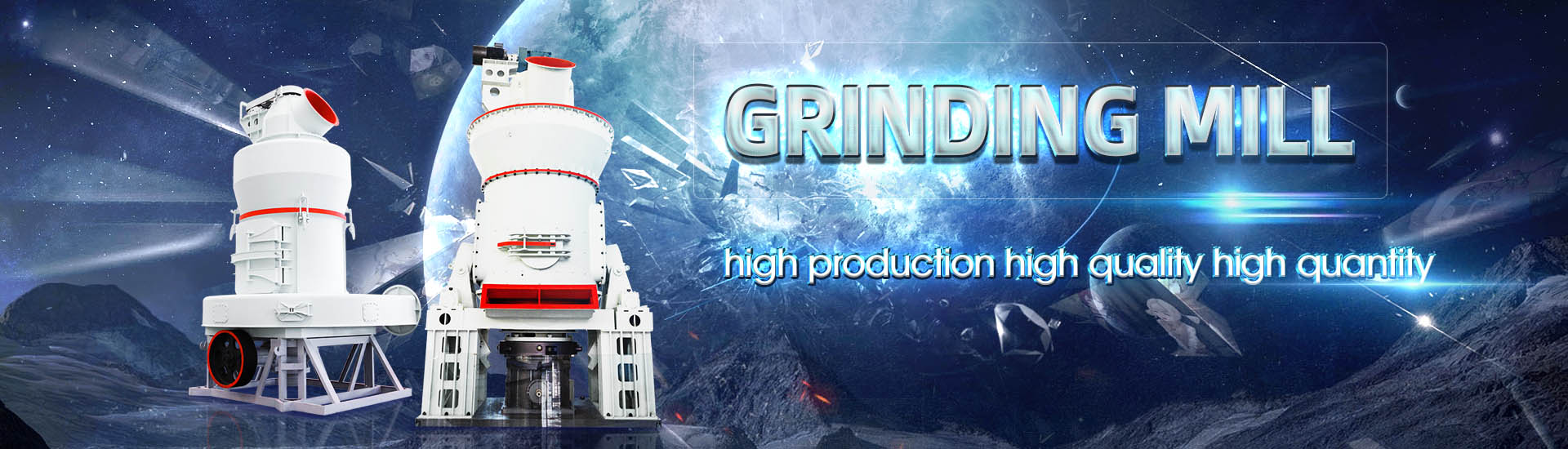
Normal vibration value of ore grinding machine
.jpg)
Measuring vibrations Atlas Copco
Manufacturers are required to declare and supply the vibration value with every power tool sold within the European Union (part of the CE certification) The vibration value is based on measurements performed in accordance with the procedures described in emission standardsVibration in grinding machine is hard to measure It is witnessed from the formation of waviness on the work piece and grinding wheel The major causes of vibration in grinding machine are ANALYSIS AND CONTROL OF VIBRATION IN GRINDING Mining can create significant noise and/or vibration through blasting in both open pit and underground mines; ore and waste rock truck traffic on the mine site; ore stockpiling, Chapter 44 Noise and Vibration Responsible Mining2022年6月10日 Findings showed that: (i) substantially higher shear and vector sum wholebody vibration exposures indicated relatively high levels of exposure on the nonpredominant axis; (PDF) Assessment of vibration exposure of mine machinery
.jpg)
ANALYSIS AND CONTROL OF VIBRATION IN GRINDING
2014年6月25日 Vibration in grinding machine is hard to measure It is witnessed from the formation of waviness on the work piece and grinding wheel The major causes of vibration in 2018年11月1日 A detailed experimental analysis of the shell vibration signal under different grinding conditions, such as wet and dry grinding, coarse and fine grinding, and changes in Mechanism characteristic analysis and soft measuring method There are 2 types of vibration in grinding operations: forced and self – excited Eccentricity and non – alignment of grinding wheel are the main reason for generation of forced vibrationVIBRATION IN GRINDING OPERATIONS utclujro2022年12月21日 The dominant standard that has been used in assessing WBV exposure values is ISO 2631–1 (Mechanical Vibration and Shock Evaluation of Human Exposure to Whole WholeBody Vibration in the Mining Industry: a Systematic Review
.jpg)
Advances in vibration analysis and modeling of large
2023年11月21日 Luo et al 62 extracted feature information values from vibration, grinding sound, and current signals during the grinding process They employed a Support Vector Machine (SVM) along with grid search and cross Work piece and tool vibration control has been a subject of primary importance in manufacturing industry High slenderness ratio is a reason for boring bar to be subjected to high amount of vibrations that accelerate the tool wear affecting ANALYSIS AND CONTROL OF VIBRATION IN 2018年9月29日 The model reasonably predicted the vibration transmissibility spectra measured on the club head and the drivingpoint response function when the grinding contact stiffness was below a certain valueA model for simulating vibration responses of 2023年11月1日 Grinding performance and machining accuracy are affected by many factors, such as the overall operation situation of machine tool, the grinding parameters and auxiliary lubrication cooling conditions, etc; [18, 23, 24]Based on the chatter stability analysis of precision grinding in many researches, the conclusions demonstrate that the relative vibration (or even Comprehensive influence of ultrasonic vibration–assisted
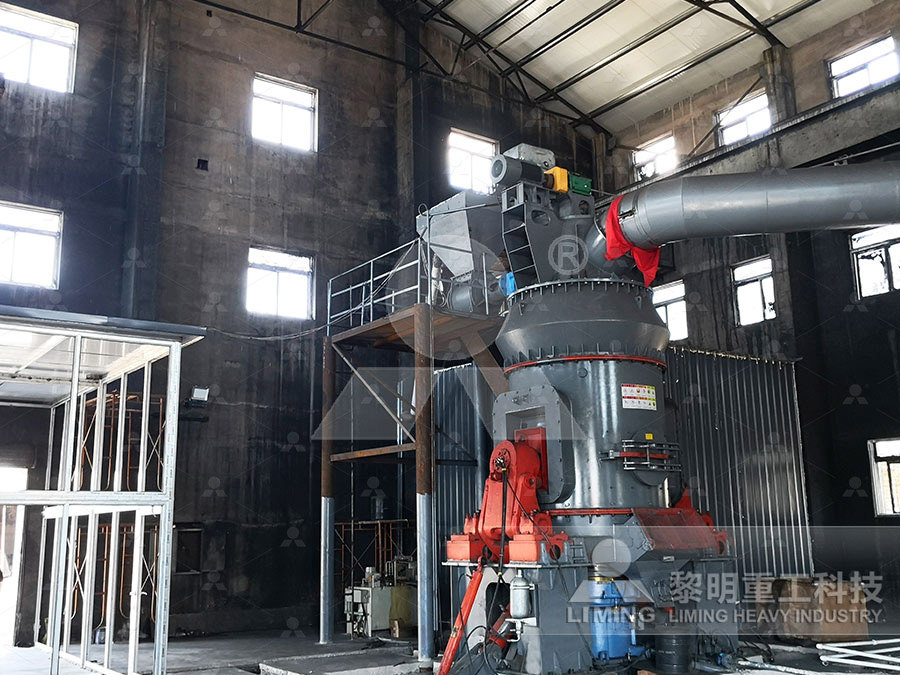
Experimental Analyses into Dry Ultrasonic VibrationAssisted Grinding
2022年9月28日 Ultrasonic vibrationassisted grinding is a composite technique that involves conventional grinding with ultrasonic vibration, and it has been used to produce an efficient and sustainable grinding process for materials that are “difficult to machine,” namely nickelbased superalloys (Ref 10), titanium alloys (Ref 11), tool steels (Ref 12), composites (Ref 13), and 2022年5月1日 The dynamometer (Kistler 9265B) was used to measure the F, including tangential grinding force (F t) and normal grinding force (F n) The surface roughness (R a) values were obtained using a Mahr surface roughness tester (MarSurf XR20) A scanning electron microscope (Phenom ProX) was used to observe the ground surface morphologyProcessing and machining mechanism of ultrasonic vibration 2020年2月10日 This article presents a new model of the flat surface grinding process vibration conditions The study establishes a particular analysis and comparison between the influence of the normal and Modeling of Vibration Condition in Flat Surface Grinding Process2022年3月2日 Ultrasonic vibration–assisted grinding (UVAG) shows excellent performance in the machining of difficulttocut materials Grinding force is one of the key factors affecting the quality of the machined surface, which has been investigated both experimentally and theoretically However, the research on the modeling of the grinding force of the separated Research on modeling of grinding force in ultrasonic vibration

Curvature effect on surface generation and uniform scallop
2021年2月15日 In normal grinding, the unbalanced vibration of the gr inding wheel leads to the further increase for scallop height According to the geometric relation of the relative movement of the grinding2024年6月3日 Ultrasonic vibrationassisted grinding (UVG) has several advantages, such as small grinding force, good surface quality, and high grinding efficiency, outperforming conventional grinding (CG) However, it is sensitive to process parameters, making optimal processing parameters crucial and a major challenge Therefore, in this study, we introduce a AAC theory for ultrasonic vibrationassisted grinding The 2023年12月15日 Ultrasonic vibrationassisted grinding (UVAG) has attracted plenty of attention to significantly improve surface integrity However, existing research has not systematically investigated the effect of vibration directions during UVAG at atomic and nanoscales, limiting our understanding of the plastic deformation mechanisms and microstructural evolution of ultra Molecular dynamics simulations of ultrasonic vibrationassisted Measuring and declaring vibration value Everyone, from manufacturer to operator, is responsible to reduce the vibration exposure Manufacturers supplying power tools within the European Union are responsible for measuring and declaring the vibration emission value for every machine model To find out more on how we measure vibrations, continueMeasuring vibrations Atlas Copco
.jpg)
Twodimensional ultrasonic vibrationassisted dry grinding gear
2023年12月28日 Ultrasonic vibrationassisted dry grinding has been focused on to alleviate the cutting fluids' negative impact on environment, avoid the unnecessary waste, and reduce the manufacturing costs However, this technology has not been used for grinding gear In order to explore its effect, this study proposes a twodimensional (ie, 2D or elliptical) ultrasonic 2023年5月3日 Tangential ultrasonic vibrationassisted grinding gear (TUVAGG) is a new promising process combining the ultrasonic vibration with conventional grinding gear (CGG) In this study, an assessment of grinding forces from the point of theoretical and experimental was provided in TUVAGG, revealing its mechanism Therefore, a prediction model of abrasive Grinding force assessment in tangential ultrasonic vibration 2013年1月1日 Superb grinding machines now produce optical quality finishes due to developments in process control and machine design It is the same for extremely high removal ratesPrinciples of Modern Grinding Technology ResearchGate2022年6月10日 Comparison of average WBV acceleration values generated by mining machinery at mines A, B and C with exposure threshold values of A (8) ISO 26311 standard and EU Directive 2002/44 / EC(PDF) Assessment of vibration exposure of mine machinery
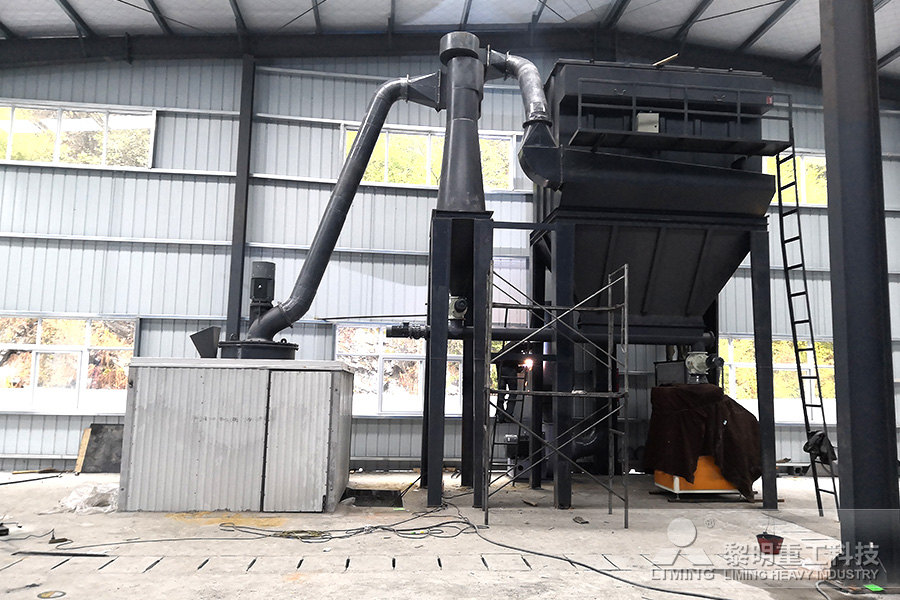
Study on Grinding Force of TwoDimensional Ultrasonic Vibration
2023年1月15日 Compared with the conventional grinding test results, it is found that the normal force and tangential force of axial ultrasonic assisted grinding are reduced by 2731% and 2252%, respectively, and the surface roughness value is reduced by 180%, which indicates that ultrasonic vibrationassisted grinding can reduce the grinding force and improve the machining 2023年8月29日 This study adopted AI to identify the normal and abnormal vibration signals generated during robotic grinding This study classified four fundamental factors affecting grinding into three levels to obtain a widely used result and designed an \(L{9} (3^{4} )\) orthogonal array for the grinding experiment During experimentation, part of the grinding wheels was added Application of Recurrence Plots and VGG Deep Learning Model to 2000年11月1日 The vibration behavior of the grinding machine spindle system is conditioned by both the vibration characteristics of the assembly components, ie shaft–bearing–housing system and the external grinding process forces While vibration characteristics of the shaft–bearing–housing components were approached by many reliable mathematical Effect of grinding forces on the vibration of grinding machine 2019年6月27日 The methodology combines ultrasonicassisted grinding with helical millgrinding to machine cemented carbide via a diamond form grinding wheel Based on the characteristics of ultrasonic longitudinaltorsional vibration, the motion trajectories of individual abrasive particles under conventional grinding (ConG) and ultrasonic longitudinaltorsional vibrationassisted Ultrasonic vibrationassisted grinding of blind holes and internal

Optimization Analysis of Vibration for Grinder Spindle MYU Group
410 Sensors and Materials, Vol 32, No 1 (2020) 24 Grinding wheel The grinding wheels used in the experiments were 1A35538127C46J7V (see Fig 5) 25 Material of workpiece The workpiece material used in these experiments was S45C medium carbon steel (270 ×2023年2月2日 21 Experimental setup As illustrated in Fig 2, the robotic abrasive belt grinding system used in this study consisted of an industrial robot, a control cabinet, a sixdimensional force/torque sensor, an abrasive belt grinding machine, a 3 M pyramid abrasive belt, workpieces, and a fixtureWe used an HSRJR605 industrial robot with a rated load of 5 kg, maximum Robotic abrasive belt grinding with consistent quality under normal 2022年2月14日 However, as the MRR value increased to 180 mm 3, the normal grinding force reached 14524 N, which is only 0833% lower than that of 315 mm 3 In this case, the normal grinding force has a steady and constant stage at MRV of 180–315 mm 3 in UVAG A different result is observed in CG, in which the normal grinding force keeps on increasingOn the grinding performance of alumina wheels in ultrasonic vibration 2022年10月14日 C/SiC composite material is the best choice for important parts such as the hotend structure of aerospace vehicles Research and optimization of the cutting force of ultrasonic vibrationassisted grinding are of great Research on Grinding Force of Ultrasonic Vibration
.jpg)
Investigation of the effect of vibration characteristics on the
2022年3月18日 The machining quality of the blade tip has a great influence on the service performance and life of the aeroengine blade The recent paper investigates the effect of vibration during the grinding process of the GH4169 nickelbased superalloy blade tip Moreover, this paper proposes a theoretical model to link the unbalance of the grinding wheel, the 2024年9月19日 For UVAG, the grinding force exhibited a gradual decrease trend, with the minimum radial force occurring at a grinding speed of 1308 m/s, at which point F y was 218 N Figure 6c shows the influence of grinding speed on axial grinding force F z, which indicated that for CG, the grinding force also exhibited a trend of first decreasing and then increasing, with Material removal characterization during axial ultrasonic vibration 2023年7月19日 The operation of belt grinding machines is usually accompanied by a significant level of noise and vibration, which adversely affect the health of operators and the accuracy of processing the Theoretical studies of vibrations and noise of grinding belt machines2016年3月10日 Common forms of vibration on grinding machines tend to fall into two categories – force vibration and selfexcited vibration Force vibration A precision cylindrical grinding operation may require displacement values below 003 mils (000003") whereas a cutoff operation at a steel mill could be greater than 100 mils (0 Measuring vibration on precision grinding machines

Effect of grinding forces on the vibration of grinding machine
2000年11月1日 In the grinding process, the relative movement between the wheel and the workpiece is considered as the main factor to cause the vibration The vibration behavior of the grinding machine spindle Download scientific diagram Scallop height increased caused by the relative vibration of grinding wheel from publication: Curvature effect on surface generation and uniform scallop height Scallop height increased caused by the relative vibration of grinding 2020年10月26日 In the present study, an MD model for VibrationAssisted Grinding (VAG) is created The workpiece is an orthogonal parallelepiped single crystal copper (Cu) substrate, whereas grinding is performed by two cubic shaped, single crystal diamond (C) abrasive grains and the total number of atoms in the system is about 104,000Investigation of the Efficiency of VibrationAssisted NanoGrinding 2018年9月29日 The model reasonably predicted the vibration transmissibility spectra measured on the club head and the drivingpoint response function when the grinding contact stiffness was below a certain valueA model for simulating vibration responses of

Comprehensive influence of ultrasonic vibration–assisted
2023年11月1日 Grinding performance and machining accuracy are affected by many factors, such as the overall operation situation of machine tool, the grinding parameters and auxiliary lubrication cooling conditions, etc; [18, 23, 24]Based on the chatter stability analysis of precision grinding in many researches, the conclusions demonstrate that the relative vibration (or even 2022年9月28日 Ultrasonic vibrationassisted grinding is a composite technique that involves conventional grinding with ultrasonic vibration, and it has been used to produce an efficient and sustainable grinding process for materials that are “difficult to machine,” namely nickelbased superalloys (Ref 10), titanium alloys (Ref 11), tool steels (Ref 12), composites (Ref 13), and Experimental Analyses into Dry Ultrasonic VibrationAssisted Grinding 2022年5月1日 The dynamometer (Kistler 9265B) was used to measure the F, including tangential grinding force (F t) and normal grinding force (F n) The surface roughness (R a) values were obtained using a Mahr surface roughness tester (MarSurf XR20) A scanning electron microscope (Phenom ProX) was used to observe the ground surface morphologyProcessing and machining mechanism of ultrasonic vibration 2020年2月10日 This article presents a new model of the flat surface grinding process vibration conditions The study establishes a particular analysis and comparison between the influence of the normal and Modeling of Vibration Condition in Flat Surface Grinding Process
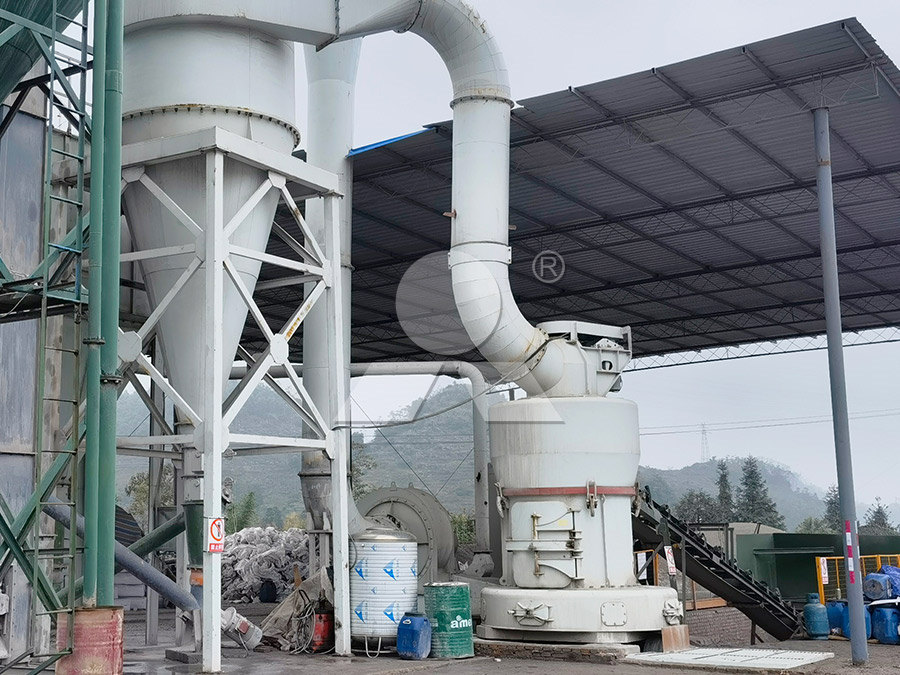
Research on modeling of grinding force in ultrasonic vibration
2022年3月2日 Ultrasonic vibration–assisted grinding (UVAG) shows excellent performance in the machining of difficulttocut materials Grinding force is one of the key factors affecting the quality of the machined surface, which has been investigated both experimentally and theoretically However, the research on the modeling of the grinding force of the separated 2021年2月15日 In normal grinding, the unbalanced vibration of the gr inding wheel leads to the further increase for scallop height According to the geometric relation of the relative movement of the grindingCurvature effect on surface generation and uniform scallop 2024年6月3日 Ultrasonic vibrationassisted grinding (UVG) has several advantages, such as small grinding force, good surface quality, and high grinding efficiency, outperforming conventional grinding (CG) However, it is sensitive to process parameters, making optimal processing parameters crucial and a major challenge Therefore, in this study, we introduce a AAC theory for ultrasonic vibrationassisted grinding The 2023年12月15日 Ultrasonic vibrationassisted grinding (UVAG) has attracted plenty of attention to significantly improve surface integrity However, existing research has not systematically investigated the effect of vibration directions during UVAG at atomic and nanoscales, limiting our understanding of the plastic deformation mechanisms and microstructural evolution of ultra Molecular dynamics simulations of ultrasonic vibrationassisted