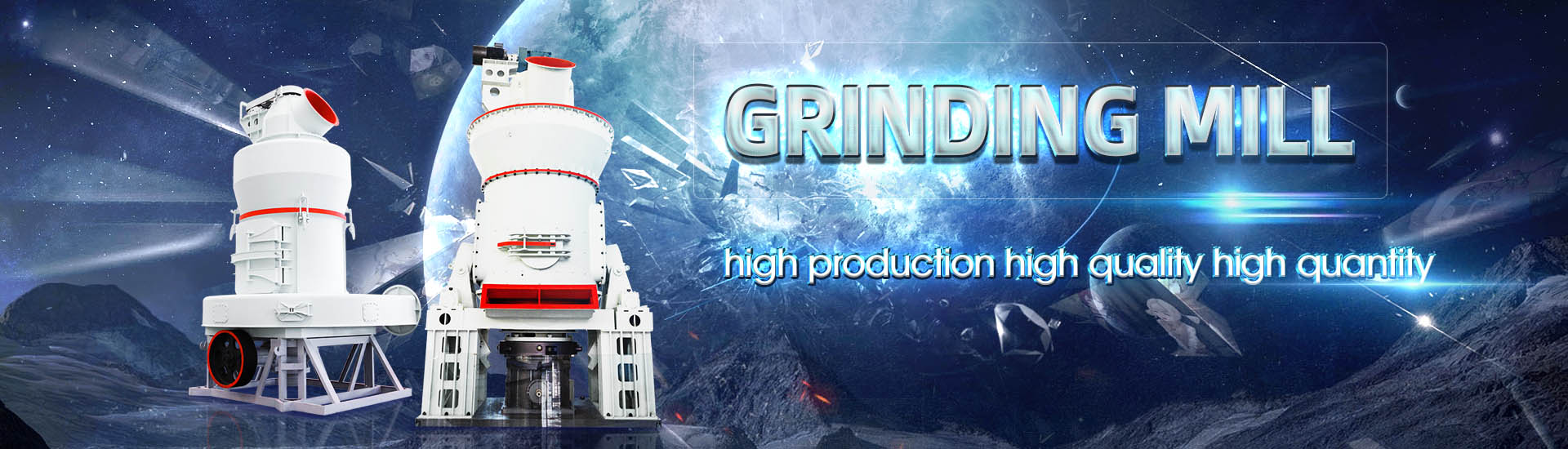
About cement mill
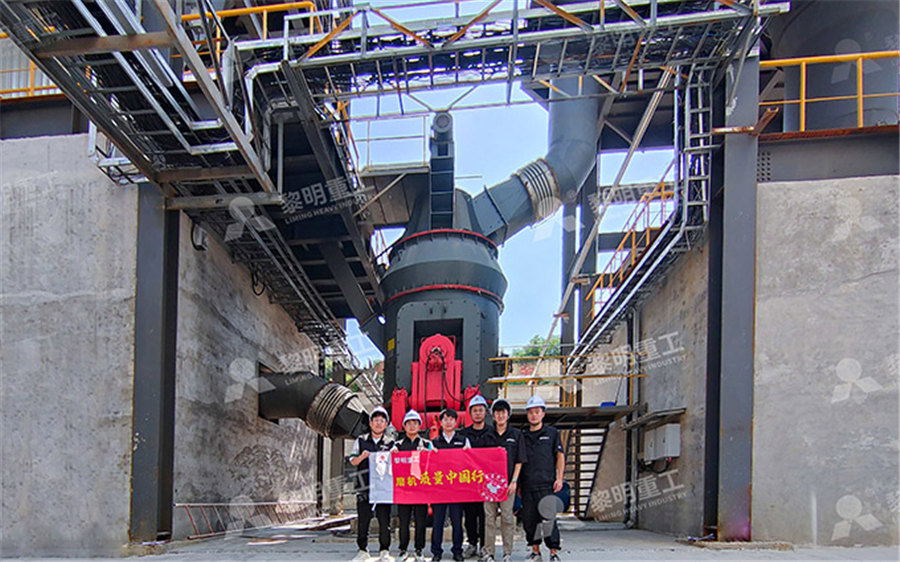
Cement Milling
Cement milling is usually carried out using ball mills with two or more separate chambers containing different sizes of grinding media (steel balls) Grinding clinker requires a lot of energy How easy a particular clinker is to grind 2015年12月9日 This paper presents an analysis of the cement manufacturing process, an outline of the pollutants generated from cement manufacturing (PDF) Cement Manufacturing ResearchGateConcrete is formed when portland cement creates a paste with water that binds with sand and rock to harden Concrete is the most widely used resource in the world after water Cement is manufactured from materials heated together at How Cement is Made Portland Cement AssociationThere are six main stages of the cement manufacturing process The raw cement ingredients needed for cement production are limestone (calcium), sand and clay (silicon, aluminum, iron), How Cement is Made Cement Manufacturing Process
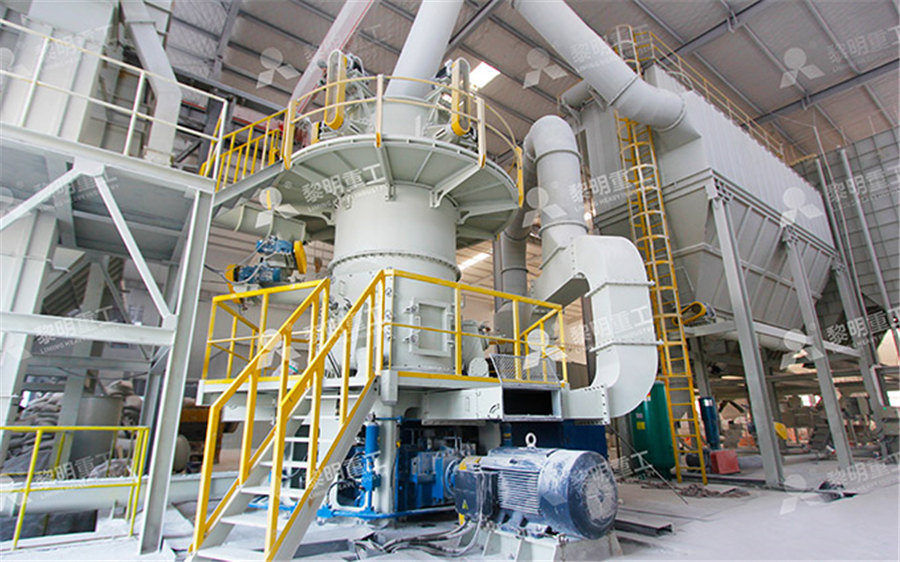
The Cement Plant Operations Handbook International Cement
The Cement Plant Operations Handbook is a concise, practical guide to cement manufacturing and is the standard reference used by plant operations personnel worldwide Providing a together in a raw mill to a particle size of 90 micrometres, producing “kiln feed” Cement Plant: The Manufacturing Process worldcementassociation 1 Limestone (CaCO3) is taken from a Cement Plant: The Manufacturing Process 4 5 World Cement All over the world, cement is one of the most important building materials Whether for houses, bridges or tunnels, we cannot imagine our modern world without it Join us for a short tour to experience how cement is made: starting How cement is made Heidelberg MaterialsThe cement mill can be used as a raw mill or cement grinding mill, AGICO Cement provides vertical cement mill, cement ball mill and other highquality cement grinding machines for you! Skip to content +86 Cement Mill Cement Ball Mill Vertical Cement Mill
.jpg)
Cement Ball Mill Cement Grinding Machine
Cement ball mill is a cement grinding machine used in the cement production line for cement clinker grinding AGICO supplies the cement ball mills for processing limestone, cement clinker, gypsum, slag, ore, etc Skip to content Blog Finish mill – 12 Cement – 13 Quality control – 14 Packing and distribution – 15 Emission abatement (dust, NO x, SO 2, etc) – 16 Maintenance – 17 Process – 18 Materials analysis –19 Plant capacity summary – 20 Storage capacity 15 Cement plant construction and valuation 244 1The Cement Plant Operations Handbook International Cement The roller grinding mill technology, patented in 1928 and continuously developed since then, has become synonymous with Loesche‘s pioneering engineering knowhow CEMENT BLAST FURNACE SLAG CEMENT RAW MATERIALCement Industry LoescheCement Mill Optimization: Practical Strategies for Enhanced Efficiency and Performance if you need to download the exact details of this post and all the information on this website + excel sheets tailored for cement industry from expert who is working as a consultant from 37 years buy the book package now Cement Mill Optimization: Practical Strategies for Enhanced
.jpg)
How Cement is Made Portland Cement Association
Cement is manufactured from materials heated together at high temperatures to form a rocklike substance that is ground into a fine powder Main Ingredients Calcium; The clinker keeps cooling and a ball mill grinds it with gypsum or other ingredients into fine cement—about 150 billion grains per pound2020年11月5日 We compare 3 cement milling and cement mill processes, including cement ball mill, vertical roller mill, and rod mill Find your answer here! Skip to content +86 s about blog contact EN ES Menu Menu Home; Cement Equipment Raw Material processing Stacker And Reclaimer; Cement Crusher;3 Necessary Cement Milling Comparison Ball Mill, Vertical Roller MillA cement roller press is also referred to as a roller press cement mill, or cement roller press machineIt is a grinding equipment that can be applied for greenfield cement grinding plants or upgraded cement grinding plants It has the features of low consumption and high efficiency compared to the traditional ball mill pregrinding system The output in a roller press grinding Roller Press In Cement Plant Roller Press Cement Mill CNBM Our bestinclass OK™ Mill is a globally successful vertical roller mill solution for grinding raw material, cement and slag Its cuttingedge design features consistently deliver the highest quality products with the greatest efficiency It is affordable to install and cost effective to operate over your cement plant’s lifetimeOK™ Raw and Cement Mill
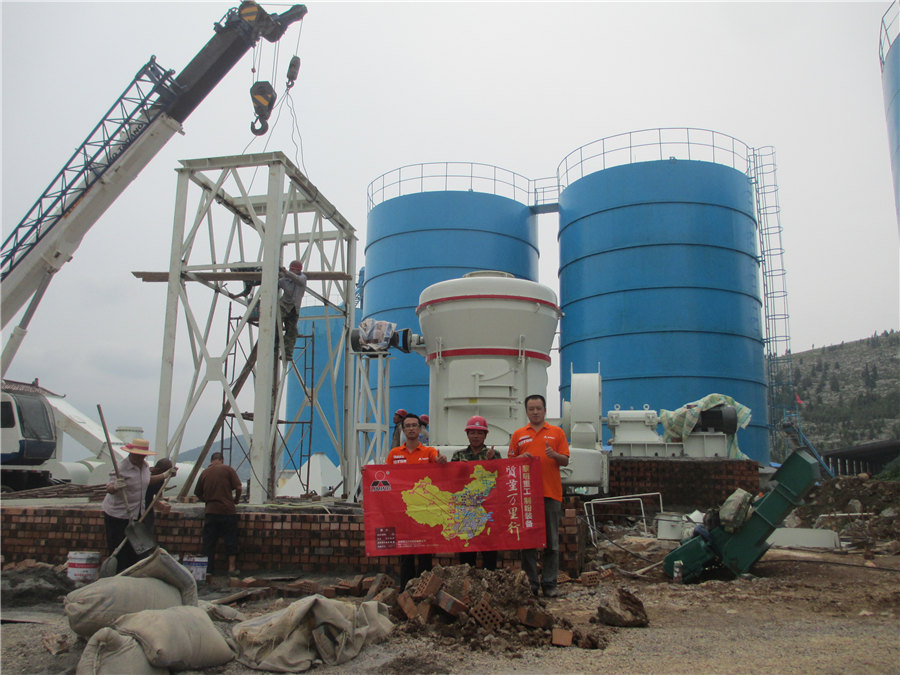
Cement Extraction, Processing, Manufacturing Britannica
2024年11月23日 Cement Extraction, Processing, Manufacturing: Raw materials employed in the manufacture of cement are extracted by quarrying in the case of hard rocks such as limestones, slates, and some shales, with the aid of blasting when necessary Some deposits are mined by underground methods Softer rocks such as chalk and clay can be dug directly by Design of cement mill liners There are several types of cement mill liners: feedendliners, liftingliners, classifying linersMagotteaux determines the optimum design and alloy for cement mill liners to give the best mill protection and Cement mill liners MagotteauxBall mill is the cement crushing equipment in the cement plant Compared with open circuit ball mill, the closedcircuit ball mill has high efficiency, high output, low cement temperature, and good comprehensive benefit It is the best Ball Mill In Cement Plant Cement Ball Mill AGICO However, particle size distribution is again a problem, and roll presses are now increasingly popular as a "pregrind" process, with the cement finished in a single chamber ball mill This gives good cement performance, and reduces energy consumption by 2040% compared with a standard ball mill system Capacity of cement millsCement mill
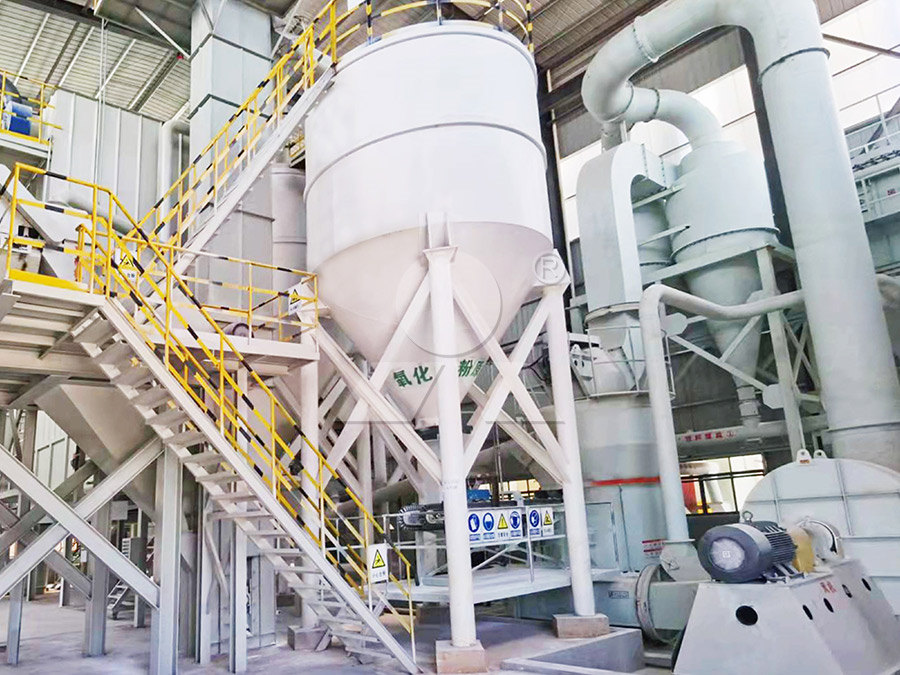
Raw Mill Moisture Content Management: A Comprehensive Guide
A cement plant in the Middle East faced issues with high moisture content in its raw materials, leading to frequent mill stoppages and reduced output By installing a rotary dryer before the raw mill, the plant reduced moisture levels by 15%, resulting in smoother mill operations and a 20% increase in production capacity 52Simply put, the roller press is the most energyefficient grinding machine on the market Since its commercial introduction into the cement industry by KHD in the 1980s, hundreds of them have been installed in the cement and minerals industries, in both finish and semifinish applications And with the lowest specific energy consumption among comparable comminution Roller Press KHD Humboldt WedagCement ball mill and cement vertical mill are two raw mills commonly used in cement plants As the main cement equipment in the cement production line, the two cement raw mills have different characteristics Skip to content Blog Contact About Cases Factory CONTACT US info@cementplantequipment CALL US +86 Raw Mill – Raw Mill In Cement Plant AGICO Cement Raw MillThe vertical cement mill is largescale cement grinding machine With advantages of energyefficient and stable quality, vertical roller mill is widely applied to many industries, such as cement, power, metallurgy, chemical and nonmetallic mining industry and etc As a typical type of Cement Mill, vertical cement mill set crushing, drying, grinding, grading transportation in one, it grind Vertical Cement Mill
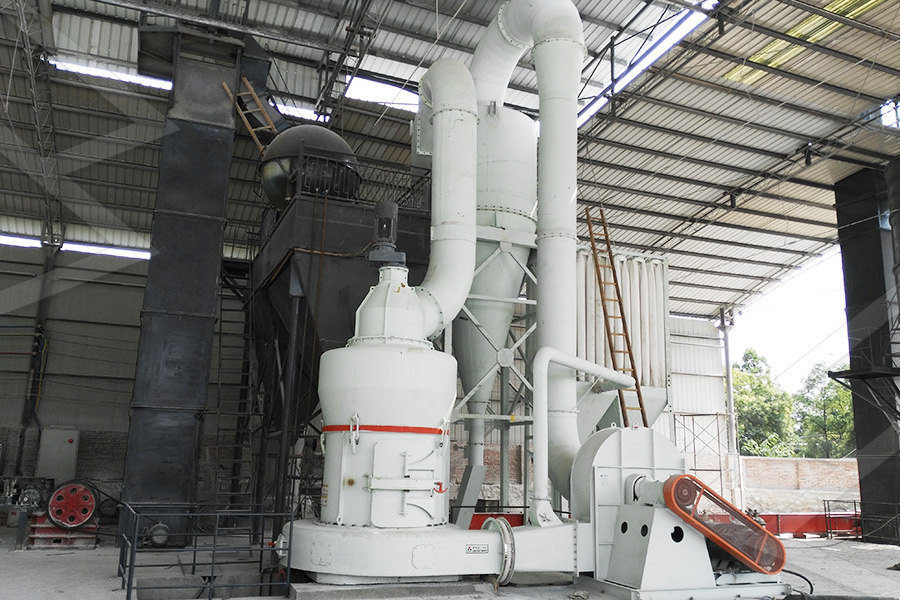
polysius® booster mill
Bead mill working principle for dry cement grinding One crucial characteristic of this mill is the high energy density, 1020 times higher than of a ball mill, and the resulting very compact design The beadstirring elements on the shaft inside the fixed shell reach a tip speed of 5 It consists of cement ball mill, dust collector, belt conveyor, bucket elevator, cement silo, powder concentrator, etc AGICO provides highquality clinker grinders and advanced cement grinding technology Skip to content Blog Contact About Cases Factory CONTACT US info@cementplantequipment CALL US +86 Cement Grinding Unit Clinker Grinder AGICO CementTypes of cement mill liners: liftingliners Magotteaux produces different liftingliners to fit your specific need in cement mill liners Xstep™ is designed for anything up to extreme running conditions It can perform a continuous lifting effect and also provides optimized cascading balls trajectories Its weight is about 20 per cent lower than that of most []Cement mill liners MagotteauxCement Mill UNIVERSAL DRIVE BALL MILLS UDCM type mills are designed to achieve maximum grinding efficiency, low energy consumption, compact plant layout and compact mill drive design All mill types may operate in either open Cement Mill Dal Machinery
CFB石灰石脱硫剂制备64.jpg)
Cement mill liners Magotteaux
Types of cement mill liners: feedendliners In the cement mill liners known as feedend liners drillings of the castings have to fit with the existing shell drilling and the slope of the flange They are made from manganese to highchrome alloys including also martensitic steels The choice of alloy is linked to the design of the casting, the running conditions in the mill and its expected The mill produces optimumquality, highresistance cement with a lower Blaine, and enables an exceptionally high cement/clinker ratio The FCB Horomill® helps cement producers reach sustainability goals through: The lowest energy Fives Sustainable grinding with FCB Horomill®2019年9月27日 Cement mill is another necessary cement equipment of the cement plant After raw material crushing, cement mill plays vital role in the further cement manufacturing process Cement ball mill, vertical cement mill, and cement roller press are common types of Cement Euipment Overview Cement Making Machines Cement 2023年8月23日 A cement mill is a fundamental component of the cement manufacturing process, playing a vital role in breaking down and grinding cement clinker into fine powder This finely ground powder, when mixed with other materials, produces the building material we commonly know as cement To achieve this crucial transformation, a cement mill comprises What Are the Parts of a Cement Mills? Cement Ball Mill
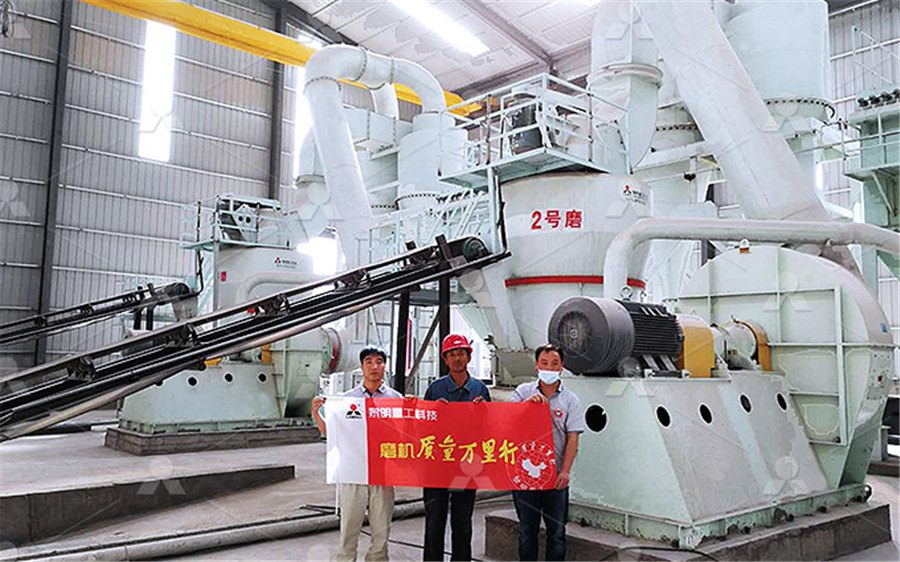
Cement mills SKF
Cement mill equipment must withstand high vibration, shock loads, slow speeds and a high concentration of particulates All of which means that contamination, loss of lubricant and even improper mounting techniques can all lead to failures for pinions or trunnionsCement mills are the milling machines used in cement plants to grind hard clinker into fine cement powders Cement ball mill and vertical roller mill are two most widely used cement mills in today’s cement grinding plants and are also the main types of cement mill we produce As a professional cement equipment manufacturer, AGICO has rich experience in the designing and Cement Mill for Sale Buy Cement Ball Mill Vertical Roller Mill 2023年12月20日 The clinker is ground to a fine powder in a cement mill and mixed with gypsum to create cement The powdered cement is then mixed with water and aggregates to form concrete that is used in construction Clinker quality depends on raw material composition, The Cement Manufacturing Process Thermo Fisher ScientificIn the construction of the cement production line, vertical mill or cement vertical mill is the main cement equipment Its installation plays a vital role in the construction of the whole production line Skip to content Blog Contact About Cases Factory CONTACT US info@cementplantequipment CALL US +86 Vertical Mill In Cement Plant Cement Vertical Mill AGICO Cement
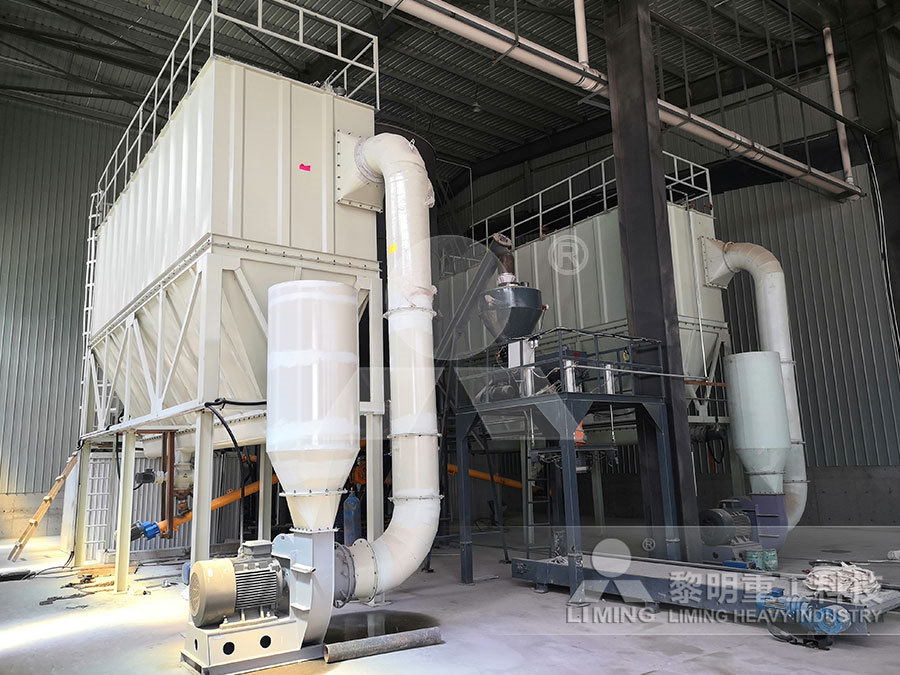
Everything you need to know about Cement Kiln Dust Generation
Everything you need to know about Cement Kiln Dust Generation and Management could be processed in a separate and possibly smaller kiln to produce a clinker that could be added to the grinding mill with the clinker from the main kiln system (Terry, 1992)The cement mill can be used as a raw mill or cement grinding mill, AGICO Cement provides vertical cement mill, cement ball mill and other highquality cement grinding machines for you! Skip to content +86 Cement Mill Cement Ball Mill Vertical Cement MillCement ball mill is a cement grinding machine used in the cement production line for cement clinker grinding AGICO supplies the cement ball mills for processing limestone, cement clinker, gypsum, slag, ore, etc Skip to content Blog Cement Ball Mill Cement Grinding MachineFinish mill – 12 Cement – 13 Quality control – 14 Packing and distribution – 15 Emission abatement (dust, NO x, SO 2, etc) – 16 Maintenance – 17 Process – 18 Materials analysis –19 Plant capacity summary – 20 Storage capacity 15 Cement plant construction and valuation 244 1The Cement Plant Operations Handbook International Cement
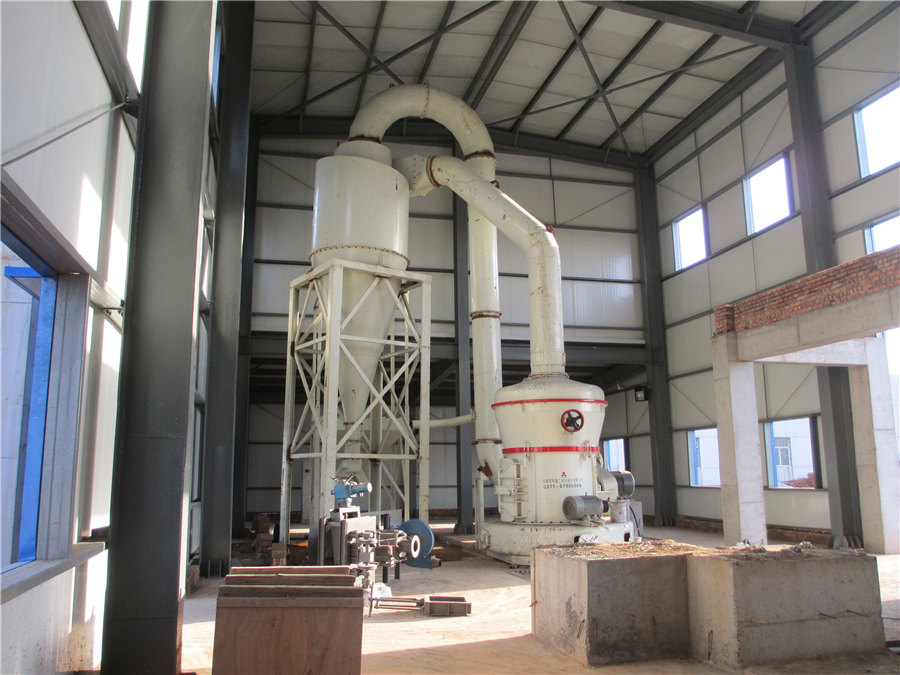
Cement Industry Loesche
The roller grinding mill technology, patented in 1928 and continuously developed since then, has become synonymous with Loesche‘s pioneering engineering knowhow CEMENT BLAST FURNACE SLAG CEMENT RAW MATERIALCement Mill Optimization: Practical Strategies for Enhanced Efficiency and Performance if you need to download the exact details of this post and all the information on this website + excel sheets tailored for cement industry from expert who is working as a consultant from 37 years buy the book package now Cement Mill Optimization: Practical Strategies for Enhanced Cement is manufactured from materials heated together at high temperatures to form a rocklike substance that is ground into a fine powder Main Ingredients Calcium; The clinker keeps cooling and a ball mill grinds it with gypsum or other ingredients into fine cement—about 150 billion grains per poundHow Cement is Made Portland Cement Association2020年11月5日 We compare 3 cement milling and cement mill processes, including cement ball mill, vertical roller mill, and rod mill Find your answer here! Skip to content +86 s about blog contact EN ES Menu Menu Home; Cement Equipment Raw Material processing Stacker And Reclaimer; Cement Crusher;3 Necessary Cement Milling Comparison Ball Mill, Vertical Roller Mill
.jpg)
Roller Press In Cement Plant Roller Press Cement Mill CNBM
A cement roller press is also referred to as a roller press cement mill, or cement roller press machineIt is a grinding equipment that can be applied for greenfield cement grinding plants or upgraded cement grinding plants It has the features of low consumption and high efficiency compared to the traditional ball mill pregrinding system The output in a roller press grinding Our bestinclass OK™ Mill is a globally successful vertical roller mill solution for grinding raw material, cement and slag Its cuttingedge design features consistently deliver the highest quality products with the greatest efficiency It is affordable to install and cost effective to operate over your cement plant’s lifetimeOK™ Raw and Cement Mill2024年11月23日 Cement Extraction, Processing, Manufacturing: Raw materials employed in the manufacture of cement are extracted by quarrying in the case of hard rocks such as limestones, slates, and some shales, with the aid of blasting when necessary Some deposits are mined by underground methods Softer rocks such as chalk and clay can be dug directly by Cement Extraction, Processing, Manufacturing Britannica