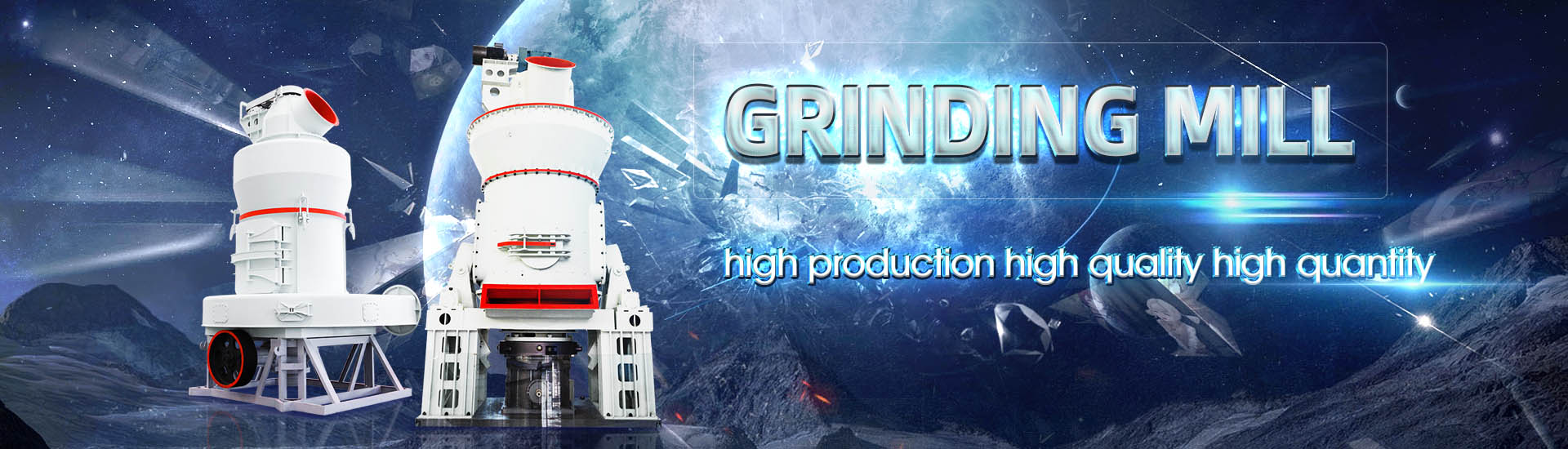
Where can I buy highefficiency energysaving grinding mill in Chengdu
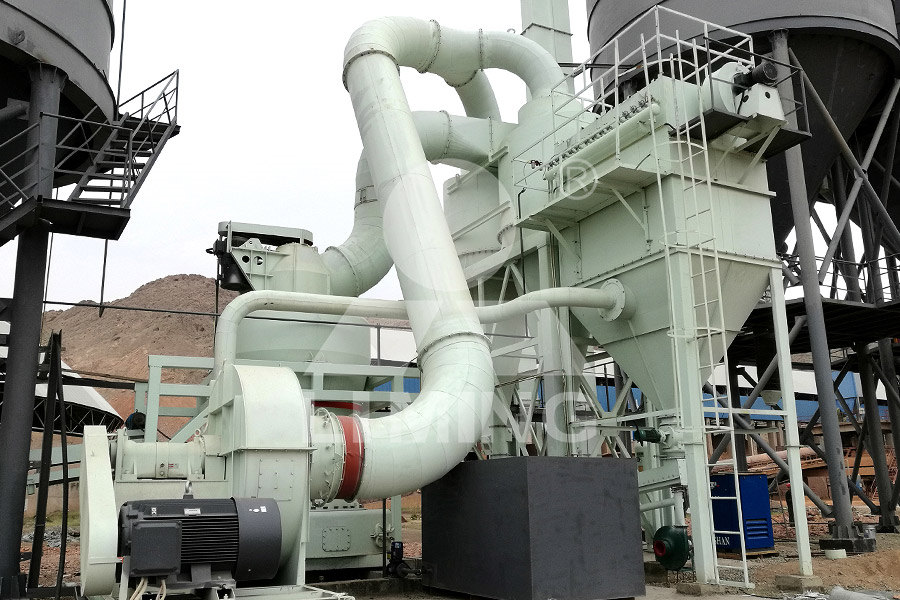
Energy Efficiency Solutions Ball Mill WEG
The solution consists of a highefficiency set: W22 Magnet IE4 Super Premium or W22 Magnet IE5 Ultra Premium motor driven by the CFW11 variable speed drive The motor speed control Metso HIGmill™ is an advanced and energyefficient fine and ultrafine grinding solution that relies on proven technology The mill takes advantage of gravitational forces and GrindForce™ rotor technology to produce a finer grind HIGmill high intensity grinding mill MetsoVertimill® is an energy efficient grinding machine They tend to grind more efficiently than, for example, ball mills with feeds as coarse as 6 mm to products finer than 20 microns This Vertimill® Metso2018年1月1日 However, highperformance dry machining processes (especially of lowstrength materials) offer about 104 times higher energy efficiency than grinding processes with small Energy efficiency of stateoftheart grinding processes
.jpg)
Grinding technology thyssenkrupp Polysius
Costeffective, reliable and energysaving: for its high performance range of mills for the grinding of a wide variety of materials, thyssenkrupp Polysius offers solutions to suit your every need 2019年8月19日 Whether you’re designing a brandnew mill circuit or optimising an existing site for longterm efficiency, High Pressure Grinding Rolls offer a range of advantages over How HPGRs compare to conventional milling WeirHigh intensity stirred milling is now an industry accepted method to efficiently grind fine and coarse particles In particular, the IsaMillTM, which was invented for, and transformed the fine IsaMillTM Technology Used in Efficient Grinding Circuits2019年11月11日 It is essential that new technologies, which will increase productivity and efficiency, help to reduce costs The efficient use of resources is critical for every sector This EFFICIENCY IN GRINDING AND ENERGY MANAGEMENT IN THE
.jpg)
EnergyEfficient Technologies in Cement Grinding IntechOpen
2016年10月5日 Energyefficient equipments such as highpressure grinding rolls, vertical roller mills, CKP pregrinders, Cemex ® mills and Horomills ® are used at both finish grinding of Ball Mills are widely used in the ceramic and mining industries, where the grinding process requires strict grain size control WEG developed an efficient solution for this applicEnergy Efficiency Solutions Ball Mill WEG2017年9月13日 Operating efficiency, based upon using operating work indices, is also a useful tool in comparing the variations in grinding mill operations such as: mill speed, mill size, size of grinding media, mill discharge arrangements, liner designs etcHow to Calculate Grinding Mill Operating Efficiency2018年1月1日 In times of unstable market development due to the energy system transformation and legislative measures concerning the reduction of CO 2 emissions, the manufacturing industry is increasingly aware of the ecological and economical importance of the factor energy A considerable share of industrial energy and resource consumption can be attributed to Energy efficiency of stateoftheart grinding processes
.jpg)
IMPROVING ENERGY EFFICIENCY IN BARRICK GRINDING CIRCUITS
additional installations either in construction or planned Grinding is an essential, but energyintensive, part of gold recovery requiring crushers, large diameter semiautogenous grinding (SAG) mills and ball mills with up to 12,000 kW motors Ore grinding can account for 60% of a site’s electrical power load and2022年1月1日 A pilotscale grinding technology of ceramic medium stirred mill was proposed in this study Based on the specific productivity and grinding efficiency, the appropriate grinding parameters were ascertained as follows: material ball ratio of 07, ceramic ball medium size ratio (10 mm: 15 mm: 20 mm = 3:2:5), stirring speed of 110 rpm, grinding concentration of 50%, Highefficiency and energyconservation grinding technology using Drivers of grinding energy transfer to ore in ball mills • Charge density –charge shape and liner design • Charge surface area • Pulp density rheology • Media mass • Classifier efficiency How can we increase the grinding surface area? 1 Increase the grinding surface • Smaller ball media, or • Different media shape 2Rethinking Grinding Efficiency in Ball Mills2009年6月1日 It can be identified as a general conclusion that this recently introduced mill is not yet applied in a wide range in MA compared to other high energy density mills (HEM) like planetary ball mill Comparison of energy efficiency between ball mills and stirred
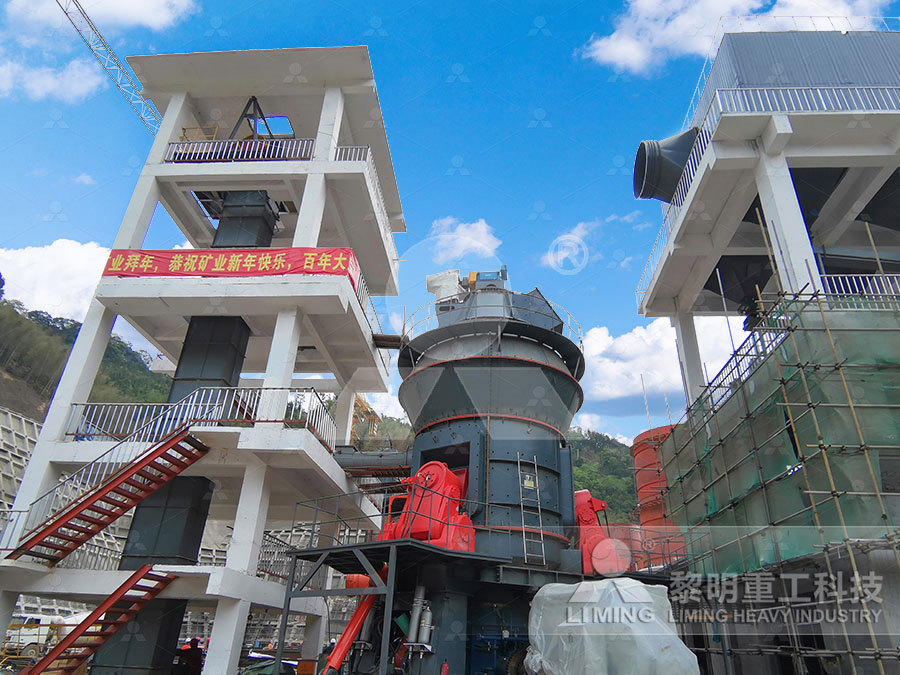
Sustainable grinding and energy savings in feed mills [Podcast]
2023年9月18日 We're talking about the improvement of energy efficiency in feed mill grinding systems What feed mills should be on the lookout for when they're selecting this equipment, and what kind of savings they can expect by implementing a more energyefficient grinding process2019年11月11日 14 November 2024 2 min reading CESCO validates highperformance bagging system for UFC's grain facility in Saudi Arabia CESCO, a global leader in grain handling, storage, and processing solutions, has announced the successful completion of the Factory Acceptance Test (FAT) for a highcapacity bagging line system as part of its extensive project with United EFFICIENCY IN GRINDING AND ENERGY MANAGEMENT IN 2020年12月21日 Energy saving potential for various energyintensive processes in mining [3] 1 Btu (British thermal unit) ≈ 1055 Joule Increasing Energy Efficiency and Productivity of the 2023年11月2日 A highefficiency (HE) washer must use less (than a traditional washer) water, energy, and detergent to be called a HE washer If it falls short of the set guidelines, it cannot sport the HE symbol While not all highefficiency HighEfficiency vs Regular Washers: What to Know
.jpg)
Highefficiency and energyconservation grinding technology
2021年11月1日 A pilotscale grinding technology of ceramic medium stirred mill was proposed in this study Based on the specific productivity and grinding efficiency, the appropriate grinding parameters were 2024年2月5日 Energysaving grid ball mill is a kind of grinding equipment widely used in industrial production It has the advantages of energy saving, high efficiency, and environmental protection However, inHow to Improve Working Efficiency of EnergySaving Grinding efficiency is the unit energy consumption rate of the mill, which represents the amount of material with a particle size of 0043 mm newly generated for every 1 kW•h of energy consumed Energy conservation and consumption reduction in grinding 2022年3月1日 Helping to reduce mining industry carbon emissions: A stepbystep guide to sizing and selection of energy efficient high pressure grinding rolls circuits March 2022 Minerals Engineering 179(2):Helping to reduce mining industry carbon emissions: A stepby

HIGmill high intensity grinding mill Metso
HIGmill high intensity grinding mill is an advanced and energyefficient fine and ultrafine grinding solution that relies on proven (grinding stages) depends on the application and can be as high as 20 Feed slurry is pumped into the bottom mill When the flow transfers significantly increasing grinding efficiency Energy efficiency2020年10月27日 High efficiency deep grinding (HEDG) with its high material removal rates can now compete with conventional cutting processes whilst maintaining surface integrity and surface finish requirements Improving the efficiency of the material grinding process2022年1月1日 Recently, to overcome the problems of high energy consumption, large medium consumption and iron pollution in traditional grinding operation [5–7], Northeastern University has innovatively developed a special ceramicmedium stirred mill (as shown in previously published article by Zhang et al [8]) with small pitch, high speed and low energy consumptionHighefficiency and energyconservation grinding technology using Grinding, semiautogenous grinding, SAG, ball mill, energy, efficiency, greenhouse gas, GHG, carbon dioxide, CO 2 INTRODUCTION Barrick and its subsidiary, African Barrick Gold, operates 26 mines worldwide and has a further six in feasibility or construction Of these mines, 19 currently are operating grinding circuits with 6IMPROVING ENERGY EFFICIENCY IN BARRICK GRINDING CIRCUITS
.jpg)
(PDF) Comparison of energy efficiency between ball mills and
The data show that the stirred mill has an advantage over the ball mill The energy saving of 25%, 37% and 27%, respectively, treating the three ore samples by using the stirred mill was realised On average, 30% energy saving can be expected Product size distributions of the two mills were compared in Fig 4For two years, the mill operated in fly ash grinding, the results in product quality and high energy efficiency convinced to keep the mill Since the second half of 2019, this mill upgrades an existing ball mill grinding circuit of the integrated polysius® booster millsmall grinding media represents the best potential to improve grinding efficiency How do the small grinding media perform in industrial grinding mills? The use of small grinding media in regrind mills proved that finer grinding can be achieved at lower energy consumption In ball mills, smaller grinding media versus 25 mm media generate aEnergy Savings and Improved Recovery with Small Grinding MediaEnergysaving ball mill is a new kind of ball mill grinder developed by us for solving the shortcomings of ordinary ball mill, such as high energy consumption, low output, and low finenessIt is a highefficiency grinder in the ball mill High Efficiency Energy Saving Ball Mill For Sale
.jpg)
An Improved Control Strategy for Ball Mill Grinding Circuits
An improved control strategy is proposed to control ball mill grinding circuits for energy saving and pollution reduction A twolayer optimization architecture combined by particle size optimization layer and energy optimization layer is developed, where the optimal particle size setpoint is calculated first, followed by the energy optimization step2023年1月1日 To achieve sustainability in buildings, high energy efficiency needs to be targeted by reducing environmental impacts through energy performance benchmarking methods [14], energysaving measures [15], the integration of wind turbines in tall buildings [16], an integrative approach using multiobjective search [17], energy modeling and overall thermal transfer value Energy Efficiency in Sustainable Buildings: A Systematic Review In ball mills, energy savings vary from 10 per cent to 40 per cent compared to 25 mm media A regrind ball mill with a mix of small grinding media can be as energy effi cient as an Isa Mill charged with 25 and 35 mm beads In vertical stirred ENERGY SAVINGS AND TECHNOLOGY COMPARISON USING SMALL GRINDING 2008年1月1日 It can be identified as a general conclusion that this recently introduced mill is not yet applied in a wide range in MA compared to other high energy density mills (HEM) like planetary ball mill Comparing energy efficiency in grinding mills ResearchGate
.jpg)
High Pressure Grinding Roll and Magnetic Separation for Energy Saving
2024年5月31日 This paper presents an industrial verification test, adding a high pressure grinding roll and magnetic separation operation after the thirdstage fine crushing operation to reduce the particle size of ball mill feed and improve the processing capacity of grinding operation The optimal process parameters of high pressure grinding roll and magnetic separation were 2022年1月1日 The size of grinding media is the primary factor that affects the overall milling efficiency of a ball mill (eg power consumption and particle size breakage)Effect of grinding media on the milling efficiency of a ball mill2021年5月1日 The result found that 3149% of energy consumption can be reduced in a month by the selected palm oil mill processes by replacing the current motor to highefficiency motor Operation hour of machinesImproving Energy Efficiency at Palm Oil Mill IndustriesBall Mills are widely used in the ceramic and mining industries, where the grinding process requires strict grain size control WEG developed an efficient solution for this applicEnergy Efficiency Solutions Ball Mill WEG
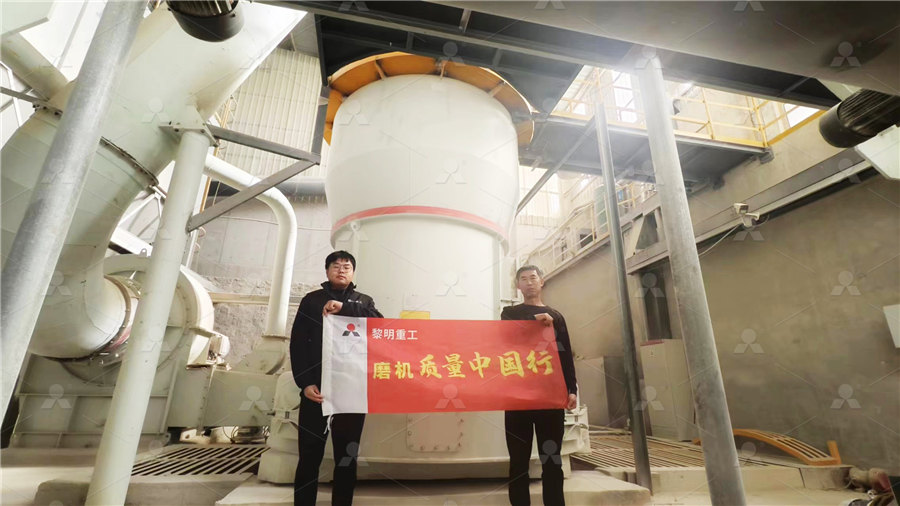
How to Calculate Grinding Mill Operating Efficiency
2017年9月13日 Operating efficiency, based upon using operating work indices, is also a useful tool in comparing the variations in grinding mill operations such as: mill speed, mill size, size of grinding media, mill discharge arrangements, liner designs etc2018年1月1日 In times of unstable market development due to the energy system transformation and legislative measures concerning the reduction of CO 2 emissions, the manufacturing industry is increasingly aware of the ecological and economical importance of the factor energy A considerable share of industrial energy and resource consumption can be attributed to Energy efficiency of stateoftheart grinding processesadditional installations either in construction or planned Grinding is an essential, but energyintensive, part of gold recovery requiring crushers, large diameter semiautogenous grinding (SAG) mills and ball mills with up to 12,000 kW motors Ore grinding can account for 60% of a site’s electrical power load andIMPROVING ENERGY EFFICIENCY IN BARRICK GRINDING CIRCUITS2022年1月1日 A pilotscale grinding technology of ceramic medium stirred mill was proposed in this study Based on the specific productivity and grinding efficiency, the appropriate grinding parameters were ascertained as follows: material ball ratio of 07, ceramic ball medium size ratio (10 mm: 15 mm: 20 mm = 3:2:5), stirring speed of 110 rpm, grinding concentration of 50%, Highefficiency and energyconservation grinding technology using
.jpg)
Rethinking Grinding Efficiency in Ball Mills
Drivers of grinding energy transfer to ore in ball mills • Charge density –charge shape and liner design • Charge surface area • Pulp density rheology • Media mass • Classifier efficiency How can we increase the grinding surface area? 1 Increase the grinding surface • Smaller ball media, or • Different media shape 22009年6月1日 It can be identified as a general conclusion that this recently introduced mill is not yet applied in a wide range in MA compared to other high energy density mills (HEM) like planetary ball mill Comparison of energy efficiency between ball mills and stirred 2023年9月18日 We're talking about the improvement of energy efficiency in feed mill grinding systems What feed mills should be on the lookout for when they're selecting this equipment, and what kind of savings they can expect by implementing a more energyefficient grinding processSustainable grinding and energy savings in feed mills [Podcast]2019年11月11日 14 November 2024 2 min reading CESCO validates highperformance bagging system for UFC's grain facility in Saudi Arabia CESCO, a global leader in grain handling, storage, and processing solutions, has announced the successful completion of the Factory Acceptance Test (FAT) for a highcapacity bagging line system as part of its extensive project with United EFFICIENCY IN GRINDING AND ENERGY MANAGEMENT IN
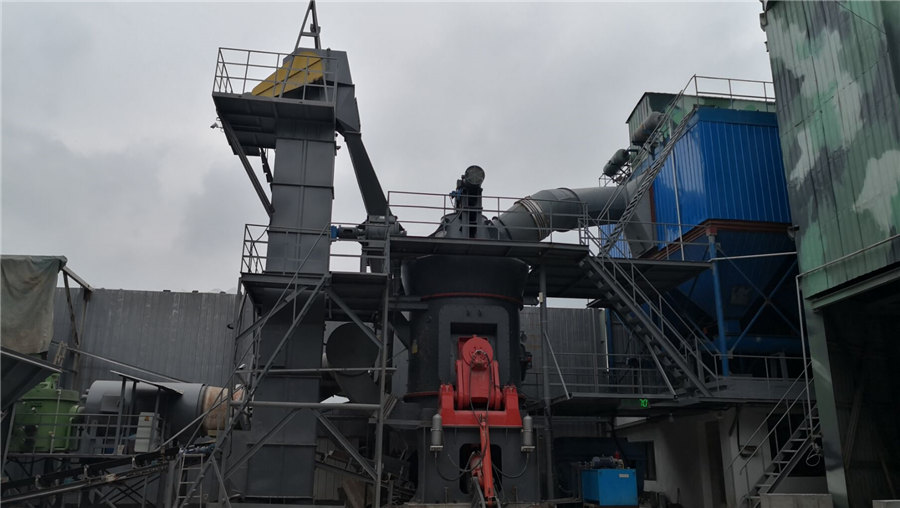
Increasing Energy Efficiency and Productivity of the
2020年12月21日 Energy saving potential for various energyintensive processes in mining [3] 1 Btu (British thermal unit) ≈ 1055 Joule