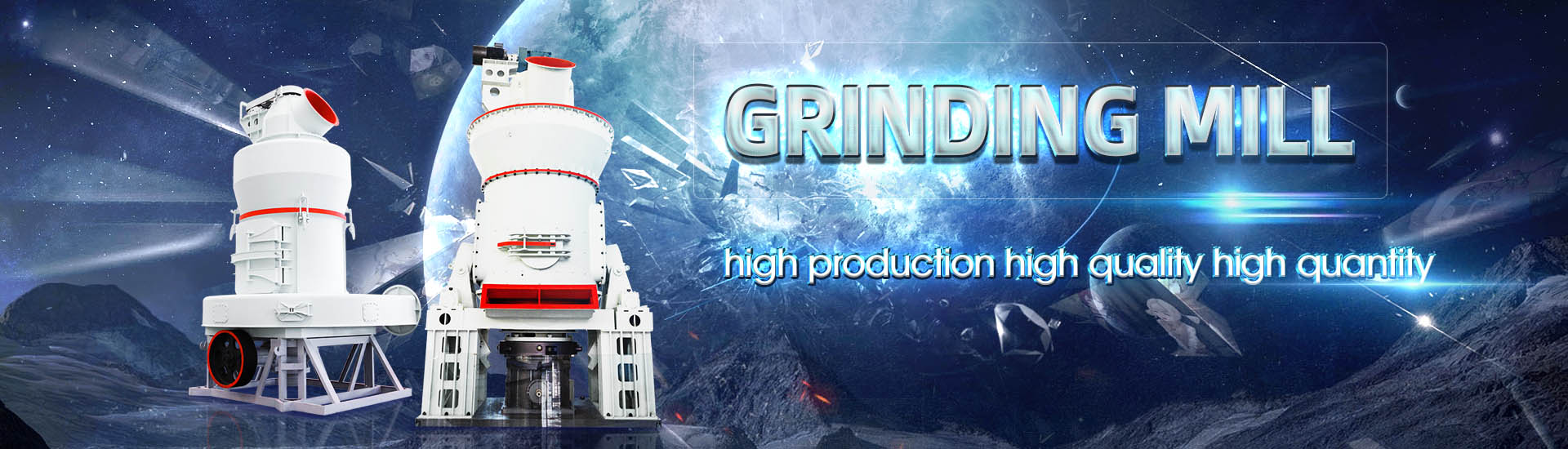
The wear will increase the highstrength mill
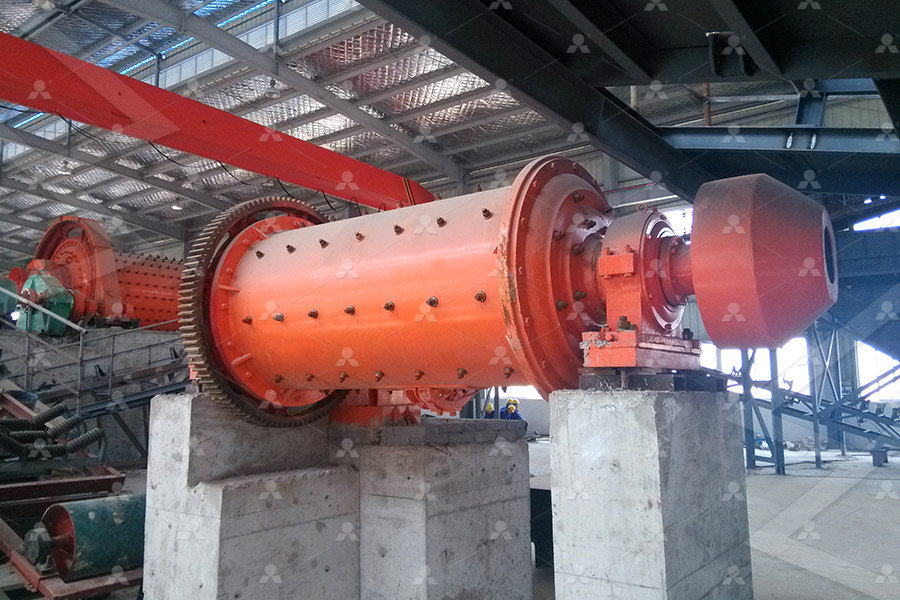
Cutting edge wear in highspeed stainless steel end milling
2021年4月19日 This study examines and compares the performance of three stateoftheart milling tools for highspeed end milling while cutting the same material, stainless steel The 2024年11月25日 The development of highstrength cast iron alloys has become critical for advancing manufacturing processes, particularly in the automotive and heavy machinery Critical analysis of wear mechanisms in carbide tools applied in the 2024年8月3日 Difficulttomachine materials are characterized by high hardness, strength, and anisotropy During machining, tools can suffer from adhesion, abrasion, material detachment, Tool wear on machining of difficulttomachine materials: a review2023年11月3日 The tool wear mechanisms and effect of tool wear on surface roughness, milling force, burr damage, surface microstructure and chips were explored The results show that Effect of tool wear on machining quality in milling C
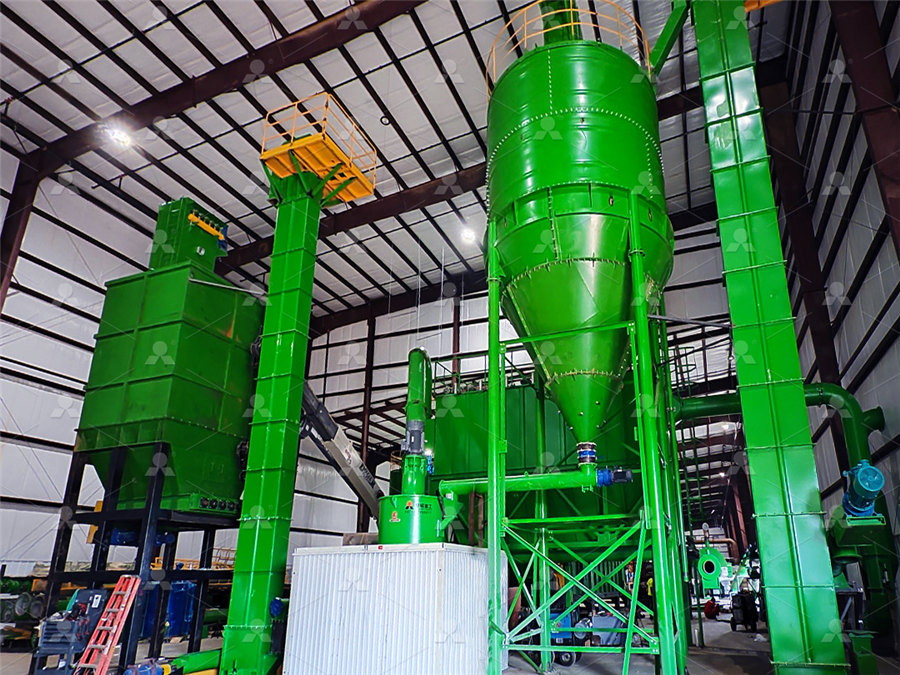
A stateoftheart review on tool wear and surface integrity
2021年11月1日 When tool wear is taken into account, while mechanical surpassed thermal impacts and residual compressive stress increases with increased tool wear, the high thermal 2024年2月15日 The highstrength wearresistant steel with a retained austenite volume fraction ranging from 52 vol% to 92 vol% has been successfully prepared using dynamic carbon Effect of retained austenite on impactabrasion wear performance 2018年1月17日 Using coated carbide end mill inserts to mill 022Cr17Ni12Mo2 stainless steel, this study further investigates the influence of process factors on cutting force and vibration on the basis of revealing tool wear mechanismsThe relationships between cutting parameters, tool 2021年6月10日 When using cutting edge roundings, which have a sufficiently high stability due to their size, the wear is influenced to a large extent by the cutting edge chipping An increase in the degree of breakouts along the Influence of End Mill Manufacturing on Cutting Edge
.jpg)
Effect of cutting speed on chip formation and wear
2017年7月21日 Results revealed that the machined chips exhibited clear sawtooth profile and were almost segmented at high cutting speeds, and apparent degree of sawtooth chip morphology occurred as cutting speed increased 1994年8月1日 Wear variables and modes are reviewed along with published methods and models used in the study and testing of roll wear This paper reviews key aspects of roll wear control — roll materialWear of hot rolling mill rolls: an overview ResearchGateThe observed effects of temperature on wear of roll materials via oxide influence may be explained as follows: i) the oxides formed in region 400 600 oC are Fe2O3 and Fe3O4 and increase abrasive WEAR OF HOT ROLLING MILL ROLLS: AN OVERVIEW2020年1月1日 Application of the proposed method in a 975 × 488 m SAG mill indicated that the liner wear profile along the liner length was nonuniform and the highest wear occurred between 125 m and 275 m The study of the lining layer abrasing wear in the semiautogenous
.jpg)
Increase Tool Life, Reduce Tool Wear Tormach
Flank Wear is wear on the portion of the tool in contact with the finished part It’s the most common type of Tool Wear and the most predictable It occurs due to abrasion of the tool by the workpiece Harder workpiece materials will be more 2021年11月1日 Keywordsaustempered ductile iron–grinding media wear–ball mill good machinability, high strengthtoweight wear to fatigue delamination as the wear load increased from 25 N to 100 N (PDF) Morphology and wear of high chromium and2022年5月9日 As an important part of the ball mill, the lining plate can not only effectively protect the barrel of the ball mill and effectively increase the load, but also enhance the impact and grinding between the medium and the material, thereby improving the grinding efficiency However, in the production process, the longterm action makes the Continue reading Five Five Reasons and Solutions for the Rapid Wear of Ball Mill Liner2021年8月12日 While the average mill wear of HiCr rolls was of the order of 0027 mm at F1 stand, it was 0313 mm, over 10 times higher, for the ICDP rolls at the next stand (F2) Average mill wear for all the ICDP rolls at F2–F6 stands was 0227 mm per roll per campaignInfluence of Roll Wear in Hot Rolling of Steel at Hot Strip Mills
.jpg)
Effect of Cold Forging on Wear Resistance of High Carbon Steel
2021年10月1日 Moreover, the wear rate of high carbon steel was found to decrease with an increase in hardness The cold forging process is found to have a significant effect on the hardness and wear rate of Metallurgical Plant Design and Operating Strategies (MetPlant 2011) 3 8 9 August 2011 Perth, WA Fig 1 Increase in throughput over liner life for a large SAG millThe Influence of Liner Wear on Milling Efficiency ResearchGateThe observed effects of temperature on wear of roll materialsvia oxide influence may be explained as follows: (i) the oxides formed in the range 400600 “C are Fe,O, and Fe,O, and increase abrasive wear; (ii) in contrast, within the range 600900 “C, the progressive formation of wustite increases the lubricating effect of the scale and Wear of hot rolling mill rolls: an overview Academiathe highest wear was between 125 m and 275 m in length of the shell of the mill The proposed liners, unlike the standard type, did not have a uniform shape, and the height of the liners increased from 152 mm to 187 mm in the area where the wear rate was high It is established thatThe study of the lining layer abrasing wear in the semi
.jpg)
(PDF) Grinding Media in Ball MillsA Review
2023年4月23日 an increased mill speed regardless of the type of liners, hence values of kinetic and potential energy increase At 80% of the critical speed, there is more liner wear because more grinding media 2024年3月1日 Forged wearresistant steel balls are commonly used in mine mills due to their high toughness, low crushing rate, and low energy consumption [[1], [2], [3]]When selecting steel balls, researchers have successively used low carbon steel, medium carbon steel and high carbon steel to produce martensitic grinding balls, however, high carbon steel grinding balls A new strategy for highly wearresistant ball using carbon Tool steels include TD2 (a high wear / low shock resistant tool steel), TS7 (a high shock / low wear resistant tool steel) and TA2 (a balanced medium wear / medium shock resistant tool steel) These designations come from Reference Tooling and Die Wear AHSS Guidelines2022年11月17日 It is indispensable to explore the appropriate level of surface residual stress to enhance the wear resistance of coated tools TiAlSiNcoated carbide tools with dissimilar surface residual compressive stresses (− 300 ~ − 600 MPa) are acquired via microsandblasting, which are used in the highspeed sliding friction experiments and turning experiments The influence Effect of TiAlSiN coating residual stress on its sliding wear and
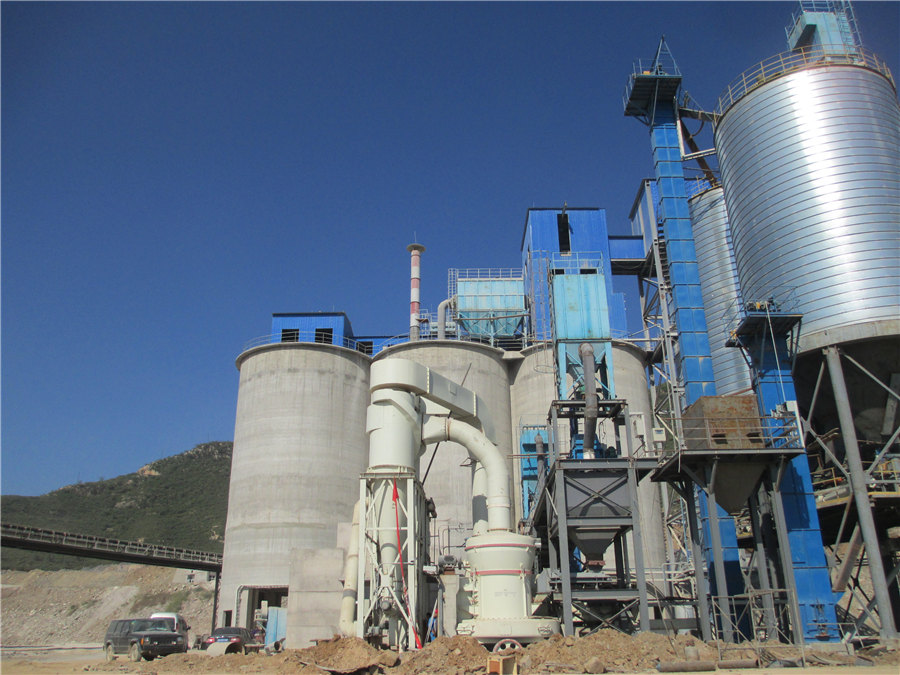
Wear mechanisms of coated carbide tools during highspeed face
2023年11月13日 However, there are serious tool wear during high speed cutting of Ti2AlNb intermetallic alloys because of its high specific strength and temperature strength, and the tool wear mechanism is unknown In this paper, the highspeed face milling trials of Ti2AlNb intermetallic alloys are performed to investigate tool wear evolutions and wear mechanisms2016年5月4日 It was found from Figure 9 that when the braking pressure is within a low range, the increase in temperature will not be obvious, and the strength of matrix material decreases slightly; so, the friction coefficient is relatively high 44 With a further increase in braking pressure, the temperature will increase gradually, which decreases the strength of matrix materialsReview on the friction and wear of brake materials2020年7月21日 In order to offer sophisticated tool monitoring systems throughout the chip formation process in turning high strength steel, a smart prediction model of tool wear machine learning algorithms An intelligent prediction model of the tool wear based on 2021年3月24日 The influence of low, medium, and high structural stiffness, corresponding to 549, 8583, and 68667 × 10 –3 N∙m 2, respectively, on wear properties of Albased alloys was reported by Tan et al The increase in structural stiffness resulted in a change of wear mechanisms from the delamination in the low stiffness case to the ploughing in the high Recent Progress on Wear‐Resistant Materials: Designs, Properties,
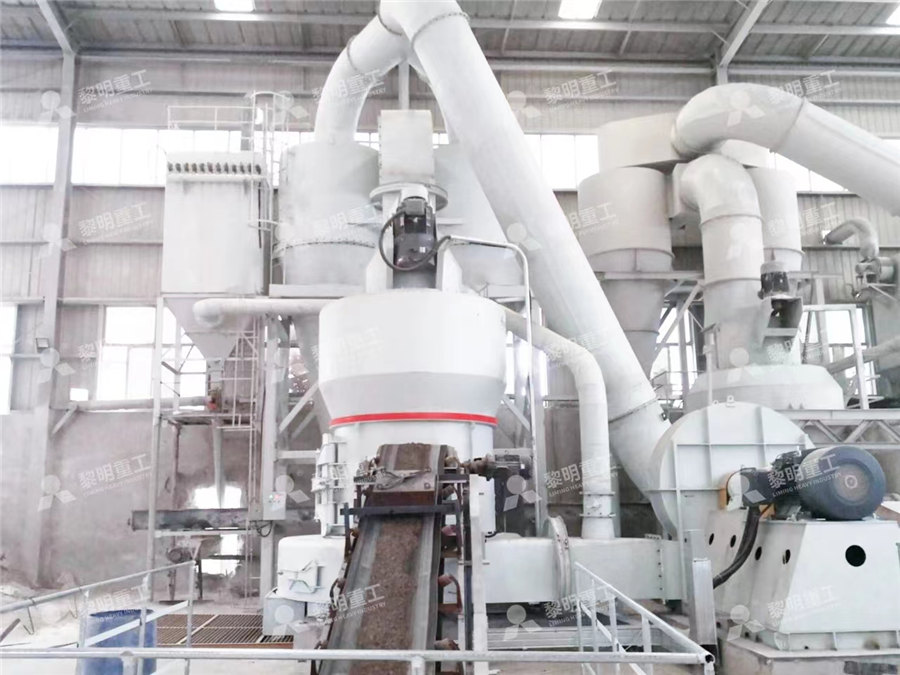
The Influence of Liner Wear on Milling Efficiency ResearchGate
2011年1月1日 The numerical calculation method is used to analyze the wear of the liner of the general structure of a semiautogenous mill in the axial direction, and the nonuniform wear of each area of the 2017年1月26日 The embryo adherence ratio increased by 103 and 110%, respectively when brown rice samples with moisture contents of 162 and 155% were milled by the vertical mill with a shaft speed of 900 Review on Parameters Influencing the Rice 2023年11月3日 However, there are few studies on tool wear in C f /SiC composites cutting [[28], [29], [30]]Liu et al [31] conducted ultrasonic vibrationassisted milling experiments on C f /SiC composites with chemical vapor deposition (CVD) diamond filmcoated milling cuttersThey discovered that microchipping and coating spalling were the most prevalent types of tool failureEffect of tool wear on machining quality in milling C2018年1月17日 As shown in Figure 4, wear morphologies, such as adhesive wear (Figure 4(f)), oxidation wear (Figure 4(a) and ), diffusion wear (Figure 4(a) and ), mechanical cracking and thermal cracking (Figure 4(c)), appear on the The relationships between cutting parameters, tool
.jpg)
Improving the Wear Resistance of PiercingMill Mandrels
periods at high temperature (800–1100 ° C at the nose) and must withstand the pressure of the deformed metal (up to 170 MPa), which moves at speeds up to 1 m/s Accordingly, the mandrel must be characterized by strength, hightemperature strength, and good heat conduction, as well as minimum inclination to weld with the rolled metal2022年1月1日 As shown in Fig 12, the wear rate of the particles increases with the revolution speed, and the increase in the wear rate is also large when the revolution speed is high In addition, the relationship between particle wear rate and rotation speed is also affected by the rotationrevolution speed ratioInvestigation of the ball wear in a planetary mill by DEM simulation 2020年11月22日 The largest wear ratio was at an angle of 30°60° degrees 12 The Nano coating layer of Tungsten Carbide is used to coat the surface of high chromium cast iron by using a thermal spray process Wear Resistance Improvement for Grinding Balls of Horizontal 2019年3月1日 Seven 4high mills equipped with individual roll bending and roll shifting actuators are generally included in the hot rolling line CVC work roll is used in the upstream mill stands (first four stands), and special parabolic work roll that can decrease the edge drop is used in the downstream mill stands (last three stands)High precision shape model and presetting strategy for strip hot
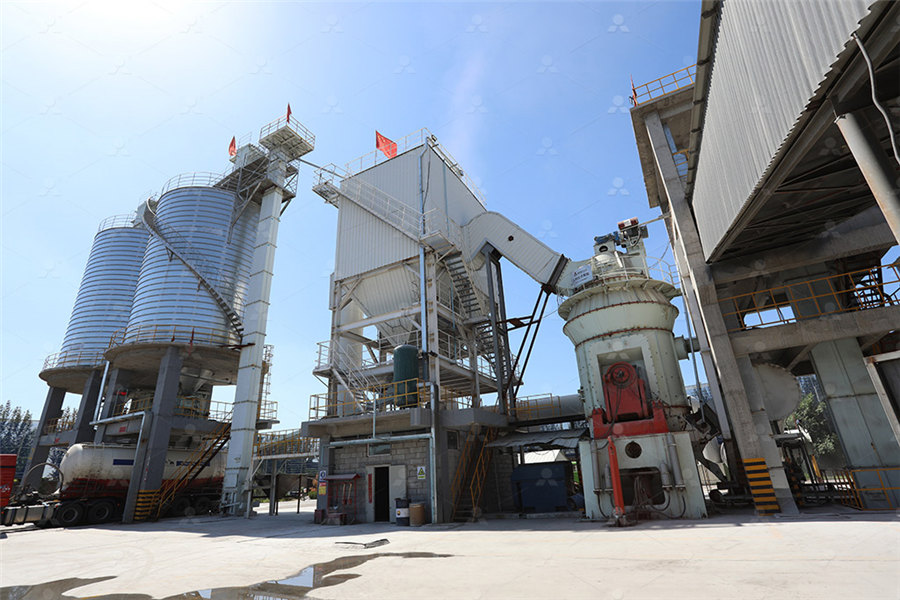
Friction and wear characteristics and simulation study of NM500
2024年9月12日 Friction and wear test equipment, scanning electron microscope, abrasion balls made of CGr15 high carbon chromium bearing steel, and liners made of NM500 steel were used for wear simulation and friction–wear experiments The variation trends of friction coefficient, wear amount, and subsurface characteristics under dry friction and slurry conditions were studied 2021年11月6日 Depending on various properties such as hardness, roughness, friction coefficient, wear resistance, and oxidation behavior, different grades of steel can be used in hot strip mills In this paper, two grades were investigated: one grade of semihighspeed steel and one grade of highspeed steel They differ in their chemical composition, principally the carbon Oxidation and wear behavior of highspeed steel and semihigh 2009年5月16日 The increase in liner life by around 50% along with increased mill throughput of over 20% Liners protect the mill shell against heavy impacts and wear, and lift charge high up [12 Modification of SAG mill liner shape based on 3D liner wear The observed effects of temperature on wear of roll materials via oxide influence may be explained as follows: i) the oxides formed in region 400 600 oC are Fe2O3 and Fe3O4 and increase abrasive WEAR OF HOT ROLLING MILL ROLLS: AN OVERVIEW

The study of the lining layer abrasing wear in the semiautogenous
2020年1月1日 Application of the proposed method in a 975 × 488 m SAG mill indicated that the liner wear profile along the liner length was nonuniform and the highest wear occurred between 125 m and 275 m Flank Wear is wear on the portion of the tool in contact with the finished part It’s the most common type of Tool Wear and the most predictable It occurs due to abrasion of the tool by the workpiece Harder workpiece materials will be more Increase Tool Life, Reduce Tool Wear Tormach2021年11月1日 Keywordsaustempered ductile iron–grinding media wear–ball mill good machinability, high strengthtoweight wear to fatigue delamination as the wear load increased from 25 N to 100 N (PDF) Morphology and wear of high chromium and2022年5月9日 As an important part of the ball mill, the lining plate can not only effectively protect the barrel of the ball mill and effectively increase the load, but also enhance the impact and grinding between the medium and the material, thereby improving the grinding efficiency However, in the production process, the longterm action makes the Continue reading Five Five Reasons and Solutions for the Rapid Wear of Ball Mill Liner
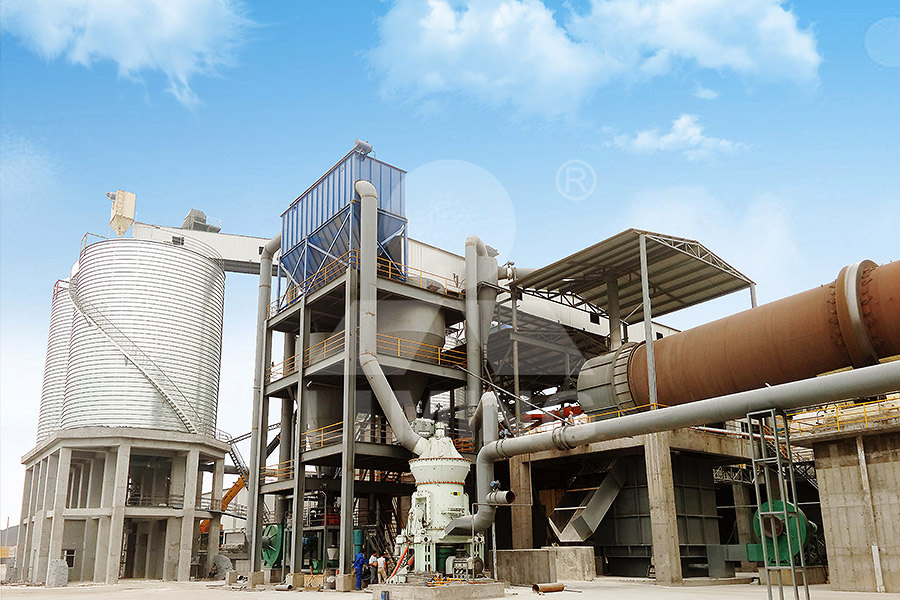
Influence of Roll Wear in Hot Rolling of Steel at Hot Strip Mills
2021年8月12日 While the average mill wear of HiCr rolls was of the order of 0027 mm at F1 stand, it was 0313 mm, over 10 times higher, for the ICDP rolls at the next stand (F2) Average mill wear for all the ICDP rolls at F2–F6 stands was 0227 mm per roll per campaign2021年10月1日 Moreover, the wear rate of high carbon steel was found to decrease with an increase in hardness The cold forging process is found to have a significant effect on the hardness and wear rate of Effect of Cold Forging on Wear Resistance of High Carbon Steel Metallurgical Plant Design and Operating Strategies (MetPlant 2011) 3 8 9 August 2011 Perth, WA Fig 1 Increase in throughput over liner life for a large SAG millThe Influence of Liner Wear on Milling Efficiency ResearchGateThe observed effects of temperature on wear of roll materialsvia oxide influence may be explained as follows: (i) the oxides formed in the range 400600 “C are Fe,O, and Fe,O, and increase abrasive wear; (ii) in contrast, within the range 600900 “C, the progressive formation of wustite increases the lubricating effect of the scale and Wear of hot rolling mill rolls: an overview Academia
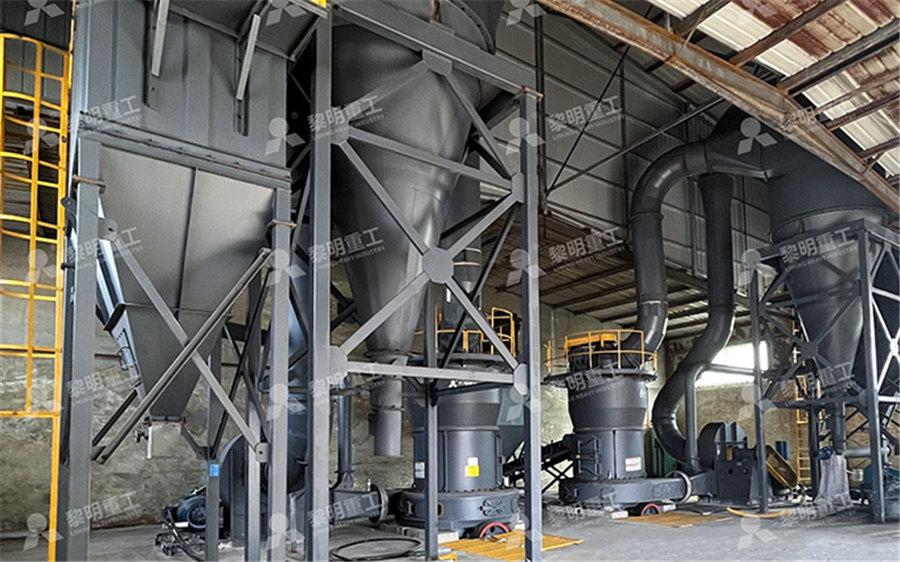
The study of the lining layer abrasing wear in the semi
the highest wear was between 125 m and 275 m in length of the shell of the mill The proposed liners, unlike the standard type, did not have a uniform shape, and the height of the liners increased from 152 mm to 187 mm in the area where the wear rate was high It is established that