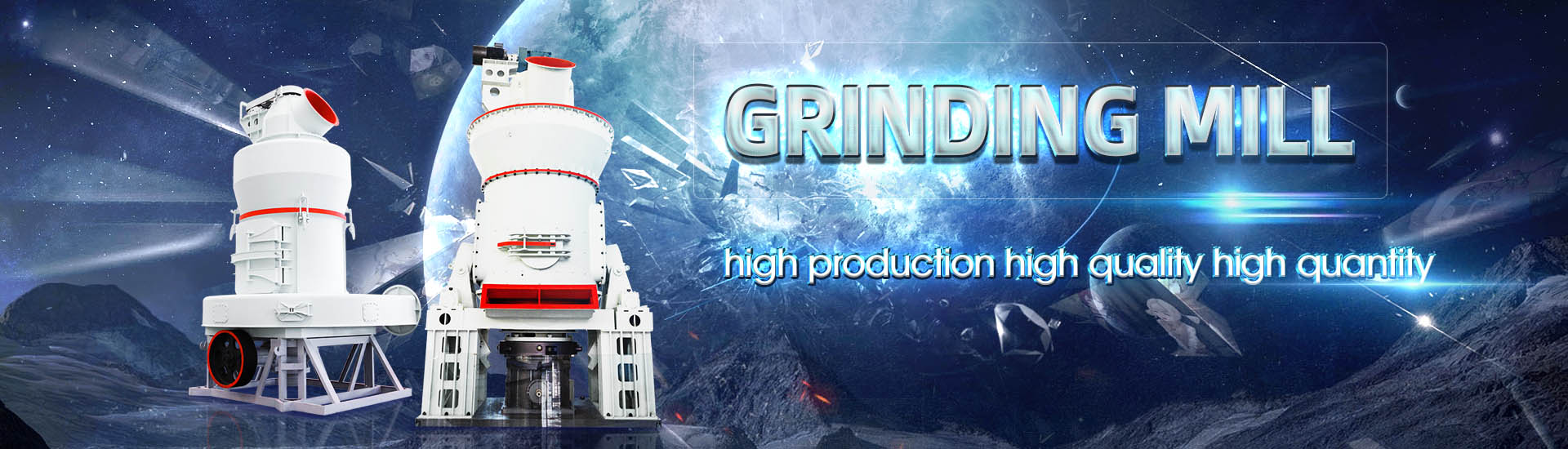
Parameter table of silica grinding machine

Parameter Optimization of Ball Milling Process for Silica
2019年3月1日 The three main parameters applied in this study are Ball to Powder weight Ratio (BPR), time milling process, and rotational speed (rpm) The materials used in the study was Bangka silica sand tailing, with an average size of D50: 267 µm, based on the measurement 2016年4月1日 Firstly, the mathematical models are required to determine the optimum machining parameters including depth of cut, feed, grit size and grit density, in order to Optimizing machining parameters to combine high productivity 2018年5月30日 The optimum conditions of grinding parameters for lower surface roughness for EN8 steel were the grinding wheel speed 1400 rpm, table travel speed 10 m min −1, depth of cut 10 µm, grinding wheel A60K5V10 and Optimization of parameters in cylindrical and surface 2018年2月19日 Based on microindentation mechanics and kinematics of grinding processes, theoretical formulas are deduced to calculate surface roughness (SR) and subsurface damage Effect of grinding parameters on surface roughness and

Grinding Parameters SpringerLink
2019年1月1日 'Grinding Parameters' published in 'CIRP Encyclopedia of Production Engineering' In general the material removal rate can be calculated by the actuating cross section A w, which is the cross section between tool and 2018年2月19日 damage during bound abrasive grinding of fused silica glass,” Appl Surf Sci 353, 764–773 Table 2 Grinding parameters by LHD meth od and SR and SSD depth for each fused Effect of grinding parameters on surface roughness and Crackfree ductile mode grinding of fused silica under controllable dry grinding conditions Wei Wanga,b, Peng Yaoa,b,n, Jun Wangc,n, Chuanzhen Huanga,b, Hongtao Zhua,b, Bin Zoua,b, Hanlian Liua,b, Jiwang Yand a Center for Advanced Jet Engineering Technologies (CaJET), School of Mechanical Engineering, Shandong University, Jinan, Shandong , China b International Journal of Machine Tools Manufacture2016年10月1日 Singlecrystal silica, ceramics and most optical glass are reported to be grindable in ductile mode with a grinding depth of several micrometers using precision machine tools [4], [5], [6]However, it is extremely difficult to grind fused silica in ductile mode without causing any cracksCrackfree ductile mode grinding of fused silica under
.jpg)
Models of grindinginduced surface and subsurface damages
2021年9月1日 Calculated strain rates under (a) different grinding parameters: grinding depth a p, wheel speed v s, feed speed v w, and (b) different abrasive grit parameters: half apex angle α, grit diameter d g, tip radius r, extrusion depth Δh Download: Download highres image (232KB) Download: Download fullsize image; Fig 182024年2月1日 Fused silica was polished to a high quality by a CO2 laser beam with a rapid scanning rate The rapid scanning rate produced a line laser heat source, resulting in a “polishing line” during the polishing process The Taguchi method was used to evaluate the comprehensive influence of polishing process parameters on the polishing qualities Four factors, namely the Process Parameter Optimization for CO2 Laser Polishing of Fused Silica the actual grinding process need further investigation This paper presents a dry grinding process using a vitrified bond CBN grinding wheel with high temperature resistance to achieve crackfree ductile mode grinding of fused silica The high temperature induced by grinding heat improves the ductile machinability of fused silicaInternational Journal of Machine Tools ManufactureChinese Journalof Engineering T : Parameters optimization experiments results Experiment BPR Jar volume Rotation speed Particle size ( m)Research Article Process Parameters Optimization of Silica Sand

[PDF] Study on Effect of Ultrasonic Vibration on Grinding Force
2014年7月8日 Ultrasonic vibration assisted micro end grinding (UAMEG) is a promising processing method for micro parts made of hard and brittle materials First, the influence of ultrasonic assistance on the mechanism of this processing technology is theoretically analyzed Then, in order to reveal the effects of ultrasonic vibration and grinding parameters on grinding 2020年10月21日 Star make model centerless grinding machine was used for grinding the workpiece MITUTOYO make tester was used to measure the surface roughness The lateral and longitudinal dimensions of the workpiece were measured using vernier calliper ranging from 0 to 300 mm Weight was measured using a weighing pan of capacity 400 gm with three decimal Analysis of Centerless Grinding Process Parameters in 2021年6月17日 The experiment was carried out on an MK2710 race grinding machine (Wuxi Machine Tool Group, Wuxi, China) for the inner ring (Fig 1a) A diamond grinding wheel (Fig 1b) with metallic bond and grain size of 120# was used for the experiment The inner surface of the ring of the Si 3 N 4 ceramics (Fig 1c) was processed (Fig 1d) in the experimentEffect of grinding parameters on surface quality in internal grinding 2024年7月13日 This paper aims to optimize the grinding parameters of a surface grinding machine through the combined application of Response Surface depth of cut, table feed, and wheel material, alongside table travel speed for surface grinding, and work speed for cylindrical grinding Fengping Li, Yao Xue, Zhengya Zhang, Wenlei Optimizing Process Parameters for Surface Grinding of Heated
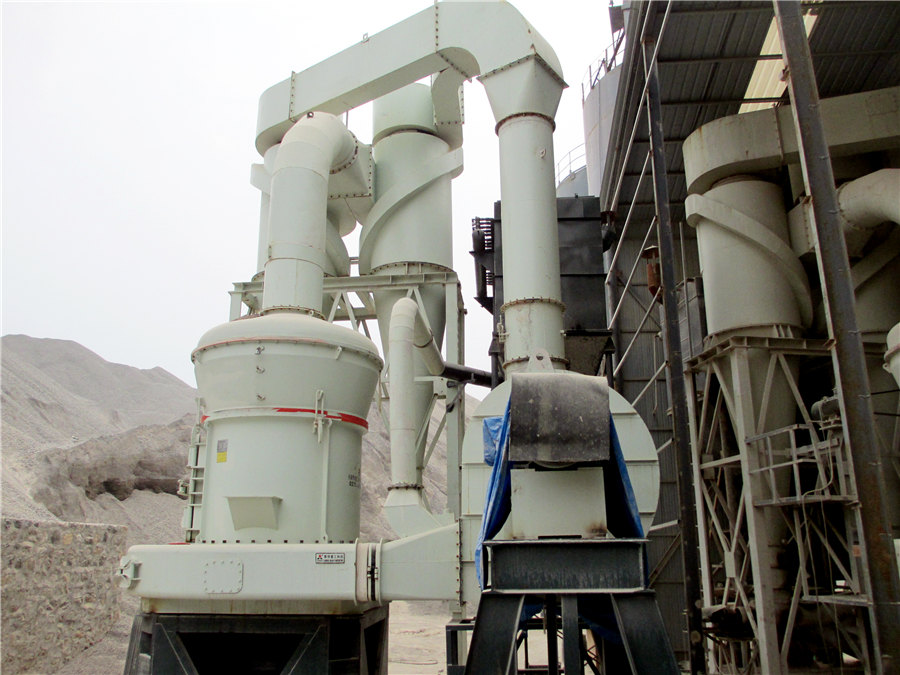
Ductile mode grinding of reactionbonded silicon
2017年9月8日 Contrast experiments were also conducted on fused silica, using the same grinding parameters; this produced only very rough surfaces, which further validated the feasibility of the proposed model2018年5月30日 The experiments were conducted on a surface grinding machine with a cylindrical grinding attachment at different combinations of grinding process parameters For surface grinding, the machine allowed rpm as well as table feed variations, whereas for cylindrical grinding, only the fixed rpm mechanism was availableOptimization of parameters in cylindrical and surface grinding for 2018年2月6日 Grinding is the material removal and a surface finish process in which the material is removed from the work surface in the phase of small chips by process of tiny abrasive particles of grinding (PDF) A Review of Cylindrical Grinding Process parameters by 2010年9月1日 There is a demand for highefficiency and high surface integrity grinding of fused silica Ductile grinding is an ideal method for producing a mirror finished surface on hard and brittle materials Ductile and Brittle Mode Grinding of Fused Silica ResearchGate
.jpg)
(PDF) Chemical Processing of Bauxite: Alumina and Silica Minerals
2022年1月23日 Chemical Processing of Bauxite: Alumina and Silica Minerals—Chemistry, Kinetics and Reactor DesignContrast experiments were also conducted on fused silica, using the same grinding parameters; this produced only very rough surfaces, which further validated the feasibility of the proposed model The demand for reactionbonded silicon carbide (RBSiC) mirrors has escalated recently with the rapid development of space optical remote sensors used in astronomy or Earth Ductile mode grinding of reactionbonded silicon carbide mirrors2024年3月1日 The main influencing factors for grinding damage include abrasive grit size, grinding depth, workpiece feed speed, and wheel speed According to the research of Sabia et al [13], the grinding subsurface damage depth (SSD) of glass ceramics is proportional to 5 times the average abrasive grit sizeMa et al [14] found that the SSD of fused silica is 4–6 times the Optimization of grinding process for hard and brittle materials Effect of grinding parameters on surface mechanical damage distributions during grinding of fused silica,” J NonCryst Solids 352(52–54), 5601–5617 (2006) 2 HEffect of grinding parameters on surface roughness and
.jpg)
Comparative Study on Improving the Ball Mill Process Parameters
2021年2月19日 Taguchibased experimental design technique has been a major research area for making systematic approaches to understand the complex process of ball mill process parameters influencing on the synthesis of ultrafine silica sand monolayer degradation To determine an optimal setting, Taguchi coupled optimization technique has been applied with a 2021年11月1日 Aiming at the difficulty of realtime ceramic surface roughness monitoring in the automatic grinding process, a time–spatial domain spectrum analysis method was proposed based on the monitored (PDF) Realtime monitoring of silica ceramic Fig 1: Grinding Machine used for experiment Fig 2: Grinding of work piece Table 1: Grinding Parameter Grinding Parameter Depth of cut in mm (D) Feed Rate in mm/rev (f) Speed rpm (N) Material Hardness (H) Level 1 20 006 145 30 Level 2 30 012 247 40 Level 3 40 018 415 50Optimization of Cylindrical Grinding Machine Parameters for 2019年12月18日 CNC cylindrical grinding machine parameters Table 1 CNC cylindrical grinding machine parameters Parameters Numerical Value Wheel speed (r/min) 1500–3000 Head frame speed (r/min)MultiObjective Parameter Optimization Dynamic Model of Grinding
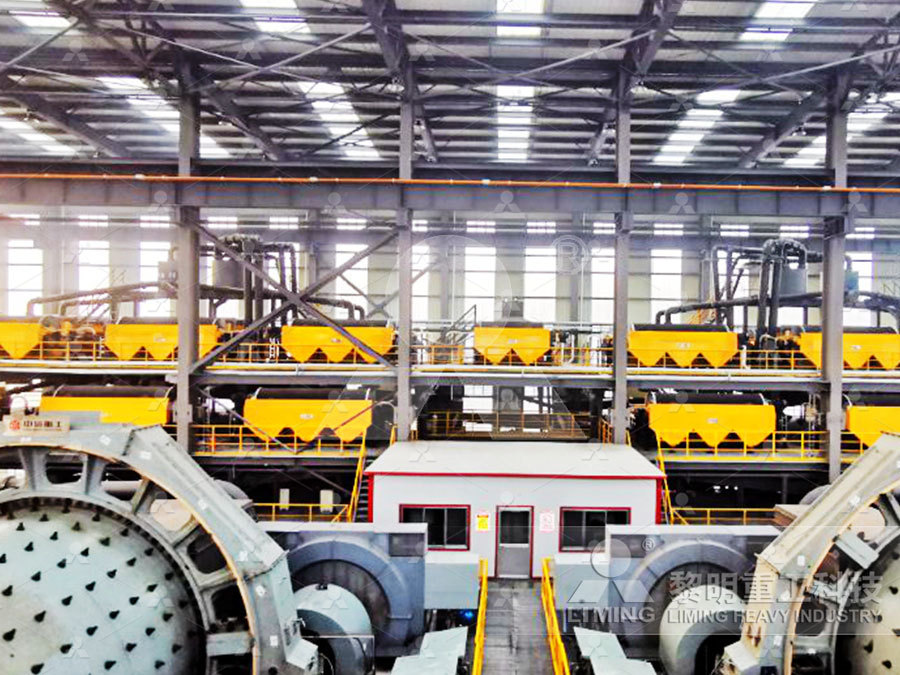
INVESTIGATION INTO GRINDABILITY OF GH4169 SUPERALLOY AND
external grinding was designed, as shown in Table 3 The three factors investigated here are Table 3 Orthogonal design external grinding tests SI characteristics measurement Samples No Grinding parameters SI characteristics measurement v w (m/min) a p (mm) v s (m/s) R a (µm) σ R0 (MPa) HV 1 (kgf/mm2) EG1 8 0005 15 0259 2418 512382 Through microgrinding experiments, this paper explored the relationship between the machining quality of CVD diamondcoated microgrinding tools and grinding parameters when processing fused silica The results showed that the machining quality improved with increasing feed speed and grinding depth but decreased with increasing spindle speedMachining performance and wear mechanism of CVD diamond 2024年3月1日 In order to increase the variety of input parameters, the PlackettBurman design method was applied Seven input parameters with 2 or 3 levels were used for the design (Table 5) The input parameters are as follows: 1 Grinding Direction (the grinding process starts from the edge of the workpiece towards the center of the workpiece or vice Evaluation of grinding parameters on the surface and sub force Therefore, a total of 75 groups of silica ceramic composites grinding experiments on the five levels of these three factors were designed These grinding parameters values are shown in Table 1Realtime monitoring of silica ceramic composites grinding
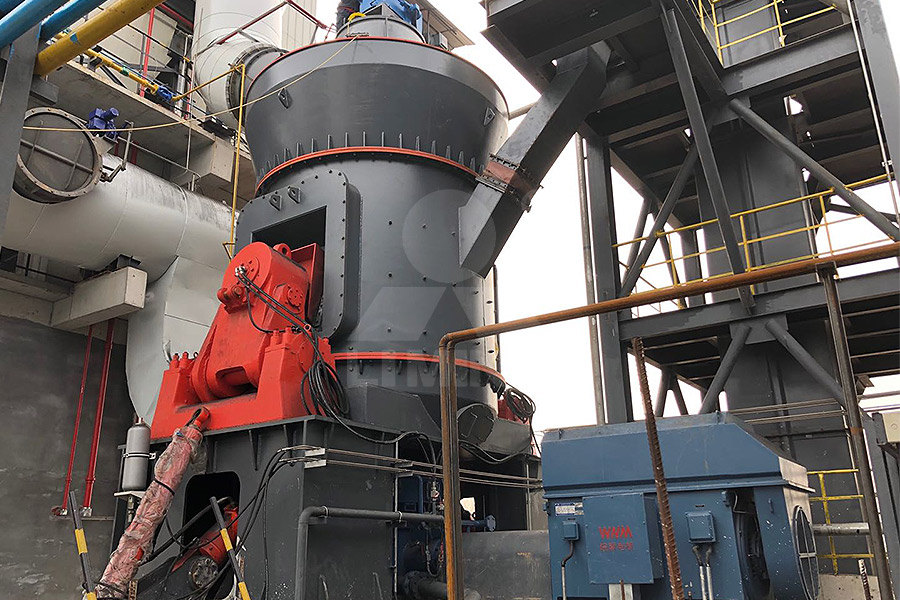
OPTIMIZING THE PROCESS PARAMETERS OF ELID GRINDING
clearly improved the quality characteristics of grinding process compared to quality levels achieved for conventional machine parameter settings Key Words: ELID Grinding, DOE, Grey Relation Analysis, Optimization 1 INTRODUCTION Metal grinding process has been one of the major manufacturing processes for centuries InDownload Table Process parameters of the grinding process from publication: Measuring strain during a cylindrical grinding process using embedded sensors in a workpiece This paper presents Process parameters of the grinding process Download Table2019年1月1日 'Grinding Parameters' published in 'CIRP Encyclopedia of Production Engineering' In general the material removal rate can be calculated by the actuating cross section A w, which is the cross section between tool and Grinding Parameters SpringerLink2018年2月19日 damage during bound abrasive grinding of fused silica glass,” Appl Surf Sci 353, 764–773 Table 2 Grinding parameters by LHD meth od and SR and SSD depth for each fused Effect of grinding parameters on surface roughness and
.jpg)
International Journal of Machine Tools Manufacture
Crackfree ductile mode grinding of fused silica under controllable dry grinding conditions Wei Wanga,b, Peng Yaoa,b,n, Jun Wangc,n, Chuanzhen Huanga,b, Hongtao Zhua,b, Bin Zoua,b, Hanlian Liua,b, Jiwang Yand a Center for Advanced Jet Engineering Technologies (CaJET), School of Mechanical Engineering, Shandong University, Jinan, Shandong , China b 2016年10月1日 Singlecrystal silica, ceramics and most optical glass are reported to be grindable in ductile mode with a grinding depth of several micrometers using precision machine tools [4], [5], [6]However, it is extremely difficult to grind fused silica in ductile mode without causing any cracksCrackfree ductile mode grinding of fused silica under 2021年9月1日 Calculated strain rates under (a) different grinding parameters: grinding depth a p, wheel speed v s, feed speed v w, and (b) different abrasive grit parameters: half apex angle α, grit diameter d g, tip radius r, extrusion depth Δh Download: Download highres image (232KB) Download: Download fullsize image; Fig 18Models of grindinginduced surface and subsurface damages 2024年2月1日 Fused silica was polished to a high quality by a CO2 laser beam with a rapid scanning rate The rapid scanning rate produced a line laser heat source, resulting in a “polishing line” during the polishing process The Taguchi method was used to evaluate the comprehensive influence of polishing process parameters on the polishing qualities Four factors, namely the Process Parameter Optimization for CO2 Laser Polishing of Fused Silica

International Journal of Machine Tools Manufacture
the actual grinding process need further investigation This paper presents a dry grinding process using a vitrified bond CBN grinding wheel with high temperature resistance to achieve crackfree ductile mode grinding of fused silica The high temperature induced by grinding heat improves the ductile machinability of fused silicaChinese Journalof Engineering T : Parameters optimization experiments results Experiment BPR Jar volume Rotation speed Particle size ( m)Research Article Process Parameters Optimization of Silica Sand 2014年7月8日 Ultrasonic vibration assisted micro end grinding (UAMEG) is a promising processing method for micro parts made of hard and brittle materials First, the influence of ultrasonic assistance on the mechanism of this processing technology is theoretically analyzed Then, in order to reveal the effects of ultrasonic vibration and grinding parameters on grinding [PDF] Study on Effect of Ultrasonic Vibration on Grinding Force 2020年10月21日 Star make model centerless grinding machine was used for grinding the workpiece MITUTOYO make tester was used to measure the surface roughness The lateral and longitudinal dimensions of the workpiece were measured using vernier calliper ranging from 0 to 300 mm Weight was measured using a weighing pan of capacity 400 gm with three decimal Analysis of Centerless Grinding Process Parameters in