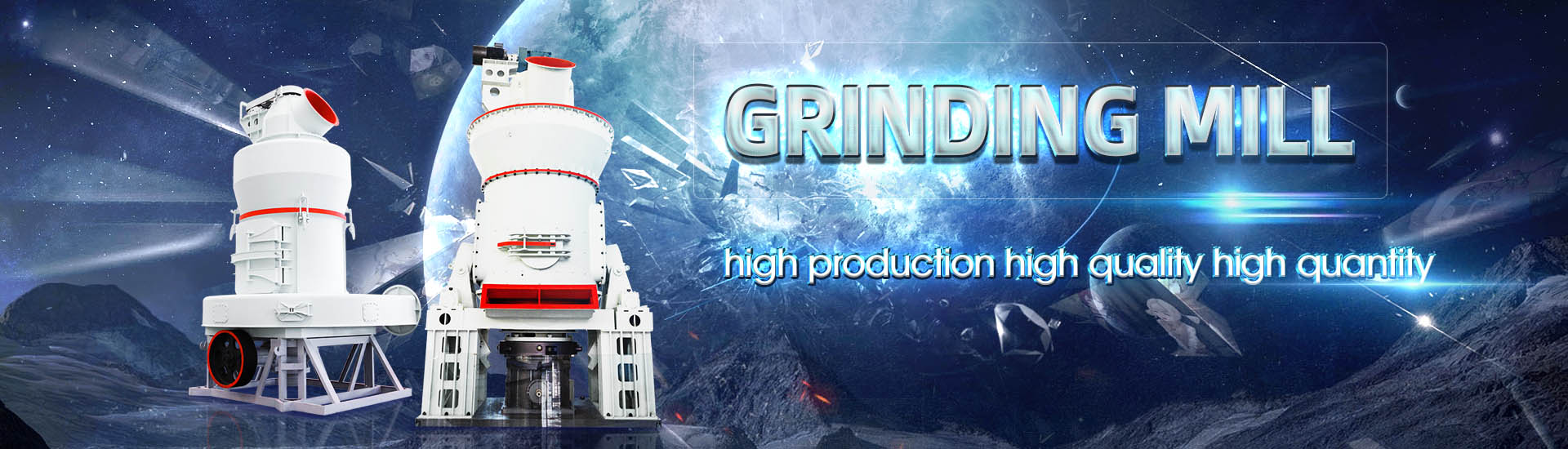
Power plant coal injection pulverized pipe tile manufacturer
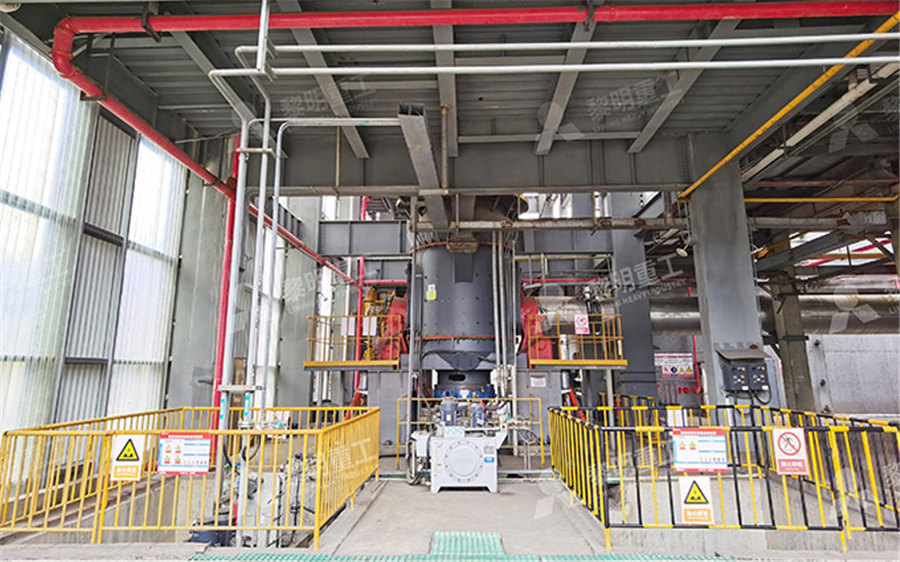
Coal Pulverizer – Power Plant Pall Corporation
Pulverization of coal is currently the favored method of preparing coal for burning Mechanically pulverizing coal into a fine powder enables it to be burned like a gas, thus allowing more Pulverized Coal Injection (PCI) using the denseflow method The Küttner developed and perfected denseflow method offers several advantages over a lowerdensity system Higher Pulverized coal injection (PCI) Iron Steel Kuettner Grouptypical application in power plants is pulverized fuel piping KALMETALL W100 Reliable wear protection is of particular importance for troublefree continuous operation of the pulverised Solutions for Wear Protection in Power Plants KalenbornThe pulverized coal injection technology is based on a combination of several unit operations Main unit operations include: Hot blast backpressure as well as pressure drops in pneumatic Pulverized Coal Injection Paul Wurth
.jpg)
Ceramic Tiled Tube for Pulverized Coal Conveying
Ceramic Tiled Tube for Pulverized Coal Conveying System of Thermal Power Plant, Find Details and Price about Steel Pipe Steel Tube from Ceramic Tiled Tube for Pulverized Coal Conveying System of Thermal Power Plant Shanxi Turbo Cast Basalt Lined Pipes, Bends and Fittings finds Applications in Coal fired Power Stations, Iron and Steel Plants, Cement Plants, Mining Industries, Mineral and Mineral Process Industries, Fertilizer IndustriesTurbo make Cast Basalt Tiles, Lined Pipes, Bends and High rates of pulverized coal injection reduce the required amount of expensive metallurgical coke Drawing upon experience gained during the installation of over 65 PCI systems started from the early eighties, we support our clients in Pulverized Coal Injection Systems Danieli CorusPaul Wurth has been a driver of the pioneering development of Pulverised Coal Injection (PCI) technologies since the early 1980s; today, more than 80 midsize and large Blast Furnaces worldwide are operating with our PCI systems Paul Blast Furnace Ironmaking Paul Wurth
制粉-10.25公众号.jpg)
Pulverized Coal Injection CISDI USA
CISDI is capable of providing coal injection mains that feed directly into the blast furnace over 1200m in length PCI system is designed with an equal pressure drop in each branch, CUMI manufactures High Purity Alumina Ceramic Tiles, CUMITUFF CT90 CT92 wearresistant tiles that are suitable for abrasive and corrosive environments to extend the productive life of a wide variety of bulk material handling and High Purity Alumina Ceramic Tiles Ceramic Lining Raw coal enters the top of the pulverizer through the raw coal feed pipe The raw coal is then pulverized between the roll and rotating ring Hot air is forced in through the bottom of the pulverizing chamber to remove unwanted moisture and transport the coal dust up through the top of the pulverizer and out the exhaust pipe directly to the burnerCoal Pulverizer – Power Plant Pall Corporation2010年10月7日 1 Ensure That Clean Air Balancing Is Within 2% Balance the fuel line system resistances by clean air testing to achieve resistance within ±2% for all pipesPulverized Coal Pipe Testing and Balancing

Pulverised Coal an overview ScienceDirect Topics
26 Examples of Early Pulverized CoalFired Power Plants Pulverized coal achieved rapid acceptance among utilities This rapid acceptance permitted and fostered the rapid development of the technology as described above And this technology became the backbone of fossilfired power plants for nearly 100 years Some examples of early pulverized on the assumptions by JPower (2007) [9] for a 1000 MW USC pulverized coalfired power plant with CCS The sending end output for Case 3 is higher than that for Case 2 as inplant power use is lowerLife cycle assessment of a pulverized coalfired power plant with Wyoming Hanna Basin coal, Rosebud seam, having a heating value 913% below that of the original coal; analysis is shown in Figure 2 This fuel change did not affect Unit 5's load carrying capability Then during 198384, OPP D began procurement of a significantly lower cost Wyoming Powder River Basin coal for their two coalfired plants This coal,WorldProven Coal Pulverizer Technology Debuts in the US Babcock Power2023年1月13日 The paper provides an outlook on future directions of research and the possible applications for pulverized coalfired boilers One potential direction for future research is to focus on the ways to improve the efficiency of pulverized coalfired boilers This could involve developing new combustion technologies that are able to more thoroughly burn the coal and Pulverized CoalFired Boilers: Future Directions of Scientific
.jpg)
Pulverized Coal Injection Paul Wurth
Pulverized Coal Injection 2 Coal Preparation and Pulverized Coal Injection Equipment in Main Structure MAIN BAGFILTERS POWER GAS BLAST FURNACE GAS DRYINGG AS GENERATOR VERTICAL ROLLER MILL DYNAMIC CLASSIFIER MILL CHARGING STOVE PLANT STOVEW ASTE GAS FAN DRYING GAS MAIN FAN Pulverized Coal Injection FT FT 92% ceramic tile lined coal steel pipes are a kind of ceramic and metal organic combining composite pipe, ceramic tube is a combination of alumina the advantages of high hardness, good chemical inertness and steel, excellent wear resistance, corrosion resistance, heat resistance and thermal shock and mechanical shock resistance92% ceramic tile lined coal steel pipes Abrasion resistant pipe2020年9月11日 Schematic of pulverized coal injection in the lower part (lanceblowpipetuyereracewaycoke bed) of a BF [49] Technological advancements in evaluating the performance of operating domestic blast furnaces employed the pulverized coal injection equipment, which increased the average domestic pulverized coal ratio to a 130 kg/t level, (Fig 2) Table 1 shows the various types of injection for the blast furnace pulverized coal equipment Table 2 shows the highest level attained in Japan for3A2 Pulverized Coal Injection for Blast Furnaces (PCI)
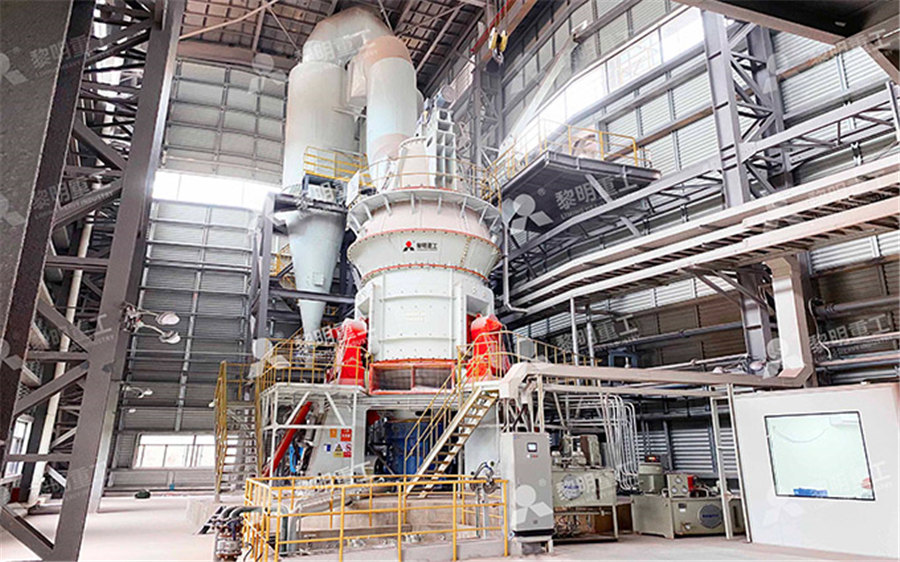
Combustion Characteristics of Coal for Pulverized Coal Injection
Various characterization methods are used to investigate the physical and chemical properties of steel plant flying dust and waste oil sludge, and the combustion characteristics of the mixtures with pulverized coal are studied via thermogravimetric analysis; the catalytic combustion mechanism is also explored The results show that two types of metallurgical byproducts with 2021年8月18日 Medium oxygenenriched blast furnaces that utilize reducing gas injections are a feasible new ironmaking process that can significantly reduce the coke ratio and carbon dioxide emissions To better inject the reducing gas into the blast furnace, two injection methods were designed in this study, and the effects of the reducing gas on the combustion of pulverized Influence of Reducing Gas Injection Methods on Pulverized Coal PCI plant Coal injection system Reduced pollution Coal grinding and injection systems are nonpolluting systems Injecting pulverized coal into a blast furnace reduces the overall pollution made by coke production Increased productivity Installation of a coal injection system can increase productivity through improved operation of the blast Pulverized Coal Injection AmmermannThe injection of the pulverized coal into the BF results into (i) increase in the productivity of the BF, ie the amount of hot metal (HM) produced per day by the BF, (ii) reduce the consumption of the more expensive coking coals by replacing coke with cheaper soft coking or thermal coals, (iii) assist in maintaining furnace stability, (iv) improve the consistency of the quality of the HM and Understanding Blast Furnace Ironmaking with Pulverized Coal Injection

(PDF) Pulverized CoalFired Boilers: Future Directions of Scientific
2023年1月13日 The paper provides an outlook on future directions of research and the possible applications for pulverized coalfired boilers One potential direction for future research is to focus on the ways 2019年2月28日 High Frequency Electromagnetic Simulation (HFSS) software was used to construct a simulation model for measuring pulverized coal concentration in power plant pipeline W L Wu, J Yu, and J Hu, "The study of diagnosing the running condition of pulverized coal in pipe," Proceeding of the CSEE, vol 21, no 7, pp 8386, 2001Simulation Study on Measuring Pulverized Coal Concentration in Power 625MWe conventional Rankine cycle power plant using pulverized coal firing (PF) (reference plant with atmospheric pulverized coal combustion) repowered with a new and potentially advantageous technology, namely, pressurized pulverized coal firing in a combined cycle (PPCC) power plant The performance of power plants is determined based on Thermodynamic analysis of a coalfired power plant Raw coal enters the top of the pulverizer through the raw coal feed pipe The raw coal is then pulverized between the roll and rotating ring Hot air is forced in through the bottom of the pulverizing chamber to remove unwanted moisture and transport the coal dust up through the top of the pulverizer and out the exhaust pipe directly to the burnerCoal Pulverizer – Power Plant Pall Corporation
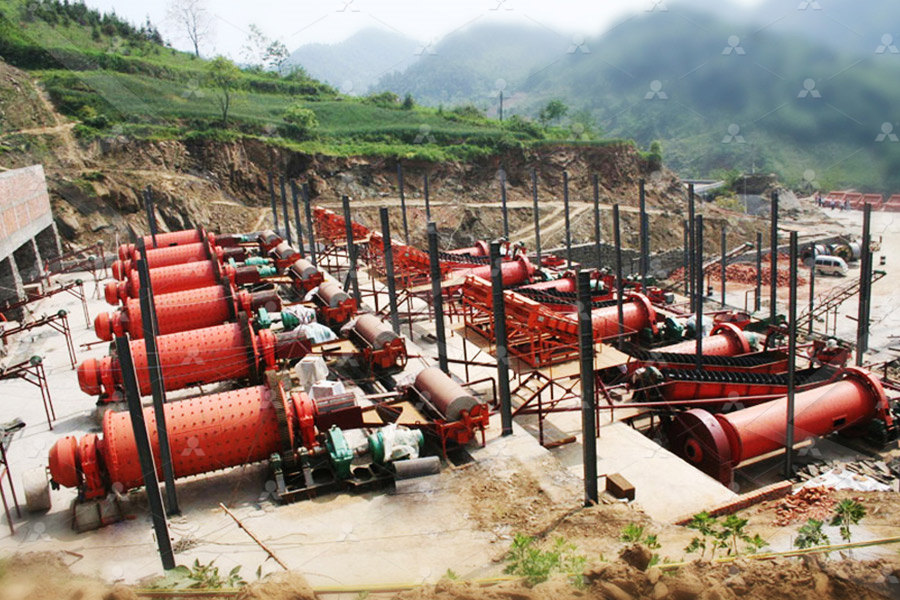
Relationship between Particle Size Distribution of LowRank Pulverized
2012年4月24日 The impact of particle size distribution (PSD) of pulverized, low rank high volatile content Alaska coal on combustion related power plant performance was studied in a series of field scale tests2024年1月1日 The blast furnace injection process system is mainly composed of raw coal storage and transportation system, dry gas preparation system, pulverized coal preparation system, pulverized coal conveying system, pulverized coal injection system, and gas supply system (Fig 1)There is also a computer control center to control the entire pulverized coal Pulverized Coal Injection of Blast Furnace Ironmaking1996年4月10日 Exhaust gas temperature in coalfired power plants can reach approximately 120 °C to 140 °C, with the thermal energy accounting for approximately 3% to 8% of the total input energyDevelopments in Pulverized CoalFired Boiler Case 2: a stateoftheart ultrasupercritical pulverized coal fired power plant as proposed by several companies to be installed in the coming years (2011–2013) in the Netherlands (Arcadis, 2007; KEMA, 2006a,b) This power plant can be considered best available technology at presentLife cycle assessment of a pulverized coal power plant with post
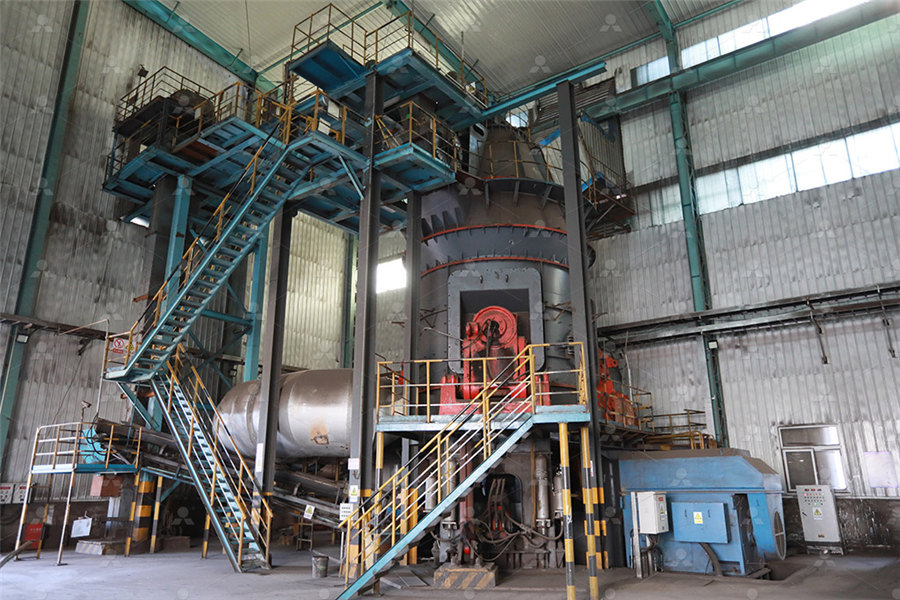
CONVERSION OF A PULVERIZED COAL POWER PLANT TO 100
pulverized coal power plant located near Liège This full conversion from coal to wood is thought to be a world premiere since the use of fossil fuel in the plant has been totally abandonedFuel preparation for a pc boiler occurs in a mill, where coal is typically reduced to 70% through a 200mesh (74μm) screen Figure 2 shows a particlesize distribution from a bowlmill grinder typically used in power plants A typical utility specification for particle size distribution of the coal is that 70% of the mass should pass through a 200mesh screen, which is equivalent to 70% Pulverized Coal Boiler an overview ScienceDirect Topics2022年11月2日 31 NO x Emission Characteristics up to a Maximum Ammonia Cofiring Rate of 20% When ammonia is cofired in a pulverized coal combustion plant, an increase in NO x concentration is expected owing to the oxidation of nitrogen in the ammonia If a significant increase occurs, removing NO x concentration from the existing flue gas treatment device Applicability of Ammonia Cofiring Technology in Pulverized Coal Since the first application using an MPS mill to process pulverized coal in Germany in the mid 1960s, there have been over 2,000 different MPS mill installations operating in coalfired power plants worldwide As one of the most popular coal pulverizers in the utility industry, the MPS mill was first introduced into the US in the early 1970sCoal Pulverizer Design Upgrades to Meet the Demands of Babcock Power
.jpg)
Application of Ceramic Grinding Sheet in Wearresisting Elbow of Coal
Application of Ceramic Grinding Sheet in Wearresisting Elbow of Coal Pulverized Coal Pipe, Know more About Knowledge for Tabular Alumina, Alumina Ceramic Mosaic Tile, Alumina ceramic Plate, High Alumina Ceramic Balls Wet It has always been a key part of power plant maintenance The comprehensive performance of the pipeline 2021年8月5日 The main Function of the Pulveriser in thermal power plant is to crush/grinding the raw coal coming from coal handling system through coal feeder into a predetermined size in order to increase the surface area of the coal If the coal is not pulverised, the coal might not burn completely, thus resulting in wastage of fuelPulveriser in Thermal Power Plant Bowl Mill Ball Mill2009年10月1日 Once pulverized coal flows have been measured, they can be balanced and optimized Until then, tuning is simply guesswork The right way to balance furnace fuel flows is to establish solid Measuring Coal Pipe Flow POWER MagazineRaw coal enters the top of the pulverizer through the raw coal feed pipe The raw coal is then pulverized between the roll and rotating ring Hot air is forced in through the bottom of the pulverizing chamber to remove unwanted moisture and transport the coal dust up through the top of the pulverizer and out the exhaust pipe directly to the burnerCoal Pulverizer – Power Plant Pall Corporation
.jpg)
Pulverized Coal Pipe Testing and Balancing
2010年10月7日 1 Ensure That Clean Air Balancing Is Within 2% Balance the fuel line system resistances by clean air testing to achieve resistance within ±2% for all pipes26 Examples of Early Pulverized CoalFired Power Plants Pulverized coal achieved rapid acceptance among utilities This rapid acceptance permitted and fostered the rapid development of the technology as described above And this technology became the backbone of fossilfired power plants for nearly 100 years Some examples of early pulverized Pulverised Coal an overview ScienceDirect Topicson the assumptions by JPower (2007) [9] for a 1000 MW USC pulverized coalfired power plant with CCS The sending end output for Case 3 is higher than that for Case 2 as inplant power use is lowerLife cycle assessment of a pulverized coalfired power plant with Wyoming Hanna Basin coal, Rosebud seam, having a heating value 913% below that of the original coal; analysis is shown in Figure 2 This fuel change did not affect Unit 5's load carrying capability Then during 198384, OPP D began procurement of a significantly lower cost Wyoming Powder River Basin coal for their two coalfired plants This coal,WorldProven Coal Pulverizer Technology Debuts in the US Babcock Power
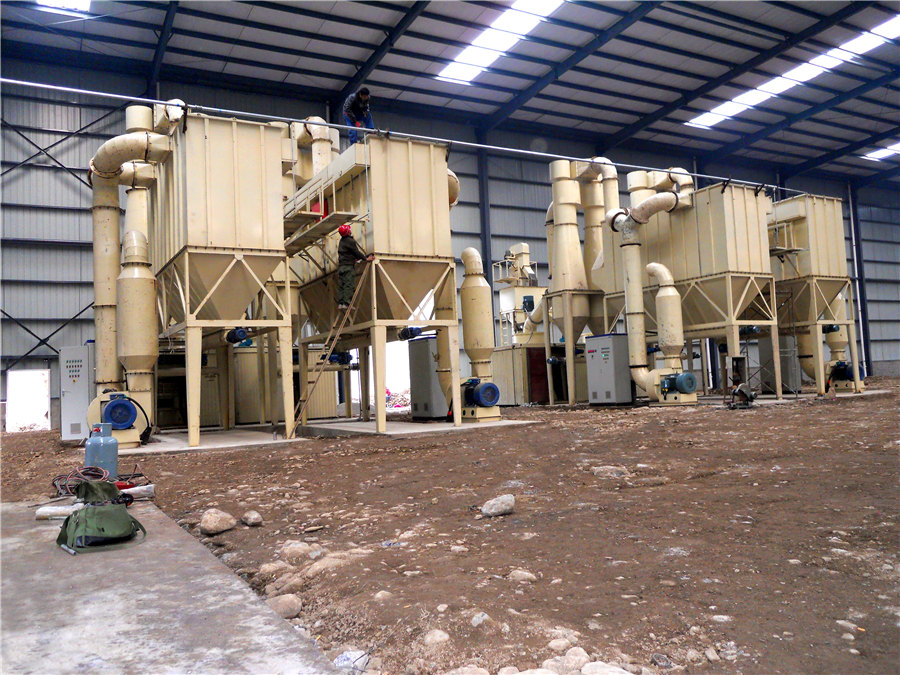
Pulverized CoalFired Boilers: Future Directions of Scientific
2023年1月13日 The paper provides an outlook on future directions of research and the possible applications for pulverized coalfired boilers One potential direction for future research is to focus on the ways to improve the efficiency of pulverized coalfired boilers This could involve developing new combustion technologies that are able to more thoroughly burn the coal and Pulverized Coal Injection 2 Coal Preparation and Pulverized Coal Injection Equipment in Main Structure MAIN BAGFILTERS POWER GAS BLAST FURNACE GAS DRYINGG AS GENERATOR VERTICAL ROLLER MILL DYNAMIC CLASSIFIER MILL CHARGING STOVE PLANT STOVEW ASTE GAS FAN DRYING GAS MAIN FAN Pulverized Coal Injection FT FT Pulverized Coal Injection Paul Wurth92% ceramic tile lined coal steel pipes are a kind of ceramic and metal organic combining composite pipe, ceramic tube is a combination of alumina the advantages of high hardness, good chemical inertness and steel, excellent wear resistance, corrosion resistance, heat resistance and thermal shock and mechanical shock resistance92% ceramic tile lined coal steel pipes Abrasion resistant pipe2020年9月11日 Schematic of pulverized coal injection in the lower part (lanceblowpipetuyereracewaycoke bed) of a BF [49] Technological advancements in evaluating the performance of
制粉-10.25公众号.jpg)
3A2 Pulverized Coal Injection for Blast Furnaces (PCI)
operating domestic blast furnaces employed the pulverized coal injection equipment, which increased the average domestic pulverized coal ratio to a 130 kg/t level, (Fig 2) Table 1 shows the various types of injection for the blast furnace pulverized coal equipment Table 2 shows the highest level attained in Japan for