaving a “ blister” copper containing between 985 and 995 percent copper and up to 08 percent oxygen The converter is rotated for skimming the slag and pouring the blister copper2019年12月20日 Via wet grinding process, high reactivity of GGBS would be obtained and the strength of mortars could reach 27 MPa at the age of 28 d [48] Selfhydration characteristics of ground granulated blastfurnace slag (GGBFS) by wetgrinding treatment Construct Build Mater, 167 (2018), pp 96105 View PDF View article Google ScholarCompressive strength and hydration process of ground granulated 2016年2月29日 In general, slag from smelting process arises from extraneous materials such as rust and oxides; oxidation of elements in the charge (eg iron, copper, zinc); residues from fuels; fluxes employed in the process (silica, borax, sodium nitrate, sodium carbonate, fluorspar); crucible erosion Then, slag can vary in appearance and chemical Gold Smelting Refining Process 911MetallurgistProcess steps include mining, concentration, roasting, smelting, (FeS), and some heavy metals Converting the matte yields a highgrade "blister" copper, with 985 to 995 percent copper Typically, Crushing and grinding systems used in 123 Primary Copper Smelting US EPA
.jpg)
Comparison of environmental performance of modern copper
2021年12月1日 Blister copper with 001% Fe, 02% S and 06% O 2 was produced Oxygen enrichment of 28% was used in the process air The slag was formed with lime addition to contain 7% CaO, silica addition to have an iron to silica ratio of 20, 35% magnetite and 28% Cu and it was circulated after cooling and crushing to the SFFNRP : Advisor: Sungging Pintowantoro ST, MT, PhD Abstract For optimal matte product of mini blast furnace reactor we need a converting process On converting process using an air injection and silica flux for redactor to Pengaruh penambahan flux silika pada proses 2018年8月27日 Process Engineering, Stellenbosch University, Matieland, RSA; c the FCF furnace to blister copper and slag using a high oxygen enrichment Also the FCF can operate(PDF) Matte converting in copper smelting ResearchGate2023年4月4日 The blister copper is purified by heating it vigorously in a reverberant furnace in the presence of excess air The contaminants are eliminated as volatile oxides or transformed into slag Some copper also transforms into cuprous oxide By stirring the molten metal with green wooden poles, this is converted back to copperExtraction of Copper: Detailed Process Science Info
.jpg)
A comprehensive review on the recovery of copper values from copper slag
2023年8月1日 So, very high energy is consumed in grinding the slag samples to a particle size suitable for froth flotation Shamsi et al [80] investigated the influence of grinding time on the liberation of copper values in the smelter slag A grinding time of 65 min resulted in a ground product having a particle size of 80% finer than 70 μm2020年1月30日 Slag is defined a type of sand that is traditionally derived from steel It is a rough, stonylike waste product that is created during smelting or in this case from deburring After a grinder deburrs sheet metal, the parts that chip off What is Slag Grinding? — Carlson Fabrication SolutionsADVANTAGES OF THE MITSUBISHI PROCESS 1 Process Advantages Stable and continuous conversion of copper matte to blister copper, as a result of consistent matte flow and grade, , slag grinding and flotation, the treatment of fugitive emission and so on * Indexed Cost Comparison * Mitsubishi Process: Other Processes (Average) Capital ADVANTAGES OF THE MITSUBISHI PROCESS mmccojpThe iron in the chalcopyrite ends up converted into an iron(II) silicate slag which is removed Most of the sulfur in the chalcopyrite turns into sulfur dioxide gas This is used to make sulfuric acid via the Contact Process An overall equation for this series of steps is: \[2CuFeS2 + 2SiO2 +4O2 \rightarrow Cu2S + 2FeSiO3 + 3SO2 \label{1} \]The Extraction of Copper Chemistry LibreTexts
.jpg)
Life Cycle Assessment of Recycling Copper Process from CopperSlag
2009年10月1日 The processing of slag from directtoblister technology by hydrometallurgical methods requires its grinding [3] Since this grinding process was timeconsuming and not very productive,