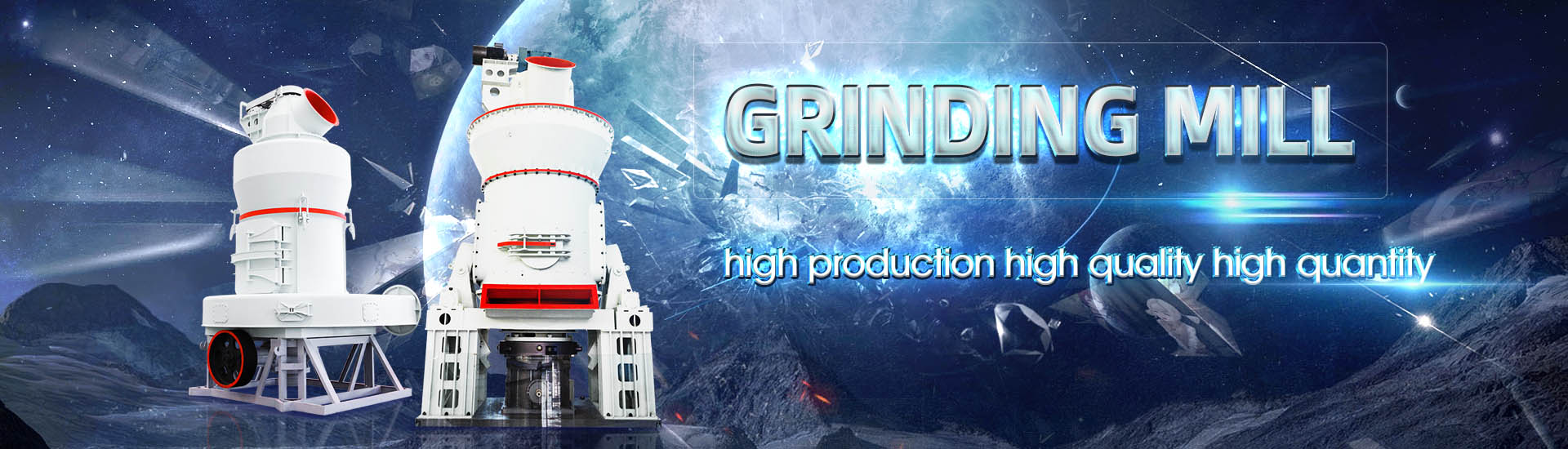
Technical parameters of highefficiency ore grinding mill
.jpg)
Effect of different parameters on grinding efficiency
2016年11月22日 The commonly used AE feature parameters for grinding AE are statistic parameters such as number of AE pulses, probability density of 2017年4月1日 Pilot plant test results with various ores showed that low energy consumption feature of vertical roller mills is applicable to the ore industry Grinding test results for zinc ore Operational parameters affecting the vertical roller mill HPGRs (high pressure grinding rolls) have been developed within the last decades for energy efficient processing of a wide variety of ores Special interest has been raised by projects Quantification of HPGR energy efficiency effects on downstream In general, BWI is only high (21 to 22 kWh/t) in the southern zone while the central and north zones range from 17 to 19 kWh/t The range and average values of different comminution Achievement of High Energy Efficiency in Grinding Mills at Santa Rita
.jpg)
Highefficiency and energyconservation grinding technology
2022年1月1日 Based on the specific productivity and grinding efficiency, the appropriate grinding parameters were ascertained as follows: material ball ratio of 07, ceramic ball medium size 2023年7月20日 Grinding operation quality indices mainly include four aspects (1) Grinding fineness, which is the percentage of the ore particles less than pecified size after being Ore Grinding SpringerLink2022年8月31日 The results show that grinding time is a significant factor affecting the particle size composition The suitable grinding concentration of Tongkeng ore and Gaofeng ore is 70% and 75%, respectively The effect of Grinding Modeling and Energy Efficiency in Ore/Raw Outotec HIGmills™ being based on existing, well proven stirred milling technology provide modern, sophisticated, flexible and energy efficient grinding solution for fine and ultra fine Outotec HIGmills; A Fine Grinding Technology
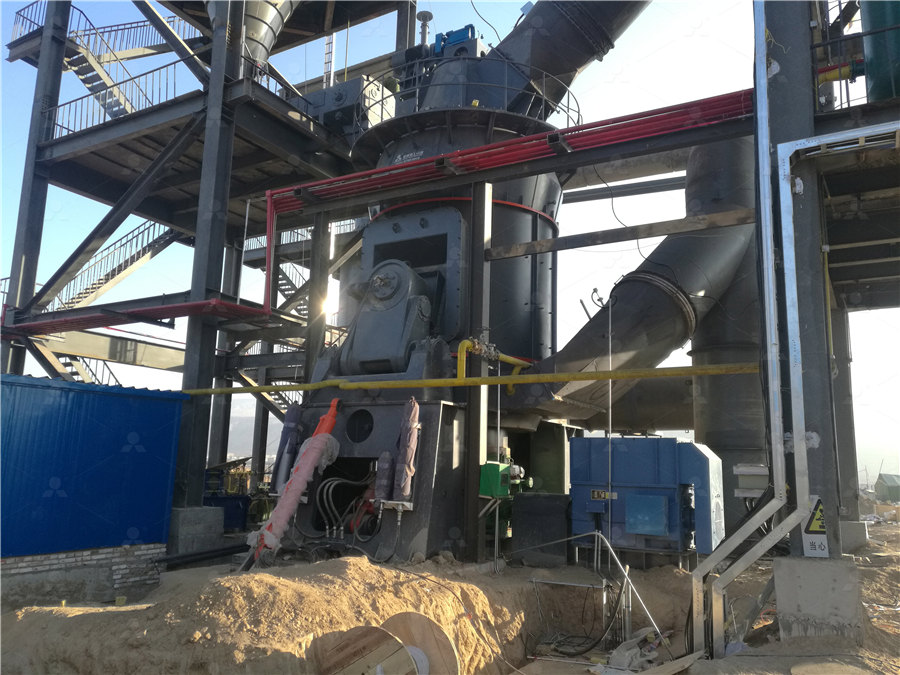
Optimization of some parameters of stirred mill for ultrafine
2011年3月10日 In this study, optimization of some parameters of stirred mill on ultrafine grinding of refractory Au/Ag ores was performed A threelevel Box–Behnken design 2021年2月26日 Milling is among the most energyconsuming technological stages of copper ore processing It is performed in mills, which are machines of high rotational masses The start of a mill filled to capacity requires Energy Efficiency Analysis of Copper Ore Ball Mill 2021年6月17日 Abstract The authors analyze the influence of the semiautogenous (SAG) mill parameters on the mill grinding efficiency, energy consumption and the tangential cumulative contact energy This paper provides a new liner parameter design and optimization method, which offers theoretical guidance for the optimization design of liner parametersPARAMETER OPTIMIZATION OF LARGE SAG MILL LINER BASED 2003年11月12日 This section highlights the applications in ore grinding mills, where near 60% of the electrical energy consumed in mining plants is employed by grinding mill drives in concentrator facilitiesTechnical Evaluation and Practical Experience of High Power Grinding
.jpg)
Rethinking Grinding Efficiency in Ball Mills
Drivers of grinding energy transfer to ore in ball mills • Charge density –charge shape and liner design • Charge surface area • Pulp density rheology • Media mass • Classifier efficiency How can we increase the grinding surface area? 1 Increase the grinding surface • Smaller ball media, or • Different media shape 22012年6月1日 As the cylinder starts to rotate, the grinding balls inside the cylinder crush and grind the feed material, generating mechanical energy that aids in breaking bonds, activating the catalyst, and Grinding in Ball Mills: Modeling and Process Control45th ©Annual Canadian Mineral Processors Operators Conference , Ottawa, Ontario, January 22 24, 2013 101 Grinding Circuit Flowsheet The milling circuit flowsheet of SantaRita operation is shown in Figure The SAG mill accepts 3 the primary crushed feed ore and operates in closed circuit with pebble crusherAchievement of High Energy Efficiency in Grinding Mills at High Grinding Efficiency: The grinding mechanism of ball mills ensures effective comminution, resulting in high grinding efficiency and reduced processing time Easy Maintenance: Ball mills are relatively simple machines with fewer moving parts, making maintenance and Ball Mill Grinding Machines: Working Principle, Types, Parts
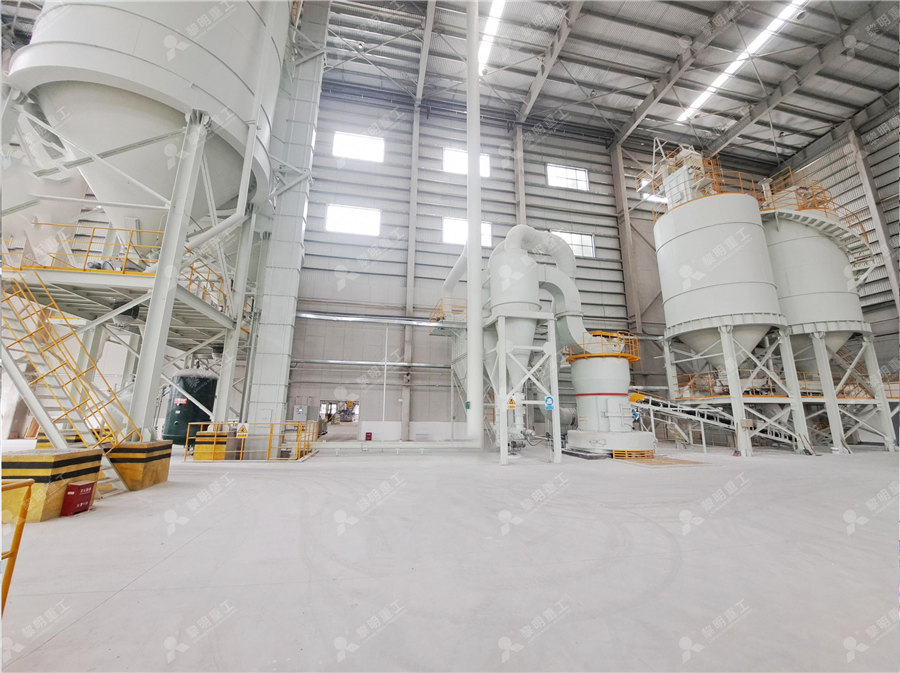
The Influence of the Grinding Media Diameter on Grinding Efficiency
2024年6月14日 The grinding process plays a crucial role in industry, allowing for the reduction of particle sizes of raw materials and substances to the required fineness—either as a finished product or for further technological processes The high demand for micro and nanopowders or suspensions is associated with the high energy consumption of the milling process Therefore, Speed also plays a role in ore grinding; too high of a speed can cause damage to the mill gears and other components, while too low of a speed can cause excessive wear on these same components It is important to find a balance between these two variables in order to achieve optimal grinding performanceFactors affecting ores grinding performance in ball mills2020年7月23日 The depletion of highgrade ores has forced the utilization of lowgrade ores The small liberation sizes in the lowgrade ores require fine grinding which is an energy intensive operationOptimization of stirred mill parameters for fine grinding of PGE Technical exploitation parameters of grinding rolls work in flour mill Res Agr Eng, 60 (Special Issue): S92–S97 The proposed research paper analyses power consumption in grinding rolls of a flour mill The observed mill has 15 grind ing passages The hourly efficiency of grinding roll on the first passage is 3,00672 kg/h The specific Technical exploitation parameters of grinding rolls work in flour mill
.jpg)
Technical Evaluation and Practical Experience of
2005年6月1日 Technical Evaluation and Practical Experience of HighPower Grinding Mill Drives in Mining Applications June 2005 IEEE Transactions on Industry Applications 41(3):866 874Combining impact and shearing actions enhances mill efficiency Proper selection of media milling equipment is vital for success in all three areas There are many different types of grinding mills (Table 1) Some devices, such as ball mills, Solids Choose the Right Grinding Mill Chemical For Gaofeng ore, the optimized grinding conditions are grinding time 38 min, grinding concentration 73% and filling ratio 34% Keywords: ores; beneficiation; grinding; optimizationOptimization of Polymetallic Complex Ores ResearchGate866 IEEE TRANSACTIONS ON INDUSTRY APPLICATIONS, VOL 41, NO 3, MAY/JUNE 2005 Technical Evaluation and Practical Experience of HighPower Grinding Mill Drives in Mining Applications José R Rodríguez, Senior Member, IEEE, Jorge Pontt, Senior Member, IEEE, Patricio Newman, Rodrigo Musalem, Hernán Miranda, Luis Moran, Fellow, IEEE, and Gerardo Technical evaluation and practical experience of highpower grinding
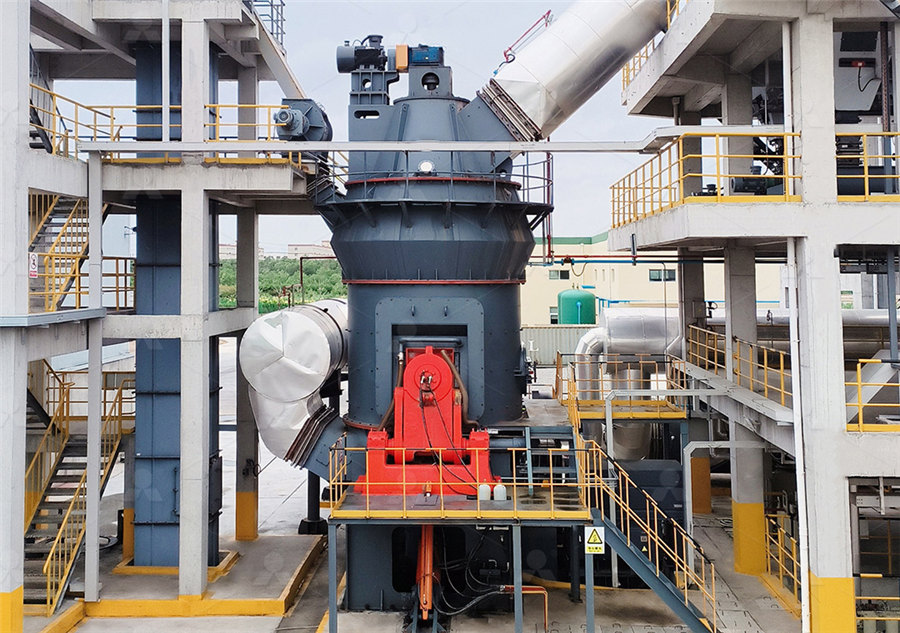
(PDF) Effects of High Pressure ORE Grinding on the Efficiency of
2014年1月20日 High pressure grinding rolls in AG/SAG mill circuits the next step in the evolution of grinding plants for the new millennium SAG 2001, Conference, Vancouver, BC 2001 Volball mill employs steel balls to generate a grinding action, ie ore particle comminution via impact and abrasion with steel balls, and is a key component of beneficiation plant production Even though it has massive benefits, such as a high reduction ratio, effective breakage impact, and a wide application (Fuerstenau andEffect of grinding media on the milling efficiency of a ball mill2013年4月16日 ABSTRACT In this study, ultrafine grinding of a refractory silver ore tailings was studied A laboratory scale pintype vertical stirred mill and ceramic beads were employed for the grinding testsInvestigation of some parameters affecting the Ultrafine grinding 2022年1月1日 A pilotscale grinding technology of ceramic medium stirred mill was proposed in this study Based on the specific productivity and grinding efficiency, the appropriate grinding parameters were ascertained as follows: material ball ratio of 07, ceramic ball medium size ratio (10 mm: 15 mm: 20 mm = 3:2:5), stirring speed of 110 rpm, grinding concentration of 50%, Highefficiency and energyconservation grinding technology using
.jpg)
Effect of Grinding Conditions on Clinker Grinding Efficiency: Ball
2024年7月31日 The production of cement, an essential material in civil engineering, requires a substantial energy input, with a significant portion of this energy consumed during the grinding stage This study addresses the gap in the literature concerning the collective impact of key parameters, including ball size, feed rate, and mill speed, on grinding efficiency Nine spherical Powder Technology 208 (2011) 121–127 Contents lists available at ScienceDirect Powder Technology j o u r n a l h o m e p a g e : w w w e l s ev i e r c o m / l o c a t e / p ow t e c Optimization of some parameters of stirred mill for ultrafine Optimization of some parameters of stirred mill for The comminution process of High Pressure Grinding Rolls (HPGR) was discovered in the 1980s by the research work of the German Professor Schönert Its main advantage is the high energy efficiency in comparison to ball mill grinding which has been the benchmark process in the cement industry by then (Schönert, 1988)Quantification of HPGR energy efficiency effects on downstream grinding CLUM series of ultrafine gypsum powder vertical grinding mills are a new type of ultrafine industrial ore grinding equipment that integrates grinding, grading, It has high grinding efficiency, low energy consumption, uniform particle shape, CLUM Ultrafine Vertical Grinding Mill
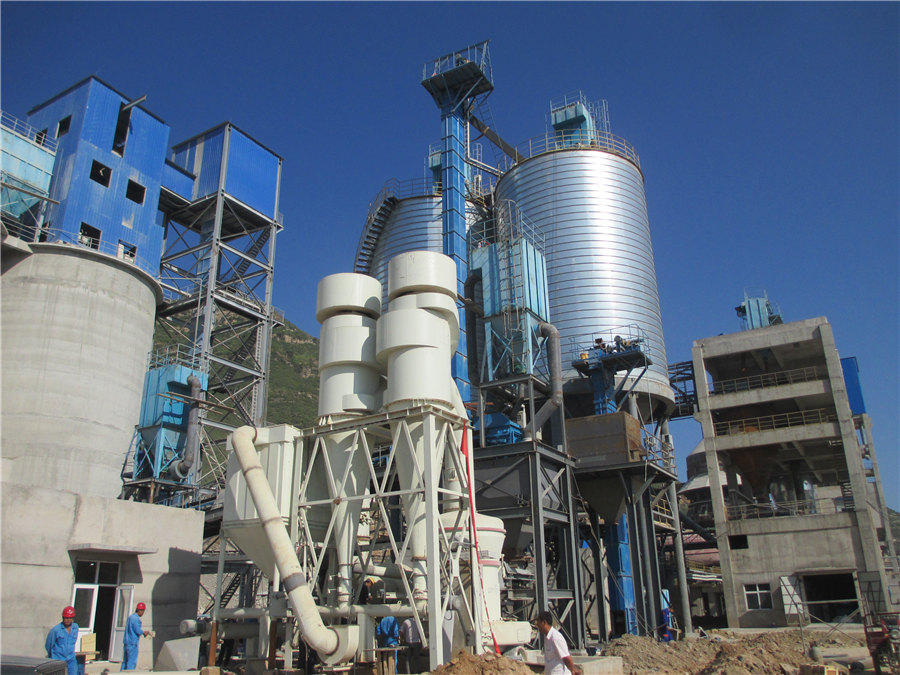
Effect of grinding media on the milling efficiency of a ball mill
ball mill employs steel balls to generate a grinding action, ie ore particle comminution via impact and abrasion with steel balls, and is a key component of beneficiation plant production Even though it has massive benefits, such as a high reduction ratio, effective breakage impact, and a wide application (Fuerstenau and2018年1月1日 The key influence factors on grinding energy efficiency and productivity It enables a combination of high speed grinding and creepfeed grinding, typically referred to and during dressing (right) Table 1 Process parameters for grinding tests workpiece material abrasive ð ‘£ð ‘£ð ‘ ð Energy efficiency of stateoftheart grinding processes2014年3月1日 The object of the study reported here is the grinding process in a tumbling mill where the mechanism of destruction by crushing is implemented, which is caused by the mechanism of compression loading(PDF) Analysis of ball mill grinding operation using mill power Optimization of stirred mill parameters for fine grinding of PGE bearing chromite ore, Particulate Science and Technology, DOI: 101080/2020 To link to this article: https://doi Optimization of stirred mill parameters for fine grinding of PGE
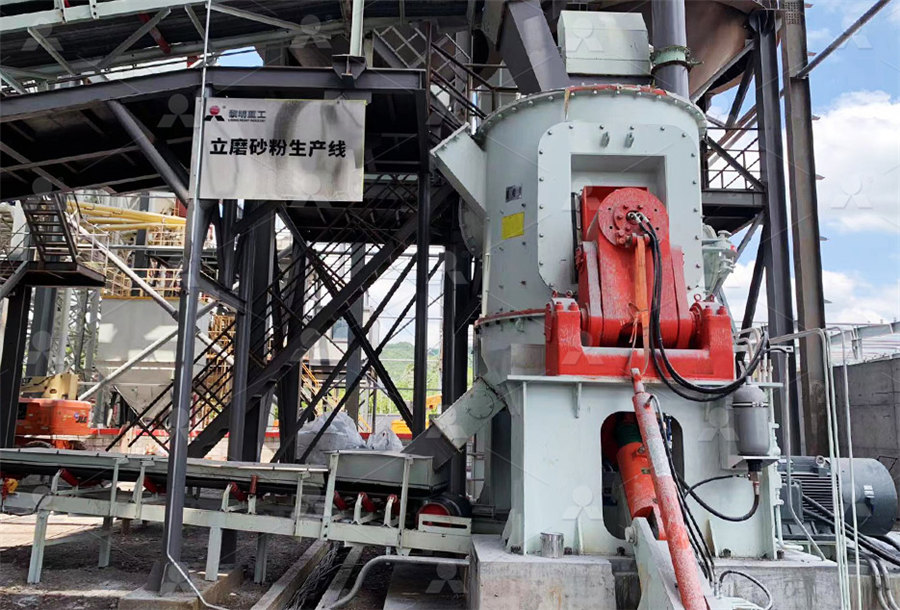
Studying the effect of different operation parameters on the grinding
The chosen parameters J L*D Db f U n t Dmax Fractional ball filling (%) Mill sizes (height*diameter) Bead sizes (mm) The formal bed porosity of beads (%) The Particlebead ratio Stirrer speeds (rpm) Grinding periods (s) Maximum particle size of feed (Starting sample) Real density of bead (gr/cm3) dgm The calculated parameters Vd Effective mill volume (cm3) Vbb ball mill grinding efficiency, media shape, liner design, mill speed, optimisation Authors Dr Rajiv Chandramohan 1, Dr Petar Bodurov 2, Nikolay Kolev 3, Dr Nirmal Weerasekera 4, Greg Lane 5 Global Technical Director of Operations, Ausenco, Vancouver (Canada) This address is being protected fromRethinking Grinding Efficiency in Ball Mills2022年1月23日 This work concentrates on the energy consumption and grinding energy efficiency of a laboratory vertical roller mill (VRM) under various operating parameters For design of experiments (DOE), the response surface method (RSM) was employed with the VRM experiments to systematically investigate the influence of operating parameters on the energy Analysis and Optimization of Grinding Performance of Vertical 2021年2月26日 Milling is among the most energyconsuming technological stages of copper ore processing It is performed in mills, which are machines of high rotational masses The start of a mill filled to capacity requires Energy Efficiency Analysis of Copper Ore Ball Mill
.jpg)
PARAMETER OPTIMIZATION OF LARGE SAG MILL LINER BASED
2021年6月17日 Abstract The authors analyze the influence of the semiautogenous (SAG) mill parameters on the mill grinding efficiency, energy consumption and the tangential cumulative contact energy This paper provides a new liner parameter design and optimization method, which offers theoretical guidance for the optimization design of liner parameters2003年11月12日 This section highlights the applications in ore grinding mills, where near 60% of the electrical energy consumed in mining plants is employed by grinding mill drives in concentrator facilitiesTechnical Evaluation and Practical Experience of High Power Grinding Drivers of grinding energy transfer to ore in ball mills • Charge density –charge shape and liner design • Charge surface area • Pulp density rheology • Media mass • Classifier efficiency How can we increase the grinding surface area? 1 Increase the grinding surface • Smaller ball media, or • Different media shape 2Rethinking Grinding Efficiency in Ball Mills2012年6月1日 As the cylinder starts to rotate, the grinding balls inside the cylinder crush and grind the feed material, generating mechanical energy that aids in breaking bonds, activating the catalyst, and Grinding in Ball Mills: Modeling and Process Control

Achievement of High Energy Efficiency in Grinding Mills at
45th ©Annual Canadian Mineral Processors Operators Conference , Ottawa, Ontario, January 22 24, 2013 101 Grinding Circuit Flowsheet The milling circuit flowsheet of SantaRita operation is shown in Figure The SAG mill accepts 3 the primary crushed feed ore and operates in closed circuit with pebble crusherHigh Grinding Efficiency: The grinding mechanism of ball mills ensures effective comminution, resulting in high grinding efficiency and reduced processing time Easy Maintenance: Ball mills are relatively simple machines with fewer moving parts, making maintenance and Ball Mill Grinding Machines: Working Principle, Types, Parts 2024年6月14日 The grinding process plays a crucial role in industry, allowing for the reduction of particle sizes of raw materials and substances to the required fineness—either as a finished product or for further technological processes The high demand for micro and nanopowders or suspensions is associated with the high energy consumption of the milling process Therefore, The Influence of the Grinding Media Diameter on Grinding Efficiency Speed also plays a role in ore grinding; too high of a speed can cause damage to the mill gears and other components, while too low of a speed can cause excessive wear on these same components It is important to find a balance between these two variables in order to achieve optimal grinding performanceFactors affecting ores grinding performance in ball mills
.jpg)
Optimization of stirred mill parameters for fine grinding of PGE
2020年7月23日 The depletion of highgrade ores has forced the utilization of lowgrade ores The small liberation sizes in the lowgrade ores require fine grinding which is an energy intensive operation