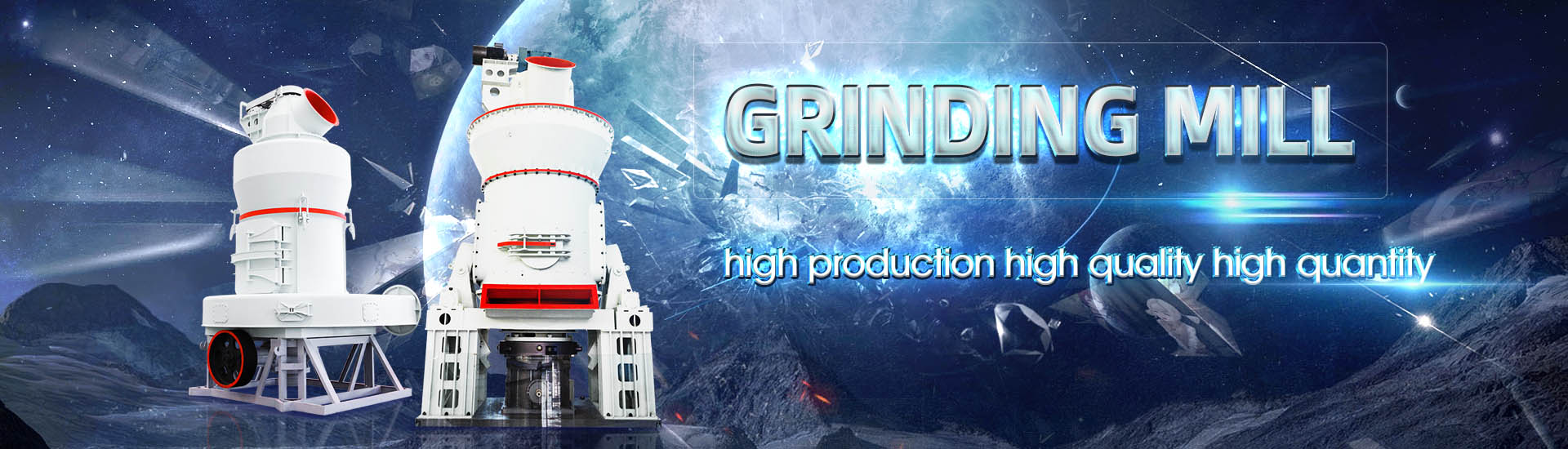
Coal injection mill scraper production
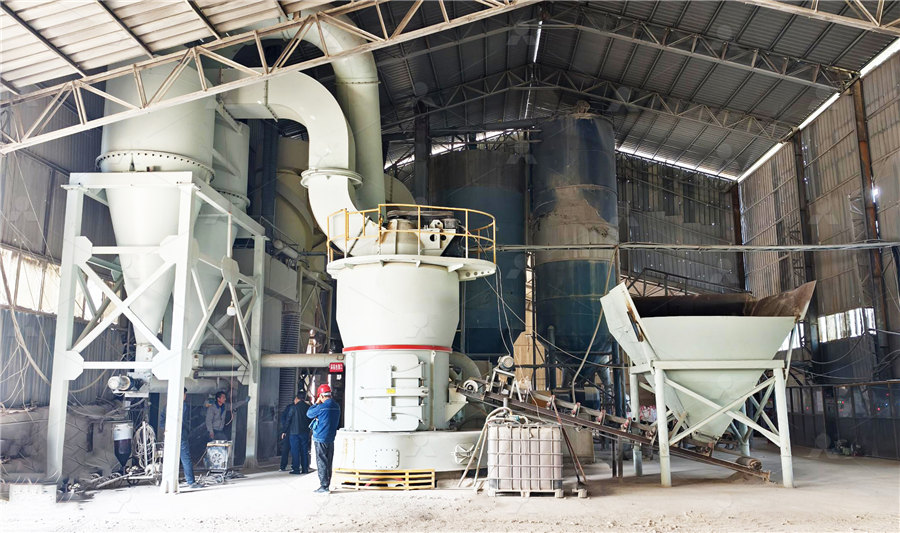
Pulverized Coal Injection Paul Wurth
Pneumatic transfer of pulverized coal into the Distribution Device as well as conveying of individual flows from the Distribution Device into the hot blast tuyeres are performed by means Pulverized Coal Injection (PCI) using the denseflow method The Küttner developed and perfected denseflow method offers several advantages over a lowerdensity system Higher Pulverized coal injection (PCI) Iron Steel Kuettner GroupPulverized coal injection technology has the potential to spur innovations to blast furnaces: recycled materials, such as waste plastics and biomass, as well as recycled ores can be injected3A2 Pulverized Coal Injection for Blast Furnaces (PCI)Tagil Metallurgical Plant started successfully the injection of pulverized coal into their blast furnace Nr 5 As scheduled, blast furnace No 6 followed approximately 1 month later Initially FIRST SUCCESSFUL PULVERIZED COAL INJECTION ABM
.jpg)
WorldProven Coal Pulverizer Technology Debuts in the US
springloaded, MB type, vertical spindle mills, each gravimetric belt feeder, seal air fan, 1800 rpm primary air fan, and four mill outlets supplying pulverized coal to one of the three horizontal 2024年8月6日 In an integrated steel plant, the pulverized coal injection (PCI) mill plays an important role in providing pulverized coal to the blast furnace The main purpose of using PCI Failure Analysis of Pulverized Coal Injection (PCI) Mill Grinding 2022年5月1日 Pulverized coal injection (PCI) is generally used in modern blast furnace (BFs) ironmaking to reduce coke consumption by burning cheaper coal This paper presents a Optimization of pulverized coal injection (PCI) rate in an 2018年10月21日 Pulverized coal injection (PCI) is a wellestablished technology for hot metal (HM) production in a blast furnace (BF) It is practiced in most of the BFs and all the new BFs Understanding Pulverized Coal Injection in Blast Furnace
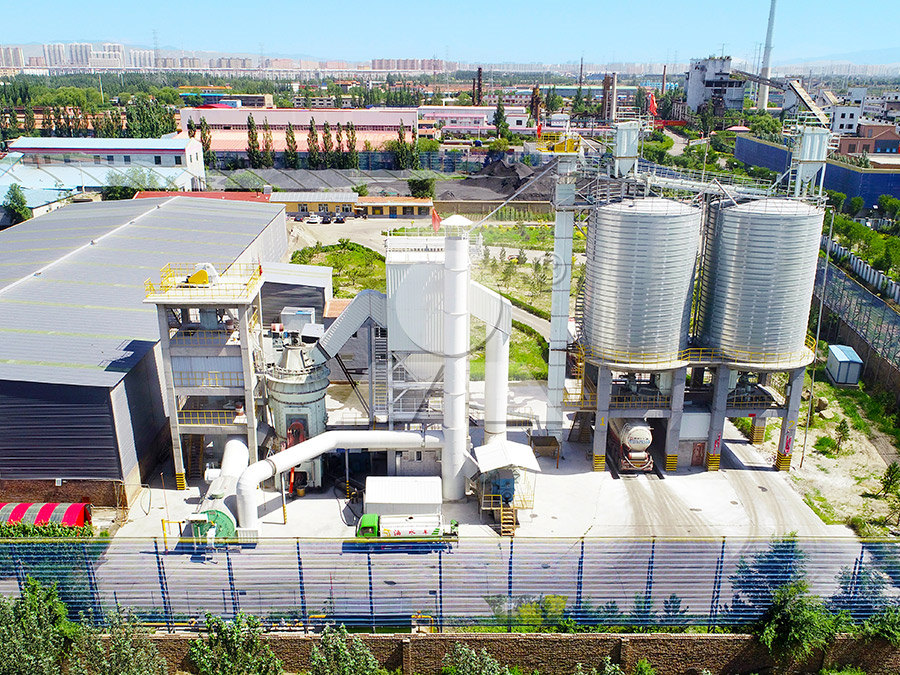
Impacts of Blending Semicoke in PCI coal on Grinding Efficiency
Pulverized coal injection (PCI) is an important means to save coke and reduce smelting costs for blast furnace As the pig iron production remains high and the PCI ratio continues to grow, the 2017年5月1日 The introduction of pulverizedcoal injection at Yenakiieve Iron and Steel Works in 2016 is described The state of the lining of the blastfurnace shaft and hearth is analyzed(PDF) Introduction of pulverizedcoal injection at2003年1月1日 Pulverized coal injection has assisted the steel industry to lower operating costs, extend coke oven life and lower greenhouse emissions As the understanding of the impact of quality of the Impact of PCI Coal Quality on Blast Furnace Coal injection system Reduced pollution Coal grinding and injection systems are nonpolluting systems Injecting pulverized coal into a blast furnace reduces the overall pollution made by coke production Increased productivity Installation of a coal injection system can increase productivity through improved operation of the blast furnacePulverized Coal Injection Ammermann
.jpg)
Pulverized Coal Injection of Blast Furnace Ironmaking
2024年1月1日 The characteristics of pulverized coal injection of blast furnace ironmaking include basic performance (ash, sulfur, and fixed carbon) and process performance (ignition point, explosibility, grindability, ash fusion temperature, combustibility, and reactivity), which is an important basis for the selection of coal types for pulverized coal injection of blast furnace SINOMALY has decades of experience of coal mill production The coal mill manufactured by the SINOMALY is made of highstrength alloy, which is wearresistant and corrosionresistant, with the maximum capacity of 85 T/hCoal Mill Coal Grinding Mill Producer SINOMALY2020年9月11日 The pulverized coal injection (PCI) is pursued to reduce the hot metal production cost by replacingthe expensive metallurgical coke with the noncoking coalTechnological advancements in evaluating the performance of coal injection (PCI) An annual reduction of 265 000 tonnes CO 2 equivalents is achieved by one biochar production plant, Ba pulp mill integrated biochar production scenario for bark basic density wood dry mass divided by green solid volume BOS basic oxygen steelmakingVTT Technology 351: Replacing Coal Used in Steelmaking with

Pulverized coal injection method Wikipedia
Pulverized coal injection was developed in the 19th century, but was not implemented industrially until the 1970s Rises in the cost of coke due to increased global demand and thus more competition for the resource have made this method attractive to the ironproducing industries and increased its value The PCI method is based on the simple concept of primary air (termed 2021年8月18日 In injection method 1, 30% MOBFRGI1 had a lower reducing gas injection volume, and the pulverized coal burnout was 6% higher than that of the TBF The 40 and 50% MOBFRGI1 reducing gas injection volumes were too large and were not conducive to the combustion of pulverized coal, resulting in a sharp decrease in its burnoutInfluence of Reducing Gas Injection Methods on Pulverized Coal FIRST SUCCESSFUL PULVERIZED COAL INJECTION STARTUP IN RUSSIA AT EVRAZ NTMK1 Alexey Kushnarev2 Philipp Bermes 3 integrated steel production plant, which in 2010 produced 43 million tons of hot Inside the mill, the raw coal is grinded to fine pulverised coal, classified and dried with drying gasFIRST SUCCESSFUL PULVERIZED COAL INJECTION ABM ROLLER MILL CONVEYING (INJECTION) HOPPERS PULVERIZED COAL STORAGE BIN STORAGE BIN BAGFILTERS PRESSURIZING GAS VESSELS DRYING GAS MAIN FANS DRYING GAS GENERATORS 3 MAIN BAGFILTERS PRESSURIZING The pulverized coal injection technology is based on a combination of several unit operations Main unit operations Pulverized Coal Injection Paul Wurth

Control Blast Furnace Pulverized Coal Injection to Increase PCI
Control Blast Furnace Pulverized Coal Injection to Increase PCI Rates Roland Weiser, Ingo Braune, Peter Matthes AMEPA GmbH Jülicher Str 320 D52070 Aachen Germany Tel: +49241168040 Fax: +492411680444 Email: info@amepa Key words: Pulverized coal injection, Coal flow meter, Controlled injection, Equal distribution, Increase of PCIThe injection of the pulverized coal into the BF results into (i) increase in the productivity of the BF, ie the amount of hot metal (HM) produced per day by the BF, (ii) reduce the consumption of the more expensive coking coals by Understanding Blast Furnace Ironmaking with Pulverized Coal Injection (PCI) using the denseflow method The Küttner developed and perfected denseflow method offers several advantages over a lowerdensity system Higher injection rates are achieved with simultaneously lower coke rates, which can optimize the fuel costs of the blast furnacePulverized coal injection (PCI) Iron Steel Kuettner Group2019年7月2日 80120 °C of low volatile coal injection and 150220 °C of high volatile coal i njection [10] Recent studies indicated that the rate of NG injection into the BF could be increasedModern blast furnace ironmaking technology: potentials to

Effects of water injection on reaction temperature and hydrogen
2024年10月26日 Underground coal gasification (UCG) is process of directly recovering energy as combustible gases such as hydrogen and carbon monoxide by combusting unmined coal resources in situ During UCG 2022年3月16日 The production process of direct reduced iron from titanomagnetite by coal reduction in air in rotary kiln is a key step in the extraction of titanium and iron This process is conducive to alleviating the stocking problem of a large amount of Tibearing blast furnace slag The relationships between particle movement and pulverized coal injection combustion in Particle motion simulation and pulverized coal injection 2022年5月1日 Optimization of pulverized coal injection (PCI) rate in an ironmaking blast furnace by an integrated process model Author links open overlay panel Lingling Liu a, However, coke production causes considerable energy consumption and greenhouse emissions and accounts for a big portion of pig iron production costs [1]Optimization of pulverized coal injection (PCI) rate in an In November 2011 Loesche GmbH obtained a contract for the first ever 4roller coal mill for the injection of pulverized coal into a blast furnace (PCI technology) The Loesche Mill Type LM 434 D has a capacity of 120 t/h and will be installed in the A coal mill for the injection of pulverized coal
.jpg)
Failure Analysis of Pulverized Coal Injection (PCI) Mill Grinding
Abstract In an integrated steel plant, the pulverized coal injection (PCI) mill plays an important role in providing pulverized coal to the blast furnace The main purpose of using PCI coal is to reduce the hot metal production cost through the utilization of noncoking coal and to extend the available coke oven life Any unplanned outage of 2014年1月1日 The emission factors of kiln end, kiln head, coal mill, crushing and cement mill was 0156 clinker g/t, 3914 clinker g/t, 1538 coal g/t, 0016 stone g/t and 0056 cement g/t respectively, the (PDF) MPS mills for coal grinding ResearchGateSafe operation of coal grinding systems: Raw coal silo protection against fire and explosions Safe operation of coal grinding systems: Raw coal yard management The purchasing process for coal grinding systems needs changes Talk at a Coal Mill Safety, Explosion and Fire Protection coal used in pulverised coal injection (PCI) in the blast furnace with sustainable biochar4 Some development continues to further optimise charcoal production to improve its product specifications for steel production5 The Torero partnership project is testing the use of biocoal (torrefied waste wood) to partially substitute coal inFact sheet Biomass in steelmaking
.jpg)
(PDF) Coal dust injection in blast furnace ResearchGate
2012年1月1日 Coal Dust Injection ( CD I ) has been playing a major role in reducing coke rate production rate of the furnace Mn ore / Mill scale is charged for cleaning the hearthMedium speed coal pulverizer Introduction Medium speed coal pulverizer also known as medium speed coal vertical roller mill is an equipment widely used in the cement production plant and cement grinding stationThe mediumspeed coal mill refers to the coal mill with a working speed of 50300r/min, which belongs to the professional equipment for the preparation and processing Medium speed coal pulverizerVertical roller millEconomy Our research group, KEPCO Research Institute had setup the a coal gasifier for the pilot test and conducted many experiments for parametric study in this project Our group focused visualization of pulverized coal injection pattern in the gasifier Through this study we found that two types of coal burners having different oxygenA study on Coal Water Mixture production using various mill With experienced technicians and production personnel in a professional process independently to produce three categories, more than 30 varieties of activated carbon, including: coconut shell charcoal, carbon, water, imported coal, carbon, electroplating, injection with charcoal, medicinal charcoal, sugar charcoal, food grade activated carbon, carbon reagents, precious metals pulverised coal injection 英中 – Linguee词典
.jpg)
Energy Conservation for Granular Coal Injection into a Blast
2012年7月31日 Due to the lack of knowledge regarding the combustion of granular coal injected into a blast furnace, injection characteristics of granular coal were first studied through proximate analysis, element analysis, and research of explosivity, ignition point, meltability of ash, grindability, calorific value, etc Using a sampling device in the raceway combined with Pulverized Coal Injection (PCI) is a process that involves blowing large volumes of fine coal granules into the BF This provides a supplemental carbon source to speed up the production of metallic iron, reducing the need for coke production As a result energy use and emissions can be reduced However, as coke provides physical support and gas permeability in the BF, its Pulverized Coal Injection Industrial Efficiency TechnologyBlast Furnace Granulated Coal Injection System Demonstration Project: A DOE Assessment WV 265070880 and PO Box 10940, 626 Cochrans Mill Road Pittsburgh, PA 152360940 2 Disclaimer This report was prepared as an account of work sponsored by an agency of the United States Government Determine Blast Furnace Production Rate As a Blast Furnace Granulated Coal Injection System Demonstration 2017年5月1日 The introduction of pulverizedcoal injection at Yenakiieve Iron and Steel Works in 2016 is described The state of the lining of the blastfurnace shaft and hearth is analyzed(PDF) Introduction of pulverizedcoal injection at
.jpg)
Impact of PCI Coal Quality on Blast Furnace
2003年1月1日 Pulverized coal injection has assisted the steel industry to lower operating costs, extend coke oven life and lower greenhouse emissions As the understanding of the impact of quality of the Coal injection system Reduced pollution Coal grinding and injection systems are nonpolluting systems Injecting pulverized coal into a blast furnace reduces the overall pollution made by coke production Increased productivity Installation of a coal injection system can increase productivity through improved operation of the blast furnacePulverized Coal Injection Ammermann2024年1月1日 The characteristics of pulverized coal injection of blast furnace ironmaking include basic performance (ash, sulfur, and fixed carbon) and process performance (ignition point, explosibility, grindability, ash fusion temperature, combustibility, and reactivity), which is an important basis for the selection of coal types for pulverized coal injection of blast furnace Pulverized Coal Injection of Blast Furnace IronmakingSINOMALY has decades of experience of coal mill production The coal mill manufactured by the SINOMALY is made of highstrength alloy, which is wearresistant and corrosionresistant, with the maximum capacity of 85 T/hCoal Mill Coal Grinding Mill Producer SINOMALY
.jpg)
Technological advancements in evaluating the performance of
2020年9月11日 The pulverized coal injection (PCI) is pursued to reduce the hot metal production cost by replacingthe expensive metallurgical coke with the noncoking coalcoal injection (PCI) An annual reduction of 265 000 tonnes CO 2 equivalents is achieved by one biochar production plant, Ba pulp mill integrated biochar production scenario for bark basic density wood dry mass divided by green solid volume BOS basic oxygen steelmakingVTT Technology 351: Replacing Coal Used in Steelmaking with Pulverized coal injection was developed in the 19th century, but was not implemented industrially until the 1970s Rises in the cost of coke due to increased global demand and thus more competition for the resource have made this method attractive to the ironproducing industries and increased its value The PCI method is based on the simple concept of primary air (termed Pulverized coal injection method Wikipedia2021年8月18日 In injection method 1, 30% MOBFRGI1 had a lower reducing gas injection volume, and the pulverized coal burnout was 6% higher than that of the TBF The 40 and 50% MOBFRGI1 reducing gas injection volumes were too large and were not conducive to the combustion of pulverized coal, resulting in a sharp decrease in its burnoutInfluence of Reducing Gas Injection Methods on Pulverized Coal
.jpg)
FIRST SUCCESSFUL PULVERIZED COAL INJECTION ABM
FIRST SUCCESSFUL PULVERIZED COAL INJECTION STARTUP IN RUSSIA AT EVRAZ NTMK1 Alexey Kushnarev2 Philipp Bermes 3 integrated steel production plant, which in 2010 produced 43 million tons of hot Inside the mill, the raw coal is grinded to fine pulverised coal, classified and dried with drying gas