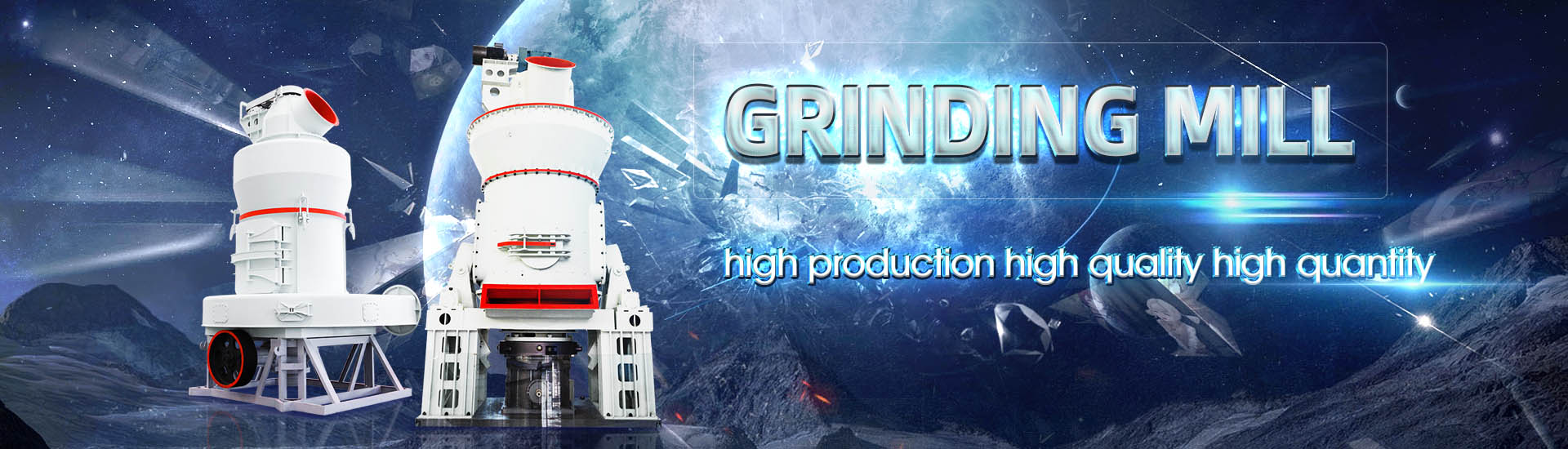
HOME→Lime workshop process production regulations, cement production dust prevention technical regulations
Lime workshop process production regulations, cement production dust prevention technical regulations
.jpg)
Technical Support Document for the Lime Manufacturing Sector
Lime production involves three main processes: stone preparation, calcination, and hydration During the calcination process, lime is sufficiently heated to generate processrelated CO2 as Air emissions in cement and lime manufacturing are generated by the handling and storage of intermediate and final materials, and by the operation of kiln systems, clinker coolers, and millsWorld Bank DocumentThe Environmental, Health, and Safety (EHS) Guidelines are technical reference documents with general and industry specific examples of Good International Industry Environmental, health, and safety guidelines for cement and lime This UK Guidance for delivering the PPC (IPPC) Regulations in the Cement and Lime sector is based on the BAT Reference document BREF (see Ref 1) produced by the European IPPC S301 Guidance for the Cement and Lime Sector Working
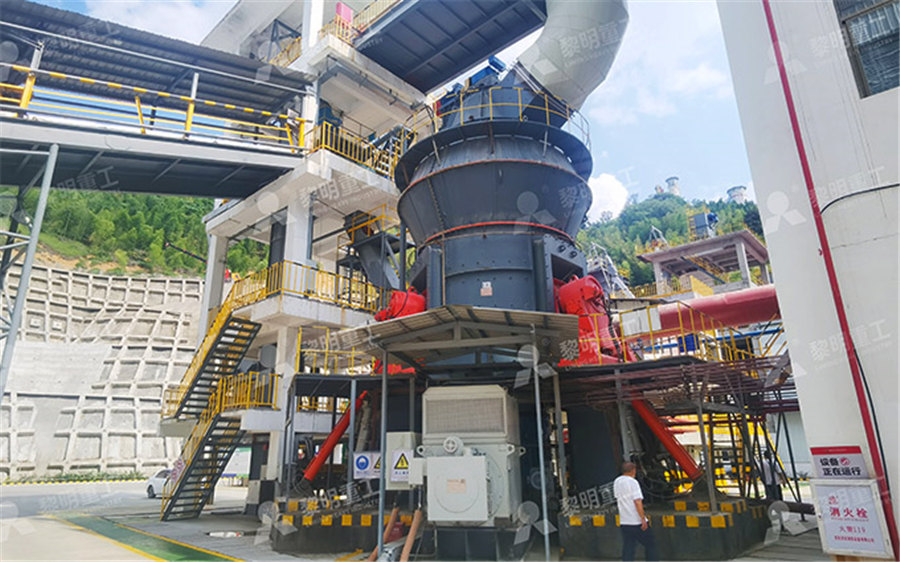
Documents Reports All Documents The World Bank
Slaked lime can have two forms: dry (powder) or milk of lime (liquid) The slaked lime production process consists of size separation, hydrating, and storage in silos (dry) for sale in bulk or 2013年11月6日 Important issues for the implementation of Directive 2010/75/EU in the production of cement, lime and magnesium oxide are the reduction of emissions to air; Best available techniques (BAT) reference document for the This BREF includes processes involved in the production of cement and lime The main operations covered are: • raw materials storage and preparation • fuels storage and Production of Cement, Lime and Magnesium Oxide EUBRITE• The Semidry Scrubber Technology is less expensive than the Wet but it is necessary to use more expensive sorbents like hydrated lime and the conversion to gypsum is limited to 20 BAT in the cement industry, including cost/benefit effects
-2.jpg)
Implementing decision 2013/163 EN EURLex
2013/163/EU: Commission Implementing Decision of 26 March 2013 establishing the best available techniques (BAT) conclusions under Directive 2010/75/EU of the European Hydrated lime is created when quicklime chemically reacts with water It is hydrated lime that reacts with clay particles and permanently transforms them into a strong cementitious matrix LIMETREATED SOIL CONSTRUCTION MANUAL2022年6月8日 Despite the tremendous industrial and technical progress that the world is witnessing, The production of cement kiln dust is a CKD with high free lime was used in the treatment processCement Kiln Dust (CKD): Potential Beneficial 2019年1月1日 These IEC standards use the following IEC definition of combustible dust as “finely divided solid particles, 500 μm or less in nominal size, which may form explosive mixtures with air at standard atmospheric pressure and temperatures”Although this definition has no criteria for determining whether these solid particles can form explosive mixtures with air, Dust explosions: Regulations, standards, and guidelines
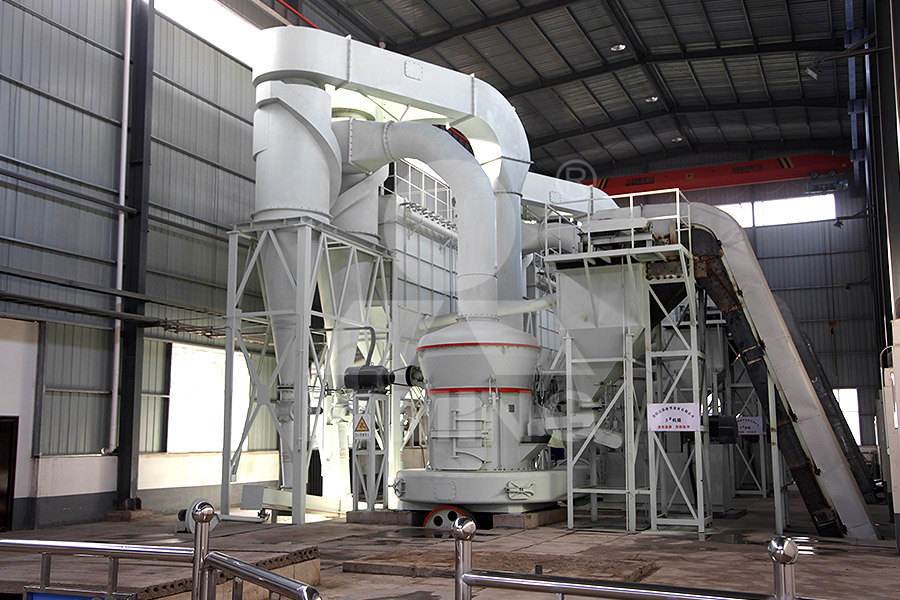
Distribution of heavy metals in Portland cement
2014年12月30日 In the process of production of cement clinker in FCL, metal elements are mostly entered by primary raw materials: limestone, marl lime, clay stone, sand; coal fly ash as secondary raw material 2023年4月12日 Cement plants generate dust during the production process, which can include raw material grinding, blending, preheating, kiln processes, clinker cooling and cement grinding Dust emitted from cement plants is a significant environmental and health concern in India, where the cement industry is a major contributor to air pollutionDust Control: Balancing Health and Sustainability Indian Cement Cement based products, like concrete or mortar, can cause serious skin problems such as dermatitis and burns This page tells you how to control these risks and why What you must do The Control of Substances Hazardous to Health (COSHH) Regulations says Construction hazardous substances: Cement HSEsharp decline in cement production over the last 15 years, from a peak of 262Mt in 2007 to 168Mt in 2017, equivalent to a reduction in cement per capita from 05 to 03 tonnes per person (3) The CO 2 intensity of cement production over that period has improved by about 7% (06t of CO 2 emitted per tonne of cement in 2017) (2)Deep decarbonisation of industry: The cement sector Europa
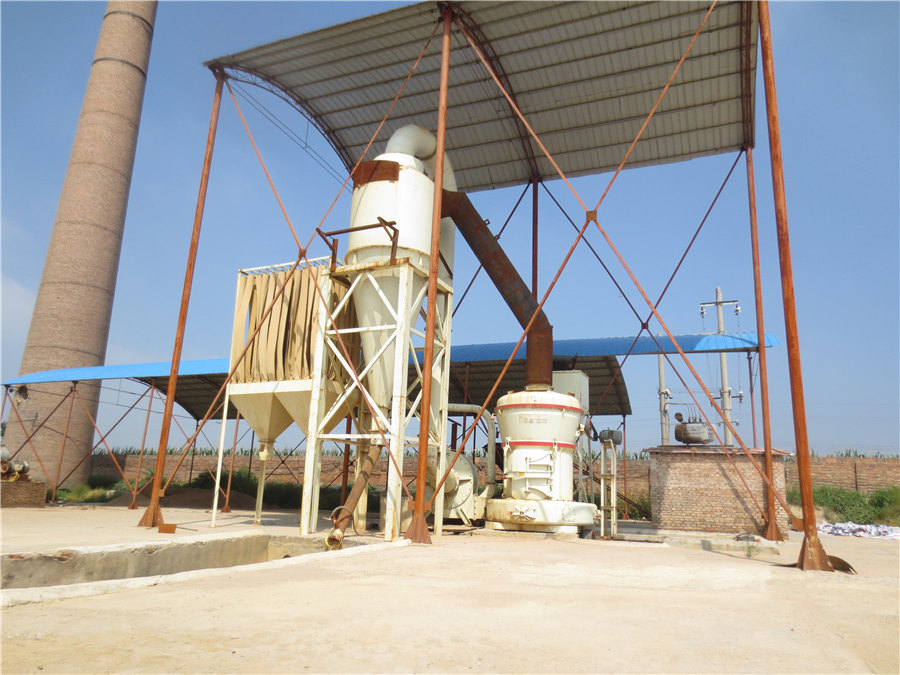
ab0cd Subsectoral Environmental and Social Guidelines: Cement Production
ab0cd Subsectoral Environmental and Social Guidelines: Cement Production Cement Production Subsectoral Environmental and Social Guidelines Page 1 2010 PROCESS DESCRIPTION Cement production facilities are often located in rural areas and close to quarries, where the raw materials required are present, for example, limestone and shaleRegarding point 31(c) above, these BAT conclusions only address the production of MgO using the dry process route based on mined natural magnesite (magnesium carbonate MgCO 3) In particular, concerning the abovementioned activities, these BAT conclusions cover the following: — production of cement, lime and magnesium oxide (dry process BAT conclusions Production of cement, lime and magnesium Mineralogy From the Müller (1977) study of nearly 100 European CKDs, it was found that the dusts are particulate mixtures of four major components: (1) unreacted raw feed, (2) partially calcined feed and clinker dust, (3) free lime, and (4) enriched salts of alkali sulfates, halides, and other volatile compoundsEverything you need to know about Cement Kiln Dust Generation 2020年3月23日 The addition ratio of lime and stacking time in the sludge limedrying process could greatly affect the carbon footprint of coprocessing limedried sludge in cement kilnFeasibility and Carbon Footprint Analysis of LimeDried Sludge
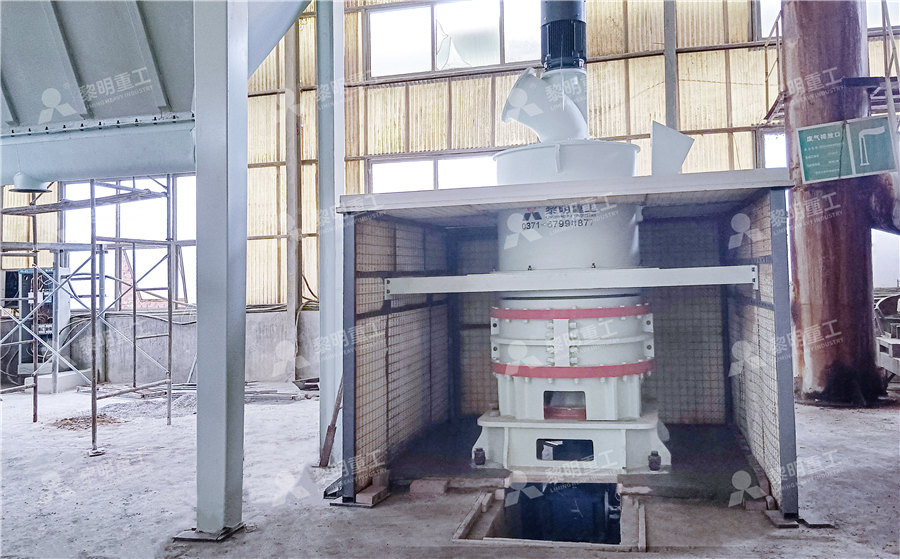
Lime Production an overview ScienceDirect Topics
42 Energy use and emissions The lime production process is energy intensive and results in CO 2 emissions from both mineralogical transformation process and energy used The production of one tonne of lime entails the emission of around 12 tonne of CO 2 (Ochoa George et al, 2010; Sagastume Gutiérrez et al, 2012)This makes lime one of the products with the highest CEMENT AND LIME MANUFACTURING APRIL 30, 2007 4 WORLD BANK GROUP • Developing a staged combustion process 6,as applicable in preheaterprecalciner (PHP) and preheater (PH) kilns ; • Lime manufacturing: Nitrogen oxide ( NO X) production is generally lower in lime manufacturing than in cement manufacturing Because limestone burning usual ly takesWorld Bank Documentthe technical areas (eg cement processes or lime processes) (Sections 23 24); • particular emissions (eg NOx or pesticides) (Section 3) Additionally, to assist Operators in making applications, separate, horizontal guidance is available on a range of topics such as waste minimisation, monitoring, calculating stack heights etcIPPC S301 Guidance for the Cement and Lime Sector Working 2022年4月12日 Carbon dioxide (CO2) emissions from China’s cement production process have increased rapidly in recent decades, comprising the secondlargest source of CO2 emissions in the country, next only to China’s provincial process CO2 emissions from cement production
.jpg)
How Cement is Made Cement Manufacturing Process
Stage of Cement Manufacture There are six main stages of the cement manufacturing process Stage 1: Raw Material Extraction/Quarry The raw cement ingredients needed for cement production are limestone (calcium), sand and clay (silicon, aluminum, iron), shale, fly ash, mill scale, and bauxite The ore rocks are quarried and crushed into smaller pieces of about 6 inches2022年7月28日 LIME: A Technical Guide for Production, Processing and Va lue Addition 11 expand acute harvest season (ei ther by delaying or hastening maturity) and toLime: A Technical Guide for Production, Processing and Value 2021年4月20日 According to statistics, the proportion of floating dust generated by various production links in coal mines is as follows: The coal mining face accounts for 50%, the tunneling face accounts for Analysis on the Development Status of Coal Mine Dust Disaster 2016年3月10日 The dust flying from cement production process are transported through the air and are deposited in an area close to the manufacturing plants and or far away to distanced placesAIR POLLUTION CONTROL IN CEMENT INDUSTRIES IN INDIA
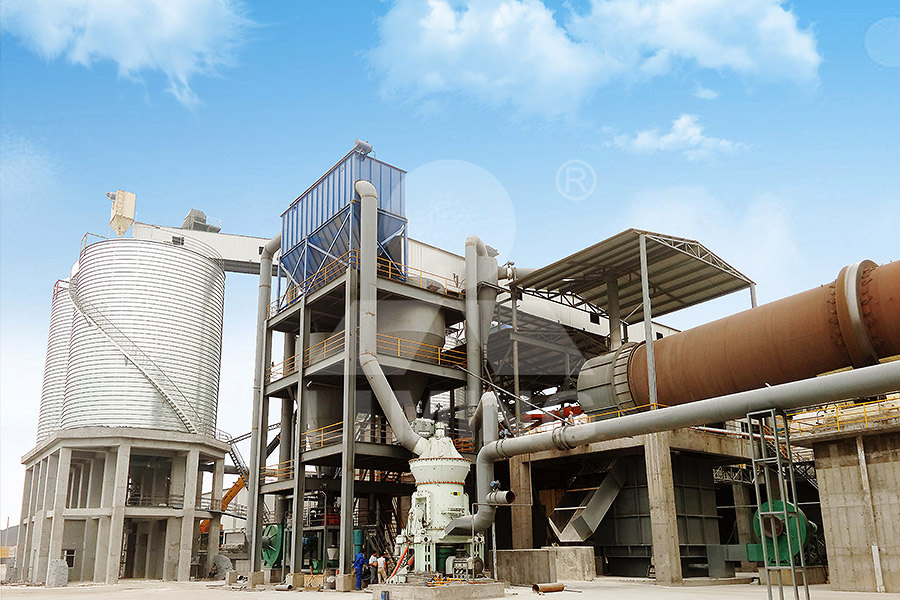
(PDF) Evaluation of solidification/stabilization in arsenic
2019年12月19日 This study focused on evaluating the effectiveness of stabilizer/binding agents in immobilizing arsenic (As) in contaminated soil using both geochemical and geophysical monitoring methods2024年6月1日 The LEILAC (Low Emissions Intensity Lime and Cement) project, led by the European Cement Research Academy, exemplifies the success of carbon capture technology in cement production [53] Employing Calix's Direct Separation Process, the initiative selectively captured CO 2 from cement kiln flue gases, utilising it in the creation of synthetic limestone Decarbonising cement and concrete production: Strategies, 2020年1月20日 The cement kiln bypass dust replacement of cement was 07% and 17%, to satisfy the Cl ions content in cements: lower than or equal to 01%, following the demand of PNEN 1971:2012 standard(PDF) Hydration of cement bypass dust2013年1月1日 Studies on cement production optimisation have been carried out on clinker simulation using AspenTech [36], cement raw materials blending using a general nonlinear timevarying model [37], cement Modelling the cement process and cement clinker
.jpg)
Fugitive Dust Control Measures and Best Practices US
fugitive dust regulations and highlight several effective strategies that have been adopted by facilities The appropriateness and effectiveness of these strategies will vary for different facilities based on many factors, including type of operation, sources of fugitive dust and local regulations These examples are not intended to2014年8月1日 Limebased sludge and marble sludge possess a large amount of calcium, which can replace the calcareous raw materials The burnability of cement clinker is improved with the addition of calcium The utilization of limedried sludge as resource for producing cementProduction of Cement, Lime and Magnesium Oxide Industrial Emissions Directive 2010/75/EU (Integrated Pollution Prevention and Control) JOINT RESEARCH CENTRE Institute for Prospective Technological Studies Sustainable Production and Consumption Unit European IPPC Bureau Draft CLM BREF (June 2012) Colour code: Black: text from the existing CLM BREFBest Available Techniques (BAT) Reference Document for the Production 2024年3月25日 Cement kiln dust (CKD), a byproduct of cement production, holds significant potential as a carbon sink This review comprehensively examines the physical, chemical, and mineralogical characteristics of CKD, highlighting its suitability for carbon dioxide (CO 2) capture and sequestrationWith a high calcium oxide content of 37–77% and notably high alkalinity, Carbon sequestration potential of cement kiln dust: Mechanisms
2FD{P}PC]854]XQ.jpg)
Strategising Dust Management Indian Cement Review
2024年4月17日 Strategies such as dust suppression, enclosure of equipment, ventilation systems, and proper maintenance practices are essential for controlling dust emissions throughout the production process Moreover, investing in advanced technologies and best practices for dust management can contribute to sustainable and responsible cement for a total European production of 28 million tonnes including commercial and captive lime production, which accounted for 20 % of the world’s total lime production In 2003, there were approximately 211 installations producing lime in the EU27 (excluding captive lime production) and in 2006, there were a total of 597 kilns producing Cement, Lime and Magnesium Oxide Manufacturing Industries nquiry time: January, 2022 Equipment requirement: 1 PQ16 type disc granulator 2 Feeding materials: Iron ore powder Client: France HOLCIM company Technical communication process: As a global executive cement design and manufacturing company, HOLCIM company has put forward special requirements for the structure of this granulator as follows 2 unpowered Quality LECA Production Line Active Lime Production Line CEMENT AND LIME MANUFACTURING APRIL 30, 2007 4 WORLD BANK GROUP • Developing a staged combustion process 6,as applicable in preheaterprecalciner (PHP) and preheater (PH) kilns ; • Lime manufacturing: Nitrogen oxide ( NO X) production is generally lower in lime manufacturing than in cement manufacturing Because limestone burning usual ly takesWorld Bank Document
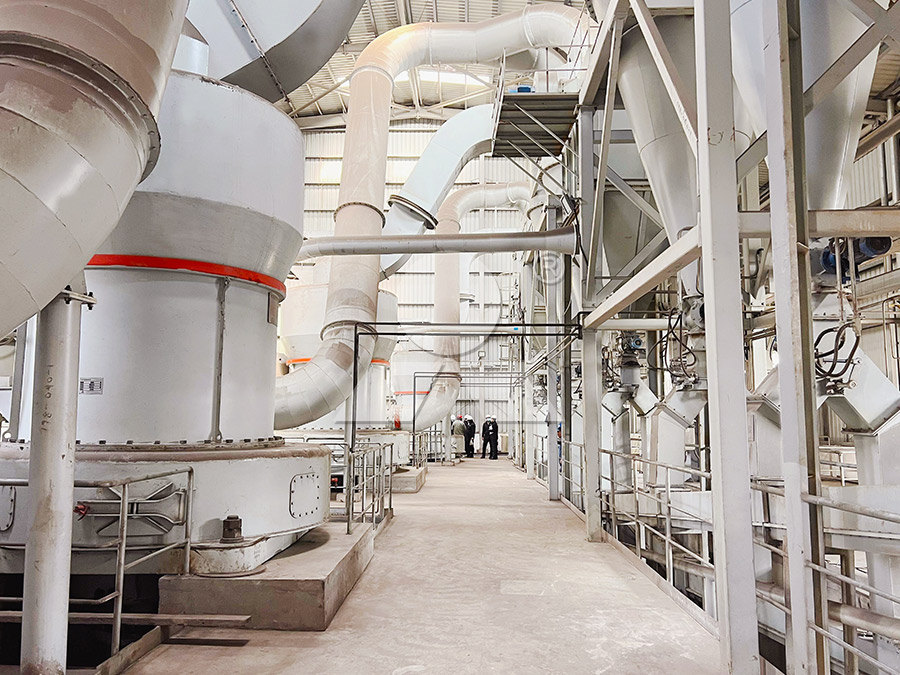
Cement Kiln Dust (CKD): Potential Beneficial
2022年6月8日 Despite the tremendous industrial and technical progress that the world is witnessing, The production of cement kiln dust is a CKD with high free lime was used in the treatment process2019年1月1日 These IEC standards use the following IEC definition of combustible dust as “finely divided solid particles, 500 μm or less in nominal size, which may form explosive mixtures with air at standard atmospheric pressure and temperatures”Although this definition has no criteria for determining whether these solid particles can form explosive mixtures with air, Dust explosions: Regulations, standards, and guidelines2014年12月30日 In the process of production of cement clinker in FCL, metal elements are mostly entered by primary raw materials: limestone, marl lime, clay stone, sand; coal fly ash as secondary raw material Distribution of heavy metals in Portland cement 2023年4月12日 Cement plants generate dust during the production process, which can include raw material grinding, blending, preheating, kiln processes, clinker cooling and cement grinding Dust emitted from cement plants is a significant environmental and health concern in India, where the cement industry is a major contributor to air pollutionDust Control: Balancing Health and Sustainability Indian Cement
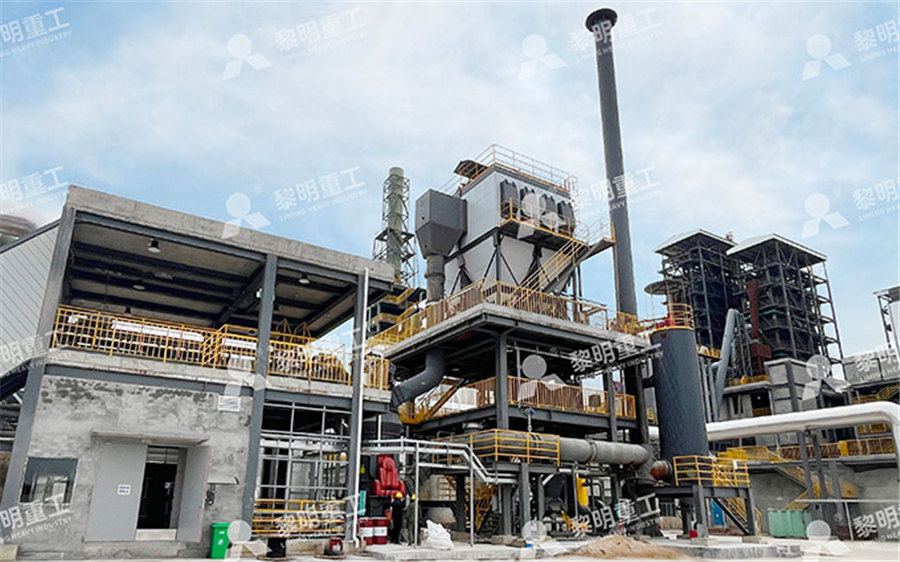
Construction hazardous substances: Cement HSE
Cement based products, like concrete or mortar, can cause serious skin problems such as dermatitis and burns This page tells you how to control these risks and why What you must do The Control of Substances Hazardous to Health (COSHH) Regulations says sharp decline in cement production over the last 15 years, from a peak of 262Mt in 2007 to 168Mt in 2017, equivalent to a reduction in cement per capita from 05 to 03 tonnes per person (3) The CO 2 intensity of cement production over that period has improved by about 7% (06t of CO 2 emitted per tonne of cement in 2017) (2)Deep decarbonisation of industry: The cement sector Europaab0cd Subsectoral Environmental and Social Guidelines: Cement Production Cement Production Subsectoral Environmental and Social Guidelines Page 1 2010 PROCESS DESCRIPTION Cement production facilities are often located in rural areas and close to quarries, where the raw materials required are present, for example, limestone and shaleab0cd Subsectoral Environmental and Social Guidelines: Cement ProductionRegarding point 31(c) above, these BAT conclusions only address the production of MgO using the dry process route based on mined natural magnesite (magnesium carbonate MgCO 3) In particular, concerning the abovementioned activities, these BAT conclusions cover the following: — production of cement, lime and magnesium oxide (dry process BAT conclusions Production of cement, lime and magnesium
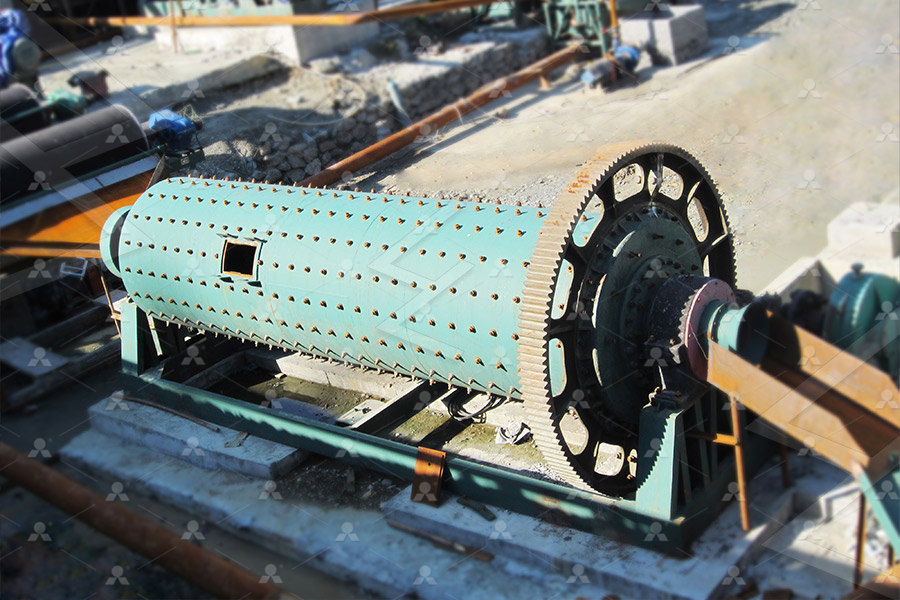
Everything you need to know about Cement Kiln Dust Generation
Mineralogy From the Müller (1977) study of nearly 100 European CKDs, it was found that the dusts are particulate mixtures of four major components: (1) unreacted raw feed, (2) partially calcined feed and clinker dust, (3) free lime, and (4) enriched salts of alkali sulfates, halides, and other volatile compounds2020年3月23日 The addition ratio of lime and stacking time in the sludge limedrying process could greatly affect the carbon footprint of coprocessing limedried sludge in cement kilnFeasibility and Carbon Footprint Analysis of LimeDried Sludge