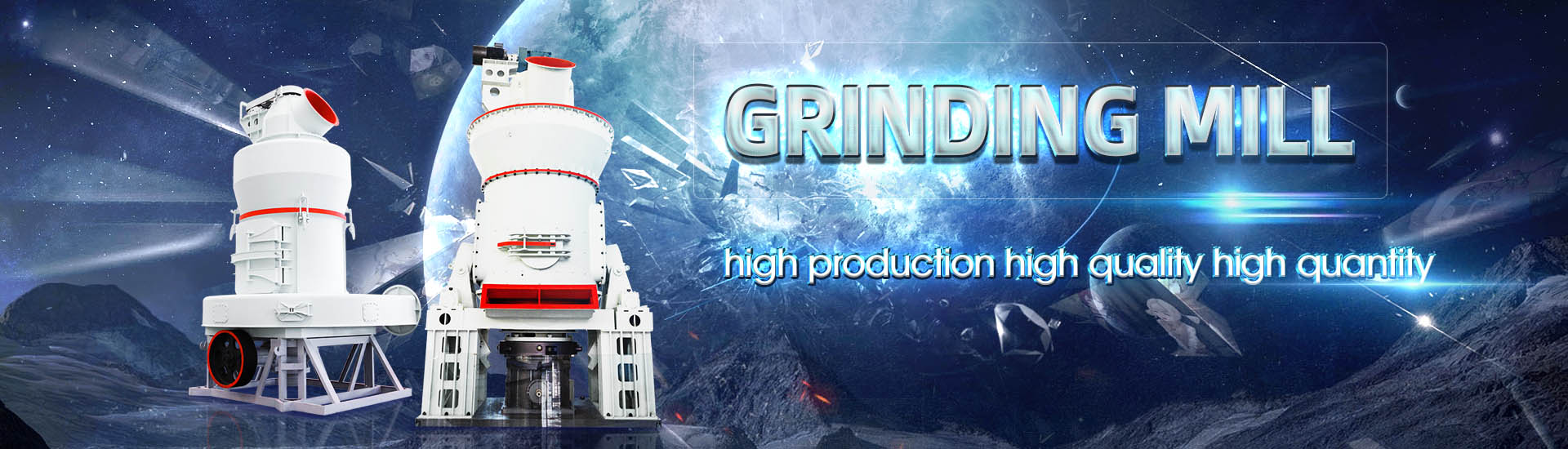
Imported highefficiency and energysaving European version grinding mill

Breaking down energy consumption in industrial
2017年1月17日 This paper reports the results of an investigation targeting two objectives: (1) characterising energy outputs in industrial grinding mill circuits, and (2) identifying the potential for2018年1月1日 Specific energy consumption was determined as a function of material removal rate and compared to results of milling and turning processes The key influence factors on Energy efficiency of stateoftheart grinding processescommon solution to grind raw materials and cement Roller presses are used mainly in combination with a ball mill for cement grinding applications and as finished product grinding BALL MILLS Ball mill optimisation Holzinger Consulting2023年7月10日 The present literature review explores the energyefficient ultrafine grinding of particles using stirred mills The review provides an overview of the different techniques for size reduction and the impact of energy EnergyEfficient Advanced Ultrafine Grinding of
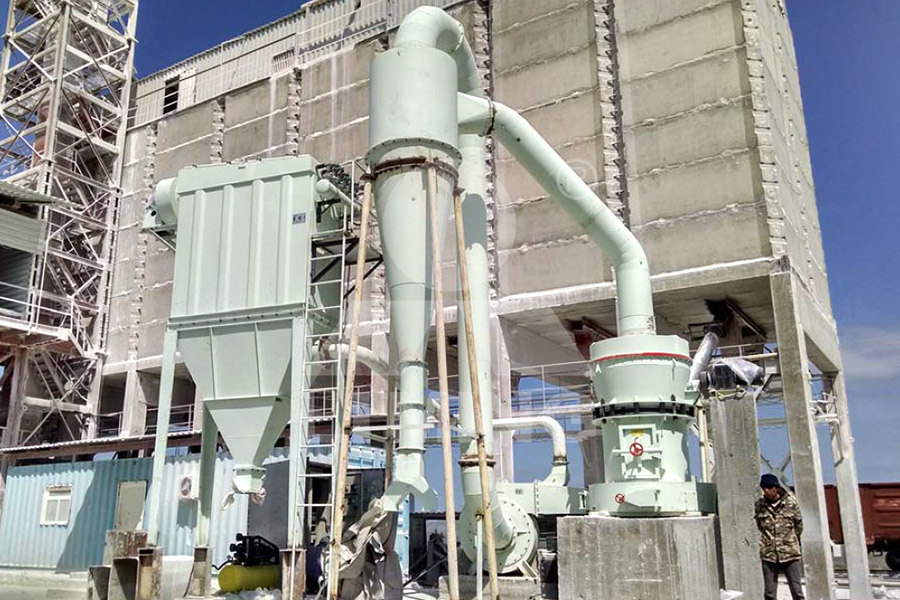
(PDF) Performance Comparison of the Vertical and
2023年2月23日 The results showed that HIGMill and IsaMill technologies behaved in a different manner for coarse and fine tail of comminution IsaMill with horizontal orientation was found to be more2013年12月18日 In a laboratory study by Nesset et al, a GIS mill charged with 5mm steel shot, and with other operating conditions similarly optimized, achieved high energy efficiencies when grinding to less than 20 μm This appears to Energy Use of Fine Grinding in Mineral Processing2009年6月1日 The work using a vertical shaft stirred mill compared with Bond ball mill, both operated in closed circuit with a classifier, demonstrated a clear trend that on average 30% Comparison of energy efficiency between ball mills and stirred 2013年7月15日 The ball mill in closed circuit with hydrocyclones is an industry standard, and well known methodologies exist for equipment sizing, selection and design(PDF) Energy Efficient Ball Mill Circuit – Equipment
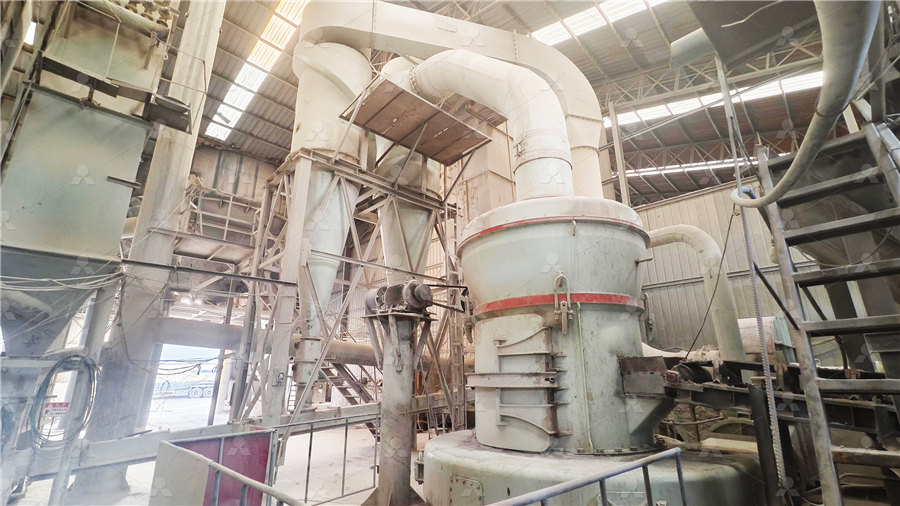
Environmental friendly energysaving MTW europeantype grinding mill
The optimized design of the grinding chamber and the use of highquality wearresistant materials further enhance the mill's energy efficiency, reducing energy consumption by up to 30% compared to traditional grinding mills 3 High Grinding Efficiency The MTW EuropeanType Grinding Mill boasts high grinding efficiency, thanks to its unique 2019年3月8日 IMPROVING THERMAL AND ELECTRIC ENERGY EFFICIENCY AT CEMENT 252 Replacing a Ball Mill with a Vertical Roller Mill, HighPressure Grinding Rolls, fuel energy saving of 50 to 80 MJ per ton IMPROVING THERMAL AND ELECTRIC ENERGY A regrind ball mill with a mix of small grinding media can be as energy effi cient as an Isa Mill charged with 25 and 35 mm beads In vertical stirred mills, energy savings vary from 30 per cent to 60 per cent To carry out the same fi nal grind, a vertical stirred mill with Millpebs will consume at least 60 per cent less energy than a ball ENERGY SAVINGS AND TECHNOLOGY COMPARISON USING SMALL GRINDING 2020年12月21日 Energy saving potential for various energyintensive processes in mining [3] 1 Btu (British thermal unit) ≈ 1055 Joule Increasing Energy Efficiency and Productivity of the
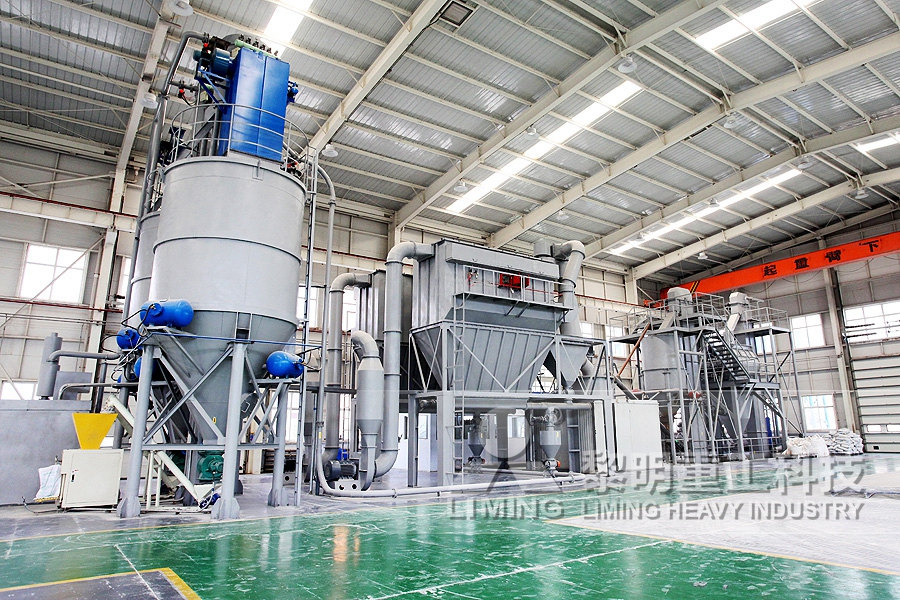
Enhancing the Grinding Efficiency of a Magnetite SecondStage Mill
2024年1月31日 Ceramic ball milling has demonstrated remarkable energysaving efficiency in industrial applications However, there is a pressing need to enhance the grinding efficiency for coarse particles This paper introduces a novel method of combining media primarily using ceramic balls supplemented with an appropriate proportion of steel balls Three grinding media The European Version Grinding Mill has emerged as a powerful force The mill's technological innovations also extend to its energy efficiency It incorporates energysaving technologies and intelligent that embrace this technology are better positioned to meet the increasingly demanding requirements of the market for highquality Indepth understanding of the european version grinding mill: 2009年1月1日 PDF Energy is an important cost factor in the US iron and steel industry Energy efficiency improvement is an important way to reduce these costs and Find, read and cite all the research (PDF) Energy Efficiency Improvement and Cost Saving Opportunities 2019年11月11日 14 November 2024 2 min reading CESCO validates highperformance bagging system for UFC's grain facility in Saudi Arabia CESCO, a global leader in grain handling, storage, and processing solutions, has announced the successful completion of the Factory Acceptance Test (FAT) for a highcapacity bagging line system as part of its extensive project with United EFFICIENCY IN GRINDING AND ENERGY MANAGEMENT IN
.jpg)
(PDF) Grinding Media in Ball MillsA Review ResearchGate
2023年4月23日 high speeds of about 90%, causing breakage o f large ore particles wh ilst reducing the mill’s energy efficiency The num ber of cataracting media increases as mill speed increases [ 62 ] 2022年1月23日 This work concentrates on the energy consumption and grinding energy efficiency of a laboratory vertical roller mill (VRM) under various operating parameters For design of experiments (DOE), the response surface method Analysis and Optimization of Grinding Performance of YGMQ4 European version of the powerful mill adopts heavyduty grinding structure, high efficiency, more wearresistant, high classification accuracy, high powder selection efficiency, environmental protection and energy saving, creating a clean production spaceYGMQ4 European version of the powerful mill adopts heavyduty grinding 即时翻译文本完整的文档文件。为个人和团队提供准确的翻译。每天有数百万人使用DeepL进行翻译。DeepL翻译:全世界最准确的翻译 DeepL Translate
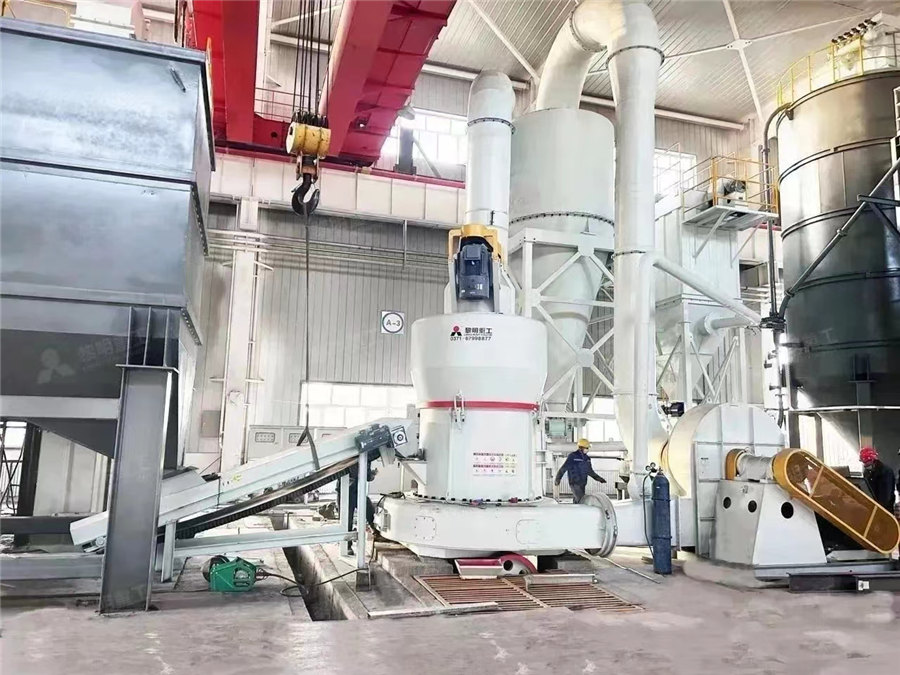
The Effects of Blasting on Crushing and Grinding Efficiency and Energy
2003年1月1日 Mining is typically conducted through a set of interdependent unitoperations, which commonly include drilling, blasting, digging and hauling, in order to deliver the required ore material into Grinding efficiency is the unit energy consumption rate of the mill, which represents the amount of material with a particle size of 0043 mm newly generated for every 1 kW•h of energy consumed Energy conservation and consumption reduction in grinding 2021年3月23日 New ball mill drive system with the prototype energysaving SMH motor [37] Startup of the LSPMSM SMH1732T motor with a filled ball mill after two hours of downtime: (a) active power, (b Energy Efficiency Analysis of Copper Ore Ball Mill Drive Systems2022年3月1日 Helping to reduce mining industry carbon emissions: A stepbystep guide to sizing and selection of energy efficient high pressure grinding rolls circuits March 2022 Minerals Engineering 179(2):Helping to reduce mining industry carbon emissions: A stepby

THE BENEFITS OF HIGH CLASSIFICATION EFFICIENCY IN CLOSED BALL MILL
2013年1月1日 The specific energy consumptions of the grinding equipment and the standard bond work indexes, used 100μm screen, of raw materials are given belowCircuitBond work index (kWh/t)Specific energy 2013年12月18日 Fine grinding, to P80 sizes as low as 7 μm, is becoming increasingly important as mines treat ores with smaller liberation sizes This grinding is typically done using stirred mills such as the Isamill or Stirred Media Detritor While fine grinding consumes less energy than primary grinding, it can still account for a substantial part of a mill’s energy budget Overall Energy Use of Fine Grinding in Mineral Processing2013年2月26日 The industry has failed to fully adapt to this technological development, which offers significant energy savings, as it did with other technical developments such as the precalciner kiln or high efficiency coolers Mill operation and maintenance Operation of a ball mill is relatively simple, with no moving mechanical parts within the mill paring ball mills and VRMS for cement grinding2009年6月1日 At product sizes finer than 80% passing 75 μm, the efficiency of ball mill grinding rapidly decreasesThe practical limit to ball mill product fineness is considered to be 40–45 μm (Gao and Weller, 1994)Although ball mills can still be found in the regrind circuits in a number of mineral processing plants, their energy consumption is high, and size reduction efficiency is parison of energy efficiency between ball mills and stirred
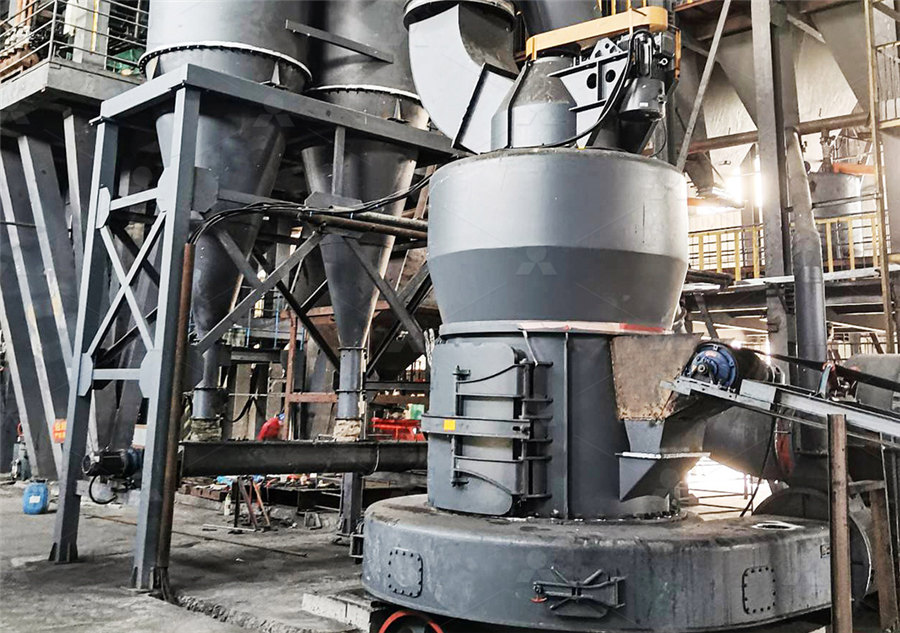
Energy and cement quality optimization of a cement grinding circuit
2018年7月1日 Among the industries, the nonmetallic industry was reported as the third largest energy user and accounted for about 12% of the global energy use [1]Within this portion, cement industry had the majority of the utilization with 85–12% [1], [2]US Energy Information Administration (EIA) [7] named cement industry as the most energy intensive among the 2017年9月11日 Grinding and separation efficiency of vertical roller mill were evaluated In addition to these, performance figures of vertical roller mill and conventional closed ball mill circuit were compared(PDF) Performance Evaluation of Vertical Roller Mill 2020年5月1日 Cement industry consumes a huge amount of electrical energy that is about 100 kWh/t (kWh per ton (10 3 kg) of cement) [16]In a cement plant, about twothirds of the total electrical energy is used for particle size reduction of raw materials and clinker [17]There is a diverse range of options to decrease the production expenses as well as CO 2 emissions that Energy and exergy analyses for a cement ball mill of a new 2023年11月1日 The ball mill on site, has problems such as uneven product particle size, low grinding efficiency, insufficient dissociation degree of useful mineral monomers, and high grinding energy consumption[[20], [21], [22], [33], [34]]The existing technological process of the first beneficiation workshop of Gongchangling Concentrator is as follows: twostage crushing, Energy conservation and consumption reduction in grinding
.jpg)
Helping to reduce mining industry carbon emissions: A stepby
2022年3月30日 All industries are facing increasing pressure to ensure that carbon emissions are reduced to help achieve the socalled 15 °C future This has led to most of the major mining companies committing to significant reductions in their operational carbon footprint – in many cases by up to 30–40% in the next 10–15 years and to place themselves in a netzero scope 2023年9月28日 Using highefficiency motors, variable speed drives, installation of soft starters and single motor in double deck roller mill can result in energy savings in the grinding process There have been many innovations in the roller mill machine, some of which have directly or indirectly led to reducing energy consumptionTips in energy saving for flour millers Miller Magazine2001年8月1日 PDF Especially after the energy crisis of 1980s, plenty of energy efficient technologies were introduced in the European ceramic industry sector, Find, read and cite all the research you (PDF) Energy saving technologies in the European ceramic 2023年1月1日 Download Citation Ball mill energy efficiency optimization techniques: A review Ball mills are essential machinery in the mining industry, thermal powerproducing companies, and cement Ball mill energy efficiency optimization techniques: A review
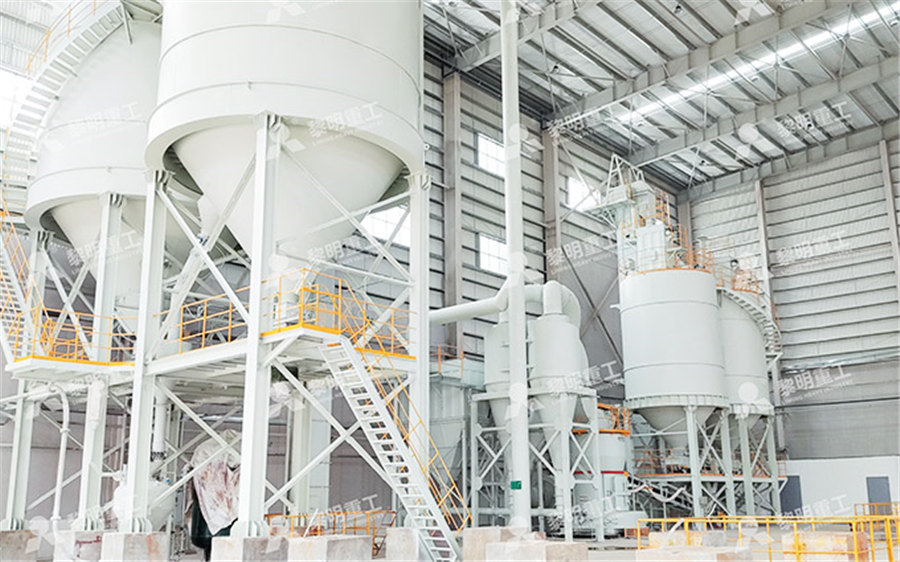
EnergyModel and Life CycleModel for Grinding Processes of
2022年5月22日 Fine and ultrafine grinding of limestone are frequently used in the pharmaceutical, chemical, construction, food, and cosmetic industries, however, research investigations have not yet been published on the combination of energy and life cycle modeling Therefore, the first aim of this research work was the examination of main grinding parameters 2013年7月15日 The ball mill in closed circuit with hydrocyclones is an industry standard, and well known methodologies exist for equipment sizing, selection and design(PDF) Energy Efficient Ball Mill Circuit – Equipment The optimized design of the grinding chamber and the use of highquality wearresistant materials further enhance the mill's energy efficiency, reducing energy consumption by up to 30% compared to traditional grinding mills 3 High Grinding Efficiency The MTW EuropeanType Grinding Mill boasts high grinding efficiency, thanks to its unique Environmental friendly energysaving MTW europeantype grinding mill2019年3月8日 IMPROVING THERMAL AND ELECTRIC ENERGY EFFICIENCY AT CEMENT 252 Replacing a Ball Mill with a Vertical Roller Mill, HighPressure Grinding Rolls, fuel energy saving of 50 to 80 MJ per ton IMPROVING THERMAL AND ELECTRIC ENERGY
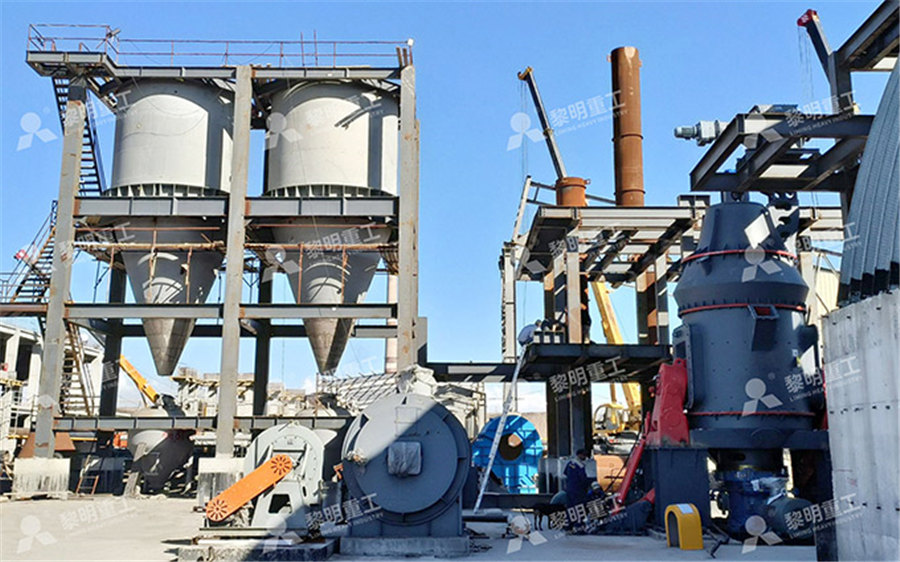
ENERGY SAVINGS AND TECHNOLOGY COMPARISON USING SMALL GRINDING
A regrind ball mill with a mix of small grinding media can be as energy effi cient as an Isa Mill charged with 25 and 35 mm beads In vertical stirred mills, energy savings vary from 30 per cent to 60 per cent To carry out the same fi nal grind, a vertical stirred mill with Millpebs will consume at least 60 per cent less energy than a ball 2020年12月21日 Energy saving potential for various energyintensive processes in mining [3] 1 Btu (British thermal unit) ≈ 1055 Joule Increasing Energy Efficiency and Productivity of the 2024年1月31日 Ceramic ball milling has demonstrated remarkable energysaving efficiency in industrial applications However, there is a pressing need to enhance the grinding efficiency for coarse particles This paper introduces a novel method of combining media primarily using ceramic balls supplemented with an appropriate proportion of steel balls Three grinding media Enhancing the Grinding Efficiency of a Magnetite SecondStage Mill The European Version Grinding Mill has emerged as a powerful force The mill's technological innovations also extend to its energy efficiency It incorporates energysaving technologies and intelligent that embrace this technology are better positioned to meet the increasingly demanding requirements of the market for highquality Indepth understanding of the european version grinding mill:
.jpg)
(PDF) Energy Efficiency Improvement and Cost Saving Opportunities
2009年1月1日 PDF Energy is an important cost factor in the US iron and steel industry Energy efficiency improvement is an important way to reduce these costs and Find, read and cite all the research 2019年11月11日 14 November 2024 2 min reading CESCO validates highperformance bagging system for UFC's grain facility in Saudi Arabia CESCO, a global leader in grain handling, storage, and processing solutions, has announced the successful completion of the Factory Acceptance Test (FAT) for a highcapacity bagging line system as part of its extensive project with United EFFICIENCY IN GRINDING AND ENERGY MANAGEMENT IN 2023年4月23日 high speeds of about 90%, causing breakage o f large ore particles wh ilst reducing the mill’s energy efficiency The num ber of cataracting media increases as mill speed increases [ 62 ] (PDF) Grinding Media in Ball MillsA Review ResearchGate